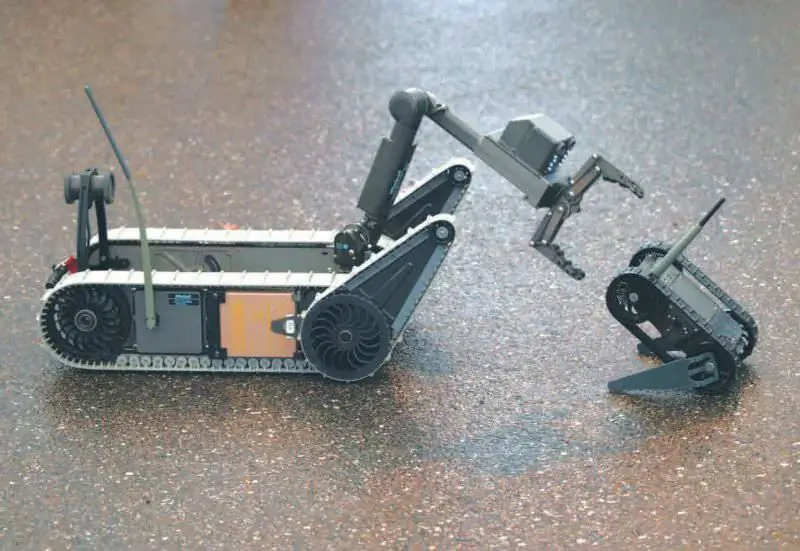
The interaction of medium and light robots (in the photo is an example of such interaction from iRobot) can manifest itself in the appearance of small consumable systems deployed by larger systems
Among the three elements represented by sea, sky and land, land is of course the most difficult for an unmanned vehicle. While unmanned aerial vehicles (UAVs) and surface or underwater uninhabited systems for the most part operate in a homogeneous space, ground robots must overcome all types of obstacles of which there are a myriad of. They not only complicate the movement of robots, but also limit the range of their communication channels
In the realm of UAVs, the rule is that the smaller the UAV, the greater the effect of wind gusts on it. Ground robots suffer from a similar size syndrome, where physical size affects mobility, at least when it comes to the most classic solutions, namely wheels and tracks, since walking and crawling mechanisms are still far from practical implementation.
Ground minibots suffer the most. Their limited mass also affects the range of communication channels and the duration of their operation, since they usually operate on batteries.
It is always difficult to categorize systems. However, the first category can be safely attributed to systems weighing up to five kilograms, the so-called ground mini-robots (let's put aside the micro category for the future, if it ever appears). The first category has subcategories, namely throwable robots up to three kilograms, since heavier robots are throwable rather than throwable devices.
The next range is the middle category, a really different world where payloads are measured in kilograms rather than grams, and where much more flexibility is provided. Here the robots themselves weigh from 5 to 30 kg.
In this article, for practical reasons, only robots that can be used by soldiers on the battlefield from a tactical point of view are considered. For example, explosive ordnance disposal robots are considered specialized systems designed to perform a specific range of tasks. The purpose of the article is to analyze what is available to the ordinary soldier to improve his safety and combat qualities of flexibility in a real situation.
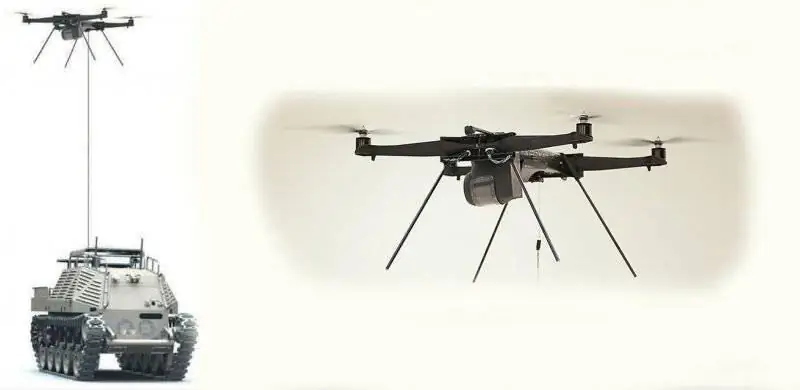
Another form of "cooperation" between ground robots and UAVs is presented here by the HDT Global Protector tracked vehicle, which deploys a tethered UAV to provide early warning of convoys.
Obviously, many multitasking ground robots can be equipped with a robotic arm, grapples, water cannon, etc., which effectively turns them into mobile bombs, although this will be just one of their many roles.
Heavy robots weighing more than 100 kg can be useful on the battlefield in tasks such as reconnaissance, resupply, evacuating casualties, etc. For example, one of the many possible uses is the Supacat, which is used by the British Army to transport ammunition to the front line. The drivers of these cars are at very high risk, so they can reasonably be replaced by robotic systems.
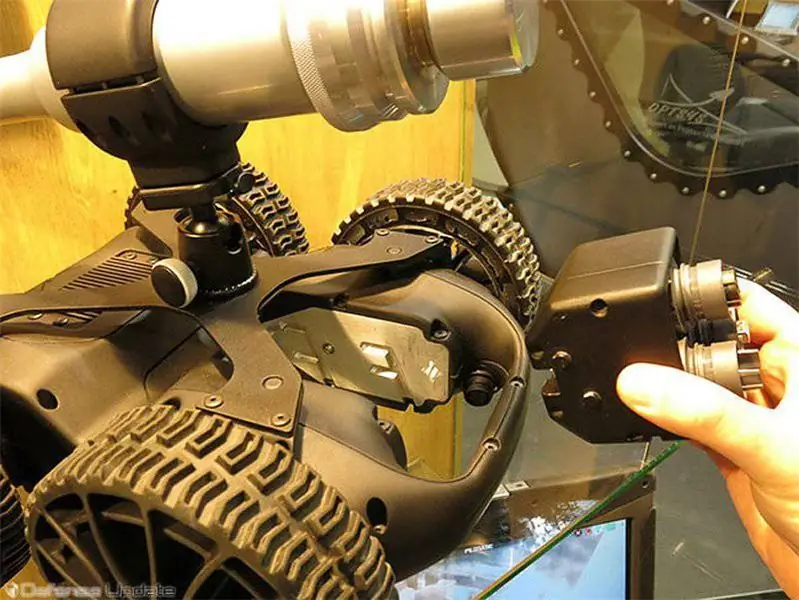
Demonstration of the modular design of Nexter Nerva robots that can accept chemical sensors, infrared cameras, tear gas grenades, an audio system, an explosive ordnance device, and a module for installing other devices
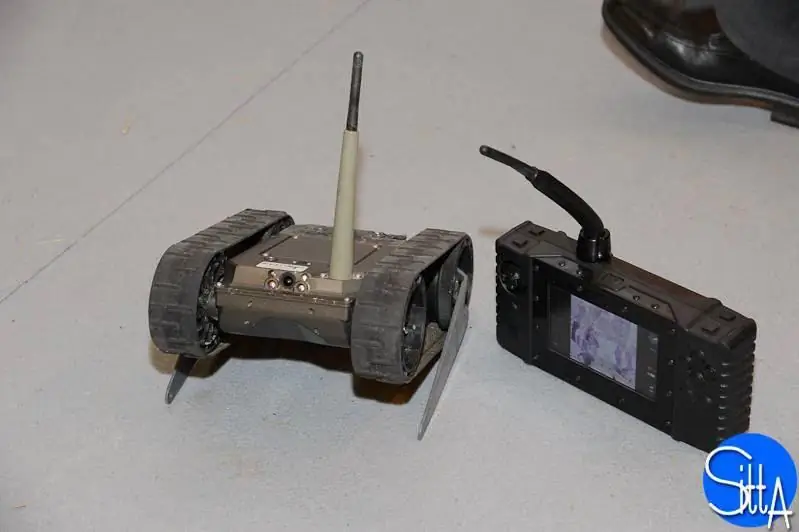
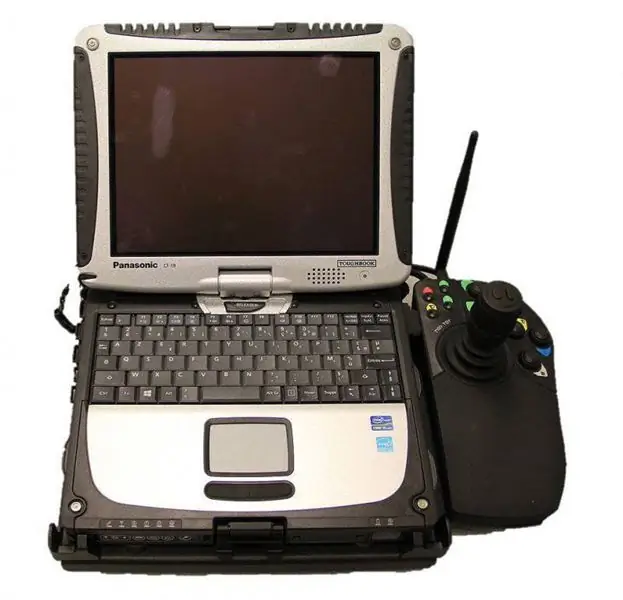
Ground-based mini-robots such as the iRobot FirstLook (above) will mostly remain remotely controlled, as increasing their autonomy may be too expensive, at least at this stage. One of the areas, however, could be improving the human-machine interface, which will allow operators to maintain their tactical position when controlling ground robots, as can be clearly seen in the example of the Nexter Nerva robot controller (below)
Fatigue and loss of concentration have been identified by the US Army as the main causes of supply convoy accidents, plus directional landmines contribute to this sad statistic. As a result, a number of companies in the US and Europe are developing systems that transform a traditional vehicle into an unmanned vehicle. A similar approach can also be applied to the equipment of engineers, that is, the scraper, for example, can be turned into a robotic demining device.
The huge advantage of these systems is that they can be purchased in relatively small quantities and installed on standard trucks or vehicles on site and then transferred to other machines, either for other tasks or in the event of a malfunction of the machine in which they were installed. …
Compared to UAVs, ground-based robots are, of course, less technologically mature. Few of them integrate an advanced form of autonomy, which could significantly reduce the workload on operators and at the same time increase the advantage of their use and make them a real factor in increasing combat readiness. Many arguments are given against their weapons (this also applies to UAVs), since their reliability is considered insufficient (how reliable a person can also be questioned, especially in light of incidents between their own forces in some areas of hostilities). Legal advisers will pay good dividends on the rapid deployment of such armed ground robots. However, it is clear that the era of ground robots has begun and they will play an increasingly important role in future battlefields.
But at present, however, another factor is having a disastrous effect on the development of ground robots - the financial crisis. In many countries, led by America, many programs have been cut, affecting the design and procurement of some of the systems mentioned in this article. This, along with other events, gave rise to negative processes in the community of ground robots. Several well-known companies are currently struggling with financial problems due to canceled orders.
Today, three programs appear to be alive in the United States: the Advanced Explosive Ordnance Disposal Robotic System, the squad-level Common Light Autonomous Robotic Kit serving as a means of transporting reconnaissance sensors, and the engineering department robot. Engineer Squad Robot. Another Squad Multi-Purpose Equipment Transport program is likely to survive the cuts and sequestration of the defense budget.
All robotic systems (air, sea and land), if they want to attract any attention of the US Department of Defense, must comply with the common architecture for unmanned systems Joint Architecture for Unmanned Systems (JAUS) and the Interoperability Profile (IOP). Head-to-head control systems, reduced workload, semi-autonomous control, the ability to operate multiple devices at the same time, most likely, are the main development trends in the field of robotic systems.
What does the future look like for ground robots? How many of them will appear on the battlefield in 2020? Hard to say. It is only obvious that this technological development, combined with the absolute need to reduce losses in the contingents of Western countries deployed in hot spots, will inevitably necessitate the advancement of deserted systems in all branches of the military operating on land. Very few at the beginning of the century were convinced of the usefulness of UAVs, and now they appear in the news every day, and many are now being promoted for commercial use. Will this also happen with ground robots? The answer is probably yes, given that according to the Office for the Development of Robotic Systems, ground robots have saved the lives of more than 800 soldiers while performing combat missions in Iraq and Afghanistan.
French army looks at ground robots
The French Minister of Defense confirmed Phase 1 of the Scorpion program in June 2014 and the French army now intends to begin Phase 2, for which robotic systems are an integral part. Robots in the operational-tactical forces will have to be used in hurried combat, and ground-based micro-robots (and their flying counterparts) will be the advanced eyes of the soldier. Other robots of this size could do their part by providing not only forceful effects on enemy ground forces, but also improving the quality of communications for task forces, for example, through the deployment of radio relay systems.
More advanced microrobots could carry out reconnaissance missions for the higher echelons, taking part in the battles of mechanized forces. Tactical versatile robots could conduct contact reconnaissance, resupply and serve as actuators, while heavier robots could be mainly used for mine clearance and engineering tasks. The use of systems that can transform standard vehicles into robots cannot be discounted.
Mini Category: New Tools for Infantry Squads
In anticipation of the appearance of ground-based nanorobots, reconnaissance, observation and information gathering tasks at close range are mainly performed by light ground robots capable of moving in restricted areas and having limited-range data transmission channels. Many of them fall into a category that we can call the category of "throwable robots", since they can be thrown by the operator at a certain distance and height, for example, inside a building, which eliminates the need to move there on their own.
Often considered disposable (consumable), they can fit in a pocket or bag and have small and lightweight controls, and some are now even controlled by smartphones. Along with the light throwable robots, there are slightly heavier robots that are easily dropped from the vehicle (when not equipped with additional sensors), but they can hardly be launched through the first floor window. They remain the systems of choice for major infantry units as they do not add much to the soldier's burden and compensate for this by providing new, easy-to-use capabilities.
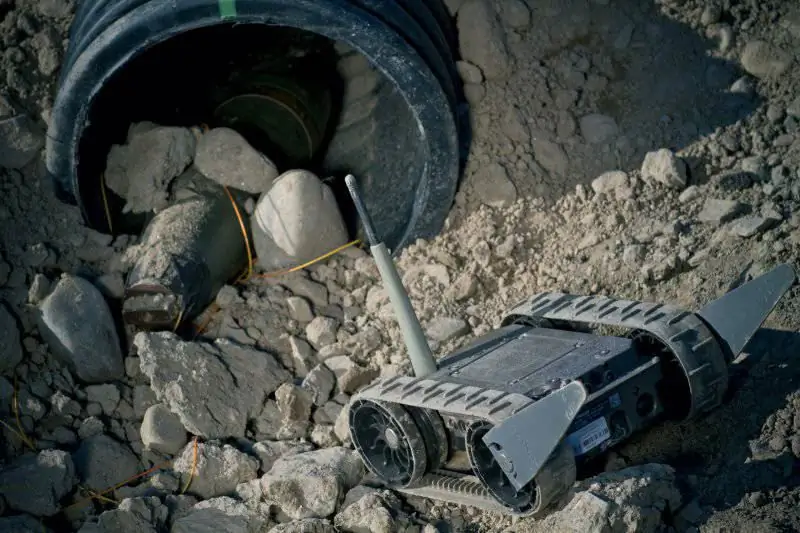
The younger member of the iRobot family in front of an improvised explosive device. The two trapezoidal levers on the sides in the foreground are called flippers.
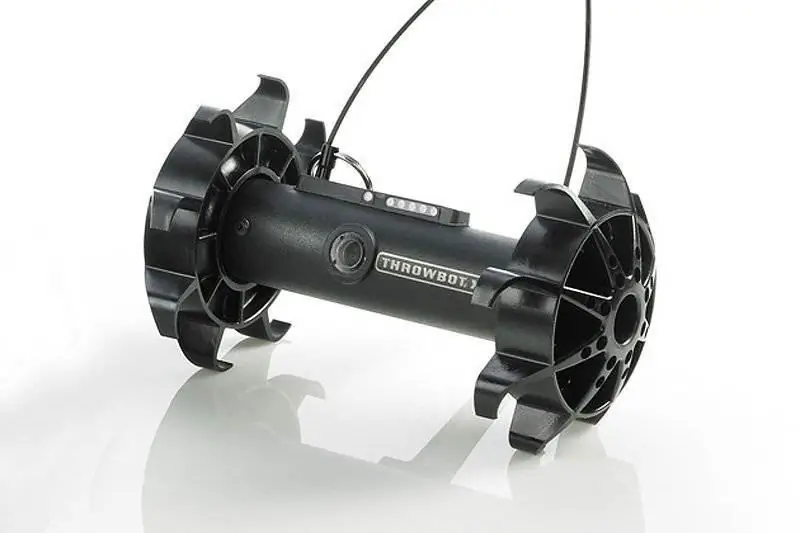
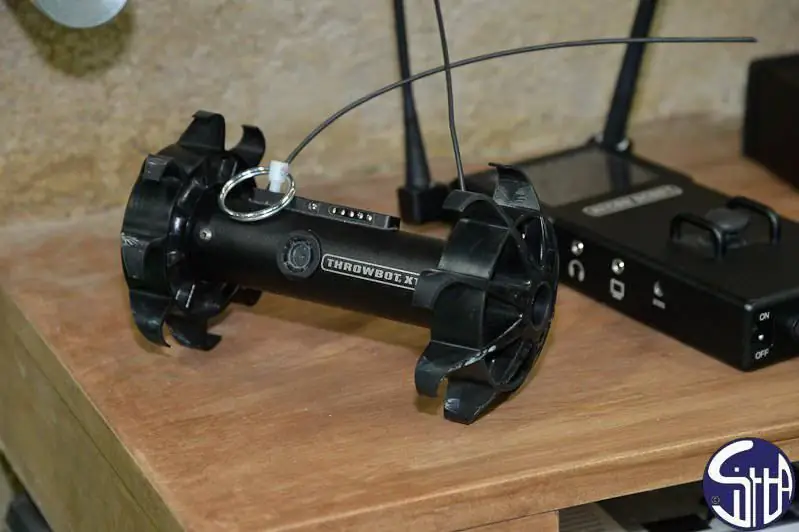
Throwbot XT is one of two best-selling ReconRobotics products; second and larger model - Reconscout XL
Abandoned
ReconRobotics: ReconRobotics, based in Minnesota, was founded in 2006 and is one of the fastest growing ground robotic systems companies. There are 4,000 production systems of this company in the world, equally divided between the military and law enforcement spheres. US defense budget cuts hit the company hard in 2014 after the US military decided not to buy more than 1,000 robots in 2013. This led to a production halt in early 2014, although the company recently said a strong international and law enforcement market would help offset lost orders from the US military. Currently, 90% of the company's sales are based on two models: Throwbot XT and Reconscout XL.
The lighter Throwbot XT system from the ReconRobotics family of robots weighs just 540 grams (the average hand grenade weighs between 400 and 500 grams) and began production in mid-2012. The comparison with a grenade is further enhanced, since in order to activate and turn on the robot, the operator must remove the pin from it. The lightweight, tubular design allows you to comfortably grab it with your hand and throw it at a range, as the company says, up to 36 meters. Good shockproof characteristics of the robot allow you to throw it from a height of 9 meters without any consequences. Inside the tube are two brushless motors that rotate the wheels at the ends of the tube, while the rear tail section provides balance and orientation. Each 114mm OD wheel has eight curved blades to maximize obstacle clearance. In addition to the sensors, the tubular housing also houses a battery that provides an operating time of one hour on a flat surface.
The main sensor is a black and white low-light camera with optics providing a 60 ° field of view and a frame rate of 30 frames per minute; When the illumination falls below a certain level, the infrared light source is automatically activated, guaranteeing visibility over 7.5 meters. The highly sensitive omnidirectional microphone allows the operator to hear noises or conversations. The acoustic signature of the Throwbot XT robot is very low, with ReconRobotics claiming a noise of 22 dB at a distance of six meters, which corresponds to a person breathing at a distance of 20 centimeters. For silent deployment of the robot, there is a small hook at the bottom of the tail to secure the cord, while ReconRobotics has developed the SearchStick to deliver it to the height. This is a telescopic aluminum rod with a length of 1.83 meters with an activated latch button (in the folded position, the length of the rod is only 0.52 meters); it also serves to return the robot at the end of a job or to use it as a camera extension. The Throwbot XT's data link can be tuned to three different frequencies, so one operator can control three robots. The speed of the device is limited to 1.6 km / h, which is quite enough for a system designed mainly for work in buildings or in urban areas. In urban conditions, the range is 30 meters, which triples in open areas.
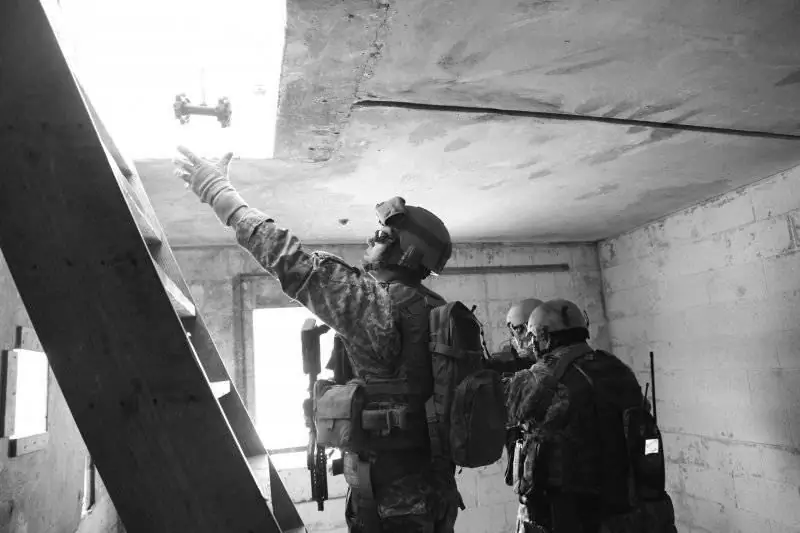
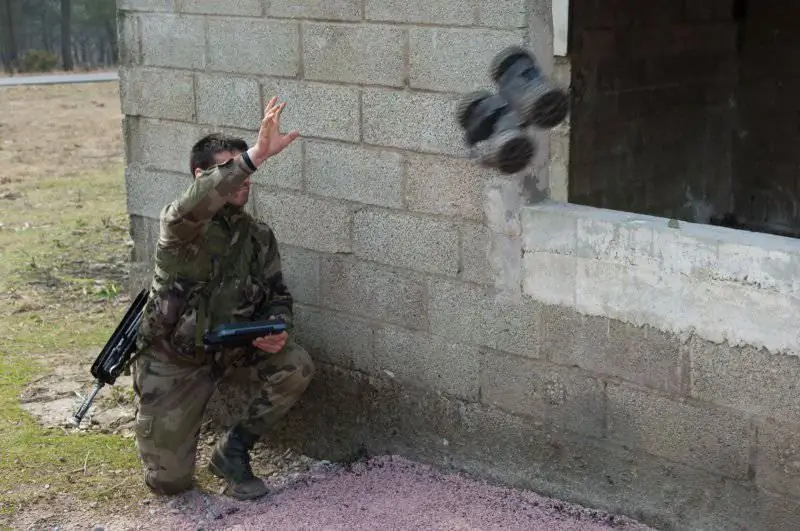
A vivid example of what a thrown robot can be used for: throw into an adjacent room and see what happens there
ReconScout IR is a direct development of the previous robot. It is equipped with a black and white infrared CCD camera with a 60 ° field of view and infrared illumination, effective at a distance of more than seven meters.
The ReconScout XL has a speed of 2.16 km / h, which is higher than that of the Throwbot, but its impact strength is lower, since it can withstand a drop from a height of only 4.6 meters and a throw of 9.1 meters. Its wheels with a diameter of 140 mm have six studs; this robot is somewhat noisier than the previous one, generating 32 dB of noise during operation at a distance of six meters. The sensors and the communication channel are the same.
ReconRobotic systems are controlled by the Operator Control Unit II (OCUII), which allows you to see images captured by the robot's camera on a 3.5-inch display, while all ambient sounds are fed into the headphones. The OCU II weighs 730 grams and features a thumb joystick for easy control of the robot's movement. The two antennas must be extended before the OCU II can operate, six frequencies are available, the height of the unit with extended antennas is 510 mm.
Historically, the main market for ReconRobotics has been the United States with thousands of systems sold, although its robots have also been sold to several other countries. In Europe, its cast systems operate in Denmark, France, Italy, Norway, Switzerland and the United Kingdom, in addition, the company's robots are used in Australia, as well as in Egypt and Jordan. In 2013, ReconRobotics were accepted by the PEO Soldier into the Soldier Enhancement Program as squad-level sensor kits by the PEO Soldier. The assessment process should be completed by 2015. ReconRobotics is currently working on the technical development of a digital version of the Throwbot XT; this will add the ability to reconfigure the radio channel, which is becoming a sine qua non on the international market.
Nexter: In 2012, the French company Nexter revealed its interest in ground minibots by releasing a prototype of the Nerva 4x4 castable robot weighing 4 kg. After further development and a manufacturing process, the original Nerva robot was designated Nerva LG, the first of a family of lightweight robots to be developed by the newly formed Nexter Robotics division. If the equipment is not installed on top of the robot, then the Nerva LG is completely reversible, in other words, it is ready to work immediately after the throw. Rear-mounted handle makes it easy to carry and cast. It can be dropped from a height of three meters and thrown to the side for seven meters. Nerva LG has two speed ranges: from zero to 4 km / h and the second from 0 to 15 km / h. The first mode is standard, allows precise control and orientation, and when high speed is required, the operator presses the button on the end of the joystick, switching the device to the high-speed mode. The standard wheels are 150 mm in diameter, although special sand wheels with wider treads and lateral grips can be fitted, a set of tracks is also available in difficult times. For special forces there is a swimming kit with floats elements and paddle wheels.
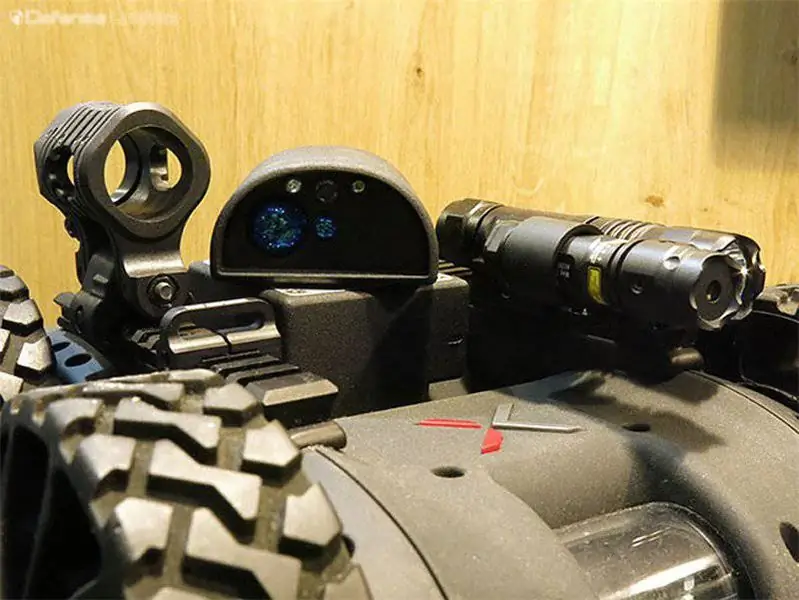
For its Nerva robots, Nexter has created quick-change modules that allow you to put a new task before the system without delay.
The fully modular robot is based on a one-click concept that allows for quick wheel and battery replacement. Nerva LG is equipped with standard sensors, which, due to four cameras, provide an all-round view (the front high-resolution camera has a backlight system), the operator hears all sounds thanks to an omnidirectional microphone. Picatinny rails or configurable strips provide a mechanical interface to the devices. The battery in the system supplies 24 volts at 1 ampere; data is sent over Ethernet.
However, Nexter developed the Nerva interface with the aim of extending the one-click concept to avionics. Thus, reconnaissance kits are available for this robot, such as thermal imaging cameras or directional microphones, as well as chemical detectors or mechanical devices for pushing or towing suspicious objects (an explosive ordnance disposal tool is being developed). The communication channel with a frequency of 2.4 GHz guarantees a range of one kilometer in open areas and 300 meters in urban areas. The duration of the Nerva LG is two hours, the robot can be controlled from different systems, from rugged computers to tablets and smartphones, in the latter case, the standard channel changes to a 100 mW wi-fi channel with a much shorter range. Typically used as a remotely controlled system, the LG Nerva robot, however, can also have semi-autonomous capabilities such as GPS positioning, automatic return home, or follow me. A large number of customers have ordered multiple systems each for field testing. Nexter expects larger orders after meeting the new avionics requirements voiced by current customers.
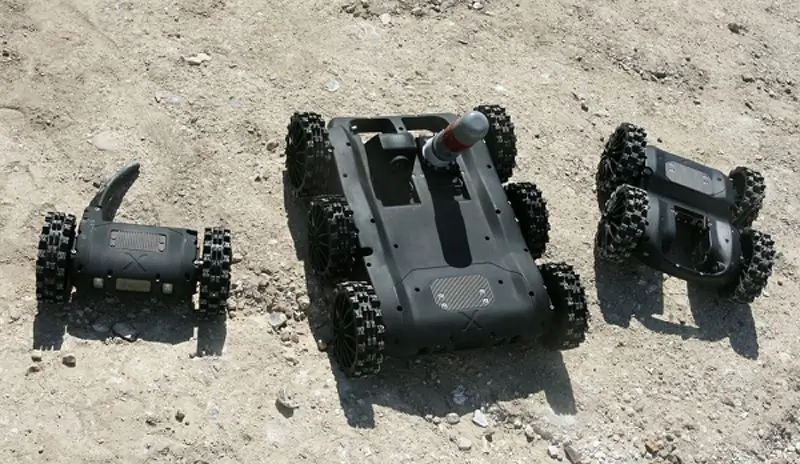
All Nexter Nerva robots were created with an eye on quick wheel change in order to adapt the robot to the surface on which it will work.
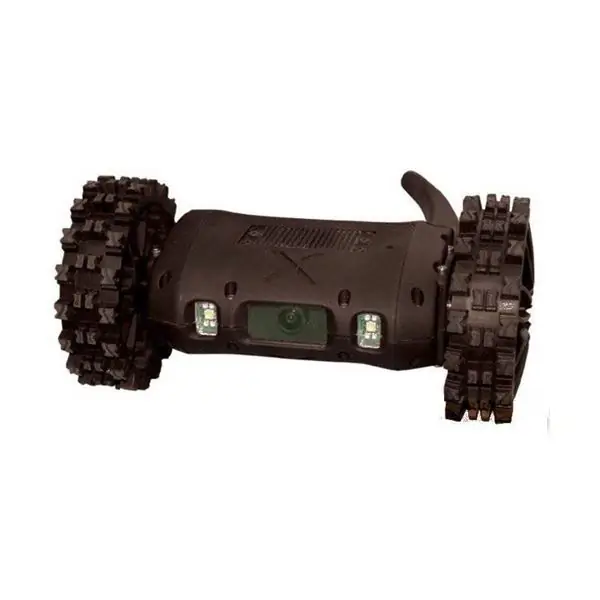

Nerva S is a lightweight member of the Nexter robot family; the rear retractable handle is used not only to throw the robot, but also to turn it on
The production model Nerva LG was shown at Milipol 2013 along with its smaller brother Nerva S. This two-wheeled robot weighs only two kilograms and can be used both indoors and outdoors; Li-ion battery 21.6 volts with a capacity of 2700 mAh allows the device to work continuously for 4 hours. The inclusion is due to the extension of the rear tail, which, in order to save space in the transport configuration, folds along the body. The tail is used not only to stabilize the robot during operation, but also to throw it over long distances, even from a moving vehicle. And since the Nerva S was originally designed as a throwable system, its weight and strength allow it to be thrown through a window. As for the LG model, the wheel change is carried out in one motion. In order to increase mobility, wheel stops can be added on each side for installing tracks, the front wheels in this case act as drive sprockets. This version of the robot received the designation Nerva DS. The Nerva S has the same speed range as the LG and uses the same communication channel. It has a high-resolution camera and microphone plus a backlight diode and a front infrared LED. The Nerva S model can also be deployed with additional devices that are mechanically attached to the Picatinny rail. The Nerva S robot is produced serially.
Novatiq: The Swiss company produces one castable PocketBot model. The robot is driven by three electric motors, all installed in the housing, one of them rotates the third rear wheel through a belt drive. Weighing just 850 grams, PocketBot can withstand drops of 8 meters and throws of 30 meters. According to the company, the three-wheel configuration can significantly reduce its kinetic energy on impact compared to the four-wheel configuration. Immediately after landing and starting to move, the PocketBot restores its normal position, as it is not a completely symmetrical system. The two main wheels are equipped with T-shaped lugs, which provide a smooth ride on level ground, as well as optimal traction on sand, rocks and vegetation. The third rear wheel is smooth, as testing has shown that the T-lugs create excessive traction, which significantly slows the robot down when cornering.
According to the company, the 14 mm ground clearance of the PocketBot robot allows it to cope with vertical obstacles of 30 mm and slopes of 40 °. A high-resolution color camera is installed in the front of the case, which can be rotated ± 90 °. In low light, the x8 digital zoom camera automatically switches to monochrome mode for low light. Infrared illumination is also available, however the operator can switch it to manual mode to use the white light illumination. A waterproof microphone is installed, as well as a small waterproof speaker that allows you to address people near the PocketBot, for example, a hostage. There are mounting points on the top of the PocketBot for attaching additional devices such as a thermal imaging camera or chemical detectors. The hardware can be installed at the factory, but then in this case you have to sacrifice the throwability of the PocketBot. The device is activated by the top switch, but it cannot be turned off by an outsider as this can only be done from the control panel.
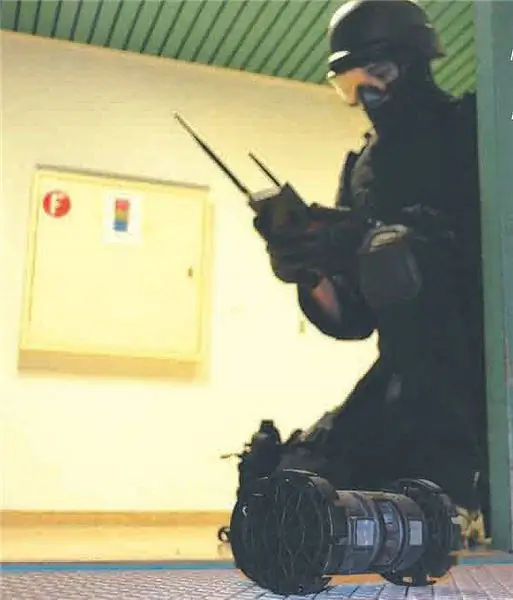
Novatiq's three-wheeled PocketBot is designed for military and police forces
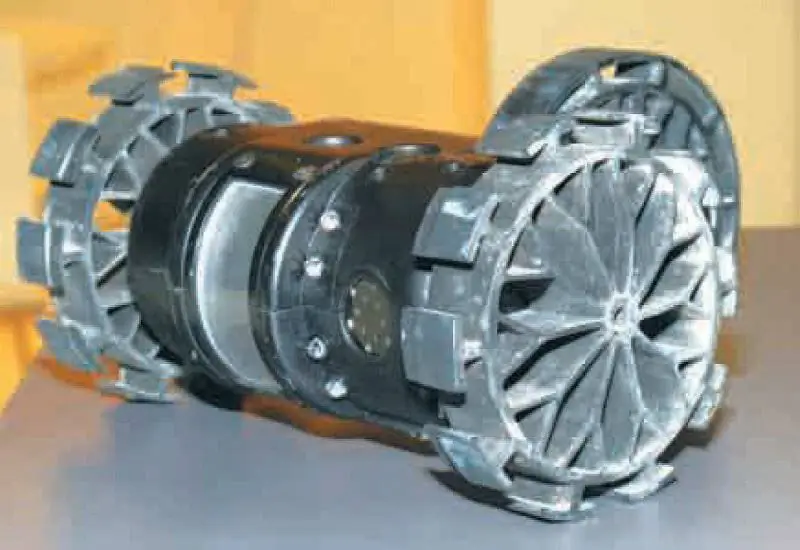
The PocketBot's two main wheels are specifically designed to provide maximum traction on different surfaces.
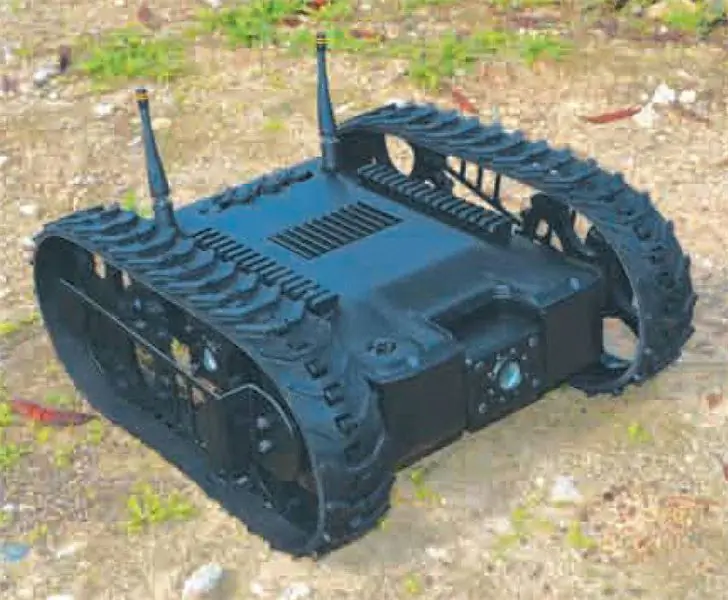
Thanks to its tracks, StoneMarten can cope with difficult terrain; various systems can be installed on the Picatinny rails
Novatiq has developed the Crab-3 control unit. This unit weighing 0, 7 kg and dimensions 200x110x450 mm has a color touch screen with a diagonal of 3.5 inches, it is powered by a quick-change battery. The same battery is in the robot itself in order to reduce the logistic load, the continuous operation time is 4-5 hours. The digital video recording system also stores images on an SD card for further analysis. The PocketBot kit consists of one robot and one control unit, two chargers, four batteries, one headset, several spare parts such as wheels, antennas, plugs, etc. The configuration of the PocketBot platform has now been finalized. It is offered by the customer with a standard data link providing a range of 250 meters in open areas and 70 meters in indirect visibility. Novatiq is ready to replace the communication channel according to the wishes of the buyer, for example, with the COFDM system (Coded Orthogonal Frequency Division Multiplexing). Novatiq has already received a number of orders in Europe and is ready to supply an unnamed customer in the Middle East for its special forces.
The second ground robot in the Novatiq portfolio is tracked and quite heavy. It is designated StoneMarten and is intended to be deployed in high-risk areas on a variety of terrain types, as the tracks minimize size and weight while maximizing performance. The robot has already been sold to unnamed buyers in Europe and Africa. It weighs 4.5 kg, which allows it to be classified in the category of throwable robots with a big stretch; the permissible drop height is three meters and the throwing height is five meters. With two electric motors, it can reach a maximum speed of seven km / h, and special flipper devices allow the robot to climb steps. This model features a high resolution front tilt color camera, panning by slow movement by rotating the robot. Three more fixed color cameras are installed at the back and sides; All cameras have white and infrared LED lights on the sides, a microphone and loudspeaker complete the standard package. Picatinny rails allow for additional equipment, four connectors are available for power supply, video and data transmission. The robot has some level of autonomy, for example, the ability to return to the last point with good communication quality or return to the operator. Like PocketBot, StoneMarten currently has an approved configuration, but the company maintains a certain level of functional flexibility to meet customer needs.
Novatiq is currently developing a new series of drones, all under the designation Nova followed by a suffix. All these products are still at the prototype stage and therefore all technical specifications are preliminary. The smallest of the new line is the NovaCTR (Close Target Reconnaissance) robot, definitely in the reject category. It weighs 600 grams (less even than the PocketBot), has a tracked configuration, and therefore can be considered as a complement to the three-wheeled PocketBot. The device has the same impact resistance as the Throwbot robot. The robot carries on board a fixed front color camera with conventional and infrared illumination, as well as a microphone and loudspeaker. The declared working range is 100 meters in line of sight and 30 meters in other cases. NovaCTR has an approved configuration and was recently added to the Novatiq portfolio; the company is currently in talks with potential buyers.
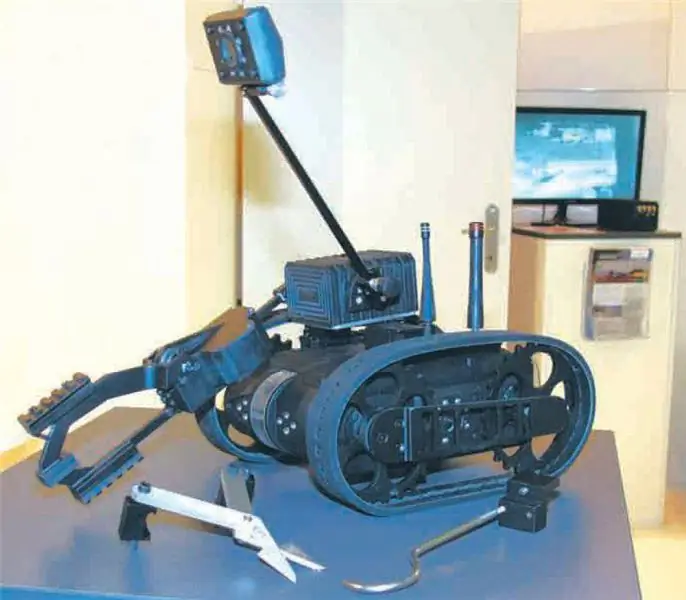
NovaSSR is the latest product from the Swiss company Novatiq, but two more new robots are in the final design stages.
There are a couple of robots in the company's catalog, they are somewhat heavier, but still fit into the category of throwable. NovaMRR (Medium Range Reconnaissance) and Nova SRR (Short Range Reconnaissance), respectively 4x4 wheeled chassis and tracked chassis with flippers. However, these two chassis can be transformed respectively into tracked and wheeled. NovaMRR has a higher top speed compared to its tracked counterpart - 10 km / h versus 4.7 km / h - while the latter is capable of overcoming steps. In terms of throwing characteristics, the wheeled chassis can withstand a drop from four meters and a throw of six meters, while for a tracked analog these figures are three and five meters, respectively. The MRR is equipped with a high-resolution front-facing color camera with virtual panoramic zoom and three fixed color cameras mounted on the sides and rear to provide 360 ° all-round coverage. The SRR also has a front-facing camera but is electrically tilted. While both robots are equipped with a microphone and speaker for two-way communication with the operator, the tracked version also has white and infrared LEDs on all four sides. Both robots can carry devices with a total mass of 2.5 kg, mounted on a Picatinny rail, an additional mechanical fixture with a plate is also available; power supply and data transmission are carried out through the connectors of the company Fischer Сonnectors.