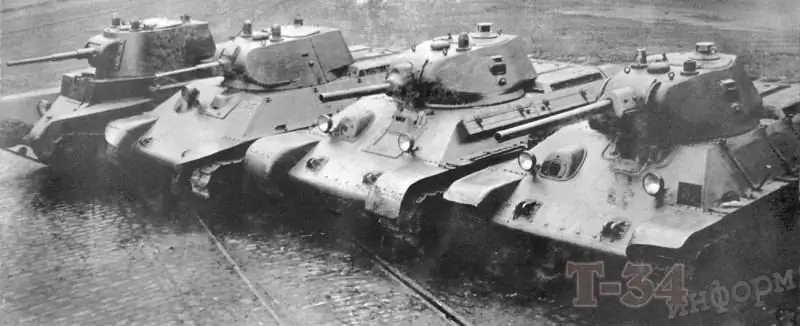
Waiting for the war
Problems with tank production in the Soviet Union in the 1920s and 1930s, associated primarily with the unavailability of the industry, were partly explained by the lagging of the armored industry. By the beginning of 1932, only two of the planned four enterprises could smelt and roll armor. These were the Izhora and Mariupol factories. Due to the excessively high requirements for the speed of production (this was a sign of that time), these factories were chronically behind plans. So, at one of the oldest enterprises in the country, the Izhora plant in the city of Kolpino, in a year they were able to master only 38% of the plan, and in Mariupol at the Ilyich plant - only one quarter. This was largely due to the production of complex cemented heterogeneous armor, which they knew how to make in our country since 1910. A similar type of armor was required to withstand sharp-headed projectiles and bullets, which the usual homogeneous medium and low hardness did not provide. At that time, cemented armor was divided into two grades: low-tempered, unilaterally cemented with a sufficiently hard back side and, in the second version, with a medium hard back side. Basically, for the production of such "sandwiches" required chromium-molybdenum and chromium-nickel-molybdenum steel, which required scarce imported ferroalloy additives. The main alloying element of these steels was chromium (1, 5-2, 5%), which promotes intensive carburization and the achievement of high hardness of the cemented layer after quenching. An attempt to use domestic manganese and silicon for case-hardened steel instead of imported chromium yielded a negative result. When alloyed with manganese, it was revealed that the steel is prone to grain growth at the carburizing temperature (920-950 degrees Celsius), especially with long exposures required for carburizing to a great depth. Correction of the carburized layer overheated during carburization presented significant difficulties and was associated with the need to apply multiple recrystallization, which caused significant decarburization of the cemented layer and sheet leads, and was also economically unprofitable. Nevertheless, until the early 30s, cemented armor was used both in aviation and in tank building. In aircraft, armor plates up to 13 mm thick were cemented, like tank armor up to 30 mm. There were also developments of bullet-resistant 20-mm cemented armor, which did not go beyond experimental development. Such armor definitely had to be massive, which required just gigantic resources for the development of production.
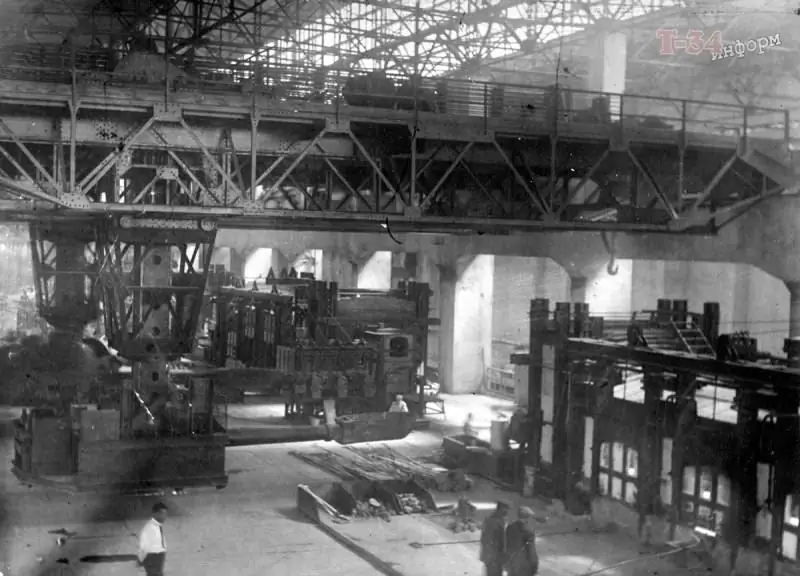
Despite such difficulties with the production of cemented armor, the hull of the T-28 tank was almost completely made of it. But gradually, the domestic industry abandoned the technologies for cementing armor plates, largely due to the extremely high rejects. Considering the production plans demanded by the government and the specialized people's commissariats, this was not at all surprising. The Izhora plant was the first to switch to the new armor, having mastered the smelting of high-hard chromium-siliceous-manganese armor "PI". In Mariupol, they mastered the heterogeneous manganese "MI". The country gradually switched to its own experience in designing armor. Until that time, it was based on foreign technologies (mainly British). The refusal to cement the armor made the sheets thicker with the same armor resistance. So, instead of 10- and 13-mm cemented armor, the T-26 hull had to be welded from 15-mm sheets of Izhora steel "PI". In this case, the tank was 800 kilograms heavy. It should be noted that the transition from expensive cemented steel to relatively low-cost homogeneous armor technologies turned out to be very useful in wartime. If this had not happened in the pre-war years, the development of smelting and rolling of expensive types of armor would have been unlikely given the evacuation of enterprises in 1941-1942.
Since the pre-war years, the main role in the search and research of new types of armor was played by the "Armor Institute" TsNII-48, which is now known as the NRC "Kurchatov Institute" - TsNII KM "Prometheus". The TsNII-48 team of engineers and scientists determined the main directions of the domestic armor industry. In the last decade before the war, the appearance abroad of armor-piercing artillery of calibers from 20 to 50 mm became a serious challenge. This forced the developers to look for new recipes for cooking tank armor.
Birth of 8C
Replace cemented armor resistant to sharp-headed projectiles and bullets on light and medium armored vehicles only with high-hardness steel. And this was successfully mastered by domestic metallurgists. Hulls of armored vehicles BA-10, light tanks T-60 (armor thickness 15 mm, frontal - 35 mm), T-26 (armor thickness 15 mm) and, of course, medium tanks T- 34 (armor thickness 45 mm). The Germans also had high-hardness armor a priority. In fact, all armor (starting with infantry helmets and ending with aviation protective structures) eventually became of high hardness, replacing the cemented one. Perhaps only heavy KVs could afford medium-hardness armor, but this had to be paid for with the greater thickness of the sheets and the final mass of the tank.
The 8C armor steel, the basis of the anti-cannon defense of the T-34 tank, became a real crown of creativity of domestic metallurgists. It should be noted that the production of 8C armor in the pre-war years and during the Great Patriotic War was two seriously different processes. Even for the pre-war industry of the Soviet Union, the production of 8C was a complex and expensive process. They were able to successfully master it only in Mariupol. The chemical composition of 8C: C - 0.22-0.28%, Mn - 1.0-1.5%, Si - 1.1-1.6%, Cr - 0.7-1.0%, Ni - 1.0-1.5%, Mo - 0.15-0.25%, P - less than 0.035% and S - less than 0.03%. For smelting, open-hearth furnaces with a capacity of up to 180 tons were required, pouring future armor into relatively small molds of 7, 4 tons each. Deoxidation of the liquid alloy (removal of excess oxygen) in the furnace was carried out in a costly diffuse method using carbon or silicon. The finished ingot was taken out of the mold and rolled, followed by slow cooling. In the future, the future armor was again heated to 650-680 degrees and cooled in air: it was a high vacation, designed to give the steel plasticity and reduce fragility. Only after that it was possible to subject the steel sheets to mechanical processing, since the subsequent hardening and low tempering at 250 degrees made it too hard. In fact, after the final hardening procedure with 8C, it was difficult to do anything other than weld the body out of it. But here, too, there were fundamental difficulties. Significant internal welding stresses arising from the low ductility of the 8C armor metal, especially with its low quality, leading to the formation of cracks, which often increased over time. Cracks around the seams could form even 100 days after the tank was manufactured. This became a real scourge of the tank building of the Soviet Union during the war. And in the pre-war period, the most effective way to prevent the formation of cracks during welding of 8C armor was the use of preliminary local heating of the welding zone to a temperature of 250-280 degrees. For this purpose, TsNII-48 developed special inductors.
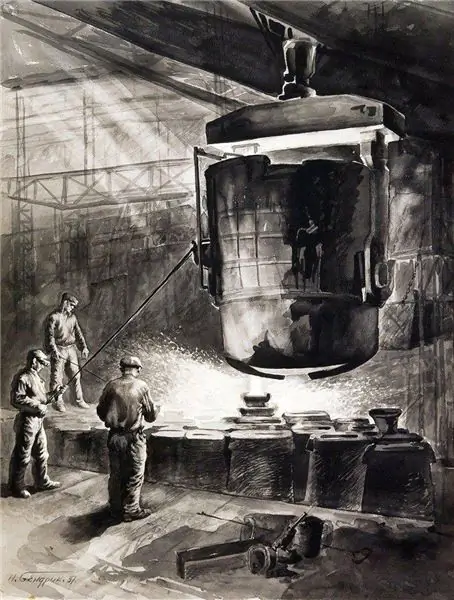
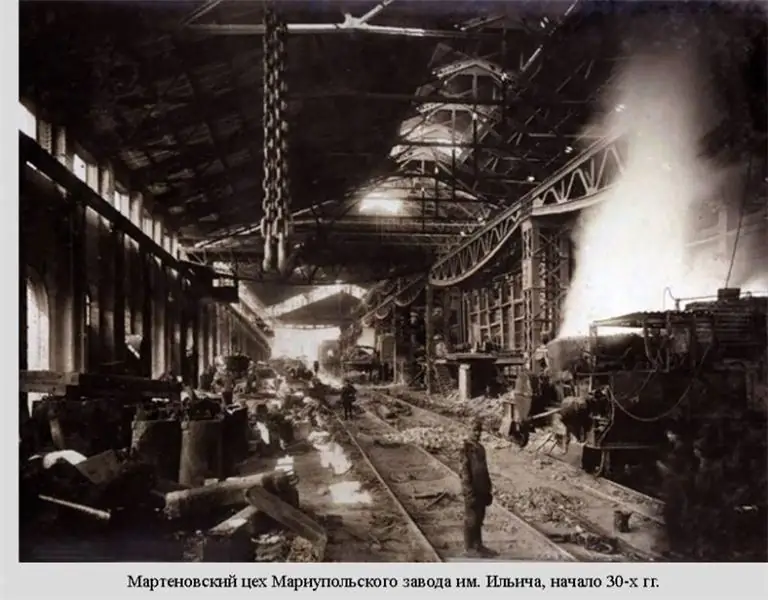
8C was not the only steel grade for T-34 armor. Where there was an opportunity, it was exchanged for other, cheaper varieties. In the pre-war period, TsNII-48 developed 2P structural armor, the production of which significantly saved energy and simplified sheet rolling. The chemical composition of 2P: C - 0.23-0.29%, Mn - 1.2-1.6%, Si - 1.2-1.6%, Cr - less than 0.3%, Ni - less than 0, 5%, Mo - 0.15-0.25%, P - less than 0.035% and S - less than 0.03%. As you can see, the main savings were in scarce nickel and chromium. At the same time, very tight tolerances for the presence of phosphorus and sulfur remained unchanged for 2P, which, of course, was difficult to achieve, especially in wartime. Despite all the simplifications, structural armor made of 2P steel was still subjected to heat treatment - quenching and high tempering, which significantly loaded the thermal equipment necessary for heat treatment of more critical armor parts of tanks, and also significantly increased the production cycle. During the war, TsNII-48 specialists were able to develop technologies for obtaining similar steels, the production of which freed up resources for the main 8C armor.