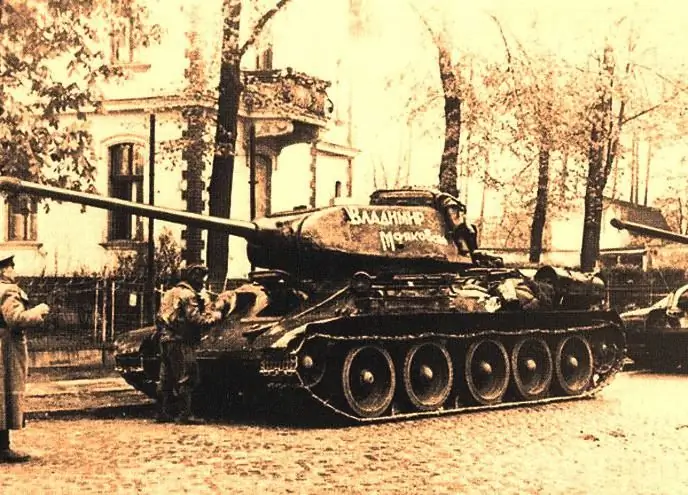
The repair of tanks during the Great Patriotic War was of great importance. Suffice it to say that during the war years, 430,000 repairs of tanks and self-propelled artillery units (ACS) were carried out. On average, every industrial tank and SPG went through the hands of repairmen more than four times! In tank armies, for example, each tank (self-propelled guns) failed two or three times and the same number of times, through the efforts of repairmen, returned to combat formation.
The main role in the repair of tanks was played by military mobile repair equipment. Their share in the total volume of armored vehicles repair was 82.6%. The restored tanks and self-propelled guns were the main source of replacement for the losses of tank units. The repairmen managed to achieve such high results thanks to the widespread introduction into practice of the aggregate method of repairing combat vehicles in the field.
In the pre-war years, the Soviet government launched a lot of work to strengthen the army, including the further development of armored forces, the creation and production of new tank designs, the improvement of the engineering and tank service, and the training of command and engineering personnel. However, by the time the war began, this huge work had not been completed.
The theoretical foundations of the organization and technology of repairing tanks in the field before the Great Patriotic War were insufficiently developed, repair facilities, especially mobile ones, were poorly developed, there was an acute shortage in the circulating fund of motors and aggregates and spare parts for their repair. The repair facilities were not yet ready for the repair of the T-34 and KV tanks that were new at that time. Evacuation facilities were very poorly developed. All this negatively affected the combat effectiveness of the armored forces. On June 15, 1941, 29% of old-type tanks (BT and T-26) needed, for example, major repairs and 44% on average. With the beginning of hostilities, the military repair units could not cope even with the current repair of tanks.
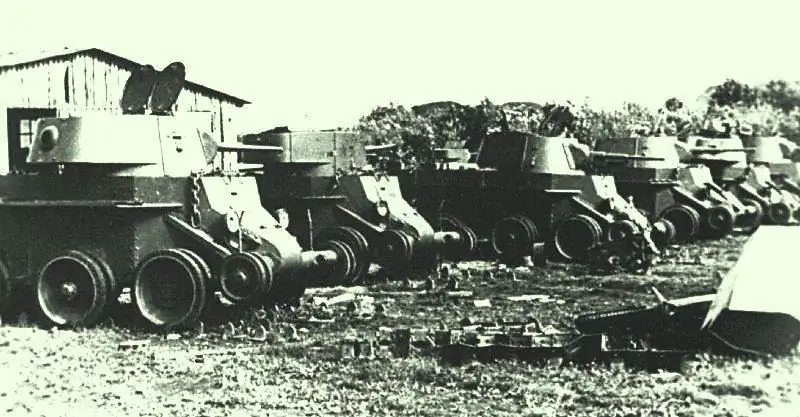
As a result of the adoption of urgent measures in the second half of 1941, 48 mobile repair bases (PRB) were formed for the average repair of equipment on the battlefield. By January 1, 1943, 108 regiment battalions, 23 separate repair and restoration battalions (orvb) and 19 army repair and restoration battalions (arvb) were already operating in the troops. To evacuate damaged armored vehicles from the battlefield, 56 evacorot were formed. The formation of repair funds continued further. The number of tanks being repaired increased steadily.
However, the increase in repair parts such as PRB and RVB did not solve the main problem - their technical equipment was such that they could not carry out overhaul of tank units, and were not intended for this purpose.
Due to an acute shortage of spare tank units, especially engines, the repairmen, despite enormous efforts, could not cope with the repair of tanks on the battlefield. Industrial plants and stationary repair plants located deep in the rear could only provide units for their own production of tanks and their repair. Very few turnaround units were produced. In addition, the delivery of units from the deep rear was accompanied by great difficulties or was completely excluded due to the overload of transport. In offensive operations, damaged and worn-out tanks, due to the lack of spare units, stood idle on the battlefield for a long time. When sending them for repairs deep in the rear, many complications arose with evacuation and transportation. As a result, many months passed before the tanks were returned to service.
In 1943, the problem of repairing tanks became particularly acute. This was due to the formation of tank armies and the beginning of major offensive operations of the Soviet troops. The military repair facilities that existed at that time, despite their significant number, could not cope with the tasks in offensive operations, did not provide the necessary survivability of tank forces in difficult weather conditions. This is eloquently indicated by the following facts: the 2nd Tank Army of the Central Front, marching from the Efremov area to the Fatezh area (200 km) on February 12-19, 1943, in conditions of heavy snow drifts and off-road conditions, left 226 tanks on the routes for technical reasons out of 408; in four tank corps of the Southwestern Front, by the beginning of the counteroffensive of the Nazi armies "South" (February 19, 1943), only 20 tanks remained in service, and all non-motorized tanks were buried and turned into fixed firing points.
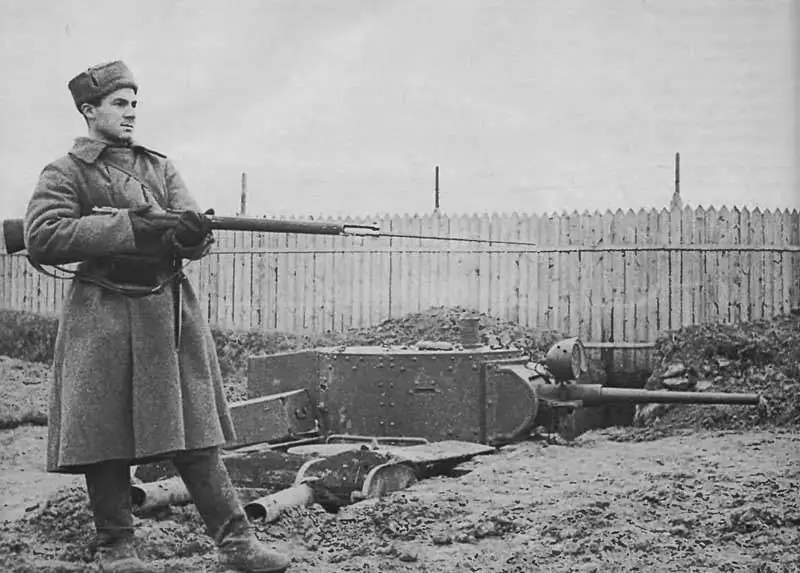
Many tanks that were out of order in battles could not be restored due to the lack of a circulating fund of tank units, primarily engines. The situation was such that each engine for the front was equivalent to a tank. Among the few repair units of the Soviet Army, the 1st stationary armored repair shop (sbtrm) of the North-Western Front mastered by the beginning of 1943 the overhaul of tank diesel engines in Vyshny Volochyok. The repairmen used the best industry experience, as well as all the best that was in the repair technology at the Moscow Central Military Repair Plant. The repair of tank diesel engines in 1 SRM was established at one time on the instructions of the commander of the armored and mechanized troops of the front, General B. G. Vershinin.
At the end of February 1943, the chief of the 1st brigade, engineer-major P. P. Ponomarev, being in Moscow, met in the reception room of the Main Armored Directorate (GBTU) with the commander of the 4th Guards Kantemirovsky Tank Corps, General P. P. Poluboyarov. The general spoke about the difficult situation with the repair of equipment in the troops, and spoke in favor of a radical improvement in the organization of the repair of tanks on the battlefield. The same question has long worried the repairmen.
Several days later P. P. Ponomarev submitted a memorandum to the head of the GBTU, General B. G. Vershinin, with a proposal to form qualitatively new repair units - mobile tank-aggregate repair plants (PTARZ). The general approved this idea. Soon, a small team was created in the 1st brigade to develop an organizational and technological project for such a plant, consisting of P. Ponomarev, S. Lipatov, V. Kolomiets and D. Zverko. Later, literally the entire team of the workshop joined the work.
The main idea was that a mobile plant could freely do without stationary production facilities and power plants. The PTARZ was supposed to act in any conditions, moving after the troops. When organizing mobile factories in difficult times of war, it was necessary to solve many complex engineering and technical problems.
The authorship of this group of officers of the 1st brigade for the development of ATARZs was legalized by order of the commander of the artillery of the Red Army No. 47 of July 20, 1944. So, for example, in order to create a coherent system of overhaul of tank units in the field while maintaining a constant technological process, as was practiced in industrial plants, where all operations were strictly regulated, new light, warm, disassembled production facilities with lifting equipment for a qualified production line were needed. repair of tank engines and transmission units. It was necessary to place on the chassis of highly passable cars and trailers a large number of various workshops, with machine tools and other equipment, test stations, laboratories, power plants, provide for the manufacture of quickly assembled and easily transported communications (water supply, steam pipe, electrical cables).
The creation of ATARZs was then a new thing, and not all specialists immediately supported it, fearing that it would not be possible to provide high quality overhaul of such complex equipment as tank diesel engines of the B-2 type at mobile plants. In addition, some were tied up by the draft decision being prepared at that time on the centralized repair of tank diesel engines at the Central Military Engine Repair Plant in Moscow. It proposed to radically reconstruct this enterprise in order to dramatically increase its capacity.
For the final solution of the issue, the head of the GBTU ordered Major Engineer P. P. Ponomarev to urgently make the basis of the PTARZ by the workshop - a sample of the production room for dismantling and assembly works (a tent tent with lifting vehicles). After numerous creative searches and elaboration of all possible options, a circular tent room with an area of 260 square meters was chosen. m with a wooden floor, double canvas walls, heating heaters and a set of lifting and transport facilities. The set of equipment and the tent weighed only 7 tons and were transported by car with a trailer.
Inspection of the production facility with a set of equipment for the assembly of tank diesel engines, diagrams of all fundamental decisions on the technology and power supply of the PTARZ took place in early April 1943, at the Central Military Engine Repair Plant in Moscow. Most of the dignitaries present approved the proposed principled decision, those who opposed the PTARZ received comprehensive explanations. On April 19, 1943, a GKO decree was adopted on the formation of two PTARZs - Nos. 7 and 8.
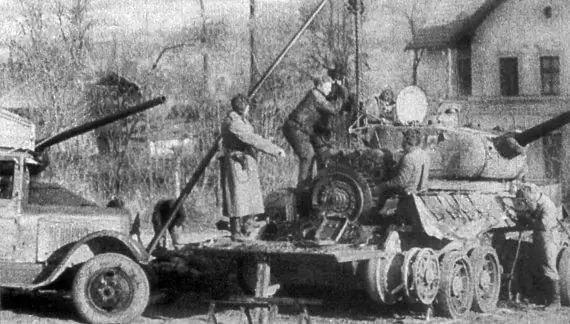
The first ever mobile tank-aggregate repair plant - PTARZ No. 7 (chief engineer-major P. P. Ponomarev) was designed, built and formed in 3, 5 months, which was a real labor feat of the personnel of the 1st brigade, which in the era effective managers”can hardly be repeated.
By order of the People's Commissar of Defense dated August 28, 1943, PTARZ No. 7 was placed at the disposal of the Supreme Command Headquarters in early September to support the combat operations of the Steppe and Voronezh fronts. Attaching great importance to the safety of the first mobile plant, the supreme commander-in-chief I. V. Stalin personally instructed the echelons with PTARZ No. 7 to accompany them along the entire route under the cover of fighter aircraft. In a short time was created and sent to the southern front ATARZ No. 8 (chief engineer-major V. G. Iovenko, later - engineer-colonel N. I. Vasiliev). Great assistance in the design of the first ATARZ was provided by the brigade of the Central Military Project headed by the architect K. A. Fomin, and in the formation of factories - generals and officers of the Central Directorates and factories of industry.
The actions of the first two mobile tank-aggregate repair plants on the fronts were very successful. In a short time, they provided the tank forces of the Steppe, Voronezh and Southern fronts with overhauled engines, units and instruments, and also helped the units quickly master the repair of tanks using the aggregate method. The State Defense Committee immediately appreciated the advantages of the ATARZ. And already on September 13, 1943, a new GKO decision was made, on the formation of five factories, and in 1944 two more. As a result of these measures in 1944, 9 fronts - 1st, 2nd and 3rd Ukrainian, all Belorussian and Baltic ones - had their own ATARZs. Based on the experience of the PTARZs, in 1943-1944, five mobile tank repair plants (PTRZ) were formed, which carried out overhaul of tanks at the fronts. PTRZ used diesel engines repaired by PTRZs. This gave the overall harmony of the overhaul aggregate system.
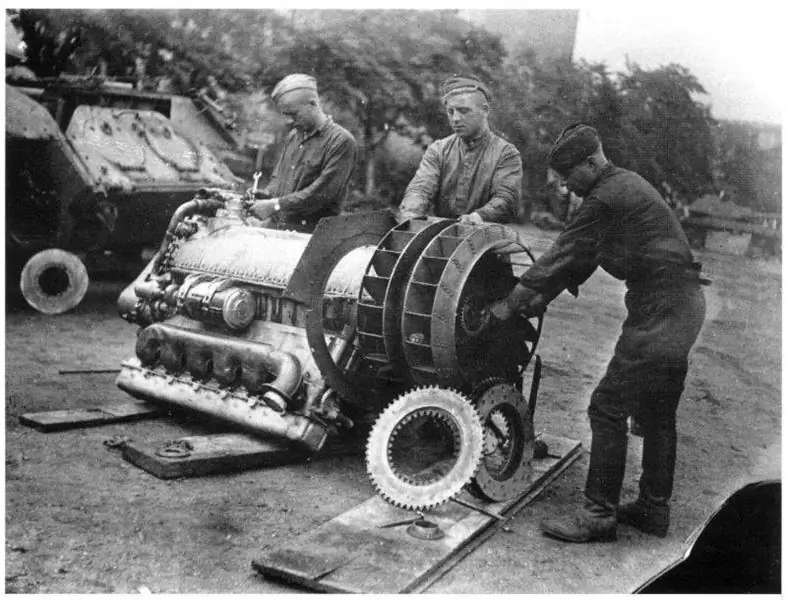
The basis of PTARZ was made up of four production departments. The first was intended for the repair of tank engines, the second - for the repair of transmission units, electrical equipment, various components and devices, the third - for the manufacture and restoration of worn parts. The fourth department was a branch of the plant, based on industrial enterprises in the liberated cities and periodically relocated behind the PTARZ by rail. He restored the most complex parts, made castings and complex forgings. By the end of 1944, at PTARZ No. 7, a powerful repair train was built for the fourth department, in which 50 specially converted 4-axle cars were used only to accommodate production workshops, laboratories and power plants. In addition to production departments, the PTARZ staff had support departments - production planning, technical control, technical control, chief mechanic, material and technical support, as well as other divisions and services.
At PTARZ, in addition to the 4th department, there were another 600-700 units of machine tools and other equipment placed in special tents and various workshops, in bodies on cars and caravans. Their total production area was equal to 3000-3500 sq. m. The capacity of mobile power plants was 350-450 kW.
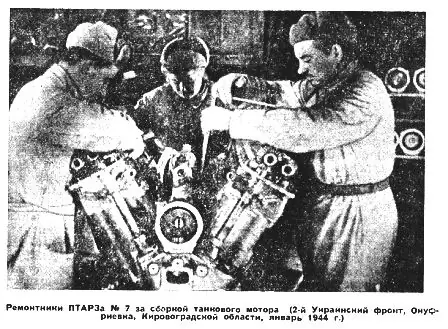
The number of ATARZ personnel according to the initial staff was 656 people (officers - 76, soldiers and sergeants - 399, civilian workers - 181). The organizational structure of the factories has been continuously improved. By the end of the war, their personnel increased to 1920 people (officers - up to 120, soldiers and sergeants - up to 1300, civilians - up to 500 people).
The technological process of repairing tank units at PTARZs was in-line and organized using the experience of tank industry factories and stationary military repair plants. In essence, the PTARZs were full-blooded industrial enterprises, but only on wheels.
Their interaction with military repair facilities, which carried out routine and medium repairs of tanks, was carried out as follows. Damaged and worn-out tanks were concentrated at the collection points for emergency vehicles (SPAMs), where repair and recovery battalions and mobile tank repair bases were deployed. The repair fund of tank engines, transmission units, components and instruments was depersonalized and sent to ATARZs for overhaul, and instead of them, the factories gave out overhauled ones in exchange. Thanks to this, the RVB and ATRB were able to repair tanks using the aggregate method. The transfer of units over a short distance within the military and frontal rear was carried out both by the transport of military repair units and the ATARZ themselves.
PTARZs not only provided the repair of tanks with the aggregate method, but also contributed to the radical technical re-equipment of all military repair equipment - ATRB, RVB and even mobile tank repair plants, being the basic organization for them. They essentially took the lead in the field tank repair industry. Skillfully maneuvering and echeloning technical means, the ATARZs, even during redeployments, did not interrupt their production activities. When necessary, they sent operational production groups as close to the front line as possible. The high mobility of the ATARZs and their ability to follow directly the troops are clearly evidenced by the drop on the Dnieper bridgehead (in the Onufriyevka area in the fall of 1943) of the forward unit of the ATARZ No. 7.
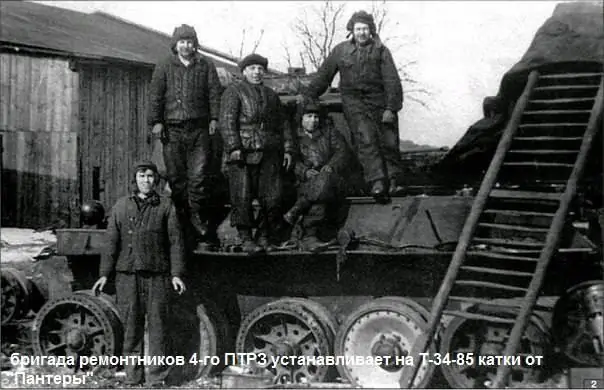
On the liberated territory, the PTARZs assisted Soviet and economic organizations in organizing the work of factories, in organizing the production of products for the front and the national economy.
Together with the troops of the Steppe and the 2nd Ukrainian fronts, PTARZ No. 7 passed about 5000 km along the roads of the war. During the war years, he repaired 3,000 tank engines, more than 7,000 tank transmission units, a significant number of various components and devices, about 1,000 units for armored cars and tractors, restored and manufactured new parts for 3.5 million rubles.
For selfless work PTARZ No. 7 in 1944 was awarded the Order of the Red Star. 70% of the personnel of the plant were awarded orders and medals. By order of the Supreme High Command, the work of PTARZ No. 7 at the front was captured in the full-length sound film "Factory at the Front".
Other ATARZs also operated successfully.
The actions of ATARZs are characterized by great mobility and mobility. They did not break away from the advanced formations by more than 100-150 km, and in many cases worked 10-12 km away from them. They could quickly (in 18-20 hours) fold up and just as quickly (in 24-28 hours) turn around and start working in a new place.
The experience of the war has shown that technical support, and above all the organization of the repair of military equipment during operations, is one of the main factors in the high combat readiness of tank forces. With the formation of mobile factories, the foundation was laid for the creation of a scientific system for the repair of tanks. The restoration of combat vehicles was of a complex nature, covering all types of tank repairs. A sharp reduction in the repair time was achieved due to the maximum approach of military repair units to the areas of hostilities, good technical equipment and sufficient capacity of their repair facilities.
The tank repair system adopted in our army during the Second World War had a decisive advantage over the German one, and mainly because with the help of ATARZs, the aggregate method of repairing combat vehicles directly on the battlefield was widely introduced. There were no mobile repair factories in the German army. Until the end of the war, the German command did not understand why, despite the loss of equipment, the Russian tank and mechanized formations soon re-entered the battle.