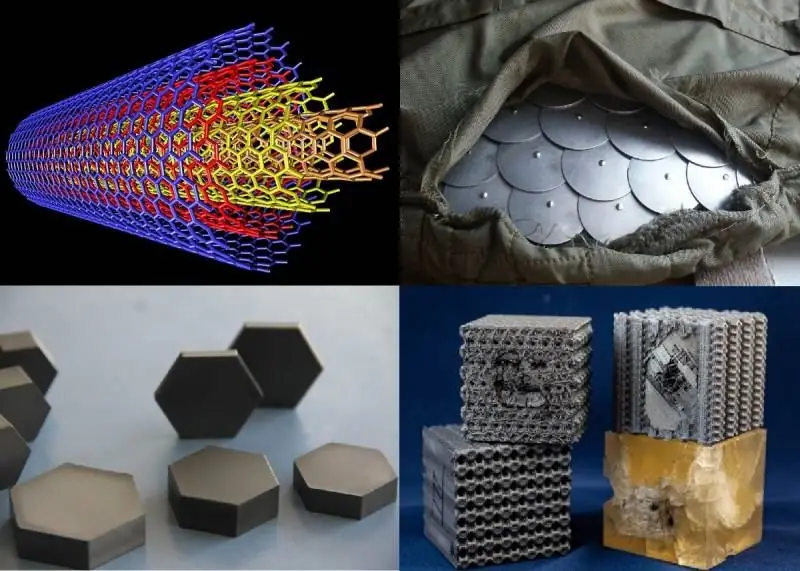
The most important task solved by the promising small arms being developed within the framework of the American NGSW program should be to ensure the guaranteed penetration of modern and advanced body armor developed in the world's leading weapons laboratories. Before returning to the problem of developing a "sword", a promising small arms capable of effectively countering American weapons developed under the NGSW program, it would be advisable to get acquainted with the "shield" - technologies for creating promising personal body armor (NIB).
There is an opinion that the problem of the NIB's impenetrability is far-fetched, since if a bullet hits the enemy, he will either be so injured that he will not be able to continue to actively engage in hostilities, or the hit will have to be in the part of the body unprotected by armored elements. Judging by the NGSW program, the US Armed Forces do not consider this problem far-fetched. The problem is that the rate of improvement of promising NIB is currently significantly ahead of the rate of improvement of small arms. And the US Armed Forces are just trying to make a breakthrough in the direction of radically improving the characteristics of small arms, the question is, will they succeed?
There are two main ways to increase the armor penetration of an ammunition - increasing its kinetic energy and optimizing the shape and material of the ammunition / ammunition core (of course, we are not talking about explosive, cumulative or poisoned ammunition). And here we actually run into a certain limit. A bullet or a core for it is made of ceramic alloys of high hardness and sufficiently high density (to increase the mass), they can be made harder and stronger, hardly denser. Increasing the mass of a bullet by increasing its dimensions is also practically impossible in the acceptable dimensions of hand-held small arms. There remains an increase in the speed of the bullet, for example, to hypersonic, but in this case, the developers are faced with enormous difficulties, in the form of a lack of necessary propellants, extremely rapid barrel wear and high recoil acting on the shooter. Meanwhile, the improvement of the NIB is going much more intensively.
Materials (edit)
Since its inception, personal body armor has come a long way from steel cuirasses and plates to modern body armor made of aramid fabric with inserts made of ultra-high molecular weight high density polyethylene (UHMWPE) and boron carbide.
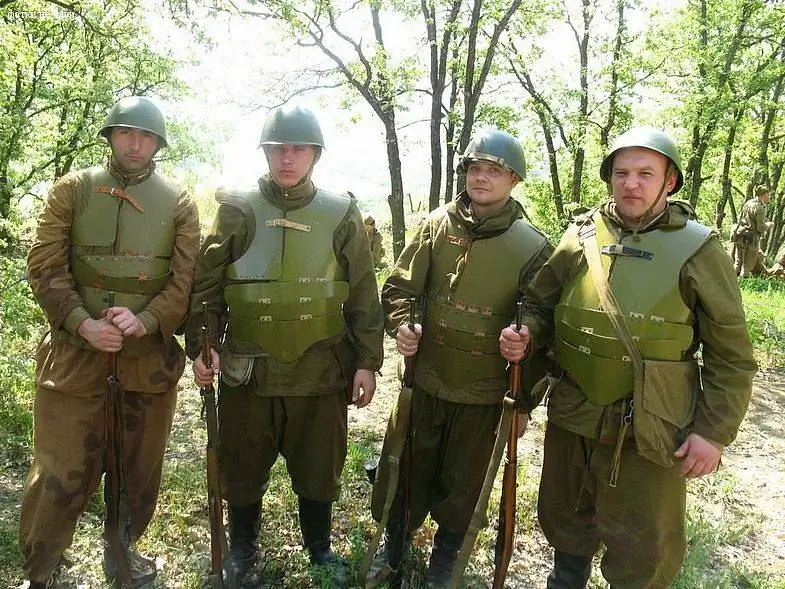
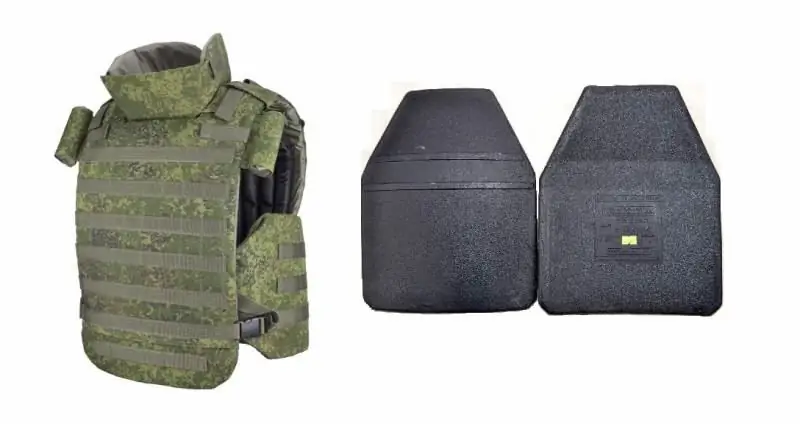
The NIB is improving in the areas of searching for new materials, creating composite and metal-ceramic armor elements, optimizing the shape and structure of NIB elements, including at the micro and nanoscale, which will effectively dissipate the energy of bullets and fragments. More exotic solutions are also being worked out, such as "liquid armor" based on non-Newtonian fluids.
The most obvious way is to improve the traditional designs of body armor by reinforcing them with inserts made of promising composite and ceramic materials. At the moment, most of the NIB is equipped with inserts made of heat-strengthened steel, titanium or silicon carbide, but they are gradually replacing them with boron carbide armor elements, which have a lower weight and significantly higher resistance.
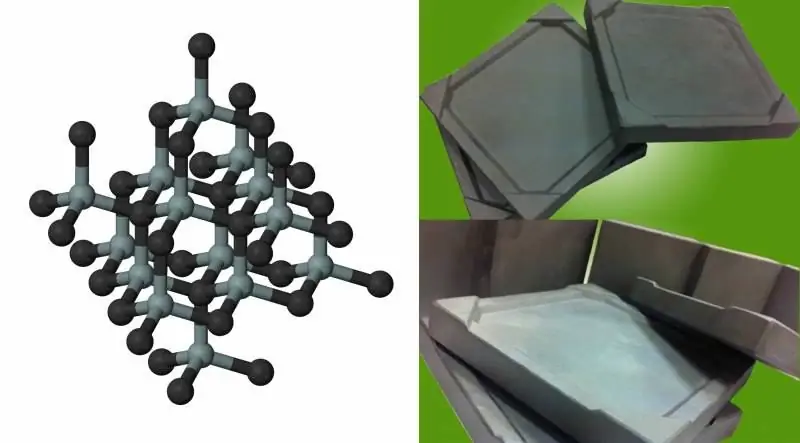
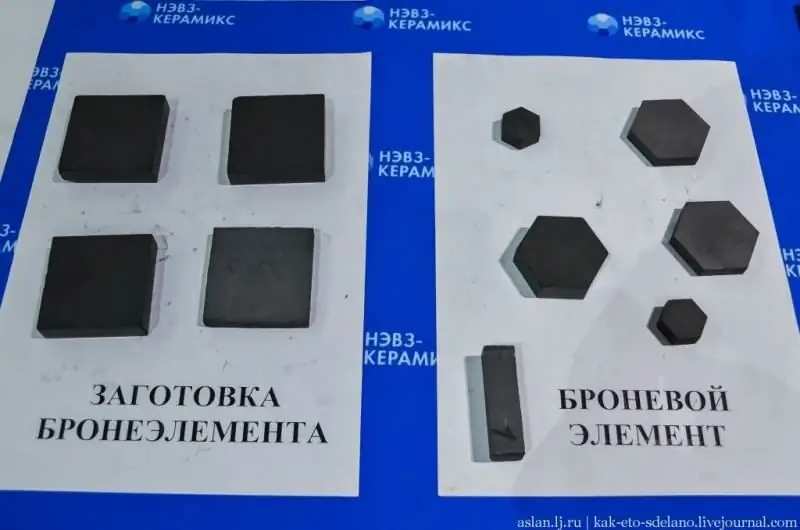
Structure
Another direction for improving the NIB is the search for the optimal structure of the placement of armored elements, which, on the one hand, should cover the maximum surface area of the fighter's body, and on the other hand, should not constrain his movement. As an example, albeit not entirely successful, but interesting development, one can cite the Dragon Skin body armor, designed and manufactured by the American company Pinnacle Armor. The "Dragon Skin" body armor has a scaly arrangement of armor elements.
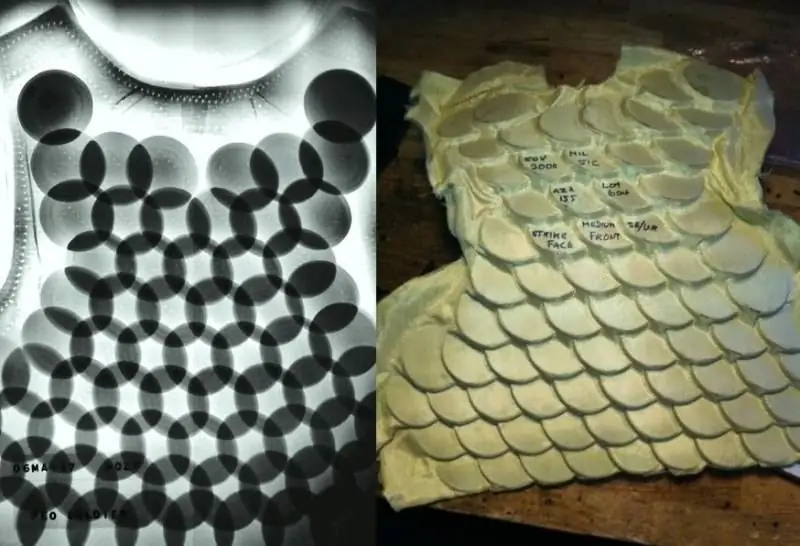
Bonded disks made of silicon carbide with a diameter of 50 mm and a thickness of 6, 4 mm provide the convenience of wearing this NIB due to a certain flexibility of the design and at the same time a sufficiently large area of the protected surface. This design also provides resistance to repeated hits of bullets fired from small arms at close range - "Dragon Skin" can withstand up to 40 hits from a Heckler & Koch MP5 submachine gun, M16 rifle or Kalashnikov assault rifle (the only question is how much of which and which cartridge ?).
The disadvantage of body armor "scaly" layout of armor elements is the almost complete lack of protection of the soldier from injury beyond the barrier, which leads to serious injuries or death of military personnel even without penetrating the NIB, as a result of which body armor of this type did not pass the US Army tests. Nevertheless, they are used by some special forces and special services of the United States.
A similar "scaly" scheme was implemented in the Soviet body armor ZhZL-74 designed for extreme protection against cold weapons, in which armor elements-discs with a diameter of 50 mm and a thickness of 2 mm made of ABT-101 aluminum alloy were used.
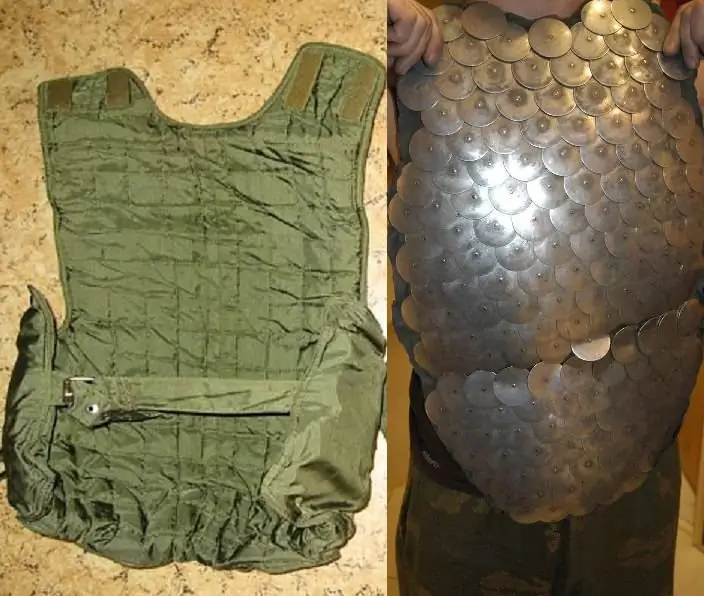
Despite the shortcomings of the NIB "Dragon Skin", the scaly arrangement of armor elements can be used in combination with other types of armor protection and shock-absorbing elements to reduce the impact of bullets and fragments beyond the barrier.
Scientists from the American Rice University have developed an unusual structure that allows the object to more efficiently absorb kinetic energy than a monolithic object from the same raw material. The basis for the scientific work was the study of the properties of carbon nanotube plexuses, which have an ultra-high density due to a special arrangement of filaments, with cavities at the atomic level, which allows them to absorb energy with high efficiency when colliding with other objects. Since it is not yet possible to fully reproduce such a structure at the nanoscale on an industrial scale, it was decided to repeat this structure in macro sizes. The researchers used polymer filaments that can be printed on a 3D printer, but arranged in the same system as nanotubes, and ended up with cubes with high strength and compressibility.
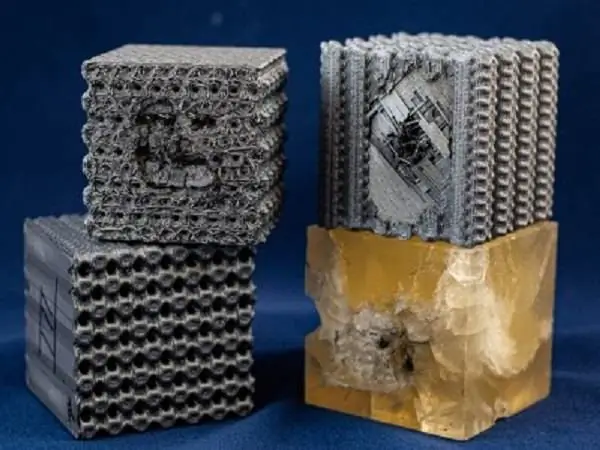
To test the effectiveness of the structure, the scientists created a second object from the same material, but monolithic, and launched a bullet into each of them. In the first case, the bullet stopped already on the second layer, and in the second it went much deeper and caused damage to the entire cube - it remained intact, but covered with cracks. A plastic cube with a special structure was also put under pressure to test its strength under pressure. During the experiment, the object shrank at least twice, but its integrity was not violated.

Foam metal
Speaking of materials, the properties of which are largely determined by the structure, one cannot fail to mention developments in the field of foam metal - metal or composite metal foam. Foam metal can be created on the basis of aluminum, steel, titanium, other metals or their alloys.
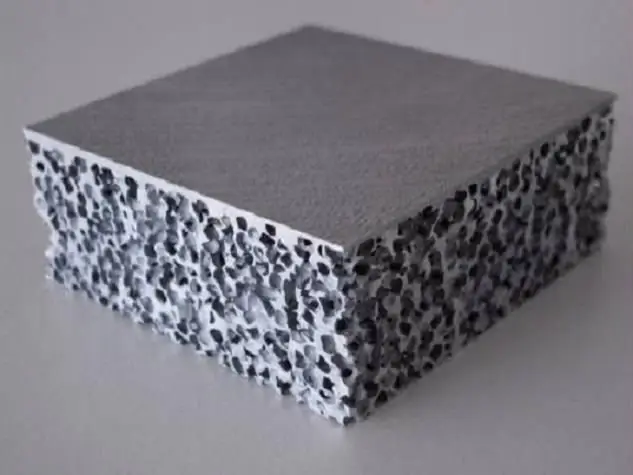
Specialists from the University of North Carolina (USA) have developed a steel foam metal with a steel matrix, enclosing it between the upper ceramic layer and a thin lower layer of aluminum. Foam metal less than 2.5 cm thick stops armor-piercing bullets of 7, 62 mm, after which a hole of less than 8 mm remains on the back surface.
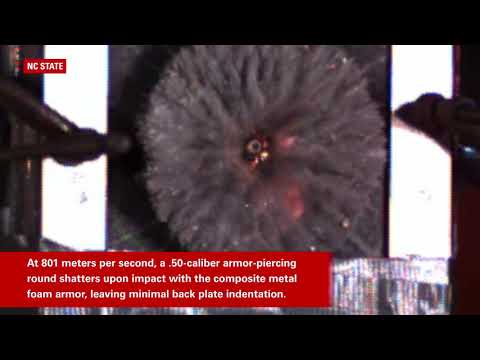
Among other things, the foam plate effectively reduces the effects of X-rays, gamma and neutron radiation, and also protects against fire and heat twice as better than conventional metal.
Another hollow-structure material is an ultralight form of foam, created by HRL Laboratories in conjunction with Boeing. The new material is one hundred times lighter than polystyrene - it is 99.99% air, but it has an extremely high rigidity. According to the developers, if an egg is covered with this material, and it falls from a height of 25 floors, it will not break. The resulting foam is so light that it can lie on a dandelion.
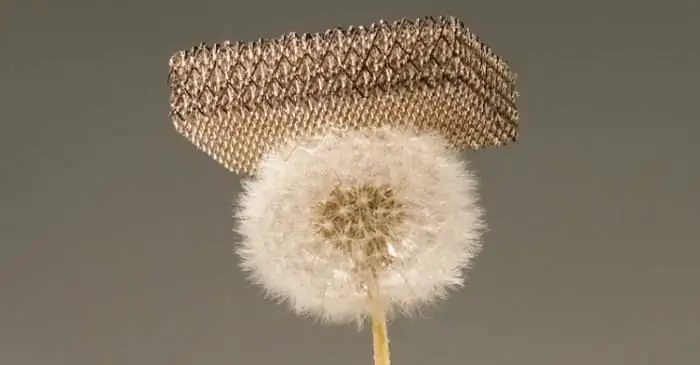
The prototype uses hollow nickel tubes connected to each other, the structure of which is similar to the structure of human bones, which allows the material to absorb a lot of energy. Each tube has a wall thickness of about 100 nanometers. Instead of nickel, other metals and alloys can be used in the future.
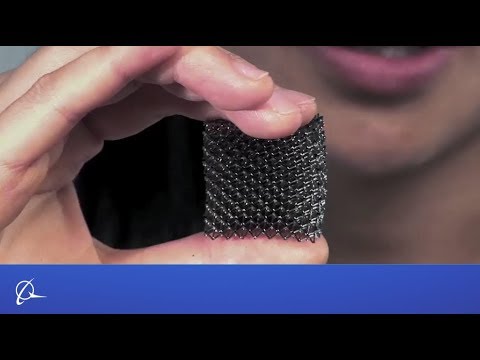
This material or its analogue, as well as the above-mentioned structured polymer material, can be considered for use in promising NIBs as elements of light and durable shock-absorbing support designed to minimize damage to the body by bullets beyond the barrier.
Nanotechnology
One of the most promising materials, which is expected to be widely used in various industries of the 21st century, is graphene, a two-dimensional allotropic modification of carbon formed by a layer of carbon atoms one atom thick. Spanish experts are developing a body armor based on graphene. The development of graphene armor started at the beginning of the 2000s. The research results are recognized as promising, in September 2018, the developers moved to practical tests. The project is funded by the European Defense Agency and is currently ongoing, with the participation of specialists from the British company Cambridge Nanomaterials Technology.
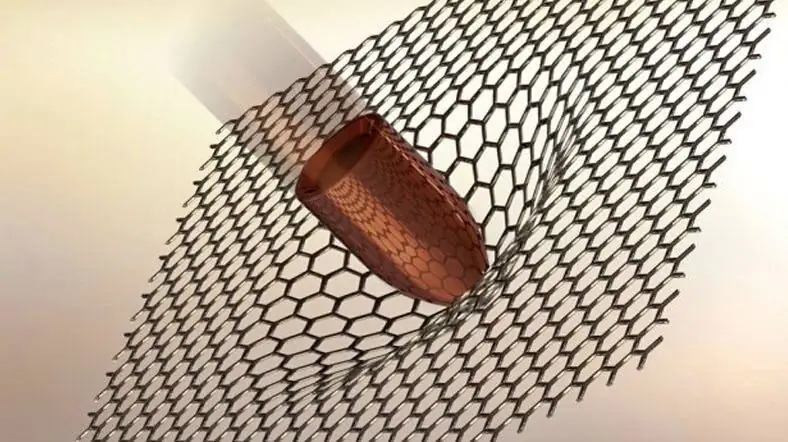
Similar work is underway in the United States, in particular at Rice University and the University of New York, where experiments were carried out to bombard graphene sheets with solid objects. Graphene armor is expected to be significantly stronger than Kevlar and will be combined with ceramic armor for best results. The greatest challenge is the production of graphene in industrial quantities. However, given the potential of this material in various industries, there is no doubt that a solution will be found. According to insider information that appeared on the pages of specialized media in December 2019, Huawei plans to launch the P40 smartphone with a graphene battery (with graphene electrodes) on the market in early 2020, which may indicate significant progress in the industrial production of graphene.
At the end of 2007, Israeli scientists created a self-healing material based on nanoparticles of tungsten disulfide (a salt of tungsten metal and hydrogen sulfide acid). Tungsten disulfide nanoparticles are layered fullerene-like or nanotubular formations. Nanotubulenes have record mechanical characteristics, fundamentally unattainable for other materials, amazing flexibility and strength, which is on the verge of strength of covalent chemical bonds.
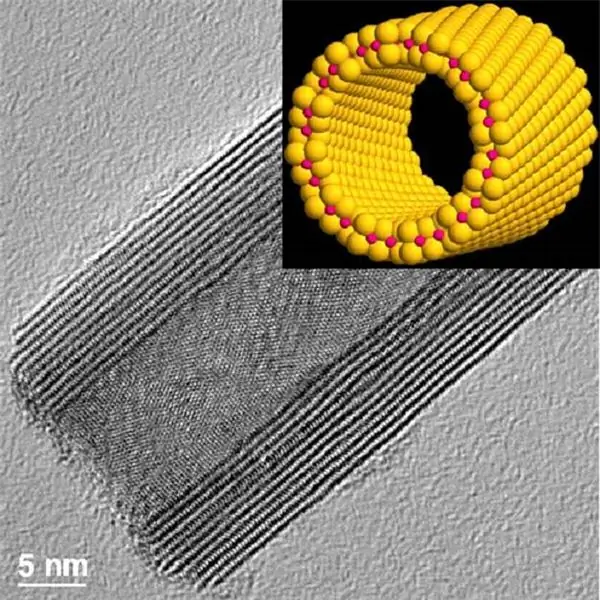
It is possible that in the future, bulletproof vests filled with this material can surpass in characteristics all other existing and promising NIB models. At the moment, the development of NIB based on tungsten disulfide nanotubes is at the stage of laboratory research due to the high cost of the synthesis of the starting material. Nevertheless, a certain international company is already producing nanoparticles of tungsten and molybdenum disulfides in the amount of many kilograms per year using a patented technology.
A major British defense company, Bae Systems, is developing a gel-filled body armor. In a gel-filled body armor, it is supposed to impregnate the aramid fiber with a non-Newtonian liquid, which has the property of instantly hardening upon impact. It is believed that "liquid armor" is one of the most promising areas for the development of promising NIB. Such work is being carried out in Russia in relation to the promising set of equipment for the soldiers "Ratnik-3".
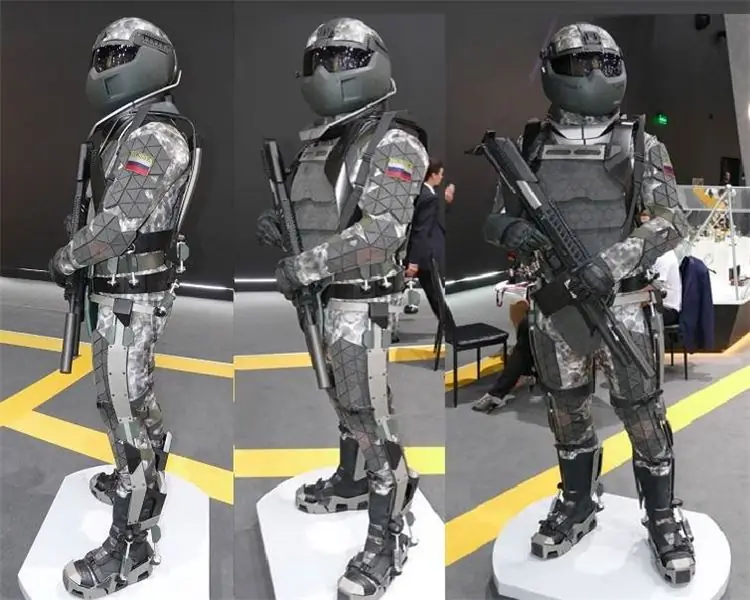
Thus, it can be concluded that promising NIBs are planned to be created using the latest technologies at the forefront of technological progress. If we talk about small arms, then here such a riot of technology is not observed. What is the reason for this, the lack of need or the conservatism of the arms industry?
Many projects of promising NIBs will certainly come to a standstill, but some of them will surely "shoot", and possibly make all small arms of the 20th century obsolete, just as bows, crossbows and muzzle-loading small arms became obsolete in their time. In addition, body armor is not the only important piece of equipment for a fighter that can radically increase his survivability in battle.