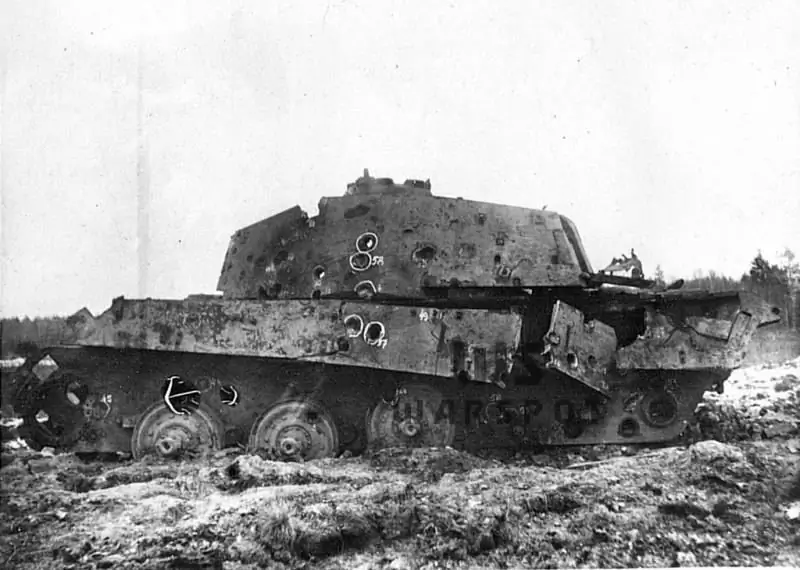
Research objects
The German tank building school, undoubtedly one of the strongest in the world, required careful study and reflection. In the first part of the story, examples of tests of captured "Tigers" and "Panthers" were considered, but domestic engineers also came across no less interesting documents, which could be used to trace the evolution of German technology. Soviet specialists, both during the war and later, tried not to let anything superfluous out of sight. After most of the tanks of Hitler's "menagerie" were fired upon from all sorts of calibers, it was the turn of a detailed study of the technologies of tank production. In 1946, engineers who were studying the technology for the production of tracked tracks of German tanks finished their work. The research report was published in 1946 in the then secret "Bulletin of the Tank Industry".
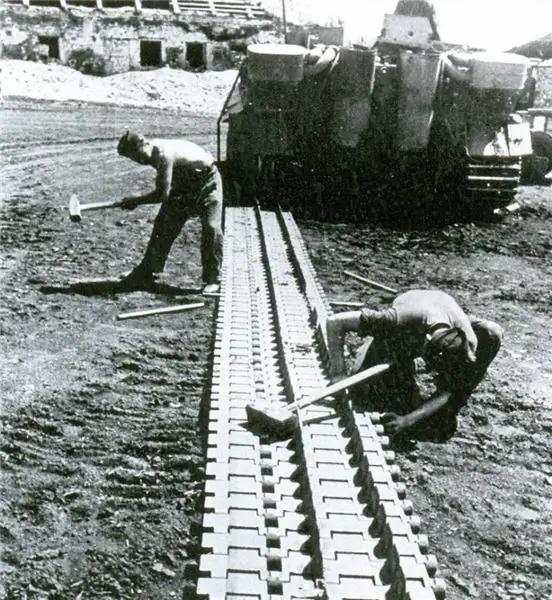
The material, in particular, points to the chronic shortage of chromium, which the German industry faced back in 1940. That is why in the Hadfield alloy, from which all the tracks of the tanks of the Third Reich were cast, there was no chromium at all, or (in rare cases) its share did not exceed 0.5%. The Germans also had difficulties with obtaining ferromanganese with a low phosphorus content, so the proportion of non-metal in the alloy was also slightly lowered. In 1944, in Germany, there were also difficulties with manganese and vanadium - due to overexpenditure on armored steels, so the tracks were cast from silicon-manganese steel. At the same time, manganese in this alloy was no more than 0.8%, and vanadium was completely absent. All tracked armored vehicles had cast tracks, for the manufacture of which electric arc furnaces were used, with the exception of monophonic tractors - stamped tracks were used here.

An important stage in the manufacture of tracked tracks was heat treatment. In the early stages, when the Germans still had the opportunity to use Hadfield steel, the tracks were slowly heated from 400 to 950 degrees, then for a while they raised the temperature to 1050 degrees and quenched in warm water. When they had to switch to silicon-manganese steel, the technology was changed: the tracks were heated to 980 degrees for two hours, then cooled by 100 degrees and quenched in water. After that, the track links were still smelted at 600-660 degrees for two hours. Often, a specific treatment of the track ridge was used, cementing it with a special paste, followed by quenching with water.
The largest German supplier of tracks and fingers for tracked vehicles was the company "Meyer und Weihelt", which, together with the Wehrmacht High Command, developed a special technology for testing finished products. For track links, this was bending to failure and repeated impact testing. The fingers were tested for bending to failure. For example, the fingers of the track links of the T-I and T-II tanks, before they burst, had to withstand a load of at least a ton. Residual deformations, in accordance with the requirements, could appear at a load of at least 300 kg. Soviet engineers noted with bewilderment that the factories of the Third Reich did not have a special procedure for testing tracks and fingers for wear resistance. Although it is this parameter that determines the survivability and resource of tank tracks. This, by the way, was a problem for German tanks: track eyelets, fingers and combs wore out relatively quickly. It was only in 1944 that work on the surface hardening of the lugs and ridges began in Germany, but the time was already lost.
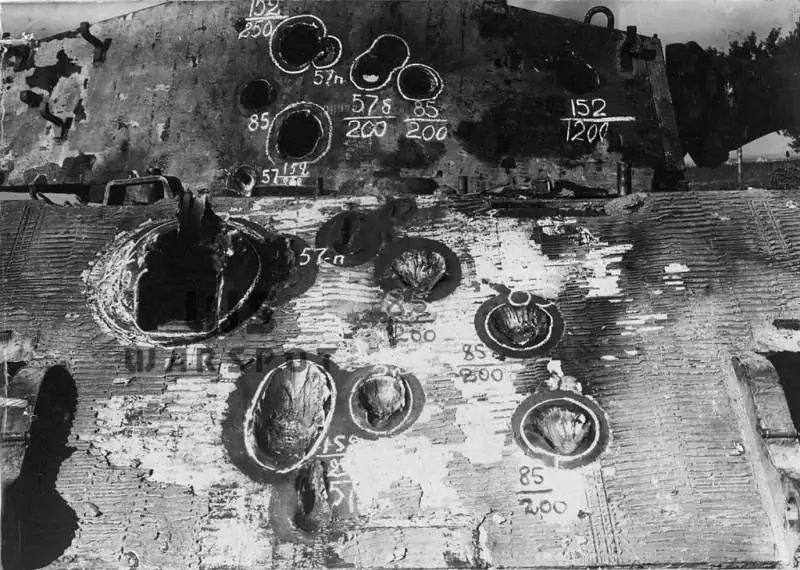
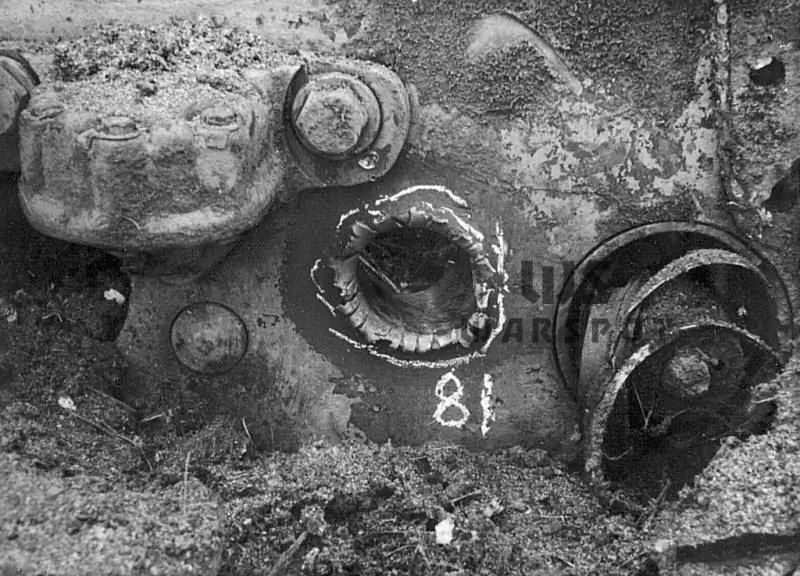
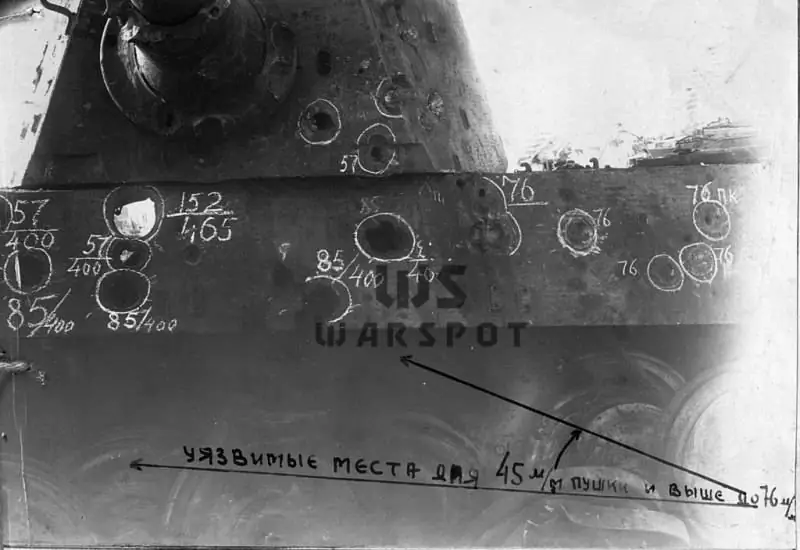
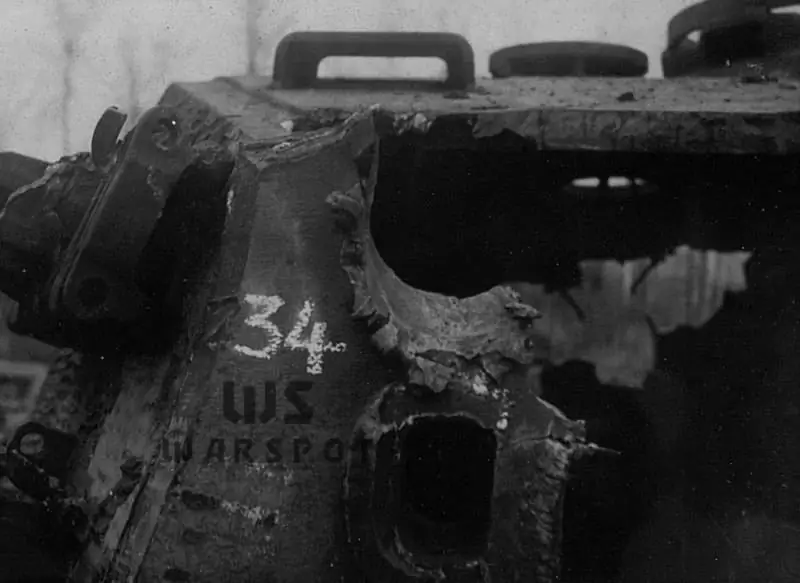
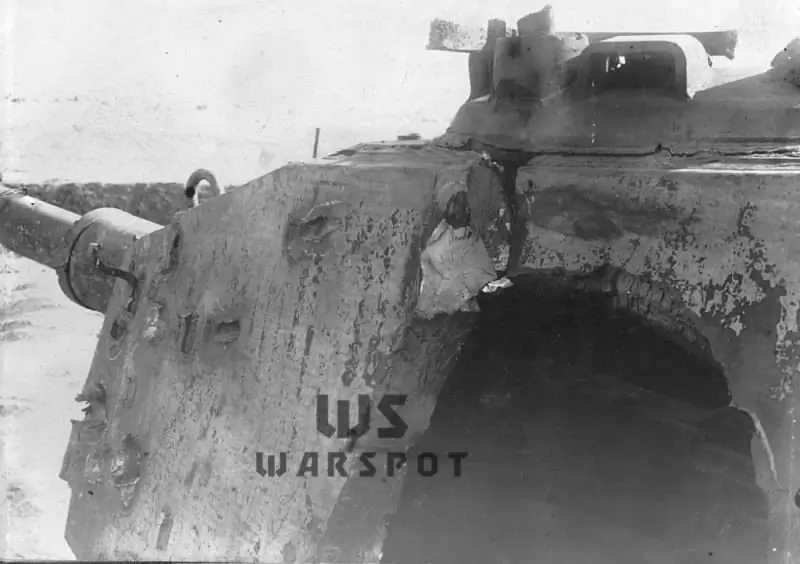
How was the time wasted with the arrival of the "King Tiger"? The optimistic tone that accompanies the description of this vehicle on the pages of the Bulletin of Tank Industry at the end of 1944 is very interesting. The author of the material is engineer-lieutenant colonel Alexander Maksimovich Sych, deputy head of the test site in Kubinka for scientific and testing activities. In the post-war period, Alexander Maksimovich rose to the rank of deputy chief of the Main Armored Directorate and oversaw, in particular, testing of tanks for resistance to atomic explosions. On the pages of the main specialized publication on tank building, A. M. Sych describes a heavy German tank not from the best side. It is indicated that the sides of the turret and hull are hit by all tank and anti-tank guns. Only the distances are different. HEAT shells took armor from all ranges, which is natural. The sub-caliber 45-57-mm and 76-mm projectiles hit from a distance of 400-800 meters, and the armor-piercing calibers 57, 75 and 85 mm - from 700-1200 meters. It is only necessary to remember that A. M. Sych does not always imply its through penetration by the defeat of armor, but only internal spalls, cracks and loose seams.
The forehead of the "Royal Tiger" was expected to be struck only by the calibers of 122 mm and 152 mm from distances of 1000 and 1500 meters. It is noteworthy that the material also does not mention the non-penetration of the frontal part of the tank. During the tests, 122-mm shells caused spalling on the back of the plate, destroyed the machine gun's course mount, split welds, but did not pierce through the armor at the indicated distances. This was not a matter of principle: the behind-the-barrier action of the arriving projectile from the IS-2 was quite enough to ensure that the vehicle was disabled. When the 152-mm ML-20 cannon was firing on the King's Tiger's forehead, the effect was similar (without penetration), but the cracks and parted seams were larger.
As a recommendation, the author proposes to conduct machine-gun fire and fire from anti-tank rifles at the observation devices of the tank - they were oversized, unprotected and difficult to replace after defeat. In general, according to A. M. Sych, the Germans hurried with this armored vehicle and relied more on the moral effect than on the fighting qualities. In support of this thesis, the article says that during production, the pipeline was not fully assembled to increase the ford to be overcome, and the instructions in the captured tank were typed on a typewriter and in many ways did not correspond to reality. In the end, the "Tiger II" is rightly accused of being overweight, while the armor and armament do not correspond to the "format" of the vehicle. At the same time, the author accuses the Germans of copying the shape of the hull and turret of the T-34, which once again confirms the advantages of the domestic tank to the whole world. Among the advantages of the new "Tiger" stand out a carbon dioxide automatic fire extinguishing system, a monocular prismatic sight with a variable field of view and an engine heating system with a battery for reliable winter start-up.
Theory and practice
All of the above clearly indicates that the Germans at the end of the war experienced certain difficulties with the quality of tank armor. This fact is well known, but the ways of solving this problem are of interest. In addition to increasing the thickness of the armor plates and giving them rational angles, the Hitlerite industrialists went to certain tricks. Here you will have to delve into the specifics of the technical conditions under which the smelted armor was accepted for the production of armor plates. "Voennaya Acceptance" carried out chemical analysis, determined strength and carried out firing ranges. If with the first two tests everything was clear and it was almost impossible to evade here, then the shelling at the range since 1944 caused a persistent "allergy" among industrialists. The thing is that in the second quarter of this year, 30% of the armor plates tested by shelling did not survive the first hits, 15% became substandard after the second hit by the projectile, and 8% were destroyed from the third test. This data applies to all German factories. The main type of marriage during the tests was spalling on the back of the armor plates, the dimensions of which were more than twice the caliber of the projectile. Obviously, no one was going to revise the acceptance standards, and improving the quality of armor to the required parameters was no longer within the power of the military industry. Therefore, it was decided to find a mathematical relationship between the mechanical properties of armor and armor resistance.
Initially, the work was organized on armor made of E-32 steel (carbon - 0, 37-0, 47, manganese - 0, 6-0, 9, silicon - 0, 2-0, 5, nickel - 1, 3-1, 7, chrome - 1, 2-1, 6, vanadium - up to 0, 15), according to which statistics were collected from 203 attacks. The slab thickness was 40-45 mm. The results of such a representative sample indicated that only 54.2% of the armor plates withstood the shelling at 100% - all the rest, for various reasons (spalling on the back side, cracks and splits), failed the tests. For research purposes, the fired samples were tested for rupture and impact resistance. Despite the fact that a connection between mechanical properties and armor resistance certainly exists, the study on the E-32 did not reveal a clear relationship that would allow abandoning field tests. The armor plates, fragile according to the results of the shelling, showed high strength, and those that did not withstand the tests on the rear strength showed a slightly lower strength. So it was not possible to find the mechanical properties of the armor plates, allowing them to be differentiated into groups according to armor resistance: the limiting parameters went far into each other.
The question was approached from a different angle and adapted for this purpose the dynamic torsion procedure, which was previously used to control the quality of tool steel. The samples were tested before the formation of kinks, which, among other things, indirectly judged the armor resistance of the armor plates. The first comparative test was carried out on E-11 armor (carbon - 0, 38-0, 48, manganese - 0, 8-1, 10, silicon - 1, 00-1, 40, chromium - 0, 95-1, 25) using samples that successfully passed the shelling and failed. It turned out that the torsion parameters of the armored steel are higher and not very scattered, but in the "bad" armor, the results obtained are reliably lower with a large dispersion of the parameters. A break in high-quality armor must be smooth without chips. The presence of chips becomes a marker of low projectile resistance. Thus, German engineers managed to devise methods for assessing the absolute armor resistance, which, however, they did not have time to use. But in the Soviet Union, these data were rethought, large-scale studies were carried out at the All-Union Institute of Aviation Materials, VIAM) and adopted as one of the methods for assessing domestic armor. Trophy armor can be used not only in the form of armored monsters, but also in technologies.
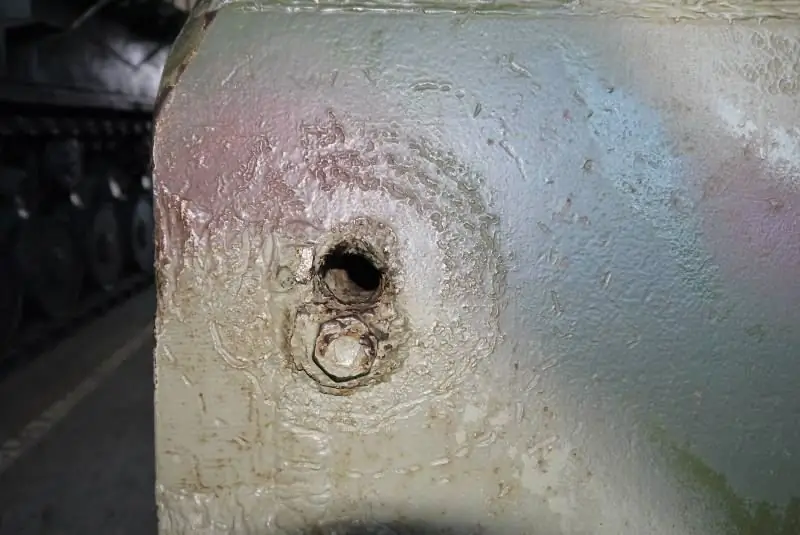
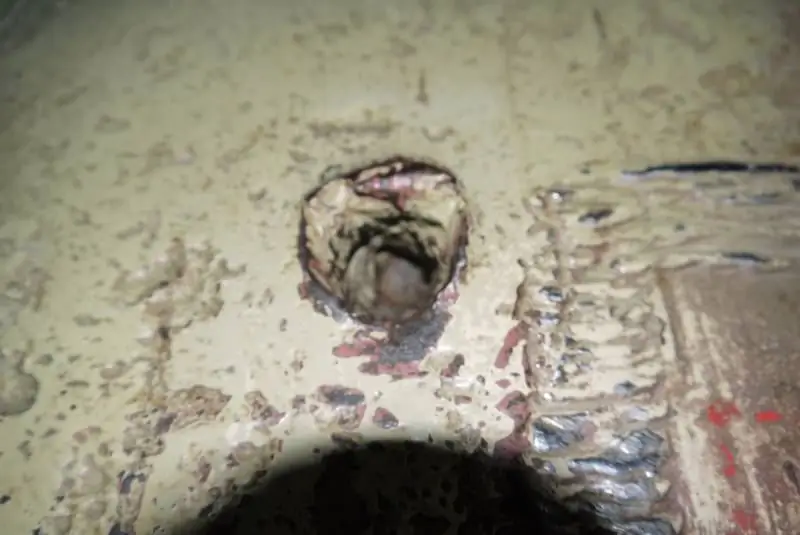
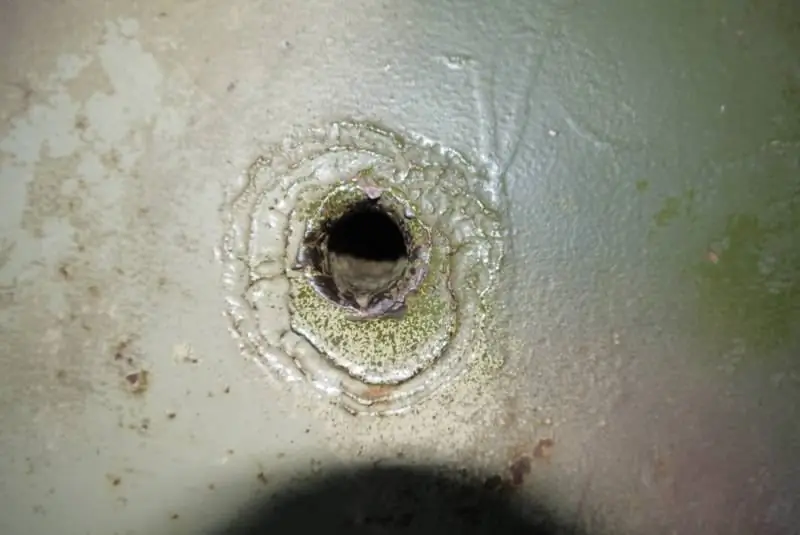
Of course, the apotheosis of the trophy history of the Great Patriotic War was two copies of the super-heavy "Mouse", of which at the end of the summer of 1945, Soviet specialists assembled one tank. It is noteworthy that after the study of the car by the specialists of the NIABT test site, they practically did not fire at it: obviously, there was no practical sense in this. Firstly, in 1945, the Mouse did not pose any threat, and, secondly, such a unique technique was of a certain museum value. The power of domestic artillery by the end of the tests at the test site from the Teutonic giant would have left a pile of wreckage. As a result, "Mouse" received only four shells (obviously, caliber 100 mm): in the forehead of the hull, in the starboard side, in the forehead of the tower and the right side of the tower. Attentive visitors to the museum in Kubinka will surely be outraged: they say, there are much more marks from shells on the armor of the "Mouse". These are all the results of the shelling by German guns back in Kummersdorf, and the Germans themselves fired during the tests. In order to avoid fatal destruction, domestic engineers performed calculations of the armor resistance of the tank's protection according to the Jacob de Marr formula with Zubrov's amendment. The upper limit was a 128 mm projectile (obviously German), and the lower limit was 100 mm. The only part that can withstand all these ammunition was the 200-mm upper frontal, located at an angle of 65 degrees. The maximum armor was at the front of the turret (220 mm), but due to its vertical position, it was theoretically hit by a 128 mm projectile at a speed of 780 m / s. Actually, this projectile, at different approach speeds, pierced through the armor of the tank from any angle, except for the frontal part mentioned above. A 122-mm armor-piercing projectile from eight angles did not penetrate the Mouse in five directions: in the forehead, side and rear of the turret, as well as in the upper and lower frontal parts. But we remember that the calculations are carried out on the through destruction of armor, and even a high-explosive 122-mm projectile without penetration could easily disable the crew. To do this, it was enough to get into the tower.
In the results of the study of "Mouse" one can find the disappointment of domestic engineers: this giant machine was nothing interesting at that time. The only thing that attracted attention was the method of connecting such thick armor plates of the hull, which could be useful in the design of domestic heavy armored vehicles.
"Mouse" has remained a completely unexplored monument to the absurd thought of the German engineering school.