Heavyweights: Sherpa foot soldiers …
A category of ground robots has emerged that will finally shed the burden from the shoulders of an infantry unit. These systems are capable of carrying heavy loads, they can follow the squad, leaving the soldier with only his small backpack with the essentials while carrying heavier duffel bags. Another typical task of these robots is to replace vehicles with crews in dangerous tasks, for example, delivering ammunition to the front line or evacuating the wounded from the combat zone to a safer area

While walking robots could be the best solution to guarantee mobility close to human mobility, for now, heavy robots intended for logistics remain wheeled or tracked.
In addition to the above, reconnaissance kits (even mounted on telescopic masts) as well as explosive ordnance disposal kits with robotic arms and ammunition neutralization devices can transform these platforms into specialized vehicles. The advantage of these platforms is that they are lightweight and easily reconfigurable for other tasks in a very short time. Their level of autonomy, as well as mobility, can vary considerably: most of the solutions currently available are based on wheels, which provide an average level of mobility in difficult terrain, where tracks have proven themselves, which in turn are more noisy and structurally complex. At this time, walking solutions have been tested on an experimental level; an example is Darpa's Legged Squad Support System (LS3) walking support system.
The LS3 is a highly mobile, semi-autonomous walking robot capable of interacting with military units. The six-legged platform will eventually have a level of mobility comparable to that of a human, allowing dismounted units to move around without looking at their robots. The LS3 robot is electrically driven, it can carry 180kg over 32km and does not need any intervention for 24 hours. The platform has been undergoing trials since July 2012 in the US Army and Marine Corps. The three main autonomous modes of the robot are as follows:
- close behind the leader, when the platform tries to follow the trail of its leader as closely as possible;
- in the corridor behind the leader, when LS3 follows the leader while maintaining more freedom to make decisions along the way and
- movement along the waypoints, when the local perception of the system allows it to avoid obstacles on its way to the place indicated on the GPS grid.
The testing phase was supposed to last about two years, so it is likely already over.
Lockheed Martin: the company's Squad Mission Support System (SMSS) is a mule-type ground robot that has been tested in real combat conditions. The system was selected in 2011 by the US Army for its workhorse trials, and four SMSS units were deployed to the military in 2012. They enjoyed great success with the military, who asked to be left in the area of hostilities. Their ability to carry almost 700 kg on their own when following the soldiers proved to be extremely useful and in at least one case the system was loaded with more than one ton of various stocks and at the same time it worked flawlessly.
Developed around 2005 and constantly being upgraded, the SMSS robot is based on the Land Tamer 6x6 XHD from PFM Manufacturing Inc, made of aluminum for marine vessels with an 80 hp turbodiesel engine. Some of the provided characteristics of the Block 1 option: total weight 1955 kg, payload 682 kg, the device can be transported inside CH-53 and CH-47 helicopters or on a UH-60 suspension. Lockheed Martin focused on adding autonomous capabilities, SMSS is capable of operating in various modes, such as manual control, remote control, voice commands, return to operator, movement to a location using selected coordinate points, return along a formed trajectory, navigation to GPS position points, follow following a person and following a vehicle.
While US Army personnel were eager to keep the SMSS apparatus in their theater of operations because of its practical value, the Army and Lockheed Martin developed other functional kits and tested them in the field. These include an advanced deployment reconnaissance system with a satellite communication channel and a route clearance system with a roller trawl. In both cases, a Lockheed Martin 9”Gyrocam optoelectronic station was installed on the mast to provide long-range reconnaissance or identify suspicious areas where bombs could be buried. The route clearance test was carried out with a roller trawl mounted on the SMSS. Also in the United States, tests were carried out to control the device using satellite communications, including command transmission ranges at a distance of over 300 km. In total, Lockheed Martin has produced eight SMSS, the last two being Block 2 standards, although no upgrade details were provided.
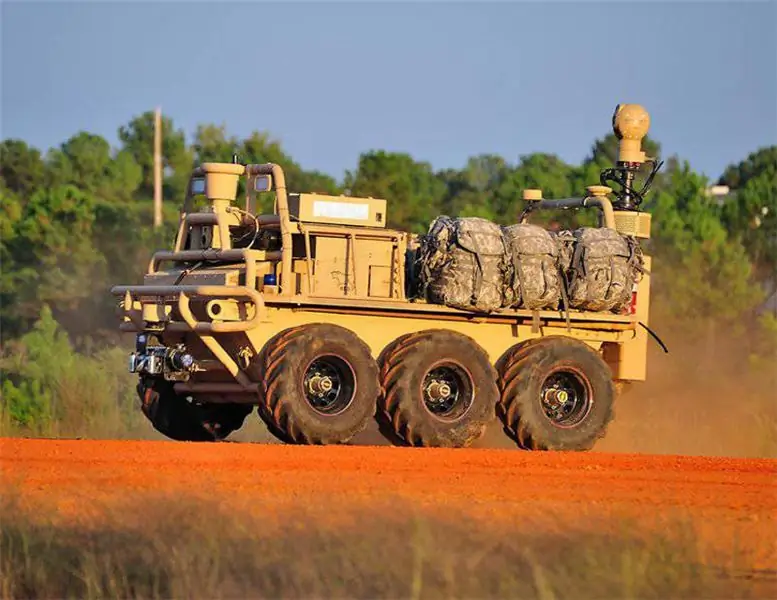
Lockheed Martin's Squad Mission Support System (SMSS) was used as a cargo platform in Afghanistan, but is currently being offered as a reconnaissance vehicle.
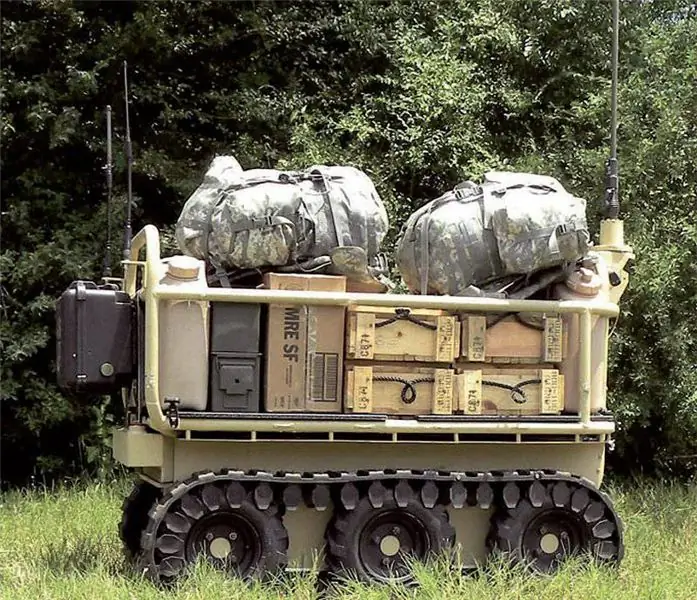
The Camel 6x6 from Northrop Grumman, which can carry over 350 kg of supplies, can be quickly fitted with rubber tracks
In August 2014, Lockheed Martin, in conjunction with the US Army Armored Research Center, held a demonstration involving two uninhabited helicopter systems: the K-MAX, developed by Kaman, and the SMSS ground robot with the Gyrocam optical unit installed. A combat mission was set - with the help of unmanned vehicles, to ensure the supply of a group of soldiers defending the village. K-MAX flew over the SMSS in the vicinity of the village, observing until the robotic system reached the soldiers, providing them with the required supplies. The semi-autonomous 8x8 vehicle then drove to the vantage point, where, using a 9”Gyrocam sensor kit on a telescopic mast, he scanned the entire area in search of enemy forces. Both SMSS and K-MAX unmanned aerial vehicles were equipped with mobile satellite communication systems, as well as local communication systems within the line of sight. As a result of further development, a new fully autonomous platform may appear, as well as non-lethal and / or lethal capabilities with a turret.
Northrop Grumman: This company developed the Camel (Carry-all Modular Equipment Landrover) robotic vehicle to provide logistical support for foot patrols. The system presents a failure on a 6x6 platform, on top of the wheels of which rubber tracks can be easily put on if necessary. Each wheel is powered by an electric motor powered by a diesel-electric generator. The engine runs on diesel fuel or JP8, and its 13 liter tank allows more than 20 hours of operation; such a solution, when approaching a potential danger, allows you to move in a silent mode. The maximum speed of the vehicle is eight km / h, it can overcome slopes of 40%, side slopes 20%, obstacles and ford 0.3 meters. Its load, stowed inside a tubular structure mounted on the chassis, can exceed 350 kg.
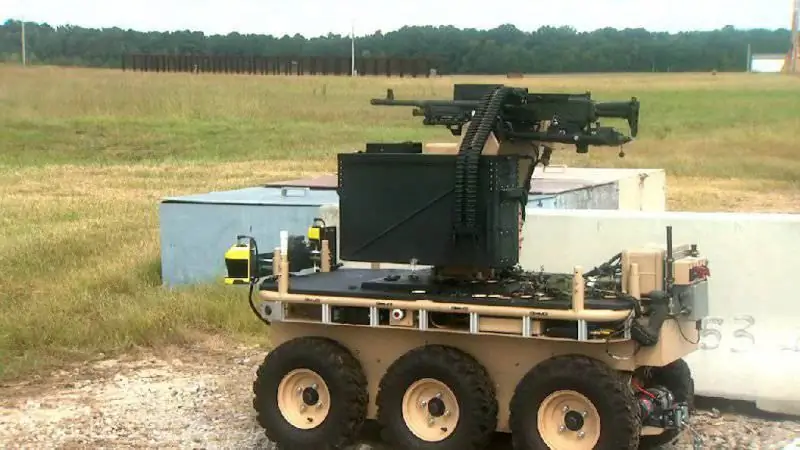
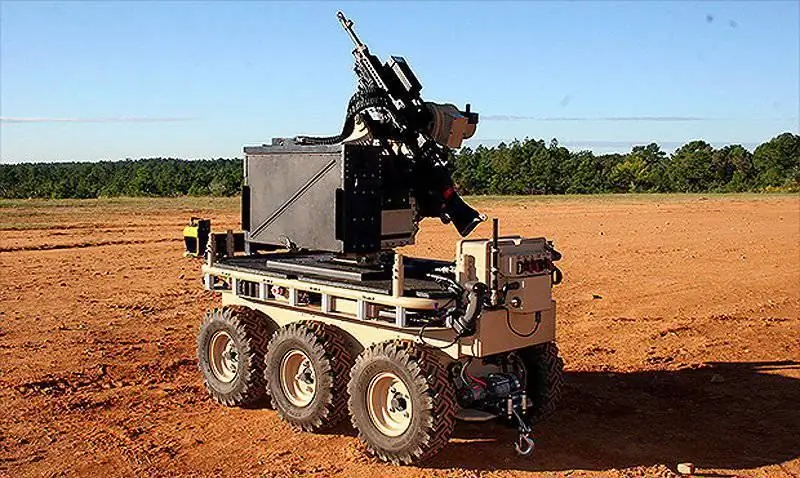
Armed variant Camel - Mobile Armed Dismount Support System during fire tests
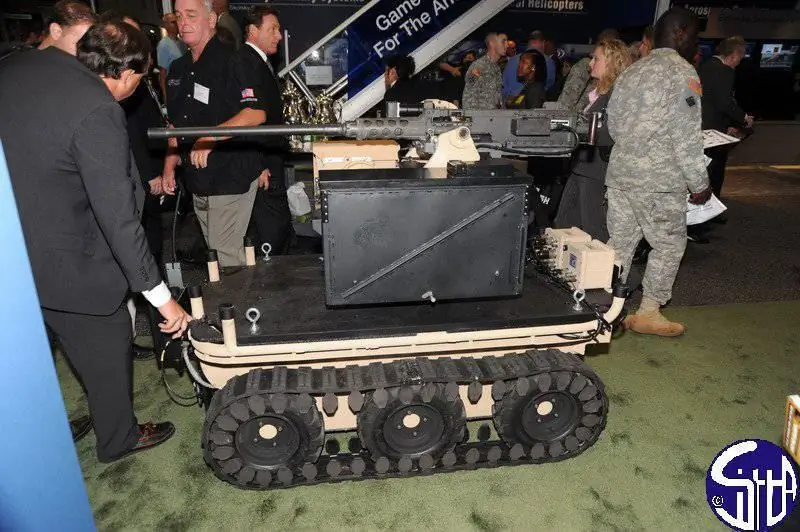
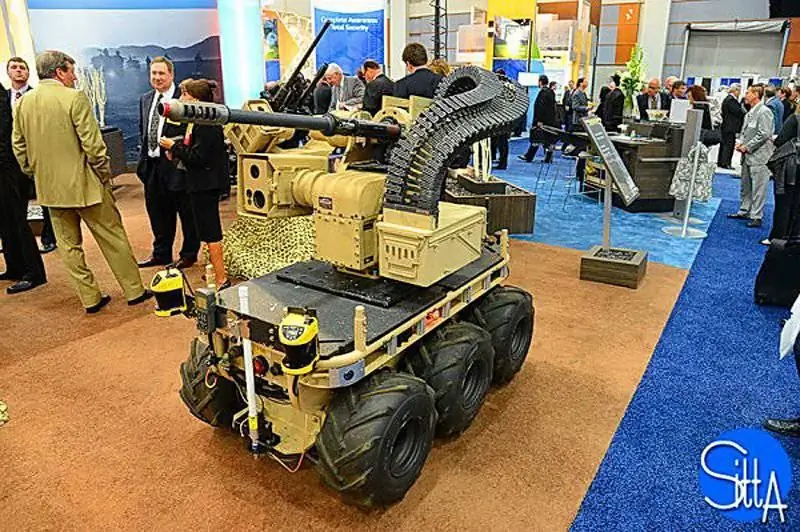
Armed version of the Camel with a remotely controlled weapon station
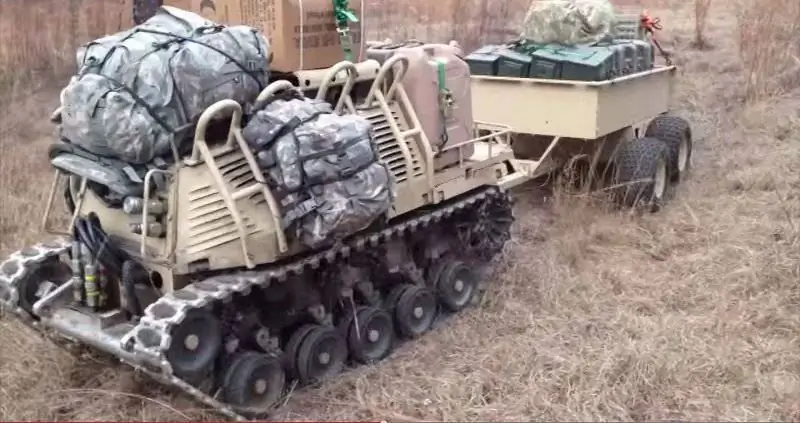
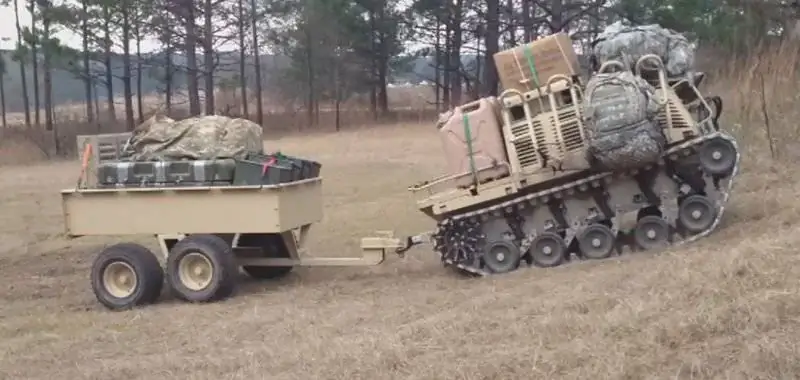
Multi-tasking robotic system Protector, developed by HDT Global; in the photo works as a cargo transporter
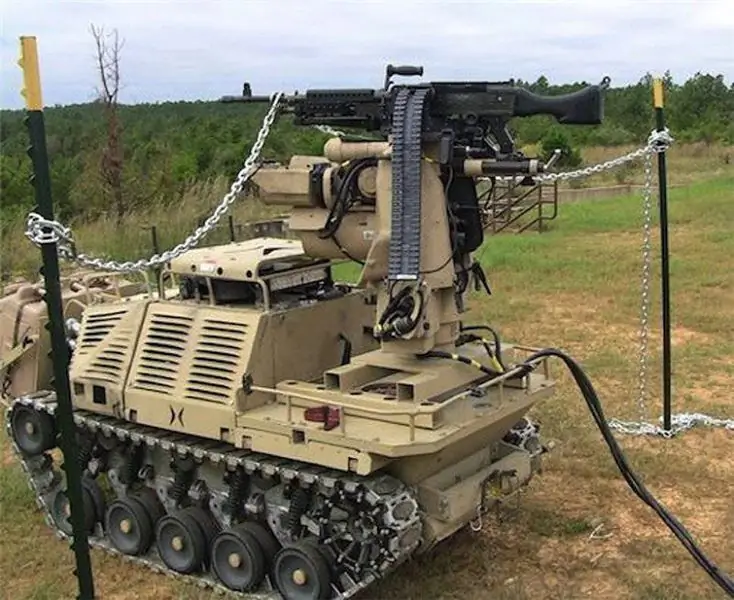
The mass and carrying capacity of the Protector allow it to be transformed into an armed platform, in the photo is a robot with an installed combat module Crows
Camel is equipped with an obstacle avoidance and detection sensor kit. It can be controlled in follow me mode or via cable. In the transport convoy, the vehicles can follow each other like the carriages of a train. Numerous optional kits are available with the already mentioned kit, such as an external battery pack for extended range, interchangeable communication channels, fiber optic, rigid cable or RF systems. According to the company, the US Army and Special Operations Command have shown great interest in the platform in the basic configuration, as well as in the armed configurations described later in this article.
HDT Global: The Protector tracked robot was developed by HDT Global as a multi-tasking system for supporting soldiers in the field. The device is equipped with a 32 hp diesel engine, it can carry a load weighing 340 kg plus pull another 225 kg on a trailer. The Protector can be quickly disassembled into portable modules so that unexpected obstacles can be overcome. The 57 liter fuel tank (diesel or JP8) allows a range of 100 km. The maximum speed of the robot is 8 km / h. The base unit is remotely controlled and the cruise control mode reduces the operator's workload.
HDT has also demonstrated that its robot can gain some level of autonomy with semi-autonomous navigation based on a variety of sensors, including optoelectronics, active RFID tags, lidar, differential GPS, heading system, and odometers on the sprocket of each track. To improve the safety of follow-me operation, at least two sensors must be matched on the leader's location before the Protector follows him. For auxiliary equipment, the system has a hydraulic output and a socket with an electrical output of 2 kW. In addition to performing practical tasks for clearing routes and neutralizing explosive objects (which is not the purpose of this article), the Protector ground robot can also be equipped with an excavator bucket and a frontal shovel in order to assist in the construction of protective structures for posts and bases (filling gabions with earth, etc..). After these works, the device can be quickly returned to the performance of patrol duties. A version with two stretchers for evacuating the wounded, a version with a tethered UAV for surveillance and an armed version with a remotely controlled combat module M-153 Crows were also demonstrated. Wireless control is carried out using a joystick for the thumb and two buttons.
In Israel, two companies Israel Aerospace Industries and Robo-team have developed a wheeled cargo platform.
IAI: The Lahav Division of Israel Aerospace Industries has developed a diesel powered 4x4 robotic wheeled platform and has given it the Rex designation. The maximum speed of the robot is 12 km / h, the carrying capacity is up to 250 kg, the unladen weight is from 160 to 200 kg. Its first task is to support foot patrols by transporting some of the soldiers' equipment. The robot can operate in three different modes. The simplest is the remote control. The second uses a mechanical "leash" that is held by the operator, and the Rex robot follows it along its path like a dog. The most intelligent is the "follow me" mode. The operator's coordinates are transmitted via a radio station to the on-board GPS system, which generates intermediate points of the route of the Rex apparatus. In this mode, multiple Rex robots can be used to transport more gear. Although this was not implemented on the prototype, the Rex device can record the route traveled in order to return to the starting point, the mode can be useful for the next resupply along the routes already traveled and, perhaps more importantly, for the return of the victims.
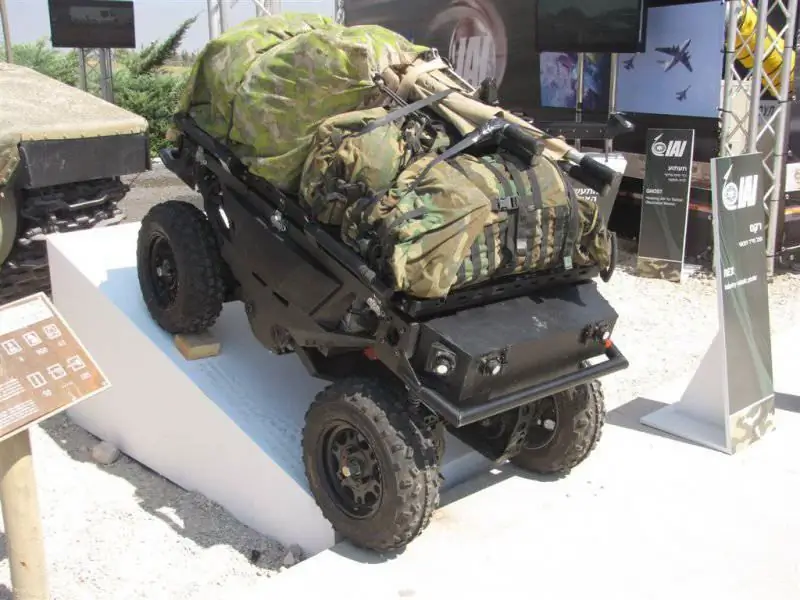
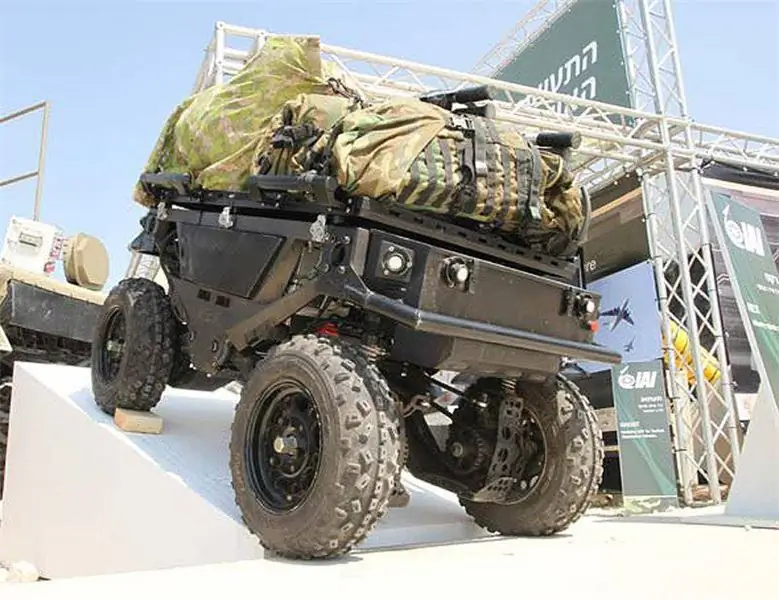
IAI Lahav Division has developed the Rex 4x4 platform capable of carrying up to 250 kg. The new version will increase the carrying capacity to at least 300 kg
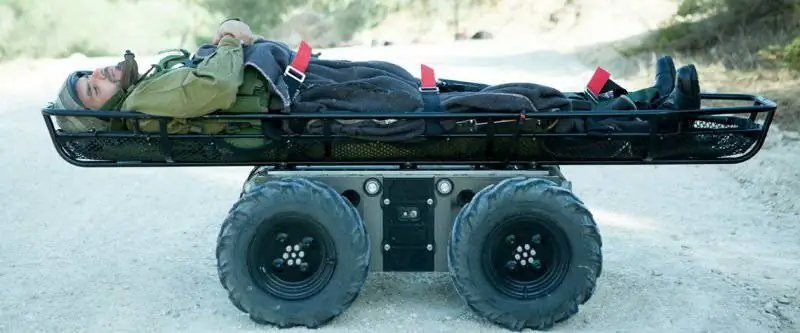
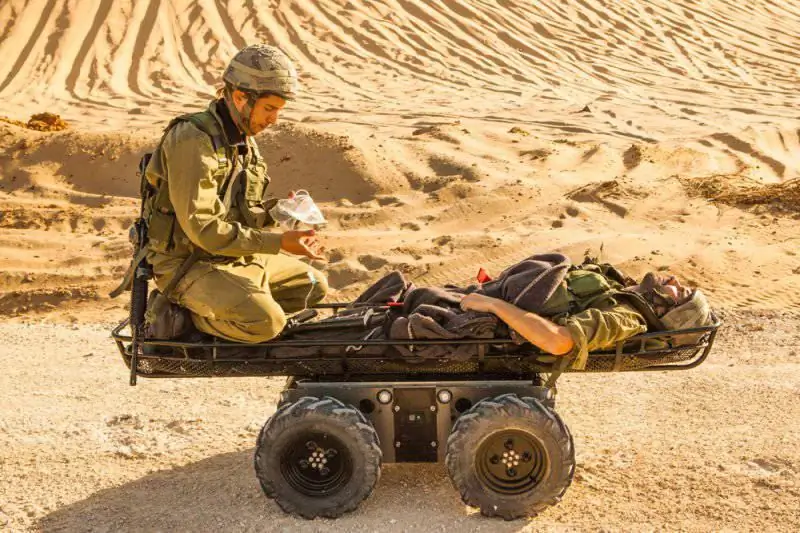
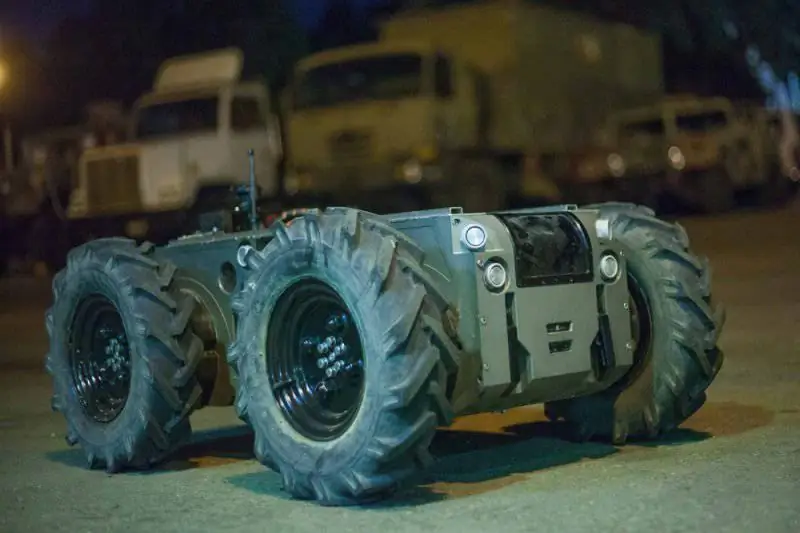
Built by Robo-team, the Probot, with a payload of almost 250 kg, can be used to resupply or evacuate the wounded. Sensor kits and explosive ordnance disposal kits are also available
Rex is offered not only for logistics tasks, but also for other tasks, such as reconnaissance with a kit that includes an optoelectronic survey station. The Rex prototype was evaluated by the Israeli and other armies, whose comments and feedback led to the creation of the second generation Rex. The main changes concerned dimensions and weight: the new robot will have a carrying capacity of at least 300 kg with an increase in its own weight to 230 or 250 kg. The operating modes will be the same as in the previous version; IAI believes that increasing the level of autonomy will significantly increase the cost, which is at odds with the company's marketing strategy. What has really changed a lot is the mover; the second generation Rex is equipped with a diesel-electric power unit, which allows silent crawling in low-visibility mode. According to IAI, a prototype of the new Rex variant will be ready for testing at the end of 2014.
Robo-Team: In the first part of this long article, we already got acquainted with the Robo-Team company. In the same category, she offers a system under the designation Probot (Professional Robot). It is an electrically powered 4x4 chassis with a payload of more than double its own weight of 120 kg. The electric propulsion system was chosen to provide maximum sonic stealth when compared to the much noisier robots in this category, powered by gasoline and diesel engines. Its top speed of 7.5 km / h makes it easy to follow the soldiers, while its ability to negotiate obstacles and 23 cm high ledges ensures ample cross-country ability. The Probot has a 360 ° view, which is provided by four day / night cameras (one per side) and a circular illumination module in the near infrared region of the spectrum. The front camera can be tilted 45 ° / + 90 ° and has a magnification of x10, and the illumination is provided by a LED white light. Available voltage 12 volts or 28 volts, there are Ethernet ports RJ45 and RS232 for matching the installed equipment with the on-board computer.
Robo-team offers kits such as, for example, a bomb disposal kit, which includes a heavy-duty manipulator arm, a reconnaissance kit, WMD and hazardous substances detection kits, etc. The Probot is equipped with a communication channel with a line-of-sight range of 1000 meters. In addition, the platform is equipped with tracking and thermal imaging sensors for automatic navigation in the city, indoors and outdoors, and the follow me system allows the Probot to automatically follow the infantry squad to which it is attached. Robo-team is not very verbose when it comes to its Probot device. Its development is still ongoing, several prototypes are with potential customers in order to receive comments from them before starting production. The company is, of course, working on autonomy kits that could easily find their place in the Probot due to its size and autonomy.
Quinetiq: In recent years, Qinetiq North America has developed many robotic systems in the heavy category for various purposes: route clearance, reconnaissance, combat, etc.
For support tasks, the company has developed solutions aimed at robotizing existing machines. Its optional Robotic Applique Kit (RAK) can be installed in about 15 minutes on 17 different Selectable Joystick Controlled (SJC) Bobcat loaders used for different types of tasks, mainly related to route clearance, such as the Minotaur and Raider I or the unmanned engineering Spartacus. For the logistics of the infantry, QinetiQ North America teamed up with Polaris Defense to develop the Raider II, as this vehicle is based on the previous Military Diesel Crew Long Box. The possibility of driving by the driver is left and in this case the maximum speed reaches 55 km / h. Without a driver, Raider II can operate in remote or autonomous modes. In the first case, it is controlled through a tactical controller Tactical Robotic Controller with a range of one kilometer; in the second mode, the device can detect obstacles, avoid obstacles, follow the operator, move along the waypoints and return home. A day and thermal imaging camera with a 640x480 sensor with pan / tilt zoom is mounted on the roll cage, while the other four cameras provide 360 ° all-round coverage. Soldiers can hang up to 10 bags on board; two stretchers can also be attached to the cargo area for evacuating the wounded.
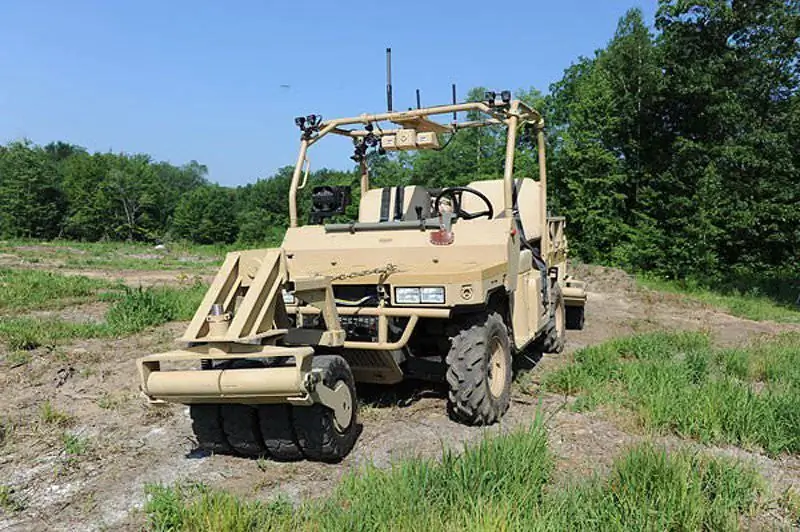
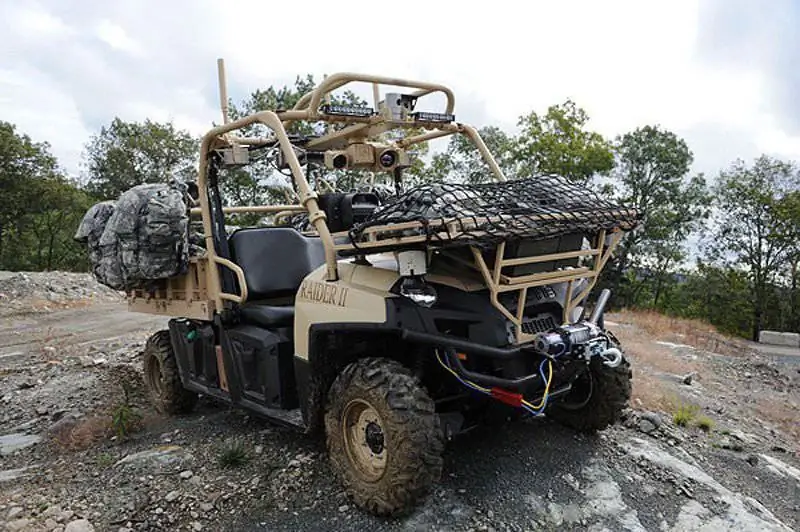
Raider I above, Raider II below
The transformation of buggy cars into self-driving systems is not new: Boeing UK and John Deere developed a similar system a few years ago, calling it the R-Gator A3 with a 635kg payload.
Sterela: Given the task of developing the landing gear for Air Cobot airports (Cobot, the florid acronym Aircraft enhanced Inspection by SmaRt & Collaborative robot), the French company Sterela unveiled the new platform at Eurosatory 2014 in the role of a mule. The 4-wheel drive chassis is equipped with integral and remote emergency shutdown systems required in an industrial environment, including obstacle detection bumpers. The carrying capacity is 100 kg, the communication channel has a range of 200 meters, the device is powered by electric motors, 48-volt lithium-ion batteries allow the device to work up to 8 hours.
The Sterela platform has separate wheel steering, it can operate in “follow me” mode or follow a preprogrammed route, the latter is offered as an option. The standard speed is 7 km / h; however, an optional engine can boost it to 18 km / h.
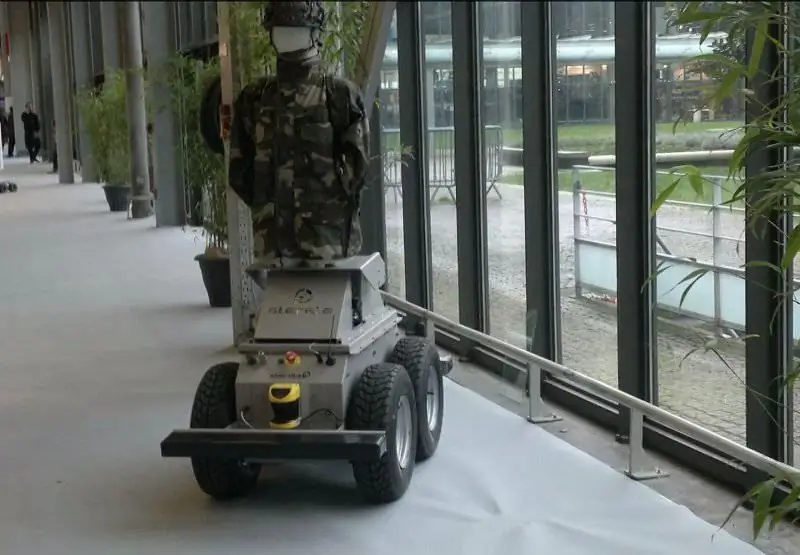
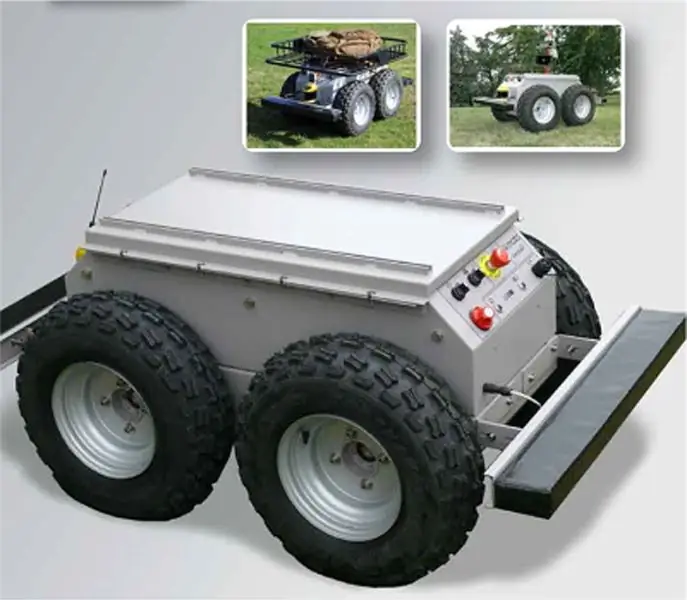
The French company Sterela has developed a 4x4 robotic platform for use in airports, but is currently offering it as a logistics tool for military missions.
Sera Ingenierie: The French company Sera Ingenierie, part of the Sogeclaire Group, has received a contract from the Defense Procurement Office to develop a robotic vehicle under the Rapid program (Regime d'Appui Pour l'Innovation Duale - provision for double innovation). The architecture is driven by transportation requirements, the resulting robot named Robbox consists of an upper beam that connects two self-propelled modules, each with either a diesel or an electric motor. The diesel module is equipped with a 16.75 hp engine. and the electric module contains a 15 kW electric motor and a 6 kWh lithium-ion battery. Depending on the choice of the layout, the steering has one or two axles. In the second case, the turning radius decreases from 5.4 to 3.4 meters, which is equal to a turn around its axis, since this is the length of the Robbox machine. The maximum onboard power is 2 kW, the maximum weight is 500 kg. It is divided into two modules, the first with the maximum dimensions of 2400x1200x400 mm, and the smaller second with the dimensions 1200x1500x550 mm. The ground clearance of 250 mm allows you to have good passability through obstacles.

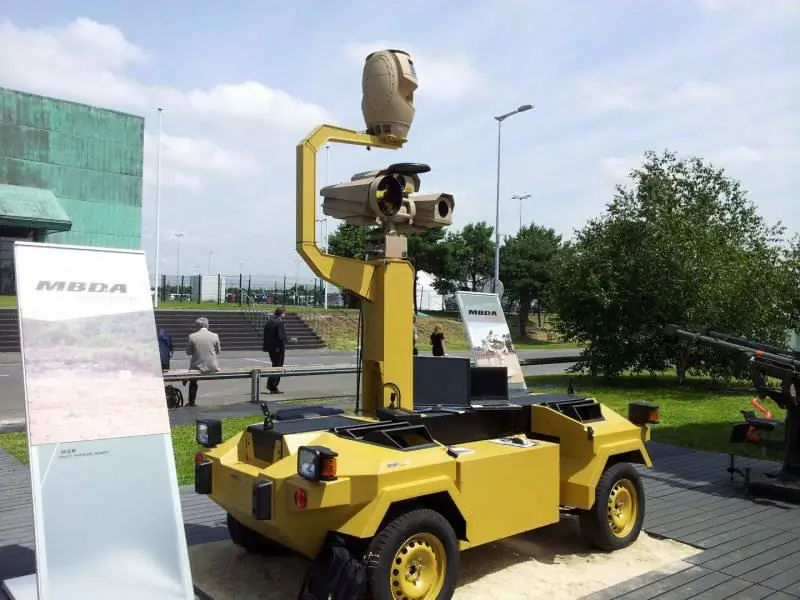
The French company Sera has developed a wheeled robotic platform called Robbox, consisting of two self-propelled modules and a central beam; in the photo there is a variant with installed sensors from MBDA
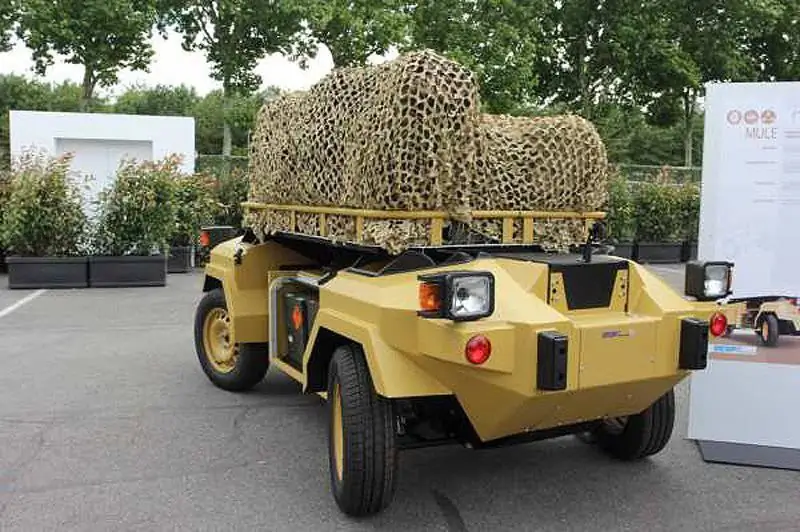
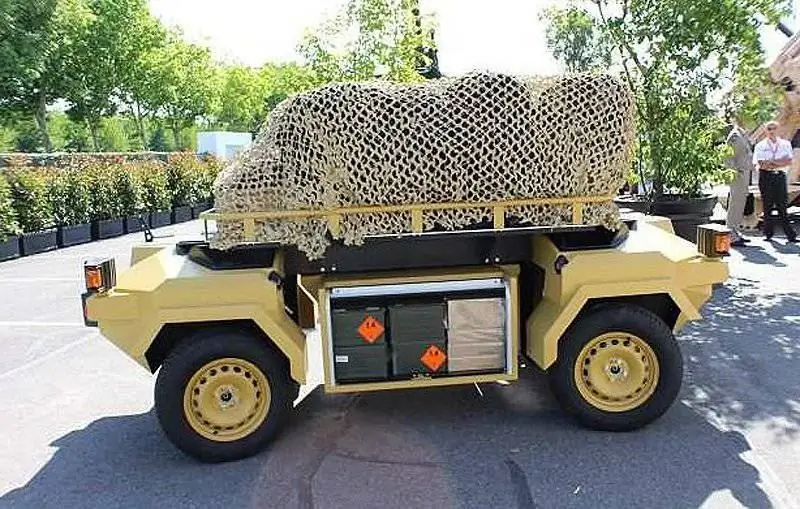
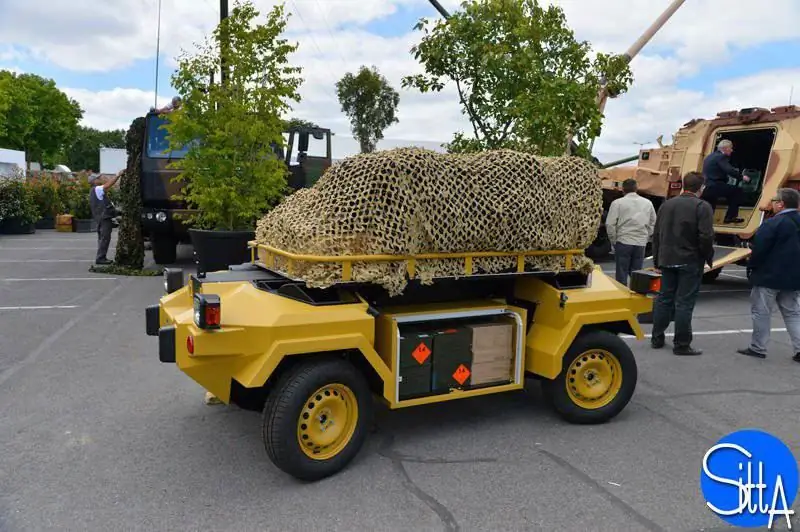
Nexter adopted Seras' Robbox as the basis for their Mule concept; apparently also considering the creation of an armed version
The Robbox can overcome slopes of 40% and vertical obstacles with a height of 250 mm. Its maximum speed in remote control mode is 40 km / h, dropping to 8 km / h in electric mode. In operation on a diesel engine, its power reserve reaches 300 km. Sera Ingnerie supplies the Robbox with three different levels of command and control, ranging from the most basic version with only actuators, the middle version with a communication link, six cameras and a remote control, to special configurations developed by third parties. Two of them, Nexter and MBDA, presented the Robbox in two different configurations at Eurosatory.
The Nexter model is named Mule and features an upper cargo area and a lower cargo area. It is capable of carrying 300 kg, but the total maximum carrying capacity is limited to 400 kg, since with all the structural elements and systems installed, the empty mass of the robot increases to 800 kg, which worsens some of its characteristics. A key system that Nexter has added is an optional control kit that includes differential GPS, odometer, magnetic compass, gyrometers, accelerometer, laser sensors for navigation and a scanning laser for obstacle detection. The developed software allows, in addition to the standard remote mode, to use also automatic modes, for example, following intermediate points, recording a path and repeating, follow me, etc. The robotic apparatus presented at the Eurosatory exhibition has not yet been sufficiently tested and in this regard, the Robbox sea trials began in September 2014. Nexter plans to begin evaluative operational trials in early 2015 with the primary goal of testing various autonomous modes, such as follow me, as the French Defense Procurement Authority intends to use Mule to develop the operational doctrine of robotic units. In this regard, advanced modes are being studied, which will allow the soldier to "ask" the robot to stop, wait, join the infantry team, etc. in order to provide real effective support for battle groups of 10 people. Nexter aims to develop a multi-purpose ground robot, which suggests that, apparently, an armed system based on this platform is already in the plans.
For its part, MBDA offered Robbox in the M2R configuration, a multi-sensor air defense platform. In this configuration, the Robbox turns into an air defense system that can be deployed in commanding positions without risking the lives of soldiers. The M2R is equipped with a Spynel-X infrared search and tracking sensor developed by the French company HGH Infrared Systems, which is capable of capturing panoramic images with a resolution of 120 megapixels with a detection range of 16 km. Once a threat is detected and tracked by the Spynel-X sensor, the electro-optical system, consisting of a day camera and a high magnification thermal imager, provides positive target identification. In Paris, the robot was presented with a Ranger MS mast sensor from Flir Systems. These sensors can be deployed for ground surveillance as well.