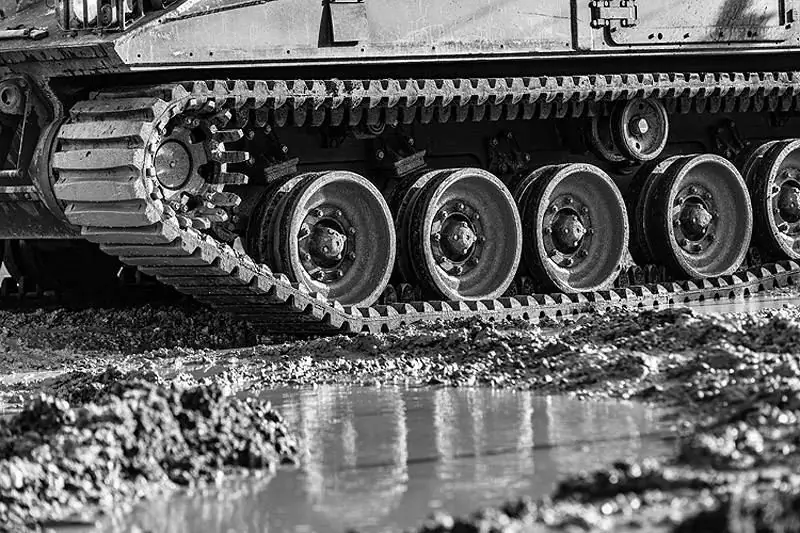
The need for platforms capable of moving over any type of terrain and operating on the battlefield in the same battle formations with heavy armored vehicles, as a rule, determines the installation of a tracked propulsion unit. At the same time, medium and light armored vehicles, which usually travel on the roads and which must be airlifted to speed up deployment, are usually wheeled.
The choice problem becomes more complicated in the case of medium-sized platforms. The mass of these machines is increasing against the background of changing operational requirements, and depending on the technological development of tracks and wheels, which can improve performance and mitigate any disadvantages, each type of propulsion device can gain an advantage here.
Steel does not surrender
Track systems dominate the market for armored vehicles heavier than 30 tons, and although steel tracks still dominate, manufacturers of composite rubber equivalents are trying to gain a foothold in this market. The development of steel tracks is mainly related to weight reduction. This is achieved through the use of lighter materials that are able to withstand the forces acting on them. First of all, they can be obtained through the development of special grades of high-strength steel.
William Cook, chief commercial officer at Cook Defense Systems (CDS), a developer and manufacturer of steel tracks, said they are offering lighter options to their customers, including the British Army. CDS also supplies all of the components that are in one way or another related to the tracks themselves, including drive sprockets, idler wheels, support and carrier rollers, etc.
“If you look at the Ajax light reconnaissance vehicle of the British Army, you will see that the track we currently supply is about 15% lighter than the one we originally offered. We have achieved this through the use of special modern materials and modern design and manufacturing tools."
He explained:
“We also use advanced finite element analysis and extended bench tests to ensure that our lightweight tracks are reliable throughout their planned service life. Finite Element Analysis (FEA) checks to see if there is 'unnecessary' mass and we test the prototypes for failure on a purpose-built test bench to make sure they can withstand the operating conditions."
During serial production, CDS ensures high product quality and guarantees zero defects by X-ray inspection of 100% of the tracks. The company also provides a complete set of assembly and maintenance tools with appropriate instructions, and dispatches technical teams to military units to advise and assist vehicle crews.
Steel tracks are available with one or two pins. The difference is that the tracks are connected to each other with either one or two fingers. One-pin tracks are lighter and offer good traction, which is why they are more suitable for light vehicles. Tracks with two fingers are heavier and more suitable for tanks, but they do not always provide the same characteristics, while they are also more expensive.
In steel tracks, the fingers are usually rubberized, that is, they are covered with a small layer of rubber, and this determines the service life of the tracks. A track with two rubberized pins will wear double the amount of rubber. CDS has invested heavily in research and development for specialty wear-resistant rubber compounds used for fingers, pads and wipers.
“Improving rubber compound performance is critical to extending track life,” explained Cook. CDS has a dedicated rubber compound testing and quality control laboratory at its track plant and is working closely with UK universities to develop more flexible rubber compounds.
The company also recently invested $ 6.4 million in its UK facilities to relocate all metal components and reduce reliance on third-party parts, including pins and staples. This improved the rhythm of the supply of tracks to the British army of its own production, which is very important, since tracks are a highly consumable component during military operations and at the same time are extremely necessary to maintain the operability of armored vehicles.
Cook said that if armored vehicle operators ultimately want to have "full combat capability," then they cannot abandon steel tracks, as they allow you to overcome the most difficult terrain, including swampy soil and mud slopes.
Regarding armored vehicles of the middle category in terms of mass, where the competition is most intense between steel and rubber tracks, Cook noted: “There will always be users who want to use their vehicles in large combat operations and therefore need steel tracks, but there will also be those who want to use their vehicles in operations where it is necessary to cover long distances on different types of roads, or in peacekeeping operations or in support operations for which rubber tracks are more suitable."
Cook emphasized that since CDS is independent of the control of any developer or manufacturer of armored vehicles, such as BAE Systems or Krauss-Maffei Wegmann, it can offer its tracked systems to any manufacturer. CDS is working with Singapore-based ST Engineering on the Hunter armored vehicle, in the Middle East to modernize Russian vehicles, with the Turkish Otokar on its Tulpar infantry fighting vehicle and with Germany's Rheinmetall on the Lynx infantry fighting vehicle under the Australian Land 400 program.
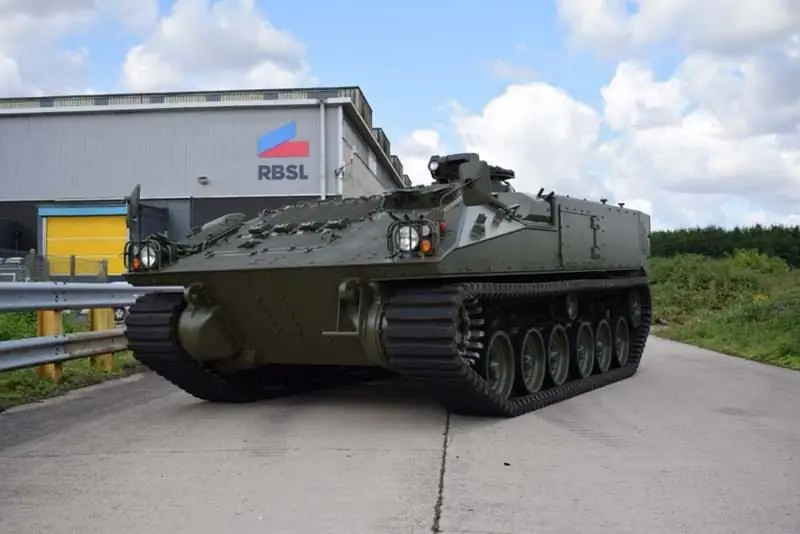
Closing the gap
Meanwhile, the performance of composite rubber tracks is constantly improving. Manufacturers want to compete not only with steel tracks in the field of heavy and medium armored vehicles, they also compete with wheeled solutions. Calvin Sloane of Soucy, a Canadian rubber track company, said his company is involved in most armored vehicle programs because of the capabilities that this type of track offers. "A long-standing controversy on the topic" Which is better: a caterpillar or a wheel? " always flared up again when it came to the mobility of armored vehicles. While wheels, in particular 8x8 machines, perform better on the road than steel tracks, rubber tracks fit well into the niche between wheels and tracks.”
Sloane explained that the road characteristics of rubber tracks allow a total of greater distance to be covered, which almost coincides with the mileage of the wheels, since the average distances between breakdowns of armored vehicles are approximately the same, but if you take a heavier car, then here rubber tracks actually provide more mileage between breakdowns.
“The 8x8 configuration generally has a GVW limit of around 35 tonnes; when you go over it, you start to lose mobility due to the size of the wheels and the power of the engine,”explained Sloane. “As this limit is exceeded and the weight of the machine increases, the benefits of the tracked propulsion unit become more evident. It is getting harder and harder to make an argument for 8x8 platforms, now composite rubber tracks are entering the scene and will play a role up to about 47 tonnes.”
Soucy is working on new brands of rubber compounds that will allow rubber tracks to perform more efficiently on vehicles over 50 tonnes and will challenge steel in the heavy armored vehicle industry. An outdated Leopard 1 tank weighing approximately 42 tons and equipped with rubber tracks is currently undergoing operational tests in Canada.
“We have chemists at the plant who work with different formulations and experiment with heat release. These are complex substances, which is why others cannot come up with the correct formula. It is not only about obtaining the caterpillar as a whole, but also about Kevlar fibers to prevent cracking of rubber and carbon nanotubes in combination with other chemicals to reduce heat generation and, as a result, increase durability …
We are experimenting with this composition, deriving dependences on the mass of the car so that it exactly matches it. Typically, we make a track from six different mixes and then we run it in our Leopard test tank, analyze which segment works best and then take that and make a complete track out of it. Soucy is working on its latest formulations, which are specifically designed for machines weighing about 55 tons, and is conducting tests to measure heat release."
Sloane added that the company is about two years away from delivering practical results. Meanwhile, the target market for composite rubber tracks is medium-sized vehicles weighing 35-48 tons. He noted that tracked platforms have better combat stability compared to explosion-sensitive wheeled vehicles, since the rubber track can absorb the blast wave. The likelihood of explosion damage to steel tracks is higher, while they create secondary damaging factors in the form of steel fragments.
Other advantages of rubber tracks include durability, Sloane says, while rubberized steel tracks with glued rubber pads need to be replaced every 600 km. Steel tracks also cause wear on the drive wheels, idlers, track and carrier rollers, rubber pads and of course the track links themselves. “With steel tracks, you have to change road wheels every 1500-2000 km, the same situation with rubber and rubber parts. The service life of the driving and directing wheels is 2000-3000 km, whereas, for comparison, the contact "rubber-rubber" is much less destructive."
Less wear and tear results in less logistical support, which is another benefit along with a reduction in noise and vibration by up to 70%. Vibration can negatively affect combat systems, ammunition, electronics and humans, as constant shaking over time leads to disastrous results. The use of rubber also helps to reduce weight and improve fuel efficiency.
Competitive market
The company tested its composite rubber tracks on the British Army's Warrior BMP, initially as a proof of concept and later as a proposal for the Ajax program. At DSEI 2019, the company showed one of its used tracks and a new track on the Warrior for clarity. Sloane said the new tracks could be part of the Warrior's BMP extension program if the Department of Defense wanted to, although there is currently no agreement from it. Rheinmetall BAE Systems Land (RBSL) uses Soucy rubber tracks on its Warrior variant of the mortar offered for the UK's Armored Battlefield Support Vehicle program.
In September 2018, as part of Phase 3 of the Australian Land 400 program, the AS21 Redback vehicles of the South Korean company Hanwha Defense and the KF41 Lynx from Rheinmetall were selected for the new tracked infantry fighting vehicle. Soucy has its own rubber track for the AS21, and CDS has steel tracks for the Lynx. The wheeled platform was chosen in an earlier program for the Combat Reconnaissance Vehicle reconnaissance vehicle, it turned out to be the Rheinmetall Boxer 8x8 armored personnel carrier.
The French army is often cited as an example of a military structure that has replaced its tracked armored vehicles with wheeled ones, including medium armored personnel carriers and infantry fighting vehicles. This experience proved to be successful during operations in Mali, when wheeled armored vehicles and wheeled artillery were transferred to the capital of Senegal, Dakar, and then reached the Malian province of Gao on their own.
Although so far no major army has followed France's example, there is a clear trend towards purchasing more mobile medium-weight 8x8 wheeled vehicles. Like Australia, the British Army chose the Boxer for its Mechanized Infantry Vehicle program to replace the obsolete FV430 tracked armored personnel carriers.
Soucy has installed its rubber track on the Malaysian army's Adnan ACV-300 infantry fighting vehicles and, according to Sloane, they have been approved by the UN for deployment in peacekeeping operations. The Soucy rubber track is also installed on the CV90s from two of the seven operating countries, Denmark and Norway.
Sloane emphasized:
“The question is whether tracks and wheels can work together in combined arms operations. With steel track platforms, they will not be able to work together over long distances. It will be a logistical nightmare, but the composite rubber track has closed the gap.”
Another look
While CDS and Soucy see great potential in tracked vehicle programs, wheeled armored vehicle manufacturers see the market somewhat differently. Peter Simson of Tyron Runflat said that there are only two large tracked BMP programs - the American Next Generation Combat Vehicle and the Australian Land 400 - while there are many programs for wheeled armored vehicles, for example, the British Boxer 8x8.
“We see these needs in connection with the fact that combat operations in populated areas and rapid maneuvering operations are expected rather than traditional warfare. The flexibility of the wheels is most suitable here, and not the sluggishness of heavy armored vehicles on tracks."
Simson said that with the use of Tyron compound rubber inserts, the availability of theater equipment is now growing and that wheeled combat vehicles and support vehicles are not flawed and meet the FINABEL Agreement pneumatic tire test standards. This standard is a strict set of criteria that must be met by military-grade wheels with impact resistant inserts for various types of damage.
The use of self-supporting wheels is very important, they allow the machine to continue its task in the event of a wheel damage or deflation.
"The reactive wheel includes a beadlock - a locking device, a special element of the wheel disk that does not allow the tire to jump off the rim, which provides full maneuverability", - said Simson.
“Centralized tire pressure control systems are making a contribution. On modern combat vehicles, they allow the driver to deflate and re-inflate the tires as needed to maximize traction on sandy or soft terrain, which further improves maneuverability and increases the likelihood of completing a mission. Without a beadlock, the wheel will simply spin on the tire, effectively immobilizing the car."
Reinforced rubber sidewalls or inserts also play an important role in absorbing the impact and shock of various obstacles on rough terrain, Simson says, and provides a secure fit for the tire.
“Conversely, composite or plastic hard inserts do not absorb impact and, if broken, can seriously damage the wheel and tire, which can lead to complete loss of mobility. In addition, it is impossible to guarantee a secure fit with plastic or composite inserts, as they, unlike rubber inserts, do not provide the compression necessary to hold the tire in place."
Tyron's All-Terrain Rubber Multi-Part (ATR-MP) inserts guarantee tire retention, shock absorption and also reduce logistical stress as no special mounting tools are required, meaning tire changes can be performed using standard tools. Simson noted that this is the reason that products with this technology are the most popular products of the company.
The ATR-MP insert is usually made in three parts, which are bolted together to provide a snug fit around the wheel. During installation, one of the tire beads is applied to the rim, then a reactive insert is installed and finally a second beadlock is added. In the case of military-style wheels, the insert is usually made in two parts, which are bolted together to ensure a secure fit. The split inserts use a steel core to provide strength and rigidity, while the surrounding rubber ensures anchorage and shock absorption.
“We also offer Tyron ATR-Carbon inserts that use carbon fiber instead of a metal base and some rubber. At the same time, all characteristics are preserved, but the mass is reduced by about 40% , - said Simson.
“For users of standard one-piece one-piece drives, Tyron has developed the Tyron ATR-Custom technology. This insert has all the benefits of Tyron's ATR-MP technology, but in just two parts."
he added.
At DSEI, the company unveiled the Tyron ATR-SP (single-piece) rubber insert.
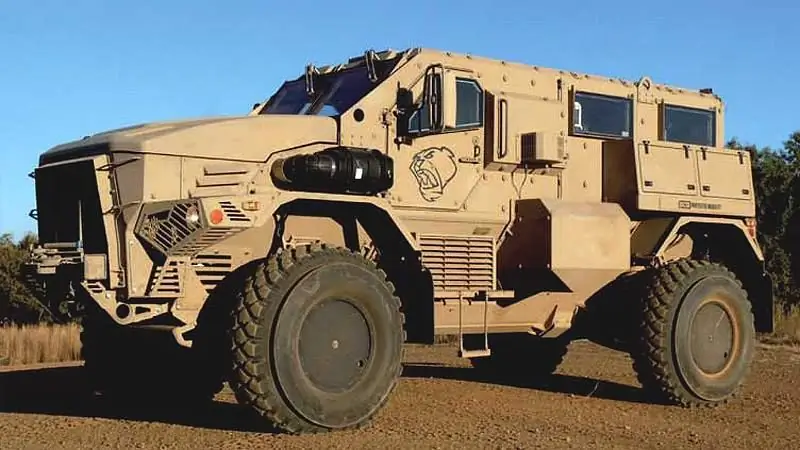
Expected needs
Simson believes that in connection with the expansion of the wheeled armored vehicle market, the demand for composite rubber inserts is growing accordingly. Tyron also supplies products for Yugoimlort's Lazar and Milos armored vehicles, DCD Protected Mobility's Springbuck and Mountain Lion vehicles, Acmat's Light Tactical Vehicle 4x4 and the Egyptian Timsah / Crocodile 4x4 vehicle.
French armored vehicle chassis company Texelis believes the French Scorpion program is a good example of the transition from tracked to wheeled vehicles. The main driver here is the need for increased mobility. This was announced by a representative of the company, noting at the same time that this transition is limited mainly to vehicles weighing less than 35 tons. The company was awarded a contract to develop a Serval 4x4 vehicle for the French army.
According to Texelis, the increased mobility requirements of many armies are in response to advances in technologies such as drone swarms, artificial intelligence and continuous battlefield surveillance. A company spokesperson added that as power transmission technology advances, wheels are becoming more reliable, “for example, sophisticated suspension systems, centralized tire pressure control systems, and inline insert technology.” This makes wheeled solutions more resilient and adaptable to various conditions, including military operations in populated areas."
Despite the growing competition from rubber tracks, wheels are still considered the preferred choice for armored vehicles, moving mainly on roads, but as the mass of these vehicles increases, the problem is becoming more acute. A Texelis spokesman noted:
"Today, there are two rather pressing issues: payload (due to armor kits plus more electronic and power generation equipment) and durability (versus steel tracks)."
The debate about which is best for armored vehicles, a caterpillar or a wheel, will continue in the future, as competition grows in the market for vehicles of the middle category by weight. Technological development complicates the decision-making on the choice of this or that propulsion device, but at the same time it benefits the military, since the mobility of armored vehicles will improve in any case.