The practice of attracting other people's developments for the development of their own technological capacities, which we talked about in the first part of the story, was widespread in tsarist Russia.
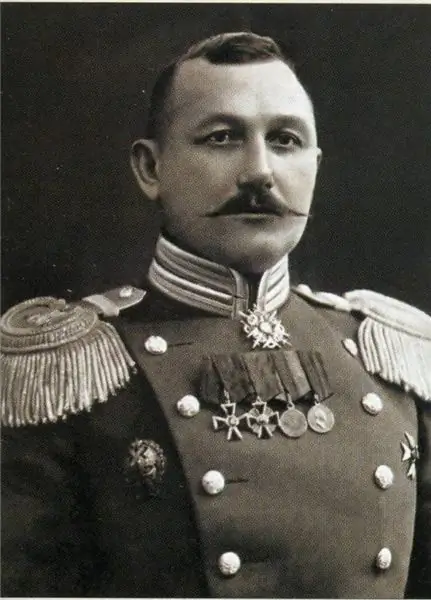
Consider an example of supplying the Russian army with scarce vehicles. By August 1914, the Russian Empire had just over 700 vehicles used for the needs of the military. The Russian-Baltic Carriage Works could produce no more than 130 cars per year, while the overwhelming majority of them were passenger cars that were little demanded by the army. As a result, a few years later, I had to turn to Western colleagues for help, whose automobile industry was much more perfect. The procurement commission under the leadership of the commander of the spare automobile company, Colonel Pyotr Ivanovich Sekretev, went to Great Britain in September 1914 to replenish the army with new equipment.
We planned to buy trucks, cars, special equipment, as well as armored cars. It is noteworthy that among the special requirements of the Russian commission was the presence of an armored roof and two machine guns rotating in different towers. At that time, neither France nor England could offer anything of the kind in a finished form, and only with Austin Motor, Peter Sekretev's team managed to agree on the development of an armored car of the required design. In fact, only 48 Austins met the requirements of the Russian army - in France they already had to buy what they had. And there were only 40 armored "Renault" with an open roof and a single machine gun.
Why does this story precede the story of the tank building of the Soviet period? It allows us to understand the fundamental difference in the approaches of the government of Nicholas II and the young Soviet republic. If in the first case the main goal was to simply saturate the catastrophically lagging army with military equipment, then in the USSR they tried to purchase technologies and samples worthy of borrowing, and sometimes even outright copying. And if we compare the effectiveness of the missions of Innokenty Khalepsky (his team went to buy armored vehicles for the USSR in 1929, as the first part of the story told about) and Peter Sekretev, it turns out that the tsarist colonel was much more "successful" - in total, 1422 vehicles were purchased in Europe … However, no attempts were made to reduce the qualitative and quantitative lag behind the West in automotive technology in tsarist Russia.
The mastery of armored vehicles acquired in the United States and Europe in the Soviet Union proceeded with a creak - there was not enough qualified specialists or the appropriate technological equipment. A separate problem was the deliberately impracticable tasks that the country's leadership played off in front of the factories. What was the reason for this? First of all, with the urgent need to mobilize military production - most developed foreign countries viewed the young Soviet republic as a dangerous breeding ground for the "communist plague." Also, one cannot discount the special approach of the USSR leadership to the formation of work plans. Stalin once wrote to Voroshilov about this:
“… In terms of tanks and aviation, the industry has not yet managed to properly re-equip in relation to our new assignments. Nothing! We will press and help - they will adapt. It's all about keeping well-known industries (mainly the military) under constant control. They will adapt and will carry out the program, if not 100%, then 80-90%. Isn't that enough?"
The results of this approach were constant disruptions of the state defense order, a high proportion of manufacturing defects, as well as an emergency mode of operation. Naturally, for non-fulfillment of unattainable plans in advance, the relevant structures were looking for and found guilty with all the ensuing consequences.
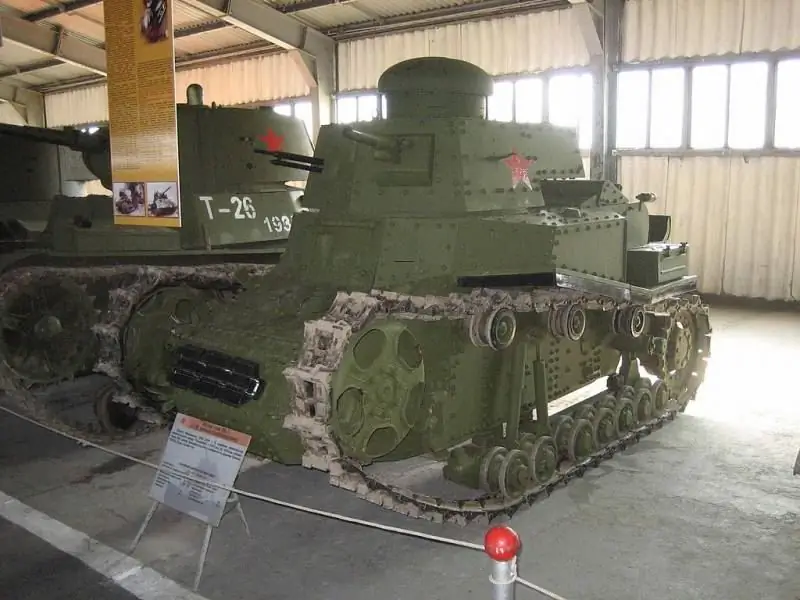
In this regard, the history of mastering the production of the T-18 (MS-1) tank at the Bolshevik plant in Leningrad in the first half of 1927 will be very remarkable.
The site for the assembly of the modernized version of the French Renault FC-1, the design of which refers us to the times of the First World War, was not chosen by chance. Before that, aircraft engines and tractors had already been made on the Bolshevik, and there was no experience. It was here in a special workshop that the first specialized tank production in the USSR appeared, which was later transformed into plant No. 174 named after K. E. Voroshilov. However, a special tank shop was built only by the end of 1929, and before that the T-18 had to be assembled virtually on the knee - on extremely worn out equipment from the Tsarist times. In 1927-1928. We were able to produce only 23 tanks using this bypass technology, and 85 more vehicles were added for the next financial year with a great delay. The authorities did not like such a pace, and it was decided to transfer part of the production of tanks to Perm, to the Motovilikhinsky machine-building plant, which had previously been engaged in cannon production.
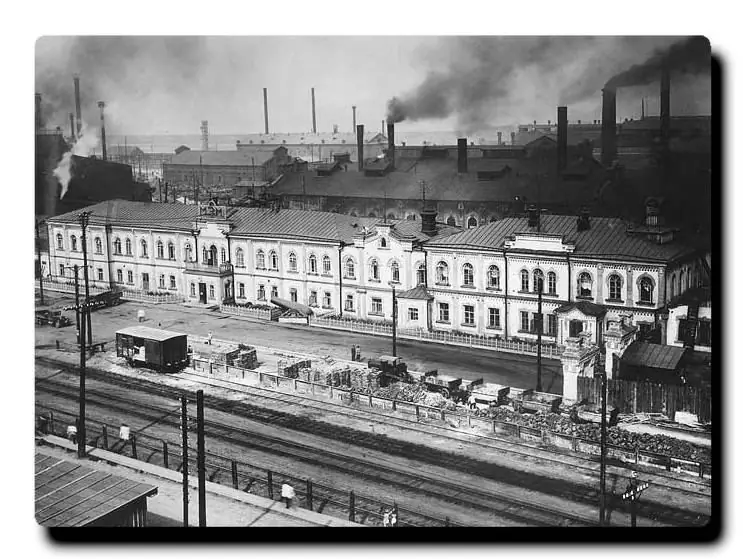
But due to the "small number of technical personnel for tank building" nothing sensible came of this. They realized this only in 1931, when the Revolutionary Military Council decided:
"Do not give more tank orders to Motovilikha."
The OGPU realized this even earlier and began to act. In the case of sabotage, the head of the Main Military-Industrial Directorate, Vadim Sergeevich Mikhailov, was arrested, who had the rank of Major General even before the revolution. Together with him, by October 1929, 91 people were under investigation, who were accused of founding a counter-revolutionary organization aimed at disrupting the country's defense by sabotaging the military industry. Five persons under investigation, including V. S. Mikhailov, were shot, the rest were given various terms of imprisonment. In fact, since the end of the 20s, the fight against sabotage in the military industry in general and in tank building in particular has become an integral part of the emergence of a young industry. And this topic, of course, requires a separate study and narration.
Inch to meter
The most serious problem in mastering the production of "creatively rethought" samples of foreign technology was the conversion of the inch measurement system to the metric one. Firstly, it was a long process, taking a lot of time under the conditions of a constant race for quantity. And secondly, even if the recalculation was performed correctly, there were still errors. It was necessary to convert inches to metric units with rounding up or down, which, of course, affected the quality of manufacturing of units and parts. Tank builders, when mastering the production of BT series tanks, initially decided not to translate drawings into centimeters and millimeters to save time. This was largely due to the serious problems that engineers faced when mastering the production of the first T-26 series. With this machine, which was based on the base of the 6-ton "Vickers", in general there were many difficulties. The first copies came out of the Leningrad plant in 1931, while the government initially put half a thousand armored vehicles in the plan for the year. Naturally, it was impossible to collect such a gigantic volume, so the bar was lowered to 300 tanks, which were also not assembled. Adjacent enterprises did not keep pace with the supply of components, and the first fifteen T-26s were welded from ordinary steel - the Izhora plant was unable to produce high-quality armor. An armor-piercing rifle bullet penetrated such a tank from a distance of 200 meters. When at the beginning of 1932 they raided the Izhora plant with a check, it turned out that the percentage of rejects during cementation of armor plates reached 90%! The failure also happened with optical devices - in the domestic industry of that time there was simply no technology for the production of analogs of British sights. Therefore, we decided to install conventional mechanical guidance devices. Tank motors were also a weak point in the production chain, which forced them to buy again from the British. At the same time, the cost of the first Soviet-made T-26s was twice the price of those purchased in Great Britain! As a result, all 15 of the first "unarmored" tanks were left as teaching aids for tank schools, and in total until the end of 1931 it was possible to assemble 120 vehicles, of which only 100 were allowed for military operation. The management team traditionally attributed the lion's share of all production shortcomings to the subversive activities of enemies of the people and sabotage. On the other hand, the tank industry in general and the Voroshilov Leningrad Plant in particular received expensive foreign machines in the first place. This was often done to the detriment of the equipment of civilian enterprises.
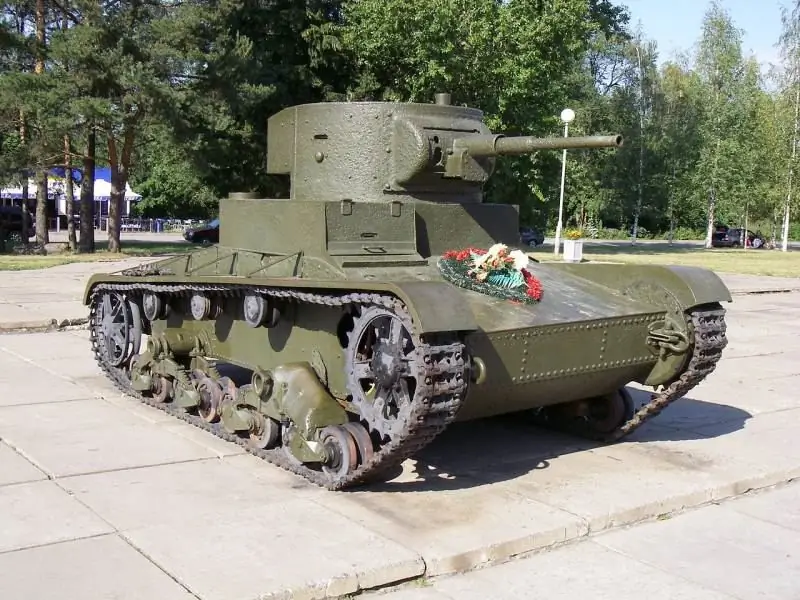
But the further history of the Voroshilov plant, where the light T-26 was also produced, cannot boast of high quality products. In April 1934, the proportion of defects in the crankcase of the T-26 engine reached 60%, and the pistons were defective in half of the cases. At the beginning of 1937, none of the tested engines could work out the warranty period (100 hours on the stand and 200 hours on the tank), which even forced the military representative to stop accepting products. For five months of the same year, the plant produced only 17 light tanks instead of the planned 500 vehicles. It is noteworthy that somewhere in this period, formulations about sabotage as the main reason for production defects began to disappear from the plant's documentation. However, the problems remained and they had to be solved in the shortest possible time.