In early August 2016, the US Navy successfully tested the Osprey MV-22 tiltrotor. This aircraft itself is not unusual. The twin-rotor vehicle has been in service with the American Navy for a long time (it was put into service in the second half of the 1980s), but for the first time in history, critical parts were installed on a tiltrotor (flight safety directly depends on them), which were 3D printed printer.
For testing, the US military printed a bracket for attaching the engine to the wing of the tiltrotor from titanium using direct layer-by-layer laser sintering. At the same time, a strain gauge was mounted on the bracket itself, designed to register a possible deformation of the part. Each of the two engines of the Osprey MV-22 tiltrotor is attached to the wing using four such brackets. At the same time, at the time of the first test flight of the tiltrotor, which took place on August 1, 2016, only one bracket, printed on a 3D printer, was installed on it. Earlier it was reported that the nacelle mounts printed by the method of three-dimensional printing were also installed on the tiltrotor.
The development of the parts printed for the tiltrotor was carried out by the US Navy Aviation Combat Operations Center located at the McGuire-Dix-Lakehurst Joint Base in New Jersey. Flight tests of the Osprey MV-22 with printed parts were carried out at the US Navy Patxent River base, the tests were recognized by the military as completely successful. The US military believes that thanks to the widespread introduction of three-dimensional printing, technology in the future will be able to quickly and relatively cheaply produce spare parts for converters. In this case, the necessary details can be printed directly on the ships. In addition, the printed parts can then be modified in order to improve the performance of the onboard assemblies and systems.
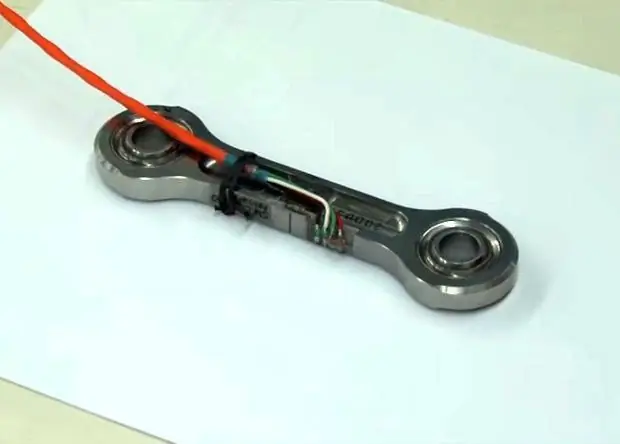
Titanium Printed Motor Mount Bracket
The US military was interested in 3D printing technologies a few years ago, but until recently, the functionality of 3D printers was not wide enough to be used routinely to build fairly complex parts. The parts for the tiltrotor were created using an additive 3D printer. The part is made gradually in layers. Every three layers of titanium dust are bonded with a laser, this process is repeated as long as necessary to obtain the desired shape. After completion, the excess is cut off from the part; the resulting element is completely ready for use. Since the tests were completed successfully, the American military will not stop there, they are going to build 6 more important structural elements of the tiltrotor, half of which will also be titanium, and the other - steel.
3D printing in Russia and worldwide
Despite the fact that the printer type of production was successfully implemented in the USA and Russia several years ago, the creation of elements for military equipment is in the process of being finalized and tested. First of all, this is due to the very high requirements for all military products, mainly in terms of reliability and durability. However, Americans are not alone in making progress in this area. For the second year in a row, Russian designers have been producing parts for the developed assault rifles and pistols using 3D printing technology. New technologies save valuable drawing time. And putting such parts on stream can provide quick replacement in the field, in repair battalions, since there will be no need to wait for spare parts from the factory for the same tanks or unmanned aerial vehicles.
For submariners, military 3D printers will simply be worth its weight in gold, since during autonomous long-distance sailing, replacing parts by the submariners themselves will give the submarine an almost inexhaustible resource. A similar situation is observed with ships going on long voyages and icebreakers. Most of these ships will receive drones in the very near future, which will eventually require repair or complete replacement. If a 3D printer appears on the ship, which will allow you to quickly print spare parts, then in a few hours the equipment can be used again. In the conditions of the transience of operations and the high mobility of the theater of military operations, the local assembly of certain parts, assemblies and mechanisms right on the spot will allow maintaining a high level of efficiency of support units.
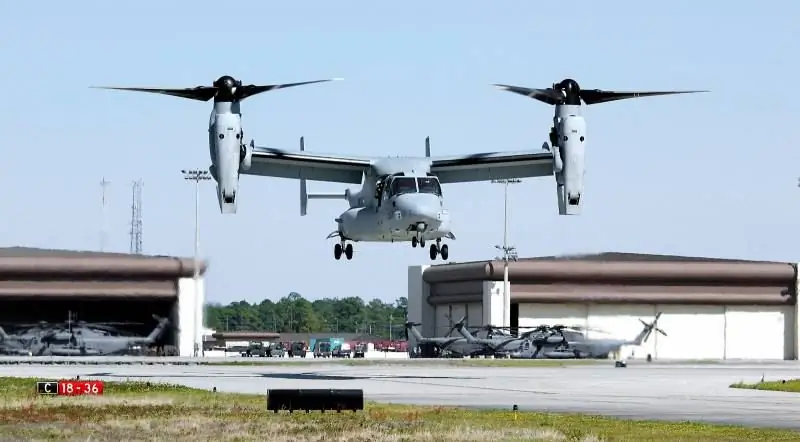
Osprey MV-22
While the US military is launching their convertiplanes, the Russian manufacturers of the Armata tank have been using an industrial printer at Uralvagonzavod for the second year already. With its help, parts for armored vehicles, as well as civilian products, are produced. But so far, such parts are used only for prototypes, for example, they were used in the creation of the Armata tank and its tests. At the Kalashnikov Concern, as well as at TsNIITOCHMASH, by order of the Russian military, designers make various parts of small arms from metal and polymer chips using 3D printers. The Tula Instrument Design Bureau named after Shipunov, the famous CPB, which is known for a rich assortment of manufactured weapons: from pistols to high-precision missiles, does not lag behind them. For example, a promising pistol and an ADS assault rifle, which is intended to replace the AK74M and APS special forces, is assembled from high-strength plastic parts that are printed on a printer. For some military products, the CPB has already been able to create molds; at present, the serial assembly of products is being worked out.
In the conditions when a new arms race is observed in the world, the timing of the release of new types of weapons becomes important. For example, in armored vehicles, only the process of creating a model and transferring it from drawings to a prototype usually takes a year or two. When developing submarines, this period is already 2 times longer. “The 3D printing technology will reduce the time period by several times to several months,” notes Alexey Kondratyev, an expert in the field of the navy. - Designers will be able to save time on drawings when designing a 3D model on a computer and immediately make a prototype of the desired part. Very often, parts are reworked taking into account the tests carried out and in the process of revision. In this case, you can release the assembly instead of the part and check all the mechanical characteristics, how the parts interact with each other. Ultimately, the timing of prototyping will allow designers to reduce the total time for the first finished sample to enter the testing stage. Nowadays, it takes about 15-20 years to create a new generation nuclear submarine: from a sketch to the last screw during assembly. With the further development of industrial three-dimensional printing and the launch of mass production of parts in this way, the time frame can be reduced by at least 1.5-2 times."
According to experts, modern technologies are now one to two years away from mass production of titanium parts on 3D printers. It is safe to say that by the end of 2020, military representatives at the enterprises of the military-industrial complex will accept equipment that will be assembled by 30-50% using 3D printing technologies. At the same time, the greatest importance for scientists is the creation of ceramic parts on a 3D printer, which are distinguished by high strength, lightness and heat-shielding properties. This material is very widely used in the space and aviation industries, but it can be used in even larger volumes. For example, the creation of a ceramic engine on a 3D printer opens up the horizon for the creation of hypersonic aircraft. With such an engine, a passenger plane could fly from Vladivostok to Berlin in a couple of hours.
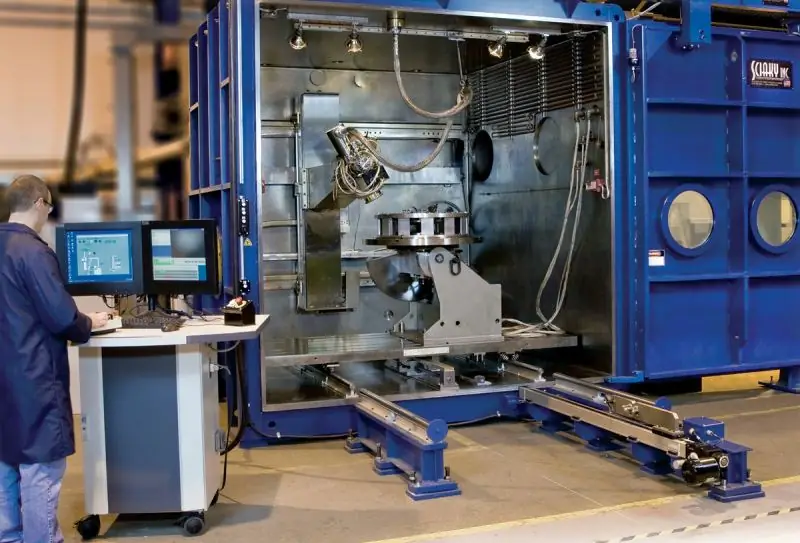
It is also reported that American scientists have invented a resin formula specifically for printing in 3D printers. The value of this formula lies in the high strength of the materials obtained from it. For example, such a material can withstand critical temperatures that exceed 1700 degrees Celsius, which is ten times higher than the resistance of many modern materials. Stephanie Tompkins, Director of Science for Advanced Defense Research, estimates that new materials created with 3D printers will have unique combinations of characteristics and properties that have never been seen before. Thanks to the new technology, Tompkins says we will be able to produce a durable part that is both lightweight and huge. Scientists believe that the production of ceramic parts on a 3D printer will mean a scientific breakthrough, including in the production of civilian products.
The first Russian 3D satellite
Currently, 3D printing technology is already successfully producing parts directly on board space stations. But domestic experts decided to go even further, they immediately decided to create a microsatellite using a 3D printer. The Rocket and Space Corporation Energia has created a satellite, the body, bracket and a number of other parts of which were 3D printed. At the same time, an important clarification is that the microsatellite was created by Energia engineers together with students of the Tomsk Polytechnic University (TPU). The first printer satellite received the full name "Tomsk-TPU-120" (the number 120 in the name in honor of the 120th anniversary of the university, which was celebrated in May 2016). It was successfully launched into space in the spring of 2016 together with the Progress MS-02 spacecraft, the satellite was delivered to the ISS and then launched into space. This unit is the world's first and only 3D satellite.
The satellite created by TPU students belongs to the class of nanosatellites (CubSat). It has the following dimensions 300x100x100 mm. This satellite was the first spacecraft in the world to have a 3D printed body. In the future, this technology can become a real breakthrough in the creation of small satellites, as well as make their use more accessible and widespread. The design of the spacecraft was developed at the TPU Scientific and Educational Center "Modern Production Technologies". The materials from which the satellite was made were created by scientists from the Tomsk Polytechnic University and the Institute of Strength Physics and Materials Science of the Siberian Branch of the Russian Academy of Sciences. The main purpose of the satellite was to test new technologies of space materials science; it will help Russian scientists test several developments of the Tomsk university and its partners.
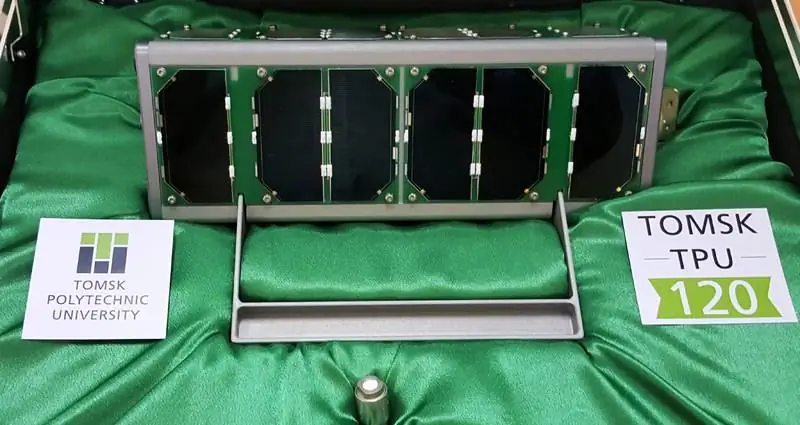
According to the press service of the university, the launch of the Tomsk-TPU-120 nanosatellite was planned to be carried out during the spacewalk of the cosmonauts from the ISS. The satellite is a fairly compact, but at the same time a full-fledged spacecraft, which has power cells, solar panels, onboard radio equipment and other devices. But its main feature was that its body was 3D printed.
Various sensors of the nanosatellite will record the temperature on board, on batteries and boards, and parameters of electronic components. All this information will then be transmitted to Earth online. Based on this information, Russian scientists will be able to analyze the state of the satellite materials and decide whether they will use them in the development and construction of spacecraft in the future. It should be noted that an important aspect of the development of small spacecraft is also the training of new personnel for the industry. Today, students and teachers of the Tomsk Polytechnic University, with their own hands, develop, produce and improve the designs of all kinds of small spacecraft, while gaining not only high-quality fundamental knowledge, but also the necessary practical skills. This is what makes the graduates of this educational institution unique specialists in the future.
The future plans of Russian scientists and industry representatives include the creation of a swarm of university satellites. “Today we are talking about the need to motivate our students to study everything that, in one way or another, is connected with space - it can be energy, materials, and the creation of new generation engines, etc. We discussed earlier that interest in space in the country has faded somewhat, but it can be revived. To do this, it is necessary to start not even from a student's bench, but from a school one. Thus, we have embarked on the path of development and release of CubeSat - small satellites,”- said the press service of the Tomsk Polytechnic Institute with reference to the rector of this higher educational institution, Peter Chubik.