Uralvagonzavod redesigned at the behest of wartime became a modern armored holding
Nizhniy Tagil Uralvagonzavod is the parent enterprise of the research and production corporation UVZ. Built in 1936 as the main manufacturer of freight rolling stock for the country's railways, the Ural Carriage Building fully justified its name. However, this enterprise, the largest in the world in terms of production volumes and technological areas, is better known as the creator of military equipment, primarily tanks.
Since October 11, 1936, when the first freight gondola cars rolled off the UVZ conveyor, the enterprise has produced more than a million cars. In 2012, Uralvagonzavod produced almost 28 thousand rolling stock products, which is the highest achievement of not only Russian, but also the world car building. Over the years of activity of the Nizhny Tagil enterprise, in addition to wagons, many other products have been mastered here - cryogenic, road-building, oil and gas. Nevertheless, Uralvagonzavod first of all entered the history of the country and the world as Tankograd. 100 thousand tanks have been produced by the Nizhny Tagil enterprise since 1941 - and this is an unsurpassed world record. Today Uralvagonzavod remains the only domestic enterprise capable of serially producing tanks and combat and engineering vehicles based on them.
Legendary "thirty-four"
The Ural Carriage Building became a tank city with the beginning of the Great Patriotic War. By October 1941, 13 enterprises were evacuated to the UVZ site in whole or in part. The largest of them were the Kharkov plant No. 183 named after the Comintern, the Moscow machine-tool plant named after Ordzhonikidze, the Ordzhonikidzegradsk steel plant and the armored hull production of the Mariupol plant named after Ilyich. The combination of all these factories and people, or rather, their merger, alloying on the Ural soil, and one of the most powerful and perfect defense plants in the world was formed, where, in addition to "thirty-fours", were produced bombs, artillery artillery shells, parts for self-propelled rocket launchers "Katyusha", armored hulls for aircraft. Nevertheless, Nizhny Tagil entered the history of the Great Patriotic War forever as the world's largest center for the production of the most important weapons of the era - tanks, the famous "thirty-fours".
T-34 is the best tank of the Second World War. This was recognized by both the allies and the main opponents in that war - the generals of the Wehrmacht. For the first time in the world, it absorbed the qualities of a machine that fully meets the requirements of a combat situation. With an optimal combination of firepower, security and mobility, the thirty-four was distinguished by the maximum possible design simplicity, reliability, manufacturability and high maintainability in the field.
From 1940 to 1945, six Soviet factories produced 58,681 T-34s. This is an absolute record in the world of tank building that has never been broken by anyone. Moreover, more than half, namely 30,627 tanks of the Soviet army, were produced by one plant - No. 183. Of these, 28,952 tanks were made after the transfer of this enterprise from Kharkov to Nizhny Tagil, to the site of the Ural Carriage Works. Almost every second T-34 that took part in the hostilities left the assembly line of the Nizhny Tagil enterprise.
The evacuation of a tank factory to Nizhny Tagil can in no way be considered an accidental decision in the hectic wartime. Already in the middle of 1940, the government commission was looking for a backup enterprise for the mass production of T-34 tanks during the war period. The initial choice fell on the Stalingrad Tractor Plant, where the assembly of combat vehicles began at the end of the same year. However, the General Staff of the Red Army and the People's Commissariat of Medium Machine Building, headed by the future People's Commissar of the tank industry Vyacheslav Malyshev, considered the STZ insufficiently powerful and insisted on the approval of the Ural Carriage Works as the main backup.
By the beginning of the Great Patriotic War, Uralvagonzavod was on the rise in its development, mastered the most complex technologies of a large-scale conveyor, which was the highest form of line organization of large-scale industrial production. UVZ already possessed powerful metallurgical and stamping facilities, as well as a strong energy sector and large areas of assembly shops. All this, according to the project of the still unfinished plant, could be significantly expanded. It would take at least eight to ten years to build similar facilities elsewhere.
Here are the lines from the letter of the representative of the State Planning Committee Kravtsov to the SNK dated February 2, 1940: “Uralvagonzavod is a handsome plant. Completed buildings require only some additional equipment and minor additions. This plant is the most loyal and reliable reserve of the car-building industry."
More than three thousand pieces of equipment were brought and installed, about 70 thousand people were evacuated. In the shortest possible time, in just two months, the production facilities of the Tagil enterprise were completely redesigned for the production of tanks. Already on December 18, 1941, the T-34-76 tank rolled off the world's first tank conveyor, and by the end of the year the first echelon of 25 vehicles went to the front.
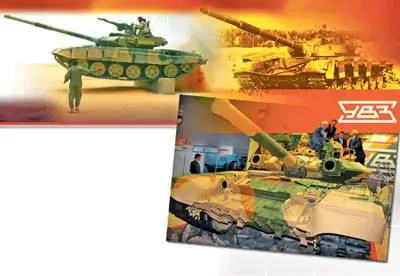
Designers and technologists had to improve many units and parts based on the capabilities of the UTW and taking into account the lack of qualified personnel. During the war period, the design bureau of the Ural Tank Plant successfully played the role of the head enterprise for improving the design of the thirty-four. The design bureau had to develop a number of units, parts and even mechanisms in several versions, taking into account the technical capabilities of a particular plant.
A tremendous amount of work has been done to improve the combat characteristics of the T-34. In 1942, a flamethrower version of the OT-34 tank was developed and put into mass production. The active use by the Germans on the Kursk Bulge in July 1943 of the new Tiger and Panther tanks forced domestic designers to sharply intensify work on equipping armored vehicles, including tanks, with more powerful weapons. As a result, after several months of hard work, a new modification of the thirty-four was created - the T-34-85 tank, which was put into service in January 1944, and two months later began to roll off the UTZ assembly line.
To increase the production of tanks, the most progressive technologies for that time were introduced into production. The powerful metallurgical production of the Uralvagonzavod made it possible to quickly master the smelting of tank steels and the mass casting of the necessary parts - from massive towers to countless tracked tracks. On August 15, 1942, at the Ural Tank Plant, the casting of towers into raw molds made by machine molding was introduced. This technology made it possible to increase the output of tower castings from five to six pieces per day at the end of 1941 to 40 at the end of 1942. Thus, the problem of the quality and quantity of the towers produced was finally solved. If before that UTZ was forced to receive towers from Uralmash (Yekaterinburg), then from now on, the Tagil residents themselves began to supply the towers of the T-34 tank to other factories.
During 1942-1943, specialists from the Kiev Institute of Electric Welding, evacuated to the plant, under the leadership of Yevgeny Oskarovich Paton, together with employees of the armored hull department of UTW, created a whole complex of automatic machines of various types and purposes. The introduction of automatic welding of armored hulls into production not only improved the quality of welded seams, but also increased labor productivity five times, and saved 42 percent of electricity.
The main difficulties were associated with the creation of mechanical assembly and armored hull flow-conveyor production. At the beginning of 1942, painstaking work began in all shops to break down production operations into the simplest components available to untrained workers. This was followed by the "alignment" of the equipment in the order of the sequence of operations, that is, in the form of production lines. At the same time, much attention was paid to debugging new and existing lines to a certain rhythm, ensuring the fulfillment of planned tasks. The first of them appeared in workshops in the same year. By the end of the war, 150 production lines for the production of tank units and parts were organized at the plant, and for the first time in the world, the flow-conveyor assembly of T-34 tanks was introduced.
If production lines were created for the machining of parts and assemblies, then the assembly line was dominated by the conveyor. Since May 1942, a T-34 tank left it every 30 minutes. Every day, the Ural Tank Plant sent an echelon of combat vehicles to the front. On June 1, 1942, a similar conveyor entered commercial operation in armored hull production. In general, the scale of the use of production lines and various conveyors at the plant in wartime has no analogues in the world of tank building.
Thanks to conveyor production, its availability to every low-skilled worker, the simplicity of the design of the T-34 tank, which made it possible to establish its production in huge quantities, one single plant in the production of mass medium tanks surpassed the entire industry of Germany and the countries of Western Europe subject to it.
The system of the People's Commissariat of the Tank Industry of the USSR in general and the Ural Tank Plant No. 183 in particular demonstrated during the Great Patriotic War a higher level of technology and organization of production than the engineering industry in Germany, which is considered unsurpassed. The leadership of Soviet industry, domestic scientists and engineers made better use of the rather meager material and human resources at their disposal and created a more efficient large-scale production of military equipment.
After the end of the war, the chief designer of the Ural Tank Plant, Alexander Morozov, wrote the following lines: “Unlike the supporters of any abstruse decisions, we proceeded from the fact that the design should be simple, not have anything superfluous, accidental and far-fetched. It is, of course, always easier to make a complex vehicle than a simple one, which is far from being capable of every designer … The structural simplicity of the T-34 made it possible, at the most difficult moment for the Motherland, not only to have tanks, but to have a lot of them, much more than the enemy had. … It made it possible to quickly organize the production of combat vehicles at many factories in the country, which had not previously produced such equipment, by the forces of people who previously knew about tanks only by hearsay."
Uralvagonzavod was awarded the Order of the Red Banner of Labor in 1942 and 1943 and the Order of the Patriotic War I degree in 1945 for organizing the mass production of tanks, the selfless work of workers and designers, their enormous contribution to the Great Victory.
Star races "seventy-two"
The vast experience accumulated in wartime in mass flow-conveyor production made it possible to easily and quickly restore the production of freight cars. But at the same time, Uralvagonzavod, which returned its former name, not only retained the status of the largest tank plant in the world, but also turned into a trendsetter of "tank fashions." Among the enterprises that produced combat vehicles before and during the war, the Ural tank demonstrated the greatest efficiency. The principles of in-line production of the enterprise approached the technologies of mass production of tanks in the best possible way. Therefore, the government's decision to preserve tank building in Nizhny Tagil even after the end of hostilities was quite reasonable. In the preserved and carefully guarded design bureau under the leadership of first Alexander Morozov, and since 1953 Leonid Kartsev, all Soviet medium tanks mass-produced in the post-war period were created. And each new model was one of the strongest in the world, combining the latest technical solutions with traditional reliability.
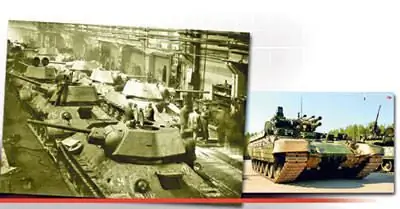
At the end of the 40s, the T-54 tank was put on the conveyor. He was born as a result of the generalization of the experience of the battles of 1941-1945 and was armed with the most powerful cannon of the time of 100 mm caliber. Numerous Soviet divisions equipped with T-54 tanks in the 50s were a strategic factor compensating for the temporary lag of our country in nuclear weapons. For ten years, the absolute superiority of the "fifty-fours" over their opponents - the tanks of NATO countries - did not allow the Cold War to develop into a third world war.
Since 1959, Uralvagonzavod began serial production of the T-55 medium tank - the world's first tank equipped with an integrated anti-radiation protection system, allowing it to operate on areas contaminated after a nuclear strike. The highest reliability, simplicity and combat effectiveness of this vehicle made the T-55 the most massive tank in the world in the 60s and 70s.
In the early 60s, the T-62 tank manufactured by Uralvagonzavod was adopted. It was the first in the world to be equipped with a smooth-bore gun with a high muzzle velocity of an armor-piercing sub-caliber projectile. Protection capable of withstanding the attack of such an BPS appeared on NATO main tanks only in the 80s.
In the late 60s - early 70s, Uralvagonzavod, on the instructions of the Ministry of Defense Industry, like two other enterprises - the Kharkov Transport Machine Building Plant and the Kirov Plant Design Bureau in Leningrad, received a task to develop a new generation mass tank combining firepower, armor protection of heavy machines and the mobility of medium. As a result, the army received three T-72, T-64A and T-80 tanks, each of which met the requirements of modern combat, and their characteristics with the next modification became more powerful. All of them claimed the title of the main tank of the Soviet army.
The dispute was to be resolved by trials, which eventually stretched out for a whole decade. They took place in various regions of the country and in the most difficult operating conditions. When comparing the T-64A and T-72 tanks, it became clear that the Tagil vehicle had a more reliable engine and chassis. The mobility "according to the passport" was approximately equal, but during the runs the "seventy-two" invariably exceeded the T-64A. Outwardly, the rougher and more massive undercarriage of the T-72 turned out to be more reliable than the elegant design of the Kharkov tank, the components of which often failed.
Soon the T-80 tank joined the test subjects, which had a powerful turbine that allowed them to develop unprecedented speed. On the flat roads he had no equal. But on the mountain and steppe routes "seventy-two" invariably prevailed. Ural tank gunners often outnumbered their rivals in terms of the number of targets they hit and hitting accuracy. The fire control systems of the T-80B and T-64B tanks were difficult to use, in contrast to the simple and convenient sight of the T-72. Thus, the Tagil "seventy-two" won the tests and subsequently became the most massive fighting tank of our time. Today, various modifications of the T-72 are in service with the armies of more than 40 countries of the world.
Tagil specialists began to improve the T-72 - then still a prototype "object 172M" - immediately after its appearance in 1970. New modifications were developed by careful selection of the most successful solutions, both constructive and technological. And their correctness was checked at the training ground, test marches and battles. For two decades, the army received serial T-72A, T-72B tanks and engineering vehicles created on their basis - the MTU-72 bridge layer and the BREM-1 armored recovery vehicle. Modernization of "seventy-two" is carried out to this day.
The ideal combination of cost and efficiency, together with almost inexhaustible reserves of modernization, made "seventy-two" a real star on the battlefield. For the development and mastering of the production of the T-72 tank, Uralvagonzavod was awarded the Order of Lenin (1970) and the Order of the October Revolution (1976), and the Ural Design Bureau of Transport Engineering in 1986 - the Order of the October Revolution.
Flying T-90
The crisis and the collapse of the Soviet Union had an extremely difficult impact on Uralvagonzavod, as well as on many other large enterprises in the country. In the face of the state, the constant consumer of military equipment and rolling stock products disappeared, and it was still necessary to win a place in the world market. In spite of everything, the Nizhny Tagil enterprise not only retained its integrity, but also preserved a unique technological complex and the main part of a highly qualified team.
The development of civilian products, the study of market arts, everyday work and worries associated with elementary survival did not diminish the defense significance of Uralvagonzavod. Of course, the incredible volumes of tank production are a thing of the past, but Tagil combat vehicles remain the most important global military-political factor. In order to retain specialists, and, consequently, production potential, Uralvagonzavod had to make a lot of efforts in finding additional orders for armored vehicles. During the 90s, the plant was engaged in the restoration of old tanks, as it turned out that the manufacturer was able to provide the quality of restoration work incomparably higher than the army tank repair enterprises. A great help is the manufacture of spare parts for previously sold tanks. However, the main achievement of the designers of Uralvagonzavod in the 90s was the production of the main battle tank of the Russian army today, the T-90, and the sale of its export version, the T-90S, abroad.
The T-90 missile and gun tank was created on the basis of the vast experience of many years of military operation and the use of T-72 tanks in various countries of the world in real conditions of modern combat, as well as the results of their tests in the most severe climatic conditions. The T-90 and its export version, the T-90S, are maximally adapted for warfare at any time of the day and in extreme situations. The guided weapon system allows firing from a standstill and on the move at stationary and moving targets at ranges of up to 5000 meters, and thanks to the ESSA thermal imaging sight with a 2nd generation camera, the effective firing range at night is at least 3500 meters. Tanks of the T-90 series are characterized by high reliability of the design of all units, assemblies and complexes, they are easy to operate, and the costs of training the crew and specialists are minimized. The 1000 horsepower four-stroke turbo-piston diesel engine and the economical powertrain provide high mobility and maneuverability regardless of the road conditions.
The T-90 was submitted for state proving tests back in January 1989, but due to the ambiguous political situation, only in October 1992 was a decree issued on its acceptance into service and on allowing the sale of the export version of the T-90S. The Tagil car was highly appreciated by both domestic and foreign experts. On trials in India in the summer of 1999, three T-90S tanks showed such endurance that hardly any other vehicle in the world will demonstrate. In the desert, with daytime air temperatures of up to 53 degrees and night temperatures of about 30 degrees, with almost complete absence of roads, each Tagil tank covered more than two thousand kilometers. The Indian military highly appreciated the test results, and the signing of a contract for the supply of a large batch of T-90S tanks to India was a great achievement for Uralvagonzavod. UVZ has been cooperating with the Indian Ministry of Defense for many years. Until now, Uralvagonzavod has been rendering assistance in the licensed production of delivered large assemblies of T-90S products and their warranty support in the troops.
The experience in the creation and serial production of the T-90S tank led to the emergence and adoption of an improved modification of the T-90 - the T-90A tank - by the Russian army. In addition to work on improving the T-90A, the Ural Design Bureau of Transport Engineering also continued to modernize old tanks and develop new engineering vehicles based on it. An engineering clearing vehicle IMR-3M was created, designed to clear the way for troops through zones of severe destruction, as well as through minefields, a BMR-ZM demining combat vehicle capable of conducting tank units through minefields under enemy fire.
The desire of Uralvagonzavod to enter the world market led to the fact that in Nizhny Tagil they began to hold their own exhibitions of weapons. Since 1999, at the test site of the Nizhniy Tagil Institute for Metal Testing in the village of Staratel, exhibitions have been annually held not only of weapons and military equipment, but also of technical means of defense and protection, which invariably gather more and more participating enterprises and attract the attention of top officials of states, domestic and foreign specialists and potential buyers. In 2000, at the exhibition, the Terminator fire support combat vehicle was demonstrated to the general public for the first time - the newest weapon, which has no analogues in the world. In 2011, the modernized T-90S was presented - the next step in the development of domestic tank building, in fact, despite the name, it is an absolutely new combat vehicle. Today Uralvagonzavod as part of the UVZ corporation is one of the main executors of the federal target program "Development of the military-industrial complex of the Russian Federation for the period up to 2020".