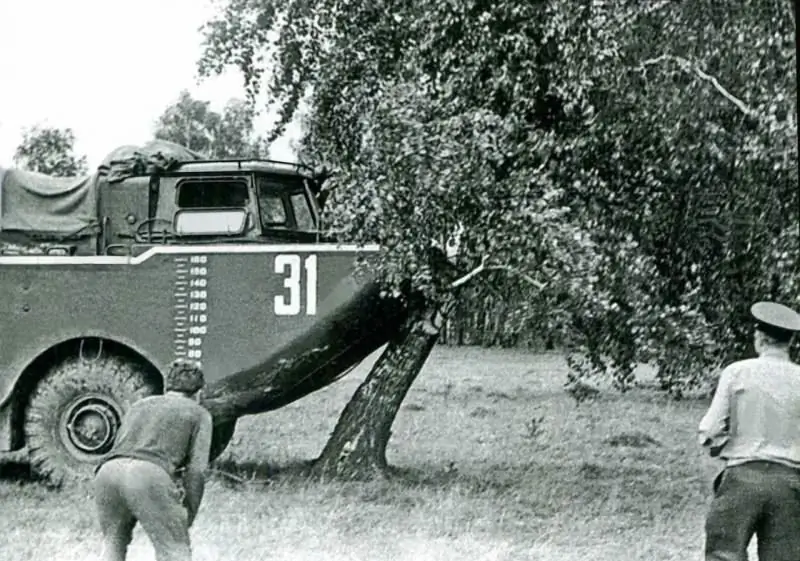
MVTU them. Bauman rushes to the rescue
In one of the previous parts of the cycle, about the development and development of machines of the ZIL-135 family, there was a mention of an amphibian with the index "B", which the head of the SKB "ZIL" Vitaly Grachev built for missilemen. It was on the basis of this machine that the Zilovites together with the scientists and engineers of the M. V. Bauman in the early 60s, they tried to build an amphibian with a plastic monocoque body. Even now, creating something like this is a non-trivial task, and 60 years ago it was revolutionary. And, of course, secret. There is no information about the work on the plastic monocoque body of the 135th series even in the well-known book “Overcoming off-road. Developments of SKB ZIL ". Only the mention of the frame ZIL-135B built on July 5, 1962 with a fiberglass body. According to the authors of the book, on July 24 of the same year, a four-wheeled amphibian was tested on a reservoir in Bronnitsy. At the same time, in 1965, an article by engineers V. S. Tsybin and A. G. Kuznetsov, dedicated to an amphibian with a plastic monocoque body, was published in the specialized and secret (for its time) magazine "Bulletin of Armored Equipment". Again, a monocoque body, that is, devoid of a frame. Subsequently, Professor Tsybin will become one of the founders of the domestic system for designing and creating elements of wheeled vehicles from composite polymer materials. The work was going on at the department CM-10 "Wheeled vehicles", which since 1953 was headed by the famous automobile engineer, chief designer of the Gorky Automobile Plant Andrei Aleksandrovich Lipgart.
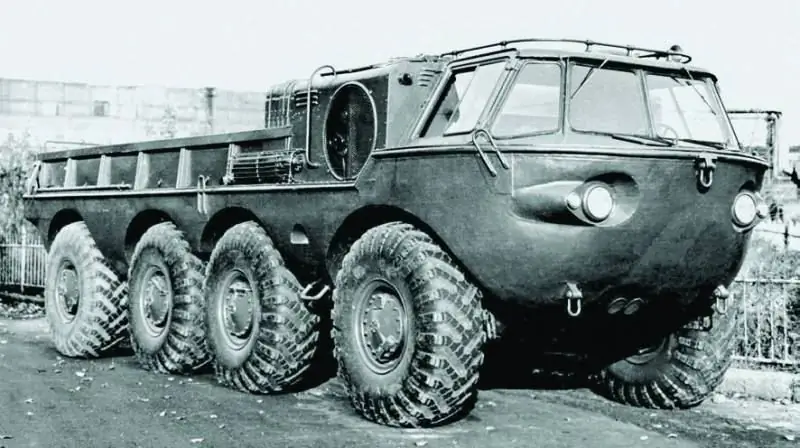
The choice in favor of a completely plastic body for the ZIL-135B was made due to the large weight of the original steel car. As you know, with the "Luna" rocket, the four-wheeled vehicle could not swim normally and once during the tests almost went to the bottom. Therefore, Vitaly Grachev tried not just to sheathe the amphibian with plastic panels, but to completely replace the metal in the structure with lightweight material. At ZIL, they did not know how to do this, therefore they turned for help to the Moscow Higher Technical School. Bauman.
One of the advantages of the all-plastic body was the reduction in the weight of the car: the material with high strength characteristics had a low specific weight. In addition, there is the possibility of manufacturing monolithic (seamless) body structures of any complexity and configuration with minimal costs for tooling and equipment. Traditional thin sheet steel did not allow simple and inexpensive manufacturing of streamlined housings. Plastic technology increased the corrosion resistance of the structure, reduced operating and maintenance costs, and made repairs easier. Researchers from MVTU noted among the pluses the almost complete absence of leaks with a bullet shot through the hull and the possibility of staining the material in bulk. Among the obvious disadvantages are high creep under prolonged stress, relatively high cost, low rigidity and low long-term heat resistance.
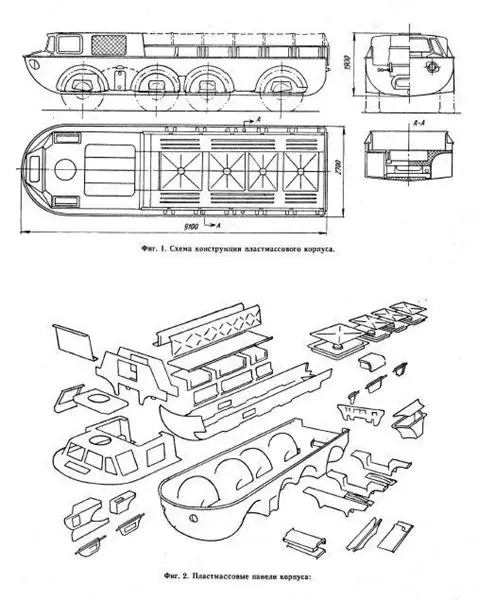
[center]
The basic ZIL-135B was a frame machine without a suspension, which seriously increased the load on the hull in motion. At the same time, the engineers could not change anything in the layout, otherwise this would lead to a complete reformatting of the design of the future missile carrier. The practice of copying the sizes and shapes of metal parts did not allow making aggregates similar in properties: plastic did not have the required rigidity. Three-layer elements made of fiberglass, foam and glue were chosen as the base material at MSTU. The metal was not completely abandoned. Steel were keelson (longitudinal power element of the hull-boat), braces of the towing device, edging of the hull and sides, instrument panel, mounting brackets for power units, sockets for drain plugs and inserts for wheel arches.
The main load-bearing system is an external monolithic panel, into which an internal panel with reinforcements and cross members between the wheel arches is inserted. The space between the panels is filled with foam with a specific gravity of 0.1-0.15 g / cm3… About the load-bearing elements of the load-bearing body further in the text of the article:
“There are also load-bearing elements between the wheel arches in the longitudinal direction: between the 1st and 2nd axles - box-section arches under the panels of the motor compartments, resting on the niches, the rear cab panel and the 2nd cross member; between the 2nd and 3rd, 3rd and 4th, 4th and rear cross-members - panels of horizontal and vertical reinforcements, forming box-section elements and resting on the side cross-members, and base reinforcements”.
The body was built from panels with a thickness of 2 to 8 mm, joined together with epoxy glue, as well as bolts, rivets and self-tapping screws. The main body material was fiberglass, consisting of polyester resin PN-1 and rope fiberglass TZHS-0, 8. The largest panel, weighing 900 kilograms and 8 mm thick, was molded by the contact method on a wooden mold. About 280 man-hours were spent on this.
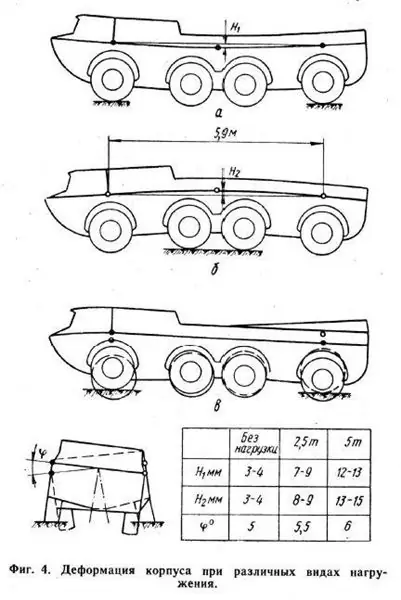
When the plastic ZIL-135B assembled using the new technology was put on the scales, it turned out that the designers won a whole ton of the amphibian's weight. This is about 10% of the weight of the steel ZIL. Further, the prototype had dynamic tests on the highway, on rough terrain, on a country road with an empty body, with full and half load. The lack of a suspension played a cruel joke here - it cut off the material under the wheel brackets. The high thermal load of the motor compartment led to the destruction of the amplifiers near the motor. Also, tests were carried out at the stand in order to find out the static deformation of the case under load. It turned out that the body bends, but, in comparison with the steel, only slightly. When an experienced amphibious all-terrain vehicle ran 10 thousand kilometers, it was dismantled. The power elements between the 1st and 2nd axles were destroyed due to the thermal effect of the motor, but everything else was in excellent condition, with the exception of a decrease in the tensile strength of the body elements during static bending by 43% at once. But here the blame was laid on the poor quality of PN-1 resin. Despite the fact that the engineers rather positively assess the results of the experimental work, the plastic ZIL never went into production. As did not go into a wide series and other plastic vehicles. Experimental work at MSTU has remained an example of Russian engineering creativity. But experiments with floating equipment at SKB "ZIL" did not end there.
"Dolphin" that swam fast
In the early 60s, almost simultaneously with the topic of ZIL-135B, the Karbyshev Central Research Institute puzzled SKB ZIL with an order for the development of a self-propelled pontoon. It was supposed to be used to guide floating crossings. Here the Zilovites also did not do without outside help: Doctor of Technical Sciences, Colonel-Engineer Yuri Nikolaevich Glazunov helped with the shape of the hull and the water-propeller. By the way, Dr. Glazunov was the creator of the pontoon park, and it was he who came up with the idea of a floating ZIL. According to the idea, the deck of the wheeled boat was to become part of the pavement for the transported equipment. At the same time, a sliding platform was mounted on the deck for transporting vehicles weighing up to 40 tons. The result was a self-propelled ferry, capable of transporting equipment on itself, docking in movable bridges, and also working as a tug. At the stage of sketches, the car was very unusual: on the water, the wheel boat moved stern forward, it was here that the wheelhouse was located. The general management of the development under the code "Shuttle" was led by SKB engineer Yu. I. Sobolev. When everything was ready for the production of amphibians, the main customer made a choice in favor of a similar machine developed in Bryansk. It is good that the decision was made before the construction of the car, otherwise it would not have been possible to repurpose it quickly. It cannot be said that the amphibian from Bryansk was better: the developers simply supported their model with the possibility of production. At ZIL, director Borodin categorically refused to put a military model into production. This played a major role in the choice of the military department. But Grachev did not despair, renamed the car "Dolphin", redrawn the layout and built one copy by the beginning of 1965.
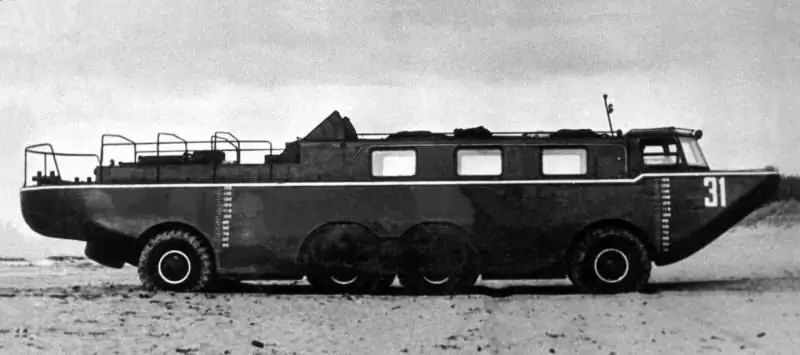

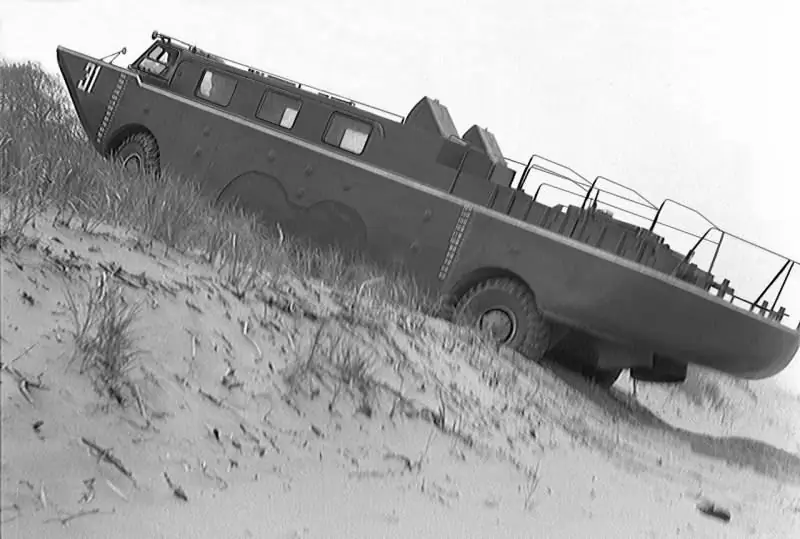
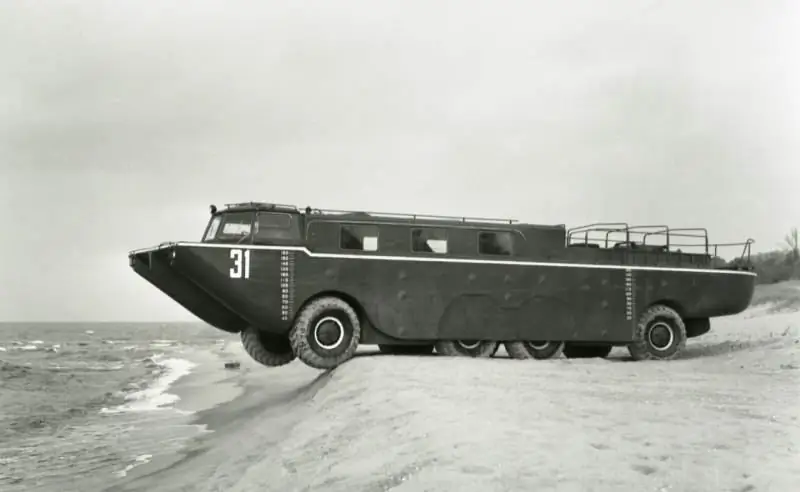
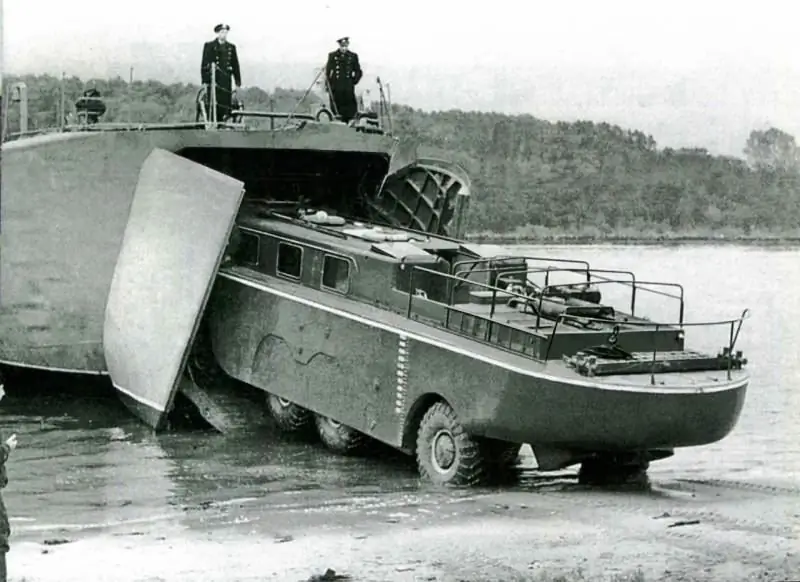
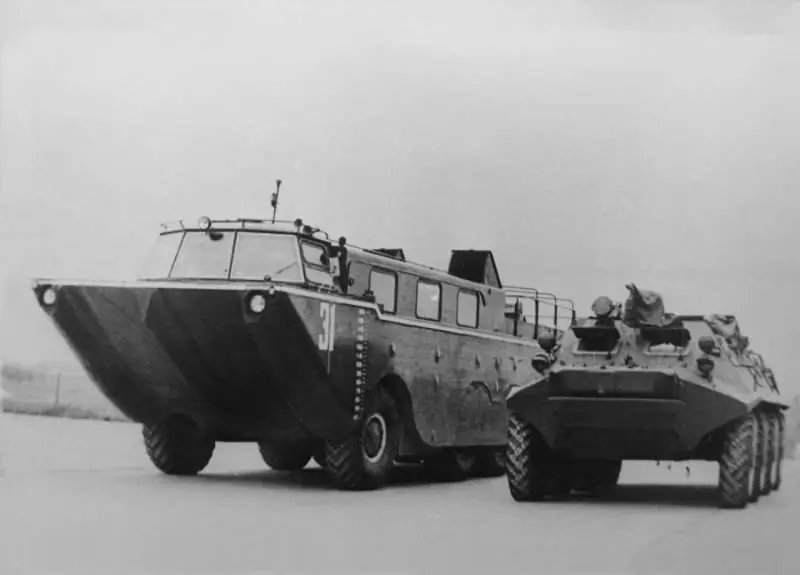
The Dolphin, created as part of the ZIL-135P project, appeared on trials in the fall of 1965 at sea in the Baltiysk region as a transport vehicle for marines. The 13, 8-meter four-axle giant was also tested on the Arctic Ocean as a reloading machine - a lighter. The body of the car was a load-bearing plastic (taking into account the developments on the ZIL-135B), and the total weight was about 20 tons. An important advantage of choosing fiberglass was resistance to bullet and shrapnel "wounds" - water through such holes did not gush with a stream, but only oozed through the "soaked" fiberglass. This is not to say that the plastic body was fragile. At one of the tests, the Dolphin easily broke a birch with a diameter of 400 mm with its nose.
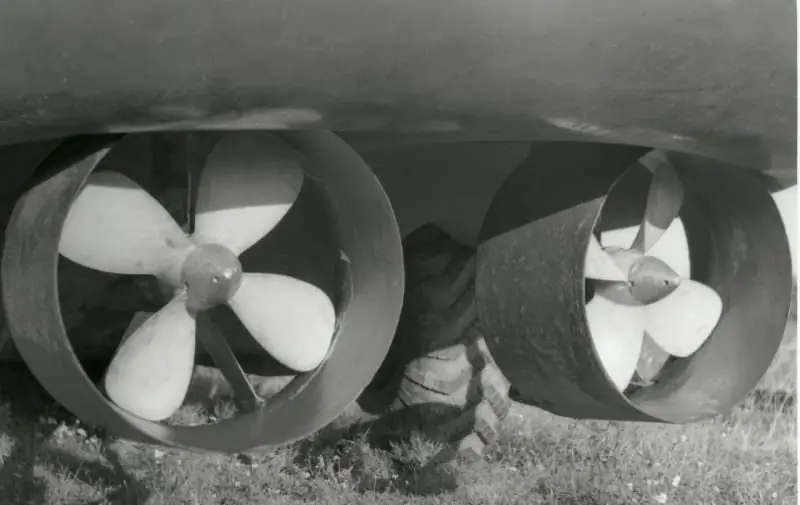
The amphibious aggregate base was completely borrowed from the original ZIL-135, but was supplemented with a system for pressurizing air into the underwater units. Movement on the water was provided by two propellers with a diameter of 700 mm, located in special annular profiled nozzles. ZIL-135P turned not with the help of water rudders, but by turning the speakers with screws. In many ways, this was an analogue of modern ship azipods. The propeller blades could be made of either brass or fiberglass. On land, the control system was pressed against the hull in special niches. The car became a record for its dynamics on the water: since 1965, none of the amphibians has been able to beat its maximum speed of 16.4 km / h. At the same time, 22 paratroopers or 5 tons of cargo could fit in the hold of the amphibian.
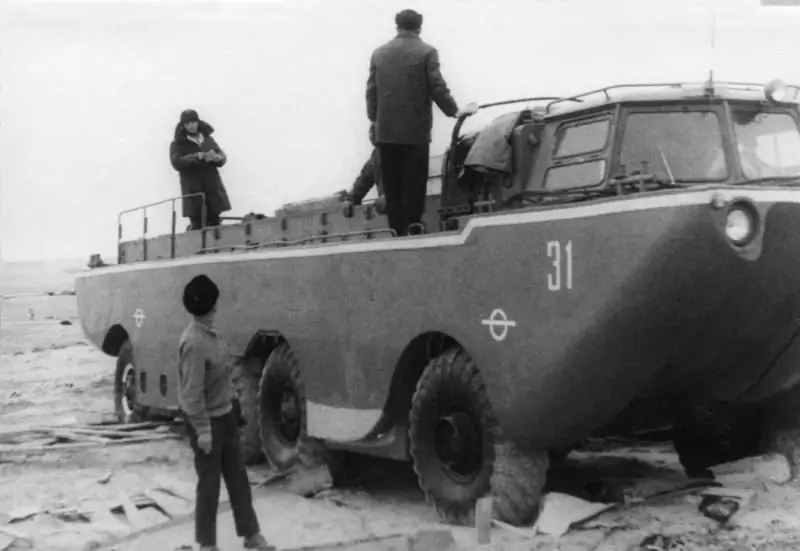
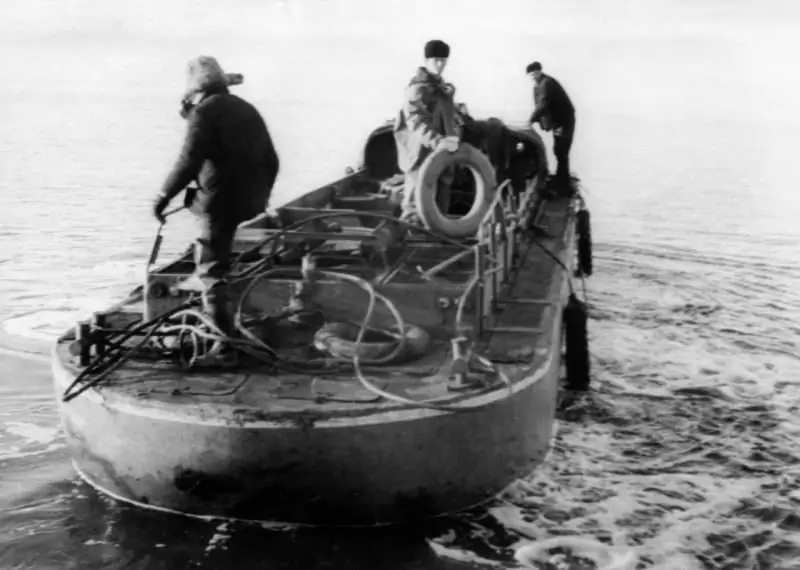
According to the results of the tests, the military sailors liked the car and, taking into account the modifications, they were ready to adopt it in the ZIL-135TA modification. However, a site for mass production was never found: the ZIL management was not ready to provide a single meter of area. Even petitions to the Cabinet of Ministers did not help. As a result, the unique car was abandoned, not leaving it to descendants even as a museum exhibit.