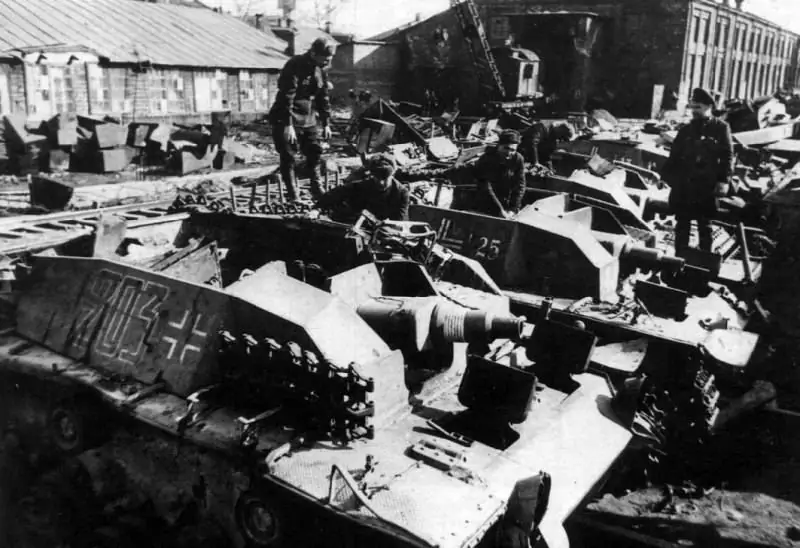
The subtleties of German booking
In the previous part of the material on the research of German armored vehicles in Sverdlovsk in 1942, the chemical composition of tank armor was discussed.
In reports, Soviet metallurgists noted the high hardness of German steel due to the high proportion of carbon. This, among other things, made the armor too fragile, which the testers encountered during the fire tests.
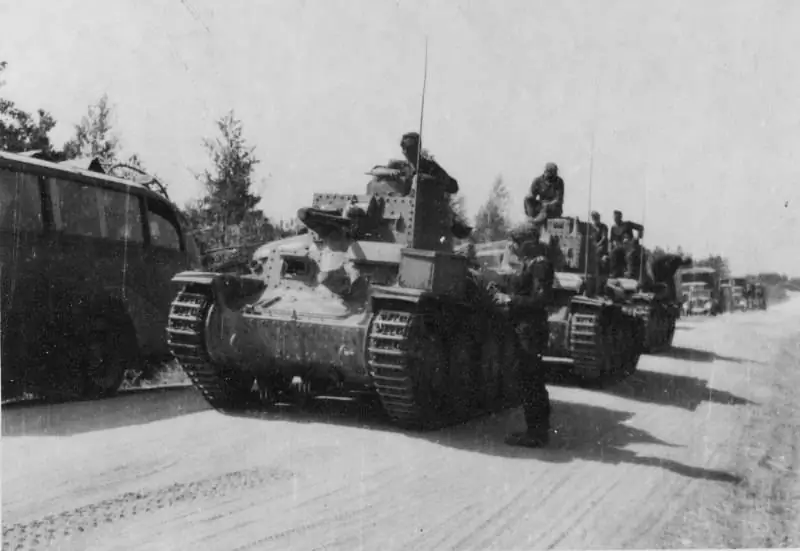
Enemy steelmakers were highly praised for their careful attention to the purity of the alloys obtained.
In most of the samples, the sulfur content did not exceed 0.006-0.015%, and the phosphorus content did not exceed 0.007-0.020%. Unfortunately, Soviet metallurgists did not always succeed in removing harmful impurities in this way. So, in Nizhny Tagil in tank production in the first quarter of 1942, the average phosphorus content in the armor was 0.029%, and only in the third quarter its share was reduced to 0.024%.
Of considerable interest was the degree of alloying of German steels, which significantly exceeded the domestic one in this parameter.
For example, bulletproof armor of captured tanks with a thickness of up to 20 mm contains more than 2% nickel in silicon-chromium-nickel steel, up to 0.45% in silicon-chromium-molybdenum steel, up to 0.45% in silicon-chromium-nickel-molybdenum steel, nickel in silicon-chromium-nickel-molybdenum steel about 3, 5% and molybdenum - 0.3%, in chromium-molybdenum-vanadium steel - molybdenum is about 0.5%.
For bulletproof armor of domestic production (grades 1-P, 2-P, etc.) of the same thicknesses, steels that are much less alloyed with molybdenum and nickel are used. And quite often they do without these alloying elements at all.
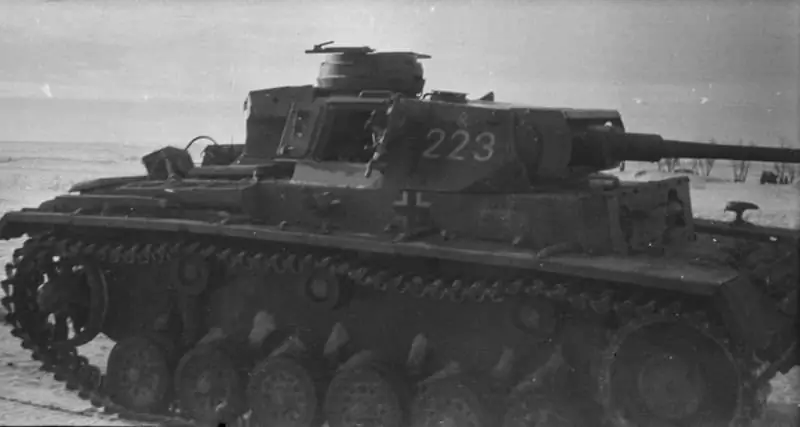
TsNII-48 specialists participating in the armor research indicate that the domestic industry has nothing to learn from German armored vehicles. Simply put, any fool can achieve high armor resistance through the widespread use of scarce nickel and molybdenum.
Try the same trick without using expensive metals - by fine-tuning the production cycle of smelting, rolling, quenching and tempering.
In many ways, for the Soviet industry, this was a forced measure - there was a chronic shortage of non-ferrous metals. And the Germans, having conquered almost all of Europe by 1941, could afford to generously sprinkle the armor with alloying elements.
The exception among the steels under study was the German chromium-molybdenum-vanadium 20-40 mm projectile armor. Analysis of these samples showed a level of alloying similar to that of domestic armor.
Continuing the research theme of alloying German armor, engineers in Sverdlovsk did not find any clear pattern between steel composition and thickness.
Recall that the following captured tanks took part in the tests - TI, T-IA, T-II, two T-IIIs with different cannons, flamethrower Flammpanzer II Flamingo, Pz. Kpfw.38, StuG III Ausf. C / D (reckless "Artsturm ") And, according to the Russian classification of 1942, the heavy T-IV.
If we take several samples of armor up to 15 mm thick from different tanks, it turns out that for some of them their proportion of alloying elements will correspond to the norm, and for some, nickel will go off scale for 3.5%. Specialists from TsNII-48 suggested:
"The use of different and often high-alloy steel for the same thickness and type of armor is most likely due to the use by the Germans not only of the armored steel grades of their production, but also of those significant reserves of armor that were captured in the occupied countries."
Under scrutiny
The next characteristic of German armor was its appearance - a fracture, as one of the main parameters of workmanship.
A bit of theory in a highly simplified form.
If a fibrous metal structure is observed at the fracture, then the quality of the armor is high, and it is quite viscous. But if there are crystalline areas or crystalline rash, then this is a sign of a gross manufacturing defect.
For example, the T-IV armor was not the most uniform in fracture analysis. With the same chemical composition and thickness, the fracture of some parts was satisfactory (and often very good with a fibrous fracture), while in other similar samples the fracture was of a substandard crystalline form.
There was a rough marriage of German steelmakers. But it was impossible to talk about such violations as about the system - after all, the sample of trophies from Soviet engineers was small.
In fairness, in connection with the rapid offensive of the Germans in 1941, the quality of domestic armor in terms of the fracture parameter also seriously decreased.
For example, for KV tanks, the People's Commissariat of Defense allowed crystalline areas and a crystalline rash on the fracture of the armor in the first six months of the war. Previously, the standard was exclusively fibrous fracture. Despite this, the experts of the Armored Institute write in their conclusions that
the requirements for the quality of armor of hull parts are lower for the Germans than in the USSR. The samples under study have missing parts with a crystalline fracture and a wide range in the allowable hardness.
The Germans mostly used homogeneous armor of high hardness.
But heterogeneous case-hardened steel, difficult to manufacture, was in short supply and was used for shielding both the frontal parts of the hull and the turret.
Tests by fire
The shelling of captured tanks from heavy machine guns, anti-tank rifles and cannons showed that the quality of German armor was unsatisfactory.
The assessment was carried out in accordance with the Technical Specifications for Armor for Tanks adopted in the USSR. The claims in German steel were as follows - high brittleness and a tendency to form cracks, splits from the impact of shells and the presence of spalling from the rear.
High-hardness bulletproof armor was excellently penetrated by 12, 7-mm domestic bullets from DK (Degtyarev Krupnokaliberny). Especially effective is fire in long bursts, when breaks of 40-50 mm in size were formed on the armor. Fractures of the armor at the site of the holes showed very dry, fine-crystalline fractures, often even with metal delamination.
They also fired at the captured tanks at the range from an anti-tank rifle 14, 5-mm B-32 bullets. Conclusion - the gun is an extremely powerful tool for the destruction of light German armored vehicles.
A little about the vulnerable and strong parts of German armored vehicles of more serious dimensions. The forehead of the captured Pz. Kpfw.38 did not penetrate up to 45 mm shells, and the DK machine gun could only take the tank from behind. The real thunderstorm of the Czechoslovak machine was the 76-mm caliber - defeat from any angle.
Not the best quality armor was found on the captured T-III. If the 45-mm domestic anti-tank gun pierced the armor through and through, then spalls up to 3 caliber shells formed on the back side. Cracks were also forming, splitting parts into pieces. But the T-III still had to be pierced with that caliber.
The results indicate that the vehicle has a fairly satisfactory protection against 37-mm and 45-mm guns at heading angles of 25-45º. In fact, the T-III's hull sides, side and rear turret parts were vulnerable to these guns. 76-mm penetrated a German tank in any scenario.
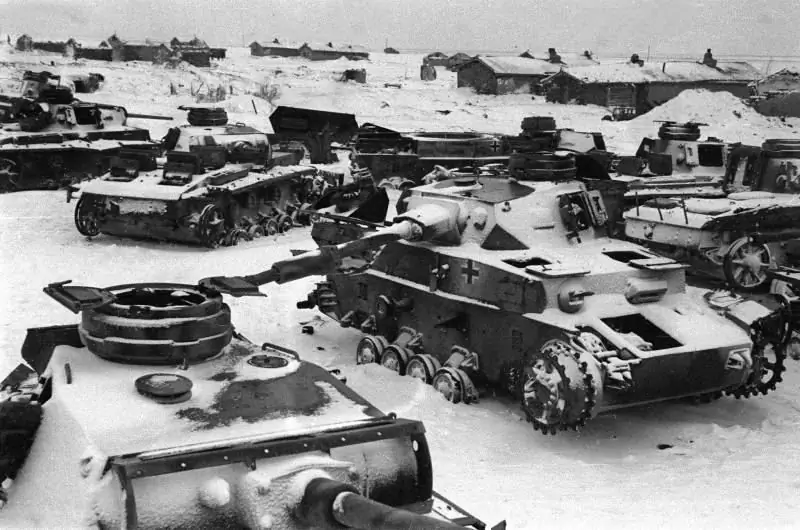
The "heavy" T-IV left the following impressions:
“The tank has a fairly satisfactory protection against a 37-mm projectile, which provides the ability to confidently maneuver within the range of directional angles of 0-30º. Within these limits of the course angles, the tank's armor reliably protects against 37-mm shells even at the shortest firing distances.
All side and stern parts are vulnerable to 37-mm shells. The most vulnerable are the unshielded part of the hull side and the upper rear part of the hull.
The tank's protection against 45-mm shells is less satisfactory, since the weakness of the unshielded part of the hull side deprives the tank of the ability to confidently maneuver under fire from a 45-mm cannon at the bow, the most important course angles.
The protection of the tank from a 76-mm projectile is completely unsatisfactory, since even its frontal parts can be penetrated by this projectile at a 45º heading angle from a distance of 1100 m, and at the same time, even a slightly lower heading angle, the tank already exposes a significant area of less protected parts under fire.
In the end, about the "Artshturm" self-propelled gun, the concept of which seemed to the Soviet engineers the most interesting.
Protection against 37-mm and 45-mm anti-tank guns is effective within the course angles of 0-40º.
From a distance of 1100 meters, the 76-mm Russian cannon penetrates the StuG III Ausf. C / D at a course angle of 15º.
At the same time, the TsNII-48 specialists advised fellow designers to adopt the layout of an unprecedented reckless tank.