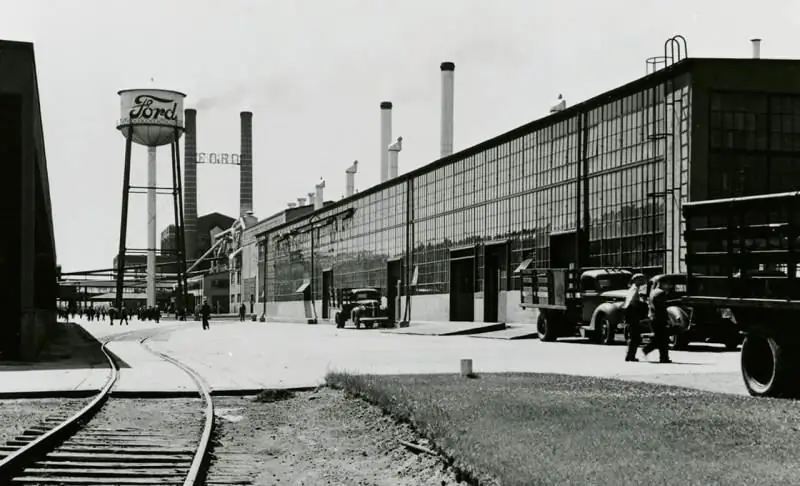
Strategic technologies
Before getting acquainted with the features of armored production at the Michigan plant "Ford" in Detroit (USA), it is worth briefly explaining the conditions under which the armored industry was being established in the USSR. As you know, everything is learned by comparison.
Armor production during World War II was one of the most important factors in strategic advantage. With the beginning of the war, the Soviet Union found itself in a disastrous position - all armored production was concentrated in the European part of the country. The rapid advance of the German army could completely paralyze the production of tank armor in the country. Only at the cost of incredible efforts to evacuate part of the factories to the east at the beginning of the war was it possible to restore the production of armor. The main "armored factories" were Kuznetsk, Nizhniy Tagil and Magnitogorsk metallurgical plants.
But the matter was not limited to a simple transfer of production to a new site behind the front line. Most of the new factories were not adapted to the smelting of tank armor - before the war, the factories worked for the needs of the People's Commissariat of Ferrous Metallurgy. Wartime has added its own adjustments. Now the open-hearth furnaces often had low-skilled workers, there was an acute problem of the lack of special thermal, pressing and metal-working equipment. Therefore, the transfer of armor production was accompanied by a serious restructuring of the technology itself for smelting military steel. So, it was necessary to adapt production to the main open-hearth furnaces for 120-180 tons, excluding the process of diffusion deoxidation. The hardening of armor plates and armor parts had to be carried out in water.
Such a simplification could not but affect the quality of the armor received. This is especially true for the most difficult to manufacture high-hardness tank steel 8C. The very first samples of armor plates on tests showed significant slate and layering of the fracture, a high tendency to crack formation during welding and straightening. In addition to this, field tests revealed the excessive fragility of the armor samples during shell fire.
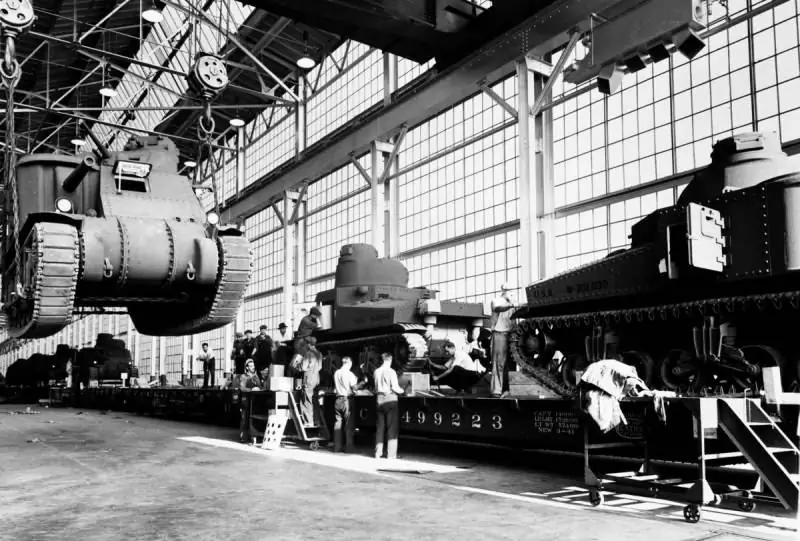
Such defects could not be ignored. And in the specialized TsNII-48 they have developed a number of improvements. First of all, from now on, armor steel was supposed to be smelted only in preheated furnaces after smelting "civil" grades of steel. The steel had to boil in the open-hearth smelting bath for at least one and a half hours, and poured into square or convex molds. In addition, metallurgists paid special attention to the sulfur content in the original pig iron (no more than 0.06%), as well as carbon and manganese. In combination with other measures, this made it possible to improve the quality of the armor. In particular, to reduce the slate and layering of the fracture.
An important problem was the technology of heat treatment of domestic armor. To put it simply, the hardening and tempering of the armor plates took too much time and energy, and the necessary equipment was lacking. It was necessary to simplify the process. In this regard, we will give a typical example. In 1942, the metallurgists of TsNII-48 managed to simplify the process of thermal preparation so much that only for parts of the bottoms of KV and T-34 tanks they saved about 3230 furnace-hours per 100 hulls.
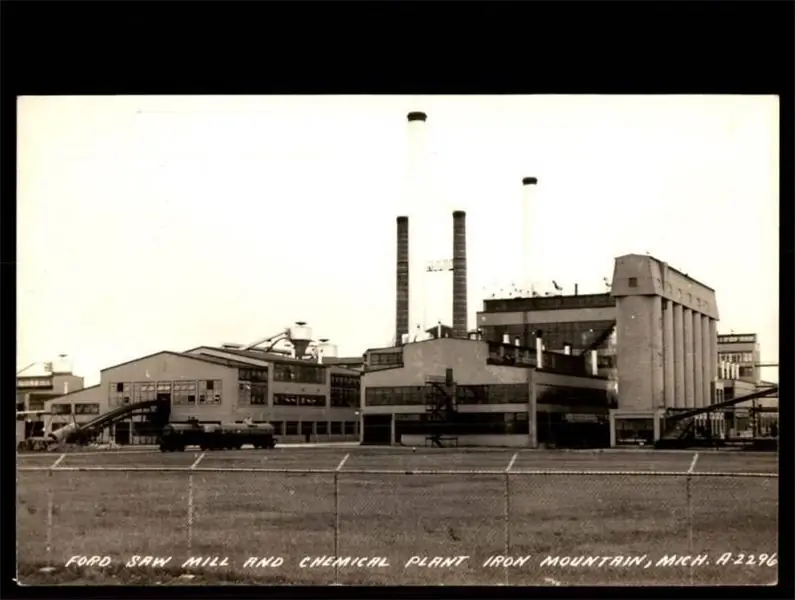
Nevertheless, until the very end of the war in the Soviet Union, the conditions for the production of strategically important tank armor were far from required. The same cannot be said about the military industry of the overseas partner, whose territory was not affected by the world war. The Soviet metallurgical engineers had to make sure of this once again on February 26, 1945, 72 days before the Victory.
American luxury
The little-known history of the visit of the Soviet delegation to the Ford armored factory in Detroit was announced by Vasily Vladimirovich Zapariy, Candidate of Historical Sciences of the Institute of History and Archeology of the Ural Branch of the Russian Academy of Sciences. The scientist's material is based on the report of Soviet metallurgists on the results of a trip to the United States stored in the Russian State Archive of Economics (RGAE). It should be noted that the RGAE is just a treasure trove of archival documents from the era of the Great Patriotic War, related to the production of military equipment and equipment. It remains only to guess how many more secrets the archive keeps in the hitherto classified evidence.
According to engineers who returned from Detroit, the armored workshop of the Ford plant was a building consisting of two spans measuring 273 meters in length, 30 meters in width and about 10 meters in height. At the same time, the shop did not smelt armor. It was mainly intended for heat treatment and cutting of steel. This naturally aroused particular interest among Soviet metallurgists, given the above-described problems of domestic armored production. The main production profile of the Ford Motors workshop was working with armor up to 76 mm thick. Heat-treated steel sheets were used to weld the hulls of light and medium armored vehicles at other factories in Detroit.
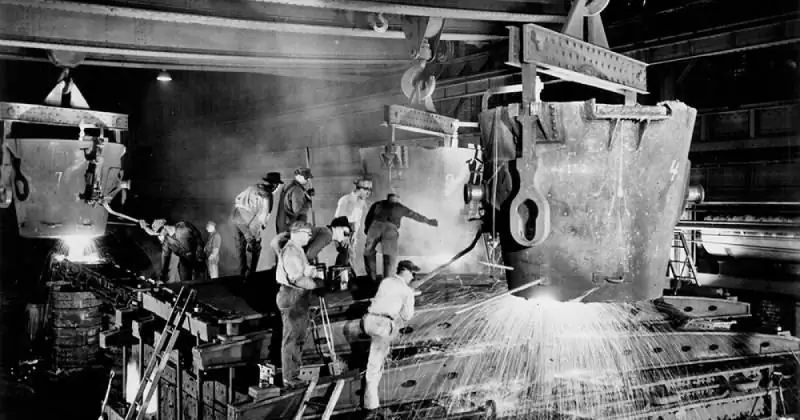
First of all, the mechanization of the production process impressed the Ford workshops. After being melted and rolled, the armor plates were delivered to the heat treatment shop on hydraulic table loaders United. The loaders, in turn, took the armor from the railway platforms located near the workshop. In the workshop itself, there were two overhead cranes designed to move armor sheets during all technological operations, with the exception of hardening processes.
To create the necessary crystalline structure of the armor, two presses, with an effort of 2500 tons each, five 70-meter conveyor method furnaces and five 100-meter gas tempering conveyor furnaces were called upon. Water was supplied to the armor hardening presses through the operation of six pumps at once, pumping more than 3700 liters per minute. As domestic engineers wrote, the complexity and cost of the design of such presses, capable of simultaneously stamping and cooling red-hot armor, were prohibitive. At the same time, there were doubts about the advisability of using presses for armor with a thickness of 30-76 mm. Here, the intensity of water supply for cooling came to the fore.
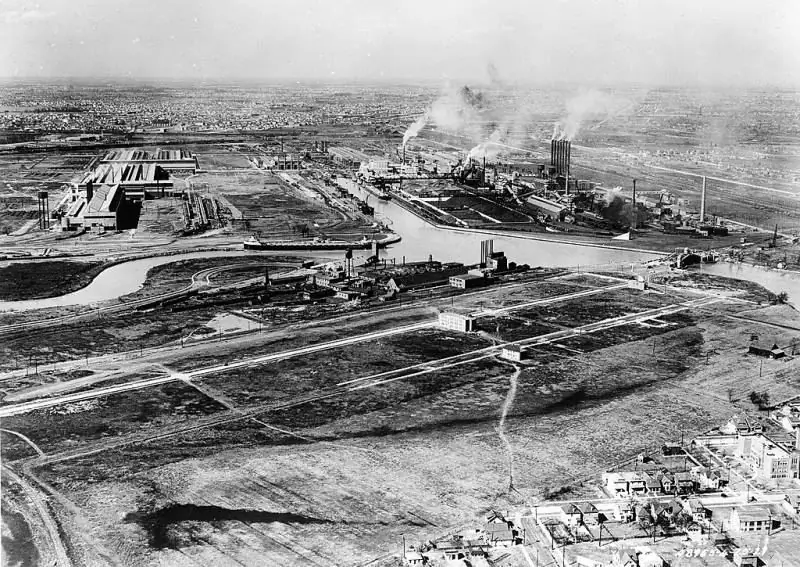
The 2,500-ton presses weren't the only ones in the Ford armored vehicle. Toledo presses # 206 were engaged in cutting thin armor and developed a pressure of 161 tons. For armor thicker than 2.5 cm, exclusively fire cutting was used.
During a visit to the enterprise, metallurgists were able to catch the process of hardening thin bulletproof armor. Under a press of 1000 tons, it stayed for 15 seconds, and then the sheet was sent for 2.5 hours for quenching at 900 degrees Celsius and for four hours of vacation at 593 degrees.
All this technical wealth was observed by Soviet engineers, not counting various "small accessories": welding machines, milling machines, scissors and the like.
The main feature of the heat treatment of the armor was the continuous flow of production. At almost all stages of processing, steel sheets were in the process of moving on roller and chain conveyors. The conveyor was controlled from a central control panel. At one of the last stages, all armor plates were inspected for the level of Brinell hardness. In this case, the fluctuation of the test parameter from sheet to sheet should be minimal - no more than 0.2 mm.
Of particular interest to the Soviet delegation were two shot blasting machines, which cleaned the armor plates almost after each technological operation. Such perfectionism and such a luxury could only be afforded by Americans, far from the hardships of wartime.