
C-17 GLOBEMASTER III transports humanitarian aid to the outskirts of Port-au-Prince, Haiti on January 18, 2010
This article describes the basic principles and data for testing NATO high-precision air delivery systems, describes the navigation of aircraft to the point of release, trajectory control, as well as the general concept of dropped cargo, which enables them to land accurately. In addition, the article emphasizes the need for accurate release systems and introduces the reader to promising operating concepts
Of particular note is NATO's growing interest in precision dropping. The NATO Conference of National Weapons Directorates (NATO CNAD) has established Precision Dropping for Special Operations Forces as NATO's eighth highest priority in the fight against terrorism.
Today, most drops are carried over the computed air release point (CARP), which is calculated based on wind, system ballistics and aircraft speed. The ballistic table (based on the average ballistic characteristics of a given parachute system) determines the CARP where the load is dropped. These averages are often based on a dataset that includes deviations up to 100 meters of standard drift. CARP is also often calculated using the average winds (at height and near the surface) and an assumption of a constant airflow profile (pattern) from the point of release to the ground. Wind patterns are rarely constant from ground level to high altitudes, the magnitude of the deflection being influenced by terrain and natural weather variables such as wind shear. Since most of today's threats come from ground fire, the current solution is to drop cargo at high altitudes and then move horizontally to steer the aircraft away from the dangerous route. Obviously, in this case, the influence of various air flows increases. In order to meet the requirements of air dropping (hereinafter referred to as airdrops) from high altitudes and to prevent the delivered cargoes from falling into the "wrong hands", precision airdropping at the NATO CNAD conference received a high priority. Modern technology has made it possible to implement many innovative dumping methods. In order to reduce the influence of all variables that impede accurate ballistic drops, systems are being developed not only to improve the accuracy of CARP calculations through more accurate wind profiling, but also systems to guide the dropped weight to the point of a predetermined impact with the ground, regardless of changes in force and direction. wind.
Influence on the achievable accuracy of air release systems
Variability is the enemy of precision. The less the process changes, the more accurate the process, and airdrops are no exception. There are many variables in the air drop process. Among them there are uncontrollable parameters: weather, human factor, for example, the difference in cargo securing and crew actions / timing, perforation of individual parachutes, differences in the manufacture of parachutes, differences in the dynamics of deployment of individual and / or group parachutes and the effect of their wear. All of these and many other factors affect the achievable accuracy of any airborne system, ballistic or guided. Some parameters can be partially controlled, such as airspeed, heading and altitude. But due to the special nature of the flight, even they can vary to some extent during most drops. Nonetheless, precision airdropping has come a long way in recent years and has grown rapidly as NATO members have invested and are investing heavily in precision airborne technology and testing. Numerous qualities of precision drop systems are under development and many other technologies are planned for the near future in this rapidly growing field of capabilities.
Navigation
The C-17 aircraft shown in the first photograph of this article has automatic capabilities related to the navigation part of the precision drop process. Precision drops from C-17 aircraft are carried out using CARP, high-altitude release point (HARP) or LAPES (low-altitude parachute extraction system) parachute release system algorithms. This automatic drop process takes into account ballistics, drop location calculations, drop initiation signals, and records basic data at the time of the drop.
When dropping at low altitudes, in which the parachute system is deployed when dropping the cargo, CARP is used. For high-altitude drops, HARP is used. Note that the difference between CARP and HARP is the free fall trajectory for drops from high altitudes.
The C-17 Air Dump Database contains ballistic data for various types of cargo, such as personnel, containers or equipment, and their respective parachutes. Computers allow ballistic information to be updated and displayed at any time. The database stores the parameters as input to ballistic calculations performed by the on-board computer. Please note that the C-17 allows you to store ballistic data not only for individuals and individual items of equipment / cargo, but also for the combination of people leaving the aircraft and their equipment / cargo.
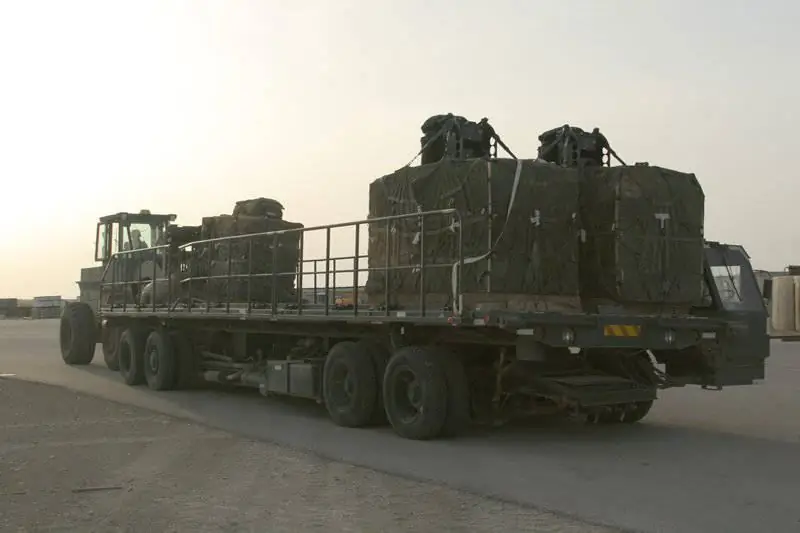
JPADS SHERPA has been in operation in Iraq since August 2004, when Natick Soldier Center deployed two systems in the Marine Corps. Previous JPADS versions such as the Sherpa 1200s (pictured) have a lifting capacity limit of around 1200 lbs, while rigging specialists typically build kits around 2200 lbs.
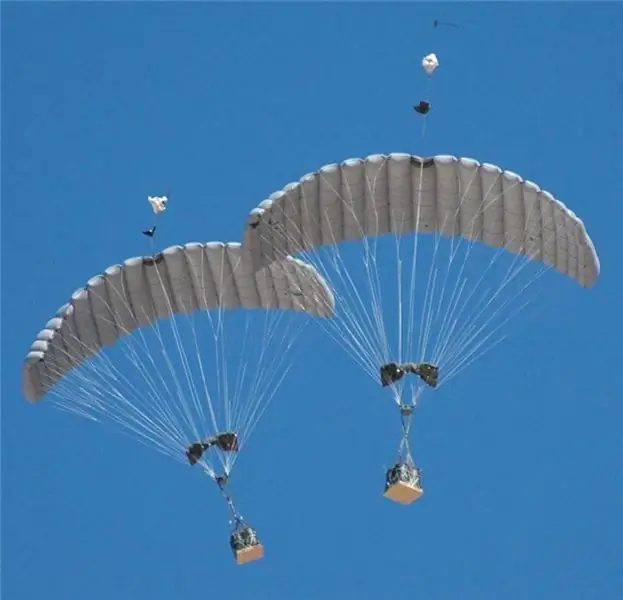
A guided 2200 lb-class cargo of the Joint Precision Airdrop System (JPADS) in flight during the first combat drop. A joint team of Army, Air Force and Contractor representatives recently adjusted the accuracy of this JPADS variant.
Air flow
After the dropped weight is released, air begins to influence the direction of movement and the time of the fall. The computer on board the C-17 calculates air flows using data from various onboard sensors for airspeed, pressure and temperature, as well as navigation sensors. Wind data can also be entered manually using information from the actual drop area (DC) or from the weather forecast. Each data type has its own advantages and disadvantages. Wind sensors are very accurate, but they cannot show the weather conditions over the RS, since the aircraft cannot fly from the ground to the specified height above the RS. Wind near the ground is usually not the same as air currents at altitude, especially at high altitude. Forecasted winds are predictions and do not reflect the speed and direction of currents at different heights. Actual flow profiles are usually not linearly dependent on height. If the actual wind profile is not known and entered into the flight computer, by default, an assumption of a linear wind profile is added to the errors in CARP calculations. Once these calculations are performed (or data entered), their results are recorded in the airdrops database for use in further CARP or HARP calculations based on actual average air flows. Winds are not used for LAPES drops as the aircraft drops the cargo directly above the ground at the desired impact point. The computer in the C-17 aircraft calculates net drift deflections in the direction of and perpendicular to the course for CARP and HARP air drops.
Wind environment systems
The radio wind probe uses a GPS unit with a transmitter. It is carried by a probe that is released close to the drop area prior to release. The resulting position data is analyzed to obtain a wind profile. This profile can be used by the drop manager to correct the CARP.
The Wright-Patterson Air Force's Sensor Control Research Laboratory has developed a high-energy, two-micron, LIDAR (Light Detection and Ranging) Doppler CO2 transceiver with an eye-safe 10.6-micron laser for measuring airflow on height. It was created, firstly, to provide real-time 3D maps of the wind fields between the aircraft and the ground, and, secondly, to significantly improve the accuracy of dropping from high altitudes. It makes accurate measurements with a typical error of less than one meter per second. The advantages of LIDAR are as follows: Provides full 3D measurement of the wind field; provides data flow in real time; is on the aircraft; as well as his stealth. Disadvantages: cost; useful range is limited by atmospheric interference; and requires minor modifications to the aircraft.
Since time and location deviations can affect wind determination, especially at low altitudes, testers should use GPS DROPSONDE devices to measure winds in the drop area as close as possible to the test time. DROPSONDE (or more fully, DROPWINDSONDE) is a compact instrument (long thin tube) that is dropped from an airplane. Air currents are established using the GPS receiver in DROPSONDE, which tracks the relative Doppler frequency from the radio frequency carrier of the GPS satellite signals. These Doppler frequencies are digitized and sent to the onboard information system. DROPSONDE can be deployed even before the arrival of a cargo plane from another aircraft, for example, even from a jet fighter.
Parachute
A parachute can be a round parachute, a paraglider (parachuting wing), or both. The JPADS system (see below), for example, mainly uses either a paraglider or a paraglider / round parachute hybrid to brake the load during descent. The "steerable" parachute provides the JPADS with direction in flight. In the final section of the descent of the cargo, other parachutes are often used in the general system. Parachute control lines go to the airborne guidance unit (AGU) to shape the parachute / paraglider for course control purposes. One of the main differences between the categories of braking technology, that is, the types of parachute, is the horizontal achievable displacement that each type of system can provide. In the most general terms, displacement is often measured as the L / D (lift to drag) of a "zero wind" system. It is clear that it is much more difficult to calculate the achievable displacement without exact knowledge of many parameters affecting the displacement. These parameters include the air currents the system encounters (winds can help or hinder deflections), the total available vertical drop distance and the height the system needs to fully deploy and glide, and the height the system needs to prepare for impact. In general, paragliders provide L / D values in the range from 3 to 1, hybrid systems (i.e. highly wing-loaded paragliders for controlled flight, which near impact with the ground becomes ballistic, provided by circular canopies) give L / D values in the range 2 / 2, 5 - 1, while traditional circular parachutes, controlled by sliding, have L / D in the range of 0, 4/1, 0 - 1.
There are numerous concepts and systems that have much higher L / D ratios. Many of these require structurally rigid guide edges or “wings” that “unfold” during deployment. Typically, these systems are more complex and expensive to use in airdrops, and tend to fill the entire available volume in the cargo hold. On the other hand, more traditional parachute systems exceed the total weight limits for the cargo bay.
Also, for high-precision airdrops, parachute systems can be considered for dropping cargo from a high altitude and delayed opening of the parachute to a low altitude HALO (high-altitude low opening). These systems are two-stage. The first stage is, in general, a small, uncontrolled parachute system that quickly lowers the load over most of the altitude trajectory. The second stage is a large parachute that opens “near” the ground for final contact with the ground. In general, such HALO systems are much cheaper than controlled precision drop systems, yet they are not as accurate, and if several cargo sets are dropped simultaneously, they will cause these weights to "spread". This spread will be greater than the speed of the aircraft multiplied by the deployment time of all systems (often a kilometer of distance).
Existing and proposed systems
The landing phase is particularly influenced by the ballistic trajectory of the parachute system, the effect of winds on this trajectory, and any ability to control the canopy. Trajectories are estimated and provided to aircraft manufacturers for input into an onboard computer for CARP calculation.
However, in order to reduce the errors of the ballistic trajectory, new models are being developed. Many NATO Allies are investing in Precision Dropping Systems / Technologies and many more would like to start investing in order to meet NATO and national Precision Dropping standards.
Joint Precision Air Drop System (JPADS)
Accurate dropping does not allow you to “have one system that fits everything” because the weight of the load, the difference in height, the accuracy and many other requirements vary greatly. For example, the US Department of Defense is investing in numerous initiatives under a program known as the Joint Precision Air Drop System (JPADS). JPADS is a controlled high precision air drop system that significantly improves accuracy (and reduces dispersion).
After dropping to high altitude, JPADS uses GPS and guidance, navigation and control systems to accurately fly to a designated point on the ground. Its gliding parachute with a self-filling shell allows it to land at a considerable distance from the drop point, while the guidance of this system allows high-altitude drops to one or multiple points simultaneously with an accuracy of 50 - 75 meters.
Several US allies have shown interest in JPADS systems, while others are developing their own systems. All JPADS products from a single vendor share a common software platform and user interface in stand-alone targeting devices and task scheduler.
HDT Airborne Systems offers systems ranging from MICROFLY (45 - 315 kg) to FIREFLY (225 - 1000 kg) and DRAGONFLY (2200 - 4500 kg). FIREFLY won the US JPADS 2K / Increment I competition and DRAGONFLY won the £ 10,000 class. In addition to the systems named, MEGAFLY (9,000 - 13,500 kg) set the world record for the largest self-filling canopy ever to take off until it was broken in 2008 by the even larger GIGAFLY 40,000 pound system. Earlier this year, it was announced that HDT Airborne Systems had won a $ 11.6 million fixed price contract for 391 JPAD systems. The work under the contract was carried out in the city of Pennsoken and ended in December 2011.
MMIST offers SHERPA 250 (46 - 120 kg), SHERPA 600 (120 - 270 kg), SHERPA 1200 (270 - 550 kg) and SHERPA 2200 (550 - 1000 kg). These systems were purchased by the US and are used by the US Marines and several NATO countries.
Strong Enterprises offers the SCREAMER 2K in the 2000lb class and the Screamer 10K in the 10000lb class. She has worked with Natick Soldier Systems Center on JPADS since 1999. In 2007, the company had 50 of its 2K SCREAMER systems operating on a regular basis in Afghanistan, with another 101 systems ordered and delivered by January 2008.
Boeing's Argon ST subsidiary has been awarded an unspecified $ 45 million contract for the purchase, testing, delivery, training and logistics of JPADS Ultra Light Weight (JPADS-ULW). JPADS-ULW is an aircraft deployable canopy system that is capable of delivering 250 to 699 pounds of cargo safely and efficiently from altitudes up to 24,500 feet above sea level. The work will be carried out in Smithfield and is expected to be completed in March 2016.
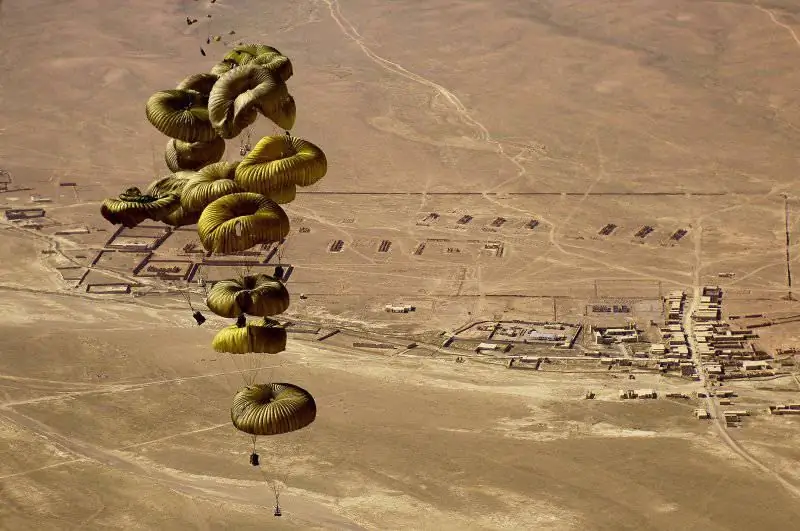
Forty bales of humanitarian aid dropped from C-17 using JPADS in Afghanistan
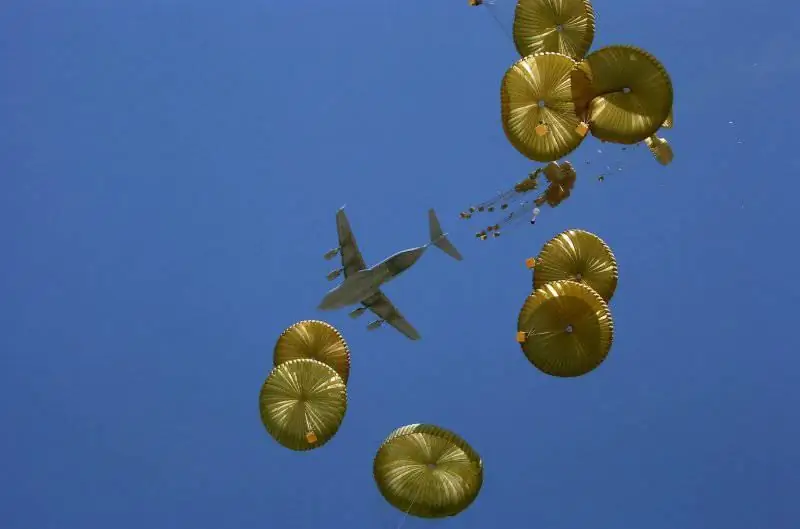
C-17 Drops Cargo to Coalition Forces in Afghanistan Using Advanced Air Delivery System with NOAA LAPS Software
SHERPA
SHERPA is a cargo delivery system consisting of commercially available components manufactured by the Canadian company MMIST. The system consists of a timer-programmed small parachute that deploys a large canopy, a parachute control unit and a remote control unit.
The system is capable of delivering 400 - 2200 pounds of cargo using 3-4 paragliders of different sizes and the AGU air guidance device. A mission can be scheduled for SHERPA prior to flight by entering the coordinates of the intended landing point, available wind data, and cargo characteristics.
SHERPA MP software uses the data to create a task file and calculate the CARP in the drop area. After being dropped from an aircraft, the Sherpa pilot chute - a small, round stabilizing parachute - is deployed using an exhaust lanyard. The pilot chute attaches to a release trigger, which can be programmed to operate at a preset time after the parachute is deployed.
SCREAMER
The SCREAMER concept was developed by the American company Strong Enterprises and was first introduced in early 1999. The SCREAMER system is a hybrid JPADS that uses a pilot chute for controlled flight throughout the vertical descent and uses conventional, circular non-steered canopies for the final phase of flight. Two options are available, each with the same AGU. The first system has a lifting capacity of 500 - 2,200 lbs, the second has a lifting capacity of 5,000 - 10,000 lbs.
SCREAMER AGU is supplied by Robotek Engineering. The 500 - 2200 lb SCREAMER system uses a 220 square meter self-filling parachute. ft as flue with loads up to 10 psi; the system is capable of passing through most of the harshest wind currents at high speed. The SCREAMER RAD is controlled either from a ground station or (for military applications) during the initial phase of flight with a 45 lb AGU.
DRAGONLY 10,000lb Paragliding System
HDT Airborne Systems' DRAGONFLY, which is a fully autonomous GPS-guided cargo delivery system, has been selected as the preferred system for the US 10,000-lb Joint Precision Air Delivery System (JPADS 10k) program. Characterized by a braking parachute with an elliptical canopy, it has repeatedly demonstrated the ability to land within a radius of 150 m from the intended rendezvous point. Using only point of touch data, the AGU (Airborne Guidance Unit) calculates its position 4 times per second and continually adjusts its flight algorithm to ensure maximum accuracy. The system features a 3.75: 1 slip ratio for maximum displacement and a unique modular system that allows the AGU to be charged while the canopy is being folded, thus reducing the cycle time between drops to less than 4 hours. It comes standard with the Mission Planner from HDT Airborne Systems, which is capable of performing simulated missions in a virtual operational space using mapping software. Dragonfly is also compatible with the existing JPADS Mission Planner (JPADS MP). The system can be pulled out immediately after exiting an aircraft or gravitationally falling using a conventional G-11 pull kit with one standard pull line.
The DRAGONFLY system was developed by the JPADS ACTD group of the US Army's Natick Soldiers Center in collaboration with Para-Flite, the developer of the braking system; Warrick & Associates, Inc., developer of AGU; Robotek Engineering, an avionics supplier; and Draper Laboratory, GN&C software developer. The program began in 2003 and flight tests of the integrated system began in mid-2004.
Affordable Guided Airdrop System (AGAS)
The AGAS system from Capewell and Vertigo is an example of a JPADS with a controlled circular parachute. AGAS is a joint development between the contractor and the US government that began in 1999. It uses two actuators in the AGU, which are positioned in line between the parachute and the cargo container and which use the opposite free ends of the parachute to control the system (i.e. the glide of the parachute system). The four riser tiller can be operated individually or in pairs, providing eight directions of control. The system needs an accurate wind profile that it will encounter over the discharge area. Before dropping, these profiles are loaded into the AGU on-board flight computer in the form of a planned trajectory that the system "follows" during descent. The AGAS system is able to adjust its position by means of lines all the way to the point of contact with the ground.
ONYX
Atair Aerospace developed the ONYX system for the US Army's SBIR Phase I contract for 75 pounds and was scaled up by ONYX to achieve a payload of 2,200 pounds. The guided 75-pound ONYX parachute system divides guidance and soft landing between two parachutes, with a self-inflating guidance shell and a ballistic circular parachute opening above the rendezvous point. The ONYX system has recently included a herd algorithm, allowing in-flight interaction between systems during a mass drop.
Small Parafoil Autonomous Delivery System (SPADES)
SPADES is being developed by the Dutch company in collaboration with the national aerospace laboratory in Amsterdam with the support of the French parachute manufacturer Aerazur. The SPADES system is designed for the delivery of goods weighing 100-200 kg.
The system consists of a 35 m2 paragliding parachute, a control unit with an on-board computer and a cargo container. It can be dropped from an altitude of 30,000 feet at a distance of up to 50 km. It is autonomously controlled by GPS. Accuracy is 100 meters when dropped from 30,000 feet. SPADES with a 46 m2 parachute delivers goods weighing 120 - 250 kg with the same precision.
Free fall navigation systems
Several companies are developing personal navigation assisted air release systems. They are mainly intended for high-altitude high opening (HAHO) parachute drops. HAHO is a high altitude drop with a parachute system deployed upon exiting the aircraft. It is expected that these free-fall navigation systems will be able to direct special forces to the desired landing points in bad weather conditions and increase the distance from the drop point to the limit. This minimizes the risk of detection of the invading unit as well as the threat to the delivery aircraft.
The Marine Corps / Coast Guard Free Fall Navigation System has gone through three prototyping phases, all phases directly ordered from the US Marine Corps. The current configuration is as follows: fully integrated civil GPS with antenna, AGU and aerodynamic display mountable to parachutist helmet (manufactured by Gentex Helmet Systems).
EADS PARAFINDER provides the military parachutist in free fall with improved horizontal and vertical displacement (deflection) (i.e., when displaced from the point of landing of the dropped cargo) in order to achieve his main target or up to three alternative targets in any environment. The parachutist puts the helmet-mounted GPS antenna and the processor unit on his belt or pocket; the antenna provides information to the parachutist's helmet display. The helmet display shows the skydiver the current heading and the desired course based on the landing plan (i.e. airflow, drop point, etc.), current altitude and location. The display also shows recommended control signals indicating which line to pull in order to travel to a 3D point in the sky along the ballistic windline generated by the mission planner. The system has a HALO mode that guides the skydiver towards the landing point. The system is also used as a navigation tool for the landed parachutist to guide him to the gathering point of the group. It is also designed for use in limited visibility and to maximize the distance from the point of jump to the point of landing. Limited visibility can be due to bad weather, dense vegetation, or during night jumps.
conclusions
Since 2001, precision airdrops have developed rapidly and are likely to become more common in military operations for the foreseeable future. Precision Dropping is a high priority short term counterterrorism requirement and a long term LTCR requirement within NATO. Investments in these technologies / systems are growing in NATO countries. The need for precision dropping is understandable: we must protect our crews and transport aircraft by enabling them to avoid ground threats while delivering supplies, weapons and personnel precisely across a widely dispersed and rapidly changing battlefield.
Improved aircraft navigation using GPS has increased the accuracy of drops, and weather forecasting and direct measurement techniques provide significantly more accurate and better weather information to crews and mission planning systems. The future of precision airdrops will be based on controlled, high-altitude deployable, GPS guided, efficient airborne airborne systems that take advantage of advanced mission planning capabilities and can provide an accurate amount of logistics to the soldier at an affordable cost. The ability to deliver supplies and weapons anywhere, at any time and in almost all weather conditions will become a reality for NATO in the very near future. Some of the affordable and rapidly developing national systems, including those described in this article (and others like them), are currently being applied in small quantities. Further improvements, enhancements and upgrades to these systems can be expected in the coming years, as the importance of delivering materials anytime, anywhere is critical to all military operations.
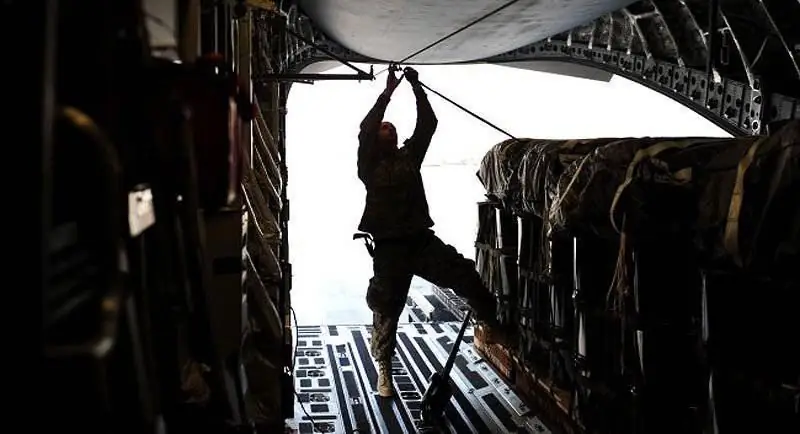
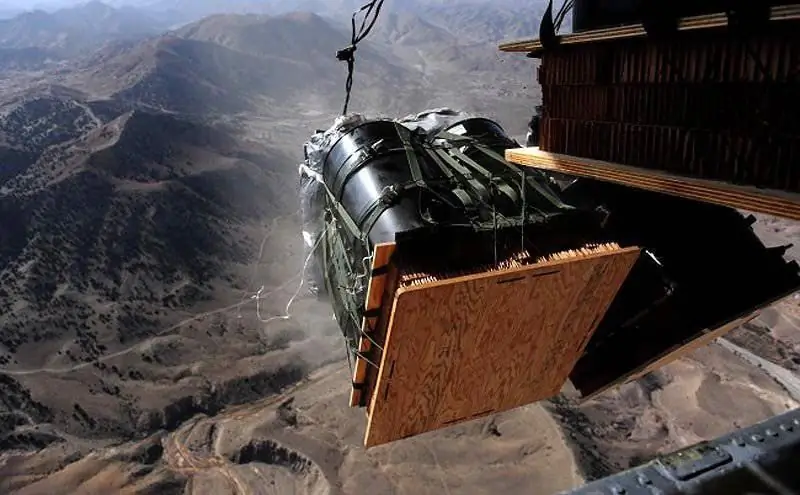
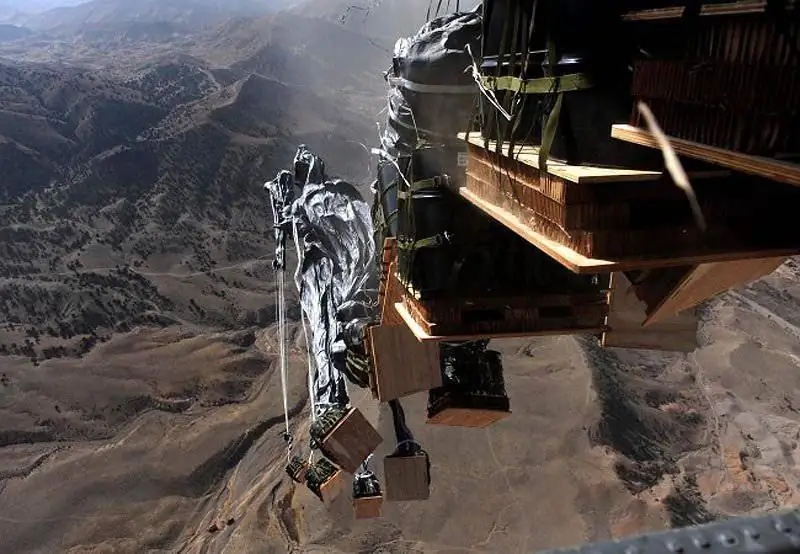
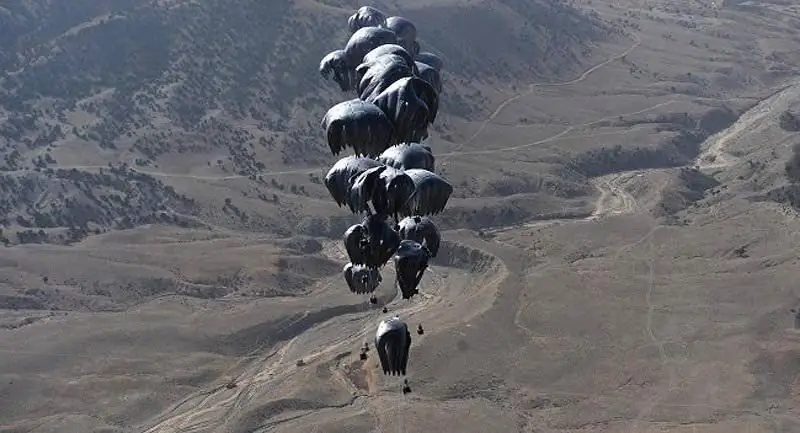
US Army riggers at Fort Bragg assemble fuel containers before being dropped during Operation Enduring Freedom. Then forty containers with fuel fly out of the GLOBEMASTER III cargo hold