1. Introduction
The first experience of the modern civil war has been accumulated, of course, in Afghanistan. And he immediately showed the insufficient effectiveness of aviation. In addition to the unpreparedness of the pilots and the shortcomings of tactics, the aircraft themselves did not correspond to the nature of the counter-guerrilla war. Supersonic fighter-bombers, created for the European theater of operations, were unable to deploy in mountain gorges, and their sophisticated aiming and navigation equipment was practically useless when searching for an unobtrusive enemy. The capabilities of the aircraft remained unclaimed, and the effectiveness of their strikes was low.
Only the Su-25 attack aircraft turned out to be a suitable vehicle - maneuverable, obedient in control, well-armed and protected. Su-25 (NATO codification: Frogfoot) - Soviet-Russian armored subsonic attack aircraft. Designed for direct support of ground forces over the battlefield day and night with visual visibility of the target, as well as the destruction of objects with specified coordinates around the clock in any weather conditions. In the Russian troops he received the nickname "Rook".
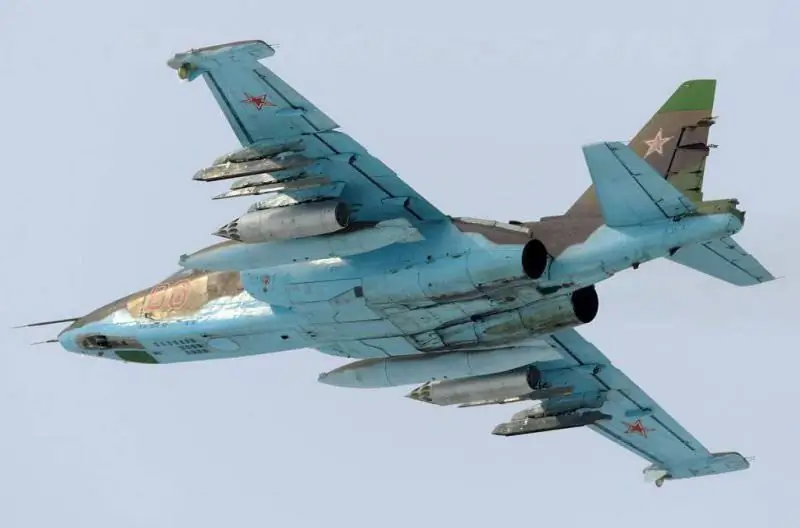
"2" History of creation
At the end of the 60s. it became clear that the Su-7B, MiG-19, MiG-21 and Yak-28 aircraft do not provide effective destruction of small-sized ground targets on the battlefield, and the lack of armoring of the cockpit and important units makes them vulnerable to small arms fire and small-caliber artillery.
In March 1968, senior lecturer of the Air Force Academy. NOT. Zhukovsky I. Savchenko invited the specialists of the Design Bureau of P. O. Sukhoi to jointly develop a project for a new aircraft to support the ground forces. The initiative group (O. S. Samoilovich, D. N. Gorbachev, V. M. Lebedev, Yu. V. Ivashechkin and A. Monakhov) developed a battlefield aircraft (SPB) and, after defining its general appearance, presented the project to P. O. Sukhoi, who approved it under the name T-8. In March 1969, a competition was held to develop a prototype of an attack aircraft with the participation of the design bureau. A. I. Mikoyan and A. S. Yakovlev (proposed modification projects for the MiG-21 and Yak-28), S. V. Ilyushin and P. O. Sukhoi (new projects for the Il-102 and T-8). The victory was won by the T-8 project, which had a more advanced sighting system and smaller, in comparison with the Il-102, dimensions and weight. The project provided for the development of an easy-to-manufacture and unpretentious in maintenance aircraft-attack aircraft, designed for operation by a minimally trained flight and ground personnel with a short preparation time for departure using an air-mobile ground service complex, which provided autonomous basing of an attack aircraft on limitedly equipped unpaved airfields.
The development of a preliminary design of an aircraft for direct support of troops over the battlefield of the St. S. Samoilovich, D. N. Gorbachev, V. M. Lebedev, Yu. V. Ivashechkin and A. Monakhov in March 1968. In May 1968, the design of an aircraft began at the P. O. Sukhoi Design Bureau under the name T-8 … The study of the aerodynamic scheme of the future attack aircraft began at TsAGI in 1968. The Ministry of Defense of the USSR, at the suggestion of the Minister of Defense A. A. Grechko, in March 1969 announced a competition for the project of a light attack aircraft, in which the Sukhoi Design Bureau (T-8), Yakovlev (Yak -25LSh), Mikoyan and Gurevich (MiG-21LSh) and Ilyushin (Il-42). The requirements of the Air Force were formulated for the competition. The competition was won by T-8 and MiG-21LSh aircraft. Issue of working drawings and preparation for the construction of a prototype aircraft - summer 1970. At the same time, the Air Force changed the requirements for maximum speed at the ground to 1200 km / h, which put the project at risk of complete overhaul. By the end of 1971, it was possible to agree on a change in the requirements for maximum speed up to 1000 km / h (0.82 M).
The design of the T-8 was resumed in January 1972 after P. O. Sukhoi approved the general appearance of the attack aircraft (1972-06-01) and signed an order to start the detailed design of the aircraft. M. P. Simonov was appointed as the project manager, Yu. V. Ivashechkin was appointed as the lead designer. Since August 1972, the chief designer of the T-8 is O. S. Samoilovich, the leading designer since 25.12.1972 is Y. Ivashechkin (he is also the chief designer since October 6, 1974). The model of the aircraft was adopted by the commission in September and the construction of the prototype began at the end of 1972. The prototype T-8-1 made its first flight at the LII airfield in Zhukovsky on February 22, 1975 (pilot - V. S. Ilyushin). The second prototype aircraft with some design changes (T-8-2) went for testing in December 1975.
In the summer of 1976, the engines on the prototypes were replaced by the more powerful R-95Sh, some structural elements were changed (1978) - the updated prototypes were named T-8-1D and T-8-2D. In July 1976, the T-8 was named "Su-25" and preparations began for serial production at an aircraft plant in Tbilisi (initially it was planned to expand production in Poland). The tactical and technical requirements for the Su-25 attack aircraft with the R-95Sh engine, a modified composition of the avionics - like the T-8-1D - were approved by the USSR Ministry of Defense only on March 9, 1977 and discussed from May 11 to May 24, 1977 at the mock-up commission …
Information about the aircraft and the code name RAM-J appeared in the West in 1977 according to space reconnaissance data (RAM = Ramenskoye (airfield), railway station near the LII airfield). The first production vehicle (T-8-3) was produced in Tbilisi in 1978 and made its first flight on June 18, 1979 (pilot - Y. A. Egorov). The state tests of the aircraft took place (the first stage) from March to May 30, 1980 (completed in December 1980). The production of the two-seat Su-25UB / UT / UTG and the single-seat Su-39 was carried out at the aircraft plant in Ulan-Ude. In March 1981, an act on the completion of state tests of the aircraft was signed and it was recommended for adoption by the USSR Air Force. In April 1981, the aircraft began to enter combat units. Since June 1981, the Su-25 took part in the hostilities in Afghanistan. Officially, the Su-25 entered service in 1987.
On January 6, 1972, the general view of the T-8 attack aircraft was approved and detailed design began under the leadership of M. P. Simonov (from August - OS Samoilovich), and from 25.12.1972 - Yu. V. Ivashechkin, who from 6.10.1974 became the leader of the topic. In May 1974, it was decided to build two copies of the T-8 aircraft, in December an experienced attack aircraft was transported to the LII airfield, and on February 22, 1975, under the direction of V. S. Ilyushin, it took off. In June 1976, a decision was made to deploy the production of attack aircraft at the aircraft plant in Tbilisi. In March 1977, the tactical and technical requirements for the aircraft were approved and the Design Bureau presented to the customer a draft design of the aircraft with R-95Sh engines, a modified wing and a more advanced sighting and navigation system.
The aircraft was officially transferred for state tests in June 1978, the first flight was made on July 21, and flights under the state test program began in September (V. Ilyushin, Y. Yegorov). By the beginning of the state tests, the modified Su-17MZ sighting and navigation system was installed on the aircraft, which ensured the use of the most modern guided weapons, incl. missiles with a laser guidance system. The cannon container was replaced with a 30 mm double-barreled cannon AO-17A (GSh-2-30 series). The pre-production prototype of the first Tbilisi assembly, on which all the conceptual solutions of the attack aircraft project were implemented, took off on June 18, 1979.
In the winter of 1979-1980. the first stage of state tests was completed on the T-8-1D, T-8-3 and T-8-4 aircraft. After the successful application in April-June 1980 of the T-8-1D and T-8-3 aircraft in Afghanistan, the Air Force leadership decided to take this into account as the second stage of state tests without flight studies of spin characteristics. The final flights under the test program took place at the Mary airfield in Central Asia, 1980-30-12.it was officially completed, and in March 1981 an act on their completion was signed with a recommendation to put the aircraft into operation. Due to the failure to fulfill some of the TTZ points, the Su-25 attack aircraft was put into service in 1987.
"3" Aerodynamic scheme
According to its aerodynamic layout, the Su-25 attack aircraft is an aircraft made according to a normal aerodynamic configuration, with a high wing.
The aerodynamic layout of the aircraft is tuned to obtain optimal performance at subsonic flight speeds.
The aircraft wing has a trapezoidal shape in plan, with a sweep angle along the leading edge of 20 degrees, with a constant relative profile thickness along the wingspan. The wing of the aircraft has a projection area of 30.1 sq. The angle of the transverse V wing is - 2.5 degrees.
The selected laws on the sweep and curvature of the airfoil ensured a favorable development of the stall at high angles of attack, which begins near the trailing edge of the wing in its middle part, which leads to a significant increase in the dive moment and naturally prevents the aircraft from hitting the supercritical angles of attack.
The wing load is selected from the conditions for ensuring flight near the ground in a turbulent atmosphere at speeds up to the maximum flight speed.
Since, based on the flight conditions in a turbulent atmosphere, the wing load is quite high, effective wing mechanization is required to ensure a high level of takeoff and landing and maneuvering characteristics. For these purposes, wing mechanization is implemented on the aircraft, consisting of retractable slats and two-slotted three-section (maneuver-take-off-landing) flaps.
The increase in torque from the released wing mechanization is countered by rearranging the horizontal tail.
The installation of containers (nacelles) at the ends of the wing, in the tail parts of which there are splitting flaps, made it possible to increase the value of the maximum aerodynamic quality. For this, the shape of the cross-sections of the containers and the location of their installation relative to the wing have been optimized. The longitudinal sections of the containers are an aerodynamic profile, and the cross sections are oval with sealed top and bottom surfaces. Tests in wind tunnels confirmed the calculations of aerodynamics to obtain higher values of the maximum aerodynamic quality when installing containers.
The brake flaps installed in the wing containers meet all the standard requirements for them - an increase in the aircraft drag by at least two times, while their release does not lead to a rebalancing of the aircraft and a decrease in its bearing properties. The brake flaps are split, which has increased their efficiency by 60%.
The aircraft uses a fuselage with side unregulated air intakes with an oblique entrance. The lantern with a flat forehead smoothly turns into a gargrot located on the upper surface of the fuselage. The gargrot in the aft fuselage merges with the tail boom separating the engine nacelles. The tail boom is a platform for the installation of a horizontal tail with an elevator and a single-keel vertical tail with a rudder. The tail boom ends with a container for a parachute-braking installation (PTU).
The aerodynamic layout of the Su-25 attack aircraft provides:
1.receiving high aerodynamic quality in cruising flight and high lift coefficients in takeoff and landing modes, as well as during maneuvering;
2. a favorable course of the dependence of the longitudinal moment along the angle of attack, which prevents access to large supercritical angles of attack and, thereby, increases flight safety;
3. high maneuverability when attacking ground targets;
4. acceptable characteristics of longitudinal stability and controllability in all flight modes;
5. steady-state dive mode with an angle of 30 degrees at a speed of 700 km / h.
The high level of aerodynamic quality and bearing properties made it possible to return the aircraft with heavy damage to the airfield.
The fuselage of the aircraft has an elliptical section, made according to the semi-monocoque scheme. The fuselage structure is prefabricated and riveted, with a frame consisting of a longitudinal power set - spars, beams, stringers and a transverse power set - frames.
Technologically, the fuselage is divided into the following main parts:
1.the head part of the fuselage with a folding nose, a folding part of the canopy, flaps of the front landing gear;
2. the middle part of the fuselage with flaps of the main landing gear (air intakes and wing consoles are attached to the middle part of the fuselage);
3. the tail section of the fuselage, to which the vertical and horizontal empennage are attached.
The braking parachute container is the tail end of the fuselage. The aircraft fuselage has no operational connectors.
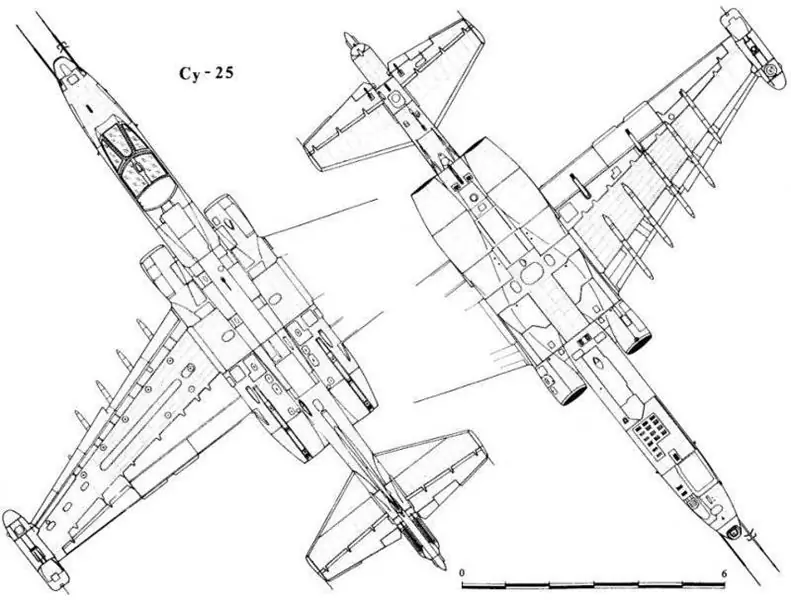
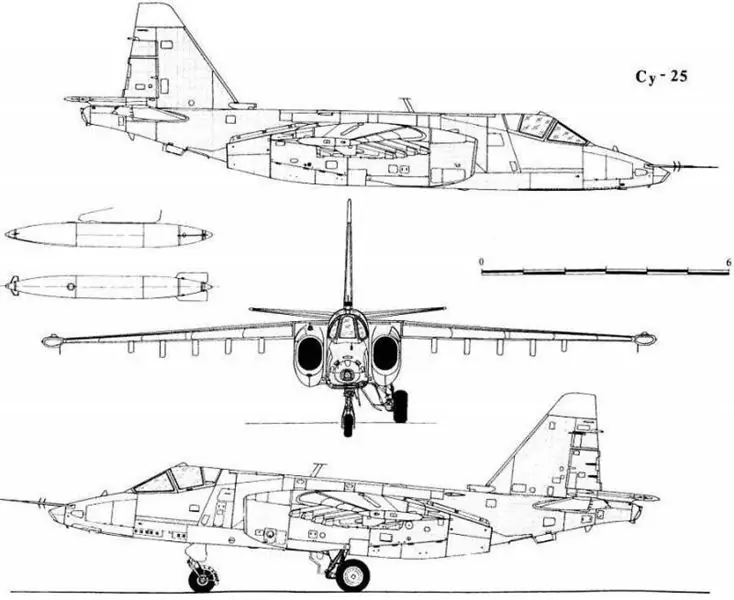
The Su-25 attack aircraft is a fairly highly protected aircraft. The systems for ensuring the combat survivability of the vehicle account for 7, 2% of its normal take-off weight, which is no less than 1050 kg. In this case, the vital systems of the aircraft are shielded by less important systems and are duplicated. During the development, special attention was paid to the protection of critical elements and components of the aircraft - the cockpit and the fuel system. The cockpit is welded from special aviation titanium armor ABVT-20. The thickness of the armor plates with which the pilot is protected is from 10 to 24 mm. The frontal glazing of the cockpit provides the pilot with bulletproof protection and is a special glass block TSK-137 with a thickness of 65 mm. At the rear, the pilot is protected by a 10 mm thick steel armored backrest and a 6 mm thick armored headrest. The pilot is almost completely protected from shelling from any small arms with a caliber of up to 12.7 mm, in the most dangerous directions from a barrel weapon with a caliber of up to 30 mm.
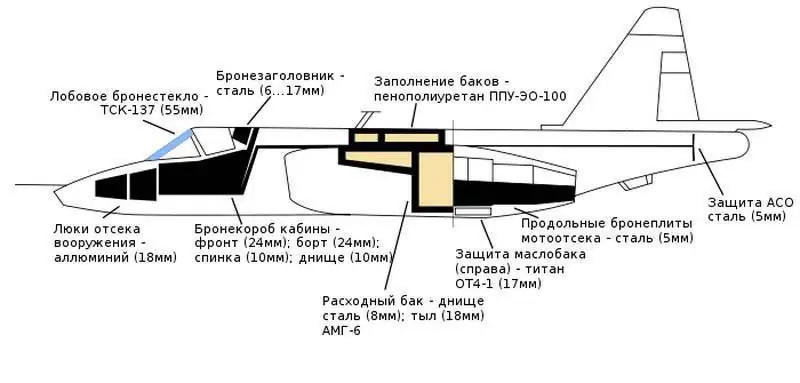
In the event of a critical hit, the pilot is rescued using the K-36L ejection seat. This seat ensures the rescue of the pilot at all speeds, modes and flight altitudes. Immediately before the ejection, the cockpit canopy is dropped. Ejection from the plane is done manually with the help of 2 control handles, which the pilot must pull with both hands.
"4" Power plant
The aircraft is equipped with two interchangeable non-afterburning turbojet engines R-95, with an uncontrolled nozzle with a downstream gearbox, with an autonomous electric start.
R-95 - turbojet single-circuit twin-shaft aircraft engine, developed in 1979 at the Federal State Unitary Enterprise "Research and Production Enterprise" Motor "" under the leadership of S. A. Gavrilov, Main characteristics:
• Overall dimensions, mm:
• length - 2700
• maximum diameter (without units) - 772
• max. height (without object units) - 1008
• max. width (without object aggregates) - 778
• Dry weight, kg. - 830
Parameters in terrestrial conditions at maximum mode:
• thrust, kgf - 4100
• air consumption, kg / s - 67
• specific fuel consumption, kg / kg.h - 0, 86
The engines are housed in engine compartments on both sides of the aircraft's tail boom.
Air is supplied to the engines through two cylindrical air ducts with oval subsonic unregulated air intakes.
The aircraft engine has an unregulated converging nozzle located in the tail section of the nacelle so that its cut coincides with that of the nacelle. There is an annular gap between the outer surface of the nozzle and the inner surface of the engine nacelle for the outlet of air blown through the engine compartment.
The systems that ensure the operation of the power plant of the aircraft include:
• fuel system;
• engine control system;
• devices for monitoring the operation of engines;
• engine starting system;
• engine cooling system;
• fire protection system;
• drainage and venting system.
To ensure the normal operation of the engines and its systems, the drainage system ensures that the remaining fuel, oil and slurry are removed from the aircraft after stopping the engines or in the event of a failed start.
The engine control system is designed to change the operating modes of the engines and provides autonomous control of each engine. The system consists of an engine control panel on the left side of the cockpit and a cable guide with rollers supporting the cable, tandems that regulate the tension of the cables, and gearbox blocks in front of the engines.
The engine oil system is of a closed type, autonomous, designed to maintain the normal temperature state of the rubbing parts, reduce their wear and tear and reduce friction losses.
The starting system provides autonomous and automatic starting of engines and their output to a stable speed. Starting engines on the ground can be done from the onboard battery or from an airfield power source.
Cooling of engines, units and fuselage structure from overheating is provided by the oncoming air flow entering through the cooling air intakes due to the high-speed pressure. Air intakes for cooling the engine compartments are located on the upper surface of the engine nacelles. The air trapped in them under the action of the high-speed pressure spreads over the engine compartments, cooling the engine, its units and structures. Exhaust cooling air flows out through the annular gap formed by the nacelle and engine nozzles.
Cooling of electric generators installed on engines is also performed by the oncoming air flow due to the high-speed pressure. Air intakes for cooling the generators are installed on the upper surface of the fuselage tail boom in front of the keel, in the tail boom the branch pipes are divided into left and right pipelines. After passing the generators and cooling them, the air enters the engine compartment, mixing with the main cooling air.
"5" Specifications:
Crew: 1 pilot
Length: 15, 36 m (with LDPE)
Wingspan: 14, 36 m
Height: 4.8 m
Wing area: 30.1m²
Weight:
- empty: 9 315 kg
- equipped: 11 600 kg
- normal takeoff weight: 14 600 kg
- maximum takeoff weight: 17 600 kg
- weight of armor protection: 595 kg
Power plant: 2 × turbojet engine R-95Sh
Flight characteristics:
Speed:
- maximum: 950 km / h (with normal combat load)
- cruising: 750 km / h
- landing: 210 km / h
Combat radius: 300 km
Practical range at altitude:
- without PTB: 640 km
- from 4 × PTB-800: 1 250 km
Practical range at the ground:
- without PTB: 495 km
- from 4 × PTB-800: 750 km
Ferry range: 1,950 km
Service ceiling: 7,000 m
Maximum altitude of combat use: 5,000 m
Armament:
One 30-mm double-barreled cannon GSh-30-2 in the lower bow with 250 rounds. Combat load - 4340 kg on 8 (10) hardpoints
Normal load - 1340 kg.
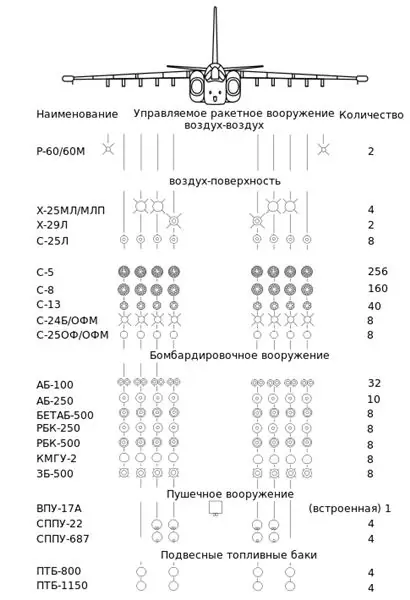
"6" The purpose of the aircraft
Su-25 is an attack aircraft. The main purpose of attack aircraft is direct air support of ground forces on the battlefield and in the tactical depth of enemy defense. The planes were supposed to destroy tanks, artillery, mortars, other technical means, as well as enemy manpower; oppose the approach to the battlefield of tactical and operational reserves of the enemy, destroy headquarters, communications and field depots, disrupt transportation, destroy aircraft at airfields and actively fight transport and bomber aircraft in the air; sink river and sea vessels, conduct aerial reconnaissance.
"7" Combat use
The Su-25 attack aircraft was used in the Afghan War (1979-1989), the Iran-Iraq War (1980-1988), the Abkhaz War (1992-1993), the Karabakh War (1991-1994), the First and Second Chechen Wars (1994-1996 and 1999-2000), War in South Ossetia (2008), War in Ukraine (2014).
The first Su-25s began to enter combat units in April 1981, and already in June, serial attack aircraft were actively working on enemy targets in Afghanistan. The advantage of the new attack aircraft was obvious. Operating at a lower speed and altitude, the Su-25 did work that other aircraft could not do. Another proof of the effective work of the Su-25 is the fact that sorties were often carried out with a bomb load exceeding 4000 kg. This aircraft became a truly unique machine, thanks to which hundreds, and possibly thousands of Soviet soldiers were saved.
In Afghanistan (1979-1989) for 8 years, starting from April 1981, the Su-25 confirmed its high combat effectiveness and survivability. According to the OKB im. P. O. Sukhoi carried out about 60 thousand sorties, fired 139 guided missiles, of which 137 hit targets, and a huge number of unguided missiles were fired. The losses amounted to 23 aircraft, with an average flight time for each of them 2800 hours. The downed Su-25 had, on average, 80-90 combat damage, and there were cases of aircraft returning to base with 150 holes. According to this indicator, it significantly surpassed other Soviet aircraft and American aircraft used in Afghanistan during the Vietnam War. During the entire period of hostilities, there were no cases of explosion of fuel tanks and loss of an attack aircraft due to the death of a pilot.
However, the Su-25 received its real baptism of fire in modern history within the Russian borders during the first Chechen campaign, when it had to work not only in the mountains, but also in the conditions of settlements. There were cases when, using high-precision weapons with laser guidance, the Su-25 worked out the target within one separate area taken at the household. Also, a pair of attack aircraft distinguished themselves during the elimination of the leader of the CRI, Dzhokhar Dudayev, who were directed at the target by the A-50 radar reconnaissance board. As a consequence, it was in the Caucasus that the effectiveness of the Su-25 and its modifications was often the key to the successful completion of the task and the withdrawal of the land group without losses.
It is also worth noting that, despite its venerable age, the Su-25 successfully worked during the recent "Ossetian-Georgian" conflict, when Russian pilots successfully coped with enemy ground targets and only three out of ten aircraft were knocked out from the Buk air defense system, which Ukraine provided to Georgia. It was during this period that a photo of one of the Su-25 aircraft appeared on the network, which flew to the airbase with a torn right engine. I flew, and without any problems, on one engine.
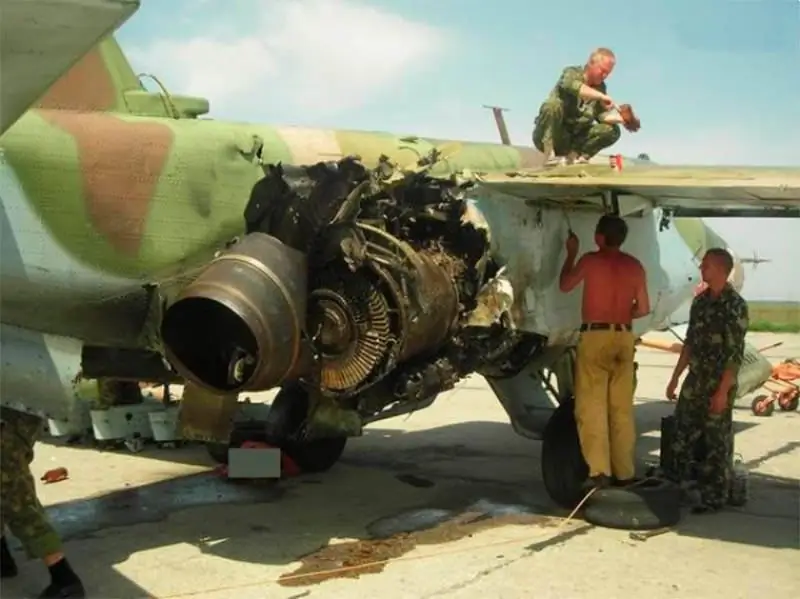
"8" Production and modifications
The Su-25 was mass-produced from 1977 to 1991. There was and is a huge number of modifications of the legendary aircraft.
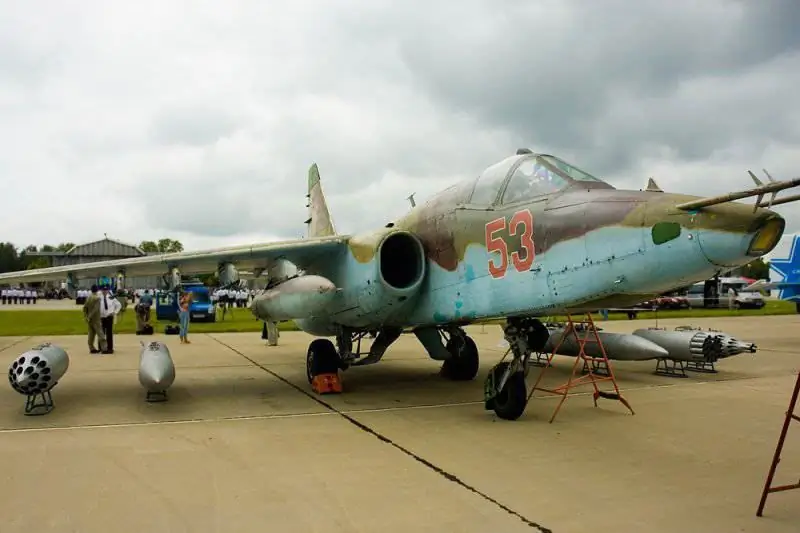
Since 1986, the plant in Ulan-Ude began production of the "twin" Su-25UB, a two-seater combat training aircraft. Apart from the addition of a second pilot's seat, the aircraft is almost completely identical to the classic attack aircraft and can be used for both training and combat.
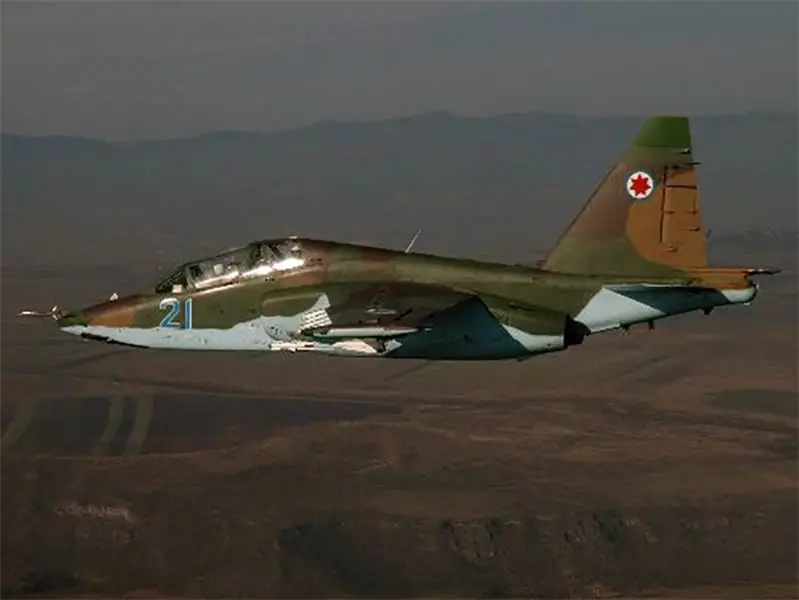
The most modern modification of the Su-25SM serial attack aircraft differs from the "original source" by a more modern complex of on-board electronic equipment and the presence of more modern weapons.

The project of the Su-25K carrier-based attack aircraft with catapult take-off did not go beyond the project stage (due to the lack of Russian aircraft carriers with catapults), but several Su-25UTG carrier-based training aircraft were produced, intended for basing on board the aircraft carrier "Admiral of the Fleet Kuznetsov" with a springboard takeoff. The aircraft turned out to be so successful that it serves as the main training aircraft for training deck aviation pilots.
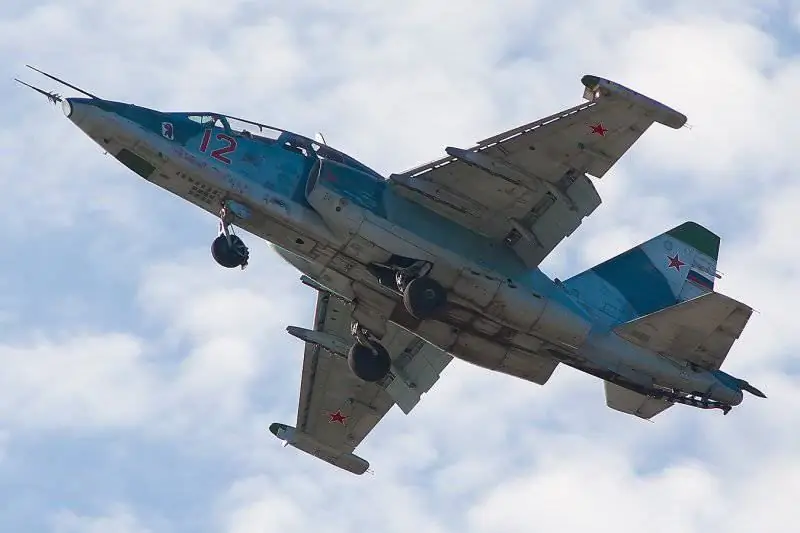
The most interesting and complex modification is the Su-25T anti-tank aircraft, the decision to create was made back in 1975. The main problem in the development of this aircraft was the creation of airborne electronic equipment (avionics) for the detection, tracking and guidance of missiles at armored targets. The airplane was based on the glider of a two-seat training aircraft Su-25UB, all the space allocated for the co-pilot was occupied by a new avionics. They also had to move the cannon into the rear compartment, widen and lengthen the bow, where the Shkval daytime optical sighting system was located to control the shooting of the Whirlwind supersonic missiles. Despite a significant increase in internal volume, there was no room for a thermal imaging system in the new car. Therefore, the Mercury night vision system was mounted in a suspended container under the fuselage at the sixth suspension point.
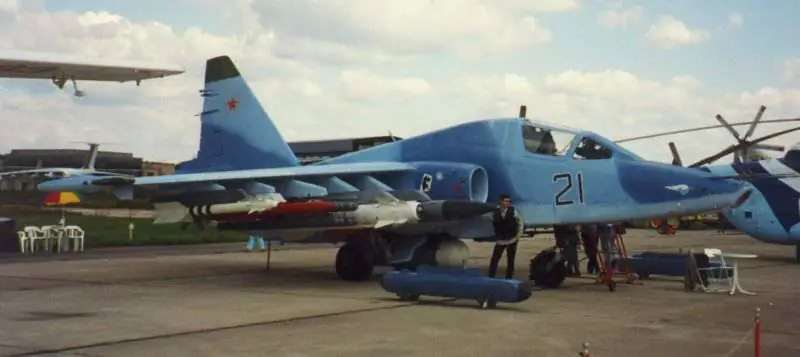
"9" The future of the Su-25
In terms of replacement, at the moment there are no worthy alternatives to the Su-25. The attack aircraft niche is so unique that it is difficult to create something more suitable for it than this attack aircraft. The Ministry of Defense said that, of course, the projects that are being prepared to replace the Su-25 exist, but their use is now premature. "The capabilities of assault aviation in Russia have not yet been exhausted," the Defense Ministry says. “At the moment, there is no need to immediately replace the Su-25 with another type of aircraft. The advantage will be achieved through deep modernization of the Su-25, both in terms of re-equipment of the aircraft itself and in terms of the weapons used in it. In particular, technologies that work on the “fire and forget” principle will be introduced.
Creating the Su-25, the designers saw in advance a huge potential for modernization. The aircraft, unique in its survivability, is today the main combat vehicle for direct support of troops.
The main attack aircraft of the Russian air force, the Su-25, will be modernized in the near future. It is planned to re-equip all existing aircraft of this type in accordance with the modification of the Su-25SM. In addition to revision, all attack aircraft will undergo major overhaul, which will extend their service life by 15-20 years.
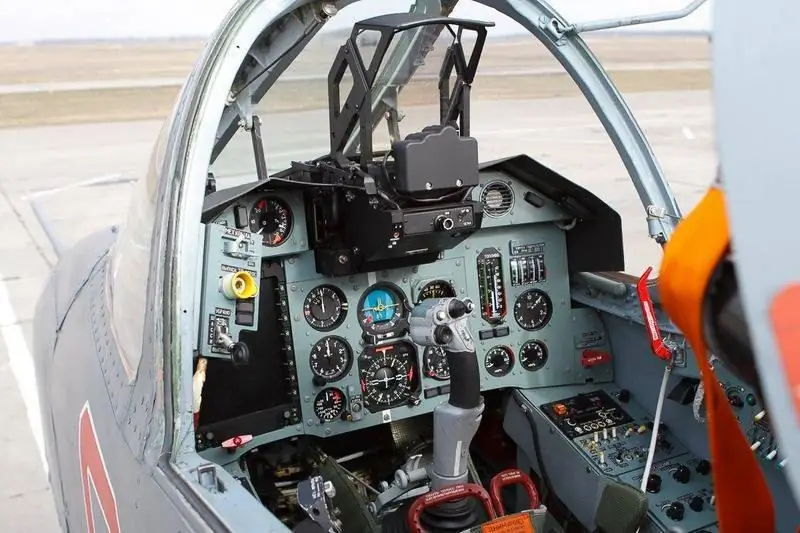
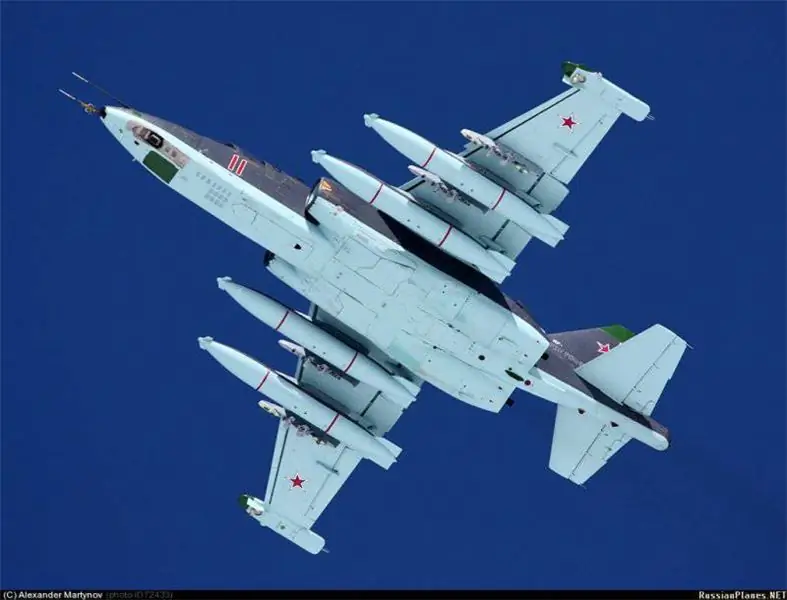
Primary sources: