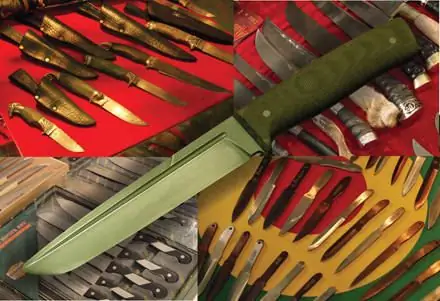
The history of knives began with knives in which the blade was rigidly attached to the handle and was constantly ready for work. Nowadays, despite the wide distribution of folding knives, such knives have not lost their relevance. They are indispensable in the field (combat, hunting, tourist), are widely used in the urban environment (knives of constant wear and self-defense knives) and dominate kitchens in apartments and catering establishments. Abroad, the name of knives with a fixed blade (fixed blade knives) in the knife slang - "fixed" was stuck behind them. However, this is not a very good definition, since many modern folding knives have a special mechanism for fixing the blade in the open state. It would be more correct to call them non-folding knives.
Unlike folding knives with a fixed blade, they have a number of advantages:
they are always ready to work - no need to open the blade, which can jam due to contamination of the hinge;
they are reliable in use - there is no risk of spontaneous folding of the blade due to a defect, pollution or destruction of the knife fixing mechanism.
An intermediate position between knives with folding and non-folding blades is occupied by knives with replaceable blades, which can be non-collapsible and collapsible.
The basis of non-separable knives with replaceable blades is a steel strip, one side of which is a knife blade, and the other is an instrumental one (sometimes a blade with a different sharpening or shape). The working blade is changed by throwing the knife handle.
Collapsible knives consist of a handle and a set of blades that can be fixed on it.
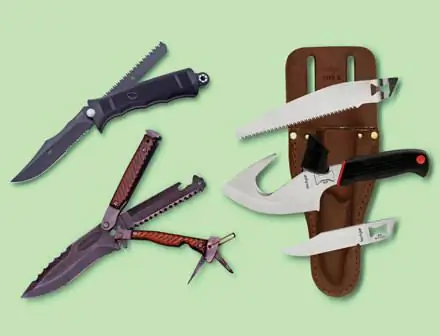
Knives with replaceable blades are superior to classic single-bladed knives in functionality, but inferior to them in reliability and ease of wearing.
Despite the fact that the design of non-folding knives is much simpler than folding ones, they have a number of features and elements. As a rule, on the sites of online stores, in catalogs and sites of knife manufacturers, the main characteristics of knives are given:
appointment;
total length of the knife;
blade length;
butt thickness;
blade hardness;
knife weight;
blade material of the handle and scabbard.
In foreign sources, the overall dimensions of the knife are usually given in inches (1 inch = 2.54 cm), and the weight in ounces (for example, 1 ounce = 28.4 g).
A complete picture of the knife can be obtained from their reviews in trade magazines or knife sites. However, for this you need to have an idea of knife terms, which can present certain difficulties for an ordinary consumer.
A lot of useful information about knives can be found on the knife forums on the Internet. However, regular participants in these forums, in addition to official terms, widely use a specific knife jargon, which for the uninitiated may seem like gibberish. Therefore, at the end of the article, there is a short dictionary of knife slang.
The purpose of this article is to help people who are not enthusiasts and connoisseurs of knives and the knife industry, but simply want to buy a reliable clamshell knife, fully aware of the purpose of its elements and not overpaying for useless design features (the cost of an awkward knife can range from hundreds to tens of thousands rubles).
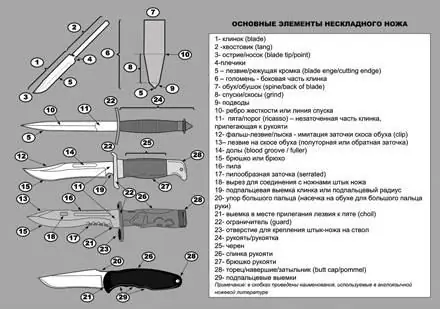
For an ordinary person, information about the legality of owning a knife is most important. Ie. Does it belong to melee weapons (CW), for the acquisition of which a special permit is required and there are certain mandatory rules for storing and wearing it, or is it a household knife (in common parlance “household”), the acquisition, carrying and use of which is not is surrounded by a strict legislative framework.
Only an expert who is guided by a number of signs and test results, the description of which can be found in special literature, can determine whether a knife belongs to XO.
For the average consumer, it is sufficient to have a copy of the certification test data sheet. This document contains not only the main characteristics of the knife and the name of the manufacturing company, but most importantly - the expert opinion on its recognition as a household one. The presence of this document with the owner of the knife will help to avoid a number of problems with law enforcement officers.
Whatever the seller or manager says, the absence of such a document, whether it is a knife shop or a specialized knife shop, indicates either its incompetence, or that the knife being purchased has not passed certification tests and may well turn out to be an XO, bringing its future owner a lot of trouble …
It should also be borne in mind that knife companies can produce different versions of the same knife model, outwardly very similar, but belonging to different categories. Therefore, when you receive the information sheet, you must carefully compare the image it contains with the knife you are holding in your hands. If the image in the information sheet does not correspond to the original - such a document is worthless.
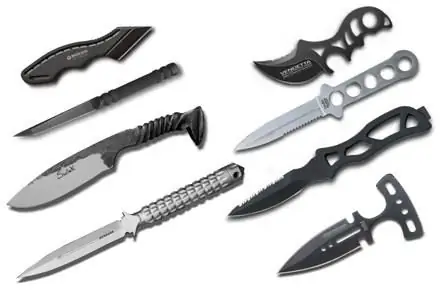
Some Chinese manufacturers produce copies of combat knives of well-known Western companies in the form of DIY kits. By itself, such a set does not require certification. However, a knife assembled from this set of parts will be a melee weapon with all the ensuing consequences.
Design
The main elements of the non-folding knife are the blade, the handle and the stopper. The blade is the basis of the knife, it is with it that all the work with the knife is performed. The handle determines the convenience of the knife. The stopper protects the fingers from slipping onto the knife blade.
These main parts can be made as separate structural elements or formed from a single piece of material. These knives include, for example, the so-called "skeletal" knives, which got their name from the shape of the handle, somewhat reminiscent of a skeleton due to the holes in it of various shapes. The handles of these knives are often wrapped with a cord for easy grip.
Blade
The blade of non-folding knives in the classic form is a strip of steel, one part of which is sharpened (the blade itself), and the second is the shank, which serves to attach the handle to the knife.
The working characteristics of the blade are determined by its material, manufacturing technology, geometric shape and section of the blade.
Blade material
In the knife industry, the most common material for making a blade was and remains various types of steel: carbon, alloyed (stainless) and patterned (damask, damask).
There are a great variety of steel grades, and their complete description can take more than a dozen pages. A wide variety of steels used for the production of knives is associated with the need to obtain mutually exclusive blade qualities - ease of sharpening and durability of cutting properties, resistance to shock loads and hardness of the cutting edge.
An indicator of wear resistance (the duration of keeping the sharpness of the blade) is the hardness of the blade. It is customary to measure it in units of the Rockwell "C" scale - HRC. The higher this number, the harder the knife blade.
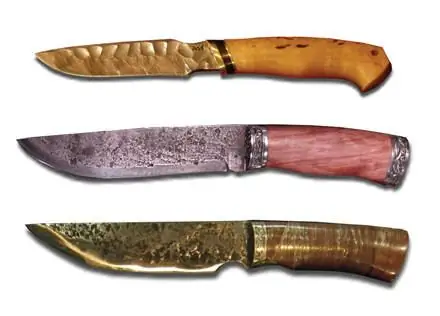
The blade acquires hardness during the heat treatment of the blade blank (quenching, tempering). With improper heat treatment, even from the most perfect and expensive steel, you can get a blade of poor quality, and vice versa, even from simple inexpensive steel, a blade with good performance can be made.
Usually the blades of non-folding knives have an indicator in the range of 42 … 61 HRC. Hardening blades to values exceeding 61 HRC leads to increased fragility of the blade, and below 42 HRC to low wear resistance (usually such blades have souvenir copies of cold steel).
The traditional material for blades is carbon steel (the main components are iron and carbon). Low-carbon steels (0, 4 … 0, 6% carbon) make it possible to produce blades, the blade of which withstands shock loads well (blade toughness), is easy to sharpen, but also dulls easily. Blades made of high-carbon steels (0, 7 … 1, 2%) retain the sharpness of the blade for a long time, but are more difficult to sharpen and poorly withstand shock loads. A common disadvantage of carbon steels is low corrosion resistance, which requires specific care of the blade or the application of a protective coating to it so that it does not rust.
A special place among blades made of high-carbon steel (up to 1, 2 … 2, 0% carbon) is occupied by blades made of damask steel. As a result of trial and error, the masters of antiquity learned how to obtain steel of a complex structure. This steel made it possible to make blades that combine hardness, resistance to mechanical stress (toughness) and elasticity. The unique properties of damask steel are associated with the formation of micro- and macroinhomogeneities in the metal structure. The presence of these inhomogeneities also determines the specific pattern on the surface of the damask blades, and the larger and clearer this pattern, the higher the quality of the damask steel.
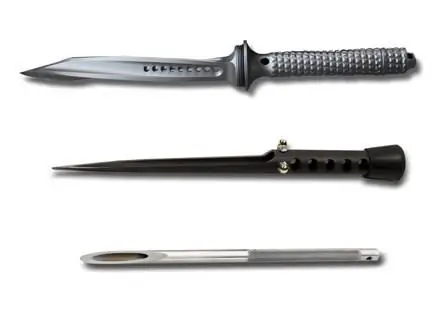
The secret of making damask steel was irretrievably lost. As a result of painstaking research of ancient damask steel samples and many experiments by the Russian scientist Pavel Petrovich Amosov in the 1830s. a technological process was developed that allows to obtain steel with properties similar to damask steels.
Damask knives are a piece and expensive product. This is due to the high labor intensity and complexity of the manufacture of damask steel, which results in the instability of obtaining high-quality damask steel and a high level of rejects (even among the most famous masters, it can account for up to a third of products).
The fashion for knives from damask steel has led to the appearance on the knife market of products that have nothing to do with real damask steel. For example, to obtain a damask pattern, forging of stainless steel is used, followed by pickling or remelting of alloy steels using the damask steel technology. It is not easy even for a specialist to distinguish such knives from real damask knives in appearance.
Nowadays, the most widespread are blades made of stainless steel, which has high performance characteristics, thanks to the additives in their composition (chromium, tungsten, molybdenum, etc.). Despite its name, such steel is also susceptible to corrosion, although to a much lesser extent than carbon steel. It is caused by the presence of impurities, which are less, the higher the culture of production and, of course, the price of a knife made of such steel.
An attempt to combine the "elasticity" and "hardness" of various grades of steel in one blade led to the creation of composite blades. That is, blades consisting of several types of steel.
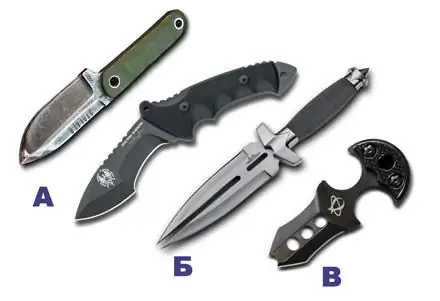
Damascus steel is produced by repeatedly forging coiled strips of low and high carbon steel. As a result, the final product combines high flexibility and blade hardness.
The surface of the damask blades has a pronounced pattern. Modern technologies for producing Damascus allow you to design the appearance of this pattern in advance and obtain a variety of images on the blade.
However, as in the case of damask steel, the production of high-quality damascus is a complex, lengthy and expensive technological operation. Its high-quality implementation is available only to a few manufacturers. The consequence of this is a high final cost of products and a high level of rejects. At the same time, it is rather difficult for a layman to distinguish a real "working" damascus from a decorative one and to assess the quality of its manufacture. Therefore, there is a high risk of acquiring a beautiful knife that looks good on a shelf in an apartment, but is useless for doing real work. Moreover, some manufacturers produce blades that imitate the surface of Damascus steel (applying a damask pattern to the blade in various ways).
Another technology for the manufacture of composite blades is packaging - the creation of a blade from a welded package of steel strips, in the center of which there are "hard" grades of steel, and on the sides - "soft" plastic ones. This makes it possible to produce blades that combine high hardness with resilience.
It should be noted that the prevailing opinion about the alleged "self-sharpening" of such knives does not correspond to reality.
The laboriousness and complexity of this technology and, as a result, the high cost of final products has led to its low prevalence. Basically, knives with multi-layer blades are produced by Scandinavian and Japanese manufacturers at a cost of several tens of thousands of rubles.
On the knife market, you can also find non-folding knives with blades made of titanium alloys, ceramics and various types of plastics.
A feature of knives made of titanium alloys is their very high corrosion resistance, strength, which is maintained up to a temperature of minus 50 ° C, elasticity and low weight. The disadvantages of a titanium blade include the low resistance of the cutting edge, the difficulty of its restoration and the high price of knives with such blades (8-10 times higher than a similar knife made of steel).
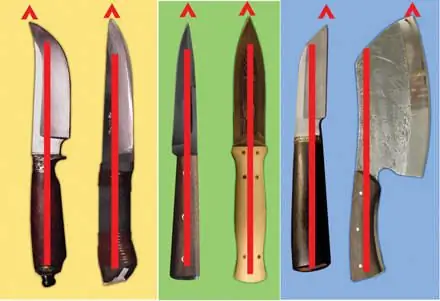
These features also determined the field of use of knives with a titanium blade - fishermen, divers, water tourism lovers. Since titanium is a non-magnetic metal, such knives are used by combat swimmers.
Ceramic blades are not subject to corrosion, have a high hardness of the cutting edge and its durability. The disadvantage of such knives is their high fragility. The result of lateral loading or the fall of the knife to the floor will break the blade. In addition, it is not possible to restore a dull cutting edge in such knives. Ceramic blades are widely used mainly in kitchen knives.
Recently, technologies have been developed for creating composite blades with a ceramic core and steel plates. Bringing them to industrial use will make it possible to create blades that combine the hardness and wear resistance of ceramic blades with the strength and resilience of steel blades.
Plastic knives are not reusable. In terms of strength and cutting ability, they are significantly inferior to knives with a steel blade. Their main advantage is "invisibility" for metal detectors, which determines the field of application - hidden carrying knives.
Additional surface treatment of the blade
The surface of the blade is often subjected to additional mechanical treatment (polishing or matting) or a protective coating can be applied to it in the form of an oxide film, polymer material, or a thin layer of metals or their compounds. The purpose of this processing is:
make the surface of the blade shiny, glare or, conversely, matte and dark (non-glare);
protect the blade from corrosion;
increase its wear resistance.
Polishing (mechanical or electrochemical) is a classic type of processing, as a result of which the surface of the blade acquires not only a mirror shine, but also additional protection against corrosion.
Matting. In some cases, glare from light on a polished surface is an undesirable factor (combat and tactical knives). In order for the surface of the blade to become matte, special methods of machining the surface of the blade are used - satin finishing, rough grinding or blasting.
When satin-finishing, the surface of the blade is covered with micro-strokes using special brushes or abrasive paper.
Rough grinding (stone-washed) of the blade is done with rolling stones.
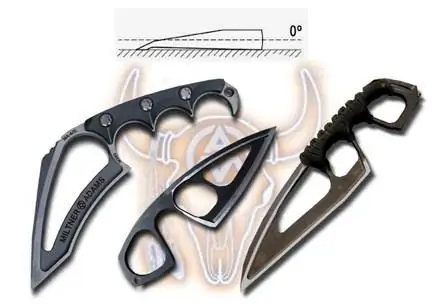
As a result of satin-finishing and rough grinding, the surface acquires a matte appearance, the glare of the blade is weakened, but it continues to reflect direct sunlight.
During blasting, a stream of small particles (sand, corundum chips, glass beads) is sent to the blade under high pressure. In contrast to the two processes mentioned above, in this case, some hardening of the blade surface occurs. But when treated with corundum particles, the surface of the blade acquires a strong roughness, which worsens the blade's resistance to corrosion.
Bluing (oxidation, blackening) - obtaining a thin oxide film on the surface of the blade. One of the simplest and cheapest coatings that give the blade a dark color. In the old days, this was one of the main methods of protecting against corrosion of carbon steel blades (stainless steel blades do not lend themselves to bluing). However, bluing does not tolerate the effects of acids (lemon juice, kebab and vegetable marinade, etc.). Therefore, it is currently only used in cheap knives or for decorative purposes.
Parkerization - coating the surface of the blade with phosphate, as a result of which the surface of the blade acquires a matte gray color and increases its wear resistance. Such a coating is rarely found in modern knives.
Nickel plating, chrome plating is widely used in the production of non-folding knives. Gives the blade the same ominous sheen often described in the literature.
Advances in modern chemistry and the introduction of new coating technologies have led to the emergence of new protective blade coatings.
Epoxy coating (epoxy powder coating) - application of heated powder of epoxy resins to the blade. These coatings can be applied to all types of steel and painted in any color. This coating protects well against corrosion, does not glare, but is not highly resistant to mechanical stress. Damage to the coating quickly leads to its flaking, so it is mainly used in inexpensive knife models.
Teflon and fluoroplastic coatings protect the blade well from the effects of water, alkalis and acids. In addition, they facilitate cutting of materials by reducing friction on the side surfaces of the blade.
Most often, this coating is black. As a result of operation, the surface of the blade is quickly covered with scratches. Since the protective film penetrates into the top layer of steel to a depth of several microns, these scratches do not lead to a loss of the protective properties of the coating.
Compared to epoxy coatings, such processing of blades is more expensive.
Coatings from compounds of refractory metals (titanium nitride TiN, titanium carbonitride TiNC, titanium carbide TiC, boron carbide B4 C, chromium nitride CrN, etc.). The coatings come in a variety of colors, ranging from golden to dark gray or black.
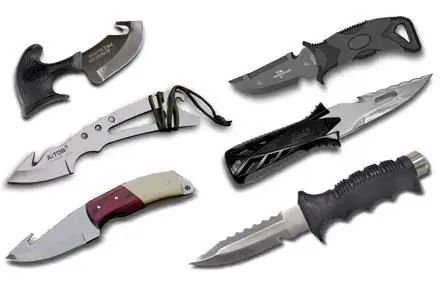
To apply these coatings, rather complex technologies are used - plasma spraying and ion-plasma deposition. A thin protective film made of these materials (3-5 microns) penetrates into the surface layer of the metal at the molecular level and perfectly protects the blade from corrosion and has high mechanical resistance.
Manufacturing companies often use their brand names to refer to these coatings. For example, the titanium carbonitride coating used in Benchmade knives is called Black-Ti.
Diamond-Like Coating (DLC) came to the knife industry from mechanical engineering. It is a thin carbon film (0.5 … 5 microns), the structure of which combines the properties of diamond and graphite. When applied to a metal surface, it significantly increases its strength properties, resistance to aggressive media, and reduces the coefficient of friction.
The last two types of coatings provide not only a high resistance of the blade to corrosion, but also provide a manifold increase in its wear resistance (hardness of the cutting edge), although the sharpness of the cutting edge is somewhat reduced. The DLC coated knife blade retains its cutting properties 5-10 times longer. However, due to the complexity of the technological process of applying these coatings, the cost of the knife also increases several times. Such coatings are used in expensive elite knives.
A common disadvantage of all the considered coatings is that on the blade of the blade their protective properties are lost after the first sharpening.
Recently, blades with traces of scale or forging have become fashionable, emphasizing the hand-made knife. However, from a functional point of view, such processing of the blade has no advantages, and in terms of resistance to corrosion, they are significantly inferior to blades with a protective coating.
Blade geometry
The shape of the geometry of the blade and its cross-section allows you to optimally realize the properties of the material from which the blade is made to perform the work for which the knife is purchased.
Usually the blade of a knife is flat and its shape does not differ from the shape of the blades of folding knives (for more details see "Anatomy of a folding knife", "Brother", January 2013). Nevertheless, there are knives in which the blade strip is twisted into a spiral, as well as knives in which a hollow metal tube is used instead of a flat strip. Such knives are intended only for stabbing in a knife fight or in self-defense and are not suitable for performing normal operations associated with cutting or planing objects.
The tip (toe) of a knife determines its stabbing ability and is formed by beveling the butt and lifting the blade. Contrary to the name, the edge of the knife may not be sharp. The rounded tip, for example, has knives for rescue operations.
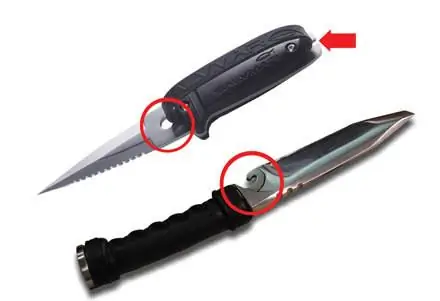
Classic knives have only one edge, although models with two points can also be found on the market. These can be double-bladed knives, the shape of which is inspired by the shape of the sacred Muslim sword Zulfiqar. It is believed that it is possible to catch the enemy's blade in the slot between the blades, although this is rather doubtful. More interesting are knives for personal self-defense, which have two points, but without a gap between the blades. In such knives, the small length of the blade is compensated by the possibility of the so-called "frontal cut", in which the target is not pierced, but the target is cut with a piercing blow.
As a rule, the thickness of the blade gradually decreases towards the point, which affects its strength. Knives with a tanto blade or modified tanto, as well as knives with a reinforced edge, are free from this drawback. The disadvantage of knives of the latter type is the difficulty of sharpening them.
Typically, the tip of a non-folding knife is on an axis through the center of the knife. Knives with a raised edge are also widespread, much less often with a lowered one. The raised tip makes it easier to concentrate the force in a certain place, and the lowered one - to get a neat straight cut of the material on a hard surface.
The blade of the blade is formed by descents and leads. Slopes can be straight (the best option, combining blade strength and good cutting properties), concave (excellent cut, but low strength) and convex. Usually the profile of the descents is symmetrical on both sides of the blade. In classic Japanese knives, an asymmetrical shape of the slopes is used - the so-called "chisel". However, when performing most of the work, this shape of the blade section is inferior to the classic symmetrical one.
One of the challenges in rebuilding a dull blade is keeping the sharpening angle accurately along the cutting edge. To facilitate this process, the American company "Miltner Adams Co" has developed a special blade profile "HollowFlat Blade", which is used in the tactical knives of this company. A special feature of this profile is a specific "side" on the blade. When sharpening the blade, the blade is parallel to the surface of the whetstone.
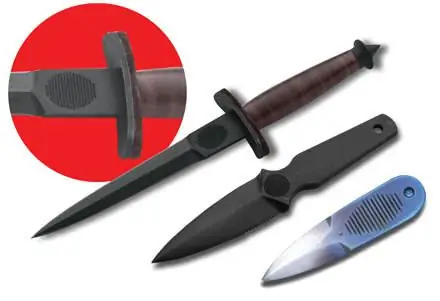
The blade itself can be straight, convex, or concave. A straight blade is the most functional and convenient for most operations performed with a knife. It is also easy to sharpen.
The pronounced convex part of the blade is called the abdomen (or belly) and provides a concentration of cutting force on a limited part of the blade.
The concave (crescent) blade allows you to rip open the cut surface.
The convex and concave shape of the blade is most often used in combat and tactical knives, as well as in knives for personal self-defense.
In addition to the classic plain (plain) sharpening of the blade, there is a sharpening in the form of teeth or waves. In total, there are five types of such sharpening: micro-teeth, teeth, wavy, hacksaw and shock teeth.
Micro serrations are a notch on the blade (A) that is made during the knife-making process using a curly cutter. In this case, the size of the micro-teeth does not exceed 1 mm.
The micro-serrated blade makes it easier to work with hard materials (frozen food). In addition, such a knife, having lost the ability to cut, will still be able to "saw".
A blunt micro-serrated blade can be sharpened to regain its cutting ability, but the micro-teeth on the blade will be lost.
This type of sharpening is sometimes mistakenly called "laser". It is often used in kitchen knives (along the entire length of the blade), and sometimes on survival knives and bayonet knives (on the part of the blade at the handle, including the butt). Quite rarely, this sharpening is located in the front of the blade. This arrangement makes it easier to pierce dense fabric.
Serrated sharpening - serrated (from the English serrated - serrated, serrated) is a series of mini-concave blades (B) with teeth from 1 to 5 mm. Unlike folding knives, on which the entire blade can have such a sharpening, in non-folding knives it occupies only a part of the blade near the handle (sometimes on the butt of the blade).
Compared to a smooth cutting edge, serrated has a number of advantages:
due to the fact that the cut occurs at different angles, it facilitates the cutting of fibrous and laminated materials - ropes, ropes, cables, braid, cardboard, etc.;
the blade retains its cutting ability longer;
the cutting of the material is faster due to the fact that with the same blade length, the length of the cutting edge with the serrated is longer.
For these advantages, you have to pay with the unevenness of the cut, the inconvenience or even the impossibility of performing a number of household work, the difficulty of restoring such sharpening. Due to the asymmetry of the blade section, with a significant cutting force, the blade can be pulled to the side.
The areas of use for such sharpening are tactical knives, survival and self-defense knives, diving and rescue knives, kitchen knives.
The most widespread form of serrated sharpening, developed by the specialists of the Spyderco company, in which two narrow teeth alternate with one wide one.
To restore a blunt serrated sharpening, special sharpening tools are used, and for a beginner, such work presents certain difficulties.
Microtoothed and serrated sharpening significantly improves the weak cutting ability of knives with plastic blades.
A wave-like or scalloped edge (scalloped) is characteristic of kitchen bread knives (B).
Hacksaw sharpening, or "saw tooth" sharpening, is a series of triangular teeth, the ends of which, unlike serrated sharpening, are located in two planes (D). It is this sharpening that allows you to saw wood and is used in camping and survival knives.
The shock teeth on the blade are large sharpened teeth on the butt of the blade (D). Their purpose is to inflict lacerations on the enemy. They were used on combat knives, but are now rare. In some models of knives, you can find a decorative version of shock teeth - a series of slots or notches on the butt of the blade.
The role of shock teeth in some way can be performed by serrated or hacksaw sharpening.
A variety of hunting knives designed for skinning animals (skinners from the English skin - skin, leather), on the butt of the blade has a special device - a skinning hook. A similar hook has diving blades, but its purpose is different - cutting ropes, ropes and cables.
Butt (butt) - the side of the blade opposite to the blade. Usually non-folding knives have a butt thickness of 1.5 to 10 mm. The thicker the butt, the stronger the knife, but at the same time its weight increases and the convenience of cutting various materials deteriorates. Thick-necked knives are sometimes called "crowbars".
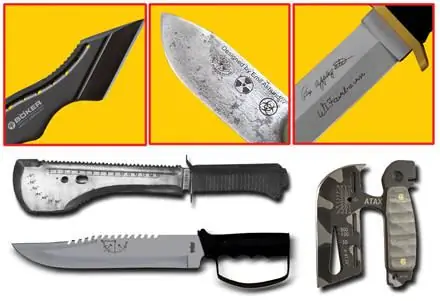
Knives, designed for people who are fond of archery, crossbow or spearfishing, have a special curly cutout on the heel of the blade, which makes it easier to pull out stuck arrows or a harpoon.
Dolly - longitudinal cuts on one or both sides of the blade. In common parlance, they are often called "bloodstreams". But they have nothing to do with bloodletting. Their purpose is to lighten the blade and increase its lateral rigidity. Sometimes, in pursuit of originality, the manufacturer makes them through, but the result is a weakening of the mechanical strength of the blade.
In the front of the blade of bayonet-knives (sometimes in survival knives), you can find a small through oval hole. With its help, the blade of the bayonet-knife attaches to the scabbard, forming wire cutters.
Semicircular cutouts on the side of the blade at the border of the blade and the handle. A small notch in front of the fifth blade with a diameter of 1-3 mm (“muzzle”) serves for the convenience of sharpening the blade. A larger semicircular notch is called a sub-finger notch or sub-finger radius. It is designed for the index finger of the hand and serves to facilitate pulling out a knife stuck in dense material.
"Thumb print" - an oval area at the heel of the blade, covered with shading. It is designed to support the thumb while holding the knife with a fencing grip. For the first time, such a structural element was used on the famous "V42" dagger of American special forces during the Second World War.
This "imprint" can also be found on the limiter or handle of mini-knives for self-defense.
Inscriptions on the blade. Well-known knife companies can put on the blade its logo, the name of the country where the knife was made, the type of steel, the name of the knife model, facsimiles of famous knifemakers, etc. On inexpensive knives, these inscriptions are applied with paint or by stamping. On more expensive models, etching or engraving is used.
In addition, the blades of survival knives can have different markings - goniometric and / or measuring, rangefinder scale, etc.