
When designing armored combat vehicles (AFVs), it is necessary to integrate numerous subsystems from different suppliers, in particular, the power unit (engine and transmission), suspension and chassis (wheeled or tracked), steering and brakes, ballistic protection, weapons, turret or remote controlled weapon module, communication system, fire control system, sighting / optocoupler systems, ergonomic seats, weapons of mass destruction system, heating and air conditioning system, ammunition, self-defense systems and vetronic.
Since the late 90s, the tendency to replace tracked vehicles with wheeled ones has intensified, one of the clear examples of this process is the Stryker armored vehicle of the American army. However, this trend later partly weakened, as the military recognized the superiority of heavier tracked vehicles in protection and firepower. Of course, vehicles of such categories as, for example, BMP and MBT, are at the top of the design of armored combat vehicles, but on the other hand, their development is an extremely complex process.
Building a good car is not easy
In every AFV project, designers have to build a triangle with three interdependent sides: firepower, mobility and protection. This makes the design of such platforms a kind of complex professional task, which is also based on rapidly changing initial data.
One could get something similar to an AFV simply by adding steel plates to the truck chassis, but creating the right platform to the highest standards is a completely different matter. For example, designing a carrier chassis is much more difficult than designing a conventional chassis. Welding of armored steel is another highest art, specialists who are able to perform this work with high quality cannot appear at the click of their fingers; a lot of effort and money must be invested in their preparation. This is why technology transfer agreements are usually part of a complete procurement contract, as emerging industrial countries strive to master these competencies.
Many AFVs are currently available on the world market, including vehicles of the MRAP category (with increased protection against mines and improvised explosive devices). But, unfortunately, the production of MRAP platforms is beyond the capabilities of many countries. But there are exceptions, for example, Panus Assembly is going to enter the world MRAP market with its Phantom 380X-1 platform. This 19-ton vehicle is already in service with the Thai Marine Corps. Chaiseri Metal and Rubber, another MRAP machine manufacturer in Thailand, has produced over 100 First Win 4x4s to date, and Malaysia has also bought a modified version called AV4.
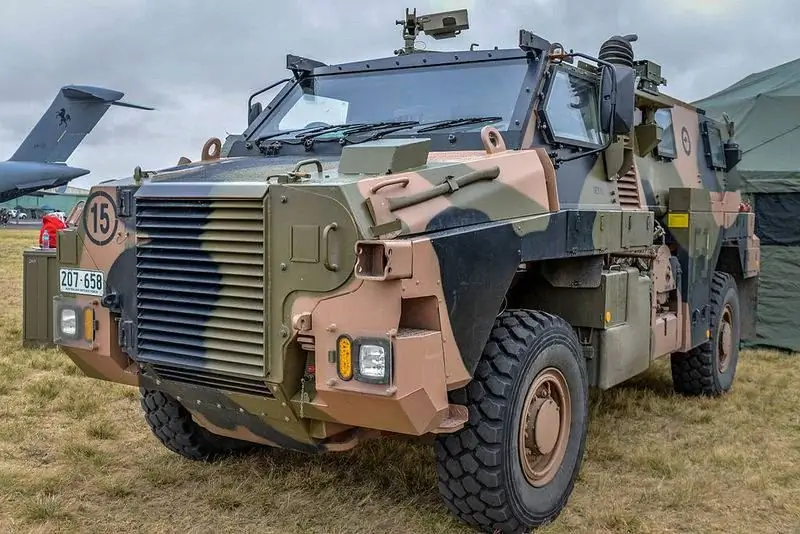
However, many countries are eager to develop their own independent projects when it comes to armored combat vehicles, but the desires do not always coincide with the possibilities. A prime example of how programs can perform poorly despite government efforts is India with its Arjun tank. The program began in the 70s of the last century, and since then this tank has gone through countless stages of development and testing. However, only 124 of these tanks have been adopted by the Indian army to date.
After the next December tests, the Indian army adopted an updated version of the tank and now wants to order the 118 MBT Arjun Mk IA, the production of which will most likely begin before the end of 2019. The new variant includes 14 major changes, including an automatic target tracking, an automatic transmission and an improved suspension. However, the Mk IA is still only an intermediate model, since the upgraded version of the Mk II will only be ready for production in 2021 or 2022.
However, the Mk II prototype, which has 72 modifications compared to the original Arjun tank, has a too large mass of 68.6 tons and therefore needs to be reduced. The Indian army demanded to modify the hull and turret and achieve this. The defense research and development organization reluctantly agreed to reduce the mass by 3 tons, but the army is not at all convinced that this will bring any result and improve the tactical mobility of the tank.
According to foreign suppliers of parts, unfortunately, many Arjun tanks in service with the troops had problems associated with a lack of spare parts. For example, in 2016, 75% of Arjun tanks failed due to technical problems. This is a slightly funny situation, as for the tank, conceived as an entirely Indian project, less than 30% of its components were ultimately manufactured by the local industry by the local industry.
India is also currently reflecting on two of its major AFV programs. First, a project on a promising Future Ready Combat Vehicle worth $ 4.5 billion to replace it with a local MBT. The second, a project worth $ 2, 8 billion for a promising BMP Future Infantry Combat Vehicle, which should replace the BMP-2.
Custom service
If a country without existing AFV infrastructure has an irresistible desire to develop its own platforms, you need to think about attracting a specialized company that offers combat vehicle design services.
One such renowned service provider is the Irish suspension and transmission company Timoney. Timoney spokesman Simon Wilkins said on the matter:
"Suspension systems, in particular independent suspensions, represent a specific area that is now associated with Timoney due to the fact that we created technology in the early 70s and have remained at the forefront of technological development ever since."
The company also focuses on power units, transmissions, axles, steering, braking systems and chassis, vehicle dynamics analysis, and full machine subsystem integration. Wilkins said Timoney could offer a complete design process or act as a subcontractor, explaining that “there is no approved out-of-the-box design for a machine development project.
“The sets of competencies of our customers are quite different, however, as well as the goals of each program. Some have a clear idea of their project, while others can rely on us to develop and develop the concept, starting from a very limited design assignment."
“We are able to tailor our participation in customer programs to meet their individual needs. In reality, this can range from providing systems engineering services, where we create a separate, rather specific system, to providing a complete turnkey solution for the development of an integrated platform, including the delivery of a prototype manufactured at our factory in Ireland."
Wilkins continued.
Some of the notable designs have appeared on Timoney's drawing boards, such as the Australian Bushmaster, the Singapore Bronco tracked and wheeled Teggeh 8x8, and the Taiwan Cloud Leopard 8x8. Wilkins commented, “We continue to work with major manufacturers in many countries and over the past few years we have supported companies such as Lockheed Martin, Hanwha Defense, Yugoimport and RT Pindad. Different operators have more than 4,000 vehicles with our technologies in service."
It is clear that technology transfer and licensing are very important to Timoney's business model. She does it on five continents, although, according to Wilkins, "Not all of our customers are striving for this and this is by no means the main part of the projects in which we participate, but it undoubtedly remains an active part of our business and in many cases is the main reason why customers come to Timoney."
He explained:
“Each customer has its own requirements and characteristics that need to be translated into a project, be it operational requirements, climatic or external factors, budgetary constraints or the competence of the local industry. These are just a few influencing factors that the designer must take into account. There is no one-size-fits-all approach, quite often our role is to explore the options available, given the required capability / cost ratio, and it’s okay for us to get the job done on a very tight schedule.”
Regarding the economic efficiency of a country building its own new AFV, Wilkins observed the following:
“Many developing countries are moving from the tradition of buying cars from established factories to creating a new independent model that includes local production, ownership and control of technology, job creation and contribution to the local economy. This is not an easy transition, as the successful development of a new machine is a huge and complex technical challenge. Well-known manufacturers usually have many years of experience on which they can rely and this competence gap is extremely difficult to close."
Wilkins also noted:
“Timoney's 50 years of experience allows us to offer our customers the opportunity to significantly advance the learning curve in a very short time and eliminate huge technical risks from the development process. We have successfully completed development programs in developing countries and continue to do so. We believe this is clearly a low-cost approach that offers a wide range of benefits."
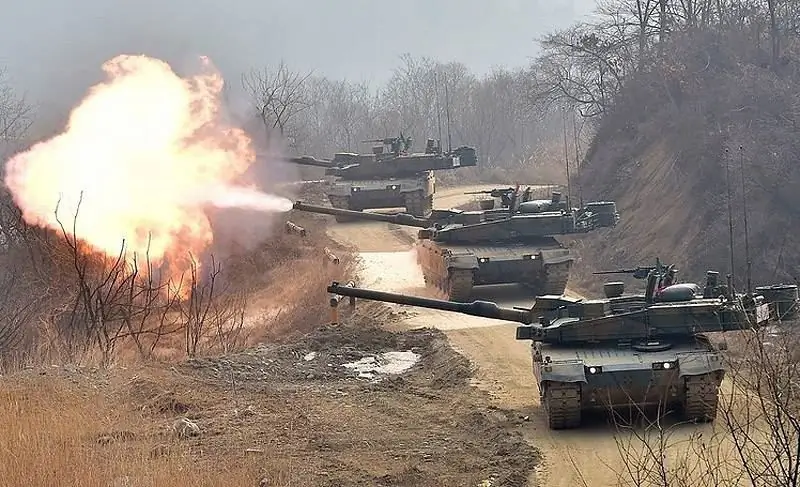
Manufacturing license
The Malaysian program for the production of 257 armored vehicles AV8 Gempita 8x8, based on the Pars machine of the Turkish company FNSS, clearly shows how the country can acquire its own capabilities through technology transfer and licensed production. Malaysia decided to start local production of the AV8 at the facilities of the local company DefTech.
However, Malaysia has subcontracted with a number of unique suppliers of various systems. Thales and the Sapura Thales joint venture play a key role in the Gempita program, providing embedded communications, vetronics and battle control systems. The Surround Camera System and Driver Vision System are also provided by Thales, a renowned optoelectronic specialist. For the reconnaissance option, this company supplied its Catherine optoelectronic station and the Squire surveillance radar mounted on a telescopic mast.
Malaysia also adapted the weapon systems to its needs, choosing the DUMV and ATGM ZT35 Ingwe from the catalog of the South African company Denel. The missiles are mounted on a Denel ACT30 turret armed with a 30mm cannon. Denel supplied 177 modular turrets (all assembled in Malaysia) and weapon systems for seven different AV8 variants. The AV8 Gempita is equipped with a Deutz engine and ZF transmission.
Although the AV8 is based on the Pars machine, Malaysia has all the intellectual property rights for export to other countries. In this regard, DefTech demonstrated the IFV25 variant in 2017 in Saudi Arabia in the hope of expanding sales.
Let's go back to Thailand. The Defense Technology Institute (DTI) is developing the Black Widow Spider 8x8 armored personnel carrier for the Thai Army, as well as a variant of the Amphibious Armored Personnel Carrier (Amphibious Armored Personnel Carrier) for the Thai Marine Corps. The AARS machine is powered by a Caterpillar C9 engine coupled to an Allison automatic transmission. It is also equipped with a buoyancy kit, floats installed on the sides of the hull allow you to swim at wave heights up to 0.5 meters.
Another difference is the elongated body between the second and third wheels and additional booking. The hull roof is reinforced to support the roof weight and rollback forces.
AARS armored personnel carrier weighing 24 tons was shown in 2017 with an uninhabited tower from ST Kinetics, armed with a 30-mm cannon and a 7.62-mm machine gun paired with it. A representative of the DTI Institute said that the AAPC is 90% unified with the Black Widow Spider machine. The latter is equipped with an uninhabited ST Kinetics turret armed with a 30mm Mk44 Bush master II cannon and a coaxial 7.62mm machine gun.
This 8x8 program clearly illustrates why some countries are trying to establish their own AFV production. The Thai military has a significant number of M113 armored personnel carriers, which need replacement and therefore the army is looking for an economical vehicle that would meet these intentions. Despite the acquisition of the Ukrainian BTR-3E1 and Chinese VN1, Thailand needs a cheaper car, worth no more than $ 3.6 million, which, as DTI hopes, will meet the needs of the military. However, bringing this machine to mass production is a technically rather complicated process and it remains to be seen whether the Thai military will invest in this Thai solution.
Ricardo, a consulting and engineering company, has been listed by DTI as a partner, while Singapore-based ST Engineering has confirmed that it will act as a technical consultant and supply components if requested by DTI. Despite the fact that in the DTI documentation the Black Widow Spider machine is similar to Singapore's Teggeh, the company insists that these projects were created independently. According to the institute, more than 60% of the components of the Black Widow Spider will be Thai-made.
The British company Riccardo is another specialist that offers AFV design services; his portfolio includes a Foxhound vehicle operated by the British Army.
Singapore probably has the most high-tech AFV production capabilities in Southeast Asia. After work on the development of Bronco and Teggeh machines with the assistance of Timoney, the newest armored combat vehicle of ST Kinetics is a next-generation combat vehicle weighing 29 tons, designated Next-Generation Armored Fighting Vehicle. The start of production of the vehicle in the BMP version equipped with the DUMV Adder M30 from ST Engineering is scheduled for this year.
However, in March, an image of a version of the vehicle equipped with the Rafael Samson 30 DUMV (a modified version of the Samson Mk II module installed on the Bionix II BMP) appeared, armed with a 30-mm Mk44 Bushmaster II cannon, a 7.62-mm machine gun paired with it and a launcher with two missiles.
Collaboration
Often, close cooperation between parent companies and component suppliers takes place, and interesting alliances are formed. For example, the Australian company EOS has developed its T2000 tower in collaboration with the Israeli Elbit Systems. An EOS spokesman said the new product "is intended for overseas markets and three tenders have been submitted so far, one of which is Australia's Land 400 Phase 3 program." Indeed, the T2000 was presented on the BMP of the South Korean Hanwha Defense AS21 Redback, proposed for Australia. The T2000 module can be armed with a 25mm, 30mm or 40mm cannon, as well as two Rafael Spike LR2 missiles in an ascending launcher. The tower is available in habitable or uninhabited configuration and can be equipped with IMI's Iron Fist active defense system and Elbit Systems' IronVision vision system.
Well-known in the defense industry, the Belgian company CMI Defense supplies its towers and weapons to various leading armored vehicle manufacturers. A company spokesman said that “The Cockerill 3105 turret with 105mm cannon, the market leader, is targeted at the light / medium tracked and wheeled vehicle segment. It is currently being mass-produced and installed on the Kaplan MT medium tank from RT Pindad and the K21-105 medium tank from Hanwha Defense Systems. The Cockerill 3105 turret was selected by SAIC for the US Army's new Mobile Protected Firepower program.
Of course, there is enough space for closer cooperation between the leading manufacturers of armored combat vehicles. For example, a report by the research corporation RAND “Opportunities for European cooperation in the field of armored vehicles” states that “… There is a significant degree of fragmentation of armored vehicle holdings in Western Europe. Approximately 37,000 vehicles consist of tracked vehicles from 47 different families and wheeled vehicles from more than 35 different families. This contributes to overcapacity in the European defense industry relative to the size of the European market and impairs industrial cooperation, consolidation and integration of supply chains."
The report identifies 18 armored vehicle manufacturers, of which only 8 export products to other countries. Market saturation has led to landmark consolidations such as the 2016 merger of KMW and Nexter. Major producers need to focus on exports in order to maintain business profitability.
The RAND report suggests that joint modular upgrades (such as new engines and improved protection) of existing armored vehicles could lead to a 52-59% cost reduction for armored personnel carriers. Meanwhile, joint purchases of finished products can save buyers 20-25%.
On the other hand, the joint development of a new platform could be 26-36% cheaper due to savings on
"The initial cost of R&D, consisting of advanced technology development, system design and integration, initial prototyping, testing and performance evaluation, and manufacturing costs from small-volume production to final machine manufacturing."
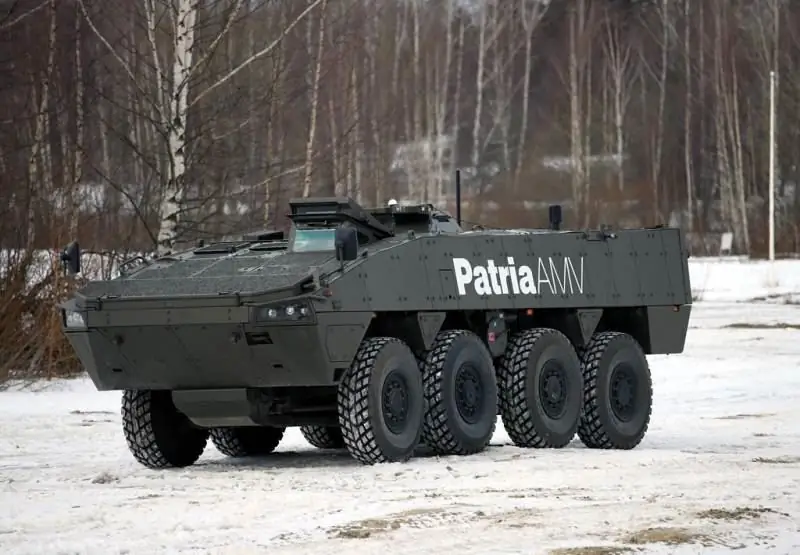
Green future
Advances in civilian hybrid vehicle technology and recent EU environmental directives are helping to revitalize research on alternative energy. A new joint European research project called HybriDT (Hybrid Drive Trains for Military Vehicles) is an example of a shift in focus.
Multinational Efforts
Currently, negotiations are underway with companies on the HybriDT contract with the prospect of its issuance in 2019. The initiative was put forward by the working group on the development of ground systems of the European Defense Agency (EDA).
The one-year project will evaluate the practicality of using a hybrid propulsion system in military ground vehicles, with a particular focus on hybrid drives. As the representative of the EOA explained, during its implementation, in addition, the volume of necessary additional developments will be checked to eliminate potential technological gaps, taking into account the specific requirements of the military. The Agency has reserved about $ 1, 1-2, 2 million for the project.
Germany is expected to lead this project, which will include Austria, Finland, France, Italy, the Netherlands, Slovenia and Sweden. However, the EOA said that there is still an opportunity for other countries to join the program at a later stage.
The HybriDT project is an example of a rapid and significant change in propulsion for military vehicles. An EDA spokesman explained that "the military should include hybrid and EV aspects in their long-term plans for the development of military vehicles."
Civilian influence
In the European Union, legislation stimulates the development of hybrid and electric drives in the civilian sphere, as a result, there is growing interest in the design of such drives for military equipment.
In recent years, the European Union has issued numerous environmental protection documents aimed at reducing emissions from civilian vehicles, for example, Real Driving Emissions and World Harmonized Light Vehicle Test Procedure issued in 2017; tax breaks were also introduced for owners of vehicles with low-emission engines. Commercial companies have thus responded by investing more in low-emission vehicle R&D, and hybrid drive and electric motor technology is now gaining interest in military circles as well.
As the representative of the EAO explained, the EU states
"Realized that hybrid technology is rapidly developing in the civilian automotive industry and will naturally have an impact on military technology."
One of these countries is Slovenia. “Technological advances in the civilian automotive industry will have a huge impact on mobility in the military sector, in all areas of operation - on land, sea and land. The future long-term development of vehicles will largely take into account the transformation of the civilian industry,”said a representative of the Slovenian Ministry of Defense.
A spokesman for the Finnish company Patria Land Systems explained:
“Emissions standards have been developed, which has forced civilian companies to pay close attention to new technologies. Companies are spending a lot of money on developing these technologies and defense structures are starting to pay attention to this, looking for something that can be useful in the military sphere."
Patria Land Systems is Finland's representative in the joint EOA project.
The driving force behind design
The change in environmental legislation in the EU also aims to influence the military equipment industry directly.
The representative of the Dutch Ministry of Defense noted that, having the prospect of banning the production of diesel engines in Europe in 2030-2040, military organizations are forced to study other types of power plants, since today diesel engines are still the basis of all military combat and auxiliary equipment.
A Patria spokesperson added:
“This shift towards hybrid solutions has been driven by political decisions. But whatever happens, you have to stay ahead and use the technologies of the future."
The hybrid technology that companies hope to borrow from the civilian industry is changing. "There are many different technologies available in the civilian market, but the real question is how the military wants to use this hybrid technology and that of course has an impact."
One of the defining characteristics of any project is the preservation of the machine's capabilities.
"It should be noted that the needs of the military are different from the civilian needs, the advantages and disadvantages are arranged in accordance with the priority based on different messages, for example, special emphasis is placed on off-road cross-country ability and provision of technical support."
In any promising project, it is also necessary to take into account technical support throughout the entire life cycle, as well as completely different operating conditions in which these machines will operate. When will these technologies become commonplace in the military? This will depend on the outcome of the HybriDT project.