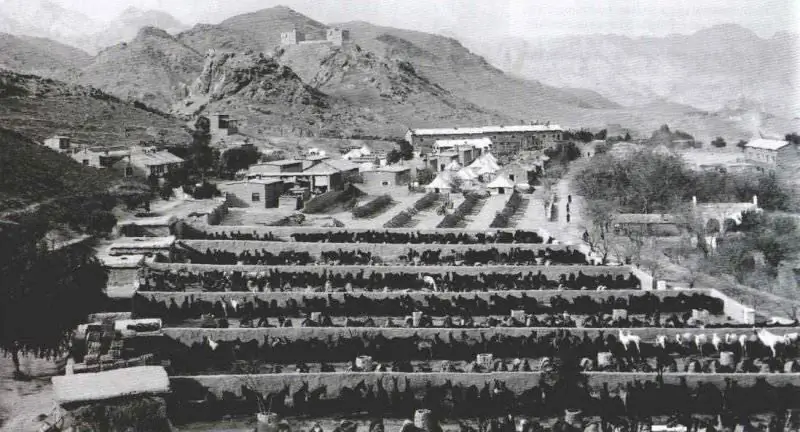
Eeyore Donkey Days. Mules of a pack transport company from the Indian service corps in the mid-30s at a base in what is now Pakistan
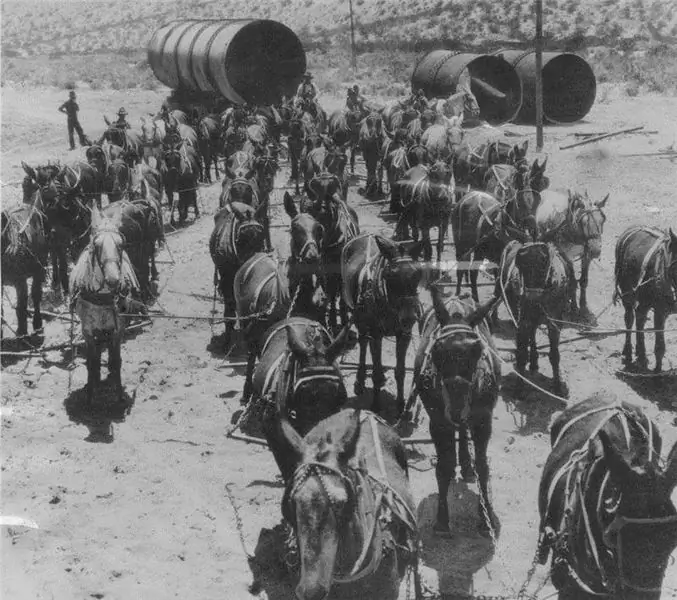
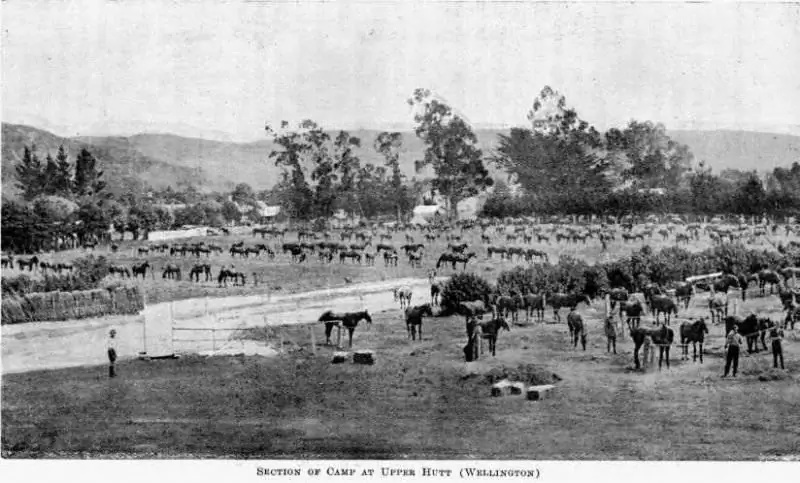
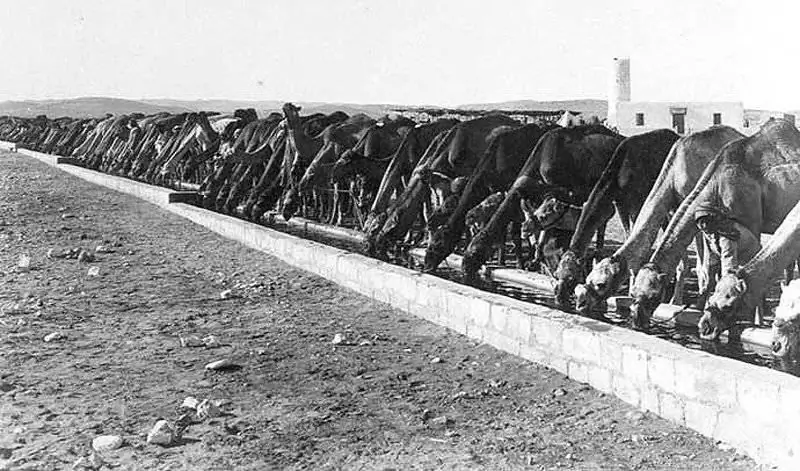
For centuries, beasts of burden of various types and subspecies have been used in military operations. As we can see in the archival photos, these are horses, mules and camels.
Today, animal-drawn transport is mainly in demand by insurgents who are prepared for the slow movement of animals, unpredictability and a significant amount of material and human resources in exchange for low cost and incredible adaptability to the environment.
For the world's leading armed forces, the presence of manned helicopters and all-terrain supply vehicles has been mandatory in combat areas since the 1960s. Despite the advantages in speed and carrying capacity that they have over other methods of transporting goods, they are not always suitable for the material and technical supply of hostilities, they are affected by cost, availability, terrain, vulnerability or banal caution. On the contrary, automatic supply systems are becoming more intelligent in connection with the need to reduce the negative impact of the combat load
In today's asymmetrical battlefield, insurgents still eagerly use time-honored, non-mechanized, inhuman logistics tools such as pack caravans, while acknowledging their unpredictability and the fact that they carry a large logistical burden of their own. On the other hand, it seems that the world's leading armies are least willing to turn back the clock, preferring to explore inanimate solutions in which, ironically, mechanical analogs of mammals costing millions of dollars can be found.
With a high degree of probability, one day such inanimate supply systems could simply be abandoned, viewed as "intricate and fun" technology suitable only for home use. However, in recent decades, the use of robotic technologies has gradually expanded in the defense sector, and now uninhabited mechanical systems are considered as potential means that reduce the need for human resources and save lives in the field of logistics (and in any other too).
Initially, these systems were interested at the command level, mainly for reasons of protecting their forces and saving manpower. Currently, however, heightened interest is also manifested at the user level, where a lot of experience has been accumulated of the direct negative influence of the mass of military equipment that a dismounted soldier must carry on a daily basis in a theater of operations, for example, in Afghanistan. If a soldier's capabilities on the battlefield are not to be diminished by excess weight to carry, then some form of mechanical assistance appears to be in dire need.
Ground-based automatic systems could, at a minimum, save lives and provide supply routes in the disputed territory. The additional "muscle power" they provide could also enhance the planned firepower and combat resilience of infantry units on the front lines. To these could be added power-driven unmanned air supply systems, most likely in the form of unmanned helicopters. This is, for example, the Marine Corps project for a promising cargo UAV (Cargo UAS) or missiles in a vertical launch container similar to the NLOS-T (Non-Line of Sight-Transport) missiles of the American army, which offer potentially other ways bypassing ambushes and directed landmines through the use of the "third dimension".
With a constant shortage of manpower and demands for border protection, the Israeli army was among the first to adopt an unmanned patrol platform in the form of the Guardium Automatic Ground Vehicle (ANA). It was developed by G-NIUS, a joint venture between Elbit and Israel Aerospace Industries (IAI). The range of missions voiced for the Guardium includes patrolling, route checking, convoy security, reconnaissance and surveillance, and direct support of hostilities. In its basic configuration, the vehicle is based on the TomCar 4x4 off-road vehicle, 2.95 m long, 2.2 m high, 1.8 m wide and 300 kg payload. The maximum speed in semi-autonomous mode is 50 km / h.
In September 2009, G-NIUS showed off the Guardium-LS, a longer version optimized for logistics. It is based on the TM57 chassis and is similar to the vehicle adopted by the British Army as the main company-level manned supply platform called the Springer. The length of the Guardium-LS is 3.42 m, it has an increased carrying capacity of up to 1.2 tons (including towed load). It can operate in controlled or automatic modes, has the same set of systems as its predecessor in the patrol version, including the Elbit / Elisra EJAB warhead suppressor; optoelectronic station IAI Tamam Mini-POP, consisting of a thermal imager, a daytime CCD camera and an eye-safe laser rangefinder; GPS navigation system; laser sonar (LIDAR) for avoiding obstacles; and stereoscopic cameras. It also has "pursuit" sensors that automatically follow the directions of a person or other vehicles in a convoy.
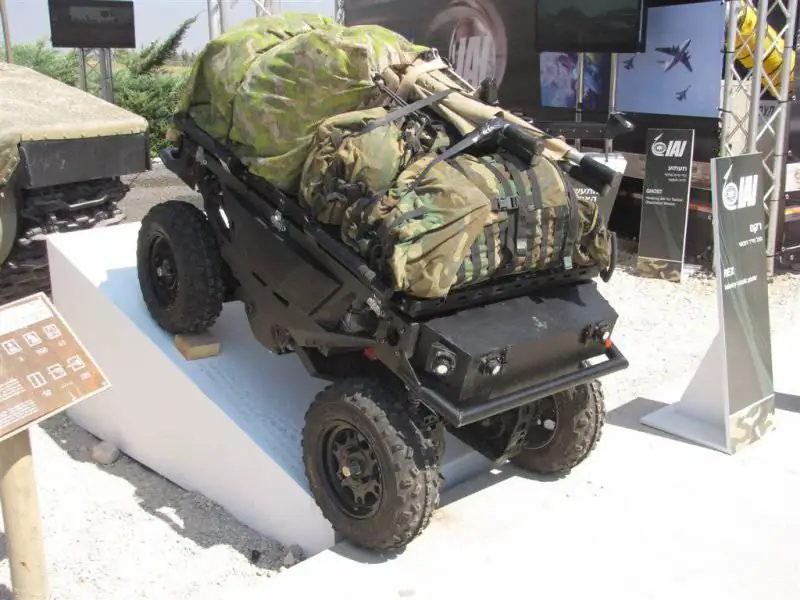
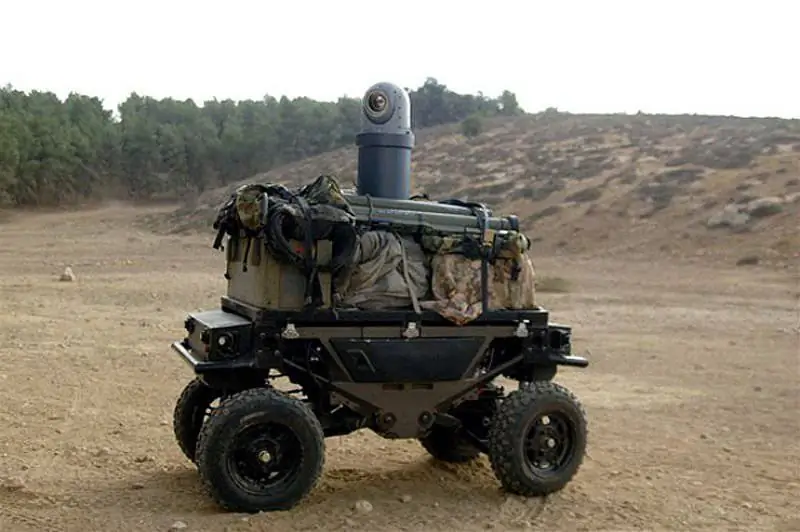
IAI's “field porter” Rex is designed to carry 200 kg of equipment, without refueling can work for three days
Direct support of hostilities
Another potential military logistics assistant from the G-NIUS family is the AvantGuard, currently also in service with the Israeli army. It uses Guardium control technology, but the platform is a modification of the Canadian company's Wolverine tracked vehicle. It is smaller and is designated Dumur TAGS (tactical amphibious ground support platform). The four-wheeled vehicle is powered by a four-cylinder 100 hp Kubota V3800DI-T diesel engine, has a top speed of 19 km / h and can be operated either in semi-automatic mode or controlled from a wearable remote control. Its weight is 1746 kg, payload is 1088 kg, it can be used for the evacuation of the wounded and other logistic tasks.
A new model among the ANA is the Rex "field porter" shown by IAI's Lahav Division in October 2009. It is based on a small robotic platform that accompanies 3 to 10 soldiers in automatic mode and is capable of carrying 200 kg of equipment and supplies for up to three days without refueling. According to the company, “the robotic vehicle follows the leading soldier at a predetermined distance using technology developed and patented by IAI. Using simple commands, including stop, drive, and follow, the soldier controls the robot without distraction from his main task. Controlling the robot in this way allows for intuitive interaction and rapid integration of the product in the field in a short amount of time. " The Rex measures 50x80x200 cm, has a maximum speed of 12 km / h, a turning radius of 1 meter and a maximum gradeability of 30 degrees.
Analogies with the canine family, but in a completely different implementation, can be seen in the four-legged apparatus developed by the American company Boston Dynamics. The project was funded by the US Department of Defense Advanced Research and Development Administration (DARPA) with contributions from the Marine Corps and the Army. Big-Dog is a robot weighing about 109 kg, 1 m high, 1.1 m long and 0.3 m wide. Its prototype was evaluated at Fort Benning as an auxiliary device for foot patrols, carrying an 81-mm mortar barrel stove and tripod. The typical load of this prototype for all terrain types is 50 kg (up and down a 60 degree slope), but a maximum of 154 kg was shown on flat ground.
The BigDog modes of movement include crawling at 0.2 m / s, rapid at 5.6 km / h, trotting at 7 km / h, or "jumping gait", which in the laboratory allowed to exceed 11 km / h. The main propulsion unit is a 15 hp water-cooled two-stroke engine that drives an oil pump, which in turn drives four actuators for each leg. BigDog has approximately 20 sensors, including inertial sensors to measure attitude and acceleration, plus sensors in the joints to measure movement and actuator force in the legs; all sensors are controlled by the on-board computer.
The computer also processes IP radio signals received from the remote operator. It gives BigDog the direction and speed it needs, plus stop / start, crouch, walk, walk fast, and slow run commands. The stereo video system developed by the Jet Propulsion Laboratory consists of two stereo cameras, a computer and software. It usually detects the shape of the surface directly in front of the robot and recognizes a free path. LIDAR is also installed in the BigDog apparatus to automatically follow the instructions of a person.
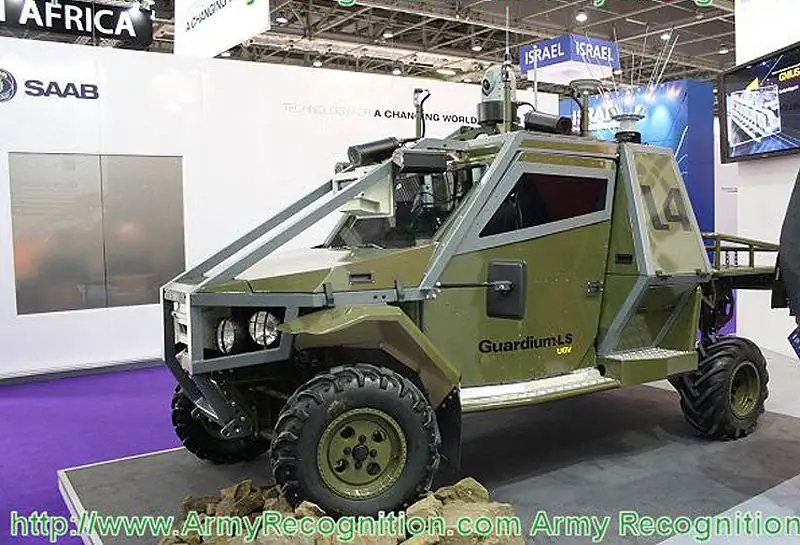
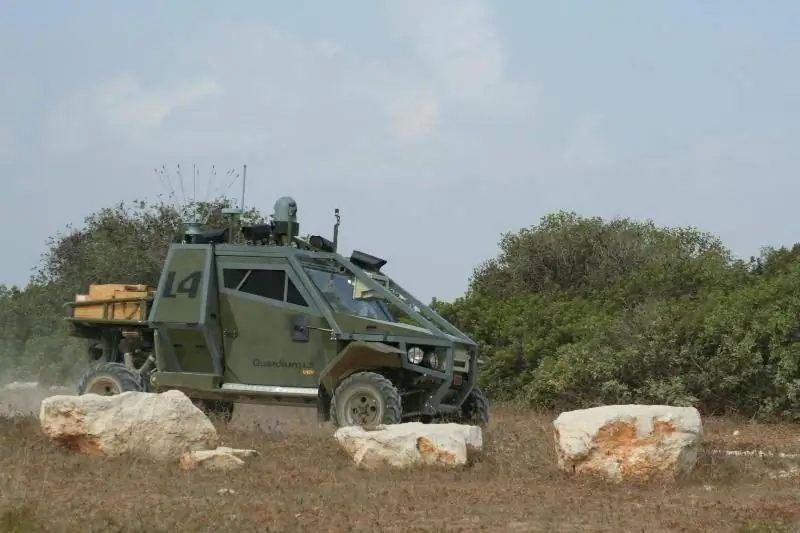
Guardium-LS is an optionally manned variant of the ANA G-NIUS Guardium, with which it has common control, visualization and electronic jamming systems. A mini-POP optoelectronic station is installed at the top of the cockpit, behind which there is a multi-element circular antenna for the EJAB explosive device suppressor
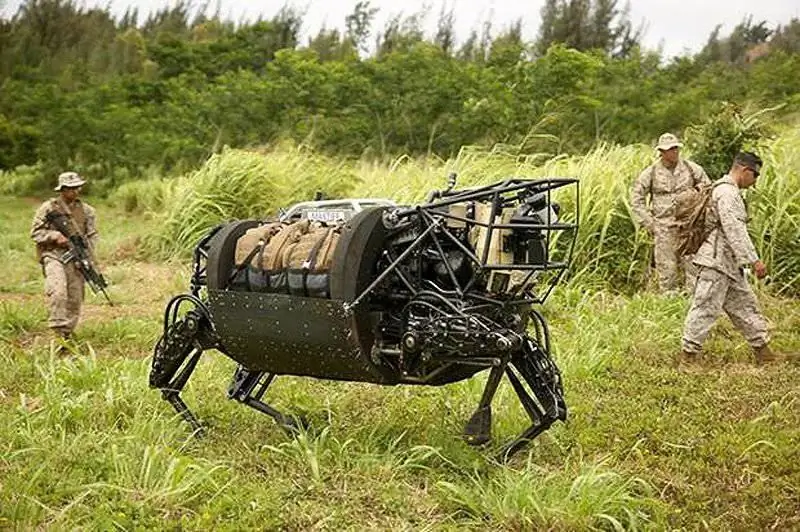
The four-legged BigDog robot, shown at the Fort Benning Infantry Center as a porter for patrol teams, automatically follows the assigned team member.
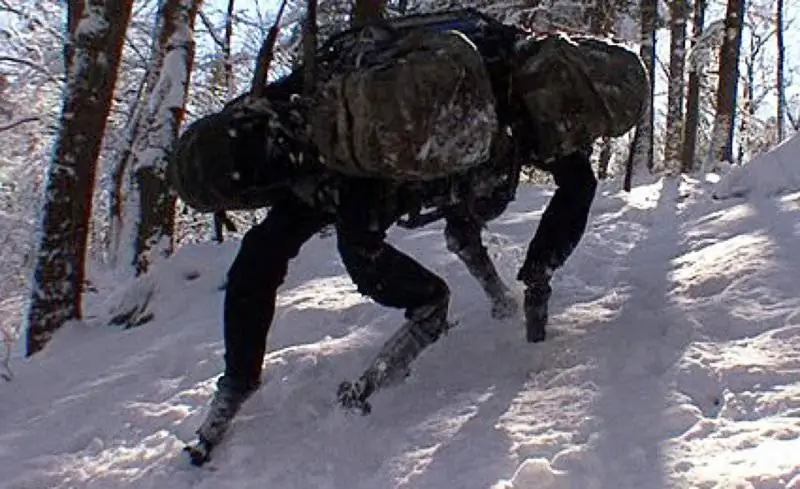
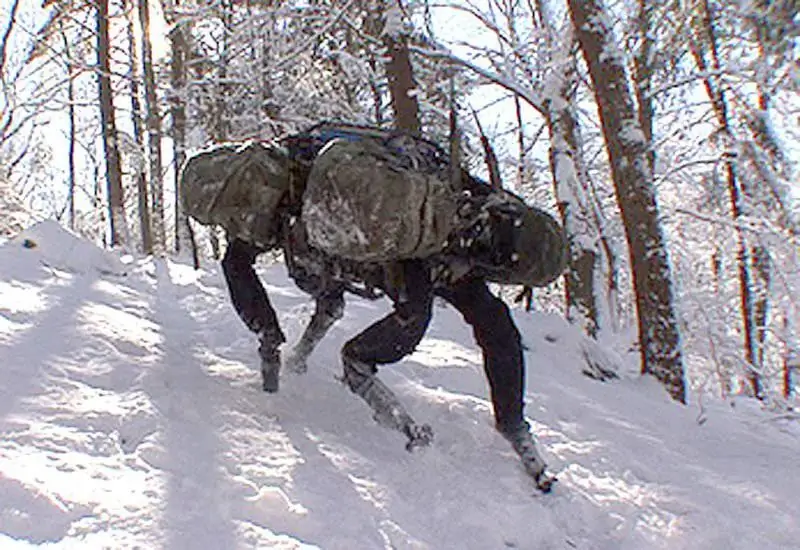
Boston Dynamics / DARPA BigDog four-legged robot overcomes a snowy slope
Rough Terrain Walking
Early on, BigDog demonstrated that it can walk 10 km over rough terrain for 2.5 hours, but Boston Dynamics is currently working on expanding design constraints so that the robot can overcome even more difficult terrain, have roll-over stability., reduced noise signatures and less operator dependency. The current voiced goal of the DARPA-sponsored LS3 (Legged Squad Support System) program, which is funded by BigDog, is the ability to carry 400 pounds (181 kg) for 24 hours.
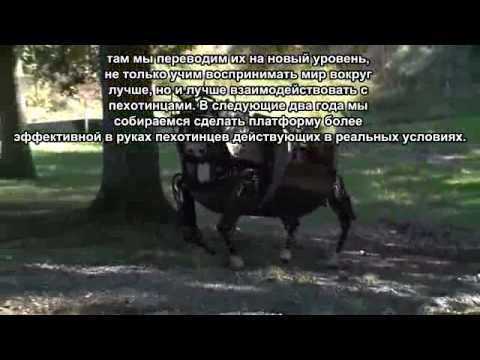
Demonstration of the LS3 Robotic Walking System to the Marine Corps Commander and Director of DARPA
The more or less traditional R-Gator supply vehicle, developed by John Deere in collaboration with iRobot, can be operated in manual or automatic modes. The car is equipped with a three-cylinder diesel engine with a capacity of 25 hp, the six-wheeled R-Gator has a 20-liter fuel tank, which is enough to cover 500 km. The transmission is stepless, the device has a maximum speed of 56 km / h in manual mode and 0-8 km / h in remote or automatic modes.
The vehicle has dimensions of 3, 08x1, 65x2, 13 m, its own weight is 861 kg, the volume of the cargo compartment is 0.4 m3 and the carrying capacity is 453 kg (towed 680 kg). R-Gator's standard video system includes fixed front and rear (for driving) color TV cameras with a field of view of 92.5 degrees and a stabilized panoramic zoom (25x optical / 12x digital) camera that rotates horizontally by 440 degrees and vertically by 240 degrees. degrees, has autofocus and sensitivity of 0.2 Lux F 2.0. This camera can be optionally replaced with a day / night optoelectronic / infrared zoom camera.
The basic communication kit R-Gator (with frequency options 900 MHz, 2.4 GHz or 4.9 GHz) has a minimum control range of 300 m, it is connected to an operator's laptop based on Windows OS or a portable control unit. The GPS Robot Positioning System from NavCom Technology can be combined with an Inertial System to improve accuracy. It is equipped with one rear LIDAR sensor and two forward LIDAR sensors that detect obstacles up to 20 meters away in remote and automatic modes.
It is worth briefly recalling the closed program that Lockheed Martin Missiles and Fire Control System carried out with its ANA MULE (Multifunction Utility / Logistics and Equipment). It was one of the "cornerstones" of the ANA family of systems, originally considered part of the canceled Army's FCS (Future Combat Systems) program.
It was assumed that the machine will be manufactured in three versions: assault ARV-A-L (Armed Robotic Vehicle - Assault Light) equipped with optoelectronic and infrared sensors and a laser rangefinder / pointer for targeting; MULE-CM (Countermine) equipped with GSTAM1DS (Ground Stand-off Mine Detection System), which allows detecting and neutralizing anti-tank mines and marking cleared passages, as well as performing limited detection of improvised explosive devices (IEDs) and other tasks unexploded ordnance disposal; and MULE-T (Transport), capable of carrying 862 kg (otherwise for two compartments) of equipment. All three options were supposed to have the same autonomous navigation system from General Dynamics Robotics Systems, designed for semi-automatic navigation and obstacle avoidance.
The MULE was specially designed to support the armored forces and had a commensurate rate of advance (maximum highway speed 65 km / h). In principle, it was supposed to have two MULE per platoon, but then this concept was revised and centralized control was defined at the battalion level.
ANA MULE had a total weight of 2, 26 tons. The main frame was supported on six independent, spring-loaded, swivel wheels, the hubs of which were fitted with electric motors from BAE Systems. This combined diesel-electric system was powered by a 135 hp Thielert diesel engine.
Branch support machine
In parallel, Lockheed Martin was working on its Squad Mission Support System (SMSS), which it funded as an independent research project to meet the urgent need for a manned and automated squad vehicle and logistics for light and fast response. With a mass of 1.8 tons, this 6x6 platform has a cruising range of 500 km on the highway and 320 km on rough terrain. The machine can be controlled either by the driver on board or by the operator remotely (“controlled autonomy”), or it can operate in an autonomous mode. The declared payload of the machine is over 454 kg, it is able to overcome a step of 588 mm and a trench with a width of 0.7 m. At full load, the cruising range is 160 km on the highway and 80 km off-road.
One of its features is the presence of a charger, which is powered by a diesel engine and which can be used to charge the batteries of personal radio stations of the squadron's personnel. SMSS can carry small AUVs, as well as two stretchers for the evacuation of the wounded. The winch at the front and the attachment points at the rear are for self-recovery.
SMSS Block 0 prototypes were tested at the Army Infantry Center at Fort Benning in August 2009, after which the company produced the first two Block 1 prototypes out of three. They have attachment points for transportation on the suspension of a UH-60L helicopter, improved noise signature management and reliability, and an upgraded set of sensors to increase the level of autonomy. In mid-2011, two SMSS systems were deployed in Afghanistan for operational testing, where their operational merit was confirmed.
It is worth noting that at the 2009 AUSA exhibition in Washington, Lockheed Martin showed SMSS in conjunction with its HULC (Human Universal Load Carrying System). This power-driven exoskeleton, in addition to its various tasks, is seen as a useful addition to SMSS as a means of unloading its cargo on the “last mile”: the point at which the terrain becomes impassable for vehicles. With a dead weight of 13.6 kg, the HULC helps the owner to carry loads up to 91 kg.
A pragmatic approach using ANA technology was adopted by Oshkosh Defense for the DARPA-funded TerraMax project. It combines remote control and autonomous capabilities with a standard military support vehicle and is expected to reduce the number of people required to conduct day-to-day support convoys in modern combat areas in the long term.
Within the TerraMax team, Oshkosh is responsible for hardware integration, modeling, wire-based control, setpoint tracking, and general layout. Teledyne Scientific Company provides highly efficient algorithms for task execution and route planning and high-level vehicle control, while the University of Parma is developing a Multi-Directional Vehicle Vision System (MDV-VS). Ibeo Automobile Sensor is developing a dedicated LIDAR system using Ibeo's Alasca XT sensors, while Auburn University integrates a GPS / IMU (Global Positioning System and Inertial Measurement Unit) package and assists with the vehicle's control system.
The TerraMax is a variant of the 4x4 MTVR military truck from Oshkosh, equipped with an independent TAK-4 suspension, 6.9 m long, 2.49 m wide, 2 m high, and weighing 11,000 kg with a payload of 5 tons. It is equipped with a six-cylinder, four-stroke, turbocharged Caterpillar C-121 diesel engine with a volume of 11.9 liters and a power of 425 hp, allowing a top speed of 105 km / h. The autonomous control system of the apparatus, developed as a set of devices, includes a video system with cameras; LIDAR system; navigation system GPS / IMU; an automated electronic system with multiplexing Oshkosh Command Zone; navigation computers for summarizing sensor data, map data management, real-time route planning and high-level control; as well as CANBus-controlled brakes, steering, engine and transmission.
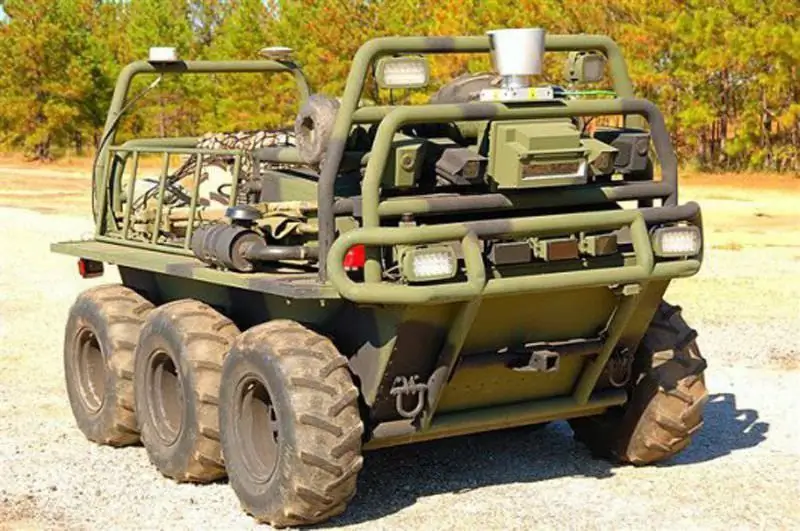
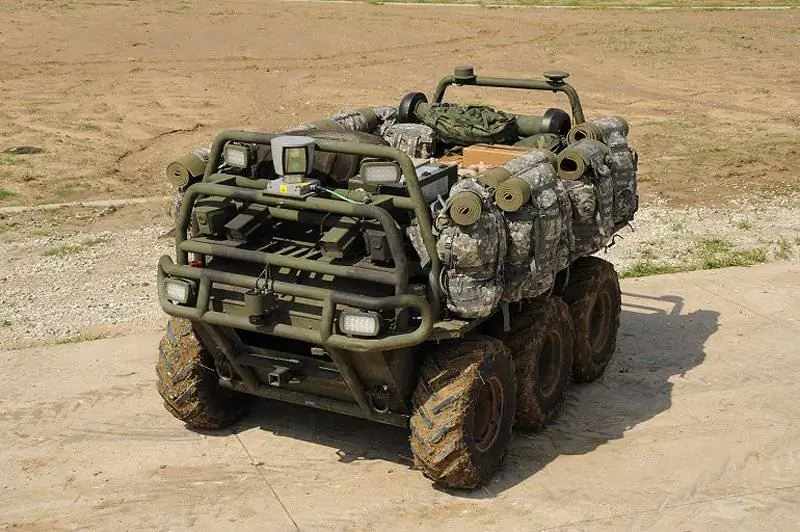
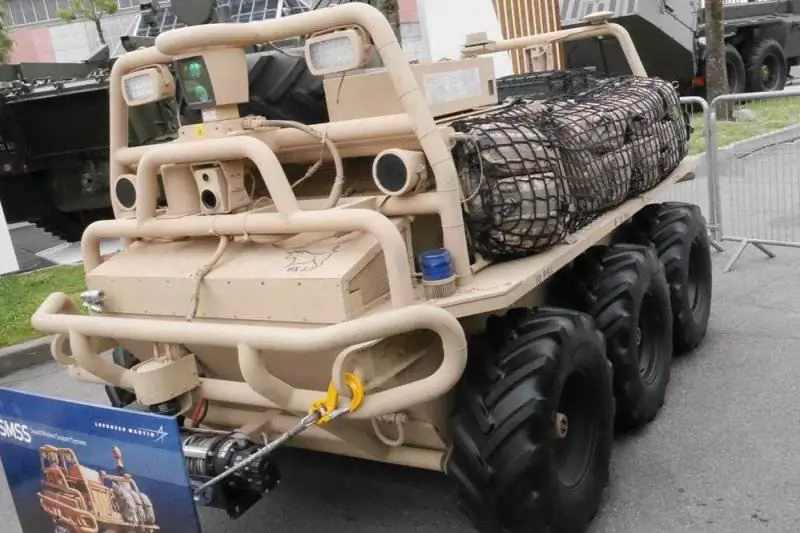
Lockheed Martin SMSS during testing at Fort Benning training camp in August 2009. SMSS acts as a support system for a dismounted department there.
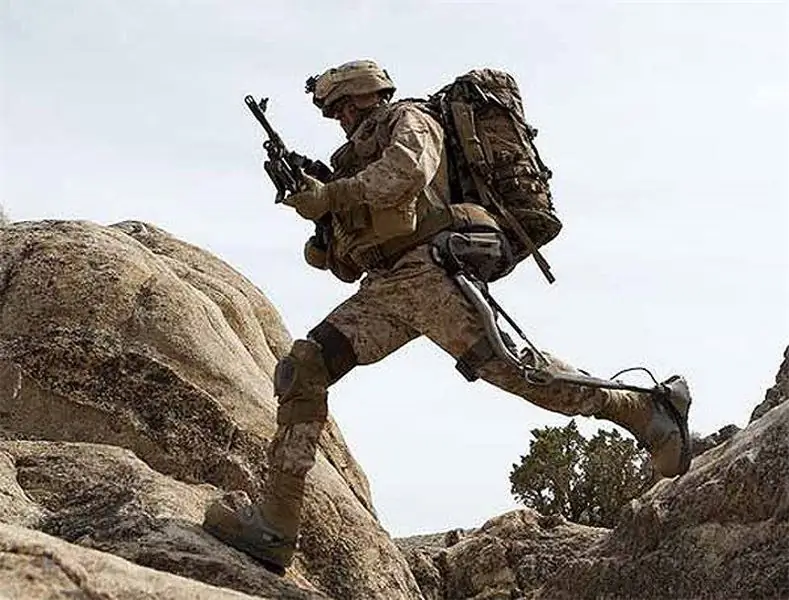
The battery-powered exoskeleton from Lockheed Martin allows the wearer to carry 200 lb (91 kg) out of the reach of the ANA. Throwing speed on a flat surface is 16 km / h
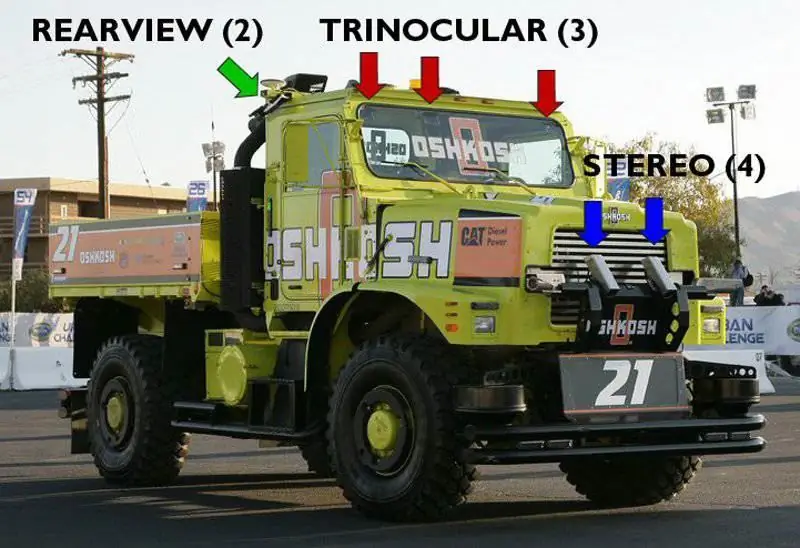
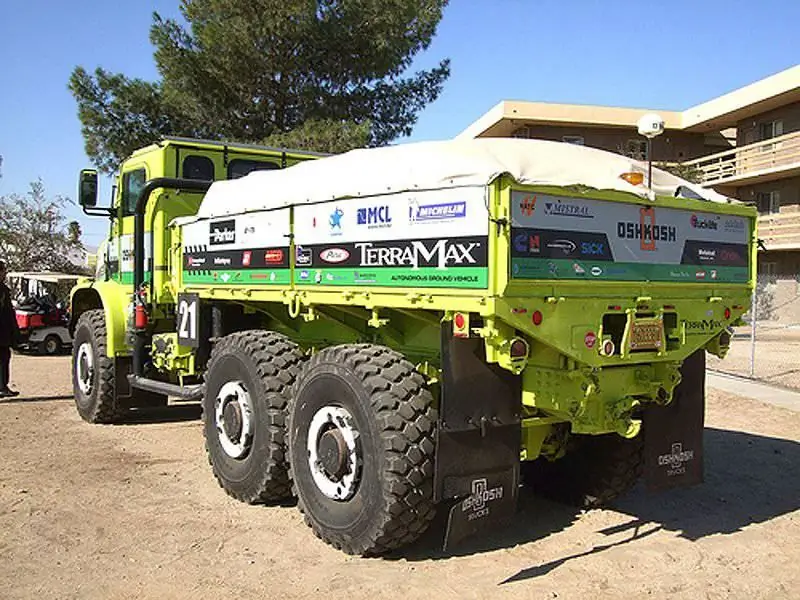
An Oshkosh MTVR TerraMax self-driving truck passes a road junction during the Urban Challenge, followed by an escort vehicle. Such technology could find application in future combat support convoys, saving lives and saving manpower.
Convoy guide
Taking part in various DARPA-funded robotic vehicle competitions, including the Urban Challenge, Oshkosh signed a corporate R&D agreement (CRADA) with the US Army's TARDEC Armored Research Center in early 2009 to adapt TerraMax technology for convoy missions. In accordance with CRADA's three-year agreement, the CAST (Convoy Active Safety Technology) simulation system is being installed on the TerraMax. It is designed to act as a route indicator for convoys and transmit information about the route to the following automatic vehicles, while it must operate safely among people, animals and other vehicles. Subsequently, in March 2009, Oshkosh announced work with the Navy's Surface Weapons Research Center to evaluate the use of the TerraMax as an MTVR (R-MTVR) robotic truck in various combat mission scenarios.
Relatively recently, Vecna Robotics has appeared on the market with its ANA Porter. It is described as a cross between personal cargo transfer systems and standard military vehicles, and is designed to move cargo weighing from 90 to 272 kg. The mass of the basic 4x4 vehicle is 90 kg, the length is 1.21 m, the width is 0.76 m and the height is 0.71 m.
It can be configured to carry various goods at a maximum speed of over 16 km / h, the maximum mileage is 50 km depending on the terrain, and is powered by a lithium polymer battery. The battery is charged in the field by an optional solar charger or generator. The maximum control distance depends on the line of sight (up to 32 km).
The Porter, currently an experimental model, is offered with a semi-autonomous control kit that features position control for load balancing plus follow me and escort modes, or with an autonomous control kit that includes GPS navigation, route planning and terrain mapping. Among other tasks, several ANA Porters could be used in autonomous columns or perform joint surveillance of the perimeter.
The Marine Corps' Cargo UAS program is an example of the search for the capabilities of a new generation of unmanned aerial delivery platforms. The Marine Corps Weapons Laboratory (MCWL) issued a requirement in April 2010 for the display in February 2011 or earlier of a cargo UAV capable of operating in remote areas.
Capt. Amanda Mauri, head of projects for airborne combat components at the MCWL laboratory, said that the requirements for the cargo UAV were mainly determined by the combat experience of Afghanistan. The MCWL worked with the Combat Development Center and other corps agencies to determine the mass of supplies that a company-sized unit in Afghanistan could handle in one day, and came up with a figure of 10,000-20,000 pounds of cargo. “In terms of distance, 150 miles round trip, it is based on the distance from the forward operating base to the forward bases, but obviously they are constantly changing,” she said.
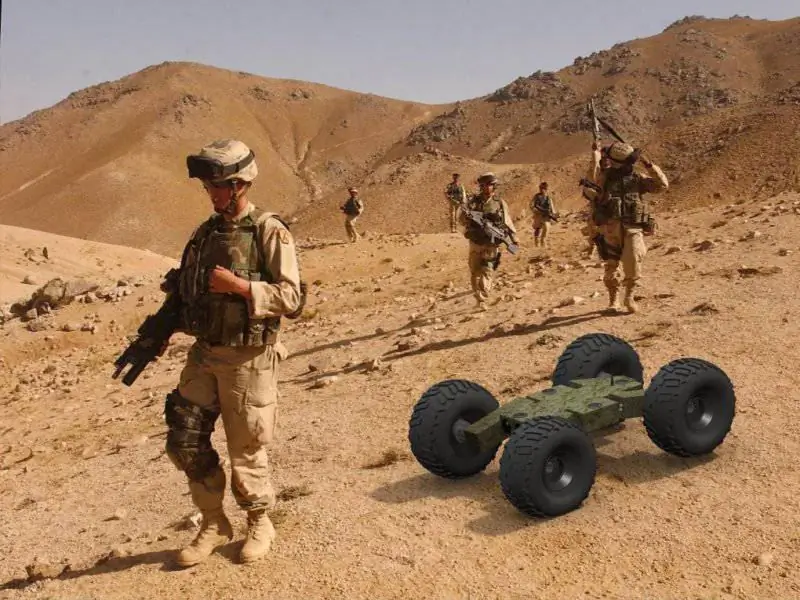
Computer image of ANA Porter by Vecna Robotics, which has already passed the prototype stage
Consequently, the capability claimed by MCWL for the demonstration phase was to deliver a minimum of 10,000 pounds of cargo (20,000 pounds in practice) over a 24 hour period over 150 nautical miles round trip. The smallest item of the entire cargo package must be equivalent to at least a standard wooden pallet (48x40x67 inches), weighing a minimum of 750 pounds with an actual weight of 1000 pounds. It must be able to independently take off from a forward base or unpaved road out of line of sight, and also be controlled remotely from its terminal; the cargo must be delivered with an accuracy of at least 10 meters.
The platform's performance is the ability to fly at full load at 70 knots (130 km / h) at 15,000 feet and hover up to 12,000 feet. The UAV must also interact with existing air control agencies in the deployment areas, and its radio control frequencies must be compatible with the frequency requirements in the deployment areas.
In August 2009, the MCWL laboratory announced the selection of two applications for the competition for a cargo UAV: these are the K-MAX systems from Lockheed Martin / Kaman and the A160T Hummingbird from Boeing. The MQ-8B Fire Scout UAV from Northrop Grumman was excluded.
Lockheed Martin and Kaman formed the K-MAX team in March 2007; it has integrated a Lockheed Martin UAV control system into the commercially successful K-MAX medium-lift helicopter, which is widely used in the construction and woodworking industries.
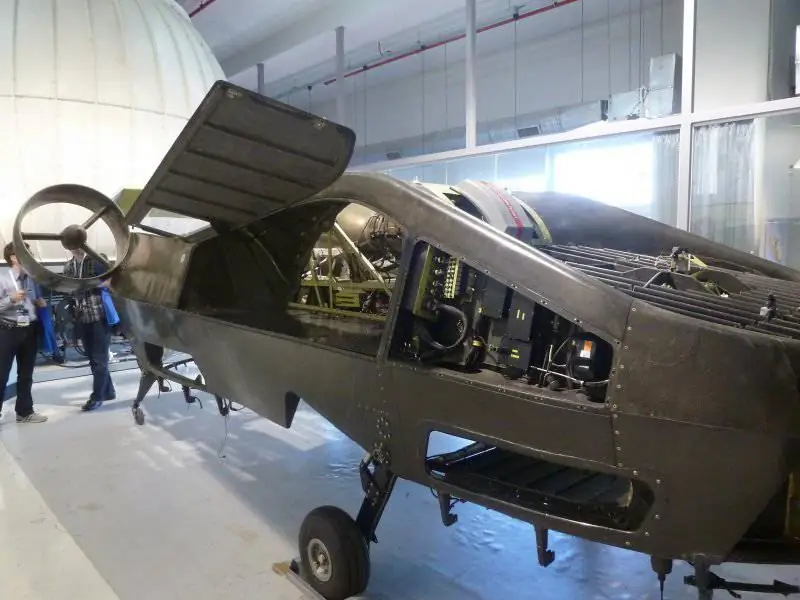
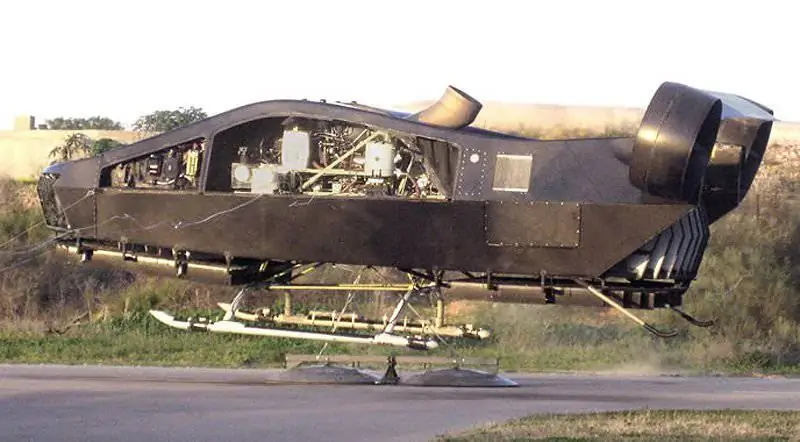
AirMule by Israel Aeronautics features an innovative internal powerplant allowing operation in confined spaces
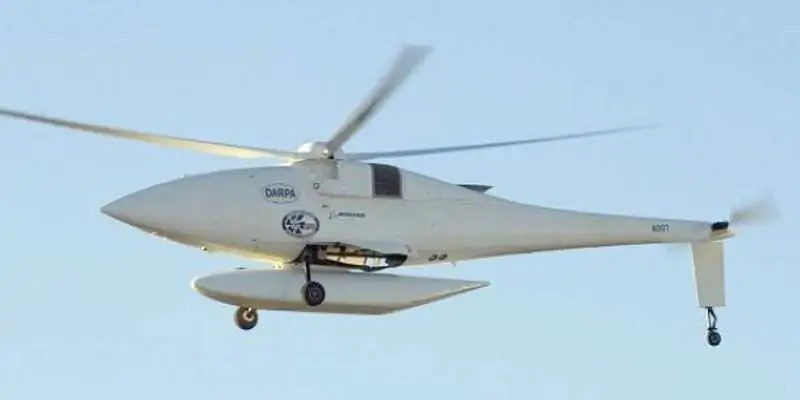
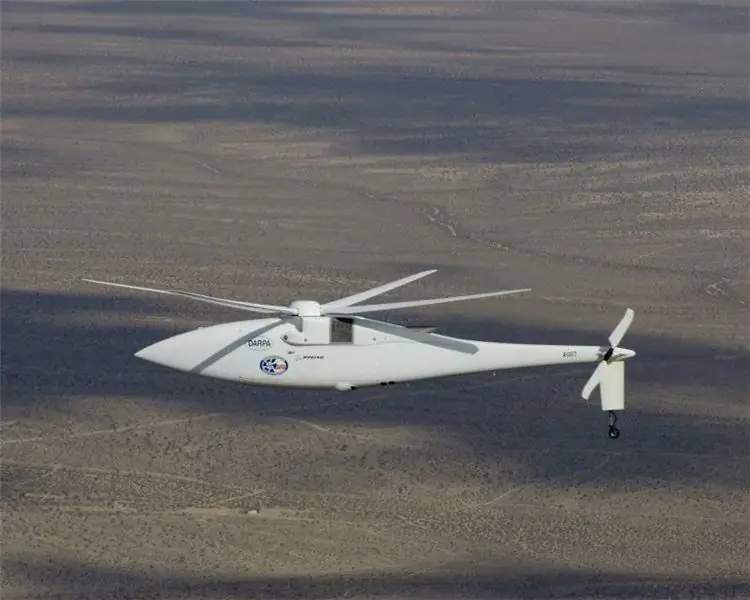
A160T Hummingbird with 1000 lb cargo nacelle
The K-MAX design features two counter-rotating criss-cross propellers, eliminating the need for a tail rotor, increasing lift and reducing seat footprint; Kaman says this allows all 1,800 horsepower from the Honeywell T53-17 gas turbine engine to be directed to the main propellers, increasing lift. With a maximum load of 3109 kg, the K-MAX can fly at 80 knots for a range of 214 nautical miles; without cargo, the speed is 100 knots, the range is 267 nautical miles. Essentially a modified manned platform, the K-MAX can be manned as needed, as the onboard controls are retained.
Jeff Bantle, vice president of rotorcraft programs, said the team “focused on meeting Marine requirements rather than exploring other ways of developing the platform. He explained that the group was working on a modification to the aircraft and a number of systems were added, including direct and indirect vision communication systems, tactical data link, flight control system and redundant INS / GPS system (both redundant)."