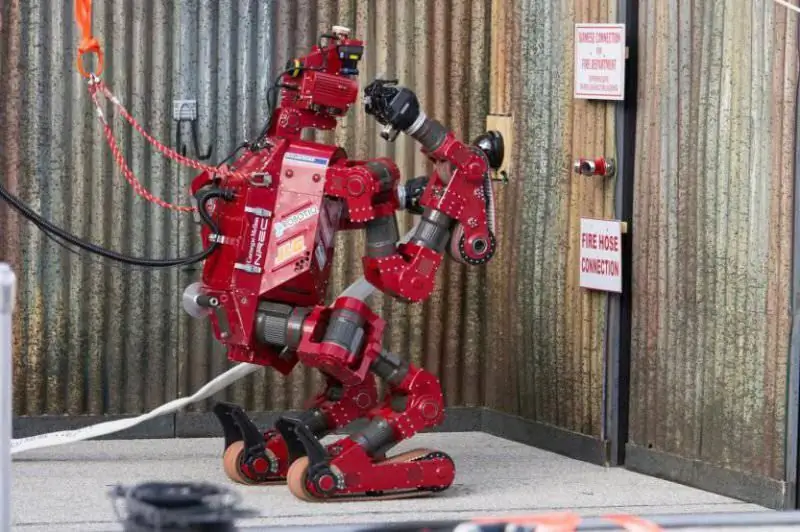
CHIMP performs one of the most difficult tasks - trying to attach a fire hose to a hydrant
Hosted by the Defense Advanced Research Projects Agency (DARPA), the Robotics Challenge promises to revolutionize the capabilities of systems and how they are designed. Let's take a look at this event and evaluate the opinion of a number of key players
On March 11, 2011, Japan was hit by a powerful earthquake with an epicenter about 70 km off the east coast of Honshu. As a result of an earthquake of magnitude 9, waves were formed that reached a height of 40 meters and propagated inland for 10 km.
The nuclear power plant Fukushima I stood in the way of the devastating tsunami. When giant waves hit the station, the reactors were catastrophically destroyed. This incident became the worst nuclear tragedy since the accident at the Chernobyl nuclear power plant in 1986. This event formed the basis for the scenario of perhaps one of the most significant robotics programs to date - DRC (DARPA Robotics Challenge - practical tests of robotic systems under the Advanced Research and Development Administration program of the US Department of Defense).
The DRC trials were announced in April 2012 and disaster relief was chosen as the scenario for these trials. The development of new systems had to be carried out within the framework of this scenario, mainly due to the fact that it was included in the 10 key missions of the US Department of Defense, identified by the White House and the Secretary of Defense in January 2012. In December 2013, within the framework of these competitions, an important stage passed, when the first "full-scale" tests were carried out in Florida for the first time.
DRCs differ in several innovative ways, they combine virtual and field testing, and they are open to funded and non-funded teams. This event consists of four so-called sections or tracks; DARPA provided financial support for two tracks Track A and Track B and opened these competitions to all new arrivals.
Of the four tracks, two (Track A and Track B) received funding. Following a general announcement and application submission, DARPA selected seven teams for Track A to develop new hardware and software; in Track B, 11 teams developed only software.
Track C is not funded and is open to new members from all over the world; Like the participants in Track B, its participants primarily used a virtual robot simulation program to test their software. Track D is intended for foreign contributors who wish to develop hardware and software, but without DARPA funding at any stage.
The key to the innovative DRC approach is the VRC (Virtual Robotics Challenge) component. The top-ranked teams - whether from Track B or C - will receive funding from DARPA, as well as the Atlas robot from Boston Dynamics, with which they will take part in field tests.
In May 2013, teams from Track B and Track C applied to qualify for VRC, which was held the following month. Out of more than 100 registered teams, only 26 continued to move to VRC and only 7 teams approached full-scale tests.
The VRCs took place in a highly accurate virtual space licensed under the Apache 2 license by the Open Source Foundation. The teams were tasked with completing three of the eight tasks that were identified for real robots in the first field tests.
Testing
While the robots demonstrated in VRC were impressive, how they would behave in field tests was not 100% certain; however, Jill Pratt, Program Director of the DRC Competition, said he was very pleased with their capabilities. “We expected that since this was the first physical part of the test, we could see a lot of hardware breakdowns, but in fact this was not the case, all the hardware was very reliable. The first few teams, especially the first three, managed to get more than half the points and made significant progress even when we deliberately interfered with the communication channel."
Pratt was also impressed with the capabilities of the Atlas robot, "It really exceeded our expectations … Boston Dynamics has done exemplary work to ensure that none of the teams are harmed by any kind of hardware failure."
However, there is still room for improvement, such as manipulator arms with limited working space and leaks from the robot's hydraulic system. The modernization process began even before the event in December 2013. Pratt said that he would also like to increase the number of different instruments in the finals and the robots will most likely have a tool belt from which they will need to select the right tools and change them during the script execution.
The Atlas robot was also praised by Doug Stephen, a researcher and software engineer at the Florida Institute for Human and Machine Cognitive Abilities, whose team came in second in field trials on Track B. "This is quite a wonderful robot … we have worked with it 200 hours of clean time in two or three months and this is very unusual for an experimental platform - the ability to work steadily and not break."
Behind the impressive capabilities of robots in DRC are literally heroic efforts; assignments are designed to be particularly challenging and challenge the hardware and software developed by the teams.
While the tasks were difficult, Pratt doesn't think DARPA set the bar too high, noting that every task was completed by at least one of the teams. Driving and joining the sleeves were found to be the most difficult tasks. According to Stephen, the first was the most difficult: “I would say definitely - the task of driving a car, and not even because of the driving itself. If you want to get completely autonomous driving, which is very difficult, then you always have a robot operator. Driving was not that difficult, but getting out of the car is much more difficult than people might imagine; it's like solving a big 3D puzzle."
In accordance with the format of the DRC Finals, due in December 2014, all tasks will be combined into one continuous scenario. This is all in order to make it more credible and give teams strategic choices about how to execute it. Difficulty will also increase, and Pratt added: “Our challenge for teams that have done great at Homestead is to make it even harder. We are going to remove the tethered cables, remove the communication cables and replace them with a wireless channel, while we are going to degrade the quality of the connection so that it is even worse than in previous tests."
“My plan at the moment is to make the connection intermittent, at times it will have to completely disappear, and I believe that this should be done in a random order, as it happens in real disasters. Let's see what robots can do, working for a few seconds, or maybe up to a minute, trying to perform some subtasks on their own, even if they are not completely cut off from the operator's control and I think it will be a very interesting sight."
Pratt said that the safety systems will also be removed in the finals. "This means that the robot will have to withstand the fall, it also means that it has to climb on its own and it will actually be quite difficult."
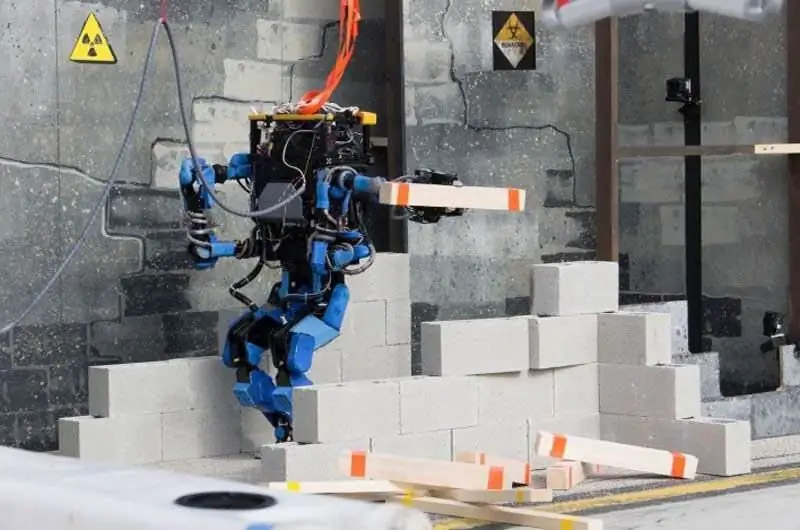
Schaft robot removes debris from its path
Challenges and strategies
Of the eight teams during the tests, five used the ATLAS robot, however, Track A participants - the winner of Team Schaft and the third prize winner of Team Tartan Rescue - used their developments. Originally from Carnegie Mellon University's (CMU) National Robotics Engineering Center, Tartan Rescue has developed the CMU Highly Intelligent Mobile Platform (CHIMP) for DRC testing. Tony Stentz of Tartan Rescue explained the team's rationale for developing their own system: "It might be safer to use an off-the-shelf humanoid robot, but we knew we could create a better design for disaster response."
“We knew we had to create something roughly human, but we didn't like the need for humanoid robots to maintain balance while moving around. When bipedal robots move, they need to keep their balance in order not to fall, and this is quite difficult on a flat surface, but when you talk about moving through construction debris and stepping on objects that can move, it becomes even more difficult. Therefore, the CHIMP is statically stable, it rests on a fairly wide base and in an upright position it rolls on a pair of tracks at its feet, so it can go back and forth and turn in place. It can be positioned easily enough to hold out your hands to carry everything you need on assignment; when he needs to move on more difficult terrain he can fall on all four limbs, since he also has caterpillar propellers on his hands.
Inevitably, teams from different tracks faced different challenges in preparing for the tests, the Institute for Human and Machine Cognitive Abilities focused on software development, because this is the most difficult problem - the transition from VRC to field problems. Stephen said that “when the Atlas robot was delivered to us, it had two 'modes' that you could use. The first is a simple set of motions provided by Boston Dynamics that you could use for motion and which has been slightly underdeveloped. It turned out that most of the teams used these built-in modes from Boston Dynamics during the Homestead competition, very few teams wrote their own robot control software and nobody wrote their own software for the whole robot …"
"We wrote our own software from scratch and it was a whole body controller, that is, it was one controller that worked in all tasks, we never switched to other programs or to another controller … Therefore, one of the most difficult tasks was to create the program code and run its on Atlas as it was kind of a black box when Boston Dynamics presented it to us, but it's their robot and their IP so we really didn't have low-level access to the onboard computer Our software runs on an external computer and then communicates with using an API (Application Programming Interface) over fiber with an on-board computer, so there are large delays and problems with synchronization and it becomes quite difficult to control such a complex system as Atlas."
While writing your own code from scratch was certainly more difficult and time consuming for the Institute for Human and Machine Cognitive Abilities, Stephen believes that this approach is more profitable, since when problems arise, they can be solved faster than relying on Boston Dynamics. In addition, the Atlas companion software was not as advanced as the software that Boston Dynamics uses in its own demos “when they sent the robot … they said quite openly that the movements are not what you see when Boston Dynamics uploads a video of the robot to Youtube. working on the software of this company. This is a less advanced version … this is enough for training the robot. I don't know if they were going to give the code to the commands to use, I don't think they expected everyone to write their own software. That is, what was delivered together with the robot is possible from the very beginning and was not intended to complete all eight tasks in the DRC practical tests."
The biggest challenge for the Tartan Rescue team was the tight schedule they had to adhere to when developing the new platform and related software. “Fifteen months ago, CHIMP was just a concept, a blueprint on paper, so we had to design the parts, make the components, put it all together and test it all. We knew it would take most of our time, we couldn't wait and start writing software until the robot was ready, so we started developing software in parallel. We didn't actually have a full-fledged robot to work with, so we used simulators and hardware substitutes during development. For example, we had a separate manipulator arm that we could use to check certain things for a single limb,”Stentz explained.
Referring to the complications that the deterioration of data transmission channels will add, Stentz noted that this decision was made from the very beginning specifically for such situations and that this is not a very difficult problem. “We have sensors mounted on the robot's head - laser rangefinders and cameras - allowing us to build a complete 3-D texture map and model of the robot's environment; this is what we use from the operator's side to control the robot and we can present this situation in different resolutions depending on the available frequency band and communication channel. We can focus our attention and get a higher resolution in some areas and a lower resolution in other areas. We have the ability to remotely control the robot directly, but we prefer a higher level of control when we define targets for the robot and this control mode is more resistant to signal loss and delays.”
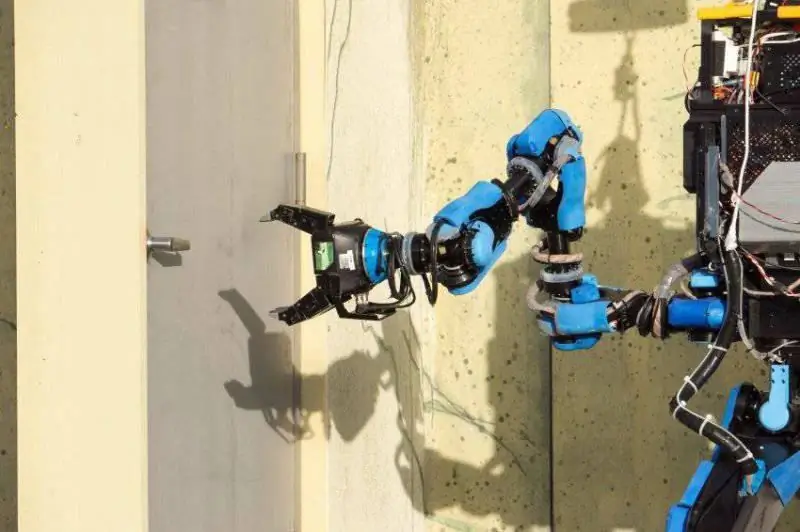
The Schaft robot opens the door. Improved robotic handling capabilities will be a must for future systems
Next steps
Stentz and Stephen said their teams are currently evaluating their capabilities in real-world tests to assess what actions need to be taken to move forward, and that they are awaiting a DARPA review and additional information on what will be in finals. Stephen said they are also looking forward to receiving some modification for the Atlas, noting one already approved requirement for the finals - the use of an onboard power supply. For CHIMP, this is not a problem, since the robot with electric drives can already carry its own batteries.
Stentz and Stephen agreed that there are a number of challenges that need to be addressed in developing the robotic systems space and creating platform types that can be used in disaster relief scenarios. “I would say that there is no one thing in the world that could be a panacea. In terms of hardware, I believe that machines with more flexible manipulation capabilities can be useful. As for software, I believe that robots need a greater level of autonomy so that they can perform better without a communication channel in remote operations; they can complete tasks faster because they do a lot themselves and make more decisions per unit of time. I think the good news is that DARPA competitions are really designed to promote both hardware and software,”Stentz said.
Stephen believes that improvements in technology development processes are also needed. “As a programmer, I see many ways to improve software and I also see many opportunities for improvement as I work on these machines. A lot of interesting things happen in laboratories and universities where there may not be a strong culture of this process, so sometimes the work goes haphazardly. Also, looking at the really interesting projects in the DRC trials, you realize that there is a lot of room for hardware improvements and innovation."
Stephen noted that Atlas is a prime example of what can be achieved - a workable system developed in a short time.
For Pratt, however, the problem is more defined and he believes that software improvement should come first. “The point I'm trying to get across is that the bulk of the software is between the ears. I mean, what's going on in the operator's brain, what's going on in the robot's brain, and how the two agree with each other. We want to focus on the hardware of the robot and we still have problems with it, for example, we have problems with production costs, energy efficiency … Undoubtedly the hardest part is the software; and it is the programming code for the robot-human interface and the programming code for the robots themselves to perform the task on their own, which includes perception and situational awareness, awareness of what is happening in the world and choices based on what the robot perceives."
Pratt believes finding commercial robot applications is key to developing advanced systems and moving the industry forward. “I think we really need commercial applications beyond disaster management and general defense. The truth is that the markets, defense, emergency response and disaster relief, are tiny compared to the commercial market."
“We like to talk a lot about this at DARPA, taking cell phones as an example. DARPA has funded many of the developments that have led to the technology used in cell phones … If this were only the defense market for which the cells were intended, they would cost many orders of magnitude more than they are now, and this is due to the huge commercial market that has made it possible to obtain incredible availability of cell phones …"
“In the field of robotics, our view is that we need exactly this sequence of events. We need to see the commercial world buying applications that will make prices fall, and then we can create systems specifically for the military, in which commercial investments will be made."
The first eight teams will take part in the December 2014 trials - Team Schaft, IHMC Robotics, Tartan Rescue, Team MIT, Robosimian, Team TRAClabs, WRECS and Team Trooper. Each will receive $ 1 million to improve their solutions and, ultimately, the winning team will receive a $ 2 million prize, although for most, recognition is much more valuable than money.
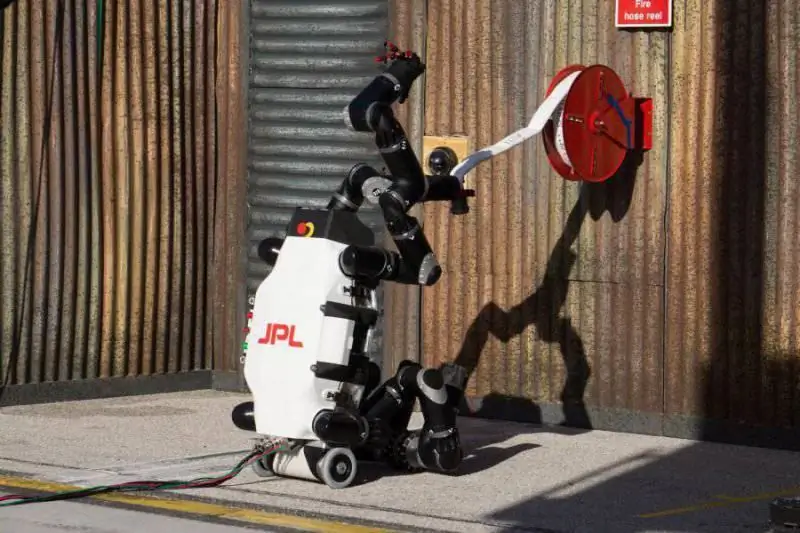
Robosimian from NASA's Jet Propulsion Laboratory has an unusual design
Virtual element
DARPA's inclusion of two tracks in DRC trials, in which only software development teams participate, speaks of the management's desire to open programs to the widest possible circle of participants. Previously, such technology development programs were the prerogative of defense companies and research laboratories. However, the creation of a virtual space in which each team can test their software allowed competitors who had little or no experience in developing software for robots to compete at the same level as well-known companies in this field. DARPA also views the simulated space as a long-term legacy of DRC testing.
In 2012, DARPA commissioned the Open Source Foundation to develop a virtual space for the Challenge, and the organization set about creating an open model using Gazebo software. Gazebo is capable of simulating robots, sensors, and objects in a 3D world, and is designed to provide realistic sensor data and what is described as “physically plausible interactions” between objects.
Open Source Foundation Chairman Brian Goerkey said Gazebo was used because of its proven capabilities. “This package is quite widely used in the robotic community, which is why DARPA wanted to bet on it, because we saw its benefits in what it does; we could build a community of developers and users around it."
Although Gazebo was already a well-known system, Gorky noted that while there was still room to strive, steps should be taken to meet the requirements identified by DARPA. “We have done very little to model walking robots, we have mainly focused on wheeled platforms and there are some aspects of modeling walking robots that are quite different. You have to be very careful about how you make contact resolution and how you model the robot. This way, you can get good parameters in exchange for accuracy. A lot of effort has gone into detailed simulation of the physics of the robot, so you can get good quality simulations and also get the robot working in almost real time, as opposed to working in one tenth or one hundredth of real time, which is likely if not for all the effort you put into it."
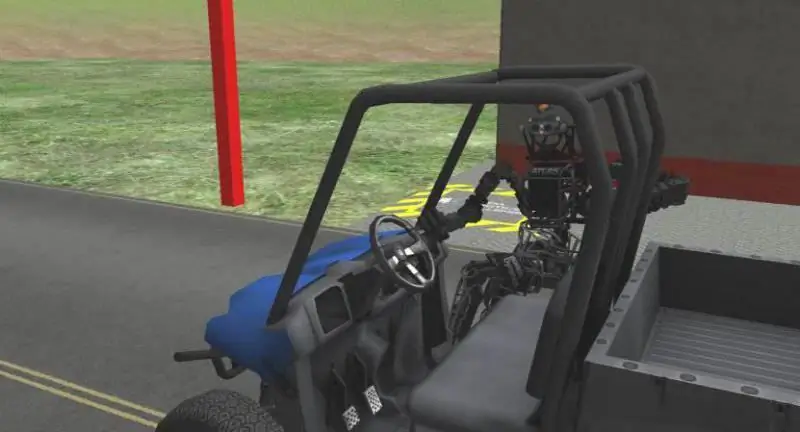
A simulated Atlas robot gets into a car during the virtual competition stage of the DRC
Regarding the simulation of the Atlas robot for virtual space, Görki said the Foundation had to start with a basic dataset. “We started with a model provided by Boston Dynamics, we did not start with detailed CAD models, we had a simplified kinematic model that was provided to us. Basically a text file that says how long this leg is, how big it is, and so on. The challenge for us was to correctly and accurately adjust this model so that we could obtain a compromise in performance in exchange for accuracy. If you are modeling it in a simplistic way, then you can introduce some inaccuracies in the underlying physics engine, which will make it unstable in certain situations. Therefore, a lot of work is to slightly change the model and in some cases write your own code to simulate certain parts of the system. This is not only a simple physics simulation, there is a level below which we are not going to go."
Pratt is very positive about what has been achieved with VRC and simulated space. “We've done something that hasn't happened before, created a realistic process simulation from a physical point of view that can be run in real time so that the operator can do their interactive work. You really need this, since we are talking about a person and a robot as one team, so the simulation of the robot must work in the same time frame as the person, which means in real time. Here, in turn, a compromise is needed between the accuracy of the model and its stability … I believe that we have achieved a lot in the virtual competition."
Stephen explained that the IHMC Institute for Human and Machine Cognitive Abilities faced different challenges in software development. “We used our own simulation environment, which we integrated with Gazebo as part of a virtual competition, but a lot of our development is done on our platform called the Simulation Construction Set … we used our software when we launched a real robot, we did a lot of modeling and this one of our cornerstones, we look forward to a lot of good software development experience."
Stephen said the Java programming language is preferred at IHMC because it has "a really impressive toolbox that has grown up around it." He noted that when combining Gazebo and his own software, “the main problem is that we write our software in Java and most of the software for robots uses C or C ++, which are very good for embedded systems. But we want to do work in Java the way we want - to make our code work in a certain time frame, as it is implemented in C or C ++, but no one else uses it. It's a big problem getting all Gazebo programs to work with our Java code.”
DARPA and the Open Source Foundation continue to develop and improve the simulation and virtual space. “We are starting to implement elements that will make the simulator more useful in a different environment, outside the rescue site. For example, we take the software we used in the competition (called CloudSim because it simulates in the cloud computing environment) and we develop it with the intention of running on cloud servers,”Görki said.
One of the main advantages of having a simulated environment open for public use and working with it in the cloud is that high-level calculations can be performed by more powerful systems on servers, thereby allowing people to use their light computers and even netbooks and tablets. to work at your workplace. Görki also believes this approach will be very useful for teaching, as well as in product design and development. "You will be able to access this simulation environment from anywhere in the world and try your new robot in it."