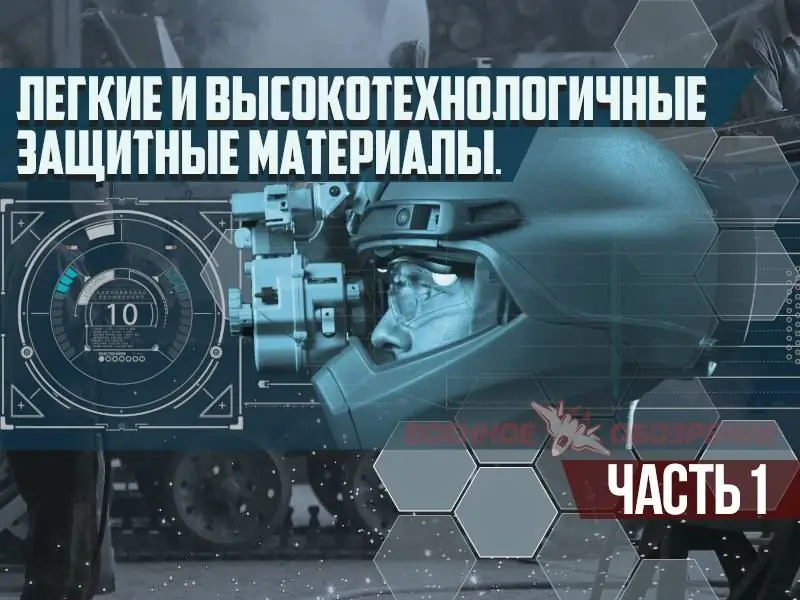
The field of protective materials is immense and growing rapidly. New materials expand the technological basis for personnel protection systems and weapon platforms. At the same time, business practices are changing, moving away from exclusive suppliers and other traditional patterns common to industries such as defense and security
The industry is trying to respond quickly to the expanding needs of military customers, not only in order to "lighten the load", but also to develop equally important characteristics of new protective materials and armor protection systems.
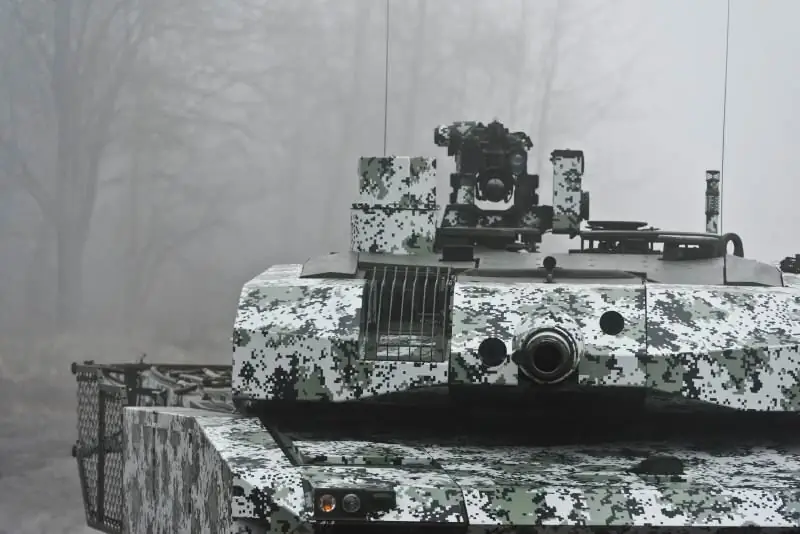
This can be confirmed by the words of the head of the body protection department at DSM Dyneema, Marco Manik, who said in one of his interviews: “We produce the strongest man-made fiber, and this is DYNEEMA fiber”.
The industry expert has categorized DSM's security solutions as a “new wave or generation of ballistic protection”. The company's offerings, which he calls "Uncompromising Technological Excellence", combine lightweight materials and superior performance, provide comfort along with other quality features, and provide customers with "everything they need to get things done."
Manik highlighted the DYNEEMA fiber-based HB laminate as one of the technological breakthroughs in ballistic protection systems. Indeed, “DYNEEMA HB fiber is not only 15 times stronger than steel, but has a number of properties that are really in demand, which we pay close attention to,” he emphasized, and when asked what customers in this area primarily want, he answered that "they want ever lighter options for their equipment."
Sherrill Ingstad, Head of Advanced Ceramics at ZM agrees with him: “We see great demand in the US and other countries for lightweight protection systems, and this is where our efforts are concentrated today. We strive to fine-tune every aspect of our work - from proprietary materials technology and R&D to our workforce alignment and manufacturing process refinement - to provide lightweight systems that reduce the burden on the military while still providing the required level of protection."
As a spokesman for Ceradyne (part of ZM), Ingstad announced that more than two million bulletproof vest inserts and over 100,000 enhanced combat helmets have been supplied to the US military to date.
Despite its relatively small mass, the ESN “provides a higher level of bullet and fragmentation protection than any other combat helmet in history,” Ingstad said. "Compared to other helmets of the same weight in service, the ESN increases the level of anti-bullet and anti-fragmentation protection by more than 35%."
The first ECH helmets entered service with the US military in 2014.
Ceradyne's personal protective system portfolio also includes the ESAPI (enhanced small arms protective insert) lightweight, enhanced small arms protective insert to protect the torso from small arms fire. Inserts are available in different sizes and fit into special internal sections of body armor for military personnel of both genders. “We supply bulletproof vest inserts to the Department of Defense Logistics Support, which then handles orders for each individual unit,” said a Ceradyne spokesman.
The company supplies modern ESAPI protective inserts of various weights. The current contract of the US Department of Defense provides for the supply of ultra-small, small and medium-sized inserts, the mass of which ranges from less than 2 kg to almost 2.5 kg. Ceradyne also offers large and extra-large inserts for body armor, which are slightly heavier.
Ceradyne began shipping inserts a month ahead of schedule last June. In accordance with it, the company must complete deliveries for this order at the end of 2017.
Protection of vehicles and their crews
The representative of RUAG Defense gave his assessment of the problems and tasks in the field of protective materials for vehicles, which, in fact, boil down to finding a compromise between economic profitability and the maximum possible weight reduction (off-road capability, airlift, etc.), and also solutions that ensure the protection of crews and the vehicles themselves from a multitude of threats, more dynamic and more deadly. A RUAG Defense spokesman also commented: “Obviously, specific needs differ from scenario to scenario, but you are always trying to find the perfect balance between levels of protection and mobility. Those who talk about the volatility of threats are right, but we are constantly exploring new ideas in the field of materials and design solutions."
Further, the representative of RUAG noted the blurring of boundaries between scenarios of modern threats and the challenges that these scenarios pose for suppliers of materials and security systems. “Threat scenarios are now not as definite as they were before. The distinction between symmetric and asymmetric military action is blurring before our eyes, now we need hybrid solutions that can cover a much wider range of threats."
RUAG strives to meet current global challenges and develops protection kits for a wide variety of vehicles, from light 4x4 armored vehicles to main battle tanks such as LEOPARD 2, and in this regard, the company's portfolio in this sector is constantly expanding.
Then the representative of the Swiss company continued: “For the German BMP PUMA, we supply mine protection along with other protection components. RUAG has taken on the development of comprehensive mine protection, protection against IEDs (improvised explosive devices) and armor-piercing projectiles for Austrian and Belgian PANDUR I armored vehicles. Production and delivery of our Roof PRO ballistic kits for the head manufacturer are in full swing."
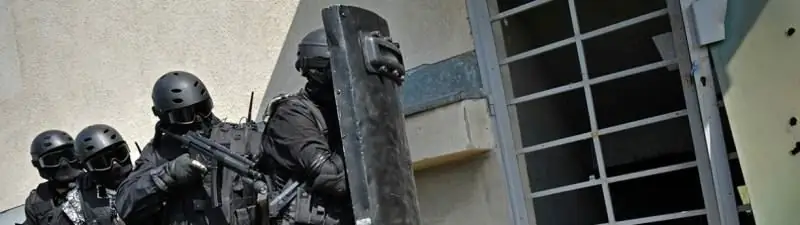
Alcoa Defense Vice President Margaret Cosentino noted another parallel and somewhat competing trend in vehicle protection. According to her, earlier, much attention was paid to additional armoring of vehicles that participated in operations in Iraq and Afghanistan, and now there is a return to speed, maneuverability and maneuverability as functions of increasing combat survivability. “For example, in special operations, ultralight vehicles are deployed for combat groups. Alcoa is working with the US Army's scientific community through its new Mobile Protected Firepower program to gain as much information as possible about innovative materials and select technology for a secure high-precision direct fire system.”
Alcoa Defense's products extend the life cycle of military vehicles, with a portfolio of products for both existing and new vehicles. Indeed, Alcoa's multicomponent products, including those made by extrusion, stamping, casting, and a full range of rolled products, are found on tactical wheeled vehicles and ground combat vehicles, ranging from aluminum armor on HMWWV jeeps (as a reaction to IEDs) and heavy off-road trucks. HEMTT, and ending with aluminum components for new platforms, such as the JLTV armored car.
“First, Alcoa Defense uses a very wide range of materials in its activities, because our business is divided equally between aluminum, titanium and nickel products, which allows us to work with the military and the main manufacturers of final products in order to obtain the right material, alloy and heat treatment to satisfy requirements for special tasks, - explained Cosentino. “Second, we focus on full vertical integration, from material to product shape, to machining and final assembly. Alcoa's efficiency gains help our customers become more efficient and more competitive.”
Another supplier of defense systems for military vehicles is QinetiQ North America (QNA). The LAST Armor Spall Liner anti-splinter liners are installed on various American-made MRAP vehicles, and its energy-absorbing BlastRide seats are installed in BMPs and armored personnel carriers in different countries. Jeff Riu, Head of Survivability Systems at the company commented: “In addition, our Q-NET passive RPG protection solutions are installed on more than 13,000 vehicles worldwide, for example, they provide protection for machines such as MAXXPRO, PL-ATU, HEMMT and STRYKER, as well as platforms from other countries. The Q-NET protection system has the potential to be installed on some variants of the JLTV armored vehicle of the US Army and Marine Corps."
QNA is also developing personal protective equipment for airplanes and helicopters, with Mr. Riu also sharing some of his company's secret sauce recipes, which are to fully address the needs of its customers in terms of cost, weight and characteristics of the final product in order to to provide them with the best possible solution. “We have achieved this by working with a variety of superior materials, including rolled armor steel, various grades of ceramics and the latest high-quality ballistic fibers. We also work tirelessly to develop innovative new solutions such as our energy-absorbing seats and our BlastPro blast attenuation technology.”
Collaboration and partnership
One of the hot topics in the discussion among the security materials business concerns agreements with multiple suppliers and other partners (in some cases hundreds of organizations) in addition to the exclusive partnership agreements that are common in other segments of the defense market.
Using the example of his company, Marko Manik spoke about DSM's commitment to innovation and optimization of new technologies in its partner network and about internal investments in research and development.
DSM prefers partners in the defense and related security sectors, and some of these partners have a stronger relationship with DSM due to their ability to innovate. “If we have a partner who has the ability to innovate faster than anyone else, then he has an advantage, because in addition to our products, there are also end products. That is why we need to work with partners who are to some extent consistent with our speed of innovation,”said Manik.
DSM Dyneema's most recent business partner is First Armor, a subsidiary of the KADDB Investment Group. In June 2016, First Armor revealed a lightweight padded panel worn in combination with a safety vest. The new First Armor liner is made from Dyneema HB212. This UHMWPE-based composite laminate is excellent for lightweight, durable defense systems created using the DYNEEMA Force Multiplier technology.
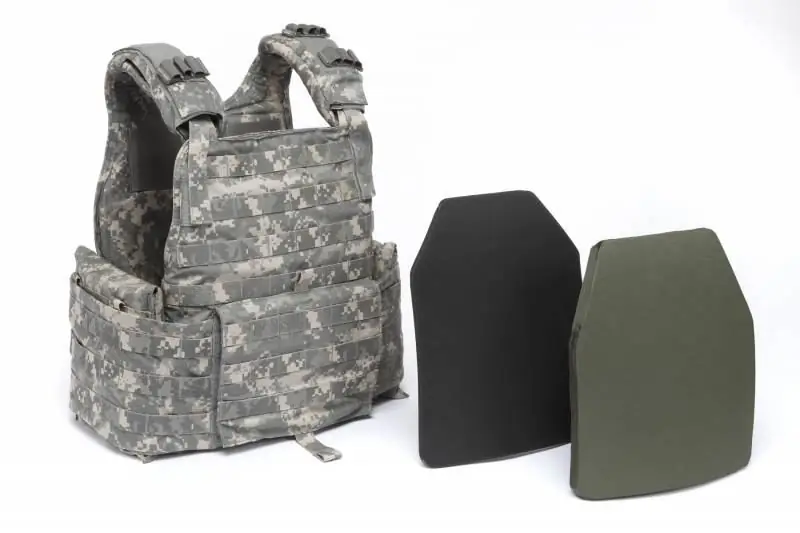
First Armor will soon offer several types of body protection systems based on various high performance materials developed by DYNEEMA.
At the beginning of last year, another DSM partner, Point Blank Enterprises, introduced its ALPHA ELITE Black body protection system, expanding the ALPHA ELITE product line. “The newest ALPHA ELITE Black, which protects against small arms bullets, is an improvement on the previous product, as it reduces weight by 17% with the same level of protection,” the company said in a press release. The ALPHA ELITE Black body armor uses the new generation DYNEEMA Force Multiplier technology from DSM.
RUAG also does not bypass any organization in this area, striving for mutually beneficial cooperation. A RUAG spokesman explained that the company “regularly studies the market for new designs and materials; and we pride ourselves on the quality of our tests and the tests we conduct to accurately determine the protective properties of materials. This allows RUAG to tailor protection solutions to any vehicle and threat at an optimal weight and cost.”
QNA's Mr. Riu commented, “We have developed strong relationships with some of the leading manufacturers of advanced ceramics, ballistic materials and composite fibers. Leveraging these connections allows us to design and deliver products that outperform our competitors.”
DuPont is another supplier that has established a “strong position” in the supply of materials used in a variety of applications. For example, Kevlar synthetic fiber technology finds a wide variety of applications - various body armor, inserts, helmets, limb protection and vehicle armoring. All of these products increase the levels of survivability of personnel, while consumers receive protective material of varying degrees of "softness" or "hardness" (common terms in this sector). “Soft protection refers to vests and other items of equipment that are often made from fabric fibers and other flexible structures to improve the fit, comfort and mobility of wearers,” explained Joseph Hovanek, chief technologist at DuPont Protection Solutions. "Hard protection refers to the tougher composite structures, such as inserts, helmets, and vehicle protection components, for which DuPont offers Tensylon polyethylene sheets in addition to Kevlar."
Hovanek spoke about one aspect of DuPont's business model, noting that the company is supplying fibers, fabrics and other structures from Kevlar to leading manufacturers of vests, helmets and armored vehicles that use these materials in the design and manufacture of their products. The industry expert added: "We are focusing on developing localized solutions, with leading manufacturers working with four of our major technical centers in different countries."
In addition to QNA and the other companies mentioned earlier that supply products to various end users, there is another firm that is active in several related areas. Combat Clothing Australia (CCA) Protect is a global defense and security supplier with a wealth of experience in the design and manufacture of ballistic protection for humans, ground platforms and aviation. The company's commercial director, Lee O'Shea, noted that “CCA Protect is active in the markets of Australia, the United States, Hong Kong, Malaysia, Singapore, the United Arab Emirates, New Zealand and Papua New Guinea.”
In particular, CCA Protect supplies hard and soft body protection systems up to Level IV, as well as vehicle armor capable of withstanding anti-tank shells. O'Shea continued: “CCA Protect's advanced armoring solutions have been selected to provide ballistic protection for the Australian Armed Forces UH-60 BLACKHAWK and CH-47 CHINOOK helicopters. CCA Protect's manufacturing facility allows for the manufacture of large single armored panels, making them ideal for Australia's Land 400 Phase 2 project.” As part of this project, Australia will update and modernize its fleet of combat reconnaissance vehicles.
To meet the requirements of its foreign customers, CCA Protect conducts a thorough analysis of solutions in order to achieve a balance between cost, mobility, protection and weight. O'Shea concluded by saying, “The rapidly changing combat space is constantly driving innovation in the ballistic defense industry. CCA Protect's state-of-the-art production facilities and experienced engineers make it possible to meet these complex challenges. The combination of advanced composites and unique bonding techniques creates ultra-lightweight, durable and thin shielding materials.”
The Swiss company Garant develops modern ballistic protection solutions FirmLiner and FlexLiner for different types of applications. Along with the use of the latest materials resulting from intensive research and development activities, Garant also has a wealth of experience gained from long-term programs in cooperation with material suppliers and end users. Popular and widely used materials include para-aramid, polyethylene, polypropylene, and fiberglass.
Transparent spinel ceramics for marine applications
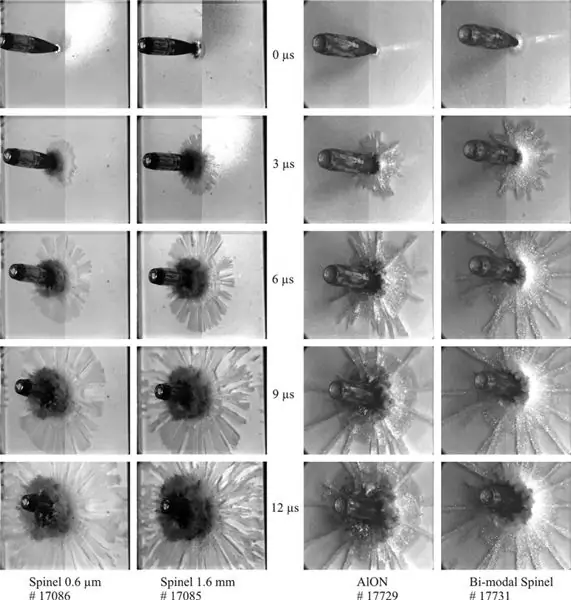
Transparent spinel (MgAl2O4) is currently the preferred material for use in a variety of marine and other defense applications. It is a crystalline material with a cubic lattice, which is increasingly used to protect a variety of ship systems, including sensors, defensive and "smart" materials and weapons.
In addition to its high strength, spinel ceramics have excellent transmittance from ultraviolet rays (0.2 µm) to mid-infrared (5 µm). For the optronic masts of the US Navy's VIRGINIA-class nuclear submarines, single spinel glass is used, which increases survivability and significantly reduces maintenance and life cycle costs. Previously, silicon glass and crystalline germanium were installed on the L-3 KEO optocoupler mast to transmit visible light and rays in the mid-infrared region of the spectrum, respectively. Both of these materials, however, turned out to be insufficiently strong and prone to damage, despite the fact that their thickness was 3, 8 cm. The problem was how to make the window from thick spinel. According to research data, spinel ceramics with a thickness of 3.8 cm, the manufacturing process of which is based on hot pressing, has very good optical properties.
The bridge of the American ZUMWALT-class destroyer (DDG 1000) is also equipped with large high-strength windows that transmit visible light and infrared waves with a wavelength of 5 microns and which must withstand wave impacts of up to 0.56 kg / cm2. As the hot-pressing process scales to large dimensions, the bridge window can be made from one large piece of spinel. Conversely, it can be produced by edge diffusion joining two or more small windows into one. The Applied Optics Division of the US Navy Research Laboratory (NRL) has demonstrated the feasibility of both of these approaches.
The Laboratory noted that the traditional method of high-temperature growth from a melt (> 2000 ° C) from single-crystal spinel is difficult to make a sheet larger than a few millimeters. In the process of solving this problem, the NRL determined that the poor quality of commercial spinel ceramics is associated with uneven mixing of the sintering additive (lithium fluoride) with the spinel powder, which leads to porosity and entrapment (residue in the final product) of this sintering additive. Scientists at NRL have developed a patented process for uniformly coating each particle of spinel powder with a sintering additive, which allows the additive to be removed during the hot-pressing process at a temperature of about 1600 ° C. According to the NRL, this allows for the production of fully compacted, uniformly transparent spinel ceramics with high optical properties, while the process is scalable and allows for the production of large windows.
Designed for harsh environments
Transparent spinel ceramics are used in other defense applications as well. Among them are high power lasers being developed for directed energy weapons. From an optical point of view, one of the most problematic places is the exit lens (window), since glass for such systems does not have sufficiently good thermal, optical and mechanical properties. The reason is that glass windows have a very low thermal conductivity leading to thermal shock. The glass's low strength also makes it difficult to use in aggressive environments, according to NRL scientists. On the other hand, the spinel's superior strength allows it to be used in harsh environments, and its high strength allows for thinner windows, which saves weight. NRL has developed an ultrapure spinel powder technology that has been used to make spinel ceramics with a record low absorption loss of 6 ppm (parts per million) / cm at a wavelength of 1.06 μm.
High optical quality spinel ceramics are also used to make durable heat-transparent radomes for infrared missiles. According to open sources, existing materials, such as crystalline silicon, are fragile and do not provide transmission of visible light. Another material, sapphire (a-Al2O3) has limited transmission at a wavelength of 5 µm. Sapphire is extremely resistant to mechanical damage, since it has a remarkable hardness (9 on the Mohs scale); it is the hardest material after diamond and silicon carbide (a-SiC). But spinel perfectly transmits visible light and has a better transmittance compared to sapphire at a length of 5 microns. In an effort to demonstrate the practical applicability of spinel, scientists at NRL changed the hot-pressing process and successfully fabricated fairings from this material.
The availability of spinel ceramics with high optical properties will also allow the manufacture of lightweight blast shields and goggles for personal protection against IEDs, as well as conformal windows for surveillance systems. Research in 2013 showed that magnesium alumina spinel is an excellent candidate for outer hardened transparent armor layers. Researchers who have systematically investigated the fragmentation of three types of spinel ceramics have shown that the fragmentation mode is one of the key parameters affecting the ballistic resistance of ceramics.