Sikorsky S-69
Despite the failure in the competition for the creation of a new attack helicopter capable of developing high speeds, the Sikorsky company did not stop researching the topic of rotorcraft. The main goal of new research was to solve the problem of helicopter movement at high speeds. The fact is that when a certain flight speed is reached, the extreme parts of the rotor blades begin to move at a supersonic speed relative to stationary air. Because of this, the bearing properties of the propeller are sharply reduced, which ultimately can lead to an accident or even a catastrophe due to the loss of sufficient lift. Work in this direction is called ABC (Advancing Blade Concept). Over time, several other firms and organizations have joined the ABC program.
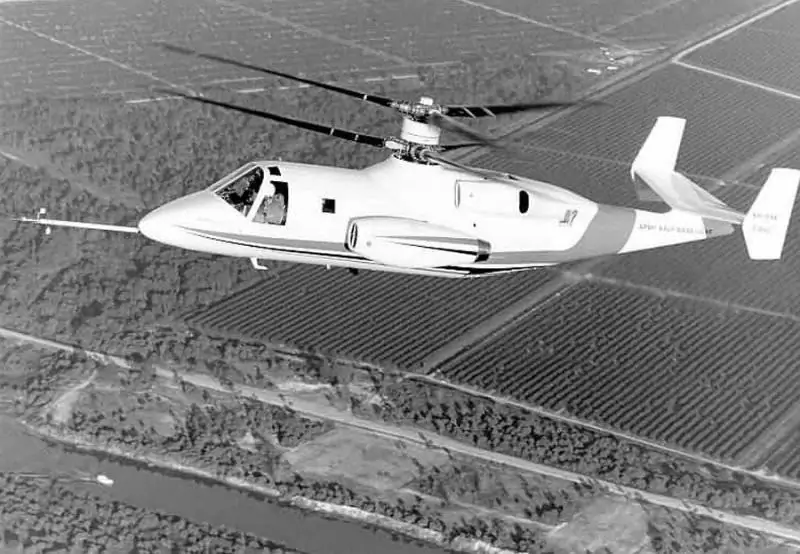
In 1972, the ABC program reached the stage of creating the first flight prototype. By this time, Sikorsky had completed the design of the S-69 experimental aircraft. To minimize the consequences of the high speed of the blades relative to the air when flying at a horizontal speed of more than 300-350 kilometers per hour, the company's engineers have found a relatively simple and original solution. Previous rotorcraft, built in different countries, for the most part were not equipped with a full-fledged swashplate. It was understood that such machines should change the pitch of all blades at the same time and at the same angle. This technical solution was explained by the possibility of simplifying the design and the presence of additional propellers that ensure horizontal flight. However, in the course of numerous theoretical calculations and blowing in wind tunnels, NASA and Sikorsky employees came to the conclusion that such a scheme is outdated and interferes with the achievement of high speed characteristics. To reduce the consequences of the high speed of the blades, it was necessary to constantly adjust the cyclic pitch of the propeller, depending on the current horizontal speed and, as a consequence, the nature of the flow around the blades in one or another section of the swept disk. Therefore, the S-69 had a full-fledged swashplate capable of adjusting both the general pitch of the main rotor and the cyclic one.
The previous rotorcraft from "Sikorsky" - S-66 - had a complex system of turning the tail rotor, which when flying "in a helicopter" compensated for the reactive moment of the main rotor, and during horizontal high-speed movement pushed the car forward. After a series of detailed considerations, such a scheme was found to be too complex and, as a result, unpromising. In addition, to simplify the transmission and increase the efficiency of the power plant, it was decided to equip the new S-69 with two turbojets for horizontal movement. At the same time, the tail rotor was removed from the design, and the carrier “doubled”. As a result, the S-69 became a familiar pine-style helicopter with turbojet engines installed on the sides. Thus, one Pratt & Whitney Canada PT6T-3 turboshaft engine with a capacity of up to one and a half thousand horsepower is located inside the streamlined fuselage, adapted to high flight speeds. Through the gearbox, he set in motion both rotors. The three-blade propellers were 762 millimeters (30 in) vertically spaced with a fairing in between. Two nacelles with Pratt & Whitney J60-P-3A turbojet engines with a thrust of 1350 kgf were installed on the sides of the fuselage.
The experimental S-69 rotorcraft turned out to be relatively small. The fuselage is 12.4 meters long, the rotor diameter is a little less than 11 meters and the total height is only 4 meters. It is noteworthy that the S-69 in aerodynamic terms was seriously different from other rotorcraft: the tail stabilizer was the only bearing plane. The efficient propeller, designed according to the ABC concept, did not require any unloading by means of additional wings. For this reason, the finished aircraft was actually a conventional pine-type helicopter with additional turbojet engines installed on it. In addition, the lack of fenders allowed for some weight savings. The maximum takeoff weight of the S-69 was five tons.
The first prototype S-69 took off for the first time on July 26, 1973. The rotorcraft showed good controllability in hovering and low-speed motion without the use of turbojet engines. The first flights, during which the operation of turbojet engines was checked, ended in an accident. Less than a month after the first flight - on August 24 - an experienced S-69 crashed. The frame and skin of the rotorcraft were soon restored, but there was no more talk about its flights. A few years later, during the next phase of the ABC program, the first prototype was used as a full-size purge model.
The flights of the second prototype began in July 1975. According to the results of the investigation of the accident of the first prototype, the flight test program was significantly changed. Until March of the 77th year, the second prototype not only flew exclusively "in a helicopter" style, but was also not equipped with turbojet engines. Instead, by the end of the first stage of testing, the "incomplete" rotorcraft carried the required weight. With the help of the main rotors alone, the S-69 in flight without turbojet engines was able to reach a speed of 296 kilometers per hour. Further acceleration was unsafe, and besides, it was not needed due to the presence of a separate power plant to create horizontal thrust. By the end of the seventies, a new speed record was set: with the help of turbojet engines, the second prototype S-69 accelerated to 488 kilometers per hour. At the same time, the cruising speed of the rotorcraft did not even reach 200 km / h, which was due to the high fuel consumption of three simultaneously operating engines.
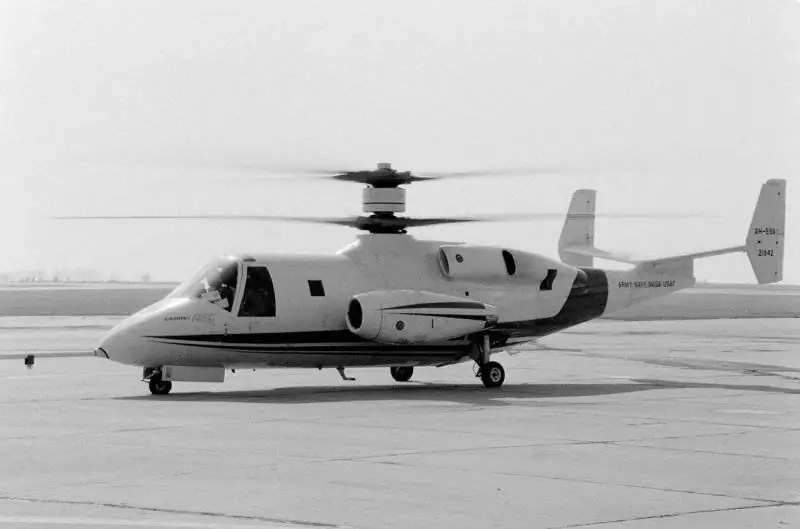
The benefits of the ABC system were evident. At the same time, the tests helped to reveal a number of design flaws. In particular, during test flights, a lot of criticism was caused by the vibration of structures that occurred at high flight speeds. The study of the problem showed that to eliminate this shaking, it was necessary to fine-tune the propellers, as well as some change in the design of the entire rotorcraft. At the very end of the seventies, work began on the creation of an updated S-69B rotorcraft. The first option, in turn, added the letter "A" to its name.
The second prototype of the rotorcraft was converted into the S-69B. During the alteration, the turboprop engine nacelles were removed from it, two new General Electric T700s turboshaft engines of 1500 hp were installed. each, new rotor blades with a larger diameter, and a major overhaul of the transmission. The rotorcraft received an updated main rotor gearbox. In addition, a separate shaft was introduced into the transmission, which went into the aft fuselage. A pushing propeller was placed there in the annular fairing. With the new pusher propeller, the S-69B was able to get even closer to the speed limit of 500 km / h. However, the main reason for the change in the design was still the improvement of the design and the development of a new version of the ABC concept. Due to the new rotors, vibrations during flight at certain speeds disappeared altogether, and at others they decreased significantly.
In 1982, all tests of the S-69B rotorcraft were completed. Sikorsky, NASA and others received all the information they needed and the remaining flying prototype was sent to the Fort Rucker Aviation Museum. The first prototype, damaged during testing and used as a purge model, is stored at the Ames Research Center (NASA). The developments obtained during the creation and testing of the S-69 rotorcraft were later used in new projects for a similar purpose.
Sikorsky X2
After the closure of the S-69 project, it took several years for further research on the ABC topic, and only in the second half of the 2000s, new and old developments reached the stage of building a new rotorcraft. The Sikorsky X2 project is somewhat similar to the previous rotorcraft of the same company, but the similarity ends in a few details of the appearance. When creating a new rotorcraft, the engineers of the Sikorsky company started from the technical appearance of the S-69B. For this reason, the X2 received a coaxial main rotor, a "squeezed" streamlined fuselage and a pusher rotor in the tail section.
It is worth noting that when creating a new rotorcraft, it was decided to make it slightly smaller than the S-69. The reason for this decision was the need to develop technologies without using any complex decisions related to the glider. As a result, the X2 rotors have a diameter of about ten meters, and the maximum take-off weight does not exceed 3600 kilograms. With such a low weight, the new rotorcraft is equipped with a LHTEC T800-LHT-801 turboshaft engine with an output of up to 1800 hp. Through the original transmission, the torque is distributed to two four-bladed main rotor and to the tail pusher (six blades). The X2 was the first rotorcraft in the world to be equipped with fly-by-wire control. Thanks to the use of such electronics, machine control has been greatly simplified. After preliminary study and adjustment of the control system, the automation takes over most of the flight stabilization tasks. The pilot only has to issue the appropriate commands and monitor the state of the systems.
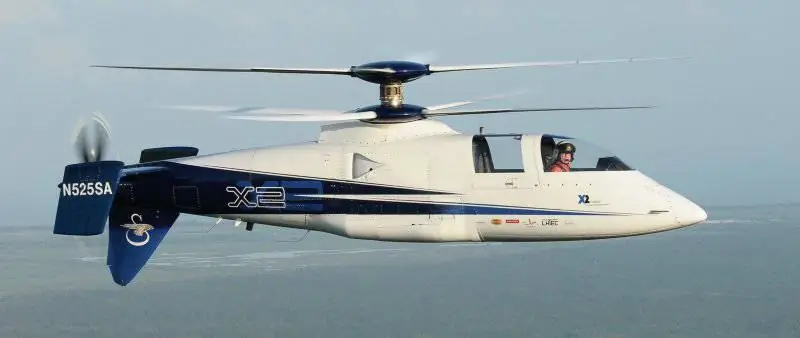
Recent advances in the ABC program, together with the fly-by-wire control system, have significantly reduced vibrations, including when flying at high speeds. In terms of aerodynamics, the X2 has elliptical propeller hub fairings; the shaft between the screws is not covered in any way, which is compensated by the correct placement of the rods and other parts. At the same time, the rotorcraft received an elongated fuselage of a relatively small section. The general layout of the fuselage was inherited by the X2 from conventional pine helicopters. In the front part there is a two-seat cockpit with pilot stations located one after the other. In the middle part, under the propeller hub, the engine and the main gearbox are located. The rotor shafts extend upward from it, and the pushing propeller drive shaft extends backward. The chassis system used is interesting. In the middle of the fuselage there are two main struts that can be retracted in flight. The tail wheel retracts into the keel located below the aft fuselage. In addition to this keel, the X2 tail assembly consists of a stabilizer and two end washers. There are no wings on the sides of the fuselage.
On August 27, 2007, a four-stage test program began with a half-hour flight. Like all other rotorcraft, the X2 first began to fly like a helicopter. During such flights, the general characteristics of the machine were checked. At the same time, unlike the same S-69, the pilots could not turn off the horizontal thrust propulsor: the tail rotor was controlled by changing its pitch. This technical solution was made to simplify the design of the transmission, into which they did not introduce an uncoupling clutch. Nevertheless, even without the disengageable tail pusher rotor, the X2 showed good characteristics inherent in helicopters. Starting in May 2010, reports began to arrive about the X2 rotorcraft reaching record speeds. At first, the new car reached 335 km / h. In September of the same year, pilot K. Bredenbeck accelerated the X2 to a speed of 480 kilometers per hour. This was slightly less than the S-69, but significantly higher than the top speed of any existing helicopter.
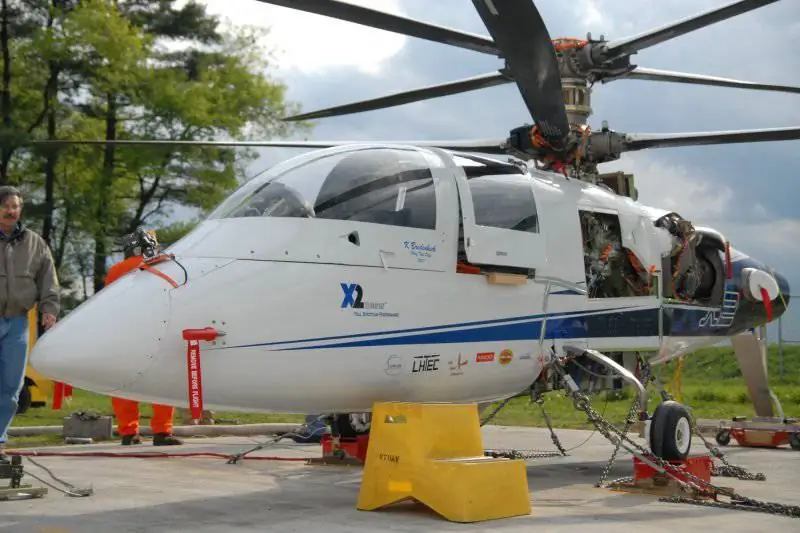
In mid-July 2011, it was officially announced that the X2 project was completed. For 23 flights with a total duration of about 22 hours, a huge amount of information was collected about the operation of all systems of the rotorcraft, as well as about its aerodynamic parameters. Despite the relatively small flight test program, the control and recording equipment of the experimental aircraft made it possible to significantly reduce the time required to collect all the necessary data. The Sikorsky X2 rotorcraft, being originally a flying laboratory, eventually became the basis for a new project of the same company, which already had certain practical prospects.
Eurocopter X3
In 2010, the European concern Eurocopter announced its rotorcraft project, which has an experimental purpose. During the X3 project (alternative names X3 and X-Cube), it was planned to test their own ideas for accelerating an aircraft with a main rotor to high speeds. Of interest is the appearance of the X3 project, in which the influence of American and Soviet programs is almost not felt. In fact, the Eurocopter X3 is a fairly modified helicopter of the classic design.
The new rotorcraft was based on the Eurocopter EC155 multipurpose helicopter. The well-developed design of this machine made it possible in the shortest possible time to design the X3 and convert the serial EC155 into it. During the conversion, the helicopter's native engines were replaced by two Rolls-Royce Turbomeca RTM322 turboshaft engines with a capacity of 2,270 horsepower. The motors transmit the torque to the original gearbox, which distributes it to the drives of three screws. The main rotor drive shaft with a decoupling clutch goes up. Two more shafts diverge to the sides and set in motion two five-blade pulling propellers, placed on special gondolas on the sides of the middle part of the fuselage. These gondolas are mounted on small fenders. Unlike the original EC155, the X3 does not have a tail rotor in the annular channel, which entailed the removal of the corresponding drive mechanisms from the design. Due to the absence of a tail rotor, the reactive moment is parried with the main rotor drive turned on using one of the pulling propellers.
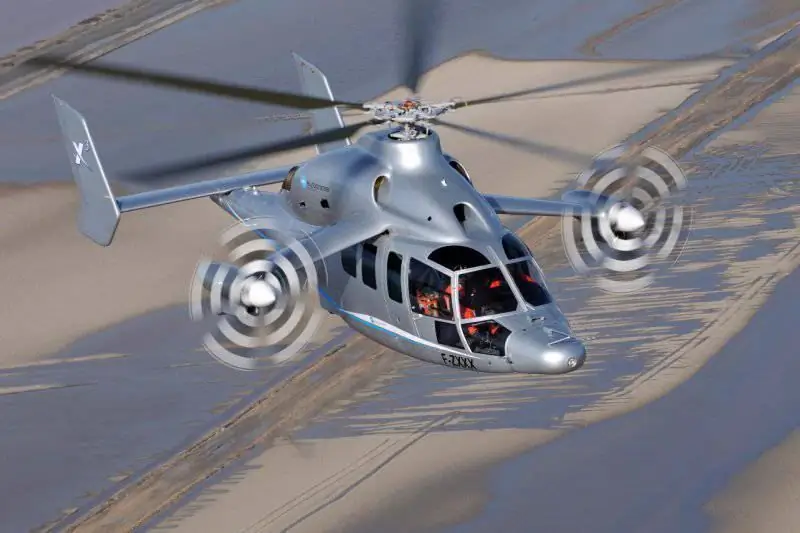
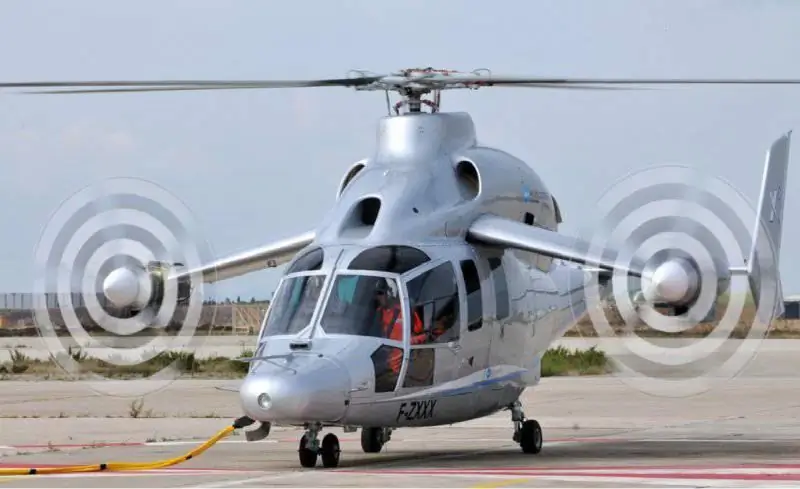
The removal of the tail rotor with a drive from the design in terms of weight was compensated for by a new stabilizer with two keel washers and pulling propeller assemblies. As a result, the X3's takeoff weight remains roughly the same as the original EC155. With a maximum load of fuel and instrumentation, the X3 weighs no more than 4900-5000 kilograms. At the same time, the change in the propeller system affected the flight ceiling - during the tests, it was possible to climb only 3800 meters.
On September 6, 2010, trials of the X3 rotorcraft prototype began. In contrast to the general appearance of the structure, the course of the tests turned out to be similar to how Soviet and American rotorcraft were tested. First, the test pilots tested the aircraft's vertical takeoff and landing capabilities, as well as the maneuverability and stability in helicopter flight. The next months were spent on eliminating the discovered problems and on a gradual increase in flight speed with the main rotor drive turned off and the pulling units turned on. On May 12, 2011, the X3 prototype set a "personal record": for several minutes it confidently kept a speed of about 430 kilometers per hour. Over the next year and a half, there was no news about the conquest of new speed marks, but this seems to be due to the need to find optimal flight modes. The tests of the Eucopter X3 rotorcraft are still going on. The appearance of the first aircraft based on it, suitable for mass practical use, is expected after 2020.
Sikorsky S-97 Raider
At a time when European aircraft manufacturers were already in full swing testing the X3 rotorcraft, Sikorsky employees continued research on the ABC topic in order to create a new rotorcraft that can be used in real conditions. In October 2010, the S-97 Raider project was officially announced. Before the development of the new rotorcraft began, the ABC concept underwent minor changes. According to the results of research in the course of the X2 program, it turned out that in order to effectively maintain the rotorcraft in the air at high flight speeds, it is possible not only to change the cyclic pitch of the main rotor, but also to slow down its rotation. With the correct calculation of the main rotor, the deceleration will noticeably shift the horizontal speed threshold towards an increase, at which problems with lift begin. Calculations have shown that the rotorcraft retains the necessary lifting force of the main rotor even when it is decelerated by 20%. This is exactly the idea Sikorsky decided to test in the course of further research and practical tests.
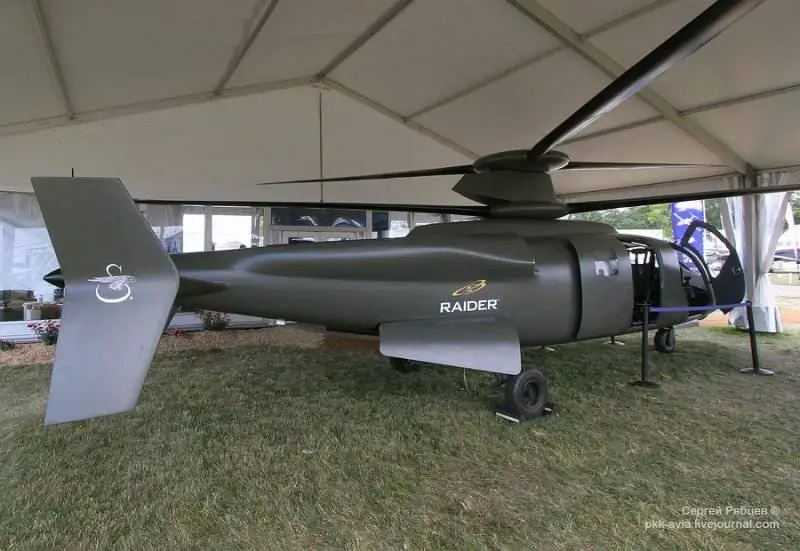

photo
The rest of the S-97 rotorcraft is largely similar to the previous X2. According to the data available now, the new machine will have a relatively small size: the length is no more than 11 meters and the diameter of the rotors is about ten. The general concept of screw placement has been preserved. So, the S-97 Raider will be equipped with two coaxial main rotor with a hub carefully closed by the fairings. The rear of the streamlined fuselage will house a five-bladed pushing propeller. At the same time, already in the early drawings of the alleged appearance of a promising rotorcraft, a change in the contours of the fuselage and a change in the design of the tail unit were noticeable.
Until a certain time, the appearance of the "Raider" could only be judged by fragmentary information that became the property of the public, as well as by a few drawings. However, even before the appearance of the technical details of the project, it became known that he would take part in the Pentagon's AAS (Armed Aerial Scout) program. The winner of the competition in the coming years will become the main aircraft of the American army, designed to conduct aerial reconnaissance at short distances from the front line. In addition, the Pentagon wants to provide a scout with the ability not only to identify targets, but also to hit them on their own. The exact composition of the required weapons has not yet been announced, but based on the provided drawings of the promising S-97, we can draw rough conclusions. On small wings on the sides of the fuselage, two blocks with weapons can be installed. Probably, these will be blocks of unguided missiles or anti-tank guided munitions. Also, a number of sources mention the possibility of installing a movable turret with a large-caliber Browning M2HB machine gun on the rotorcraft.
At this year's EAA AirVenture Oshkosh show, Sikorsky presented to the public for the first time a full-size model of its new S-97 rotorcraft. This mockup, with the exception of a few minor details, repeats the appearance of the aircraft shown in the earlier drawings. In addition, this year, the estimated technical data of the machine was clarified. So, it became known that the first prototypes of the S-97 will be equipped with turboshaft engines of the General Electric T700 family. However, in the future, the following prototypes, and after them the serial rotorcraft, will receive new engines, which are currently being developed under the AATE program. With the new S-97 engine with a takeoff weight of about five tons, it will be able to accelerate to 440-450 kilometers per hour. In this case, the flight range will exceed 500 kilometers.
The layout of the new rotorcraft raises some questions. The turboshaft engine requires a separate air intake. The S-97 has two of these holes. Moreover, both of them are located in the middle of the fuselage, closer to the tail. This fact and the contours of the fuselage may hint at the location of the engine in the tail section of the rotorcraft. However, in this case, it is not entirely clear how exactly the drive shafts of the main and pusher propellers are divorced. Other elements of the appearance of the promising S-97 are quite understandable and indicate the intention of the authors of the project to provide it with a high flight speed. Among other things, the fuselage of an elongated teardrop shape and neat fairings for the main rotor hub can be noted.
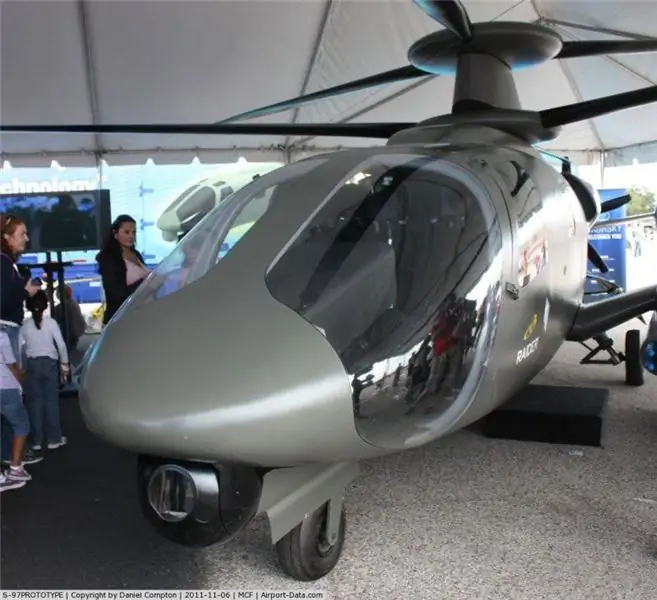
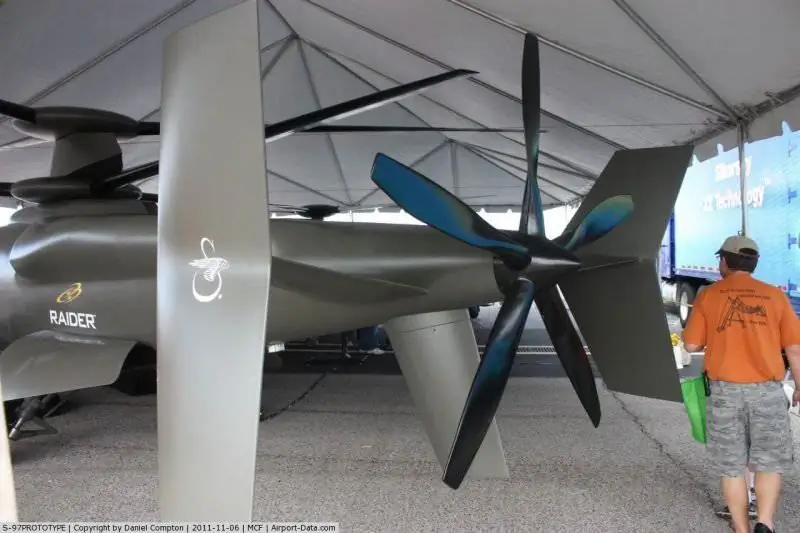
Also of interest is the internal equipment of the rotorcraft. The available photos of the S-97 layout show the cockpit equipment. Thanks to the large windscreens, the two pilots have a good view forward and down to the side. On the dashboard of the rotorcraft, there are two color multifunctional displays and a certain panel with buttons. Probably, the composition of the cockpit equipment can be expanded by other control panels, located, for example, on the ceiling or between the pilot's seats. The designers of the Sikorsky firm have interestingly solved the problem of the placement of the controls. On the S-97 model, as you can see in the photo, pedals are completely absent, and in their places are small footrests. Flight control, apparently, is planned to be carried out using two handles on the armrests of the pilot's seat. Most likely, the right stick controls the cyclic pitch of the main rotor, while the left is responsible for its overall pitch and engine power. It is not yet entirely clear how it is planned to regulate the level flight speed. In view of the fact that so far only a model has been presented, there is every reason to assume a repeated change in the composition of the cockpit equipment, including the controls.
Immediately behind the cockpit, there is a volume intended for the carriage of passengers or cargo. On the mock-up in this cockpit, three landing seats and a certain metal box were installed, probably to accommodate any small loads. The passenger and cargo compartment is accessed through two sliding doors on the sides of the fuselage. Perhaps, in the future, new engines or other technical solutions will make it possible to increase the volume of the cargo-passenger compartment and, for example, install more seats for the soldiers in it. In addition, according to the experience of multipurpose helicopters of a similar class of carrying capacity, the rear cockpit can be equipped with devices for attaching any weapon for firing at ground targets.
Keep in mind that only a mockup was shown at the AirVenture Oshkosh. The first flight of the prototype of the S-97 Raider rotorcraft is scheduled for 2014, so some of the nuances of the design and equipment may be changed. As for the speed records, they will appear even later, approximately at the end of 2014 or even in 2015.
Promising Russian projects
In our country, JSC Kamov is the most active in the subject of rotorcraft. His Ka-92 project currently has the greatest prospects. This multipurpose rotorcraft is a modified helicopter with a coaxial rotor design and coaxial pusher propellers. According to preliminary calculations, two turboshaft engines (approximate power was not announced) will be able to accelerate the car to a speed of about 500 km / h. With such a speed, the Ka-92 rotorcraft will be able to carry up to 30 passengers over a distance of about 1400 kilometers. The Ka-92 project resembles the English Fairey Rotodyne in its objectives: it should become a rotary-wing vehicle with low requirements for the size of the take-off and landing area. At the same time, it must have flight data with which it can compete with short-range passenger aircraft.
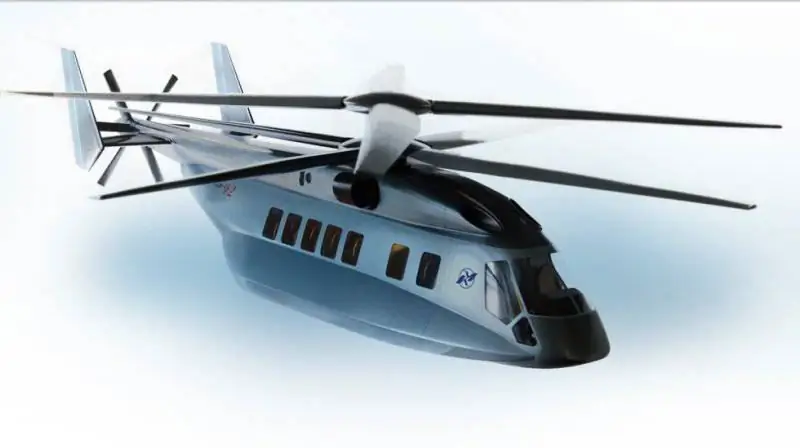
Another project of the Kamov company - the Ka-90 - does not have such great practical prospects and, in fact, is an experimental work. The concept presented in 2008 can help rotary-wing aircraft not only accelerate to 450-500 kilometers per hour, but also reach the bar of 700-800 km / h. To do this, it is proposed to create a horizontal thrust with a turbojet engine, as well as to change the design of the rotor blades and hub. According to the Ka-90 project, the two main rotor blades should have a relatively large width and small thickness. Such a rotorcraft takes off vertically or with a slight takeoff, then, with the help of a turbojet engine, it accelerates to a speed of about 400 km / h. After reaching this speed, the rotorcraft stops the main rotor and fixes it in a position perpendicular to the flow. The propeller now functions as a wing. With further acceleration, a special mechanism in the main rotor hub gradually increases the sweep of such a "wing" until the propeller blades are folded along the fuselage. It is interesting that in the science fiction film "Day 6" (2000, directed by R. Spottiswood), aircraft appeared with precisely this method of combining the best features of an airplane and a helicopter. At the same time, the Whispercraft from the movie did not fold the blades completely and performed high-speed flight in a swept "wing" configuration. The prospects for the Ka-90 are not completely clear. Even if work on this project is still ongoing, no new information has been received for several years. Perhaps too bold and until a certain time useless project was simply frozen, as they say, until better times.
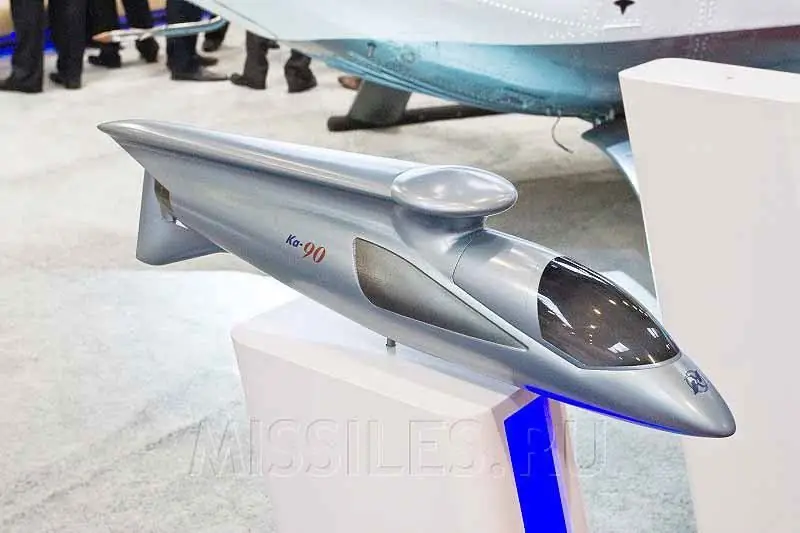
Simultaneously with the Ka-92 and Ka-90 MKZ them. M. L. Mila presented his own project belonging to the same class of technology. The Mi-X1 project involves the creation of a multi-purpose rotorcraft with a take-off weight of 10-12 tons. The aircraft, equipped with two VK-2500 engines, must carry up to 25 passengers or up to four tons of cargo. The goal of the project is to achieve a cruising flight speed of at least 450-470 kilometers per hour. The maximum speed indicators, in turn, must exceed 500 km / h. The design flight range is 1,500 kilometers. The Mi-X1 rotorcraft is largely similar to the Ka-92, but it has only one main rotor. The main difficulty of the project is to ensure the correct flow around the rotor blades. To resolve this issue, research and design work began in due time on the suppression of flow stall on the retreating blade. Blowing in wind tunnels, theoretical calculations and other scientific research on the Mi-X1 project are quite complicated, therefore, even in 2008, the first flight of the prototype of the new rotorcraft was attributed to 2014-15.