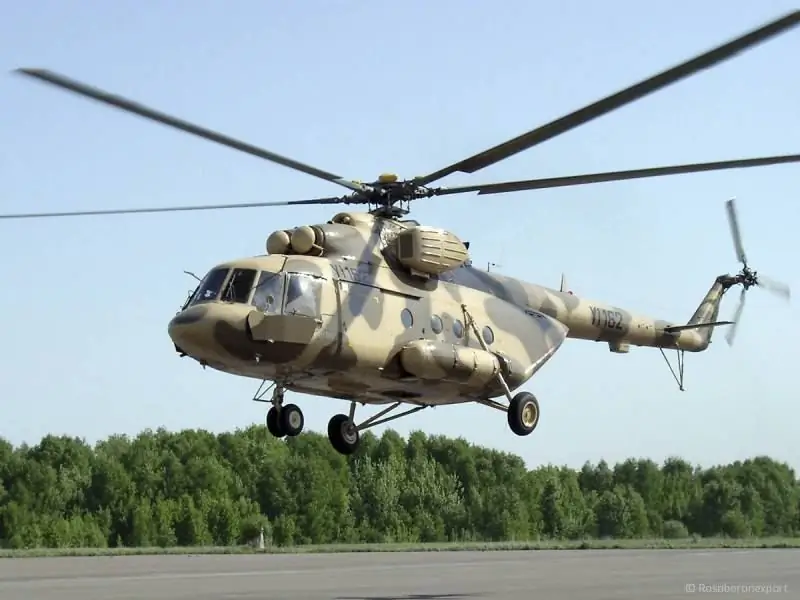
Throughout the history of helicopters, various designs of the carrier system were regularly proposed, but only one of them became classic and subsequently received significant development. Other solutions, providing for different options for the propeller drive, blade designs, functions, etc., could not compete with it. Often, such an outcome of a bold project was due to objective shortcomings and problems.
Technical classics
The classical helicopter scheme provides for several fairly simple solutions. In the fuselage of the machine is placed a power plant with a gearbox that delivers torque to the main and tail rotor. The large diameter main rotor is based on a swashplate, which provides a change in lift and / or maneuvering, and also has several large aspect ratio blades.
This design is relatively simple, it is well developed and lends itself to easy rebuilding and scaling to meet existing requirements. In addition, it is devoid of some disadvantages, such as the need to seal joints in pipelines or the risk of overlapping blades.
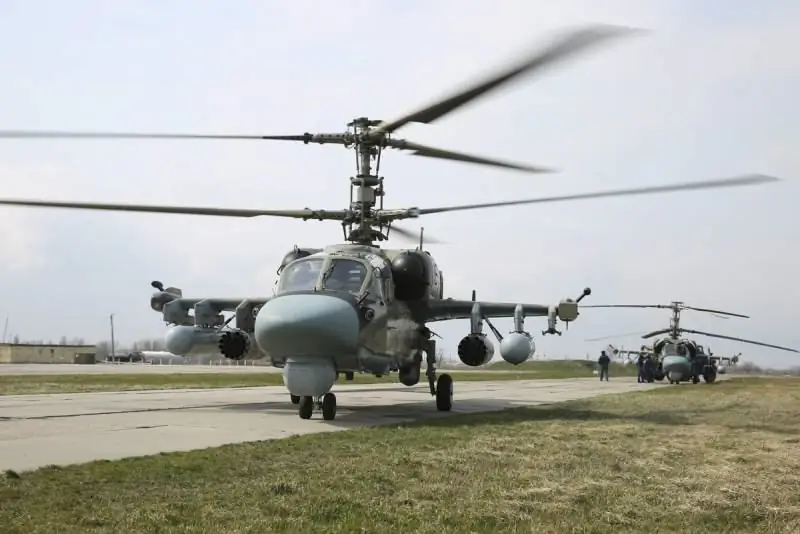
However, there are also disadvantages. The helicopter of the classical scheme has limitations on the horizontal flight speed associated with the specifics of the flow around the rotor blades. In some modes, other negative phenomena may occur, such as a vortex ring. With a single main rotor, you have to design a long and strong tail boom to accommodate the tail rotor.
The development of the classical scheme led to the emergence of multi-rotor helicopters with longitudinal, transverse or other placement of several bearing systems. A coaxial scheme has become widespread, in which two screws of a traditional look are assembled on a single bushing. Also, the classic support system and a number of its units became the basis for several alternative designs.
Jet propeller
The single-rotor helicopter is faced with the problem of reactive torque, and various solutions have been proposed to deal with it. Back in the thirties, the idea of a rotor with a jet drive appeared almost simultaneously in several countries. Such a propeller is not connected to the engine inside the fuselage and, accordingly, does not force it to rotate in the opposite direction.
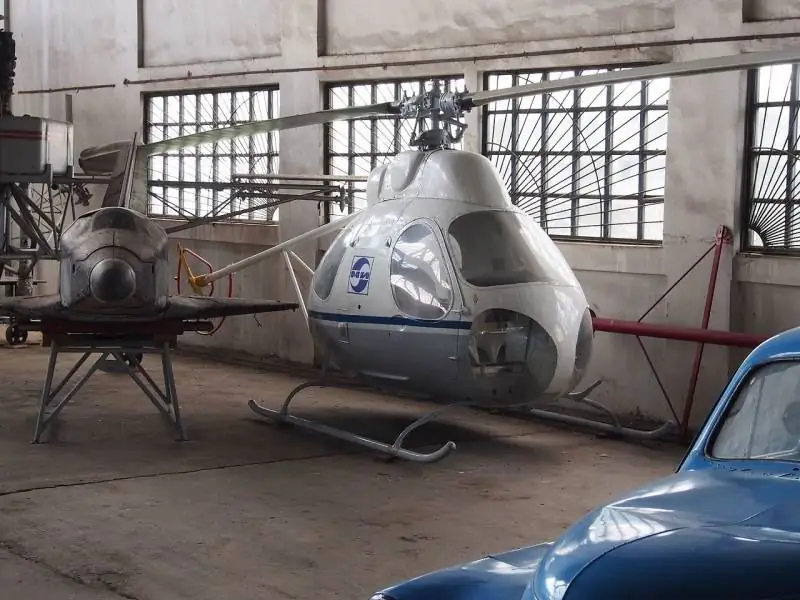
The jet rotor is distinguished by the presence of its own engines at the tips of the blades. The propeller can be driven by a compact turboprop or ramjet engine. Also known are designs with the supply of compressed gases from a gas turbine engine in the fuselage to the nozzles or to the combustion chamber in the blade.
The jet rotor idea received a lot of attention in the fifties and sixties; a number of pilot projects have been developed in different countries. They were offered as light vehicles of the Dornier Do 32 or B-7 ML type. Mile and Hughes XH-17 heavy transport helicopter. However, none of these samples has progressed beyond small-scale production.
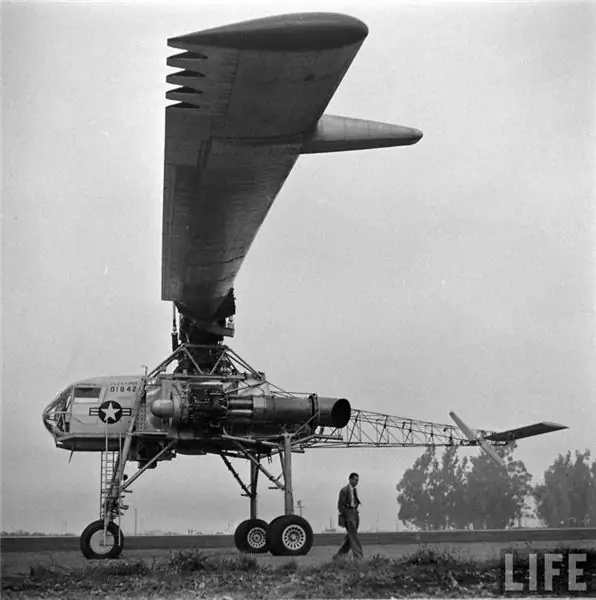
The main problem with the jet propeller is the complexity of the hub. Through it, compressed gas and / or fuel must be supplied to the movable blade, which requires transmission and sealing means. On the blade itself, it is necessary to place an engine of one kind or another, which imposes new requirements on its design. Building a robust design with these capabilities proved to be too difficult, and the expected benefits could not justify the effort.
Crossed blades
In the thirties, a so-called scheme was proposed. synchrocopter. This concept proposes the use of two two-bladed rotors, the hubs of which are placed at a minimum distance with the axle camber outward. The propellers must rotate towards each other, and the special design of the gearbox excludes overlap of the blades.
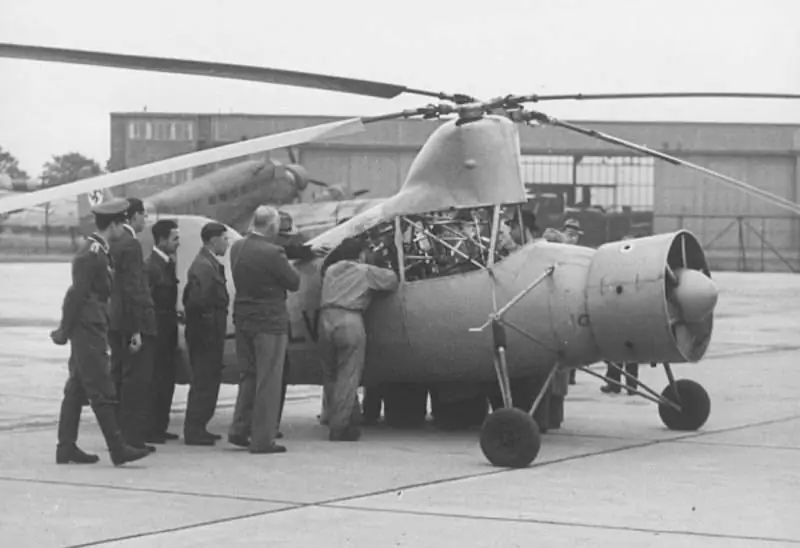
The synchrocopter carrier system is capable of creating the required lift and providing flight in the same modes as the classical scheme. It has the advantage of being able to increase the overall thrust and lifting capacity, and the expansion of the thrust vectors increases stability in hovering and other modes. In this case, the reactive moments of the two propellers compensate each other and eliminate the need for a steering system.
However, synchrocopters are not widely used. In the thirties, such equipment was produced by the German company Flettner, and since 1945 this topic has been dealt with in other countries. The helicopters of the American company Kaman Aerosystems are best known. Until a certain time, synchrocopters were in demand, but then the direction faded - now there is only one sample in the series. For all the time, no more than 400-500 serial machines of this class were built.
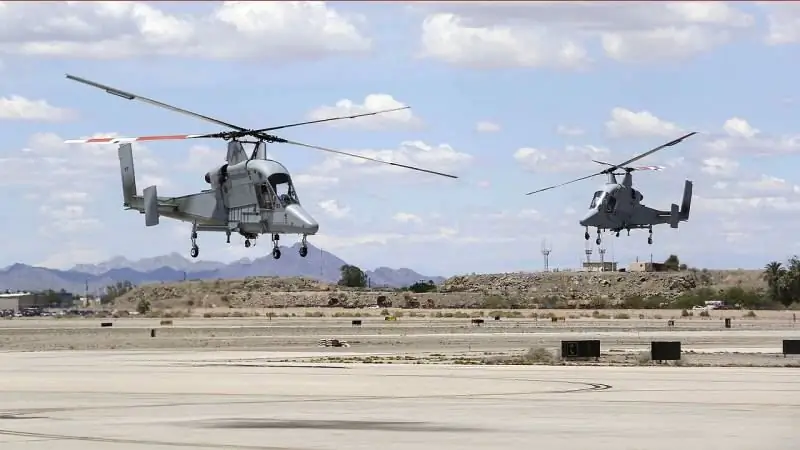
The main disadvantage of a synchrocopter is the complexity of the gearbox, which delivers torque to two closely spaced propellers. A single rotor drive with the same characteristics turns out to be much easier. In addition, a pair of two-bladed propellers have limited thrust potential. So, the modern "heavy" synchrocopter Kaman K-Max lifts no more than 2700 kg and loses in this respect to many helicopters of the classical scheme.
Spin and stop
The idea of combining a rotating propeller and a fixed wing is known. In this case, the rotation of the main rotor is used for takeoff and acceleration. At a certain speed, the propeller must stop, and its blades must turn into a fixed wing. This makes it possible to develop a high flight speed, but requires the development and implementation of new solutions.
As an example, consider the Sikorsky X-Wing project, which has been developed since the mid-seventies to complement the S-72 helicopter. The latter was a helicopter with a main and tail rotor, equipped with a developed wing of a small sweep. On the sides of the fuselage there was a pair of gas turbine engines that provided power to the shaft (for propellers) and created jet thrust (for high-speed flight).
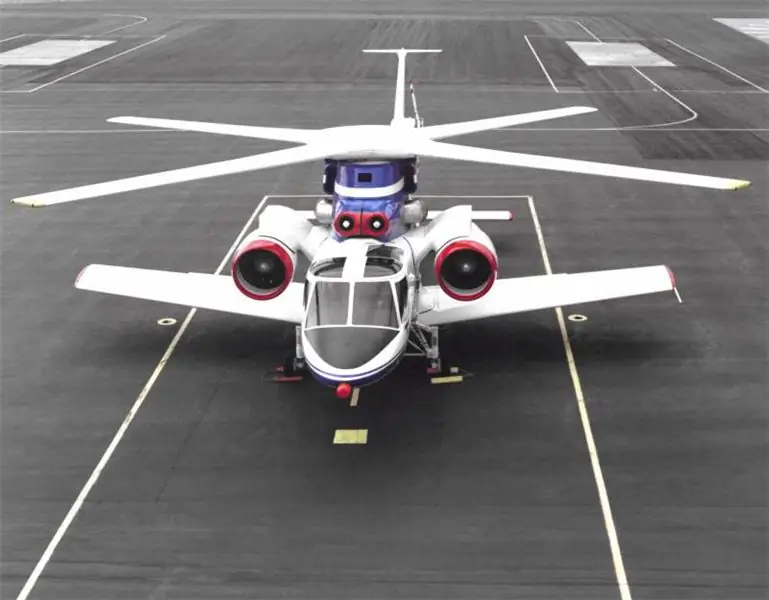
The X-Wing carrier system received a disc fairing hub equipped with a swashplate with a common pitch only. We used rectangular blades with a vertically symmetrical profile. On the leading and trailing edge of the blade there were openings for the release of compressed air from the compressor outside. The air, due to the Coanda effect, was supposed to "lengthen" the profile of the blade, helping it create lift. Depending on the way the air is supplied, the blade can work equally efficiently when rotating and in a stationary position.
The X-Wing system was successfully tested in a wind tunnel and was even installed on an experienced S-72. However, shortly before the planned flights, in 1988, NASA and DARPA ordered to stop work. With all the expected benefits, the unusual carrier system was too complex. In addition, the project stretched out for more than 10 years, and its cost exceeded the permissible limit. For this reason, the X-Wing concept was not further developed.
Lens in flight
Right now, the French company Conseil & Technique is working on the concept of a light air taxi helicopter with an unusual carrier system. The proposed design of the propeller loses to the traditional one in terms of the created lift at takeoff and landing modes, but differs in greater simplicity and the ability to create increased thrust in horizontal flight. The ability to reduce noise is also stated.
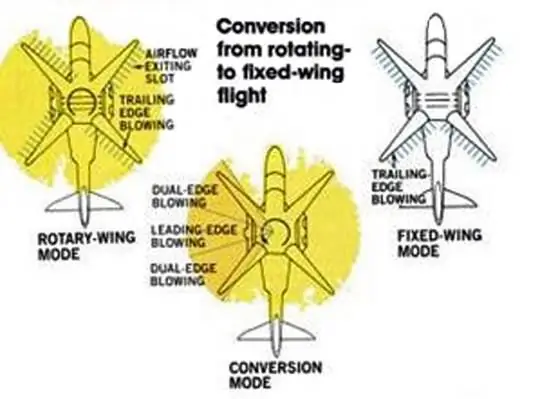
The original propeller is built on the basis of a lenticular disk that occupies 70% of the swept area. It is proposed to mount short blades of the airfoil along its edges. The possibility of placing the swashplate is not reported; traction control can be performed by changing the speed.
Tests have shown that during horizontal flight, the disc part creates a significant lifting force, due to which the structure as a whole bypasses the traditional design propeller in terms of characteristics. In addition, it was possible to bring the angle of attack to 25 ° without stalling the flow. The aircraft under development, according to calculations, will be able to reach speeds of up to 200 km / h.
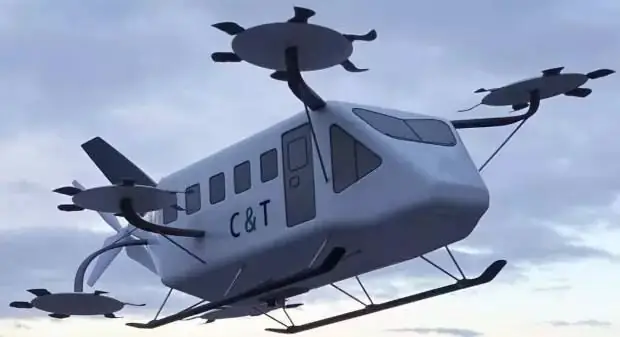
The project of the Conseil & Technique company is still at the stage of research and design development. Probably, in the near future it will be brought to tests on mock-ups, after which a full-fledged experienced multi-rotor helicopter may appear. It is not known whether this alternative design will be able to solve all the tasks and find a place in the aviation industry.
Looking for alternatives
Long decades of existence and active operation of helicopters have shown all the advantages of the classic design of the carrier system. Attempts to create alternative schemes that have minimal similarity with it have not yet been crowned with special success. However, scientists and engineers do not stop working and continue to search for promising ideas.
Another project of this kind is being created right now, and its results will become clear in the near future. At the same time, it is clear that none of the new bearing systems will be able to have a noticeable effect on the general state of affairs, and the classical scheme and various variants of its development will retain their place in aviation technology. However, new developments - subject to sufficient perfection - can find their niche, where their advantages will be most appropriate and profitable.