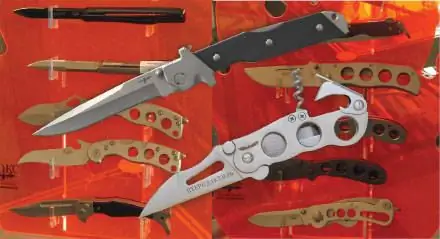
The blade is the main part of the knife. It is on him that the cutting and piercing properties of the knife depend. The main factors that determine the operational characteristics of the blade are the material and technology of its manufacture, as well as its shape and cross-section.
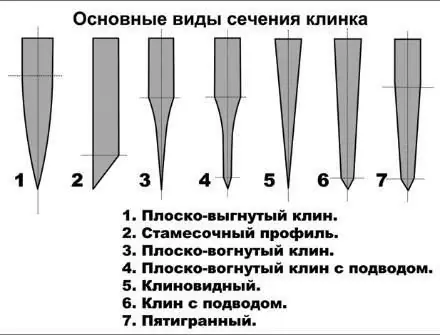
The blades of modern folding knives are made from corrosion-resistant types of steel. On blades of well-known manufacturers, the steel grade is often stamped on the blade at the base of the handle. On cheap knives, you can often see the inscription on the blade - "stainless" or "rostfrei", which simply means "stainless steel".
Currently, several dozen different grades of steel are used in the knife industry. Since different countries have different standards for the designation of steel grades, the same steel may have different designations. The most common steel grades used for making folding knife blades are shown in the table.
For an inexperienced user, it is enough to take into account the fact that the more expensive the steel, the longer it keeps sharpening, but this increases the fragility of the cutting edge and makes it difficult to edit the knife at home.
The quality of the blade is largely influenced by the technology of thermal hardening of steel used by the manufacturer. With proper heat treatment, even relatively cheap types of steel provide good cutting qualities of the knife, and vice versa, even expensive types of steel with flaws in heat treatment will not provide a good quality of the blade. This is the reason for the high cost of folding knives from well-known manufacturers who have modern equipment and carefully monitor the quality of the blade.
The hardness of the cutting edge is expressed in Rockwell units. Typically, folding knife blades are hardened to 42-60 HRC. The larger this number, the longer the knife keeps sharpening, but you have to pay for this with less resistance to shock loads and the complexity of sharpening the knife. Conversely, at low HRC values, the cutting edge is more plastic, easy to sharpen, but poorly holding the sharpening. With an increase in hardness above 61 HRC, the blade of knives with a normal butt thickness becomes very fragile. Blade of blades hardened to 42 units. or less, has low strength and is difficult to cut common materials. This figure is not shown on the packaging of knives. Even when describing a model on the manufacturer's website, it is not always possible to see it.
When using the knife, it is necessary to take into account the fact that the knife blade is very sensitive to temperature rise. That is why you should not stir up the coals of a fire with a knife or use an electric grinder for a locksmith or carpentry tool to sharpen it.
The surface of the blade can be polished, matt, blued, chrome-plated or have a special protective coating.
Polishing increases the blade's resistance to corrosion, but such a surface shines in the sun, which is not entirely acceptable in tactical knives.
Matting increases the anti-reflective properties, but worsens the corrosion resistance of the knife.
When bluing the blade, a thin layer of a protective oxide film is created on its surface, while the blade acquires a dark color.
When chrome plating, a thin layer of chrome is applied to the surface of the blade, which prevents corrosion of the blade, but not its cutting edge.
In modern knives, the blade coating made of synthetic materials (epoxy resins, Teflon), which provide high resistance to moisture or acidic and alkaline environments, is becoming more common. Because this coating prevents the blade from glaring in the sun, it is often referred to as "anti-glare" and is often used for tactical knives. The disadvantage of such coatings is low wear resistance and sensitivity to scratches.
Recently, with the reduction in the cost of industrial production of Damascus steel, more and more blades are made from it. Damascus steel is produced by forging several layers of steel with different carbon content. As a result, a beautiful pattern appears on the surface of the blade. Modern industrial production of Damascus steels makes it possible to design the shape of this pattern in advance ("mosaic damascus").
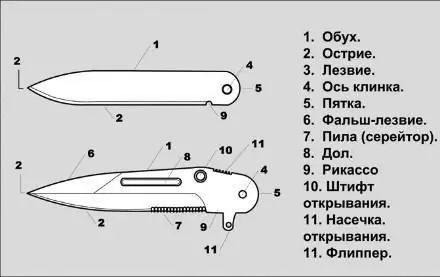
The combination of low-carbon steel strips for ductility and high-carbon strips for cutting edge hardness results in blades with excellent performance. In addition, the cutting edge of Damascus steel knives has micro-teeth, which increase the cutting ability of the knife.
Damascus steel blades look very impressive. However, it should be borne in mind that the risk of getting a defective blade made of Damascus steel is much higher than when purchasing a knife with a conventional steel blade. This is due to the rather complex technology for the manufacture of such steel.
Dales, which are often called blood channels, are longitudinal notches along the axis of the blade and serve to lighten the weight of the blade. At the same time, they increase the stiffness of the blade in the transverse direction. Sometimes they are through cutouts.
Ricasso - the unsharpened part of the blade at the handle serves for the convenience of sharpening the knife.
False blade came from combat knives with a fixed blade, which has one and a half sharpening.
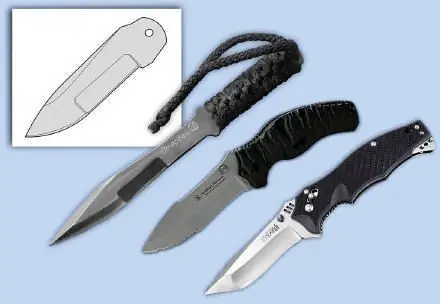
A wide variety of blade shapes are used in folding knives.
For ordinary household operations, knives with a straight blade or a blade converging to a point are preferred.
The disadvantage of the classic shape of the blade is its lower strength at the point, since the thickness of the blade gradually decreases towards the point. Blades in the form of "tanto" or "modified tanto" are free from this drawback. At the beginning of this century, first on knives with a fixed blade, and then on folding knives, a special shape of a blade with a reinforced edge began to be used.
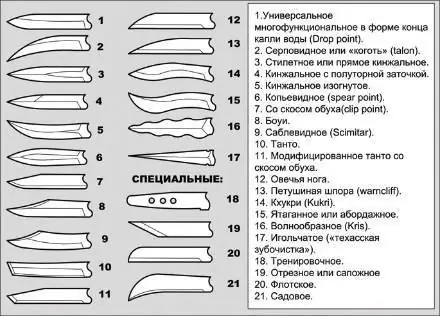
If increased cutting properties are required from the knife (self-defense knives), blades with a convex or wavy blade are used. At the end of the last - beginning of this century, knives with a sickle blade, which is characteristic of Malaysian karambit knives, came into fashion. Such a blade does not cut, but rips open the surface of the target like a plow. Knives with such a blade are used for self-defense or for cutting car seat belts.
The same purposes are served by knives in which the blade is located at an angle to the handle. This idea got its maximum development in the STI pistol grip knives.
Flat wedge has high performance, combining the strength of the blade and a sharp blade. Due to the uniform distribution of force, it cuts well soft materials of large thickness. Disadvantages - the complexity of sharpening, does not cope well with cutting hard materials.
Chisel profile - differs in manufacturability and ease of sharpening. It is widespread on the blades of Asian knives. It has excellent chopping properties, it cuts well non-thick materials.
Flat cone wedge and its variety is a flat-concave wedge with a supply - it is distinguished by its simplicity of manufacture, it is easy to correct and sharpen, it perfectly performs a shallow cut. Disadvantages - low mechanical strength, difficulty in cutting thick materials due to protruding side ribs.
Wedge profile has excellent cutting properties. The disadvantage is the fragility of the cutting edge and the difficulty of sharpening (it is necessary to sharpen the entire plane of the blade). From this disadvantage, a wedge-shaped section with a supply is free.
Pentahedral profile combines manufacturability, strength, good cutting qualities, good correction. Disadvantages - Difficulty sharpening when restoring the cutting edge.
In addition to the blade, folding pocket knives can have additional auxiliary tools - an awl, a corkscrew, a can opener, a bottle opener. In the so-called "Swiss Army knives", the number of such tools can reach several dozen. Such multifunctional knives are called "multitool".

For self-defense, knives with two working blades are also produced, which allow you to hit the target with the forward and reverse movement of the hand without changing the orientation of the knife or changing its grip.
Saw (sereytor)
Part of the blade of the blade can be sharpened in the form of a saw for cutting fibrous materials. In the knife literature, such a sharpening is called "serrated" or "serrated" (from the English serrated - sawtooth). In self-defense knives, serrated sharpening facilitates cutting through thick outerwear and can be performed along the entire length of the blade.
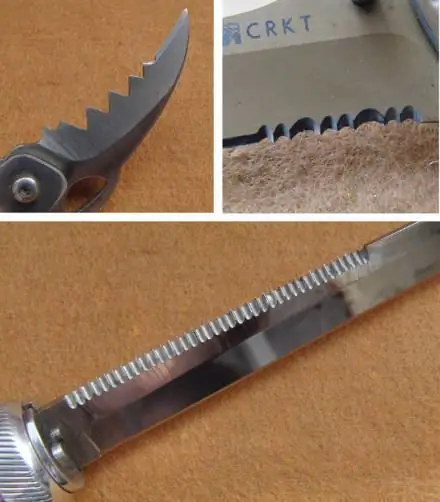
The tooth configuration of this mini saw may vary from manufacturer to manufacturer. The presence of a seritor makes it difficult to sharpen the blade at home - for this you need to have a special tool and skills to work with it, or contact the appropriate specialist.
Structural elements for opening the knife
Most modern folding knives are designed to be opened with one hand, either right or left. For this, at the base of the blade there are special elements - cylindrical pins, round or square dies or holes in the blade (the round hole is protected by a patent owned by the American company Spiderco, and other manufacturing companies are forced to use other forms). It is more convenient to open knives with protruding elements - pins or dies, but they reduce the effective length of the blade.
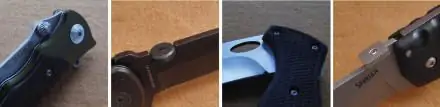
At the beginning of this century, a special device appeared on knives in the form of a hook on the butt, which provides automatic opening of the knife when it is pulled out of a trouser pocket. Owners of such knives should be aware that if the trousers are made of thin material, then after several cycles of pulling out the knife, they will most likely burst.
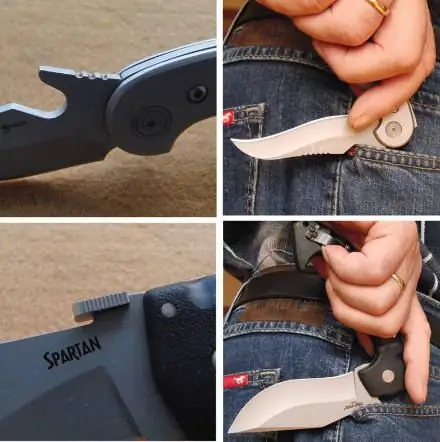
Much less common on modern knives is a special semicircular cutout on the blade. It is most often used in models with several working blades or tools, or in knives without blade fixation, which are well known to the older generation from Soviet times.
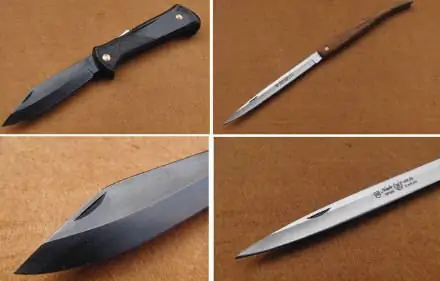
Another element that facilitates the opening of the knife is a flipper (from the English flipper - fin) - a special protrusion on the butt of the blade. To open a conventional knife, it is enough to slightly move the blade, pressing the flipper with your finger, and then bring the blade to the working position with an energetic swing of the hand. In semi-automatic knives, there is no need for such a swing - the blade is adjusted to the working position by a spring mechanism automatically.
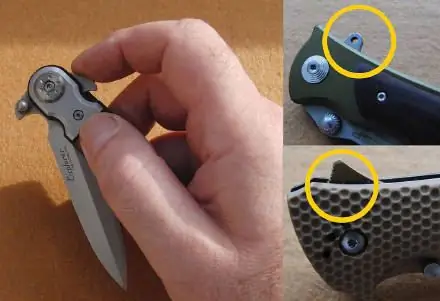
In addition, the flipper acts as a kind of guard, preventing the hand from slipping onto the blade.
Structural elements for more reliable knife control
The most common grip for folding knives is the straight diagonal (fencing) grip. In this grip, the thumb is placed on the butt of the blade.
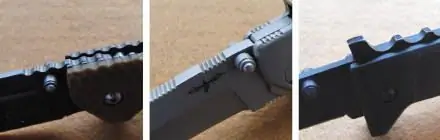
For more comfortable control of the knife, a special notch is made at the point of contact of the thumb on the butt of the blade. The part of the handle adjacent to the blade can also have a notch.
Lever
The handles of most modern knives have a batch typesetting design, consisting of an internal frame (frame) in the form of metal liner strips (liner) and linings. Elements for fixing the blade, an automatic opening mechanism (for semi-automatic and automatic knives) are mounted inside the frame.
Simple monolithic handles with a slot for a blade or a handle made of a bent strip of steel are rarely found in modern knives - mainly in the French "Opitel" and African "Duk-duk".
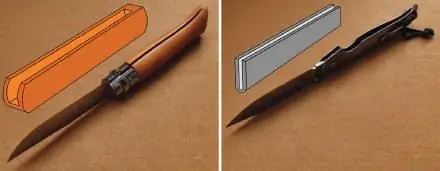
Previously, the connection of the parts of the handle into a single whole was carried out using rivets. The axis of the blade was also riveted. In modern models, screw connections are usually used for this. The use of screw connections allows you to eliminate the loosening of parts that appears during the operation of the knife, to regulate the "softness of the blade", facilitates the disassembly of the knife for maintenance work.
Most foreign folding knives use torx screws. To work with such screws, a special tool is required - screwdrivers or socket wrenches with a corresponding head. Some companies include such keys with the knife, otherwise they have to be purchased additionally.
The shape of the handle, its cross-section, as well as the texture of the linings determine the convenience and safety of using the knife.
The rectangular section of the knife is technologically advanced in production, but not convenient when performing long-term work with a knife. The round handle fits comfortably in the hand, but does not allow the knife orientation to be felt by touch. Therefore, the most convenient handles are oval.
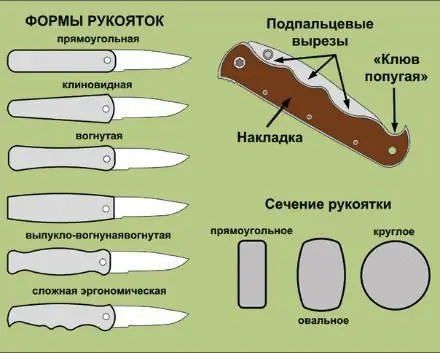
The rectangular shape is compact, but at the same time it does not provide protection against slipping of the hand onto the blade. The wedge-shaped shape of the handle better protects the hand when working with the tip of the knife, but when trying to pull out a knife stuck in a dense material, the hand will slide off the handle. Small pocket knives often have this shape for performing small household tasks.
The concave shape of the handle provides a more secure grip, but is not entirely comfortable. The convex shape of the handle fits perfectly in the hand and is comfortable to work with. This is the shape of the handle that the time-tested Finnish knives have.
Even more convenient is the handle of the convex-concave shape and the shape that is often used on tactical knives.
In modern knives, handles of complex shape, taking into account the ergonomics of the hand, are increasingly used. However, its configuration is calculated for a medium-sized hand, and a person with a large or, conversely, a small hand, will not be able to take full advantage of its advantages.
Overlays
For their manufacture, materials of natural (wood, bone, horn) and artificial origin (metals, plastic) can be used.
The main advantage of wooden linings is their "warmth" and the beauty of natural material. Exotic wood species with a very beautiful texture can be used in expensive handiwork knives. The main disadvantage is poor wear and moisture resistance. Multilayer varnish in some way solves the problem, but it reduces the reliability of holding the knife in the hand.
Horn and bone are another naturally occurring material. Handles made of these materials polish well and look very beautiful. Disadvantage - they can crack and are easily scratched.
Metal pads are highly durable, but in the cold season, knives with such handles are inconvenient to use. In addition, they are difficult to hold in a wet or sweaty hand, even with a notch on them. In modern knives, titanium alloys based on aluminum or titanium are used for their manufacture. Damascus steel can also be used in expensive designer knives.
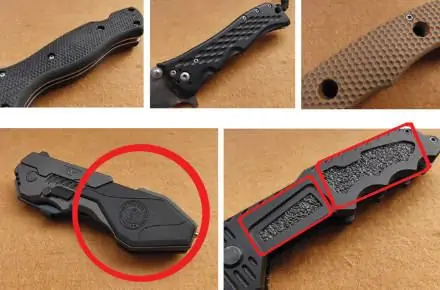
Materials based on synthetic resins allow simulating the structure of natural materials and at the same time avoiding their inherent drawbacks, although they lose weight to them. One of the most popular materials of this type is one of the types of textolite - "micarta".
Recently, pads made of various types of plastic are increasingly used, such as ABC, Zitel, Kydex, etc. These materials are technologically advanced, moisture resistant, durable and resistant to the external environment. They allow you to produce onlays of any shape with any pattern of texture - from the simple roughness inherent in the material of the onlays or rectangular notches to specially designed surface types. For example, CRKT's For Those Who Serve knives use a special honeycomb structure to prevent the knife from slipping in the hand.
For the same purpose, rubberized inserts or structural elements-inserts such as sandpaper are used.
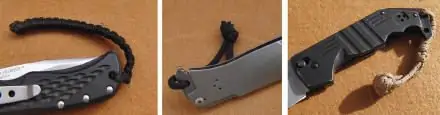
Many folding knife models have a round hole in the end of the handles for attaching a lanyard or lanyard to it.
Security elements
Although modern blade retainer designs are quite reliable, nevertheless, as noted above, there is a possibility of accidental folding of the blade. To prevent this, modern knives have special fuses. For knives with a butt lock, they are usually located in the notch area of the locking lever. On models with a linear lock, they are located at the front of the handle under the thumb. Supplementing the blade retainers with fuses practically turns the knife from a folding knife into a knife with a fixed blade.
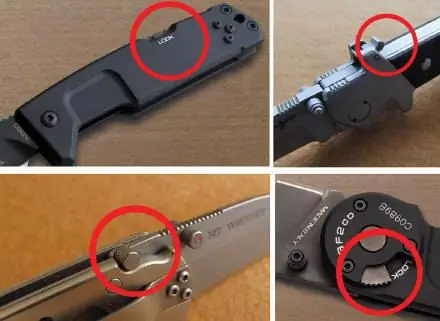
For the safe carrying of semi-automatic and automatic knives, a safety device must prevent the knife from opening in a clothing pocket if the trigger is accidentally pulled. Therefore, in such knives, the safety catch often has a double action - it blocks the blade in the closed and open state.
Clip for carrying
A steel spring clip is an almost indispensable attribute of modern folding knives. In the knife literature, the term "clip" is often used for its designation (from the English clip - clip, paper clip). It provides a convenient carrying of the knife in clothing pockets or on a trouser belt.
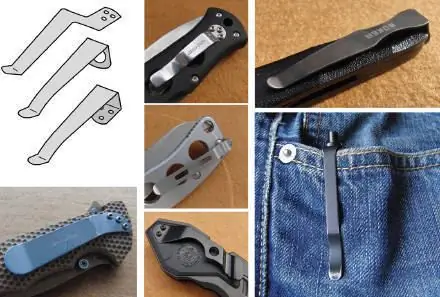
Many knife manufacturers make the clamp adjustable - that is, it can be attached to different sides of the handle depending on whether the owner is right-handed or left-handed. In addition, sometimes it is possible to change not only the side of the clamp fastening - at the base or at the end. In this case, in the pocket, the knife will be oriented either with its tip down or up. Some experts believe that when carrying the knife upside down, there is a possibility of a cut when trying to pull the knife out of the pocket if, for whatever reason, the blade comes out of the handle. At the same time, with this orientation of the knife, it is more quickly brought into working condition.
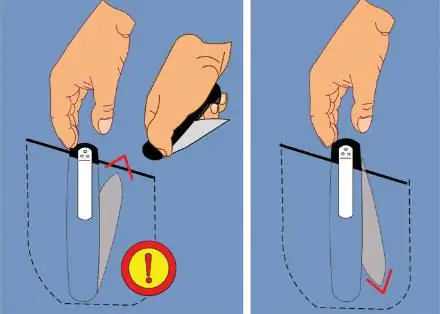
In some models of folding knives, the clip attachment point is not in the Z-shape, but in the shape of the letter "L" or "P". In this case, when carrying a knife in a pocket of clothing, the upper part of the handle is hidden from outside view - only the spring plate of the clip protrudes from the pocket. Outwardly, it looks like a regular ballpoint pen.
Elements that expand percussion possibilities
For self-defense purposes, the knife can be used without opening the blade. In this case, it is used as a palm stick and the blow is delivered by the parts of the handle protruding from the fist. In tactical knives and self-defense knives, the end of the handle to increase the effectiveness of such blows is often triangular in shape or a special impactor in the form of a cylinder, cone or pyramid.
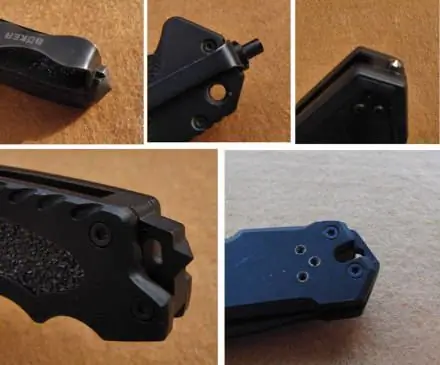
Concluding the review of folding knife designs, it should be noted that the legality of a knife, that is, the fact that it is not a melee weapon, can only be determined by an expert by law. Therefore, when purchasing a knife, you should always ask the seller for a copy of the information sheet for the certification test report (in common parlance it is often called a "certificate"). The absence of such a document, no matter what the seller says, may indicate that the knife you like has not passed the melee weapon test. Moreover, it is best if such tests were carried out by the parent organization - the “Forensic Center of the Ministry of Internal Affairs”. It is better to always have a copy of this document with you, which will allow you to avoid unnecessary conflicts with law enforcement officials.
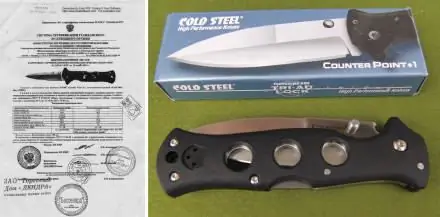
Most of the quality folding knives on the Russian knife market are products of foreign companies.
Unfortunately, most of the serial domestic folding knives are inferior to foreign ones in almost all respects, and among them you can rarely find original models.
Russian craftsmen and knife companies prefer to create knives with a fixed blade, and among them there are very original models that have no analogues abroad, which include Vitaly Kim's knives, the Kondrat knife, the NDK-17 knife (a saboteur's knife designed by Kochergin) … This is largely due to the more complex technology and the expensive equipment required for it.
Among Russian craftsmen, only a few design and produce original folding knives of the author's work, which are not inferior to foreign ones (including in price). As an example, the folding knives of the Ural master Urakov and the workshop of the Shirogorov brothers are shown.
The rapid pace of development of the Russian knife industry allows us to hope for the emergence of domestic folding knives that are not inferior to foreign models.