On the labor front, a struggle unfolded to increase the production of tanks
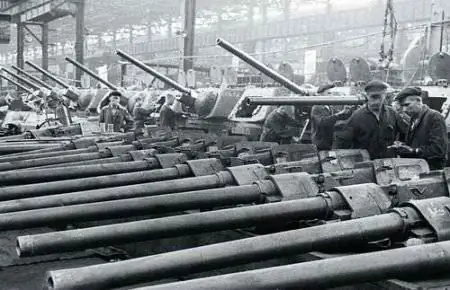
At the end of 1941 - the first half of 1942, the production of T-34 tanks was carried out at three factories: No. 183 in Nizhny Tagil, Stalingrad Tractor (STZ) and No. 112 "Krasnoe Sormovo" in Gorky. Plant No. 183 was considered the head plant, as was its design bureau, department 520. It was assumed that all changes made to the design of the thirty-four by other enterprises would be approved here. In fact, everything looked a little different. Only the performance characteristics of the tank remained unshakable, while the details of the vehicles of different manufacturers differed significantly from each other.
GENERAL CHARACTERISTICS
For example, on October 25, 1941, plant No. 112 began to manufacture prototypes of simplified armored hulls - without mechanical processing of the edges of the sheets after gas cutting, with joining parts in a "quarter" and spike joining the frontal sheet with the sides and fenders.
On the drawings of the head plant, which arrived at Krasnoye Sormovo, there was a hatch in the rear wall of the tower, closed by a removable armor plate with six bolts. The hatch was intended for dismantling a damaged gun in the field. The metallurgists of the plant, according to their technology, cast a solid wall of the tower, and a hole for the hatch was cut out on a milling machine. It soon became clear that when firing from a machine gun, vibration occurs in the removable sheet, leading to the detachment of the bolts and tearing it off.
Attempts to abandon the hatch were made several times, but each time representatives of the customer objected. Then the head of the armament sector A. S. Okunev proposed to raise the aft part of the tower with the help of two tank jacks. At the same time, the gun, removed from the trunnions, freely rolled out onto the roof of the MTO into the hole formed between its shoulder strap and the roof of the hull. During tests, a stop was welded to the leading edge of the hull roof, which protected the tower from slipping during lifting.
The production of such towers began at the plant number 112 on March 1, 1942. The military representative A. A. Afanasyev proposed to weld an armored visor instead of a thrust bar over the entire width of the hull roof, which would simultaneously serve as an emphasis and protect the gap between the end of the tower and the roof of the hull from bullets and shrapnel. Later, this visor and the absence of a hatch in the rear wall of the tower became the distinctive features of the Sormovo tanks.
Due to the loss of many subcontractors, tank builders had to show miracles of ingenuity. So, in connection with the termination of deliveries from Dnepropetrovsk of air cylinders for emergency engine start at Krasny Sormovo, artillery shells rejected by machining were used for their manufacture.
They got out as best they could at STZ: from August 1941, there were interruptions in the supply of rubber from Yaroslavl, therefore, from October 29, all thirty-fours at STZ began to be equipped with cast road wheels with internal depreciation. As a result, a characteristic external feature of the Stalingrad tanks was the absence of rubber tires on all road wheels. A new design of the track with a straightened treadmill was also developed, which made it possible to reduce the noise when the machine was moving. Eliminated "rubber" and on the driving and steering wheels.
Another characteristic feature of the STZ tanks was the hull and turret, which were manufactured according to a simplified technology developed by Plant No. 264 following the example of Krasny Sormov. The body armor parts were connected to each other in a "thorn". Variants in the "lock" and in the "quarter" were preserved only in the connection of the upper frontal sheet of the hull with the roof and the bottom with the lower sheets of the bow and stern. As a result of a significant reduction in the volume of machining of parts, the assembly cycle of housings has been reduced from nine days to two. As for the tower, they began to weld it from sheets of raw armor, followed by hardening already assembled. At the same time, the need for straightening the parts after hardening has completely disappeared and their adjustment during assembly "in place" has become easier.
The Stalingrad Tractor Plant produced and repaired tanks up to the moment when the front line approached the factory workshops. On October 5, 1942, in accordance with the order of the People's Commissariat of Heavy Industry (NKTP), all work at the STZ was stopped, and the remaining workers were evacuated.
The main manufacturer of thirty-fours in 1942 remained plant No. 183, although after the evacuation it did not manage to reach the required mode immediately. In particular, the plan for the first three months of 1942 was not fulfilled. The subsequent growth in the production of tanks was based, on the one hand, on a clear and rational organization of production, and on the other, on a decrease in the labor intensity of manufacturing the T-34. A detailed revision of the design of the machine was made, as a result of which the production of 770 was simplified and the production of 5641 parts was completely canceled. 206 purchased items were also canceled. The labor intensity of the housing machining has decreased from 260 to 80 standard hours.
The chassis has undergone significant changes. In Nizhny Tagil, they began to cast road wheels of the Stalingrad type - without rubber tires. Beginning in January 1942, three or four such rollers were installed on the tank for one side. The scarce rubber was removed from the guide and drive wheels. The latter, in addition, was made in one piece - without rollers.
The oil cooler was excluded from the engine lubrication system and the oil tank capacity was increased to 50 liters. In the power supply system, the gear pump was replaced by a rotary type pump. Due to the shortage of electrical components until the spring of 1942, most tanks did not have some instrumentation, headlights, a taillight, a fan electric motor, a signal and TPU.
It should be emphasized that in a number of cases, changes aimed at simplifying the design and reducing the complexity of manufacturing combat vehicles were not justified. Some of them subsequently turned into a decrease in the operational characteristics of the T-34.
SCIENCE AND INVENTION HELPED
The increase in the production of thirty-fours in 1942 was facilitated by the introduction, first at plant No. 183, and then at other enterprises, of automatic welding under a layer of flux, developed by Academician EO Paton. The 183rd plant turned out to be the leader in this business not by chance - by the decision of the Council of People's Commissars of the USSR, the Institute of Electric Welding of the Academy of Sciences of the Ukrainian SSR was evacuated to Nizhny Tagil, and to the territory of the Ural Tank Plant.
In January 1942, as an experiment, a hull was made, in which one side was welded by hand, and the other side and nose were under a layer of flux. After that, to determine the strength of the seams, the hull was sent to the landfill. As EO Paton said in his memoirs, “the tank was subjected to brutal shelling from a very short distance with armor-piercing and high-explosive shells. The very first hits on the side, welded by hand, caused a solid destruction of the seam. After that, the tank was turned and the second side, welded with a machine gun, came under fire … Seven hits in a row! Our seams withstood, did not give in! They turned out to be stronger than the armor itself. The seams of the bow also withstood the fire test. It was a complete victory for automatic high-speed welding."
At the factory, the welding was put on the conveyor. Several carriages left over from pre-war production were rolled into the workshop, bevels were cut out in their frames according to the configuration of the sides of the tank hull. Above the line of carts, a tent made of beams was placed so that the welding heads could move along the beams along and across the body, and by connecting all the carts together, we got a conveyor. In the first position, transverse seams were welded, on the next - longitudinal, then the body was rearranged on the edge, first with one side, then with the other. The welding was completed by turning the body upside down. Some places where the machine could not be used were brewed by hand. Thanks to the use of automatic welding, the labor intensity of manufacturing the body has decreased five times. By the end of 1942, there were six automatic welding machines in plant No. 183 alone. By the end of 1943, their number in tank factories reached 15, and a year later - 30.
Along with the problems of welding, the bottleneck was the production of cast towers, which were molded into the ground. This technology required more work to trim and gas trim the sprues and fill seams between mold blocks. The chief metallurgist of the plant, P. P. Malyarov, and the head of the steel shop, I. I. Atopov, proposed the introduction of machine molding. But this required a completely new tower design. Its project in the spring of 1942 was developed by M. A. Nabutovsky. It went down in history as a tower of the so-called hexagonal or improved form. Both names are rather arbitrary, since the previous tower also had a hexagonal shape, perhaps more elongated and plastic. As for the "improvement", this definition entirely refers to the manufacturing technology, since the new tower was still very cramped and inconvenient for the crew. For its shape close to the correct hexagon, the tankers received the nickname "nut".
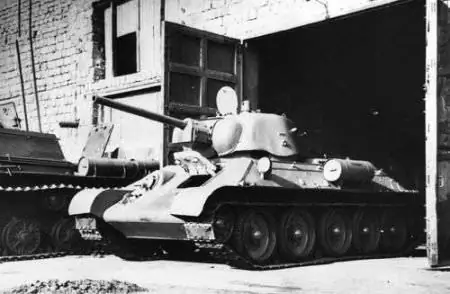
MORE MANUFACTURERS, WORER QUALITY
In accordance with the order of the State Defense Committee dated October 31, 1941, Uralmashzavod (Ural Heavy Engineering Plant, UZTM) was connected to the armored hull production for the T-34 and KV. However, until March 1942, he only issued the cutting of hulls, which he supplied to Krasnoe Sormovo and Nizhny Tagil. In April 1942, the full assembly of hulls and the manufacture of thirty-four turrets for plant number 183 began here. On July 28, 1942, UZTM was instructed to organize the production of the entire T-34 tank and double the production of turrets for it due to the shutdown of plant number 264.
Serial production of the T-34 began at Uralmash in September 1942. At the same time, many problems arose, for example with the towers - due to the increase in the program, the foundries could not ensure the fulfillment of the plan. By the decision of the plant director B. G. Muzurukov, the free capacities of the 10,000-ton Shleman press were used. The designer I. F. Vakhrushev and the technologist V. S. At the same time, UZTM not only fully ensured its program, but also supplied a significant number of such towers to the Chelyabinsk Kirovsky Plant (ChKZ).
However, Uralmash did not produce tanks for long - until August 1943. Then this enterprise became the main manufacturer of ACS based on the T-34.
In an effort to compensate for the inevitable loss of the Stalingrad tractor, in July 1942, the State Defense Committee gave the task to begin production of thirty-fours at ChKZ. The first tanks left his workshops on August 22. In March 1944, their production at this enterprise was stopped in order to increase the production of heavy tanks IS-2.
In 1942, the plant No. 174 named after K. Ye. Voroshilov, evacuated from Leningrad to Omsk, also joined the production of the T-34. The design and technological documentation was handed over to him by the plant No. 183 and UZTM.
Speaking about the production of T-34 tanks in 1942-1943, it should be noted that by the fall of 1942, there was a crisis in their quality. This was led by the constant quantitative growth of the manufacture of thirty-fours and the attraction of more and more new enterprises to it. The problem was considered at the conference of the NKTP plants, held on September 11-13, 1942 in Nizhny Tagil. It was led by the deputy commissar of the tank industry Zh. Ya. Kotin. In the speeches of him and the chief inspector of the NKTP G. O. Gutman received harsh criticism of the factory collectives.
The separation had an effect: during the second half of 1942 - the first half of 1943, many changes and improvements were introduced to the T-34. In the autumn of 1942, external fuel tanks began to be installed on the tanks - aft rectangular or side cylindrical (on ChKZ machines) in shape. At the end of November, the drive wheel with rollers was returned to the thirty-four, stamped road wheels with rubber tires were introduced. Since January 1943, tanks have been equipped with Cyclone air cleaners, and since March-June, with five-speed gearboxes. In addition, the ammunition load was increased to 100 artillery rounds, and an exhaust tower fan was introduced. In 1943, the PT-4-7 periscope sight was replaced by the PTK-5 commander's panorama, many other, smaller improvements were introduced, such as the landing handrails on the tower.
Serial production of T-34 tanks of the 1942 model (so unofficially, but they are most often referred to in the literature) was carried out at factories No. 183 in Nizhny Tagil, No. 174 in Omsk, UZTM in Sverdlovsk and ChKZ in Chelyabinsk. Until July 1943, 11,461 tanks of this modification were produced.
In the summer of 1943, the commander's cupola began to be installed on the T-34. An interesting detail: the priority in this matter is defended in their reports on tank building during the Great Patriotic War by three plants - No. 183, Uralmash and Krasnoye Sormovo. In fact, the Tagil residents proposed to place the turret in the rear of the turret behind the hatches and put a third tanker in the turret, as on an experienced T-43 tank. But even two crew members were cramped in the "nut", what a third there! The Uralmash turret, although it was located above the left commander's turret hatch, was of a stamped design, and it was also rejected. And only the cast Sormovskaya "registered" on the thirty-four.
In this form, the T-34s were mass-produced until mid-1944, with the last to complete their production at plant # 174 in Omsk.
MEETING WITH "TIGERS"
It was these machines that bore the brunt of the fierce tank confrontation on the Kursk Bulge (in parts of the Voronezh and Central Fronts, thirty-fours accounted for 62%), including the famous Prokhorov battle. The latter, contrary to the prevailing stereotype, took place not on some separate field, like Borodinsky, but unfolded on a front up to 35 km long and was a series of separate tank battles.
On the evening of July 10, 1943, the command of the Voronezh Front received an order from the Supreme Command Headquarters to deliver a counterattack against a group of German troops advancing in the Prokhorovka direction. For this purpose, the 5th Guards Army of Lieutenant General A. S. Zhadov and the 5th Guards Tank Army of Lieutenant General of Tank Forces P. A. Rotmistrov (the first tank army of uniform composition) were transferred from the reserve Steppe Front to the Voronezh Front. Its formation began on February 10, 1943. By the beginning of the Battle of Kursk, it was stationed in the Ostrogozhsk region (Voronezh region) and included the 18th and 29th tank corps, as well as the 5th Guards Mechanized Corps.
On July 6, at 23.00, an order was received demanding the concentration of the army on the right bank of the Oskol River. Already at 23.15 the advance detachment of the unification set off from the place, and after 45 minutes the main forces moved behind it. It is necessary to note the impeccable organization of the redeployment. Oncoming traffic was prohibited along the routes of the convoys. The army marched around the clock, with short halts for refueling cars. The march was reliably covered by anti-aircraft artillery and aviation and, thanks to this, remained unnoticed by enemy reconnaissance. In three days, the association moved 330-380 km. At the same time, there were almost no cases of failure of combat vehicles for technical reasons, which indicates both the increased reliability of tanks and their competent maintenance.
On July 9, the 5th Guards Tank Army concentrated in the Prokhorovka area. It was assumed that the combination with two tank corps attached to it - the 2nd and 2nd Guards corps at 10:00 on July 12, would attack the German troops and, together with the 5th and 6th Guards combined-arms armies, as well as the 1st Tank Army, would destroy the wedge-in Oboyan direction of the enemy grouping, preventing its retreat to the south. However, the preparation for the counterstrike, which began on July 11, was thwarted by the Germans, who delivered two powerful blows on our defenses: one in the direction of Oboyan, the other on Prokhorovka. As a result of the partial withdrawal of our troops, the artillery, which played a significant role in the counterstrike, suffered losses both at the deployment positions and in the movement towards the front line.
On July 12, at 8.30 am, the main forces of the German troops, consisting of the motorized SS divisions "Leibstandarte Adolf Hitler", "Reich" and "Death's Head", numbering up to 500 tanks and assault guns, went on the offensive in the direction of Prokhorovka station. At the same time, after a 15-minute artillery barrage, the German group was attacked by the main forces of the 5th Guards Tank Army, which led to the deployment of an oncoming tank battle, in which about 1200 armored vehicles took part from both sides. Despite the fact that the 5th Guards Tank Army, operating in the 17-19 km strip, was able to achieve a density of battle formations of up to 45 tanks per 1 km, it could not complete the assigned task. The losses of the army amounted to 328 tanks and self-propelled guns, and together with the attached formations, they reached 60% of the original strength.
So the new German heavy tanks were a tough nut to crack for the T-34. “We were afraid of these" Tigers "on the Kursk Bulge, - recalled the former commander of the thirty-four E. Noskov, - I honestly confess. From his 88-mm cannon, he, "Tiger", with a blank, that is, an armor-piercing projectile from a distance of two thousand meters, pierced our thirty-four through and through. And we from the 76-mm cannon could hit this thick-armored beast only from a distance of five hundred meters and closer with a new sub-caliber projectile …"
Another testimony of a participant in the Battle of Kursk - the commander of a tank company of the 10th Tank Corps PI Gromtsev: “First they fired at the Tigers from 700 meters away. is shooting at our tanks. Only strong July heat favored - "Tigers" here and there caught fire. It turned out later that gasoline vapors that accumulated in the engine compartment of the tank often flared up. Directly it was possible to knock out "Tiger" or "Panther" only from 300 meters and then only to the side. Many of our tanks then burned down, but our brigade still pushed the Germans two kilometers away. But we were at the limit, we could not endure such a fight anymore."
The same opinion about the "Tigers" was shared by the veteran of the 63rd Guards Tank Brigade of the Ural Volunteer Tank Corps N. Ya. Zheleznov:, they stood in an open place. And try to come? He will burn you 1200-1500 meters away! They were arrogant. In essence, while the 85-mm cannon was out, we, like hares, ran from the Tigers and looked for an opportunity, as it were, to wriggle out and slam him into the side. It was hard. If you see that a "Tiger" is standing at a distance of 800-1000 meters and starts "baptizing" you, then while driving the barrel horizontally, you can still sit in the tank. As soon as you start driving vertically, you better jump out. You will burn! This was not the case with me, but the guys jumped out. Well, when the T-34-85 appeared, it was already possible to go one-on-one here …"