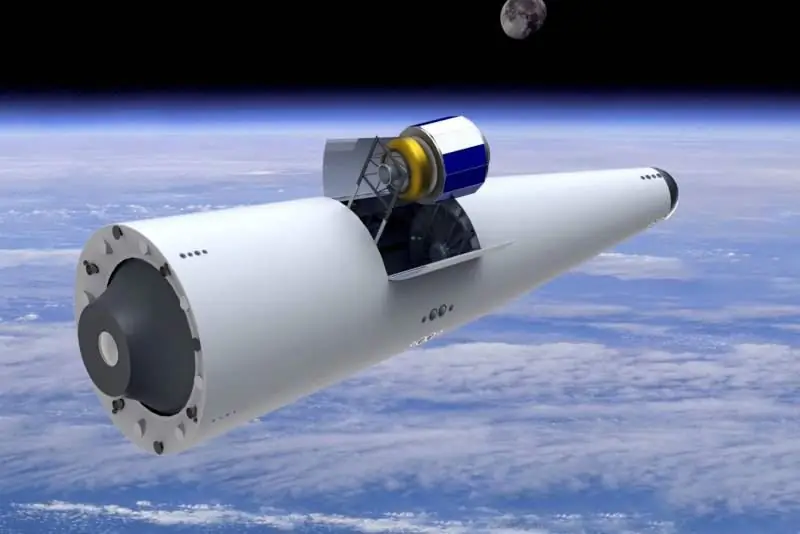
It is believed that technologies always develop gradually, from simple to complex, from stone knife to steel - and only then to a programmed milling machine. However, the fate of space rocketry turned out to be less straightforward. The creation of simple, reliable single-stage missiles for a long time remained inaccessible to designers. Solutions were required that neither material scientists nor engine engineers could offer. Until now, launch vehicles remain multistage and disposable: an incredibly complex and expensive system is used for a few minutes and then thrown away
“Imagine that before each flight you would assemble a new plane: you would connect the fuselage to the wings, lay electrical cables, install the engines, and after landing you would send it to a landfill … You cannot fly far,” the developers of the State Missile Center told us. Makeeva. “But that's exactly what we do every time we send cargo into orbit. Of course, ideally everyone would like to have a reliable one-stage "machine" that does not require assembly, but arrives at the cosmodrome, refueled and launched. And then it comes back and starts again - and again "…
On the halfway
By and large, rocketry tried to get by with one stage from the earliest projects. In the initial sketches of Tsiolkovsky, just such structures appear. He abandoned this idea only later, realizing that the technologies of the early twentieth century did not allow realizing this simple and elegant solution. Interest in single-stage carriers arose again in the 1960s, and such projects were being worked out on both sides of the ocean. By the 1970s, the United States was working on single-stage rockets SASSTO, Phoenix and several solutions based on the S-IVB, the third stage of the Saturn V launch vehicle, which delivered astronauts to the moon.
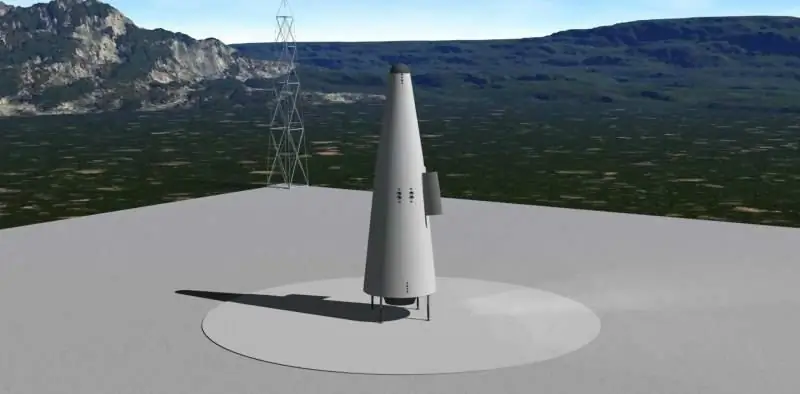
“Such an option would not differ in carrying capacity, the engines were not good enough for this - but still it would be one stage, quite capable of flying into orbit,” the engineers continue. "Of course, economically it would be completely unjustified." Composites and technologies for working with them have appeared only in recent decades, which make it possible to make the carrier one-stage and, moreover, reusable. The cost of such a "science-intensive" rocket will be higher than that of a traditional design, but it will be "spread out" over many launches, so that the launch price will be significantly lower than the usual level.
It is media reusability that is the main goal of developers today. The Space Shuttle and Energia-Buran systems were partially reusable. The repeated use of the first stage is being tested for SpaceX Falcon 9 rockets. SpaceX has already made several successful landings, and at the end of March they will try to launch one of the stages that have flown into space again. “In our opinion, this approach can only discredit the idea of creating a real reusable media,” notes the Makeev Design Bureau. "You still have to sort out such a rocket after each flight, install connections and new disposable components … and we are back to where we started."
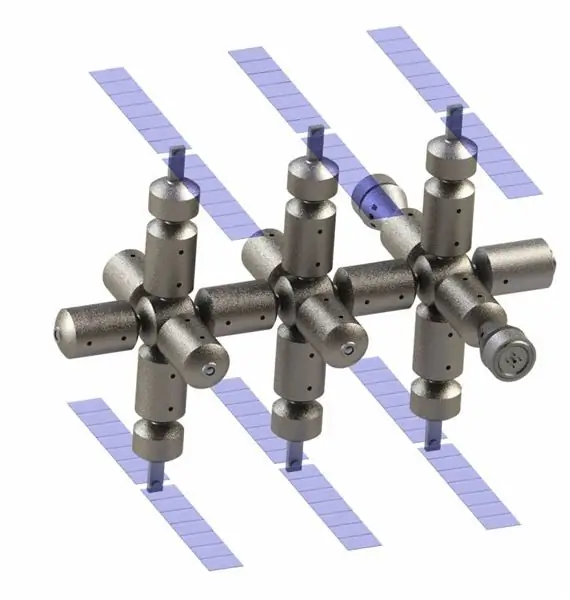
Fully reusable media are still only in the form of projects - with the exception of the New Shepard of the American company Blue Origin. So far, the rocket with a manned capsule is designed only for suborbital flights of space tourists, but most of the solutions found in this case can be easily scaled for a more serious orbital carrier. Representatives of the company do not hide their plans to create such an option, for which powerful engines BE-3 and BE-4 are already being developed. "With every suborbital flight, we are approaching orbit," assured Blue Origin. But their promising carrier New Glenn will also not be fully reusable: only the first block, created on the basis of the already tested New Shepard design, should be reused.
Material resistance
The CFRP materials required for fully reusable and single-stage rockets have been used in aerospace technology since the 1990s. In those same years, engineers at McDonnell Douglas quickly began implementing the Delta Clipper (DC-X) project, and today they could well boast of a ready-made and flying carbon fiber carrier. Unfortunately, under pressure from Lockheed Martin, work on the DC-X was discontinued, the technologies were transferred to NASA, where they tried to use them for the unsuccessful VentureStar project, after which many engineers involved in this topic went to work at Blue Origin, and the company itself was taken over by Boeing.
In the same 1990s, the Russian SRC Makeev became interested in this task. Over the years since then, the KORONA project ("Spacecraft disposable rocket, single-stage carrier [of space] vehicles") has undergone a noticeable evolution, and intermediate versions show how the design and layout became more and more simple and perfect. Gradually, the developers abandoned complex elements - such as wings or external fuel tanks - and came to the understanding that the main body material should be carbon fiber. Together with the appearance, both the weight and the carrying capacity changed. “Using even the best modern materials, it is impossible to build a single-stage rocket weighing less than 60-70 tons, while its payload will be very small,” says one of the developers. - But as the starting mass grows, the structure (up to a certain limit) has an ever smaller share, and it becomes more and more profitable to use it. For an orbital rocket, this optimum is about 160-170 tons, starting from this scale its use can already be justified."
In the latest version of the CORONA project, the launch mass is even higher and approaches 300 tons. Such a large single-stage rocket requires the use of a highly efficient liquid-propellant jet engine operating on hydrogen and oxygen. Unlike engines in separate stages, such a liquid-propellant rocket engine must be able to operate in very different conditions and at different altitudes, including takeoff and flight outside the atmosphere. “A conventional liquid engine with Laval nozzles is effective only at certain altitude ranges,” explain the Makeyevka designers, “so we came to the need to use a wedge-air rocket engine.” The gas jet in such engines automatically adjusts to the pressure “overboard”, and they remain efficient both at the surface and high in the stratosphere.
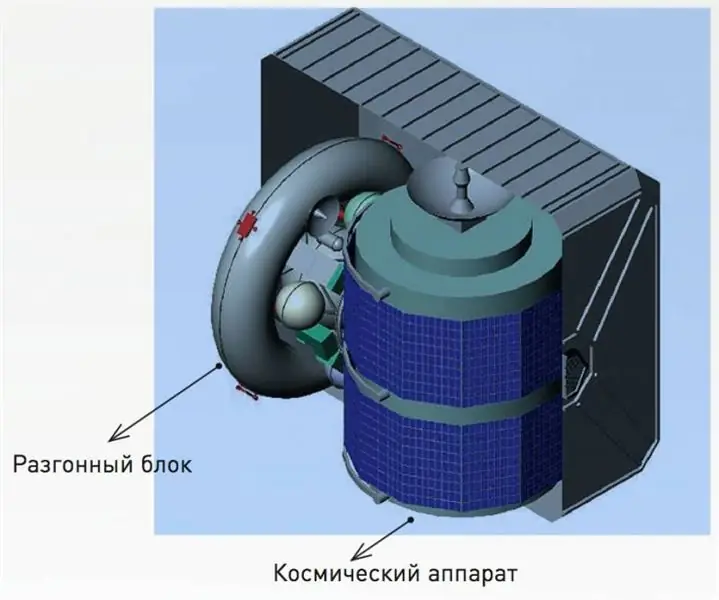
So far, there is no working engine of this type in the world, although they have been and are being dealt with both in our country and in the USA. In the 1960s, Rocketdyne engineers tested such engines on a stand, but they did not come to installation on missiles. CROWN should be equipped with a modular version, in which the wedge-air nozzle is the only element that does not yet have a prototype and has not been tested. There are also all technologies for the production of composite parts in Russia - they have been developed and are successfully applied, for example, at the All-Russian Institute of Aviation Materials (VIAM) and at JSC Kompozit.
Vertical fit
When flying in the atmosphere, the KORONA carbon-fiber load-bearing structure will be covered with heat-shielding tiles developed by VIAM for the Burans and since then have been noticeably improved.“The main heat load on our rocket is concentrated on its“nose”, where high-temperature thermal protection elements are used,” the designers explain. - In this case, the expanding sides of the rocket have a larger diameter and are at an acute angle to the air flow. The thermal load on them is less, which allows the use of lighter materials. As a result, we have saved more than 1.5 tons. The mass of the high-temperature part does not exceed 6% of the total mass of the thermal protection. For comparison, in the Shuttles it accounts for more than 20%."
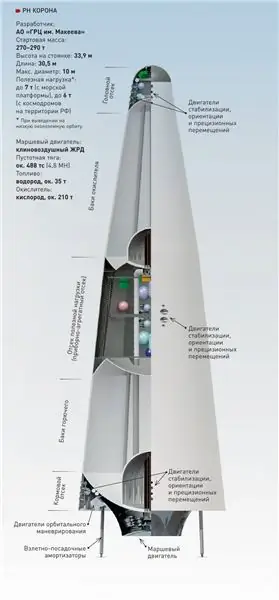
The sleek tapered design of the media is the result of countless trial and error. According to the developers, if you take only the key characteristics of a possible reusable single-stage carrier, you will have to consider about 16,000 combinations of them. Hundreds of them were appreciated by the designers while working on the project. “We decided to abandon the wings, like on the Buran or the Space Shuttle,” they say. - By and large, in the upper atmosphere, they only interfere with spacecraft. Such ships enter the atmosphere at hypersonic speed no better than an "iron", and only at supersonic speed do they switch to horizontal flight and can properly rely on the aerodynamics of the wings."
The axisymmetric cone shape not only allows for easier thermal protection, but also has good aerodynamics when driving at very high speeds. Already in the upper layers of the atmosphere, the rocket receives a lift, which allows it not only to brake here, but also to maneuver. This, in turn, makes it possible to make the necessary maneuvers at high altitude, heading for the landing site, and in the future flight, it remains only to complete the braking, correct the course and turn aft down, using weak maneuvering engines.
Recall both the Falcon 9 and the New Shepard: there is nothing impossible or even unusual in vertical landing today. At the same time, it makes it possible to get by with significantly less forces during the construction and operation of the runway - the runway on which the same Shuttles and Buran landed had to have a length of several kilometers in order to brake the vehicle at a speed of hundreds of kilometers per hour. “The CROWN, in principle, can even take off from an offshore platform and land on it,” adds one of the authors of the project, “the final landing accuracy will be about 10 m, the rocket is lowered onto retractable pneumatic shock absorbers.” All that remains is to carry out diagnostics, refuel, place a new payload, and you can go flying again.
KORONA is still being implemented in the absence of funding, so the developers of the Makeev Design Bureau managed to get only to the final stages of the draft design. “We have passed this stage almost entirely and completely independently, without external support. We have already done everything that could be done, - the designers say. - We know what, where and when should be produced. Now we need to move on to the practical design, production and development of key units, and this requires money, so now everything depends on them."
Delayed start
The CFRP rocket expects only a large-scale launch; upon receipt of the necessary support, the designers are ready to begin flight tests in six years, and in seven to eight years - to begin experimental operation of the first missiles. They estimate that this requires less than $ 2 billion - not much by rocket science standards. At the same time, a return on investment can be expected after seven years of using the rocket, if the number of commercial launches remains at the current level, or even in 1.5 years - if it grows at the predicted rates.
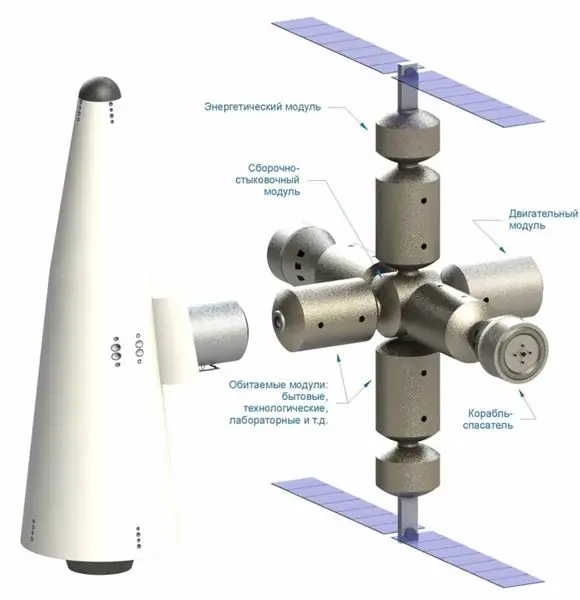
Moreover, the presence of maneuvering engines, rendezvous and docking facilities on the rocket also makes it possible to count on complex multi-launch launch schemes. Having spent fuel not for landing, but for finishing the payload, it is possible to bring it to a mass of more than 11 tons. Then the CROWN will dock with the second, "tanker", which will fill its tanks with additional fuel necessary for the return. But still, much more important is reusability, which for the first time will relieve us of the need to collect the media before each launch - and lose it after each launch. Only such an approach can ensure the creation of a stable two-way traffic flow between the Earth and the orbit, and at the same time the beginning of a real, active, large-scale exploitation of near-Earth space.
In the meantime, the CROWN remains in limbo, work on New Shepard continues. A similar Japanese project RVT is also developing. Russian developers may simply not have enough support for a breakthrough. If you have a couple of billions to spare, this is a far better investment than even the largest and most luxurious yacht in the world.