Stovetop fuel is highly efficient for rocket engines
Rocket and space world at a crossroads: global trends call for lower costs and increased environmental safety of space services. Designers have to invent new liquid-propellant rocket engines (LPRE) using environmentally friendly fuels, replacing expensive, highly energy-intensive liquid hydrogen with cheap liquefied natural gas (LNG) with a methane content of 90-98 percent. This fuel, coupled with liquid oxygen, makes it possible to create new highly efficient and inexpensive engines with the maximum use of existing elements of design, material, technological and production backlog.
LNG is non-toxic, and when burned in oxygen, water vapor and carbon dioxide are formed. Unlike kerosene, which is widely used in rocketry, LNG spills evaporate quickly without harming the environment.
First tests
The ignition temperature of natural gas with air and the lower limit of its explosive concentration are higher than those of hydrogen and kerosene vapors; therefore, in the region of low concentrations, in comparison with other hydrocarbon fuels, it is less explosive.
In general, the operation of LNG as a rocket fuel does not require any additional fire and explosion prevention measures that have not been used previously.
The density of LNG is six times that of liquid hydrogen, but half that of kerosene. The lower density leads to a corresponding increase in the size of the LNG tank compared to the kerosene tank. However, taking into account the higher ratio of oxidizer and fuel consumption (it is approximately 3.5 to 1 for the liquid oxygen (LC) + LNG fuel and 2.7 to 1 for the ZhK + kerosene fuel), the total volume of the ZhK + fuel refueled LNG increases only by 20 percent. Taking into account the effect of cryogenic hardening of the material, as well as the possibility of combining the bottoms of LC and LNG tanks, the weighting of the fuel tanks will be relatively small.
And finally, the production and transportation of LNG has long been mastered.
The Design Bureau of Chemical Engineering (KB Khimmash) named after A. M. Isaev in Korolev, Moscow Region, began work (as it turned out, stretching out for years due to very meager funding) on the development of ZhK + LNG fuel in 1994, when the design - design studies and a decision was made to create a new engine using the schematic and structural base of the existing oxygen-hydrogen HPC1 with a thrust of 7.5 tf, successfully operated as part of the upper stage (Cryogenic Upper Stage) 12KRB of the Indian launch vehicle GSLV MkI (Geosynchronous Satellite Launch Vehicle).
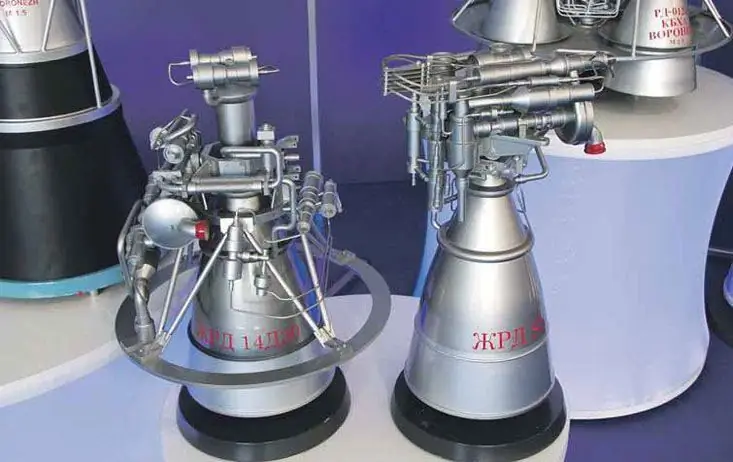
In 1996, autonomous firing tests of a gas generator using liquid liquid and natural gas as fuel components were carried out, which were mainly aimed at checking the start-up and stable operation modes - 13 inclusions confirmed the operability of the gas generator and gave the results that were used in the development of recovery gas generators operating on open and closed schemes.
In August-September 1997, the Khimmash Design Bureau conducted fire tests of the steering unit of the KVD1 engine (also using natural gas instead of hydrogen), in which a chamber deflected in two planes at an angle of ± 39.5 degrees was combined in a single structure (thrust - 200 kgf, chamber pressure - 40 kg / cm2), start and stop valves, pyrotechnic ignition system and electric drives - one standard KVD1 steering unit passed six starts with a total operating time of more than 450 seconds and a chamber pressure in the range of 42-36 kg / cm2. The test results confirmed the possibility of creating a small chamber using natural gas as a coolant.
In August 1997, KB Khimmash began firing tests of a full-size closed circuit engine with a thrust of 7.5 tf on ZhK + LNG fuel. The basis for the manufacture was a modified KVD1 engine of a closed circuit with afterburning of the reducing gas generator gas and cooling the chamber with fuel.
The standard oxidizer pump KVD1 was modified: the diameter of the pump impeller was increased to ensure the required ratio of the oxidizer and fuel pump heads. Also, the hydraulic tuning of the engine lines was corrected to ensure the calculated ratio of components.
The use of a prototype engine that had previously passed a cycle of firing tests on LCD + liquid hydrogen fuel provided the maximum reduction in research costs.
Cold tests made it possible to work out the method of preparing the engine and the stand for hot work in terms of ensuring the required parameters of LNG in bench tanks, cooling the oxidizer and fuel lines to temperatures that guarantee reliable operation of the pumps during the start-up period and stable and stable engine start.
The first fire test of the engine took place on August 22, 1997 at the stand of the enterprise, which today is called the Scientific Test Center of the Rocket and Space Industry (SRC RCP). In the practice of KB Khimmash, these tests were the first experience of using LNG as a fuel for a full-size closed-circuit engine.
The objective of the test was to obtain a successful result due to some reduction in parameters and facilitation of engine operating conditions.
The control of reaching the mode and operating in the mode was carried out using throttle controllers and the ratio of the consumption of fuel components using the HPC1 algorithms, taking into account the mutual influence of the control channels.
The program of the first firing test of the closed circuit engine was completed in full. The engine ran for a specified time, there were no comments on the condition of the material part.
The test results confirmed the fundamental possibility of using LNG as a fuel in the units of an oxygen-hydrogen engine.
There is a lot of gas - no coke
Subsequently, the tests were continued with the aim of a more in-depth study of the processes associated with the use of LNG, checking the operation of engine units in wider application conditions, and optimizing design solutions.
In total, from 1997 to 2005, five firing tests of two copies of the KVD1 engine, adapted for the use of ZhK + LNG fuel, lasting from 17 to 60 seconds, the methane content in LNG - from 89.3 to 99.5 percent, took place.
On the whole, the results of these tests made it possible to determine the basic principles of the development of the engine and its units when using “ZhK + LNG” fuel and to proceed in 2006 to the next stage of research involving the development, manufacture and testing of the C5.86 engine. The combustion chamber, gas generator, turbopump unit and regulators of the latter are structurally and parametrically made specifically for operation on ZhK + LNG fuel.
By 2009, two fire tests of the C5.86 engines with a duration of 68 and 60 seconds were carried out with a methane content in LNG of 97, 9 and 97, 7 percent.
Positive results were obtained on starting and stopping the liquid-propellant engine, operating at steady-state modes in terms of thrust and the ratio of fuel components (in accordance with the control actions). But one of the main tasks - the experimental verification of the absence of solid phase accumulation in the cooling path of the chamber (coke) and in the gas path (soot) with sufficiently long turns on - could not be performed due to the limited volume of bench LNG tanks (the maximum turn-on duration was 68 seconds). Therefore, in 2010, a decision was made to equip the stand for conducting firing tests with a duration of at least 1000 seconds.
As a new workplace, the NRC RCP test bench was used for testing oxygen-hydrogen liquid-propellant rocket engines, which has capacities of the corresponding volume. In preparation for the test, the significant experience gained earlier during the seven fire tests was taken into account. In the period from June to September 2010, the bench systems of liquid hydrogen were refined for the use of LNG, the C5.86 engine No. 2 was installed on the bench, comprehensive tests of the measurement, control, emergency protection systems, and regulation of the ratio of fuel components consumption and pressure in the combustion chamber were carried out.
The bench tanks were filled with fuel from the transport tank of the refueling tanker (volume - 56.4 m3 with a refueling of 16 tons) using an LNG refueling unit, including a heat exchanger, filters, shut-off valves, and measuring instruments. After the filling of the tanks was completed, the bench lines for supplying fuel components to the engine were cooled down and filled.
The engine started and ran normally. The changes in the regime took place in accordance with the influences of the control system. From 1100 seconds, the temperature of the gas generator gas constantly increased, as a result of which a decision was made to stop the engine. The shutdown took place on command at 1160 seconds without any remarks. The reason for the temperature increase was the leakage of the outlet manifold of the combustion chamber cooling path that arose during the test - a crack in the weld of the plugged process nozzle installed on the manifold.
The analysis of the results of the conducted fire test made it possible to conclude:
- in the process of operation, the engine parameters were stable in modes with various combinations of the ratio of the consumption of fuel components (2, 42 to 1 - 3, 03 to 1) and thrust (6311 - 7340 kgf);
-confirmed the absence of solid phase formations in the gas path and the absence of coke deposits in the liquid path of the engine;
- the necessary experimental data were obtained to refine the calculation method for the cooling of the combustion chamber when using LNG as a cooler;
- the dynamics of the exit of the cooling channel of the combustion chamber to the steady-state thermal regime has been studied;
-confirmed the correctness of technical solutions to ensure start-up, control, regulation and other things, taking into account the peculiarities of LNG;
-developed C5.86 with a thrust of 7.5 tf can be used (alone or in combination) as a sustainer engine in promising upper stages and upper stages of launch vehicles;
- the positive results of firing tests confirmed the feasibility of further experiments to create an engine on ZhK + LNG fuel.
At the next fire test in 2011, the engine was turned on twice. Before the first shutdown, the engine ran for 162 seconds. On the second start-up, carried out to confirm the absence of solid phase formation in the gas path and coke deposits in the liquid path, a record duration of operation of an engine of this dimension with a single start - 2007 seconds was achieved, as well as the possibility of thrust throttling was confirmed. The test was terminated due to the depletion of fuel components. The total operating time of this engine instance was 3389 seconds (four starts). The performed flaw detection confirmed the absence of solid phase and coke formation in the engine paths.
A set of theoretical and experimental work with C5.86 No. 2 confirmed:
- the fundamental possibility of creating an engine of the required dimension on the fuel pair of the components "ZhK + LNG" with the afterburning of the reducing generator gas, which ensures the maintenance of stable characteristics and the practical absence of a solid phase in the gas paths and coke deposits in the liquid paths of the engine;
-the possibility of multiple starting and stopping the engine;
-the possibility of long-term operation of the engine;
-the correctness of the adopted technical solutions to ensure multiple start-up, control, regulation, taking into account the features of LNG and emergency protection;
-Capabilities of the NIC RCP stand for long-term tests.
Also, in cooperation with NRC RCP, a technology for transportation, refueling and thermostating of large masses of LNG has been developed and technological solutions have been developed that are practically applicable for the procedure for refueling flight products.
LNG - the path to reusable flights
Due to the fact that the components and assemblies of the demonstrator engine C5.86 No. 2 due to limited funding were not optimized to the proper extent, it was not possible to fully solve a number of problems, including:
clarification of the thermophysical properties of LNG as a coolant;
obtaining additional data to check the convergence of the characteristics of the main units when simulating on water and operating on LNG;
experimental verification of the possible influence of the composition of natural gas on the characteristics of the main units, including the cooling paths of the combustion chamber and gas generator;
determination of the characteristics of liquid-propellant rocket engines in a wider range of changes in operating modes and basic parameters both with single and multiple starts;
optimization of dynamic processes at startup.
To solve these problems, KB Khimmash manufactured an upgraded C5.86A No. 2A engine, the turbo pump unit of which was for the first time equipped with a starting turbine, an upgraded main turbine and a fuel pump. The combustion chamber cooling path has been modernized and the fuel ratio throttle needle has been redesigned.
A fire test of the engine was carried out on September 13, 2013 (methane content in LNG - 94.6%). The test program provided for three switches with a total duration of 1500 seconds (1300 + 100 + 100). The engine started and operated normally, but at 532 seconds the emergency protection system generated an emergency shutdown command. The cause of the accident was the ingress of a foreign metal particle into the flow path of the oxidizer pump.
Despite the accident, C5.86A No. 2A worked for quite a long time. For the first time, an engine was launched, intended for use as part of a rocket stage, which requires multiple start-ups, according to the implemented scheme using an onboard rechargeable pressure accumulator. A stable operating mode was obtained for a given thrust mode and the maximum ratio of the fuel components consumption that was realized earlier. Possible reserves for boosting thrust and increasing the ratio of fuel components consumption have been determined.
Now KB Khimmash is completing the manufacture of a new copy of C5.86 for testing for the maximum possible resource in terms of operating time and the number of starts. It should become a prototype of a real engine on ZhK + LNG fuel, which will give a new quality to the upper stages of launch vehicles and breathe life into reusable transport systems. With their help, space will become available not only for researchers and inventors, but, possibly, just for travelers.