The fact of the existence of a bathyscaphe, which managed to conquer the deepest abyss, testifies to the technical possibility of creating manned vehicles for diving to any depth.
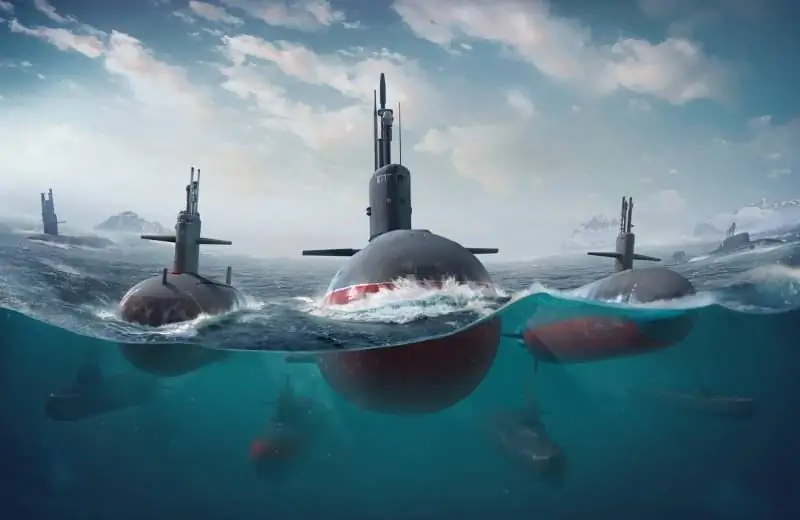
Why is none of the modern submarines even close to being able to dive - even 1000 meters?
Half a century ago, the bathyscaphe, assembled from the improvised means of standard steel and plexiglass, reached the bottom of the Mariana Trench. And I could continue my dive if there were great depths in nature. The safe design depth for Trieste was 13 kilometers!
More than 3/4 of the area of the World Ocean falls on the abyssal zone: an ocean bed with depths of over 3000 m. Genuine operational space for the submarine fleet! Why isn't anyone taking advantage of these opportunities?
The conquest of great depths has nothing to do with the strength of the hull of the "Sharks", "Boreyev" and "Virginia". The problem is different. And the example with the bathyscaphe "Trieste" has absolutely nothing to do with it.
They are similar, like an airplane and an airship
Bathyscaphe is a "float". Tank car with gasoline, with a crew gondola fixed under it. When ballast is taken on board, the structure acquires negative buoyancy and sinks into depth. When ballast is dropped, it returns to the surface.
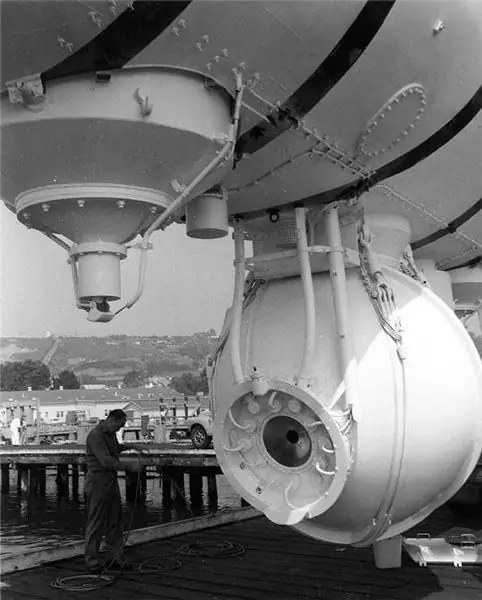
Unlike bathyscaphes, submarines need to repeatedly change the depth of being under water during one dive. In other words, the submarine has the ability to repeatedly change the buoyancy reserve. This is achieved by filling ballast tanks with seawater, which are blown through with air when surfacing.
There are three air systems commonly used on boats: high pressure air (HPP), medium pressure (HPA) and low pressure air (HPP). For example, on modern American nuclear-powered ships, compressed air is stored in cylinders at 4,500 psi. inch. Or, humanly, about 315 kg / cm2. However, none of the compressed air consuming systems uses VVD directly. Sudden pressure drops cause intense freezing and blockage of the valves, at the same time creating the danger of compression bursts of oil vapors in the system. The widespread use of VVD under pressure over 300 atm. would create unacceptable hazards aboard the submarine.
VVD through a system of pressure reducing valves is supplied to consumers in the form of VVD under a pressure of 3000 lb. per sq. inch (approximately 200 kg / cm2). It is with this air that the main ballast tanks are blown. To ensure the operation of the other mechanisms of the boat, launching weapons, as well as blowing trim and equalizing tanks, "working" air is used at an even lower pressure of about 100-150 kg / cm2.
And this is where the laws of drama come into play!
With a dive into the sea depths for every 10 meters, the pressure increases by 1 atmosphere
At a depth of 1500 m, the pressure is 150 atm. At a depth of 2000 m, the pressure is 200 atm. This exactly corresponds to the maximum value of IRR and IRR in submarine systems.
The situation is aggravated by the limited volumes of compressed air on board. Especially after the boat has been under water for a long time. At a depth of 50 meters, the available reserves may be sufficient to displace water from ballast tanks, but at a depth of 500 meters, this is only enough to blow through 1/5 of their volume. Deep depths are always a risk, and one must proceed with the utmost caution.
Nowadays, there is a practical possibility of creating a submarine with a hull designed for a diving depth of 5000 meters. But blowing the tanks at such a depth would require air under a pressure of over 500 atmospheres. Designing pipelines, valves and fittings designed for this pressure, while maintaining their reasonable weight and eliminating all associated hazards, is today a technically insoluble task.
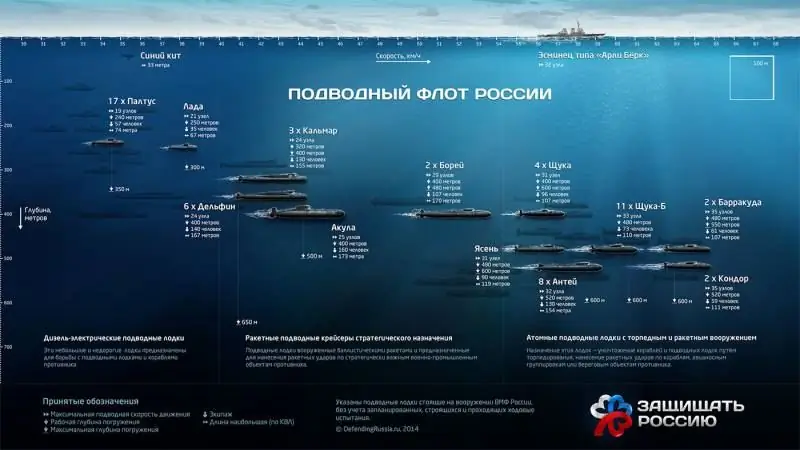
Modern submarines are built on the principle of a reasonable balance of performance. Why build a high-strength hull that can withstand the pressure of a kilometer-long water column when surfacing systems are designed for much shallower depths? Having sunk a kilometer, the submarine will be doomed in any case.
However, this story has its own heroes and outcasts.
American submariners are considered traditional outsiders in the field of deep-sea diving
For half a century, the hulls of American boats have been made from a single HY-80 alloy with very mediocre characteristics. High-yield-80 = 80,000 psi high yield alloy inch, which corresponds to the value of 550 MPa.
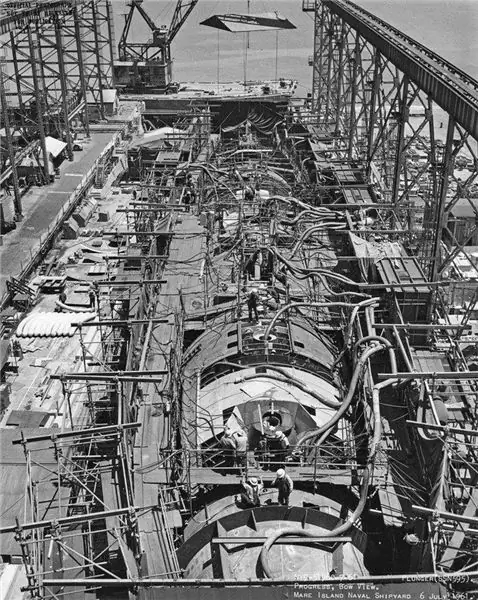
Many experts express doubts about the adequacy of such a solution. Due to the weak hull, the boats are unable to fully exploit the capabilities of the ascent systems. Which allow blowing of tanks at much greater depths. It is estimated that the working submersion depth (the depth at which the boat can be for a long time, making any maneuvers) for American submarines does not exceed 400 meters. The maximum depth is 550 meters.
The use of HY-80 allows to reduce the cost and speed up the assembly of hull structures, among the advantages have always been called the good welding qualities of this steel.
For the ardent skeptics, who will immediately declare that the fleet of the "potential enemy" is massively replenished with non-combatable trash, the following should be noted. Those differences in the rates of shipbuilding between Russia and the United States are due not so much to the use of higher-quality steel grades for our submarines, as to other circumstances. Anyway.
Overseas, it has always been believed that superheroes are not needed. Underwater weapons should be as reliable, quiet and numerous as possible. And there is some truth in this.
Komsomolets
The elusive "Mike" (K-278 according to NATO classification) set an absolute record for diving depth among submarines - 1027 meters.
The maximum immersion depth of the "Komsomolets" according to calculations was 1250 m.
Among the main design differences, unusual for other domestic submarines, there are 10 kingstonless tanks, located inside a durable hull. Possibility of firing torpedoes from great depths (up to 800 meters). Pop-up escape pod. And the main highlight is the emergency system for blowing the tanks with the help of gas generators.
The body made of titanium alloy made it possible to realize all the inherent advantages.
Titanium itself was not a panacea for conquering the depths of the sea. The main thing in the creation of the deep-water Komsomolets was the build quality and the shape of a solid hull with a minimum of holes and weak points.
Titanium alloy 48-T with a yield strength of 720 MPa only slightly surpassed the structural steel HY-100 (690 MPa) in strength, from which the SeaWolf submarines were made.
The other described "advantages" of the titanium case in the form of low magnetic properties and its lower susceptibility to corrosion were not in themselves worth the investment. Magnetometry has never been a priority method for detecting boats; under water, everything is decided by acoustics. And the problem of marine corrosion has been solved for two hundred years by simpler methods.
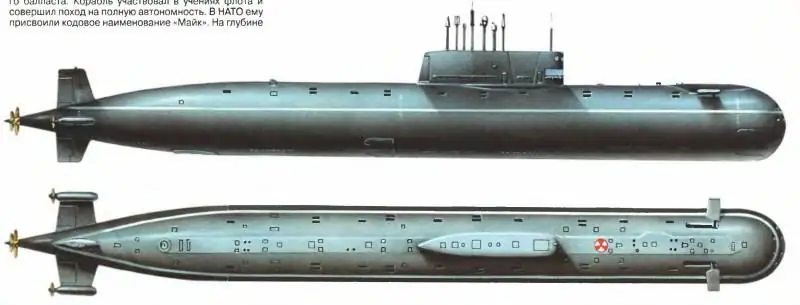
Titanium from the point of view of domestic submarine shipbuilding had TWO real advantages:
a) less density, which meant a lighter body. The emerging reserves were spent on other load items, for example, power plants of greater power. It is no coincidence that submarines with a titanium hull (705 (K) "Lira", 661 "Anchar", "Condor" and "Barracuda") were built as conquerors of speed.;
b) Among all high-strength steels and alloys titanium alloy 48-T turned out to be the most technologically advanced in the processing and assembly of hull structures.
"Most technologically advanced" does not mean simple. But the welding qualities of titanium at least allowed the assembly of structures.
Overseas had a more optimistic view of the use of steels. For the manufacture of hulls for new submarines of the XXI century, high-strength steel of the HY-100 brand was proposed. In 1989, the United States laid the foundation for the lead SeaWolfe. After two years, optimism has dwindled. The SeaWolfe hull had to be taken apart and started anew.
Many problems have now been resolved, and steel alloys equivalent in properties to HY-100 are finding wider applications in shipbuilding. According to some reports, such a steel (WL = Werkstoff Leistungsblatt 1.3964) is used in the manufacture of a durable hull of German non-nuclear submarines "Type 214".
There are even stronger alloys for the construction of housings, for example, steel alloy HY-130 (900 MPa). But because of the poor welding properties, shipbuilders considered the use of the HY-130 impossible.
No news from Japan yet.
耐久 means yield strength
As the old saying goes, "Whatever you do well, there is always an Asian who does it better."
There is very little information in open sources about the characteristics of Japanese warships. However, experts are not stopped by the language barrier or the paranoid secrecy inherent in the second-strongest navy in the world.
From the available information, it follows that samurai, along with hieroglyphs, widely use English designations. In the description of the submarines, there is an abbreviation NS (Naval Steel - naval steel), combined with digital indices 80 or 110.
In the metric system, "80" when designating a steel grade most likely means a yield strength of 800 MPa. The stronger steel NS110 has a yield strength of 1100 MPa.
From an American point of view, the standard steel for Japanese submarines is the HY-114. Better quality and more durable - HY-156.
Mute scene
"Kawasaki" and "Mitsubishi Heavy Industries" without any loud promises and "Poseidons" learned to make hulls from materials that were previously considered incompatible and impossible in the construction of submarines.
The given data correspond to obsolete submarines with an air-independent installation of the "Oyashio" type. The fleet consists of 11 units, of which the two oldest, which entered service in 1998-1999, were transferred to the category of training units.
"Oyashio" has a mixed double-hull design. The most logical assumption is that the central section (strong hull) is made of the most durable steel NS110, a double-hull design is used in the bow and stern of the boat: a light streamlined shell made of NS80 (pressure inside = outside pressure), covering the main ballast tanks outside the strong hull. …
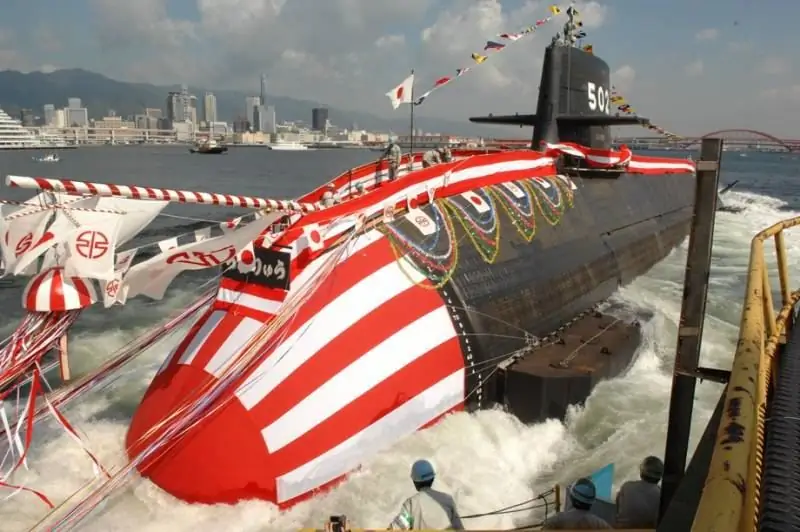
Modern Japanese submarines of the "Soryu" type are considered improved "Oyashio" while retaining the basic design solutions inherited from their predecessors.
With its robust NS110 steel hull, Soryu's working depth is estimated to be at least 600 meters. The limit is 900.
Taking into account the circumstances presented, the Japanese Self-Defense Forces currently have the deepest fleet of combat submarines.
The Japanese "squeeze" everything possible from the available. Another question is how much this will help in a naval conflict. For confrontation in the depths of the sea, a nuclear power plant is required. The pitiful Japanese "half measures" with increasing the working depth or creating a "battery-powered boat" (the Oryu submarine that surprised the world) looks like a good face for a bad game.
On the other hand, traditional attention to detail has always allowed the Japanese to have an edge over the enemy. The emergence of a nuclear power plant for the Japanese Navy is a matter of time. But who else in the world has technologies for manufacturing ultra-strong cases made of steel with a yield strength of 1100 MPa?