New news continues to come from the Chinese exhibition Airshow China 2012. Of the latest novelties presented at the show, the most interesting is the new Chinese high-speed helicopter project. As can be seen from the design of the rotorcraft, which received the code name Avant-Courier, when it was created, the maximum flight speed was put at the forefront. This is evidenced by the "licked" fuselage, fairings of rotor hubs, as well as two small wings with engine nacelles and propellers. Until now, only helicopters designed to develop high flight speeds had such an appearance. The appearance of the Chinese Avant-Courier indicates that China has joined the helicopter race.
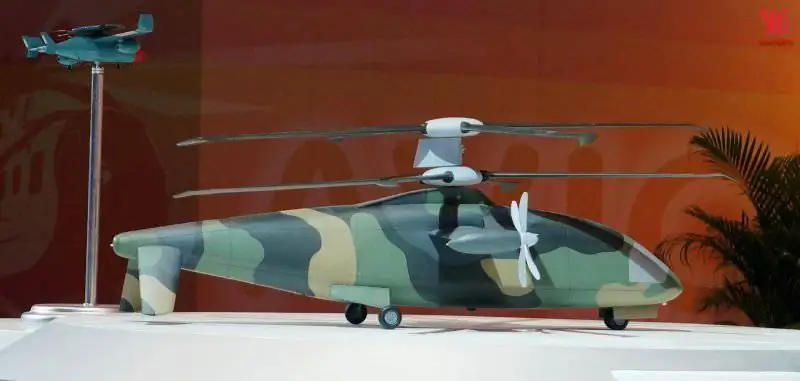
The scheme used by the Chinese in domestic technology is called the term "rotorcraft". This means that the aircraft has a separate main rotor that holds the aircraft in the air and a separate system for creating horizontal thrust. The main advantage of such a scheme lies in the absence of the need to develop and manufacture a complex screw sleeve with a swash plate. In addition, the horizontal thrust becomes the "responsibility" of a separate system, rather than the rotor, and, as a consequence, the engine power is consumed more efficiently, which makes it possible to achieve much higher flight speeds. All the advantages of the helicopter, such as the ability to hover and take off / land on small areas, are fully preserved. Until a certain time, rotorcraft almost on equal terms competed with helicopters for the right to become the main class of vertical takeoff aircraft, but for a number of reasons - primarily due to a relatively complex transmission - they lost. Nevertheless, the development of rotorcraft continued, although in terms of number they cannot compete with helicopters.
Fairey Rotodyne
One of the first rotorcraft projects that had good prospects for practical use was the English Fairey Rotodyne, created in the mid-fifties. The goal of this project was to manufacture a promising multipurpose (primarily transport) aircraft capable of carrying a payload at a higher speed than the helicopters then available. At the same time, in terms of speed, the required apparatus was inferior to the available aircraft, but did not require large take-off and landing sites. After a short reflection on the appearance of the future machine, the engineers of the Fairy company recalled the old idea with a separate main and separate pulling screws. As a result of research and development work, the first prototype of the Rotodyne machine was built in 1957. He was something that combines the features of a helicopter and an airplane. In the upper part of the cigar-shaped fuselage, a propeller pylon was installed. On the sides of the vehicle there were two wings with a nacelle on each. In the tail section of the fuselage, a stabilizer with two keel-washers was provided.
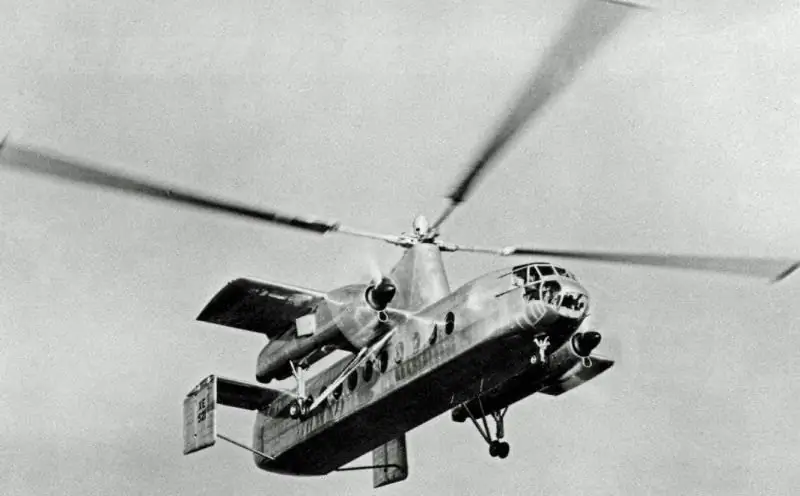
The power plant of the Rotodain is of particular interest. The device had as many as six engines. The first two of them are Napier Eland NE1.7 turboprop with a capacity of 2800 hp each. - housed in engine nacelles on the wing. Through their own gearboxes, they rotated the pulling screws. The main rotor was spun up by means of four miniature jet engines (one on each blade) of our own design. An air bleed system was installed on turboprop engines, which entered the engines on the blades, where it was mixed with fuel. The burnt mixture drove the rotor into rotation. Such a system was quite complex and unusual for aviation technology, however, the use of a propeller jet drive made it possible to simplify the design of the entire Rotodyne due to the absence of the need for a tail rotor to counter the reactive moment of the main rotor. In addition, the Rotodine power plant provided for the possibility of turning off the main rotor drive, after which the device could fly like an autogyro and spend all the engine power on horizontal thrust. The resulting rotorcraft Rotodyne had solid dimensions: a rotor diameter of 27.5 meters, a total length of almost 18 meters and a dry weight of 7200 kilograms. Initially, only the option for the transport of passengers was developed. The cabin of the device could accommodate up to forty people with luggage. At maximum load, the takeoff weight of the Rotodine was a little short of fifteen tons.
On November 6, 1957, the first prototype of the rotorcraft took off. In the course of the first flights "over-the-air", the controllability was once again tested: the fact is that the yaw control was carried out not by the thrust of the tail rotor, which was not there, but by a separate change in the pitch of the pulling propellers. The very first flights showed the viability of such a system. Until the end of the first stage of testing, Rotodine reached a speed of 250 km / h and an altitude of 2100 meters. At the same time, all flights took place without turning off the main rotor engines and without the use of pulling propellers. In the spring of 1958, the second stage of testing began, during which the rotorcraft began to switch to the autorotation mode and fly with the help of turboprop engines. At the very beginning of 1959, Fairey Rotodyne set a speed record for rotorcraft. On a closed 100-kilometer route, it accelerated to 307 km / h. This was nearly 80 kilometers per hour faster than the previous helicopter record. At the same time, calculations showed that without changing the design, Rotodine is capable of reaching the bar of 400 km / h.
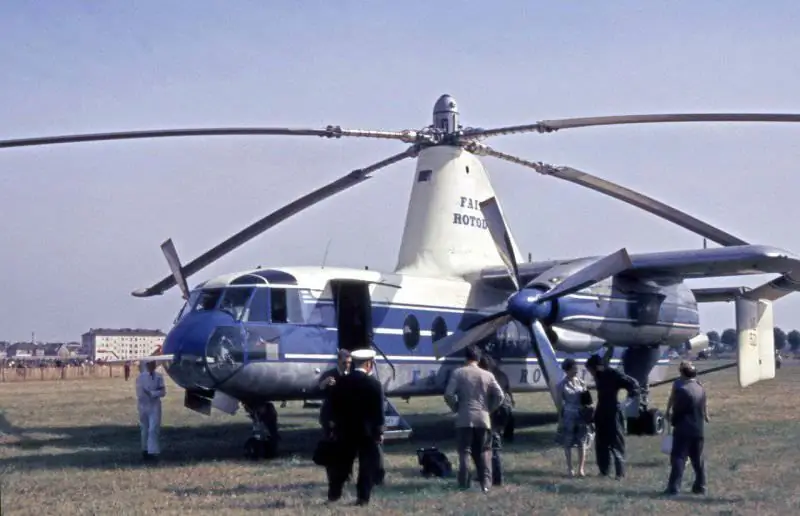
The Rotodyne was first shown to the public at the 1958 Farnborough Air Show, where its unusual design immediately attracted great attention. However, in addition to curious "ordinary" visitors, potential customers are also interested in them. Even before the end of the tests, several large air carriers expressed a desire to receive such equipment, and the Canadian company Okanagan Helicopters (now CHC Helicopters), without waiting for the end of the salon, signed a preliminary contract for the supply of at least one new rotorcraft. Moreover, even the Pentagon and the Royal Air Force of Great Britain became interested in a promising machine. However, many customers wanted to get a car with a higher carrying capacity. The calculations of the economists of the company "Fairy" at the very beginning of the work showed that the most financially efficient option would be a rotorcraft, capable of carrying 60-65 passengers. It was on 65 places that several shipping companies insisted. The redesign of the project required a solid financial investment - about 8-10 million pounds. Because of this, the Rotodyne project at the very end of the fifties got into a very awkward situation. Potential customers did not want to pay for the design work, and Fairey Aviation did not have its own funds.
In addition to its own problems with financing the Rotodine project, the plans of the British government were hit. Reduced government orders forced Fairy Aviation to become part of Westland, and the latter had no plans to develop its Rotodyne program. Funding for a promising rotorcraft was insufficient, which led to the delay in testing. Because of this, most of the shipping companies abandoned their plans. In 1962, despite the initial plans to start mass production, the Rotodyne project was canceled. An interesting and bold aircraft could not cope with bureaucracy, financial problems and distrust of businessmen.
Kamov Ka-22
Almost simultaneously with the creation of the English Rotodine, a somewhat similar project began in our country. Rather, only the timing of the main design work roughly coincided, and the ideas of both projects appeared at the end of the forties. The first Soviet rotorcraft with characteristics suitable for practical use grew out of the idea of towing a helicopter by an airplane. In this case, the towed vehicle could switch to autorotation mode and save a lot of fuel. However, the practical application of the "plane-helicopter" link did not look very convenient. It was decided to develop an aircraft that could combine all the positive features of the available types.

By May 1952, the design bureau of N. I. Kamova completed the preliminary design of the future rotorcraft called the Ka-22. Already in the early stages, it was proposed to make the aircraft two-screw, with a transverse position of the rotors. In addition to the relative simplicity of the airframe design, this made it possible to significantly simplify the transmission: the engines located in the nacelles under the main rotors could simultaneously drive the pulling propellers. In fact, the most difficult part of the transmission was the synchronization mechanism, which ensured the simultaneous identical rotation of both rotors and, in the event of a shutdown of one of the engines, distributed the power of the remaining one. At the same time, the Ka-22 scheme at that time was considered not entirely suitable for mass use. All previous transverse helicopters suffered from the same problem - strong vibrations. Then the opinion appeared that the vibrations of the structure are an organic disadvantage of the transverse arrangement of the screws.
It is worth noting that in addition to vibrations, the promising project had a number of other problems. For example, calculations showed the need to create a power plant and transmission capable of operating at a capacity of about 12 thousand horsepower. I also had to spend a lot of time studying the screws. At a flight speed of about 400 km / h, the flow velocity at the ends of the rotor blades exceeded the speed of sound, which significantly deteriorated their characteristics. Nevertheless, the designers of the Kamov Design Bureau and TsAGI employees coped with aerodynamic and engineering problems. Ten years after those works, N. I. Kamov defended his doctoral dissertation, which partially related to the Ka-22 project. According to M. L. Mil, for this project it was necessary to immediately give a doctorate in technical sciences.
The finished project looked like this. On the fuselage of a cross-section close to rectangular, the tail unit was mounted from a stabilizer and a keel. In the middle part of the fuselage, a wing span of 23.8 meters was installed, at the ends of which two engine nacelles were placed for D-25VK engines with a capacity of 5500 horsepower. The nacelles also housed transmission systems that distributed power to the main and pulling screws. The empty Ka-22 weighed almost 26 tons. The maximum payload exceeded 16 tons. At the same time, in some cases, the rotorcraft could carry no more than five tons of cargo - in this case, an acceptable flight range was achieved.
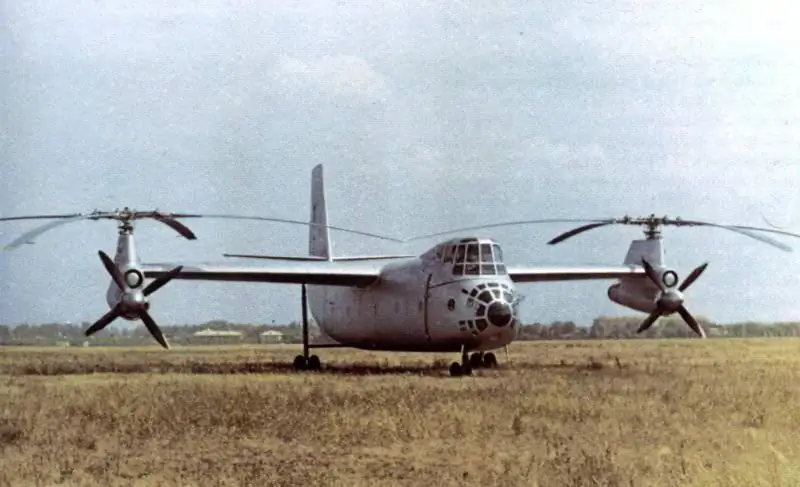
The first prototype of the Ka-22 rotorcraft was built in 1958, but after being transferred to the flight test station, some modifications were needed. Because of them, the first flight took place only in the middle of the 59th year. By the end of the year, flight missions were added to helicopter flights, which included the inclusion of pulling propellers. On April 29, 1960, the first circle flight ended shortly after the start. The crew of pilot D. K. Efremov, a few seconds after takeoff, felt a strong vibration and was forced to land near the airfield. The cause of the trouble was the detachment of the skin of one of the blades of the right main rotor. In the future, the tests of the Ka-22 were repeatedly interrupted for a short time due to constant technical deficiencies and improvements. Nevertheless, in November 1961, the new rotorcraft set a world record, lifting 16485 kilograms of cargo to a height of 2557 meters.
The most serious accident during the tests of the Ka-22 happened at the end of the summer of 1962, when a prototype rotorcraft, which was being ferried from the Tashkent aircraft plant to Moscow, crashed. When approaching the Dzhusaly airfield, the aircraft fell on its side and fell to the ground, burying seven crew members under it. The cause of the accident was the disconnection of the fastening sleeve of the pitch control cable of the right main rotor. The second rotorcraft to be overtaken was sent for inspection and revision. Tests resumed only in the spring of next year. The new stage of flights according to its program repeated the previous ones: first, takeoffs with the help of rotors, and then test flights "like an airplane". The latest tests were generally considered successful, but the rotorcraft still required refinement for use in the air force. During the tests, the car reached a maximum speed of 356 kilometers per hour. A further increase in flight speed was associated with a certain risk, however, the bar at the estimated 400 km / h could still be conquered.
Nevertheless, fine-tuning was not needed, and the speed of four hundred kilometers per hour remained unattainable. Even at the end of 1963, the Ka-22 project remained at the stage of testing prototypes. By this time, its main competitor, the Mi-6 helicopter, went into production and was put into service. The Ka-22 was originally developed as an alternative to the new heavy-duty helicopter. Difficulties in the design and testing of the finished rotorcraft ultimately affected the timing of the project, which ultimately put an end to it. The leadership of the aviation industry and the Department of Defense lost interest in the complex and lengthy project in 1964. Work on the Ka-22 was stopped.
Lockheed ah-56 cheeyenne
Lockheed has always been renowned for its cutting edge engineering. Often, the implementation of new ideas cost the customer large sums or was stopped due to technical problems, but this almost did not affect the "zeal" of the designers. In the sixties, employees of "Lockheed" tried themselves in the creation of rotary-wing machines. Needless to say, the project turned out to be interesting and, to a certain extent, bold? The resulting rotorcraft AH-56 Cheeyenne still attracts the attention of specialists, but the actual fate of the project turned out to be sad.
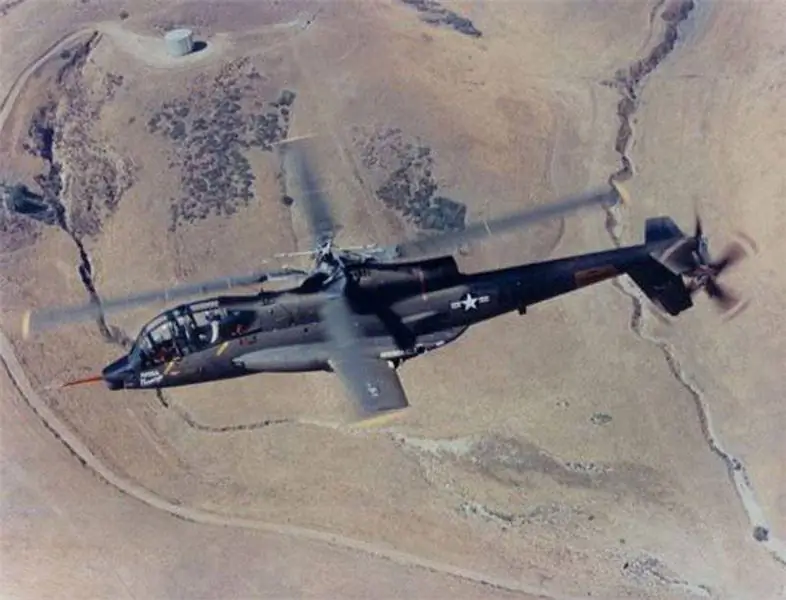
In the mid-sixties of the last century, the Pentagon wanted a new attack helicopter with good flight and combat characteristics. The program of the military department received the designation AAFSS and 12 design organizations were involved in it. Only two firms entered the final stage of the competition - Lockheed with its AH-56 Cheeyenne project and Sikorsky with the S-66. The technical requirements for the new helicopter included high speed. The military assumed that the new attack helicopter should spend a minimum amount of time entering the attack area. For this reason, both projects involved the installation of a pusher propeller in the tail of the helicopter. This fact makes the helicopters under consideration an aircraft of the "rotorcraft" class. It is noteworthy that engineers at Lockheed and Sikorsky have chosen different methods of countering the reactive moment of the main rotor. Lockheed did it simply: to the tail rotor with four blades they added a three-bladed pusher located at the very end of the tail boom. A special mechanism was designed at the Sikorsky firm that turned the tail rotor 90 °. After such a turn, the main rotor went into autorotation mode and did not create a reactive moment. However, the customer found the S-66 helicopter layout too complex. In 1966, this project was closed in favor of the Lockheed AH-56 Cheeyenne.
The relative simplicity of the Cheyenne's tail section was more than offset by the general boldness of other technical solutions. The rotorcraft helicopter received a thin fuselage with convex cockpit glazing. For its recognizable characteristic shape, the rotorcraft acquired the nickname Dragonfly - "Dragonfly". At the top of the fuselage, a low-profile propeller hub was installed, on which three blades were hung. For helicopters of that time, a three-bladed propeller was quite a bold decision. Most rotary-wing aircraft of the time had an even number of blades for easier balancing and less vibration. A turboshaft engine was located in the middle of the fuselage, behind the propeller hub. On the first copies of the AH-56, it was a General Electric T64-GE-16 with a capacity of just under 3,000 horsepower. With a maximum takeoff weight of about 7,700 kg, the Cheyenne could carry up to 1,700 liters of kerosene. This gave the rotorcraft a unique maximum range of up to 1400 kilometers. Despite the low weight, the important units of the helicopter and the crew had anti-bullet and anti-splinter armor. The crew of two was located in a common cockpit; the pilot's workplace was located behind and above the navigator-gunner's workplace.
Realizing the great future of combat helicopters and rotorcraft, Lockheed designers did not waste time on avionics. Its main element was the General Electric XM-112 sighting and observation system. This system included 12 periscopes, a laser rangefinder and a night vision device. Thanks to the XM-112, the navigator-gunner could control a 210 ° wide sector in front of the car. A yaw turn could provide all-round visibility. The XM-112 system was combined with the guidance complex of the newly created BGM-71 TOW anti-tank missiles. Missiles and other weapons were placed on six pylons under the wing. Also, three radio stations for communication with the base and ground connections, equipment for the "friend or foe" identification system, a radio altimeter, an automatic heading machine and other necessary electronic equipment were built into the monitoring and weapon control system. A characteristic feature of Cheyenne's avionics is the maximum integration of all equipment. The greater, in comparison with previous helicopters, the number of various electronics practically did not affect the convenience of handling it. The only disadvantage of advanced avionics is the high price of the entire complex. However, in those days, the American military did not skimp on military equipment.
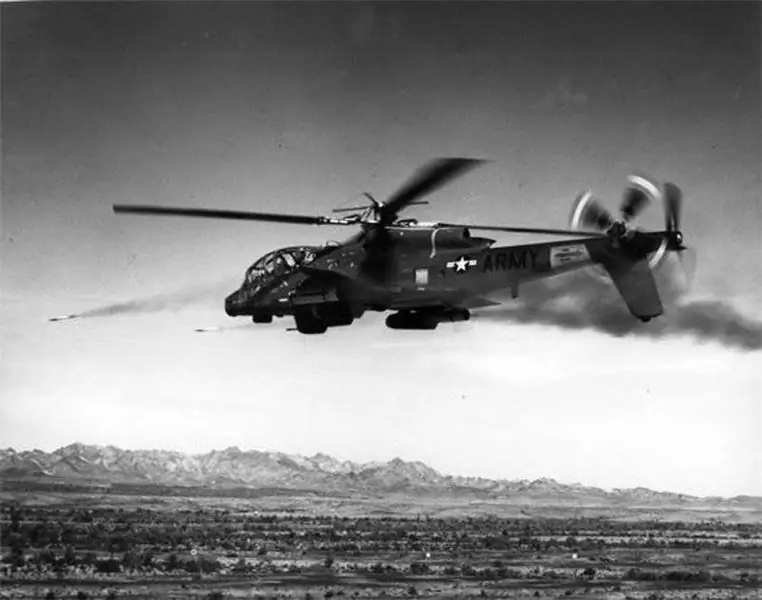
The potential operator of the Sheeyenne rotorcraft could choose from a fairly wide range of weapons. So, a remotely controlled turret from Emerson Electric was placed in the nose of the combat vehicle. Under the spherical casing of the turret, it was possible to place a six-barreled XM-196 Gatling rifle machine gun, an XM-129 40-mm automatic grenade launcher or an XM-52 30-mm automatic cannon. The ammunition load of various barrel systems was different, however, in the nose of the rotorcraft there was enough space to accommodate boxes with cartridges or shells. Six external sling nodes could carry another 907 kilograms of weapons, for example, unguided rockets or TOW ATGMs. In general, the combat potential of the Cheyenne significantly exceeded the capabilities of the newly created Cobra AH-1.
The flight characteristics of the new rotorcraft were also higher. The AH-56 climbed to a height of one thousand meters in less than a minute and could fly at a range of up to 1400 kilometers. During the tests, a maximum speed of 407 kilometers per hour was reached. On September 21, 1967, the first flight prototype of the helicopter took off. He clearly showed the convenience of the high-power engine and the applied system with two tail rotor. However, during the transition from hover to level flight, as well as during the latter, the Cheyenne behaved unstably. Minor improvements were interspersed with test flights. This practice lasted until the spring of 1969: on March 12, the third flight copy crashed. During the flight, the rotor began to vibrate, which caused it to hit the lantern. The blow was so strong that pilot D. Bale, who was in the upper cockpit, immediately died. After this incident, there was a proposal to equip the rotorcraft with ejection seats and a system for shooting the blades. By this time, the total number of Cheeyenne built or under construction was eight.
The Cheyenne was left with many technical and operational problems. Lockheed's employees were actively working to eliminate them, but the Vietnam War has already entered an active stage. The American military urgently needed an attack helicopter, which soon became the AH-1 Cobra. By the end of the spring of 69, the Pentagon terminated its contract with Lockheed. Bell received a lucrative offer in the amount of about one hundred million dollars. Later, other contracts followed for several hundred Cobras drums. As for the AH-56, Lockheed continued the project on its own initiative and at its own expense. The Cheyenne in the AH-56A version had an updated chassis, a new four-blade propeller and a more powerful General Electric T64-GE-716 engine. In addition, the composition of the equipment was adjusted and the production technology was slightly simplified. In accordance with the new project, two rotorcraft were built. In 1972, Lockheed presented the military with an updated combat vehicle, but they no longer showed any interest. The project was finally closed, and soon the Pentagon began a new program, the result of which was the AH-64 Apache helicopter.
The first rotorcraft of the Lockheed firm turned out to be too complex and daring for its time. Besides, Cheyenne was not lucky enough to show up at the right time. Due to the battles in Vietnam, the main customer lost interest in a promising aircraft, even if it was an unusual rotorcraft class. Of the ten AH-56 built, only four survived to this day, which are now museum pieces.