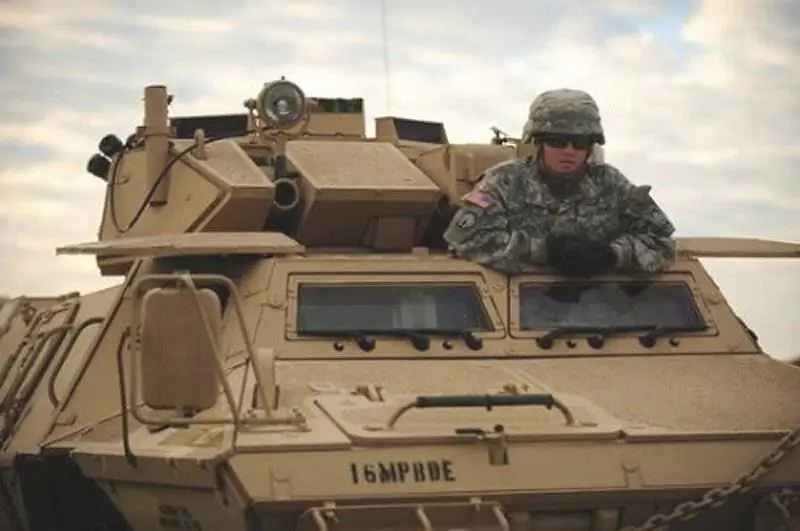
Modern AFVs, such as the M1117 ASV in the photo, are usually protected by the main structural armor of steel and aluminum, plus additional protection components made of various alloys, ceramics, composites, or a combination of these.
For the United States and its strategic partners, the need for improved defense and armor capabilities to meet current and anticipated tactical commitments is clear. The US-led multinational mission in Afghanistan, which is still striving for its logical conclusion, will benefit from the lessons learned in Iraq regarding the missions and requirements of protecting its troops and strategizing for new initiatives to develop defense systems
The Defense and Reservation System (SPB) (another term for Structural Defense) is a strategic tool because it has a noticeable effect on critical systems and resources and also has a direct impact on the fighter. This mainly applies to asymmetric operational environments in which threats to fixed positions and perimeter security, as well as dismounted troops and patrol vehicles, are particularly acute. While these engagements evolve rapidly, the presence of electronic warning systems, combined with effective defense solutions, can often give the military a decisive advantage, allowing them to survive, counterattack and dominate. Conversely, the absence of a suitable or effective infrastructure to defend their forces can leave both combatants and non-combatants vulnerable to ambush tactics, and this is one of the key, albeit sobering, lessons of modern operations in regional theaters of war.
Key aspects
Structural armor refers to those types of strategic materials that are resistant to ballistic attacks and that can be integrated into stationary, transportable or mobile transport systems and personal ballistic protection solutions. Traditional materials such as steel and aluminum or reinforced concrete, as well as advanced materials, including nanomaterials and ceramic composites, can be used in the production of SZB. Some examples of structural armor applications include the manufacture of permanent and temporary structures such as watchtowers, troop or security vans, vehicle protection systems, and combatant personal protection. The latter may include wearable shields or checkpoint protection systems and transportable armored combat positions.
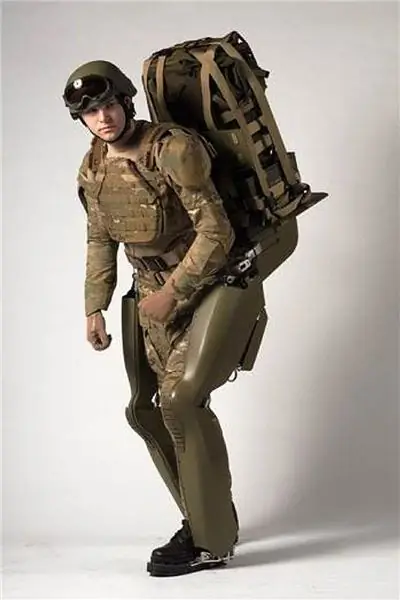
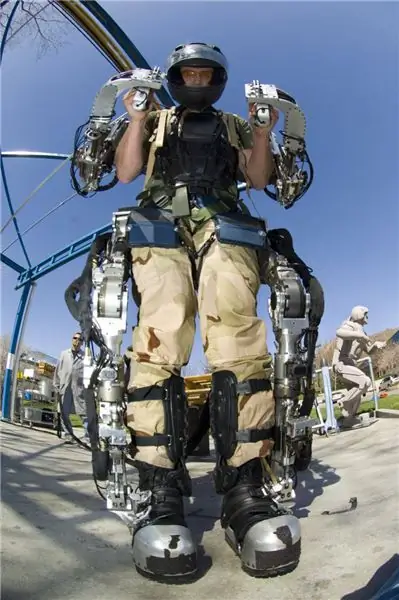
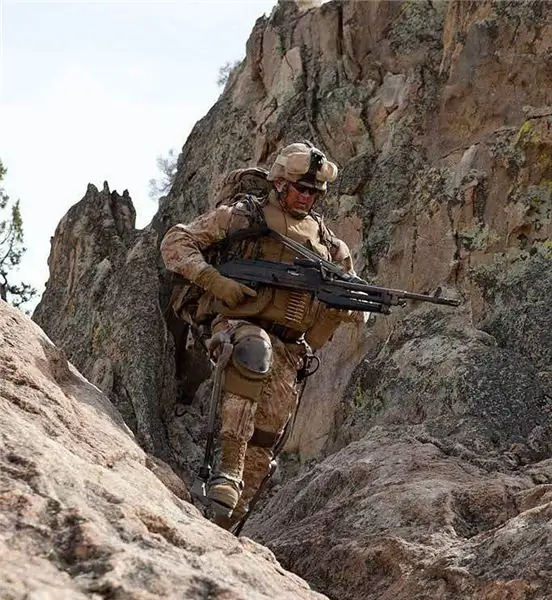
Three attempts to create an exoskeleton concept: projects BLEEX, Raytheon SARCOS and Lockheed Martin HULC
Consequently, Protection and Reservation Systems (SPB) can be of great help in increasing tactical and strategic survivability in combat and other high-risk environments. They are a key factor in programs to protect their forces. They are also the basis for countering many types of asymmetric attacks, such as roadside mines and RPGs during missions in urban environments and counterinsurgency operations. Since they can be created from lightweight composites and other advanced and exotic materials, they can also be useful in the area of signature management for protected infrastructures, such as covering vehicles with more masking materials from ground-based radars. In fact, we can say that the applications of SZB are very diverse - as well as the materials from which they can be made.
Some of the materials from which the SZB are formed can be classified as exotic and new materials, that is, those that have new properties in addition to the capabilities of traditional materials. For example, nanomaterials, including nanotubes and nanofibers, as well as advanced composite materials, can improve armor performance. Structures in suspected non-combat areas, which were previously viewed as having a low degree of defense for combat attacks, are now included in the SZB implementation plans. The 2012 National Defense Authorization Act, for example, provides for increased security standards in military building projects in the military construction, creation and modernization of existing infrastructure in the United States and NATO countries. In private sector construction, SOC requirements for new construction projects and renovation of existing buildings are also increasing due to safety, ergonomic and environmental considerations, as structural protection also has the ability to reduce noise and increase thermal insulation. However, the requirements for the protection of combatants remain one of the highest concerns for military planners.
The United States Corps of Engineers (USACE) is responsible for US government programs to build military, civilian, and national security infrastructure both globally and domestically. Perhaps the most famous project built by USACE, the Pentagon, stands as a reminder of the importance of SIS programs and their relevance to ongoing operations and national security and troop protection missions. Construction was completed in 1941, with a small amount of metal used due to a shortage of strategic raw materials during wartime, the Pentagon was built almost entirely of reinforced concrete. In the conclusion of the American Society of Civil Engineers' study of the condition of the building immediately after September 11, it was said that elements of the original design and construction of the Pentagon contributed to its resilience during the attack of the jet liner, they limited physical destruction and loss of life. The design characteristics of integrity, redundancy and energy absorption were highlighted in the group's report. It said that such elements "should in the future be included in the designs of buildings and other structures in which resistance to progressive destruction is considered very important."
Similar, if not identical, properties and requirements apply to fixed and mobile government structures at home and abroad, large and small, and should include security enhancements such as ballistic attack resistance as built-in structural elements to protect against realistically anticipated threats. Consequently, SZBs are of key importance across the entire range of military and civilian efforts and are likely to become commonplace in the future.
Rules of thumb for creating protection
Monolithic systems
The stronger the better, "adequate" strength will destroy the projectile
The tough the better, "adequate" toughness resists cracking
The thicker the better
The harder the better
One thick plate is better than two thin layered plates
The more the slope (angle of meeting) the better
Multi-material systems (hybrid)
Firmer is not always better, but a hard veneer is usually present
Toughness is not always better, but a tough base is usually present
Thicker is not always better
Harder is not always better
Two thin plates can be better than one thick
More slope is not always better
Adaptive benefits
Traditional armor materials have shown limitations in the face of new security challenges, while advanced materials, including composites and nanomaterials, have demonstrated significant advantages over older systems, increasing the survivability of the soldier even in extreme conditions.
The shortcomings of existing defense systems could be, perhaps, one of the legacies of the Cold War. Military doctrines of that time did not focus on military operations in built-up areas (English term MOBA - Mobility Operations For Built-up Areas) or military operations in urban conditions (English term MOUT - Military Operations in Urban Terrain). Likewise, the doctrines that emerged after the Gulf War were based on deployable high-tech, high-precision capabilities in shock and awe scenarios with a limited time frame. This, of course, did not happen in Iraq, where high-tech offensive systems and tactics were of primary importance in the early stages of the conflict, and the need to maintain the operational pace over a long period of time became critical.
SZBs provide advantages to forces involved in long-term operations at the theater or regional level, including those that occur in the context of MOUT campaigns. Many of these benefits, for example, in the protection of weapons and valuable objects in the presence of high risk, are obvious, some others are less obvious. These can include environmental and ergonomic safety issues and the hardening, sealing and protection of combat electronics and other critical information infrastructure from potentially damaging asymmetric impacts. However, SZB as a set of technologies will also have a broader meaning than even those that run through the entire field of defense technology. This is due to the fact that structural armor is a technology sector common to all branches of the military, which affects other defense applications and categories of military equipment, tasks and national security applications.
The above can be expanded. The SZB should be included in the requirements for the protection of nuclear and strategic facilities (due to its suitability for stationary, semi- and fully mobile systems under all combat conditions), the military and civilian sectors in non-combatant built-up areas (because buildings will benefit from security measures and new construction methods that increase resilience to terrorism and natural disasters such as hurricanes and earthquakes), modernization and initiatives to transform troops, combat electronics and data processing (due to its ability to enhance the protection of electronic infrastructure) and combat vehicles (due to their ability to create reliable ballistic protection for mobile personnel).
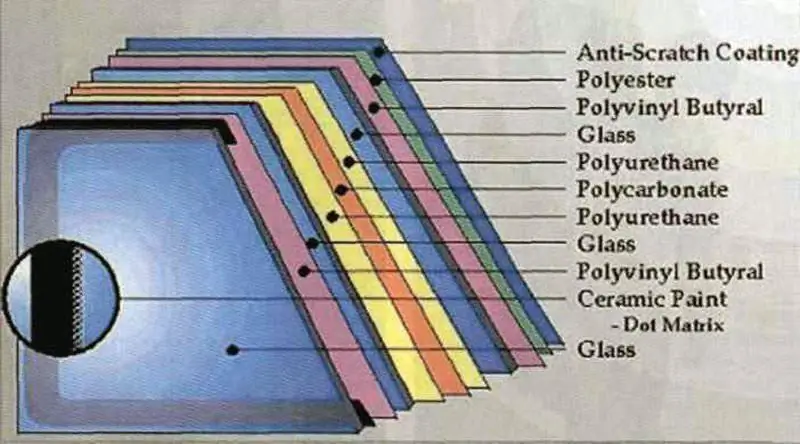
Structure of a typical sandwich panel of transparent armor
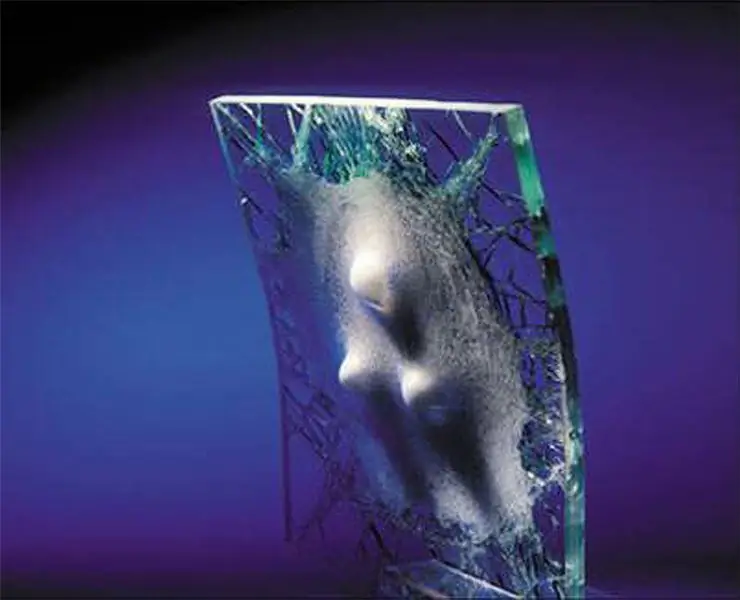
The glass structure used by most bulletproof glass manufacturers: first glass as the outer layer, several layers of glass and polyvinyl butyral in the middle, then polyurethane and finally polycarbonate. The advantages of this method lie in the ability of polycarbonate to expand and "catch" the debris formed by the harder glass surfaces. This expansion is possible over two inches.
NWBs are also aligned with budget reform initiatives. This is because some applications in this technology area allow for the modernization and refurbishment of existing facilities and systems at low cost and the creation of an entirely new infrastructure, which in turn allows for the benefits of a stable budget for other components of overall modernization programs and initiatives. For example, the US Department of Defense's 2010 budget allocated $ 1.4 billion for military development programs, $ 15.2 billion for troop protection initiatives (the largest single request after military intelligence spending), and $ 1.5 billion for combating IEDs (improvised explosive devices). SPBs can improve cost efficiency in these defense sectors. Consequently, it is a technology with potentially large payments for the development of programs for national and international security and the fight against terrorism, such as embassies and other long-term engineering projects, to protect VIPs and protect personnel involved in critical situations.
Other advantages of adopting SZBs and integrating them into the development of military programs include the fact that the materials themselves and the advanced methods of their production and subsequent processing and refinement share a common basic platform for development in the field of exotic and advanced materials, including nanomaterials. They can be embedded in the SZB in order to provide additional capabilities, such as an embedded sensor matrix and biometrics, which themselves become part of the protection system itself. A number of global initiatives are underway to develop structural protection, manufacture and design and use SSS, which use their unique set of characteristics for use in a variety of applications.
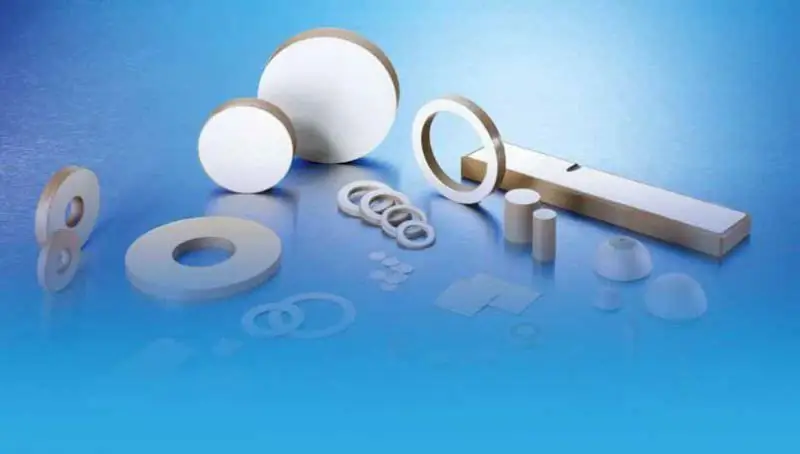
Piezoelectric components from Ceramtec
In the United States, materials for SZB and related processes are developed in the centers and services of the Department of Defense and private sector industry. Among the most important centers of ongoing R&D, it is worth noting the ARL military research laboratory, whose weapons and materials research department is engaged in protection initiatives in programs for a promising truck, weapon system and future vehicle. The University of Delaware Center for Composite Materials is also conducting DOD-funded research on advanced shielding materials, and other SZB development centers will be highlighted.
Advanced nanomaterials
Structural protection can be made from a variety of materials using an expanded range of advanced design, fabrication and molding techniques. The pace of material development is one of the fastest in defense technology and applied sciences, driven by strategic challenges. This applies to the discovery of new materials, as well as to continually improving the use of existing defense-valued products that are suitable for transformational development in the defense of their forces.
Nanomaterials have found widespread use in development programs in this application sector, and many revolutionary fabrication processes are under development or have gone into industrial production. At the forefront of advanced materials development is graphene, first discovered in 2004, a graphite homologue whose unusual characteristics make it promising for a number of applications, including the potential use of structural protection. Graphene is a sheet of graphite just one atom thick, making it thus the thinnest material discovered to date. Due to the fact that it is about two hundred times stronger than steel, graphene is also one of the most durable materials ever created in the laboratory. Graphene also has unusual electrical conductivity properties, which heralds revolutionary applications in semiconductor microprocessors. This makes graphene a material with great potential in several key technology areas. However, although all this is promising, the use of graphene for the development of military programs still remains in the future due to the lack of applied research on this very new material, the difficulties of producing in industrial quantities while maintaining high profitability.(For "advanced experiments with two-dimensional material - graphene" A. K. Geim and K. S. Novoselov were awarded the Nobel Prize in physics for 2010).
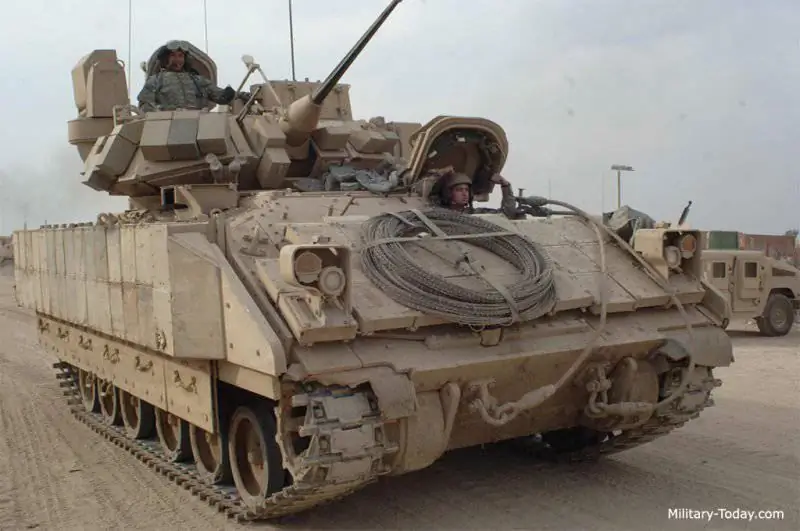
The M2 / M3 BRADLEY BMP uses 7039-T64 (upper half) and 5083-H131 (lower half) aluminum alloy armor. However, combat experience in Iraq led to increased protection due to an additional layer of armor made of multilayer steel plus elements of passive (compositional) and reactive armor, which we see in the photo.
However, carbon nanotubes (CNTs) are much better known in the field of research and development initiatives and have already found numerous practical applications not only in the military field, but also in the field of national security and law enforcement. Advanced armor materials from long carbon nanotubes can be made in a variety of shapes and structures, including sheets, fibers, plates, and molded shapes. The final "nano-improved" materials are lightweight but extremely durable, and their electrothermal properties can be changed during the manufacturing process. When fabricating composite structures, CNT-based armor provides a flexible, lightweight solution that provides superior protection against ballistic attacks on vehicles and other fixed or mobile combat infrastructure. Under the existing contract with the Natick Labs laboratory, Nanocomp Technologies has developed composite panels based on CNT just a few millimeters thick for personal protection of personnel, they stop a 9 mm bullet at close range.
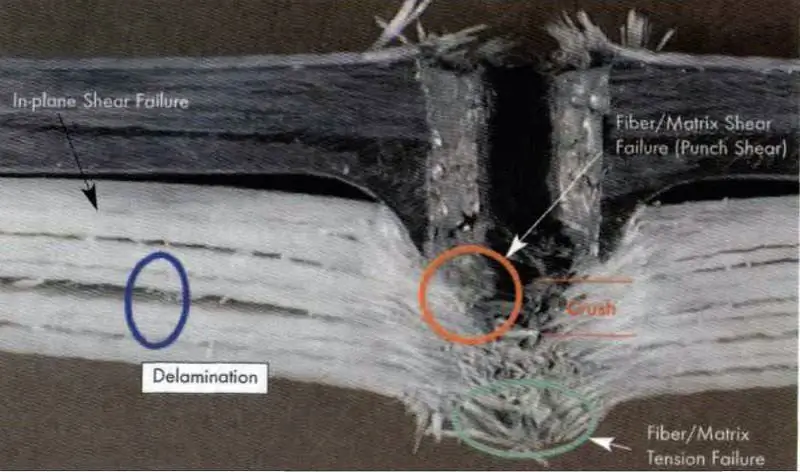
Damage when punching a composite material
Composite materials
Somewhat similar to metal alloys, composite materials differ essentially in that they are insoluble in each other and can be formed from the constituent materials in other ways than elements or mixing of metal phases. However, like alloys, composites can be formed from two or more components, which can vary significantly in shape or structure. Composite materials can be made according to a wide variety of processes. These include new bonding techniques such as lamination, sandwiching, sintering, particle injection molding, fiber weaving, and nano-manufacturing techniques such as microcompression. When manufactured as ballistic protection systems, they are classified as composite structural armor (CSA) and form a number of new materials such as metal intermetallic laminates (MIL) and ceramic matrix composites (CMC).
Ballistic composites are typically manufactured as honeycomb structures and laminates of thick walled composite, rubber and ceramic layers that are combined to provide an optimal balance of structure and ballistic performance with minimal weight. Among these laminates are opaque, translucent and transparent armor composites that are used as an explosion-proof glass replacement for vehicles. Epoxy fiberglass and fiberglass composites provide excellent protection for vehicles in combat areas where the risk of IED attacks is very high. Aluminum foam with closed cells CCAF (Closed-Cell Aluminum Foam) has a low weight combined with high strength, stiffness, absorbs energy well, its manufacturing characteristics can be different due to the structure of the microstructure that forms them. When ballistic, CCAF exhibits significant non-linear deformation and stress wave attenuation. Composite armor panels containing CCAF can withstand the impact of 20mm fragmentation shells, according to information provided by the American laboratory ARL.
Ballistic composites in this category are suitable for vehicle explosion protection, such as ballistic shielding for MRAP vehicles deployed in urban combat environments. They can also be used in other areas, such as cannon barrels. They are often made in the form of cover plates or panels that are installed inside and outside protected machines as bottom plates, spall guards and linings. Ceramic composites can be made in the form of structural armor with good anti-explosion and anti-fragmentation characteristics (many secondary fragments and debris). This makes ceramic composites well suited for structural armor applications, especially for MRAP and other small and medium-sized combat vehicles, whose design should be a compromise given the weight constraints due to the fact that heavy armor has a negative effect on vehicle mobility. However, larger vehicles, including tactical trucks and armored vehicles (such as the Rhino Runner armored bus), are better candidates for integration with standard metal armor solutions.
When incorporated into advanced composites of nanomaterials, the resulting nanocomposites can provide additional levels of performance or protection over unreinforced materials, or the same levels while decreasing mass. Polymers and monomers, including plastic polymers, can also be manufactured for use as advanced composite materials for structural protection applications. One characteristic of nanopolymers implanted with nanoparticles - that the wavelength is less than the wavelength of visible light (about 400 nanometers) - suggests that the finished materials can be transparent. Several types of such polymerized strategic materials have been manufactured with similar characteristics. Obviously, these properties are strategically valuable when modifying or replacing traditional bulletproof glass in combat and security vehicles.
SmartArmour is a multi-layer, multifunctional reservation system manufactured by SmartNano Materials of Piano, can be supplied transparent or opaque to the end-user specifications, it can withstand armor-piercing bullets, blast wave, shell fragments and detonation at IEDs. However, Vitreloy zirconium and beryllium metal glass is also manufactured with similar properties by Amorphous Technologies International. ARL's RDECOM R&D Center has developed a liquid armor for ballistic protection based on a shear thickening fluid of solid silica nanoparticles suspended in polyethylene glycol; it has been successfully tested on body armor with Kevlar.
Device-processing is the saturation of structural armor materials with nanostructures that can combine high-performance semiconductor processors into armor elements. Such "smart materials" can be built into armored walls, an example of the use is piezoelectric. They are natural materials that emit electrical impulses when shaken, deformed or compressed. Piezoelectrics, previously commercially used in turntable needles, can be embedded in armor structures, such as panels, modular elements, and installed in load-bearing walls in the form of thermal, vibration and shock sensors.
In a project funded by the US Department of Energy and carried out by the Berkeley laboratory at the University of California, state-of-the-art piezoelectric materials based on piezoelectric materials with a perovskite crystal structure are being developed. However, Accellent Technologies, a Minneapolis-based defense firm specializing in structural monitoring, has developed a hardware and software suite called the SMART Layer that combines sensors into structural components such as panels and walls. The company's system uses embedded multisensors that use microprocessor-based thermal, tensile and fiber-optic sensors to detect changes in the integrity of observed structures using a proprietary active scanning method. Diaform Armor Solutions, a division of Ceradyne Inc., has created lightweight structural armor solutions using thermoplastic composites to rapidly fabricate three-dimensional structural shapes that can form modular elements of reinforced structural assemblies.
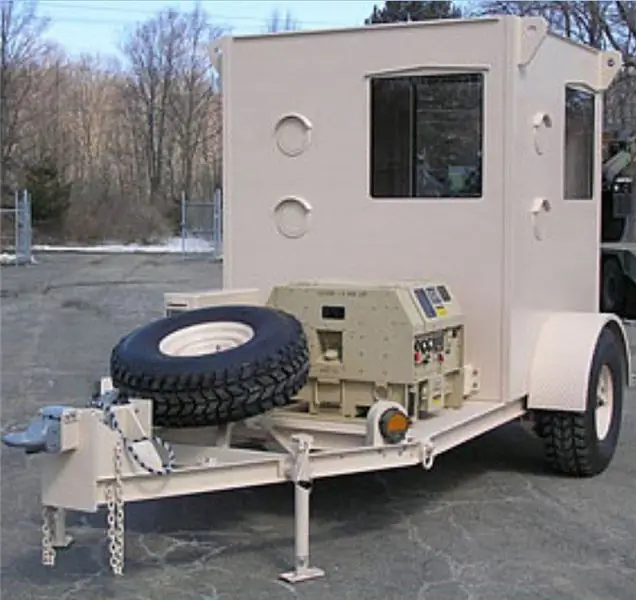
Bulletproof Protech Security Module
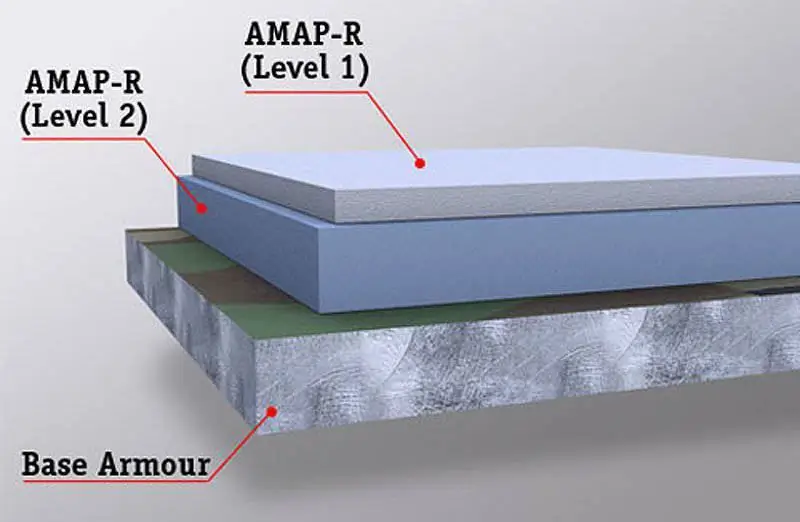
IBD Deisenroth Advanced Multi-Layer Armor Concept
Modular design elements that meet the ballistic armor matrix (BAM) standards are also widely used in new designs, additions and modifications to existing structures, where the most important characteristics are increased safety and resistance to ballistic attacks. The BAM specification, patented by Antiballistic Security and Protection (ASAP), Inc, describes multi-layer armored structural elements, such as walls, ceilings and floors, composed of layers of hard sheets of aramid fiber and hardened tool steel (for example, Thermasteel, manufactured by Thermasteel Corporation), or hardened steel mesh. BAM specifications include BAM-1, BAM-1A, and BAM-8; each of them describes increasing levels of structural protection. Zagros Construction has developed its wall system, ThermalBlast, which the company says is highly resistant to ballistic attacks and force incursions. It uses the patented BAM-8 system consisting of a protective, lightweight bulletproof inner wall (or BAM Inner Matrix), partly composed of ballistic Kevlar, which can also be incorporated into ceilings and floors and other ThermaSteel panels. The company recommends its ThermalBlast system for embassies, governments and post offices, military installations, ammunition depots and other critical facilities. US Bullet-proofing manufactures its range of bulletproof steel panels as a single ballistic sheet solution, which the company assesses to meet NIJ Armor Level IV.
SZB materials are also used in some offensive systems, such as the linings of missile silos and launch tubes and containers carried on mobile anti-missile launchers, which require good thermal abrasion and kinetic shock resistance characteristics. The HyperShield system, developed by the American company V-System Composites, which uses integrated armor tiles and advanced composite structures, is a low-cost, lightweight bulletproof armor solution and has an NIJ Level III protection level for missile defense, which also includes transport vehicles and ballistic requirements for aircraft. A buried nuclear warhead, such as the American B-61, can also use structural armor materials, while nuclear munitions intended for ground detonation in the so-called "carpet bombing", such as the American B-53 bomb, will also require armoring of the shell. from shock loads.
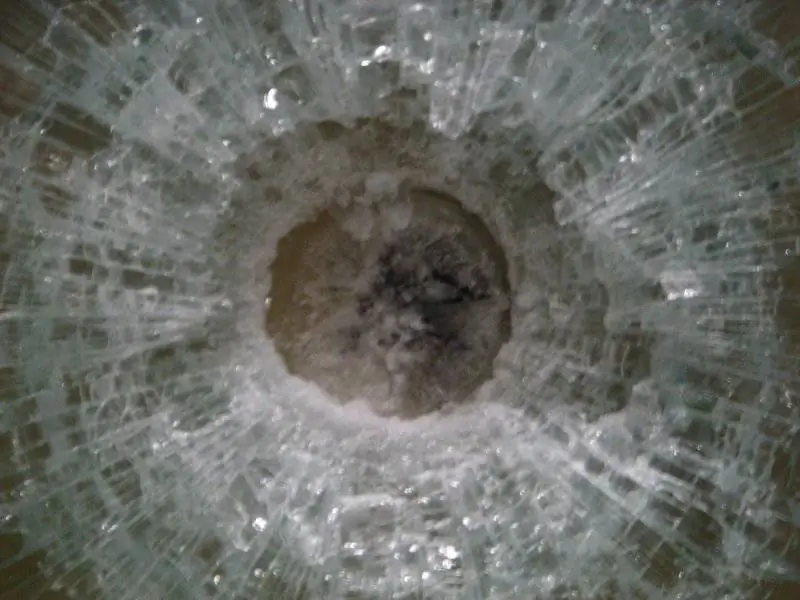
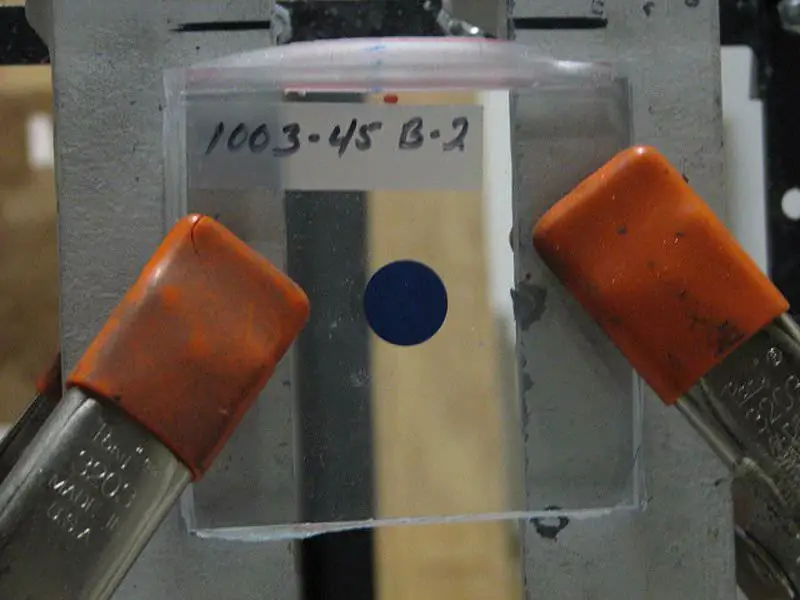
Frontier Performance Polymers, with the support of Army Center Natick, has successfully developed breakthrough polymer technology and an innovative manufacturing method for lightweight, transparent armor to protect the eyes and face. This material with a basis weight of 0.16 kg / cm2 has the same ballistic characteristics as the aramid / phenolic materials used in military helmets, but costs 10 times less
Traditional materials
However, the traditional materials used in the manufacture of protective structures, such as unalloyed steel and reinforced concrete, are by no means materials of the past. Metal alloys in particular remain the preferred materials due to their proven shielding properties and existing manufacturing facilities for their production and defense applications. These so-called “tough” armored solutions not only apply to ballistic steels and strategic alloys, but also to advanced composite materials with good ballistic properties. This also applies to types of armor made of or reinforced with fiber, or tightly woven mesh. As a structural armored material, concrete has the desired characteristics and continues to be widely used while having a low manufacturing cost.
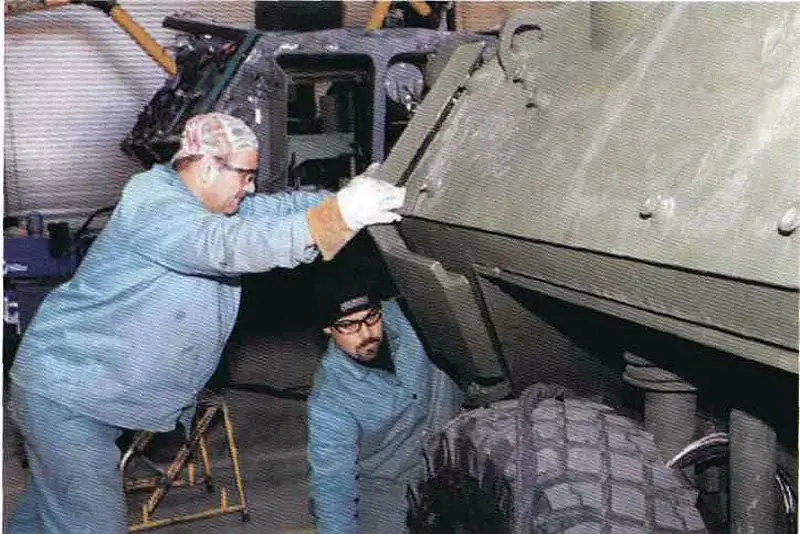
The US Marine Corps LAV 8x8 is receiving additional composite armor elements over its aluminum alloy hull as part of an ongoing modernization program.
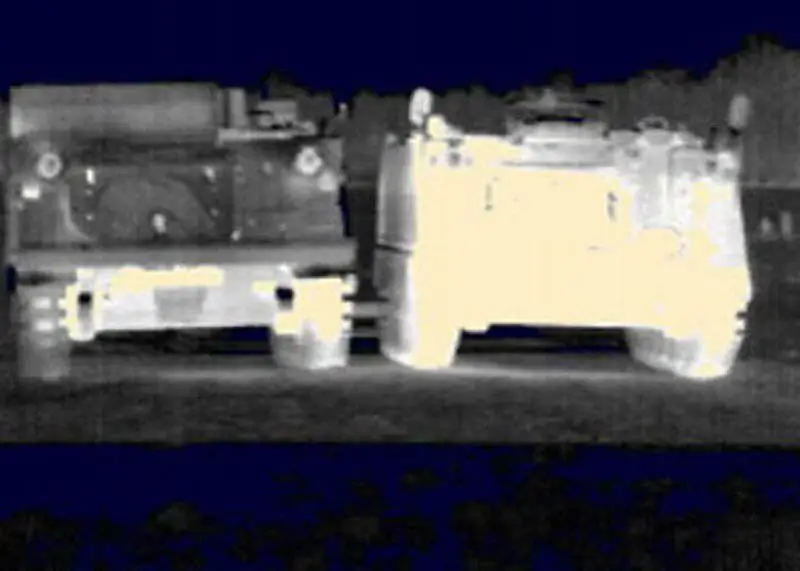
Armored material from AMAP-S IBD Deisenroth serves an important support function in reducing the vehicle's thermal signature
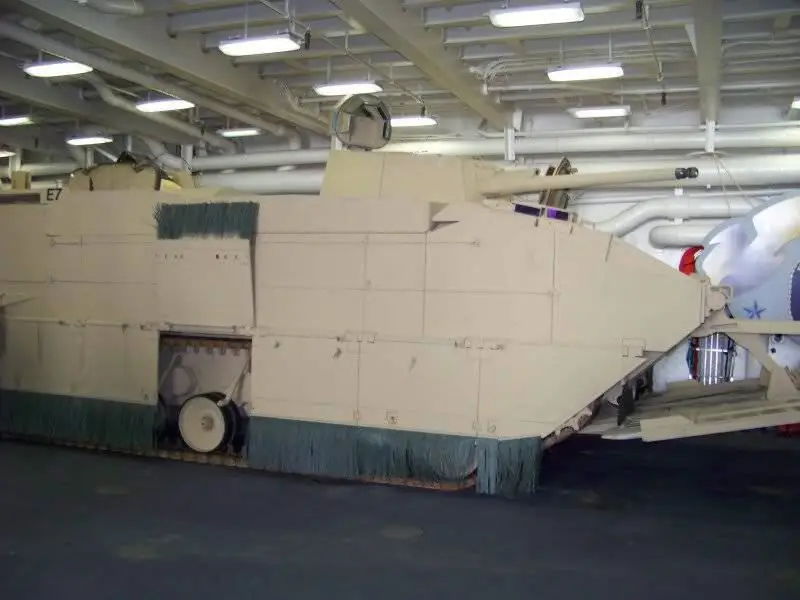
Expeditionary fighting vehicle EFV (Expeditionary Fighting Vehicle) of the Marine Corps is the first armored fighting vehicle, which used armor 2518-787, an alloy of aluminum, copper, manganese. Although this alloy is tough and has good ballistic properties, it has poor ballistic toughness in conventional butt welds. This forced the manufacturer to exclude butt welds and main fillet welds from the structure in order to increase impact resistance, the plate to the plate is now mechanically attached. In the end, many problems with this program prompted the closure of this promising project.
Alloys are some of the toughest materials from which structural armor can be made. Alloys are a combination of two or more chemical elements - metals (or metallic and non-metallic elements), usually "fused" together or dissolved in each other during the melting process. The result is a material with better performance than each component individually. Titanium and titanium alloys are common structural armor elements. Their use includes "traumatic" plates in personal booking systems, which provide a high degree of protection for highly vulnerable areas of the body. Beryllium-aluminum alloy has also been shown to be successful in many cases. The particular strength and stiffness of this alloy surpasses those of conventional titanium alloys, resulting in lower structural weight and improved performance. Armor steels are also strategic materials suitable for structural armor.
A number of so-called "superalloys" or "high performance alloys" have also been produced commercially under the brand names. Among them is the high-strength Hastelloy alloy, whose main component is a transition metal - nickel; Kovar, a cobalt-nickel alloy prized for its excellent coefficient of thermal expansion; nickel-copper-iron alloy Monel; and nickel-chromium alloy Inconel.
Laser hardening is one of the processing processes that enhances the functional characteristics of base metals and alloys. There are other types of property enhancements, including microcompression, a processing process that uses a focused ion beam technique to saturate advanced materials with substructures for added strength and durability. Superplastic shaping is also used, resulting in metal and ceramic products with extremely high tensile strength.
The NETL (National Energy Technology Laboratory) laboratory of the US Department of Energy received an assignment from the Tank-Automotive and Armaments Command (TACOM) and the ARL military research laboratory to carry out a program to develop a cast steel armor plate for American military vehicles, including the BRADLEY BMP. On it, the NETL-TACOM-Lanoxide Corp and DARPA jointly developed a cast hatch, and a side effect of the program was the receipt of patch armor. Later, under the program, a titanium armor plate (using the Ti-6Al-4V aviation alloy) was developed for the M-1A1 ABRAMS MBT hatch in collaboration with TACOM and the main contractor General Dynamics. More recently, NETL has developed high-strength AFV armor using sintered titanium powder alloys to increase the strength of the final material. The armor materials made from silicon infiltration (SiSiC) and sintered silicon carbide (SSiC) are products of CeramTec of North America from New Jersey, the American division of the German company CeramTec AG. These materials demonstrate good chemical thermal stability and high resistance to tribological stress (tribology is a scientific discipline that studies the friction and wear of machine components and mechanisms in the presence of lubricants).
Ohio-based AT&F Advanced Metals of Orville is a privately held company that specializes in the fabrication and processing of durable metals and alloys, including titanium, zirconium, niobium, nickel alloys and duplex stainless steel, serving civil and defense customers. Even more specific is the Steel Solutions and Nuclear division of this company. It also manufactures materials for SZB based on high strength low alloy steel, carbon steel, steel based alloys. The company also provides structural armoring for nuclear facilities, including reactor internals and containers for nuclear waste.
Other programs
Other SZB programs are being conducted across the full spectrum of deployed forces and a multitude of global military operations. Their immediate demands and missions are directly related to the current and future protection of their communications forces, as these areas of application cover ballistic protection of vehicles, modernization of the soldier as a system, and contribute to the survival of military infrastructure against various asymmetric threats commonly encountered in regional peacekeeping operations.
Advanced armoring of vehicles, military and government installations, and military personnel deployments on the front lines and in the rear will only benefit from deployed capabilities. While many applications are improvements and upgrades to existing capabilities and systems as such, such as new types of additional armor for combat vehicles to protect against IEDs, others are innovative and future-generation systems.
The German company IBD Deisenroth Engineering AG manufactures the AMAP High-tech Survivability Enhancement System. It is a range of structural armor solutions using multiple manufacturing methods and advanced materials, including high strength alloys and composites. Among them is the AMAP-IED, which combines ceramic armor and anti-fragmentation lining technology and which can be supplied as modular elements and which is designed to increase the protection of military vehicles. IBD calls the AMAP-IED a next generation protection system and classifies it as protection against fragments of artillery shells up to 155 mm in caliber, as well as roadside mines and IEDs. AMAP-T is a transparent armor made using ceramic glass, which the company describes as having superior transparency and extreme durability, meeting STANAG Levels 1 to 4.
Vehicle roof protection is provided by AMAP-R and AMAP-ADS, which are weapon-optimized materials, the former made from ultra-light composite materials suitable for vehicle roof armor. The most interesting armor solution is the AMAP-S. Optimized for ballistic protection and signature management, it reduces the signature of military vehicles when scanned by reconnaissance sensors in the visible, infrared, radar and acoustic spectra. These materials can be used as a complement to existing machine bodies, that is, they can be installed on new models or machines already in service.
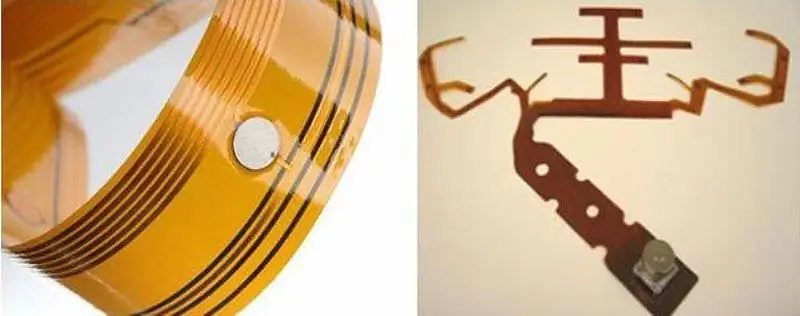
Accellent SMART Layer Sensor Tapes Samples
The BAE division of the American corporation ProTech offers a range of structural armor solutions that include several types of bulletproof fences and armored combat positions, including armored booths and guard towers, mobile safety fences and vehicle-mounted protection systems for tower-type soldiers. Stationary solutions for structural armor of this company are represented by a number of prefabricated armored fighting positions AFPS (armored fighting positions), which are able to protect against bullets of caliber 9 mm - 12.7 mm. Other AFPS solutions from ProTech include transportable armored structures optimized for perimeter and checkpoint security, vital asset protection, guardhouse security and border checkpoints.
ProTech also manufactures modular systems that can be designed according to end-user specifications. Similar systems, based on transportable armored containers manufactured by EADS, have been developed in cooperation with KMW under a contract with the German Federal Defense Procurement Agency. An armored container system called TransProtec, which can accommodate 18 people, including equipment, is optimized to protect ground forces from IED attacks, sniper fire, shrapnel, mines and weapons of mass destruction and is currently in service with the Danish and German armies, in the latter the system is called MuConPers (universal container for transporting people).
Plasan North America, a division of Israel's Plasan Sasa, has also developed structural armor solutions under a multi-million dollar contract with the US Department of Defense for the protection of new MRAP vehicles. According to the contract, Plasan is the main contractor in the joint production program with BAE Systems as a subcontractor for the supply of reservation systems for Oshkosh M-ATV machines, most of which work in Afghanistan under a contract with the TACOM command of the American army. Plasan is a world leader in the design of complementary armoring systems and under-blast protection systems for the protection of tactical vehicles in the military and civilian areas.
Advanced soldier protection systems fall within the realm of structural protection applications and include mechanically powered combat exoskeletons. They promise to have a significant impact on ground combat operations if such systems reach their full potential. Several major DOD and private sector technology development program initiatives are currently open in the United States. One of these programs is carried out by the US Army's Natick Labs Research Center for Soldiers Development according to the Future Warrior Concept, which provides a fully integrated system for the soldier, which includes six main subsystems. NSRDEC (MIT's Natick Research Center for Soldier Nanotechnologies) and the Soldier System Integration Lab (SSIL) are also working on these programs. The ultimate goal of SSIL is to develop what SSIL calls a 21st century combat suit. which combines high-tech capabilities with low weight.
The Berkeley Robotics and Human Engineering Laboratory (BLEEX) has developed a prototype of a self-propelled exoskeleton consisting of two anthropomorphic powered legs, a propulsion system, and a backpack-type frame on which various cargo. The exoskeleton allows the user - or "pilot" - to carry extremely heavy loads while facilitating walking and running up and down inclines throughout the range of normal travel without the use of physical force by the operator.
The Raytheon Sarcos initiative is in progress at the Raytheon plant in Salt Lake City. It represents more ambitious work to develop a soldier's exoskeleton, which Raytheon claims is essentially a wearable robot that increases wearer strength, endurance and mobility. The XOS exoskeleton, which dates back to the original experimental system developed by Sarcos, currently allows the pilot to lift loads up to 200 pounds and perform high-effort tasks such as climbing stairs and inclines without fatigue, but is currently hydraulically driven. requires a stationary external source of energy for itself. It also introduces Lockheed Martin's HULC exoskeleton program, which is also designed to carry 200 pounds of loads at any time and in any terrain, and is designed to be fully hydraulic and does not require an external power source. The HULC system includes an onboard microprocessor connected to sensor interfaces, which allows the exoskeleton to sense the pilot's intent and move in conjunction with it. The HULC system is highly modular, allowing for quick and efficient field replacement of major components, and is energy efficient in design to enable battery operation during extended missions. However, the HULC, like the exoskeleton from BLEEX, is conceived more as a system for carrying loads, rather than replacing the natural physical capabilities of a soldier. Currently under development by the Japanese company Cyberdyne of Ibaraki, HAL (Hybrid Assistive Limb) is an overall powerful system designed to increase a person's physical strength from two to 10 times. Despite the appearance of "Iron Man", its adaptability to future military tasks remains in question.
Further actions
In summary, an important mission for SZB can be broadly defined as reducing vulnerability to hostile actions, especially ballistic attacks, for which many, if not all, traditional materials currently do not provide adequate levels of troop protection.
Combat often teaches commanders harsh lessons that have seemed obvious in the past. One of the hardest lessons of modern warfare is the inadequacy of armor protection to improvised threats, which include suicide car attacks on military and civilian targets and IED attacks on transport and theater personnel. Old habits, especially military habits, die off especially hard. But historically, these habits tend to disappear under the pressure of combat, such as French cavalry versus English bows during the Hundred Years War, or the inadequacy of Soviet-style Iraqi armored vehicles to attacks from precision guided munitions and more advanced MBTs during the Gulf War.
Responding to challenges quickly and with appropriate countermeasures is the key to military success and security stability. So, if they are taken seriously when it comes to troop protection and are a major defense issue in this transformational era of power restructuring, then structural protection and SZB using this technology should become a defense procurement and R&D priority for all military leaders. Today's asymmetric threats to military and civilian infrastructure, as well as asymmetric combat in regional combat operations, affect defense policy development and systems design and procurement globally. This is as it should be in the predictable future.
Such armored military systems were mainly seen as complements to other priority solutions, and not as an integral part of many and most combat systems. But everything is changing. Protection and armor systems represent great potential and enhance capabilities in 21st century operations. Their use will expand and become the standard for many, if not most, defense systems at all levels.