Components
The quality of equipment produced in a particular country directly depends on the quality of components and the availability of technologies for national manufacturers. This thesis is relevant for almost all industries in all countries of the world. For example, you can look at the path of domestic car manufacturers. The low quality of components, traditional for the USSR, multiplied by the economic problems observed after the collapse of the Union, made all automobile manufacturers using domestic units in their products uncompetitive. The only way to survive in such conditions was to borrow off-the-shelf technologies. This path, as a rule, leads to the loss of independence of the automotive industry, loss of technological priority and competencies, loss of the market, and, as a result, to a reduction in the number of highly qualified jobs, a reduction in tax revenues, degradation of industry, economic losses of a particular enterprise and the country as a whole. An example is the GAZ plant. The plant moved to equipping its cars with Chrysler and Cummins engines, then attempts were made to localize the production of Maxus and Chrysler Sebring cars, which turned out to be unsuccessful. Ultimately, the passenger program was curtailed, the production of medium-sized trucks dropped to almost one-off, and GAZelle-Business vehicles use many foreign-made components, including high-tech ones - clutches, bearings, suspension and steering components. In the new generation car "Gazelle-Next" the share of foreign components is even higher. In the workshops where the Volga car was previously produced, the production of VW and Skoda cars is now deployed. In parallel with GAZelle, the plant launched production of old generation Mercedes Sprinter light trucks. Ultimately, the competence to develop their own cars is practically lost. Unfortunately, a similar situation is observed at other domestic enterprises - KAMAZ and VAZ, which are systematically turning into production sites of world auto concerns, without the ability to develop and introduce their own technologies.
The current state of affairs in this area is nothing more than a legacy of the Soviet era, fueled by the influence of foreign capital, imposing obsolete technologies that have left the Western market.
Backlog
During the Soviet era, there was a proven system for the development and implementation of new automotive components and assemblies into production. At the first stage of the work, fundamental and applied research was carried out, mainly by scientific institutes with the appropriate competence. The research results were transferred to factories for subsequent implementation. At the second stage, already by the efforts of enterprises, the development and testing of prototypes was carried out, including in conjunction with institutes. After the experimental design work, a decision was made to introduce a particular development. The whole process, including the distribution of financial flows, was controlled by the Ministry of the Automotive Industry of the USSR.
Unfortunately, this system functioned well only in preparation for the Third World War and did not fully meet the requirements of the national economy. In this connection, there has been a bias towards technical and technological retrograde. The design of cars produced by this or that car plant has remained practically unchanged since their launch in production for decades. There was no need to talk about advanced innovations - at best, it was possible to achieve acceptable reliability of the car and its components.
Bourgeois approach
Due to market processes and tough competition in the automotive industry, foreign manufacturers could not act on the basis of decisions of the party and government, and had to rely solely on their own capital. Without government support, the success was achieved by the manufacturer who offered the best product at the lowest price. The processes of globalization and the struggle for the environment have further exacerbated competition.
It should be noted that even a large car manufacturer cannot conduct research and development work in many areas at once, since this requires huge resources. That is why small enterprises, including those with venture financing, engaged in the development of a certain technology, have become so widespread. The activities of such enterprises are associated with a high degree of risk, but they allow creating truly advanced, outstanding innovations. Several domestic enterprises using this model have successfully developed and commercialized. Their technologies can be directly used in the automotive industry, for example, the manufacturer of domestic LEDs CJSC Optogan or LLC Liotech, a manufacturer of electrochemical energy storage devices, can be noted. But…
Advanced developments
Unfortunately, advanced developments in the automotive industry are practically not implemented. We, apparently out of inertia, are trying to use the Soviet approach in the fight against a very strong foreign competitor. For example, in the early nineties, the question of developing a new platform - a road tractor (SKSHT) - became acute. The parent company was BAZ, and one of the key components for this platform was a new hydromechanical transmission (GMT). In 1995 OJSC VNIITransmash created the design of such a transmission. It was supposed to produce samples of this gearbox at the Transmission enterprise, which, having not had time to make a single sample, ceased to exist. All the accumulated potential and the team were lost. In the middle of the 2000s, the question of resuming work on an automatic transmission for military vehicles (BAT) again became acute. However, all attempts to revive the GMF were unsuccessful. A possible reason for the termination of work in this direction at that time was the reorientation of the Ministry of Defense to the purchase of foreign samples of automotive equipment, excluding the development of domestic analogues. The author means the purchase of Lynx (Iveco LMV) vehicles and 12-10FMX40 tankers based on Volvo cars assembled in Russia from car sets, as well as testing of Centauro and Freccia armored vehicles, German-Dutch Boxer GTK for the purpose of their further purchase. As a result, SKSHT BAZ is equipped only with a manual transmission, which makes increased demands on the qualifications of the driver, has a bad effect on cross-country ability, and reduces the engine resource. The topic of the introduction of automated transmissions on military vehicles has not lost its relevance. According to the requirements of the Ministry of Defense, promising vehicles of various types (MRAP, armored personnel carriers, unarmored trucks) in the foreseeable future should be equipped with engines with a capacity of more than 500 hp. Operating a manual gearbox with an engine of this power requires very high qualifications of the driver.
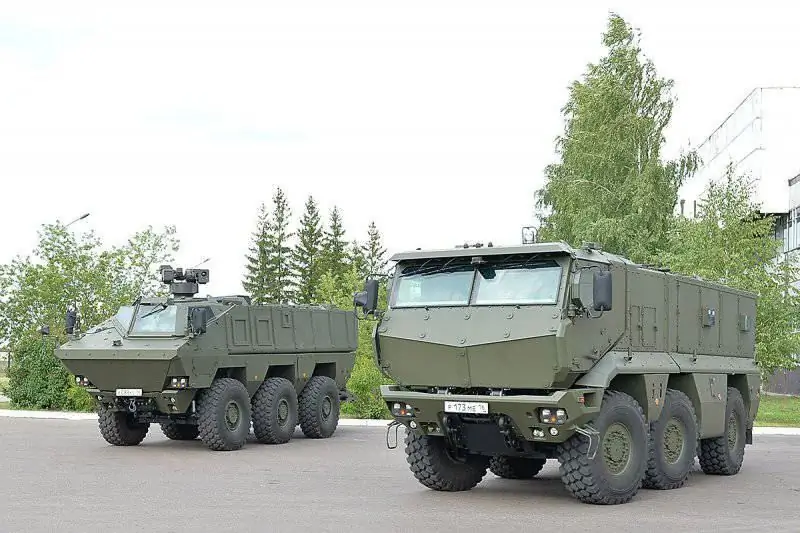
Prototypes of protected Typhoon-K vehicles KamAZ-63969 (left) and KamAZ-63968 (right), equipped with Allison Transmission 4000
In support of these words, we can cite the example of promising cars of the Typhoon family, which are compelled to be equipped with gearboxes of the American company Allison Transmission Inc., the world leader in the production of automatic transmissions for commercial and military equipment. If the KAMAZ and Ural factories are able to bring these vehicles to production, then it is quite possible to expect opposition from the US government agencies in the supply of these transmissions for military equipment. It should also be borne in mind that the transmission control system is microprocessor-based, which means there is no guarantee that it does not have unprocessed, hidden functions.
Innovations
Realizing this and drawing on the experience of other countries, where technological innovation is a good business with huge profits, in Russia, starting in 2006, funds and companies were created that deal with venture and project financing with state participation. These include the Russian Venture Company (RVC) and Skolkovo. In 2008, one of the participants in this event, the VTB Capital Venture Fund, financed the Supervariator company, which is developing a technology that is completely atypical for the Russian venture business - a continuously variable automobile transmission. The use of non-standard financial instruments to increase the technological potential of the Russian industry this time turned out to be surprisingly fruitful. The above examples are very contrasting - an experienced team that worked for many years in a specific direction, with government support, the presence of an experimental plant and a customer represented by the RF Ministry of Defense, failed to correctly navigate the situation and ceased to exist, and the modest team of a small enterprise managed to do what that no one in Russia has ever succeeded. The company has developed an original multi-flow electromechanical continuously variable transmission - a supervarier. Bench tests of prototypes have confirmed the tangible superiority of the supervariator over existing and future transmissions of other types. The average efficiency of the prototype was 94%, and the maximum efficiency in the most demanded modes exceeded 99%. The development is completely domestic, which is confirmed by three dozen patents received by the company. Due to the possibility of practically unlimited scaling, the supervarier can be used on all types of military and commercial vehicles. According to the available information, the team of the enterprise is developing a promising family of continuously variable transmissions with a capacity of 300-500 hp. which can be used on the overwhelming number of modern VTA samples. A promising development can replace American Allison boxes in Typhoon vehicles or SKSHT BAZ mechanical transmissions.
However, the implementation of the above-described innovative technologies does not occur in the automotive industry.
conclusions
The problem of personnel and technology leakage abroad is not new for Russia. In such a complex and costly area as the automotive industry, the technological passivity of enterprises that are not ready or willing to innovate, the loss of technology is especially painful. Unlike modern IT startups, which form the backbone of venture capital business in Russia, mechanical engineering startups are much more costly. Large costs and risks promise the possibility of creating a very large and long-term business with a product life cycle of 20-25 years. With the urgent need to create 25 million highly skilled jobs by 2020, this opportunity cannot be neglected.