Many VO readers liked the story about mortars of different times and peoples, but they felt that they should tell in more detail about such a miracle of 19th century technology as the 920-mm Mallet mortar. Well, we fulfill their request.
By the time the Eastern War broke out (1853-1856) in 1853, Britain's most powerful and heavy land gun was the 13-inch mortar, which could fire 167 pounds of shells. However, it soon became clear that something even more powerful was needed for the Crimea, and the talented English engineer Robert Mallett wished to design this very "something". Since such a weapon turned out to be too large, he decided to make his huge mortar sectional so that it could be delivered to the site and assembled in parts. In this way, such an important problem as the laboriousness of delivering heavy guns to the battlefield was solved, which, on top of all other difficulties, was also very much hampered by the lack of roads. However, Mallet's ideas were too much at odds with the practice that existed at that time and caused distrust among the military.
Mallet's first project was dated October 1854. In accordance with it, he wanted to do without "pillows" made of wooden wedges or bars, which were usually placed under the muzzle of the mortar when aiming at the target and to give its barrel a given elevation angle, and to do with the emphasis directly on the carriage platform. He also proposed to make it from three rows of hewn logs, stacked on top of each other crosswise to fix the trunk on it at an inclination of 45 °.
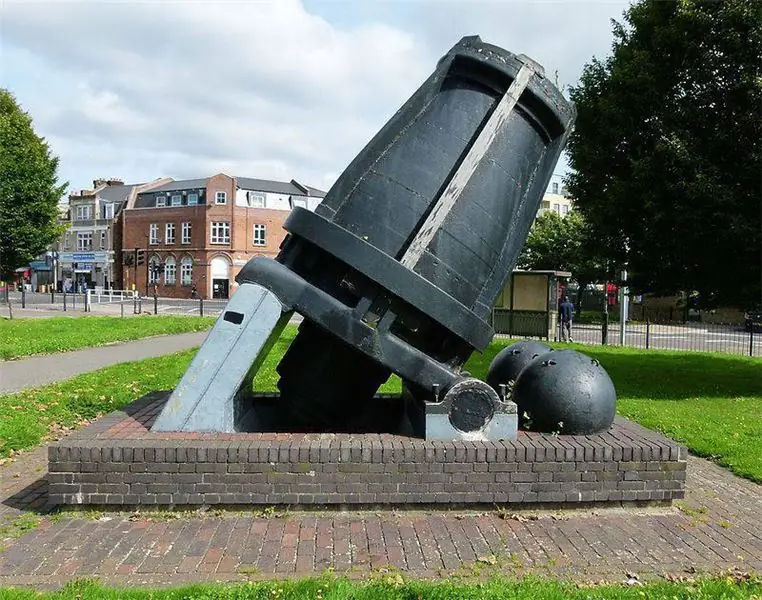
Mortar Mallet in London, on Green Terrace.
In December 1854, he presented his project to Captain Boxer, who later became famous for the creation of his rifle cartridge, and to other experts at the Woolwich Arsenal. But already in January, Mallet realized the importance of using such mortars not only on land, but also at sea, and considered it necessary to increase the functionality of his creation as a whole. To this end, he changed the design and made the weapon itself, let's say - "more perfect", so that its placement does not require logs and allows to a greater extent to change the angles of its aiming at the target.
The Artillery Upgrade Committee reviewed his new proposal in January 1855. But he turned out to be not ready for such revolutionary innovations and focused all his attention on the fact that the proposed solutions were not tested in practice and were too unusual. Mallet quickly got tired of all these nit-picking and on March 24, 1855, he wrote a letter to the Prime Minister of Great Britain, Lord Palmerston. Palmerston was impressed by the capabilities of the new weapon, and he invited Mallet to an audience. Nevertheless, even the appeal to the "top" could not overcome the stubbornness of the officials sitting in the Committee, and they in every possible way hindered the implementation of its project. But Lord Palmerston was not used to giving in. Therefore, on May 1, 1855, he declared to General (later Field Marshal) Hugh Dalrymple Ross, Lieutenant General of Artillery, that he was so confident in the success of the Mallet project that he assumed, as Prime Minister of the kingdom, all responsibility for its implementation.
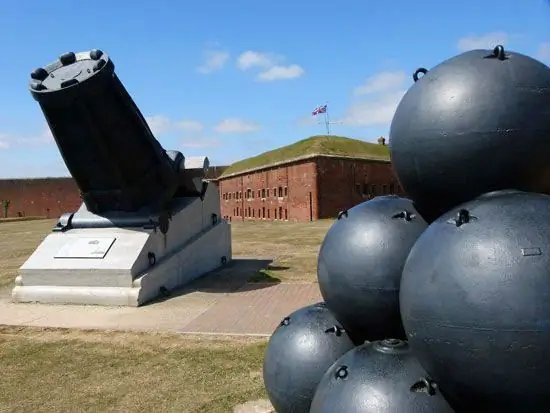
Mortar Mallet. Fort Nelson.
Only then did the Artillery Committee organize a tender for the project. On May 7, 1855, the Thames Iron Walk of Blackwell, where the famous Blackwell frigates were built, announced that they could make two Mallet mortars in just 10 weeks from receipt of the order at a cost of £ 4,900 each. Exceeding the weight of 35 tons was to be charged with a fine of 140 pounds sterling per ton. The offer was immediately accepted, and the next day the order was placed.
Meanwhile, the company's employees discussed all the specifics of order fulfillment and found that making castings, bending and welding wide and heavy rings that made up the barrel of the mortar was too difficult a task and could delay the execution of the order. Therefore, they proposed to first cast square sheets of iron, and only then cut these rings out of them, thus not resorting to bending and welding, while stating that they would agree to the project only if this condition was met. Mallett agreed to this very reluctantly, but nothing could be done. Work on the manufacture of parts for the mortar began on June 11, 1855, and already two weeks were enough to prove the viciousness of the proposed method. The company had to abandon it, as a result of which it … went bankrupt. Litigation began, the conclusion of contracts with the legal successors of the bankrupt, the calculation of costs, since part of the work had already been done. As a result, three firms had to finish work on mortars at once: Meir & Co, Horsfall & Co from Liverpool and, in part, Fawcett, Preston & Co. The latter turned, drilled and machined large castings supplied by Horsfall & Co. Not surprisingly, delays followed one another. Only in March 1857, work on the mortars was completed, and they were handed over to the government a month later in May - 96 weeks after the issuance of the contract and more than a year after the end of the Crimean War. That is, when these mortars were no longer needed by anyone. But despite this, 50 more shells were made for them at a price of £ 16 per ton, which were produced by the Hood company.
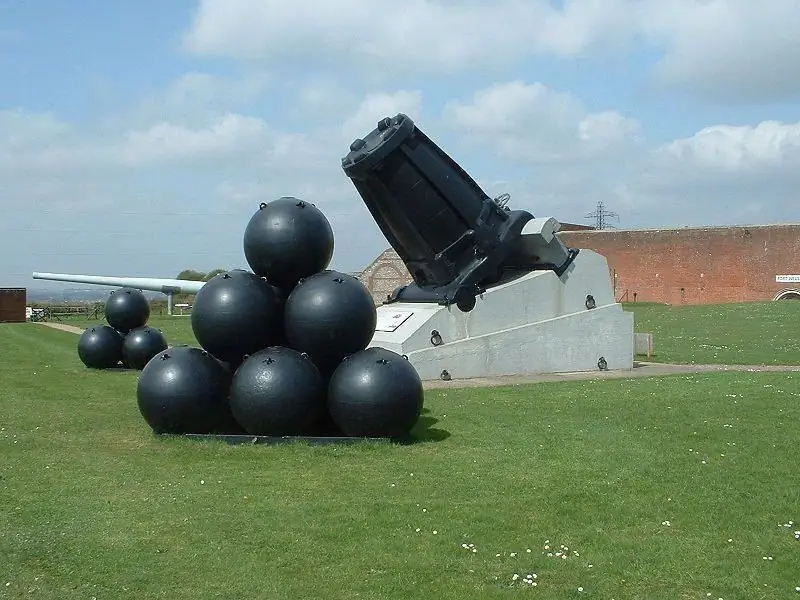
Mallet's mortar and shells.
The shells were of three types: light, medium and heavy, weighing 2362 to 2940 pounds respectively. The projectile's projectile charge weighed 480 pounds. The propellant charge consisted of bags of gunpowder, 10 pounds each and could not be more than 80 pounds according to calculations. The internal cavity of the bomb was slightly eccentric, so that when flying out of the barrel, the projectile would not tumble in the air, but flew the heaviest part forward. The fuse was of the Twice system, that is, it caused a bomb to explode from hitting the target, but it could also ignite with an ordinary fuse cord.
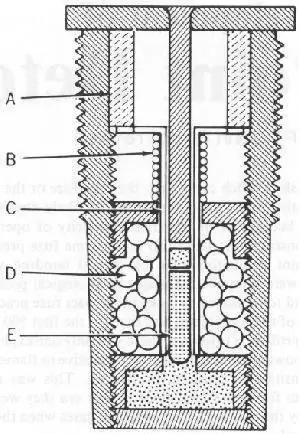
The device of a mechanical fuse "Tays" for shells of smooth-bore and even rifled shells of the middle of the 19th century, which caused their explosion when hitting an obstacle: A - lead ring, B - spring, C - safety tube, D - lead balls, E - glass ampoule with shock composition (explosive mercury and an additional charge of pyroxylin). The projectile was inserted into the barrel so that the fuse was looking forward. When fired, the ring (A) bent or cut off the top of the safety tube (C) by inertia; and the safety spring (B) threw it out of the projectile along with the lid, exposing a glass ampoule with explosive mercury and a pyroxylin block (E) for exposure to the surrounding lead balls (D). When hitting an obstacle, the balls broke the ampoule, which initiated the explosion first of the ampoule itself and the pyroxylin block, and then of the main charge. True, sometimes shells with such a fuse could explode in the air!
Technologically, the mortar consisted of the following parts:
1. Bases made of cast iron 30 inches thick and weighing 7.5 tons. This part had trunnions, a flange for attaching longitudinal rods and a groove - a stop for a wedge-shaped support, which helped to set the elevation angle of the barrel. It also drilled a hole 37 "in diameter at the bottom and flared up to 48" and 13 "deep.
2. The mortar chamber was forged from wrought iron about 70 inches long and weighing 7 tons. Its maximum outer diameter was 36 inches - and was reduced by three steps to 24 inches. It was reinforced with two layers of wrought iron hoops and one heavy hoop at the very end. The body was in the shape of a cone for a cast-iron base. The chamber for the propellant charge was also tapered, having a depth of 48.5 inches, a diameter of 14 inches at the base and up to 19 inches "at the exit." The front part of the chamber had a bowl-shaped shape for a snug fit of the spherical projectile.
3. The muzzle of the gun, 80 inches long, consisted of three large rings of wrought iron. In turn, these three rings were assembled from 21, 19 and 11 narrower rings, located so that a detachable connection was obtained. The largest hoop was 67 inches in diameter and 19 feet long; the smallest is 40 inches in diameter. The thickest part of the barrel was 16 inches thick and the thinnest was 9 inches.
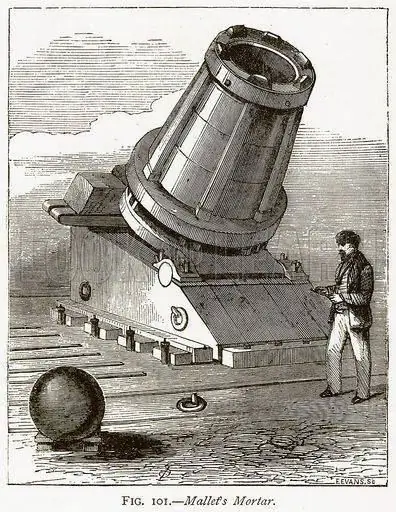
Mallet's mortar with antique engraving.
4. Six almost square-section wrought iron pulling down the barrel connected the upper barrel ring and the cast iron base, tying them together. The cross-sectional area of each rod was 21 sq. inch. On the base, they were fixed with wedges and dowels. These rods went into square sockets on the barrel ring, and were held on it with spring ring locks.
When assembled, the mortar weighed 42 tons and was arranged so that its heaviest part had a weight of no more than 12 tons. This made it possible to transport and assemble it in the right place using a crane. The barrel of the mortar was placed on a platform covered with an iron plate, which provided a support for two "pillows" - heavy beech wedges, allowing you to change the angle of the shot from 40 ° to 50 °.
Since the peace with Russia had already been signed by this time, and even the gravel for the "pillow" needed for testing required money, which, as always, was not enough, the Minister of War considered that only one mortar should be tested. On 19 October, shooting began in the Plumstead Marshes area. After seven shots, one of the outer rings cracked, and they decided to stop firing. The mortar was repaired for 56 pounds, since it was easily disassembled, and on December 18, 1857, the tests were continued. This time, after six shots, the central hoop of the lower ring was torn apart. It was decided to make another refurbishment for £ 156. In the meantime, the Royal Laboratory prepared twenty lighter projectiles weighing £ 2,400 at a cost of £ 11 each. They started firing on July 21, 1858. However, several cracks appeared in a number of parts. These minor breakdowns were repaired by the royal gun factory, and the shooting was repeated for the fourth and last time on July 28, 1858. On that day, the farthest shot was fired at 2,750 yards with a 2,395 pound projectile at a 45 ° angle with a full 80 pound load. The flight time of the projectile to the target was 23 seconds. However, then breakdowns of individual parts followed one after another. And although the cost of repairs was supposed to be only £ 150, the military refused to finance it. Thus, the entire project was spent 14,000 pounds sterling of public money, including the cost of 19 rounds, at an average price of about 675 pounds each - too high, as it was considered, a high price for a hopeless project.
And so the largest mortar in the world sank into oblivion. Back then, armament costs were not considered a priority. The armies spent more money on oats than on cartridges and quiver feathers than on finding new lethal machines that their inventors almost forced the military to do. Well, in the end, both mortars ended up in museums and exhibition grounds, where they stand on their concrete pedestals, surprising people with their appearance and recalling the talent of the engineer Mallet, who was only a little (and fortunately!) Late for the battles of the Crimean War.