During the Second World War, the basis of the fleet of vehicles of the American armed forces was made up of Willys MB cars, various trucks, DUKW amphibians and other vehicles on wheeled chassis. It quickly became clear that the wheels do not show themselves in the best way on sandy beaches. As a result, new proposals began to appear concerning the increase in the cross-country ability of wheeled vehicles on difficult surfaces. After the war, a project was developed that received the working designation Squirrel Cage.
Long before the end of the war and the Allied landings in Normandy, British engineers created a special engineering tank Churchill Bobbins. It differed from other armored vehicles in a large frame on which a drum was mounted for transporting a textile tape-track. Moving through difficult terrain on its own tracks, such a tank had to unwind the tape and lay it on the ground. It should have been used as an improvised road to move equipment with insufficient traffic.
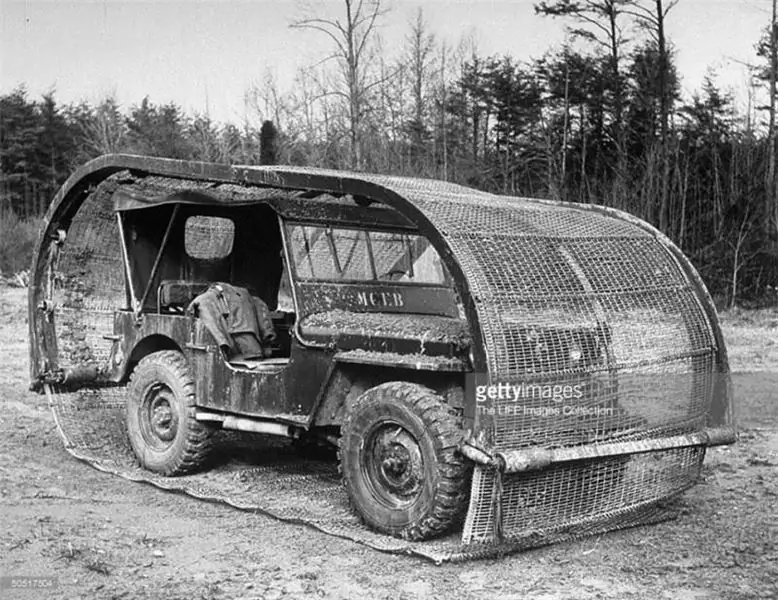
Squirrel Cage system on Willys MB car. December 1, 1948
The pavement-laying tank partially solved the problem of moving wheeled vehicles over sand and other specific surfaces, but this idea had certain drawbacks. So, to organize a large amphibious assault operation, it was required to attract a significant number of engineering tanks and allocate special floating craft for their delivery. The organization of the landing would be easier if wheeled vehicles could have their own means of laying the "road".
In 1948, specialists from the United States proposed their own solution to the existing problem. A group of Marine Corps officers serving at Quantico, Virginia, has developed a set of original equipment for mounting on serial wheeled vehicles, capable of increasing its cross-country ability by multiplying the surface area of the supporting surface.
As far as we know, the original development received a very simple name that fully revealed its essence - Squirrel Cage ("Squirrel wheel"). Indeed, the new units of unusual design had to play the role of the wheel itself, while the machine equipped with them had to take on the "duties" of the squirrel. In other words, a kind of caterpillar propeller was proposed, in which the wheeled vehicle was supposed to perform the functions of a cart with rollers and wheels.
As follows from the available data, the first version of the "Squirrel wheel" was developed for use with a light multi-purpose vehicle such as the Willys MB. This technique was widespread among the troops, and the creation of special equipment for it could lead to understandable positive consequences. As conceived by the authors of the project, the Squirrel Cage system was supposed to be easy to manufacture and install on a car. At the same time, the latter should not have required serious modifications to the basic design.
It was proposed to install a special curved frame made of metal profiles on the jeep. The largest frame elements were the L-shaped side guides. The front and back of these guides were rounded with a large radius, while the central ones were made straight. A pair of curved parts had to be connected to two transverse strength members located at the level of the bumpers of the base car. In the center of such a structure, there was a third curved guide with a smaller section and reduced weight.
On the front and rear sections of the resulting frame, it was proposed to install shafts with wide rollers. A pair of rollers was inside the structure, the second one was outside in relation to them. In addition, in these parts of the "Squirrel wheel" fasteners were placed, with the help of which the entire structure was to be installed on a production car.
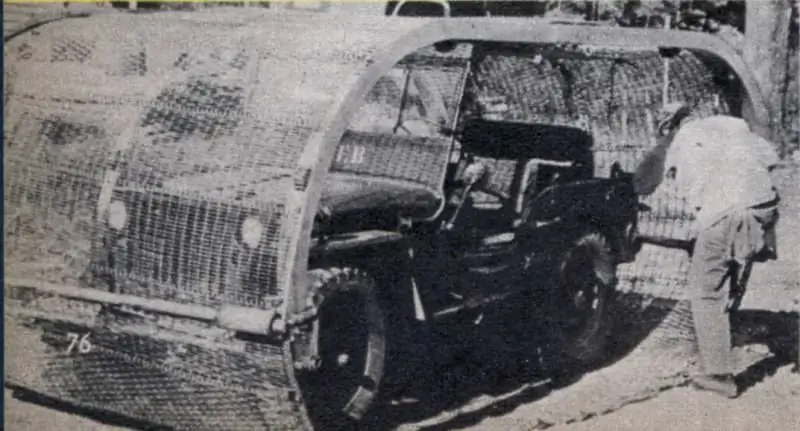
"Willis" and "Wheel" from a different angle
It was proposed to increase the supporting surface of the machine using a metal mesh that serves as a caterpillar. The project envisaged the use of a medium-sized mesh, woven from a sufficiently strong wire. The side edges of the mesh were reinforced with metal bands. At equal intervals, transverse rods were installed on the mesh, providing the required rigidity of the resulting tape. In this case, one of the rods served as a lock connecting the two ends of the rectangular mesh.
It was proposed to hang the reinforced mesh on a frame mounted on a car, pass it under the wheels and then connect it into a continuous tape. The base frame of the system was distinguished by its low height and in the working position was located directly above the roof of the car. For obvious reasons, when using the Squirrel Cage system, the jeep crew had to raise the roof. Otherwise, they risked being hit by hail of sand, mud, or pebbles lifted by the mesh belt.
Inside the looped mesh, the Willys MB or other vehicle could move forward or backward. At the same time, the wheels, running over the nearest section of the mesh, had to stretch it in the right direction. The result was a kind of soft caterpillar with frictional engagement of the driving wheels. The lower branch of such a caterpillar hung in the air or lay on the ground, while the upper one moved along the three guides of the main frame.
The presence of a mesh, reinforced with transverse rods, made it possible to increase the area of the supporting surface in the most noticeable way, complementing the contact spots of the wheels. The car in the Squirrel Wheel was no longer afraid of sand or any other difficult surface, and its crew and passengers could expect to quickly overcome the beach.
No later than the fall of 1948, the Quantico base built a prototype of the Squirrel Cage system, intended for installation on a Willys vehicle. One of the existing cars was soon equipped with new equipment and sent for testing. The jeep with the "Wheel" was run in at one of the nearest test sites. In addition, some further testing was carried out on nearby beaches. In this case, the potential of the structure was tested in the context of use with amphibious technology.
From the point of view of cross-country ability "Squirrel wheel" showed itself in the best way. Despite a certain amount of flexibility and bending in the horizontal plane, the mesh lay correctly under the wheels and increased the support surface. Using such a "caterpillar", the car could drive on muddy dirt roads, on sand, etc. The installation and dismantling of the frame with the mesh did not take much time and did not lead to serious difficulties in operating the equipment.
However, there were some serious problems. The main drawback of the Squirrel Cage was the lack of maneuvering capability. The steering wheels of the car were constantly on a belt that was not characterized by high lateral flexibility. As a consequence, turning the steering wheel could not produce real results. At the same time, there was a risk of belt skewing, up to and including jamming.
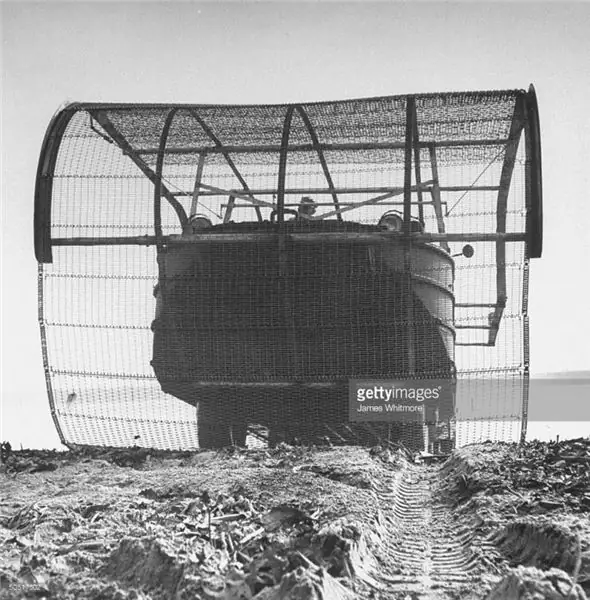
The Squirrel Cage system on the DUKW amphibian. December 1, 1948
The lack of maneuvering ability could also lead to other problems. For example, a sufficiently large bump could cause the car to deviate from the intended route and interfere with further movement or even lead to a collision with other equipment following a parallel course.
Finally, the need to rewind a rather heavy mesh sliding along metal rails resulted in increased engine loads, but did not allow high speed to be obtained. A car with the Squirrel Cage system moved faster through mud or sand than without it, but high speeds comparable to those on the highway were not achievable.
With such problems, the "Squirrel Wheel" system could only be used to land on difficult terrain and quickly traverse it. For further movement, the crew of the car would have to drop the net by pulling out the connecting rod, and then slide off it. Thus, the original project, as a whole, solved the tasks assigned to it, but could do this only with some restrictions. The correct organization of the operation of such systems made it possible to reduce to a certain extent the negative influence of these factors.
Soon, the Squirrel Cage project was redesigned taking into account the requirements of other production equipment. The second carrier of this system was the DUKW amphibious wheeled amphibious vehicle. The "Wheels" modification for such a machine had some differences from the basic version. First of all, it differed in its dimensions, determined in accordance with the dimensions of the amphibian. In addition, a new base frame design was used.
The new frame is based on a pair of wider curved side rails. The front of these guides, bending, rose above the body of the base machine. There was a flat horizontal section behind the front bend. This was followed by another bend, after which the second horizontal element was located. The side guides were interconnected by several transverse beams. In addition, there were three lightweight guides between them. Longitudinal and transverse elements were connected with low inclined struts, fixed on the roof of the DUWK amphibian hull.
The front part of the frame has lost the rollers to hold the mesh. At the same time, three inclined beams appeared under it, with the help of which part of the mass of the frame was transferred to the frontal part of the hull. The grid, as a whole, has not changed. I had to use a wider "track", but the mesh size remained the same. At the same time, longer and thicker transverse rods were needed.
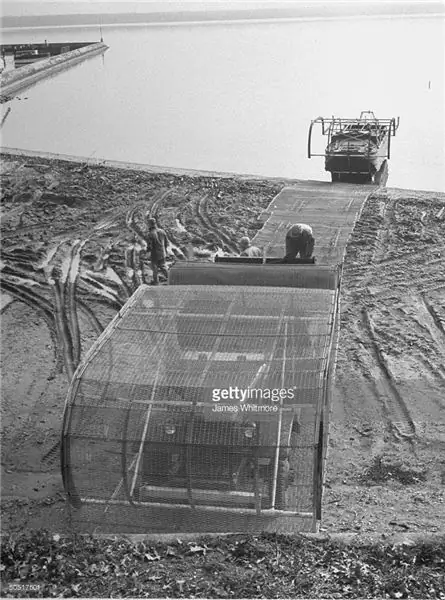
Prototypes of the "Squirrel Wheel" are being tested. In the foreground is a jeep with the means of laying the net. Behind - an amphibian, facing the prepared "road". December 1, 1948
Despite the solid rework of the design, this version of the Squirrel Cage in its capabilities did not differ much from the basic modification for jeeps. There were the same benefits and the same limitations. However, the gain in cross-country ability could completely neutralize all the characteristic problems.
The "squirrel wheel" for the DUKW amphibian was distinguished by a lowered rear section of the frame. This design feature could be the result of a new original proposal. At some point, the authors of the project decided to use the Squirrel Cage system as a flexible pavement paver. In this configuration, a drum was to be placed at the rear of the frame for transporting long netting.
When going into a given area, the stacker had to throw the free end of the net over the front of its frame and run over it. Further forward movement led to the reeling of the net from the drum and placing it on the ground. Thus, the paving machine, using the basic principles of the original project, not only moved on a difficult surface, but also left a path for the passage of other equipment or infantry.
It is known that in the fall and winter of 1948, tests of a similar paver, built on the basis of the Willys MB car, were carried out. There is no exact information on this, but it can be assumed that the carrying capacity of only 250 kg, part of which was also spent on transporting the frame, would not have allowed taking on board a large supply of tape and equipping a long road in one flight. It was possible to get rid of such a problem with the help of a different base chassis. For example, the DUKW amphibian could take on board more than 2 tons of payload.
Tests of several prototypes of the Squirrel Cage systems, built on the basis of serial wheeled vehicles, were completed no later than the beginning of 1949. Based on the results of the inspections, all the necessary conclusions were made, and the specialists of the armed forces made their decision.
Despite the obvious advantages, the military leaders considered the proposed system to increase the cross-country ability not perfect for practical use. The frame and mesh took away a noticeable part of the vehicle's carrying capacity, did not allow maneuvering, and also had some other disadvantages. The paver was also considered unpromising. As a result, the Squirrel Wheel system was not adopted, and at the beginning of 1949 all work on this project was curtailed.
It should be noted that such a decision by the command did not have a negative impact on the further development of the army and the ILC fleet. By this time, several projects were launched to create promising tracked armored vehicles intended for the transport of personnel. Protected tracked vehicles with high terrain and water navigation capabilities did not need additional equipment like the Squirrel Cage. Thus, the further development of military equipment using already known and mastered technologies made the original project simply unnecessary. In the future, American designers did not return to such ideas.