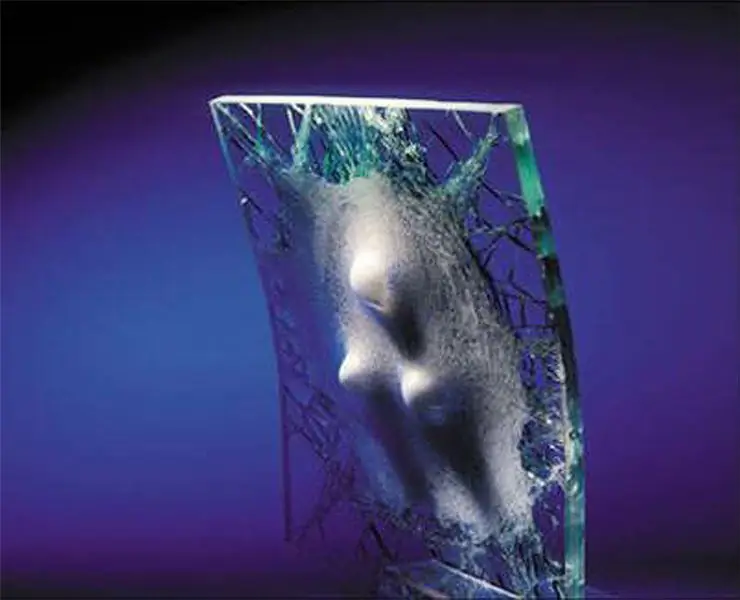
Military vehicles have traditionally been made of heavy, expensive, but high-strength armor steel. Modern ceramic composite materials are increasingly used as non-bearing protection for combat vehicles. The main advantages of such materials are significantly lower cost, improved protection and weight reduction by more than half. Consider the modern basic ceramic materials used today for ballistic protection
Due to its ability to withstand very high temperatures, significantly higher than that of metals, hardness, the highest specific strength and specific stiffness, ceramics are widely used for the manufacture of linings for engines, rocket components, cutting edges of tools, special transparent and opaque shields, which, of course, are among the priority areas for the development of military systems. However, in the future, the scope of its application should significantly expand, since within the framework of research and development carried out in many countries of the world, new ways of increasing plasticity, crack resistance and other desirable mechanical properties are being searched for by combining a ceramic base with reinforcing fibers in the so-called ceramic matrix. composite materials (KMKM). Also, new manufacturing technologies will allow for the mass production of very durable, high-quality transparent products of complex shapes and large sizes from materials that transmit visible and infrared waves. In addition, the creation of new structures using nanotechnology will make it possible to obtain durable and lightweight, superheat-resistant, chemically resistant and, at the same time, virtually indestructible materials. This combination of properties is today considered mutually exclusive and thus very attractive for military applications.
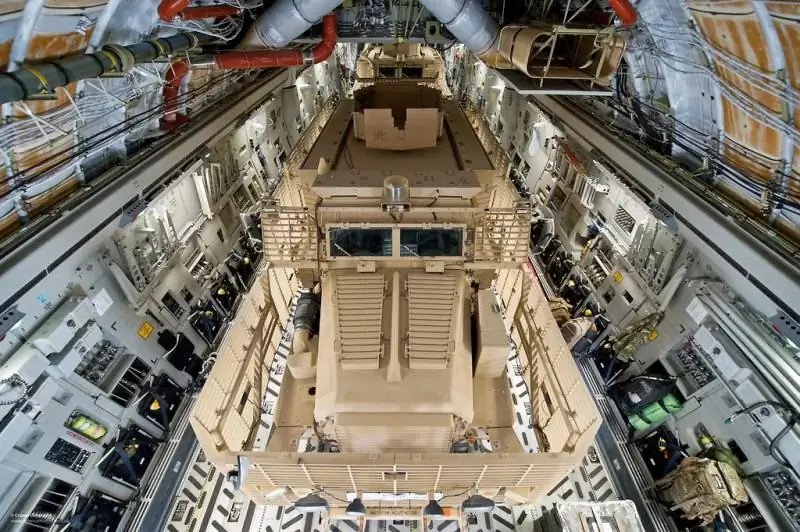
Ceramic-matrix composite materials (KMKM)
Like their polymer analogs, CMCs consist of a base substance, called a matrix, and a reinforcing filler, which is particles or fibers of another material. Fibers can be continuous or discrete, randomly oriented, laid at precise angles, woven in a special way to obtain increased strength and stiffness in given directions, or evenly distributed in all directions. However, whatever the combination of materials or fiber orientation is, the bond between the matrix and the reinforcing component is critical to the properties of the material. Since polymers are less rigid than the material that reinforces them, the bond between the matrix and the fibers is usually strong enough to allow the material to resist bending as a whole. However, in the case of CMCM, the matrix can be stiffer than the reinforcing fibers so that the bonding force, similarly optimized to allow slight delocalization of the fiber and matrix, helps to absorb impact energy, for example, and prevent the development of cracks that would otherwise lead to to brittle destruction and splitting. This makes CMCM much more viscous compared to pure ceramics, and this is the most important property of highly loaded moving parts, for example, parts of jet engines.
Lightweight and hot turbine blades
In February 2015, GE Aviation announced successful trials of what it calls “the world's first non-static CMC kit for an aircraft engine,” although the company did not disclose the materials used for the matrix and reinforcement material. We are talking about low-pressure turbine blades in an experimental model of the F414 turbofan engine, the development of which is intended to provide further confirmation of the material's compliance with the declared requirements for operation at high shock loads. This activity is part of the Adaptive Engine Technology Demonstrator (AETD) Next Generation Self-Adaptive Engine Demonstration Program, in which GE is collaborating with the US Air Force Research Laboratory. The aim of the AETD program is to provide key technologies that could be implemented in engines of sixth generation fighters and, starting in the mid-2020s, in engines of fifth generation aircraft, such as the F-35. Adaptive engines will be able to adjust their pressure ratio and bypass ratio in flight in order to obtain maximum thrust during takeoff and in combat, or maximum fuel efficiency in cruise flight mode.
The company emphasizes that the introduction of rotating parts made of CMC into the “hottest and most heavily loaded” parts of a jet engine represents a significant breakthrough, since previously the technology allowed using CMC only for the manufacture of stationary parts, for example, a high-pressure turbine shroud. During the tests, the KMKM turbine blades in the F414 engine went through 500 cycles - from idle speed to takeoff thrust and back.
The turbine blades are much lighter than conventional nickel alloy blades, which allowed the metal discs to which they are attached to be smaller and lighter, the company said.
“The shift from nickel alloys to rotating ceramics inside the engine is a really big leap forward. But it's pure mechanics,”said Jonathan Blank, head of CMC and polymer binders at GE Aviation. - Lighter blades create less centrifugal force. This means you can shrink disc, bearings and other parts. KMKM made it possible to make revolutionary changes in the design of a jet engine”.
The goal of the AETD program is to reduce specific fuel consumption by 25%, increase flight range by more than 30% and increase maximum thrust by 10% compared to the most advanced 5th generation fighters. “One of the main challenges in moving from static CMC components to rotating components is the stress field in which they must operate,” said Dan McCormick, Advanced Combat Engine Program Manager at GE Aviation. At the same time, he added that testing the F414 engine yielded important results that will be used in the adaptive cycle engine. “A low-pressure CMC turbine blade weighs three times less than the metal blade it replaces, in addition, in the second economical mode, there is no need to cool the CMC blade with air. The blade will now be more aerodynamically efficient as there is no need to pump all this cooling air through it."
KMKM materials, in which the company says it has invested more than a billion dollars since it began work on them in the early 90s, can withstand temperatures hundreds of degrees higher than traditional nickel alloys and are distinguished by silicon carbide fiber reinforcement in a ceramic matrix., which increases its impact strength and crack resistance.
GE appears to have done some pretty hard work on these turbine blades. Indeed, some of the mechanical properties of KMKM are very modest. For example, the tensile strength is comparable to the tensile strength of copper and cheap aluminum alloys, which is not very good for parts that are subjected to large centrifugal forces. In addition, they exhibit a low strain at break, that is, they elongate very slightly at break. However, these shortcomings seem to have been overcome, and the low weight of these materials definitely made an important contribution to the victory of the new technology.
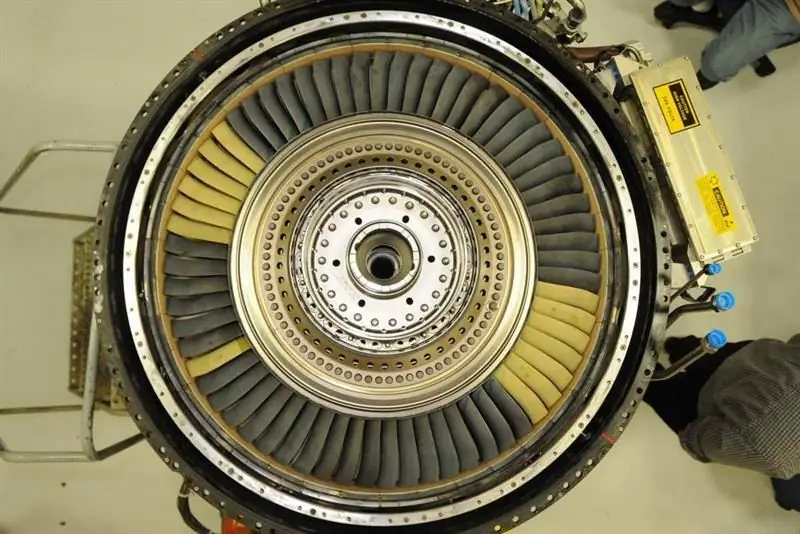
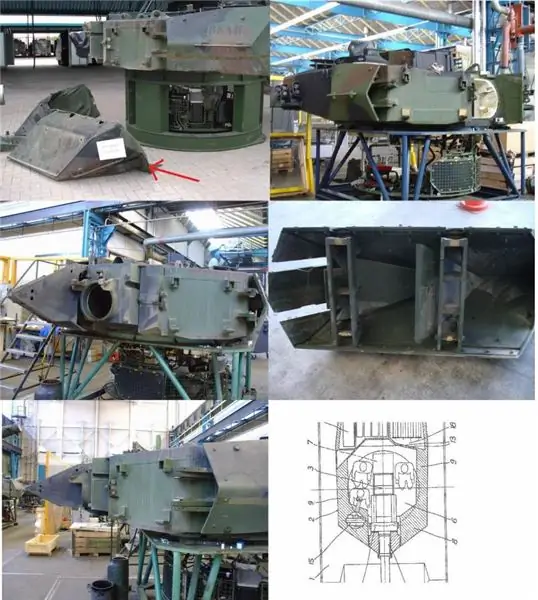
Modular armor with nano-ceramics for the LEOPARD 2 tank
Composite armor contribution
Although protection technologies, which are a combination of layers of metal, fiber-reinforced polymer composites and ceramics, are well established, the industry continues to develop increasingly complex composite materials, but many of the details of this process are carefully hidden. Morgan Advanced Materials is well known in the field, announcing an award at the Armored Vehicles XV conference in London last year for its SAMAS defense technology. According to Morgan, the SAMAS protection widely used on British Army vehicles is a composite material reinforced with materials such as S-2 Glass, E-Glass, aramid and polyethylene, then formed into sheets and cured under high pressure: “Fibers can be combined with hybrid ceramic-metal materials to meet special design and performance requirements."
According to Morgan, SAMAS armor with a total thickness of 25 mm, used for the manufacture of protective capsules of the crew, can reduce the weight of light protected vehicles by more than 1000 kg compared to vehicles with a steel capsule. Other advantages include the ease of repair with less than 5mm thicker thicknesses and the inherent splinterproofing properties of the material.
Explicit spinel progress
According to the US Navy Research Laboratory, the development and production of transparent materials based on magnesium aluminum oxide (MgAI2O4), also known collectively as artificial spinels, is booming. Spinels have long been known not only for their strength - 0.25 "thick spinel has the same ballistic characteristics as 2.5" bulletproof glass - but also the difficulty of making large parts with uniform transparency. However, a group of scientists from this laboratory has invented a new process for low-temperature sintering in a vacuum, which allows you to get parts with dimensions limited only by the size of the press. This is a major breakthrough compared to previous manufacturing processes, which began with the process of melting the original powder in a melting crucible.
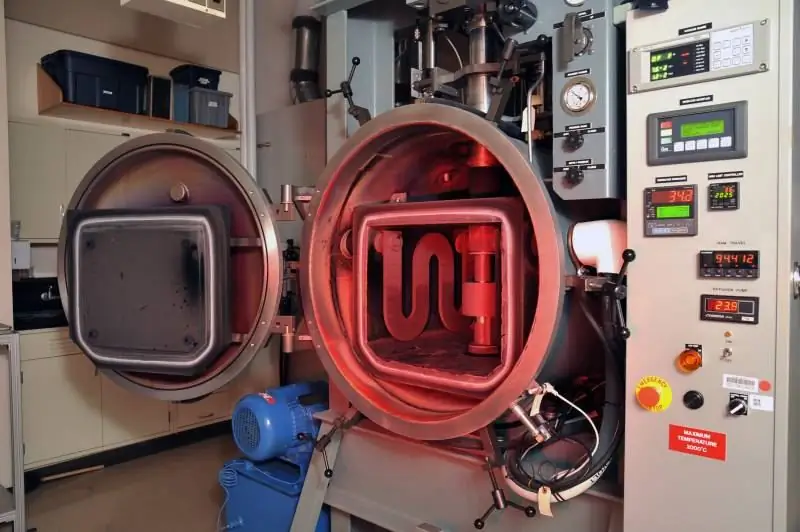
One of the secrets of the new process is the uniform distribution of the lithium fluoride (LiF) sintering additive, which melts and lubricates the spinel grains so that they can be evenly distributed during sintering. Instead of dry mixing lithium fluoride and spinel powders, the laboratory has developed a method for uniformly coating the spinel particles with lithium fluoride. This can significantly reduce the consumption of LiF and increase the light transmittance up to 99% of the theoretical value in the visible and mid-infrared regions of the spectrum (0.4-5 microns).
The new process, which allows for the production of optics in various shapes, including sheets that fit comfortably with the wings of an airplane or drone, has been licensed by an unnamed company. Possible applications for spinel include armored glass weighing less than half the mass of existing glass, protective masks for soldiers, optics for next-generation lasers, and multispectral sensor glasses. When mass-producing, for example, crack-resistant glasses for smartphones and tablets, the cost of spinel products will significantly decrease.
PERLUCOR - a new milestone in bullet and wear protection systems
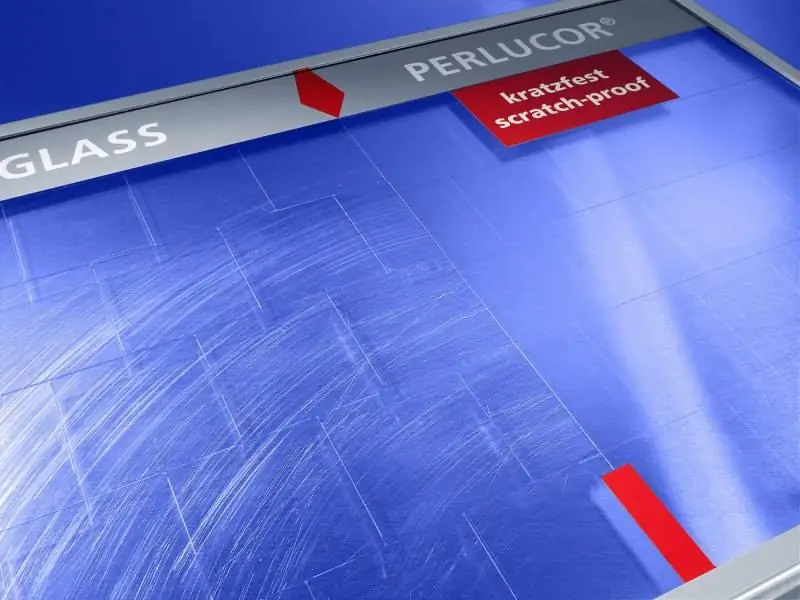
CeramTec-ETEC developed PERLUCOR transparent ceramics a few years ago, which has good prospects for both defense and civilian applications. The excellent physical, chemical and mechanical properties of PERLUCOR were the main reasons for the successful market entry of this material.
PERLUCOR has a relative transparency of over 90%, is three to four times stronger and harder than ordinary glass, the heat resistance of this material is about three times higher, which allows it to be used at temperatures up to 1600 ° C, it also has an extremely high chemical resistance, this allows the use it with concentrated acids and alkalis. PERLUCOR has a high refractive index (1, 72), which makes it possible to manufacture optical objectives and optical elements of miniature dimensions, that is, to obtain devices with powerful magnification, which cannot be achieved with polymers or glass. PERLUCOR ceramic tiles have a standard size of 90x90 mm; however, CeramTec-ETEC has developed a technology for producing complex-shaped sheets based on this format according to customer specifications. The thickness of the panels can in special cases be tenths of a millimeter, but, as a rule, it is 2-10 mm.
The development of lighter and thinner systems of transparent protection for the defense market is progressing at a rapid pace. A significant contribution to this process is made by the transparent ceramics of the SegamTes company, which is part of the protection systems of many manufacturers. When tested in accordance with STANAG 4569 or APSD, the weight reduction is in the order of 30-60 percent.
In recent years, another direction in the development of technologies developed by SegatTes-ETEC has taken shape. Vehicle windows, especially in rocky and desert areas such as Afghanistan, are prone to stone impacts and scratches from the movement of wiper blades on a sandy, dusty windshield. Also, the ballistic characteristics of bullet-resistant glasses that have been damaged by stone hits are reduced. During hostilities, vehicles with damaged glass are exposed to serious and unpredictable risks. SegamTes-ETEC has developed a truly innovative and original solution for protecting glass from this type of wear. A thin layer (<1 mm) of PERLUCOR ceramic coating on the windshield surface helps to successfully resist such damage. This protection is also suitable for optical instruments such as telescopes, lenses, infrared equipment and other sensors. The flat as well as curved lenses made from PERLUCOR clear ceramics extend the lifespan of this highly valuable and sensitive optical equipment.
CeramTec-ETEC successfully presented a bulletproof glass door panel and a scratch and stone resistant protective panel at the DSEI 2015 in London.
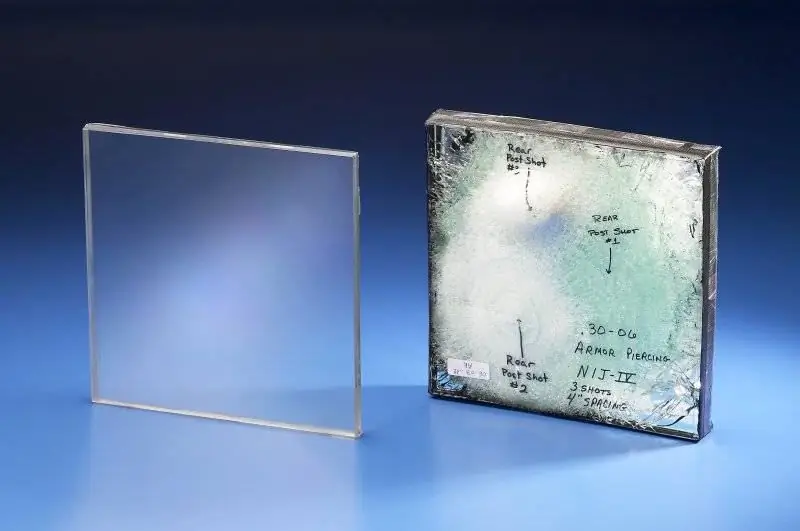
Durable and flexible nanoceramic
Flexibility and resilience are not qualities that are inherent in ceramics, but a team of scientists led by professor of materials science and mechanics Julia Greer of the California Institute of Technology took up the problem. The researchers describe the new material as "tough, lightweight, regenerable three-dimensional ceramic nanolattices." However, this is the same name for an article published by Greer and her students in a scientific journal a couple of years ago.
What is hidden underneath is best illustrated by a cube of aluminum oxide nanolattices several tens of microns in size, taken with an electron microscope. Under the action of the load, it shrinks by 85% and, when it is removed, is restored to its original size. Experiments were also carried out with lattices consisting of tubes of different thicknesses, with the thinnest tubes being the strongest and most elastic. With a tube wall thickness of 50 nanometers, the lattice collapsed, and with a wall thickness of 10 nanometers, it returned to its original state - an example of how the size effect increases the strength of some materials. The theory explains this by the fact that with a decrease in size, the number of defects in bulk materials proportionally decreases. With this architecture of the lattice of hollow tubes, 99.9% of the volume of the cube is air.
Professor Greer's team creates these tiny structures by running a process similar to 3D printing. Each process begins with a CAD file that drives two lasers that "paint" the structure in three dimensions, curing the polymer at points where the beams amplify each other in phase. The uncured polymer flows out of the cured lattice, which now becomes the substrate to form the final structure. The researchers then apply the alumina to the substrate using a method that accurately controls the thickness of the coating. Finally, the ends of the lattice are cut to remove the polymer, leaving only the crystal lattice of hollow alumina tubes.
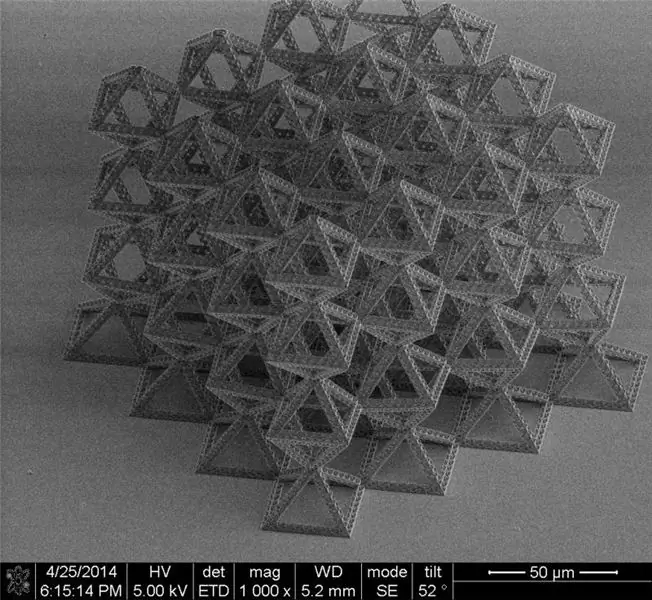
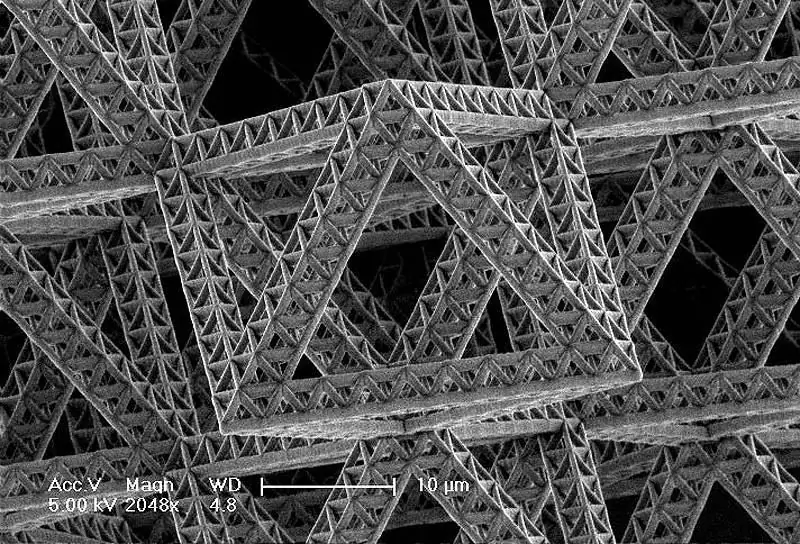
Strength of steel, but weighs like air
The potential of such "engineered" materials, which are mostly air by volume, but are all the less strong as steel, is enormous, but difficult to comprehend, so Professor Greer gave several striking examples. The first example, balloons from which helium is pumped out, but at the same time retaining their shape. The second, future aircraft, whose design weighs as much as its manual model weighs. What is most surprising, if the famous Golden Gate Bridge were made of such nanolattices, all the materials needed for its construction could be placed (excluding air) on a human palm.
Just as the enormous structural advantages of these strong, lightweight and heat-resistant materials suitable for countless military applications, their predetermined electrical properties could revolutionize energy storage and generation: “These nanostructures are very lightweight, mechanically stable, and at the same time huge surfaces, that is, we can use in a variety of applications of the electrochemical type."
These include extremely efficient electrodes for batteries and fuel cells, they are a cherished goal for autonomous power supplies, portable and transportable power plants, as well as a real breakthrough in solar cell technology.
“Photonic crystals can also be named in this regard,” Greer said. "These structures allow you to manipulate light in such a way that you can completely capture it, which means you can make much more efficient solar cells - you capture all the light and you have no reflection loss."
“All this suggests that the combination of the size effect in nanomaterials and structural elements allows us to create new classes of materials with properties that have never been achievable,” said Professor Greer at the European Organization for Nuclear Research in Switzerland. "The biggest challenge we face is how to scale up and move from nano to the size of our world."
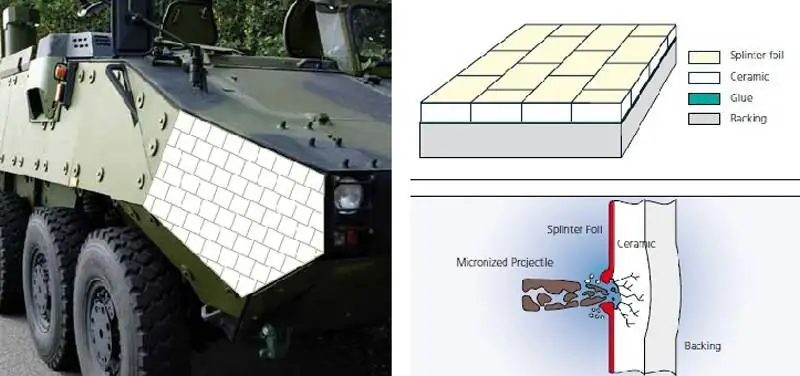
Industrial transparent ceramic protection
IBD Deisenroth Engineering has developed a transparent ceramic armor with ballistic performance comparable to opaque ceramic armor. This new transparent armor is about 70% lighter than armored glass and can be assembled into structures with the same multi-impact characteristics (ability to withstand multiple hits) as opaque armor. This allows not only to dramatically reduce the mass of vehicles with large windows, but also to close all ballistic gaps.
To obtain protection in accordance with STANAG 4569 Level 3, the bulletproof glass has a surface density of approximately 200 kg / m2. With a typical window area of a truck of three square meters, the mass of the bulletproof glasses will be 600 kg. When replacing such bulletproof glasses with IBD ceramics, the weight reduction will be more than 400 kg. Transparent ceramics from IBD is a further development of IBD NANOTech ceramics. IBD has succeeded in developing special bonding processes that are used to assemble ceramic tiles ("mosaic transparent armor") and then laminate these assemblies to strong structural layers to form large window panels. Due to the outstanding characteristics of this ceramic material, it is possible to produce transparent armor panels with a significantly lower weight. The backing, in combination with the Natural NANO-Fiber laminate, further enhances the ballistic performance of the new transparent protection due to its greater energy absorption.
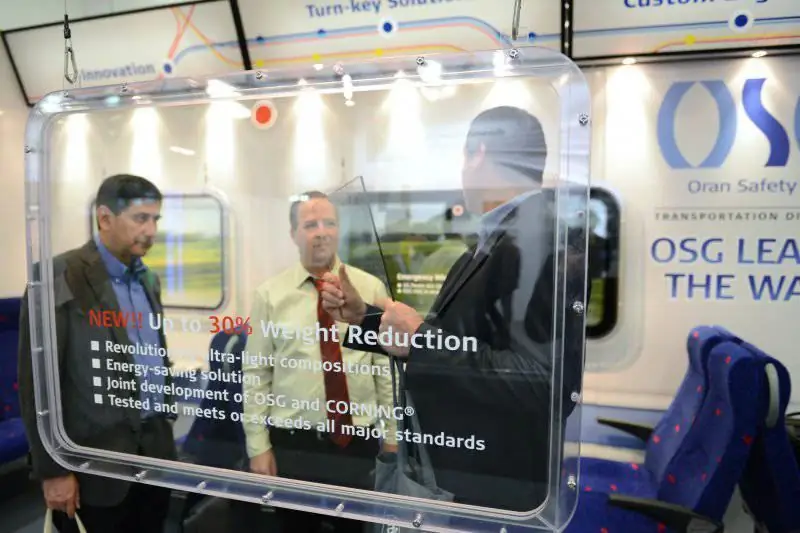
The Israeli company OSG (Oran Safety Glass), responding to increasing levels of instability and tensions around the world, has developed a wide range of bulletproof glass products. They are specifically designed for the defense and civilian sectors, the military, paramilitaries, high-risk civilian occupations, the construction and automotive industries. The company promotes the following technologies to the market: transparent protection solutions, ballistic protection solutions, additional advanced transparent armor systems, digital Visual Windows, emergency exit windows, ceramic windows with color display technology, integrated indicator light systems, shock-resistant glass shields stones, and, finally, ADI anti-splinter technology.
OSG transparent materials are constantly tested in real life situations: repelling physical and ballistic attacks, saving lives and protecting property. All armored transparent materials have been created in accordance with major international standards.