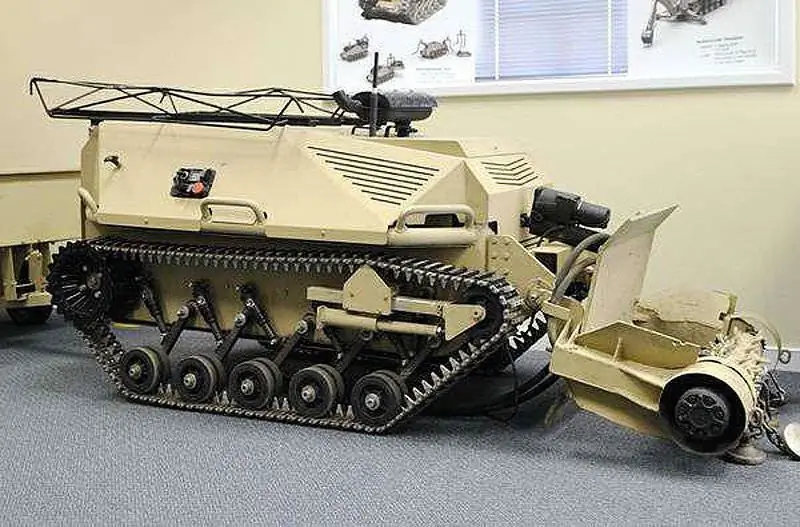
Heavy-duty Protector tracks define its high level of mobility
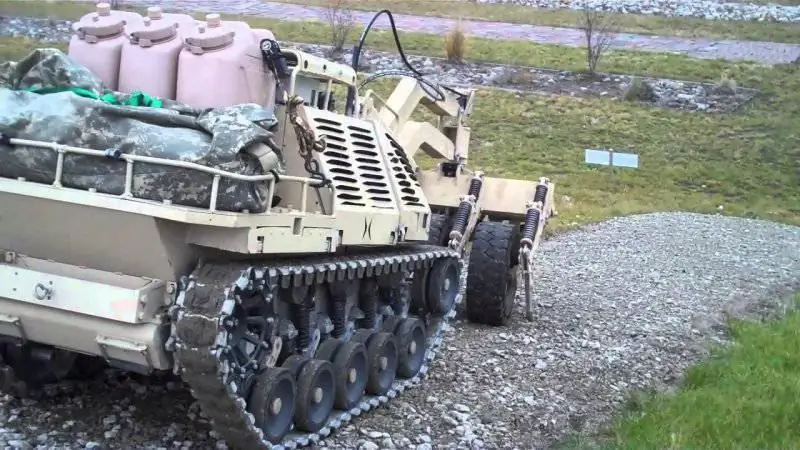
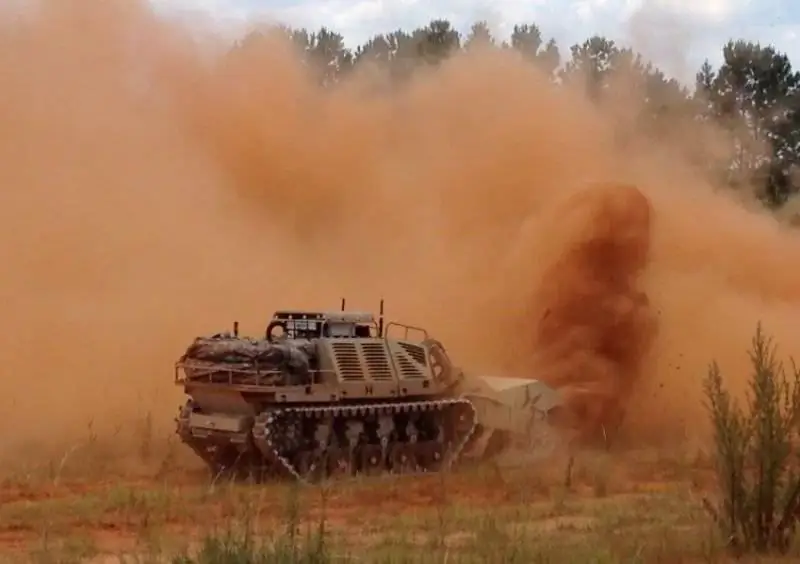
Protector can be configured for a wide variety of tasks, although its main job is to clear routes
HDT Robotics' Protector Automatic Ground Vehicle (ANA) is ready to test a number of new capabilities in the upcoming US Army demonstration.
At the DSEI defense exhibition in London, HDT Global Production Director Tom Van Doren announced that the Protector will be sent in engineering and military configurations to the US Army's Combat Training Center at Fort Benning in early October.
The Protector is primarily designed to provide dismounted forces with a route clearing tool that operates in difficult terrain where a highly mobile platform is required.
The device has a modular configuration, it can be divided into three parts, each of which can be carried by four people.
The ANA Protector has two motors. The diesel engine is installed in the central section, it drives two hydraulic motors, which ensure the movement of the apparatus; another diesel engine is installed in the rear basket, it drives the striking trawl.
The vehicle uses diesel engines because, according to Van Doren, HDT "wanted the smallest diesel system that could carry significant cargo," while adding that larger cargo vehicles, such as Lockheed Martin's Squad Mission Support System, could have a larger lifting capacity, but not as maneuverable as the Protector, while small electric vehicles do not have sufficient capabilities and autonomy.
Van Doren said the engineering configuration is being developed for US Army engineering units and will have an excavator bucket and a loader bucket, both driven by a hydraulic motor. The loader bucket has a lifting capacity of 90 kg and a lifting height of 2.5 meters, while the excavator arm can dig a trench 1.5 meters deep.
The company has also tested new control methods for the craft, including follow and control via QinetiQ North America's Tactical Robotic Controller. This controller is already in use in real-life applications, including the US Army's Spartacus and Minotaur unmanned engineering vehicles. These capabilities have also been tested at the Combat Training Center. In addition, a satellite communication system was installed on the device, which demonstrated a data transmission delay of one second.
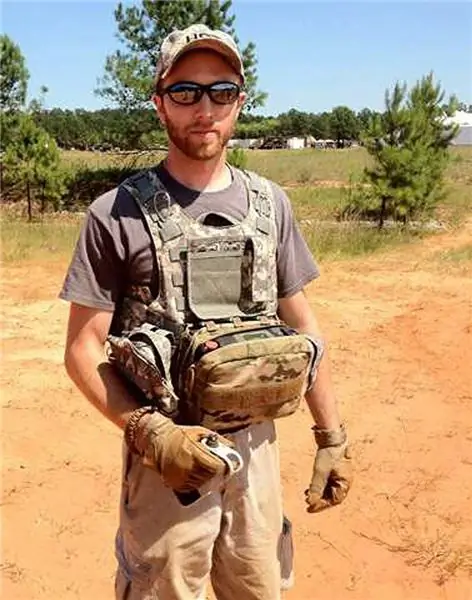
The guy is holding a finger joystick to control the Protector robot
Standard control of the system is provided by a two-button thumb navigation joystick that can be attached to the Picatinny rail, allowing control of the apparatus from the front forearm of the rifle. The controller connects to a radio relay station that can be carried in a MOLLE (Modular Lightweight Load Carrying Equipment) pocket and allows communication with the vehicle up to 400 meters away. Van Doren said the thumbstick is the preferred control method as it allows the soldier to maintain situational awareness rather than focus on the control display. Two control finger joysticks will be used to work with engineering hinges.
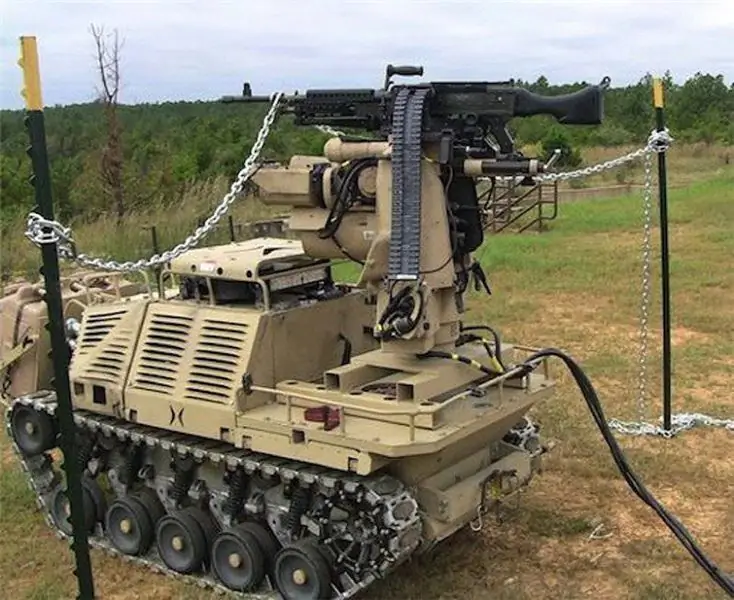
Protector from HDT Robotics in an armed configuration
For testing at the combat training center, the armed configuration of the device will be obtained through the installation of a remotely controlled combat module Protector from Kongsberg.
In addition, a distinctive feature of the device is the tracks developed by the company, which allow you to reach speeds of up to 5 mph without a striker trawl and 3 mph when clearing passages with a striking trawl. The tracks increase the vehicle's cross-country ability and help to overcome 45-degree slopes and 30-degree side slopes.
Van Doren also mentioned that in addition to clearing the passages and the tasks that the ANA performed during trials in October, the Protector can be used to evacuate victims, since a stretcher can be installed from each side of the vehicle. Without a striker trawl, the device can also carry 400 kg of cargo and tow a trailer weighing 230 kg.
AHA Protector can also be used as a battery charger and generate electricity up to 2 kW.
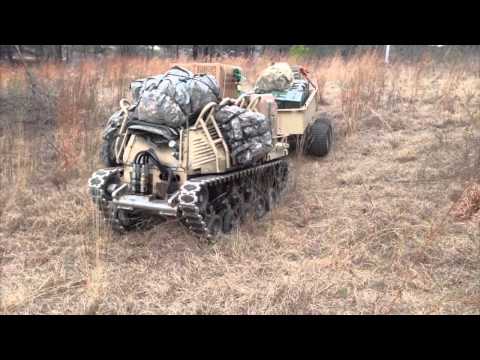
The Protector Robot tracked robot being tested at Fort Benning