Robots on wheels!
Electronically controlled automatic transmissions, electronically controlled throttle valves plus electrically controlled steering systems, which are now increasingly standard features of modern vehicles, are heavenly manna for robotic platform developers. Indeed, the control signals can now be easily integrated into the existing processing units of these machines, which means that the bulky drives previously needed can be gradually sent to landfill
The special advantages of such systems are not only that they can be transferred from one machine to another. Ultimately, they will become so cheap that the “inline control” system will essentially remain in place in the vehicle and simply shut down to return to normal use (ie, manual control) of the vehicle.
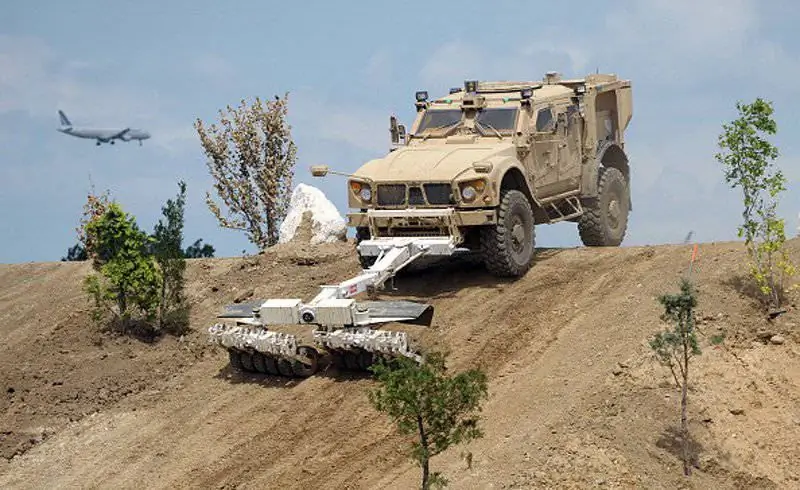
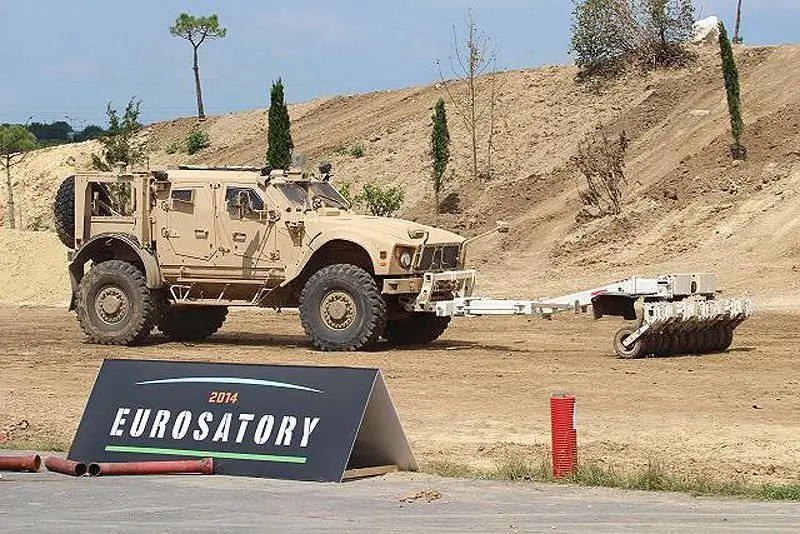
The M-ATV with a roller trawl shown by Oshkosh at Eurosatory 2014 was equipped with the Terramax robotic kit, the sensors of which are visible in the lower corner of the picture.
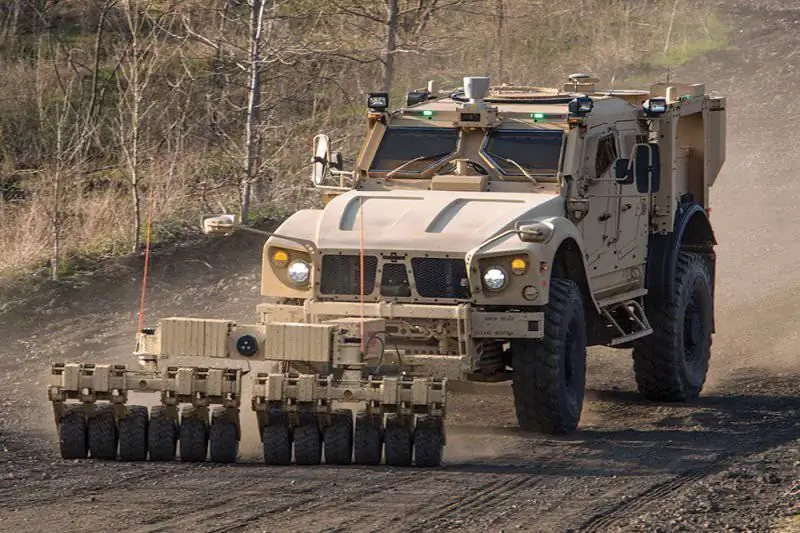
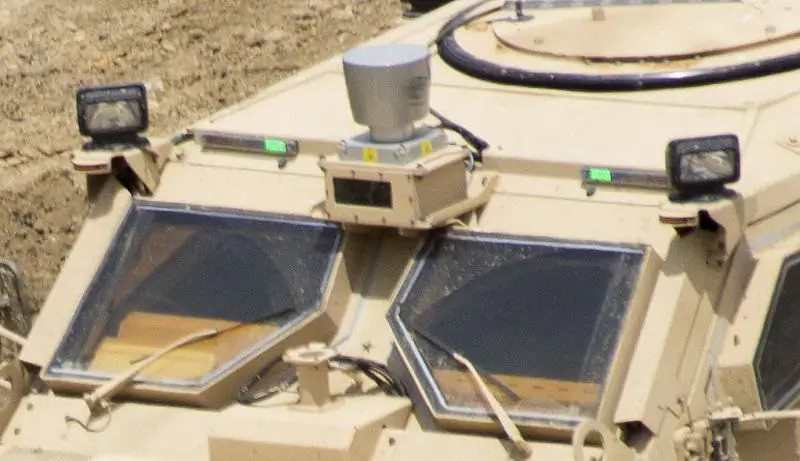
A close-up of the Terramax's rooftop sensors, which provide a clear view of what lies ahead, but at the same time the question arises - why are the windshields so clean!
Oshkosh: Among the American large vehicle manufacturers, the leader in heavy robotic vehicles is, of course, Oshkosh Defense. She began developing TerraMax robotic technology in the early 2000s at the request of the Defense Advanced Research Projects Agency Darpa. After years of development and improvement, in August 2012, the US Marine Corps Combat Laboratory and Oshkosh Defense applied TerraMax technology to test a transport convoy, which consisted of five conventional vehicles and two unmanned vehicles. The latter moved autonomously, albeit under the control of an operator with a remote control unit. While the company maintains its commitment to the Office of Naval Research on a cargo robot program, which will provide supply convoys with robotic means to eliminate contact with the enemy as much as possible, Oshkosh is also looking for other applications for its constantly upgraded TerraMax system. …
At the AUVSI 2014 and Eurosatory 2014 exhibitions, Oshkosh presented the M-ATV armored vehicle equipped with a Humanistic Robotics roller trawl capable of operating in autonomous mode. The vehicle's dynamic performance has been adapted to the trawl and Oshkosh will continue to experiment with mine clearance over the next couple of years. The demo, shown in Paris, was equipped with a roof-mounted lidar (laser locator). It is regarded as the primary sensor and is especially effective in dusty environments, “helping” the radars installed at every corner of the machine. In turn, optoelectronic sensors allow the operator to receive clear and distinct visual information about the environment. The modernization of the system mainly consisted of the development and installation of a new and faster computer capable of handling the higher sensor resolution required for improved perception of the surrounding area, which includes the detection of obstacles and suspicious objects in dust or greenery, which in turn allows the car to move faster. (just like a motorist at night is able to go faster with more powerful headlights). The new kit has an open architecture that allows new types of sensors to be installed into the TerraMax system without any problems.
Lockheed Martin: Fort Hood, January 14, 2014. A convoy of four vehicles, two Palletized Loading System trucks, an M915 articulated truck and a Humvee escort crossed the False City, clearing all types of obstacles including local traffic, pedestrians, and more. What made the event so special was that, with the exception of the Humvee, all the cars in the convoy were driverless - literally. They were equipped with the optional Autonomous Mobility Applique System (Amas), developed by Lockheed Martin in accordance with a contract received in October 2012. The task was to develop a multi-platform kit that combines inexpensive sensors and control systems that could be installed on army and marine vehicles, reducing the burden on the driver or providing full automatic driving under supervision. The car retains the ability to drive manually, but adds sensors and control functions that alert the driver of danger. According to military statistics, most of the accidents in transport convoys are caused by fatigue and loss of concentration. Amas is part of the Cast (Convoy Active Safety Technology) program, which leverages Lockheed Martin's expertise with the SMSS robot. The main sensors here remain GPS, lidar and radar, plus a control system, which, having a certain level of artificial intelligence, ensures decision-making. A second series of demonstration tests were completed in June 2014 at the Department of Energy's Savannah River Proving Ground.
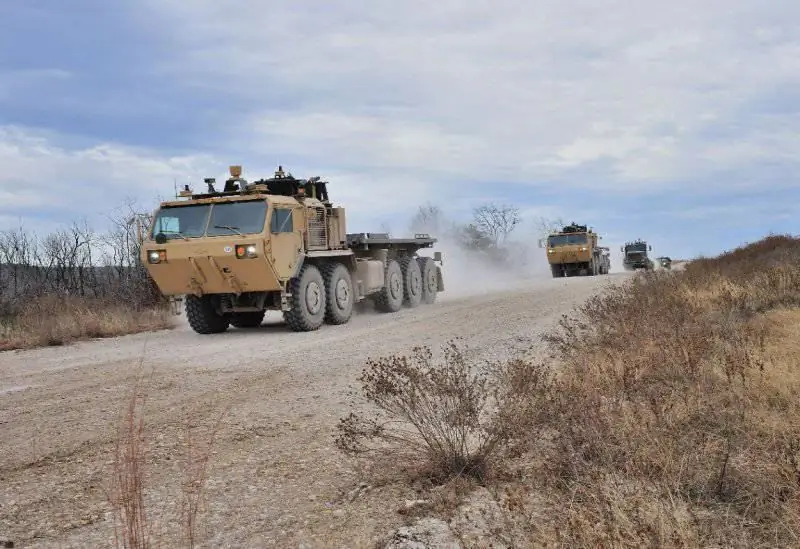
The Autonomous Mobility Applique System was developed by Lockheed Martin as part of the Convoy Active Safety Technology program
The unmanned vehicle-leader and the convoy of six autonomous systems equipped with the Amas system that followed it at speeds up to 65 km / h took part in the tests (the length of the columns was also doubled in the tests). All vehicles were medium and heavy trucks of the FMTV family: one MTVR, two PLS, two M915 tractors and one HET Further safety tests were carried out in July 2014, followed by a performance demonstration in July-August 2014.
Mira: The British company Mira specializes in advanced vehicles and systems, including robotics. The company has developed a platform-independent set of Mace (Mira Autonomous Control Equipment - Mira's autonomous control equipment), which can be integrated into virtually any ground platform to obtain the required level of autonomy (remote, semi-autonomous and autonomous modes), depending on the needs of the customer. Mace was installed on various vehicles in order to show its potential applications (solutions based on Sherpa and Land Rover vehicles for logistic support of dismounted infantry, while a vehicle equipped with the Guardsman surveillance kit based on the Mace kit worked as a 4x4 perimeter security platform) …
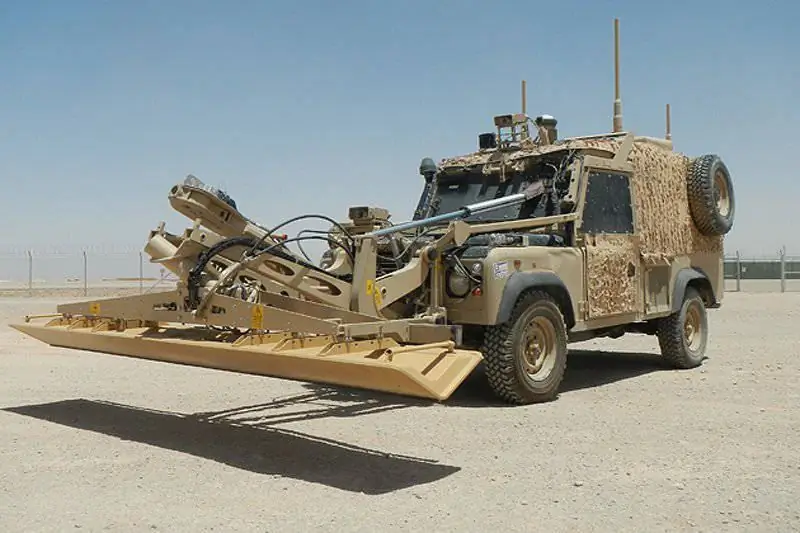
The platform-independent Mace robotic kit, developed by the British company Mira, has been deployed in Afghanistan on Land Rover vehicles for the detection of directional landmines.
Currently, one of the MACE solutions implemented in practice is the "Project Panama" system, which operates as an unmanned complex for checking and clearing routes. The system has been in service since 2011 in Afghanistan, it is used to detect bombs and is based on the Snatch Land Rover (SN2) cross-country vehicle. The Panama vehicle is used in remote and autonomous modes at ranges of up to 20 km in order to ensure maximum personnel safety. In mid-June 2014, the British army announced that Panama would remain in service until 2030, and Mira guarantees the further development of its MACE technology platform. At AUVSI, Mira demonstrated its capabilities in roadside inspection; After several years of using lidar and radar, the focus of the new system has been on the detection of suspicious objects using technical vision. This is not only related to cost - a vision detection system costs an order of magnitude less than a lidar-based system - but also because the use of additional types of sensors allows additional data to be transferred to the system and, therefore, increases reliability and accuracy.
Ruag: The Swiss company Ruag Defense is also working on a kit that transforms traditional vehicles into vehicles with controlled autonomy. The kit was named Vero (Vehicle Robotics) and was first shown in the spring of 2012 aboard a light armored vehicle GDELS Eagle 4. The system was shown at Eurosatory 2014 in remote control mode, it is also able to follow a pre-planned route, indicated by sequential coordinates. Compared to the car shown in 2012, which operated only in remote control mode, the car at the exhibition in Paris had a set of obstacle avoidance sensors installed in front. Two lidars were installed on the left and right of the bumper (of course they will be transferred to the hood to reduce distortion from rising dust), and the radar was installed in the center of the bumper with another device to the right of it, called the "special optical sensor" by the company.
According to Ruag Defense, several months of testing are required to qualify the software and hardware. Currently, the Vero kit is integrated on two more military vehicles, the models of which are not disclosed. And in 2015, the system will be installed on a purely robotic platform weighing about three tons, although the choice between tracks and wheels has not yet been made. Ruag is in discussions with partners and has yet to decide whether it will install its Vero system on an existing or specially designed platform.
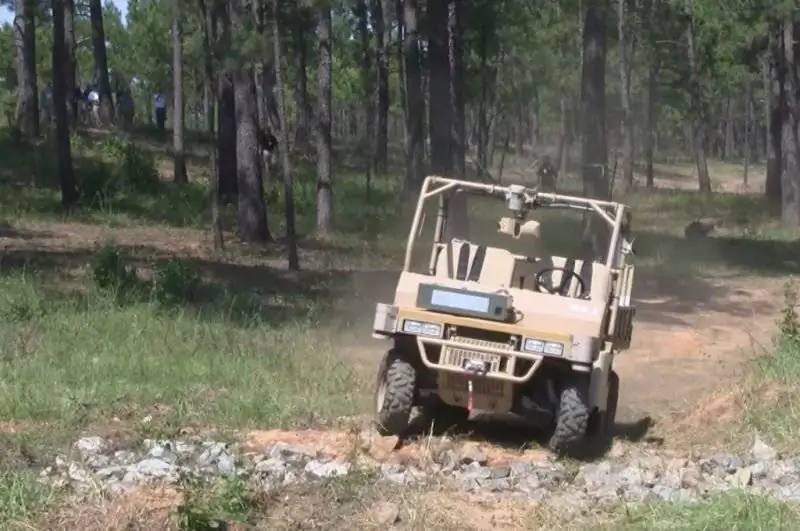
Ground Unmanned Support Surrogate robotic complex was developed by Torc Robotics based on the Polaris MVRS700 6x6 chassis
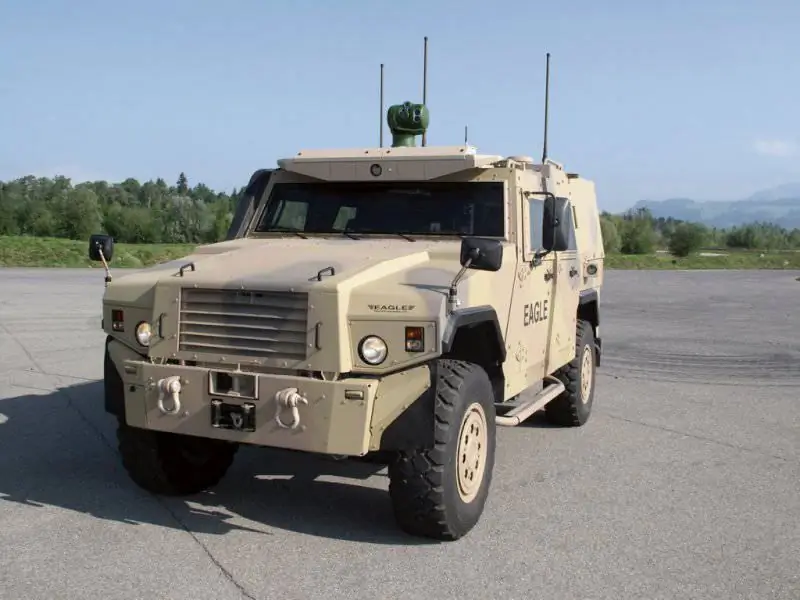
The Swiss company Ruag is working on its Vero kit, which is currently installed on the GDELS Eagle 4. Some of the sensors are installed on the roof, and some are installed on the bumper.
Torc Robotics: The American company, a specialist in robotic solutions for the military, mining, engineering and agricultural sectors, is currently working under the Marine Corps Ground Unmanned Support Surrogate (Guss) program. Torc Robotics has been involved since 2010 in the development of a light vehicle capable of independently delivering supplies to troops in combat conditions, transporting marine supplies or evacuating the wounded. Using robotic modules, Torc Robotics has transformed four Polaris M VRS700 6x6 buggies into robotic vehicles capable of carrying a load of about 900 kg.
The AutoNav module is a key element to create a robotic vehicle with three different modes of operation: point-to-point navigation, follow me and remote. The interface is a hand-held WaySight device that allows the operator to select the operating mode, as well as either control or monitor the machine. This technology was then refined and carried over to the M1161 Growler, the vehicle chosen by the Marine Corps to be transported inside the V-22 Osprey tiltrotor. The program is currently known as Guss AITV (Autonomous Internally Transportable vehicle). The sensor kit includes an inertial navigation system, cameras and lidar. It was first tested in real-life exercises during the Rimpac 2014 exercise in Hawaii in June, showing its practical value in wounded evacuation operations and in reducing the burden on infantry. After the exercise, the need for some technological improvements was identified. The company's additional modular system was also used to develop the Robotic Assault Zone Terminal Evaluation Kit, capable of assessing potential soil heterogeneity on the runways in order to reduce the risk for special teams of mine surveyors inspecting the runways. The kit uses many of the technologies developed for the Guss robocar and fits on a Polaris LTATV vehicle equipped with an MDA Mosquito soil sampler.
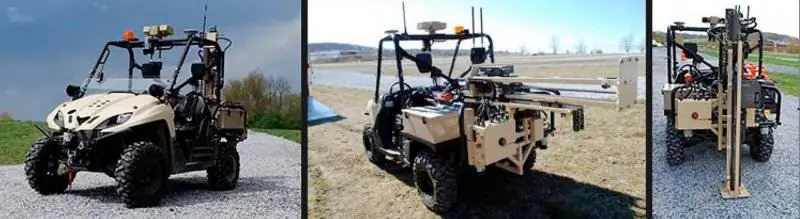
Polaris LTATV robotic vehicle equipped with Robotic Assault Zone Terminal Evaluation Kit with MDA Mosquito Soil Sampler (right in working position)
Polaris vehicles were recently selected by the Darpa Defense Advanced Research Projects Agency to compete in the Robotics Challenge simulating disaster relief scenarios of various origins. The Polaris Ranger XP 900 EPS vehicles, which were supposed to serve as a vehicle for robotic drivers, were equipped with robotic kits, and also implemented SafeStop Electronic Throttle Kill and Brake Actuation technology, which allowed to ensure the mobility of vehicles at the testing ground for modeling natural and man-made disasters. A power supply system for the robot was installed on a platform with a lifting capacity of 453 kg, and inside the cab, a bench and a steering column with an adjustable tilt in order to provide sufficient space for the robots to work with the machine.
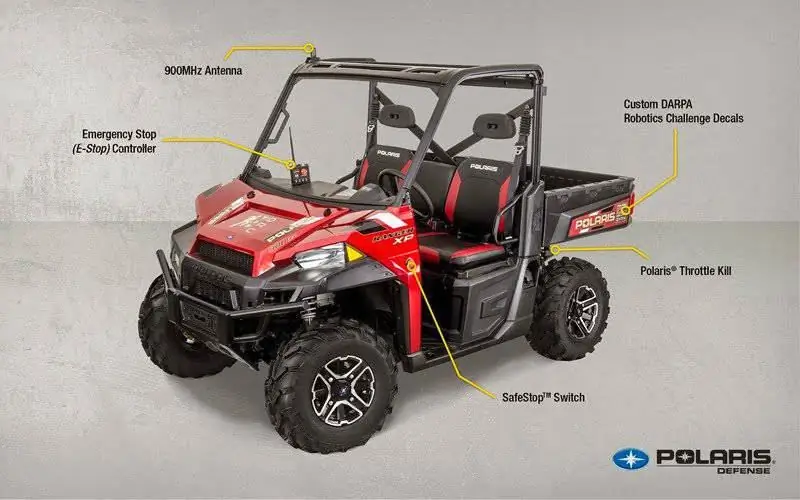
Polaris Defense is increasingly thinking about "robotization" when creating their machines. Its Ranger XP 900 EPS was selected by Darpa to compete in a robotic platform competition simulating a disaster relief operation.
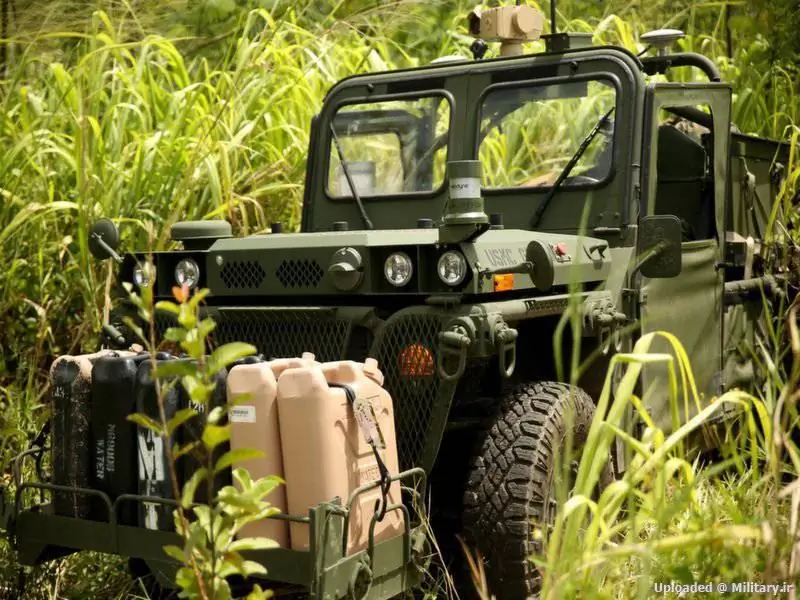
Torc Robotics used the lessons learned from the Guss program to robotize the M1161 vehicle transported in the Osprey tiltrotor. The resulting Guss AITV system was demonstrated at the Rimpac 2014 exercise
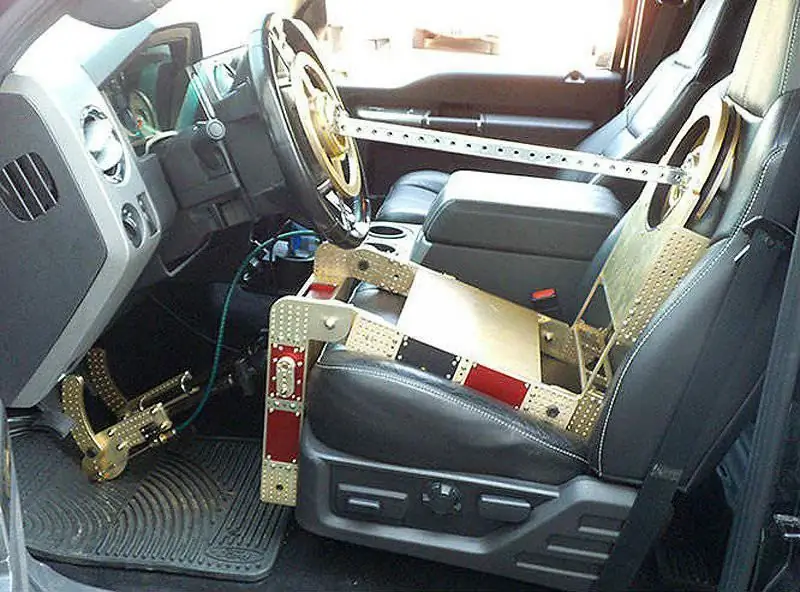
The Kairos Pronto4 Uomo is an add-on kit that closely resembles human functionality. It can be installed in just a few minutes in the cab of a standard human-driven vehicle
Kairos Autonomi: Why not replace the driver with a mechanical structure that mimics the structure of the human body? Engineers at Kairos Autonomi have followed this path by creating an optional Pronto4 Uomo robot kit that can be installed on a standard machine in ten minutes to provide remote control and GPS guidance. The system was shown in 2013, it weighs only 25 kg and folds into a suitcase. The metal structure simulates human movements, two "legs" press the brake and gas pedals, and the "hand" on the universal joints turns the steering wheel. The system can be powered by a standard military BA5590 battery and since no connection to the vehicle's on-board network is required, this reduces kit installation time.
The Kairos Autonomi catalog also has a more traditional Pronto 4 add-on kit. This modular system can robotize a conventional machine, giving it varying levels of automation, ranging from remote control to semi-autonomy. Installing the kit takes less than four hours. The Pronto 4 set consists of several modules among the "brain" functions performed by a computer module, while interface modules (steering wheel, brake, throttle and gearshift actuators) allow it to be connected to the machine. The system is available in various configurations, with a total weight of about 10 kg.
Selex ES: The company enlisted the help of the Milanese firm Hi-Tec in its work to reduce the risks to patrol teams by robotizing vehicles (where possible), especially robotizing machines that are less protected and therefore cheaper. For the developed system, designated Acme (Automated Computerized Mobility Equipment), Hi-Tec provides actuators, navigation systems, data processing and software, while Selex supplies infrared and daytime vision systems with narrow and circular (360 °) fields of view, infrared illumination, sensory data system analysis and simulators.
Selex ES has now finalized the final configuration, with a final prototype expected in fall 2014. The current Acme system, which is completely free from the restrictions of the International Arms Trade Regulations, should be ready for mass production in early 2015. Selex ES is already in talks with many potential customers. The interface and driving system are installed in half an hour or an hour. The carbon fiber steering system weighs 7 kg as opposed to its 12 kg steel counterpart. A stepper motor with a torque of 28 Nm provides rotation speeds from 18 to 180 rpm. Navigation sensors include a noise-immune GPS from QinetiQ Canada with two antennas operating on seven frequency bands (Acme is compatible with Galileo and GLONASS), as well as a semiconductor inertial measurement unit with a deviation of 0.5% per hour (this unit is used when the GPS signal is lost, usually for a short time). A roof-mounted laser scanner provides obstacle avoidance. The system weighs 60 kg, in automatic mode, the maximum speed is 40 km / h, and in remote mode, the company advises not to exceed 100 km / h. However, it should be noted that the Acme system must always remain under the supervision of the operator. It is able to repeat a predetermined route with an accuracy of two centimeters with deviations in speed up to 0.5 km / h. The throttle stepper motor delivers 14kg of force at 300mm / s. The pneumatic system is used to drive the clutch and brake, delivering a force of 60 kg at a speed of 300 mm / s. New georeferenced maps (georeferenced) can be used for the Acme system. A hardened push-button control console was developed as Selex ES decided to move towards game-style control systems that are more familiar to young soldiers. Selex ES is currently working on a program to "stitch" the images into a 360-degree view, which will eventually (possibly by the end of 2015) be implemented in a 3D helmet designed for remote driving.
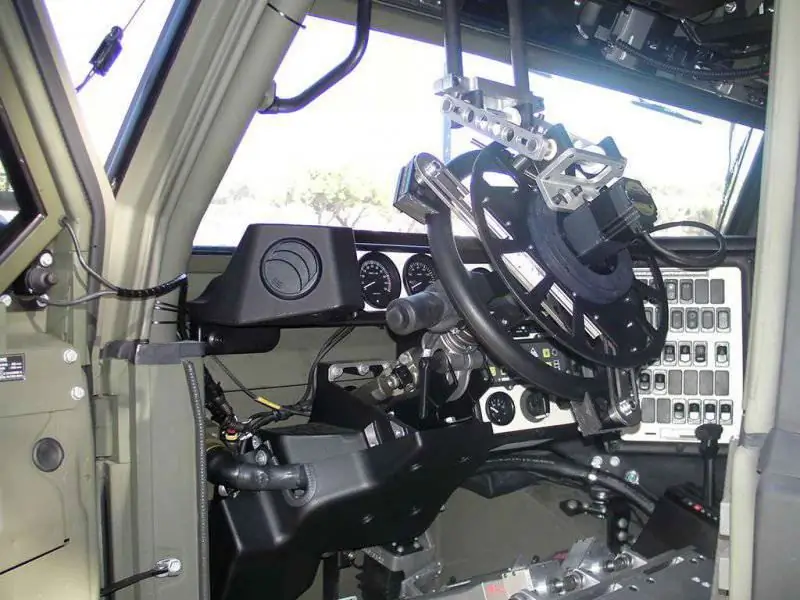
Selex ES's Acme Automated Computerized Mobility Equipment has recently been upgraded with new sensors. The company is also working on the development of new human-machine interfaces.
Oto Melara: The Italian company Oto Melara offers an additional system that was originally developed for civilian purposes. The remote control kit contains several actuators that can move the steering wheel, pedals and other controls. The system can be installed and removed in about one hour, but Oto Melara is currently working on new systems in response to the needs of the smart transport convoy.
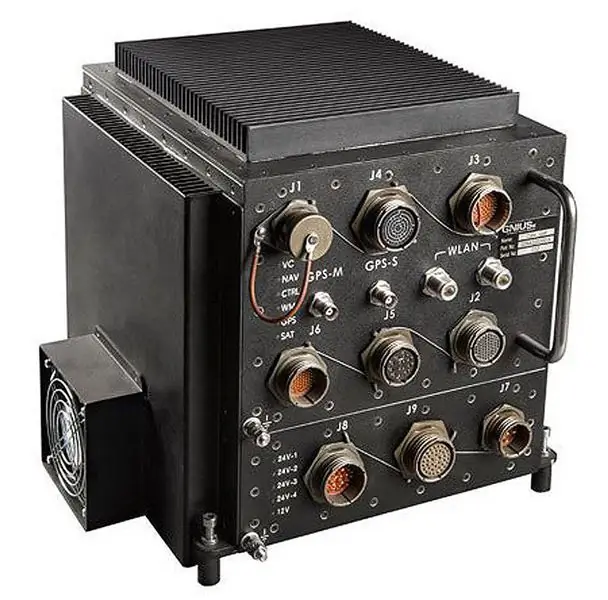
The Israeli company G-Nius, drawing on the rich experience gained with the Guardium series of robots, has developed a robotic kit that allows you to transform a ground platform into an unmanned system, the "brain" of which is shown in the photo
G-Nius: In addition to the robotic vehicles described above, the Israeli company G-Nius has developed a new robotic kit that allows you to turn any ground platform into an unmanned system with obvious mechanical variations in order to adapt to a specific vehicle. Whereas the previous G-Nius system consisted of many black boxes, the new product consists of one box, which includes a functional computer, navigation box, video / audio system and power distribution box.
Standard sensors include day / night uncooled thermal imaging cameras, rear and side cameras and communications, and obstacle avoidance can be added. The system allows you to work in four modes of different levels of autonomy. Line-of-sight operation is guaranteed at a distance of 20 km, but satellite communications can be added for longer distances. The new robotization kit is independent of the connected equipment, and thus all types of devices, from reconnaissance systems and silencers to weapons, can be connected to the kit. G-Nius offers its kit for various types of platforms, from light wheeled vehicles to tracked infantry fighting vehicles.