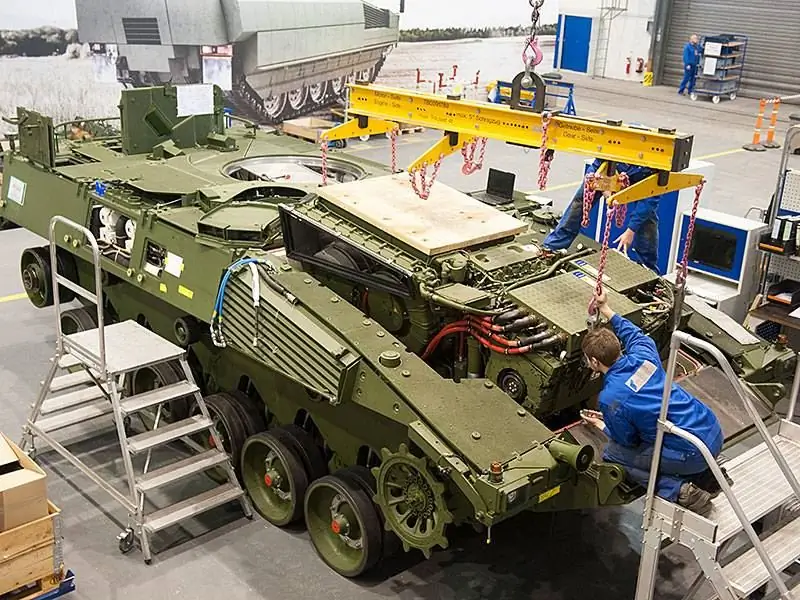
Excellent mobility in the toughest conditions is the paramount characteristic of all military vehicles. However, it is much more difficult to achieve this for armored vehicles, but it is extremely important so that they can successfully perform their tasks
Mobility is very important for armored vehicles, but at the same time it competes with other critical characteristics, such as, for example, ensuring the survivability of the vehicle and crew. And here this requirement can easily conflict with the requirement to maintain mobility. However, it is clear that soldiers, whose safety depends on such vehicles, need increased off-road patency, faster acceleration and higher speed, all without negatively affecting survivability. These demands are driving the development of new power packs and chassis systems in order to find optimal solutions to meet these often conflicting requirements. However, in order to comply with them, a combination and balance of a number of design parameters is necessary. These include the characteristics of the suspension system, which directly affects the quality of movement, the support surface of the tracks or wheels, which determines the ground pressure, vehicle ground clearance and engine output. The last characteristic is considered to be the most important and the most difficult to achieve. This is due to the fact that even in the issue of generating and distributing engine power, the designer has to make compromises, sometimes even stepping on the throat of his own song. The increase in power in an armored vehicle is limited by factors such as the volume of the engine compartment, the need to maintain a range, weight restrictions and the need to meet the power requirements of on-board systems, for example, communication equipment, navigation systems, sensors, and active and passive protection systems.
Effective protection against today's evolving threats is imperative, especially those that place the greatest demands on the powertrain and undercarriage. Protection almost inevitably means armor, and armor adds bulk. A contradiction arises that forces us to make inconvenient trade-offs: as the threat level rises, the level of protection must also be increased. An increase in the level of protection, as a rule, translates into a need for additional armor, and additional booking can contribute to an increase in the mass of the vehicle. Maintaining or improving the running characteristics of an armored vehicle inevitably entails an increase in engine power and efficiency of the transmission and power drives connected to it. However, the weight of a vehicle is also determined by its size: the larger the vehicle and the surface area that must be armored, the heavier it becomes. Thus, the new power unit (engine with transmission and drives) must not only be more powerful, but it must at least fit into the allocated volume or, preferably, have a lower total volume. This criterion, first of all, is absolute for power units designed to modernize existing armored vehicles, but it is also highly desirable for new platforms.
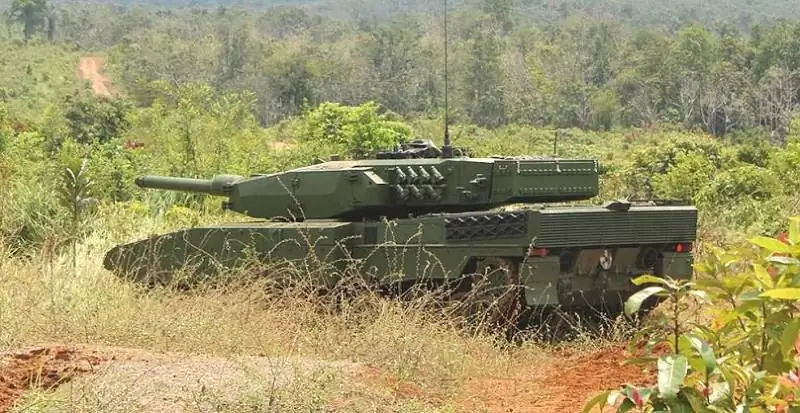
The generally accepted value for the level of mobility provided by an armored vehicle is the so-called power density, or the ratio of power (most often in horsepower) to the mass of the vehicle. This relationship, although it does not take into account all the possible factors that determine mobility, is a suitable, albeit crude criterion, and is useful both as a design parameter and as a tool for comparing different machines. As a rule, the higher the specific power, for example, in hp. per tonne, the better the overall driving performance that the machine will show. Despite the fact that when evaluating a vehicle, its maximum speed is often taken into account, for a combat vehicle, acceleration or engine throttle response (the ability to quickly and smoothly transition from stable operation at minimum power to maximum power) may actually be much more important. characteristic. Often overlooked in vehicle performance, the ability to quickly accelerate and move quickly to safety in response to attacking action is invaluable. It directly affects the survivability of the vehicle and its crew. Thus, the available power not only contributes to increased mobility, but also survivability, especially when used in combination with self-defense measures, including sensors for detecting a shot and laser irradiation, as well as passive and active countermeasures.
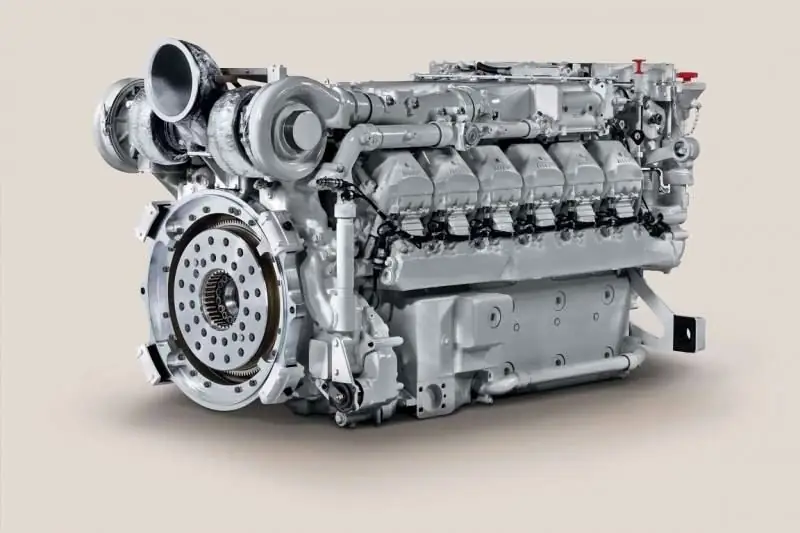
Power in small
Despite individual cases of using gas turbine engines, such as in the M1 Abrams family of main battle tanks (MBT) produced by General Dynamics, the most popular engine for armored vehicles continues to be a diesel engine or, more precisely, a multi-fuel diesel engine. One of the leaders in the production of power units is the German company MTU. Its integrated approach is that in a single "power unit" includes not only the engine, transmission and power drives, but also subsystems for air supply and filtration, cooling, power generation and others. Each of the components of the power unit is carefully designed and assembled in order to obtain the most compact and efficient solution. MTU recognizes that for a combat vehicle designer and integrator, power-to-volume ratio is critical. Giovanni Spadaro, Head of SOEs at MTU, explained that for them “the integration of all components into a single system is very important, we are tirelessly developing our philosophy of symbiotic development of all parts of the developed solution. For us, this means that literally everything, architecture, concept, software and all parameters, is aimed at improving the characteristics of the final complete power unit. " The impact of this approach on the final platform is enormous, given the close collaboration with major leading military vehicle manufacturers such as Krause-Mafei Wegmann (KMW), Nexter, BAE Systems and General Dynamics. A spokesman for General Dynamics Land Systems explained: "As for the power unit, more power is better, smaller size is better, cheaper is generally excellent, but with a mandatory increase in levels of safety, reliability, quietness and maintainability."
MTU has demonstrated that the adaptation and modification for military purposes of commercial power units is suitable for light and medium armored vehicles, for example, the ARTEC Boxer four-axle combat armored vehicle, which is equipped with an MTU 8V199 TE20 diesel engine. However, for heavier armored vehicles and tanks, their own engines are needed, such as, for example, the 880 and 890 series engines, designed specifically for installation in heavy military platforms. The capabilities of modern power units are demonstrated in the Puma tracked infantry fighting vehicle. Spadaro said that “the MTU power unit for the Puma includes the gearbox, starter / generator and cooling and air purification systems. The diesel engine MTU 10V 890 is known for its very high power density and compact dimensions. Compared to other military engines of the same power class, weight and volume have been reduced by about 60 percent.” The Director of Specialty Engines at MTU commented that "This unit is more compact than any previous power unit." The benefits of MTU motors are especially evident when installing power units in previous generations of machines. Its engines from the EuroPowerPack range were used by the French company GIAT (now Nexter) to replace the engines of Leclerc-EAU tanks for the United Arab Emirates. Engines of this family are also installed on the Challenger-2E MBT, while significant volume savings were achieved while increasing the range due to reduced fuel consumption.
Renowned for its heavy construction equipment, Caterpillar has become a premier supplier of engines for tactical and armored vehicles. Its offerings to the military are based on off-the-shelf commercial systems in use around the world. Hence the significant benefits - reduced cost associated with production volumes and the availability of technical support. Nevertheless, the company's developments are known for military use, for example, the C9.3 engine with an increased specific power of 600 hp. However, the real innovation is that the C9.3 is capable of varying its power rating. In order to meet the stringent European Euro-III emission requirements, it switches to a mode reduced to 525 hp. power. Caterpillar notes that “The benefit is that the user can choose the operating mode. It is possible to achieve maximum performance during active operation in the field, but during training or when working in areas with a civilian population, you can go into emission control mode. " In fact, this "switch" is rooted in technologies that Caterpillar developed for commercial systems.
The company is invariably chosen for programs of replacement and modernization of existing armored vehicle fleets. For example, its CV8 engine is currently installed on the British Army Warrior tracked infantry fighting vehicles. This work is being carried out under a contract with Lockheed Martin to upgrade the vehicle to the WCSP (Warrior Capability Sustainment Program) standard, which will extend the operation of the vehicles until 2040. Caterpillar is also changing the engine of the American Army's Stryker family of armored vehicles with a capacity of 350 hp. for the C9 engine with a capacity of 450 hp. The new engine "fits" into the volume occupied by the previous engine. The replacement is part of General Dynamics' proposal for an ECP-1 technical change, which includes a 910 amp alternator, suspension upgrades and other improvements.
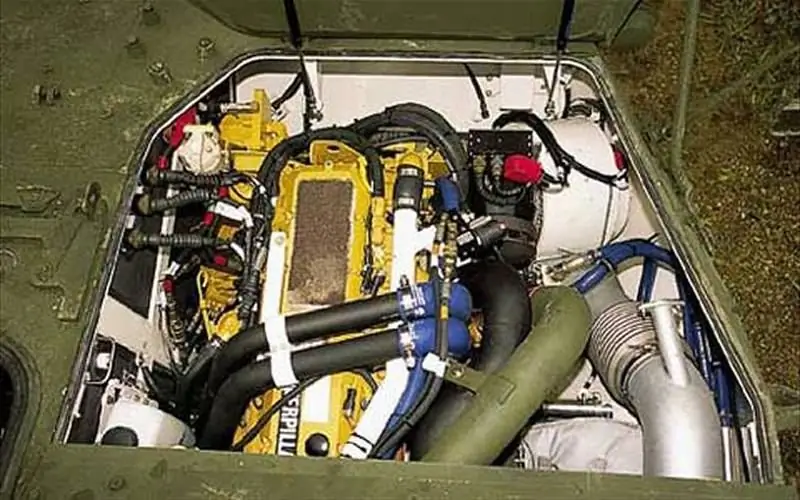
Electric actuators
Traditionally, power from the engine is transmitted mechanically to the wheels or tracks. Electric drives replace this physical connection with electric motors housed in drive wheels or sprockets. The energy to run these electric motors can be taken from batteries, an internal combustion engine, or both. The "hybrid" approach uses either a diesel or a gas turbine engine that, free of mechanical connections, can now be installed anywhere in the chassis, giving designers more design freedom. It is also possible to install two motors, which was implemented by BAE Systems in its mobile test facility HED (Hybrid Electric Drive). BAE Systems spokesman Deepak Bazaz noticed that two HED engines are connected to generators and batteries, which allows it to work in different modes: one engine works in idle mode, saving fuel, two engines work when more power is needed, or in silent observation mode. works only on rechargeable batteries. The HED concept is implemented on the tracked AMPV (Armored Multipurpose Vehicle) platform, but it is planned to be scalable and used on a vehicle of any weight category, both wheeled and tracked. The experimental power plant HED was modified by BAE Systems for a hybrid concept by Northrop Grumman as part of its proposal for a ground combat vehicle of the American army GCV (Ground Combat Vehicle).
In a paper by the NATO Technology Research Organization, "Hybrid electric vehicles are superior in speed, acceleration, climbability and quietness to power-driven vehicles … while fuel savings can range from 20 to 30 percent." The electric motors also provide almost instant acceleration, good throttle response and better traction. The latter directly depends on the improved torque that is inherent in electric motors. For combat vehicles, this means several advantages: less reaction time when moving to cover, more difficult to get into and better cross-country ability. The HED unit is powered by two six-cylinder engines, a custom-engineered QinetiQ transmission and 600-volt lithium-ion batteries.
Another attractive aspect of the electric drive is its ability to generate more efficient and higher levels of electrical energy. The power plant of the Northrop Grumman / BAE Systems GCV platform will be able to provide 1,100 kilowatts, although it is significantly smaller and lighter than traditional power units. However, since energy storage is an important part of the hybrid electric drive, battery mismatch is becoming a major problem. Therefore, several types of advanced batteries with higher energy density are currently being considered for hybrid vehicles, including lithium ion, nickel metal hydride, nickel sodium chloride and lithium polymer. However, all of them are still at the stage of developing the technology and have certain drawbacks that must be solved before they are recognized as suitable for use in military applications. Another area of work that needs to be developed so that hybrid drives can be massively installed on armored vehicles is the removal of the design constraints of modern traction motors. Although successfully integrated into HED-type demonstration prototypes, these systems have limitations in size, weight, and cooling. Until these problems are resolved, all electrical circuits, despite their advantages, will remain an illusion for armored vehicles.
However, many research organizations remain interested in the electric drive concept. For example, under contracts from the Defense Advanced Research Projects Agency (DARPA), QinetiQ will test its hub motor (gearmotor) concept by setting it up for pilot test mock-ups. Numerous gearboxes, differentials and power drives will replace the powerful compact electric motors in the wheels of the machine. It is possible that this concept can also be implemented on existing wheeled armored vehicles. In fact, in June 2017, BAE Systems signed an agreement with QinetiQ to introduce new electric drive technology into combat vehicles. A representative of the company BAE Systems said that this will "offer customers a proven low-cost technology that will enhance the capabilities of current and future combat vehicles."
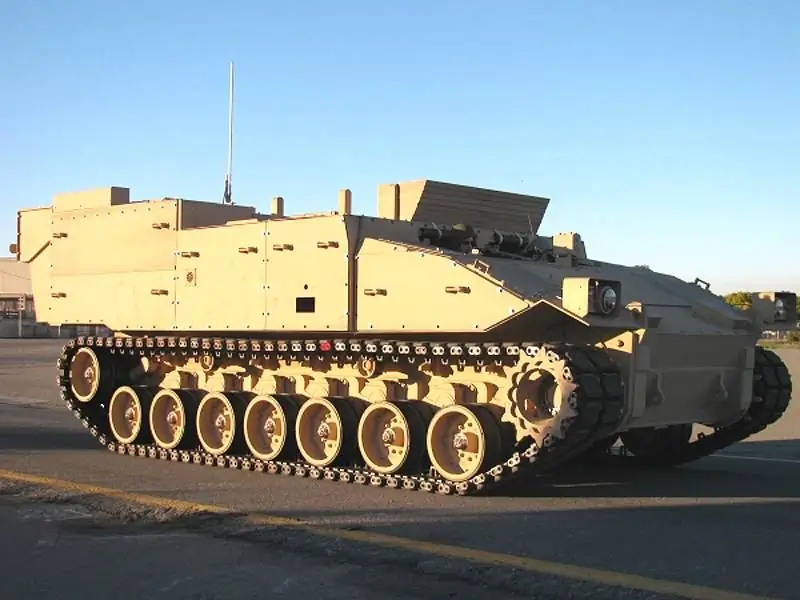
Future challenges of power
Over the past decade, the needs of combat vehicles for electrical power have increased several times. Mark Signorelli, head of combat vehicles at BAE Systems, noted that "in the future, it will be increasingly difficult for armored vehicles to meet electricity needs." Attempts are under way to address this growing problem. For example, a 300 amp CE Niehof generator is being considered for the M2 Bradley family, and two 150 amp generators for the new AMPV platform. Mr. Spadaro from MTU stated that “the key factors that have influenced and are influencing the development of solutions for generating more power are the constantly growing mass of MBTs and wheeled vehicles (mainly as a result of requirements for higher levels of protection) and at the same time the need for more electricity for onboard systems of any type, be it electronics, protection systems and comfort for the crew, for example, an advanced air conditioning system. " MTU believes that “they are being addressed by the deeper integration of the electrical components into the power unit. A good example here is again the aforementioned power unit MTU of the Puma armored vehicle, which includes a starter / generator with a rated power of 170 kW, supplying current to two cooling fans, and an air conditioning refrigerant compressor."
The power of armored vehicles directly affects combat capabilities and survivability. The main criteria for survival on the battlefield are as follows: "take all measures so as not to be noticed, if seen, not to be hit, if you are hit, not to be killed." The first is facilitated by the ability to move to where the opponent does not expect you. The second requires fast acceleration and good maneuverability to find cover and is complicated by the enemy shooter's ability to effectively capture the target to kill. And the third is determined by the ability to take appropriate passive protection and employ passive and active countermeasures. However, each of these criteria can adversely affect others. For example, additional armor increases mass and, as a result, mobility.
Advances in the field of power plants for armored vehicles, new engines, transmissions and power drives, innovative methods of integration and layout allow developers of military equipment to satisfy the most daring wishes of customers. Many of the improvements that we see on military platforms are directly taken from commercial projects: engines and on-board computers, digital electronic control, automatic monitoring of the state of systems, electric drives and energy storage, and, finally, practical implementations of hybrid solutions. However, challenges to this delicate balance are forcing industry to develop more and more innovative solutions.