During the development and operation of the Space Shuttle reusable spacecraft, NASA has carried out a large variety of auxiliary research programs. A variety of aspects of the design, manufacture and operation of advanced technology were studied. The purpose of some of these programs was to improve certain operational characteristics of space technology. So, the behavior of the chassis in different modes was studied in the framework of the LSRA program.
By the early nineties, Space Shuttle ships had become one of the main American means of delivering cargo into orbit. At the same time, the development of the project did not stop, now touching upon the main features of the operation of such equipment. In particular, from the very beginning, ships faced certain restrictions on landing conditions. They could not be planted with clouds below 8,000 feet (slightly over 2.4 km) and with a crosswind greater than 15 knots (7.7 m / s). Expanding the range of permitted meteorological conditions could lead to known positive consequences.
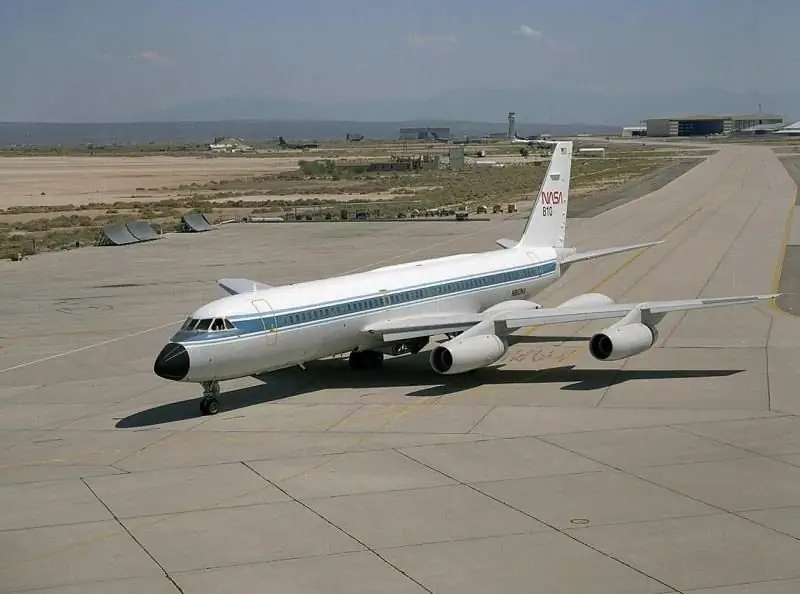
Flying laboratory CV-990 LSRA, July 1992
Crosswind restrictions were primarily related to the strength of the chassis. The landing speed of the Shuttle reached 190 knots (about 352 km / h), due to which the slip, compensating for the side wind, created unnecessary loads on the struts and wheels. If a certain limit was exceeded, such loads could lead to the destruction of tires and to certain accidents. However, the reduction in landing performance requirements should have had positive results. Because of this, a new research project was launched in the early nineties.
The new research program is named after its main component - Landing Systems Research Aircraft. Within its framework, it was supposed to prepare a special flying laboratory, with the help of which it would be possible to check the peculiarities of the operation of the Shuttle chassis in all modes and under various conditions. Also, to solve the assigned tasks, it was necessary to carry out some theoretical and practical research, as well as prepare a number of samples of special equipment.
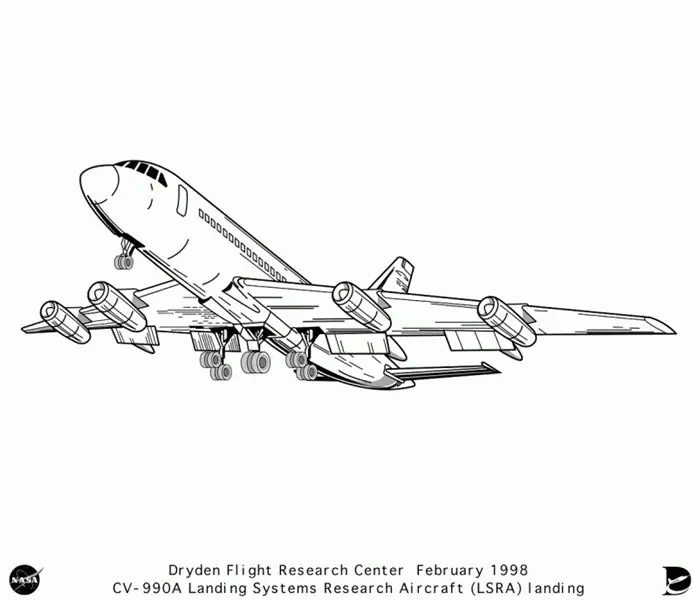
General view of the machine with special equipment
One of the results of the theoretical study of the issues of improving landing characteristics was the modernization of the runway of the Space Center. J. F. Kennedy, Florida. During the reconstruction, the concrete strip with a length of 4, 6 km was restored, and now a significant part of it was distinguished by a new configuration. The 1 km sections near both ends of the strip received a large number of small lateral grooves. With their help, it was proposed to divert water, which reduced the restrictions associated with precipitation.
Already on the reconstructed runway, it was planned to conduct tests of the LSRA flying laboratory. Due to the various features of its design, it had to completely simulate the behavior of a spacecraft. The use of the working strip used in the space program also contributed to obtaining the most realistic results.
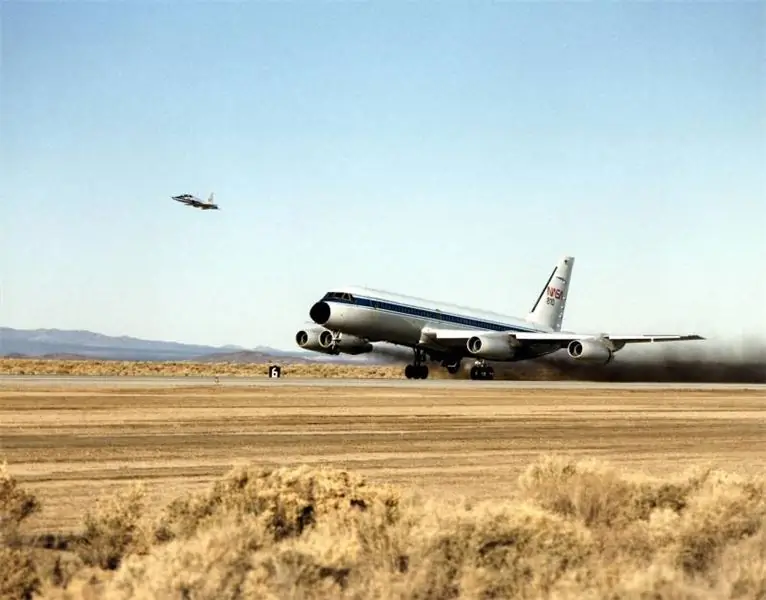
The flying laboratory is landing with the strut extended. December 21, 1992
In order to save and speed up work in the flying laboratory, it was decided to rebuild the existing aircraft. The former passenger liner Convair 990 / CV-990 Coronado became the carrier of the special equipment. The aircraft at NASA's disposal was built and transferred to one of the airlines in 1962, and was operated on civilian lines until the middle of the next decade. In 1975, the aircraft was purchased by the Aerospace Agency and sent to the Ames research center. Subsequently, it became the basis for several flying laboratories for various purposes, and in the early nineties it was decided to assemble an LSRA machine on its base.
The goal of the LSRA project was to study the behavior of the Shuttle landing gear in different modes, and therefore the CV-990 aircraft received the appropriate equipment. In the central part of the fuselage, between the standard main supports, a compartment was located for installing a rack that simulates a spacecraft assembly. Due to the limited volume of the fuselage, such a strut was fixed rigidly and could not be removed in flight. However, the rack was equipped with a hydraulic drive, the task of which was to move the units vertically.
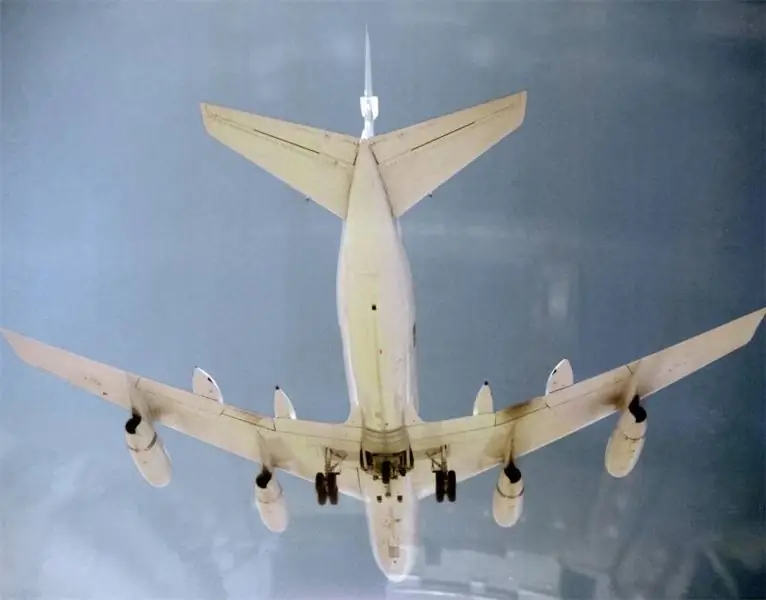
CV-990 in flight, April 1993
The flying laboratory of the new type has received the main strut of the Space Shuttle. The support itself had a rather complex structure with shock absorbers and several struts, but it was distinguished by the necessary strength. In the lower part of the rack, there was an axle for one large wheel with a reinforced tire. The standard units borrowed from the Shuttle were supplemented with numerous sensors and other equipment that monitors the operation of the systems.
As conceived by the authors of the Landing Systems Research Aircraft project, the CV-990 flying laboratory was supposed to take off using its own landing gear and, having completed the necessary turns, to land. Immediately before landing, the central support, borrowed from space technology, was pulled up. At the moment of touching the main struts of the aircraft and compressing their shock absorbers, the hydraulics had to lower the shuttle support and simulate touching the landing gear. The post-landing run was partially done using the test chassis. After reducing the speed to a predetermined level, the hydraulics had to raise the test support again.
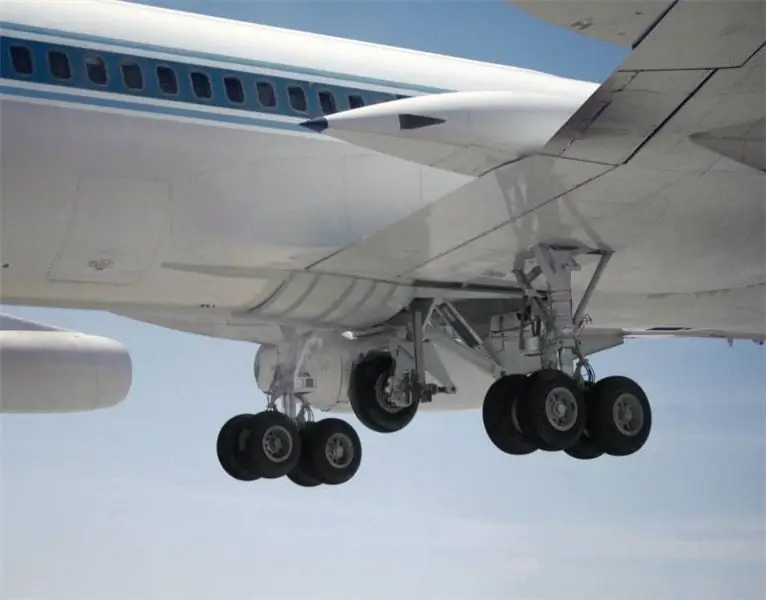
Established main landing gear and research equipment. April 1993
Together with the "alien" strut and its controls, the experimental aircraft received some other means. In particular, it was necessary to install ballast, with the help of which the load on the chassis, inherent in space technology, was simulated.
Even during the development stage of the test equipment, it became clear that working with the test chassis could be dangerous. Hot wheels with high internal pressure, which have experienced serious mechanical stress, could simply explode with one or another external impact. Such an explosion threatened to injure people within a radius of 15 m. At twice the distance, the testers risked hearing damage. Thus, special equipment was required to work with dangerous wheels.
An original solution to this problem was proposed by NASA employee David Carrott. He purchased a 1:16 scale RC model of a WWII tank and used its tracked chassis. Instead of a standard tower, a video camera with signal transmission means, as well as a radio-controlled electric drill, were installed on the hull. The compact machine, dubbed the Tire Assault Vehicle, had to independently approach the chassis of a crumpled CV-990 laboratory and drill holes in the tire. Thanks to this, the pressure in the wheel was reduced to a safe level, and specialists could approach the chassis. If the wheel could not withstand the load and exploded, then people remained safe.

Test landing, May 17, 1994
The preparation of all components of the new test system was completed in early 1993. In April, the CV-990 LSRA flying laboratory took to the air for the first time to test aerodynamic performance. During the first flight and further tests, the laboratory was operated by pilot Charles Gordon. Fullerton. It was quickly established that the shuttle's fixed support, in general, does not impair the aerodynamics and flight characteristics of the carrier. After such checks, it was possible to proceed with full-fledged tests that corresponded to the original goals of the project.
Landing tests of the new chassis started with a tire wear check. A large number of landings have been performed at various speeds within the acceptable range. In addition, the behavior of the wheels on various surfaces was studied, for which the Convair 990 LSRA flying laboratory was repeatedly sent to different aerodromes used by NASA. Such preliminary studies made it possible to collect the necessary information and in a certain way adjust the plan for further tests. In addition, even they were able to influence the further operation of the Space Shuttle complex.
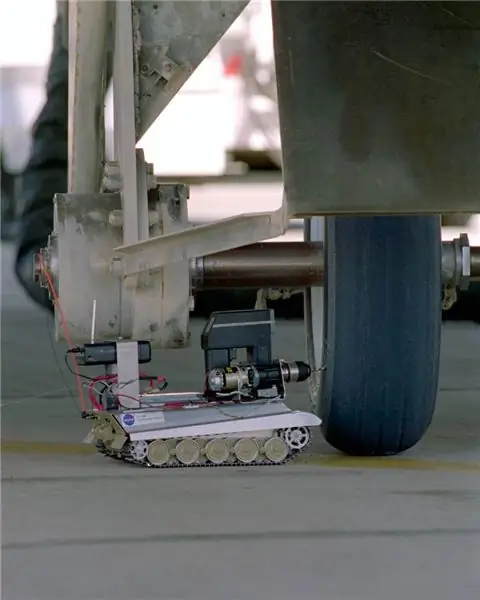
The Tire Assault Vehicle product works with the tire under test. Jul 27, 1995
By the beginning of 1994, NASA specialists began testing other technology capabilities. Now the landings were carried out at different strengths of the side wind, including those exceeding the allowable one for the Shuttle landing. The high landing speed, combined with slip on touch, should have resulted in increased abrasion of the rubber, and new tests were expected to carefully study this phenomenon.
A series of test flights and landings, carried out over several months, made it possible to find the optimal modes in which the negative impact on the wheel design was minimal. With their use, it was possible to obtain the possibility of a safe landing in a crosswind of up to 20 knots (10, 3 m / s) in the entire range of landing speeds. Tests have shown that the rubber of the tires was partially abraded, sometimes down to the metal cord. Despite this wear and tear, however, the tires retained their strength and allowed for a safe completion of the run.
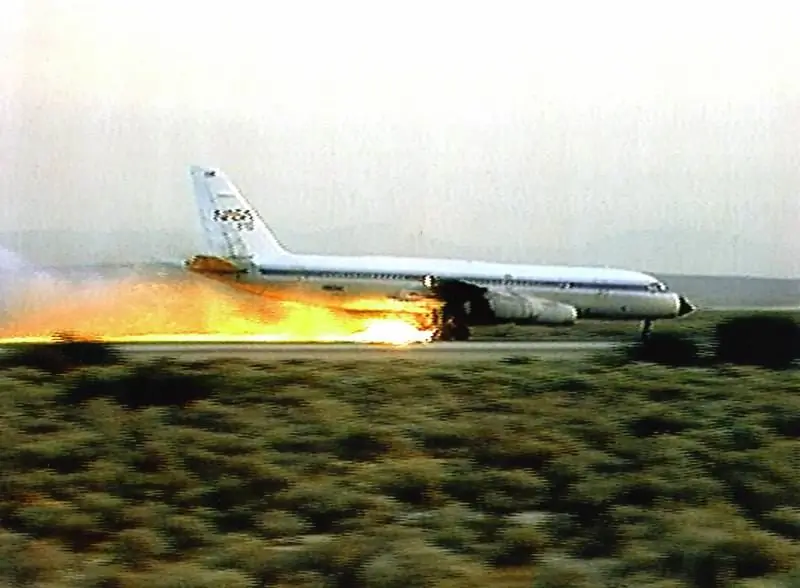
Landing with tire destruction. August 2, 1995
The study of the behavior of existing tires at different speeds with different crosswinds was carried out at several NASA sites. Thanks to this, it was possible to find the best combination of surfaces and characteristics, as well as make recommendations for landing on various runways. The main result of this was to simplify the operation of space technology. First of all, the so-called. landing windows - time intervals with acceptable weather conditions. In addition, there were some positive consequences in the context of the emergency landing of the spacecraft immediately after launch.
After the completion of the main research program, which had a direct connection with the practical operation of equipment, the next stage of testing began. Now the technique was tested at the limit of possibilities, which led to understandable consequences. Within the framework of several test landings, the maximum possible speeds and loads on the spacecraft chassis were achieved. In addition, slip behavior in excess of permissible limits was studied. The chassis components were not always able to cope with the resulting loads.
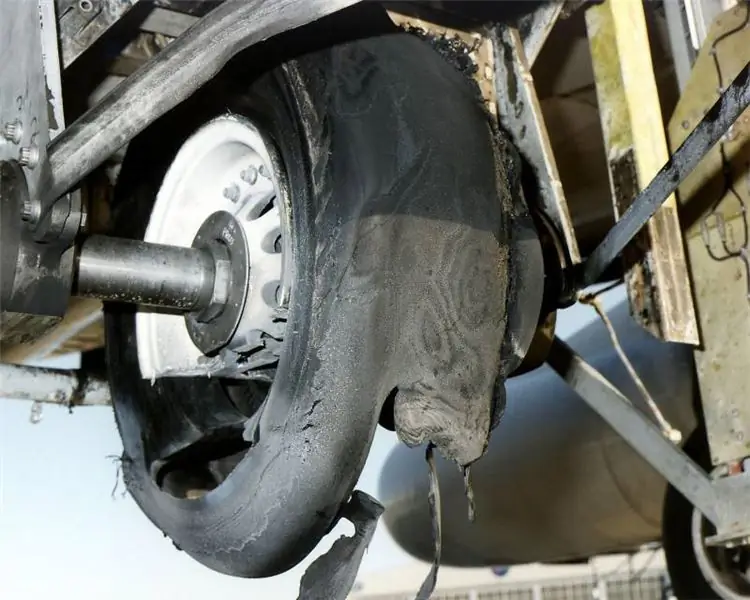
The investigated wheel after an emergency landing. August 2, 1995
So, on August 2, 1995, when landing at a high speed, the tire was destroyed. The rubber was torn; the exposed metal cord could not withstand the load either. Having lost support, the rim slid along the runway surface and grinded down almost to the axle. Some parts of the rack were also damaged. All these processes were accompanied by a monstrous noise, sparks and a trail of fire that stretched behind the counter. Some of the parts were no longer subject to restoration, but experts were able to determine the limits of the wheel's capabilities.
The test landing on August 11 also ended in destruction, but this time most of the units remained intact. Already at the end of the run, the tire could not withstand the load and exploded. From further movement, most of the rubber and cord was torn off. After the end of the run, only a mess of rubber and wire remained on the disc, not at all like a tire.
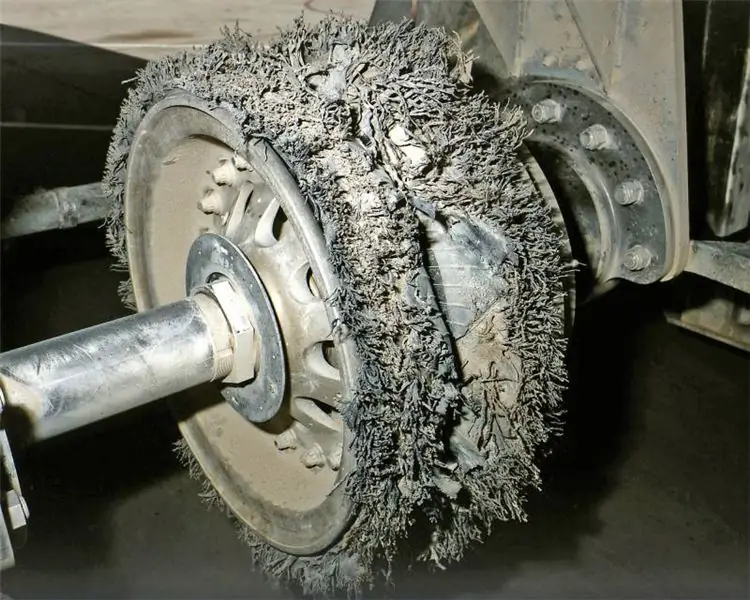
Landing result on August 11, 1995
From the spring of 1993 to the fall of 1995, NASA test pilots conducted 155 test landings of the Convair CV-990 LSRA flying laboratory. During this time, numerous studies have been carried out and a large amount of data has been collected. Without waiting for the end of the tests, experts in the aerospace industry began to summarize the results of the program. No later than the beginning of 1994, new recommendations were formed for the landing and subsequent maintenance of space technology. Soon all these ideas were implemented and brought some kind of practical benefit.
Work under the Landing Systems Research Aircraft research program continued for several years. During this time, it was possible to collect a lot of necessary information and determine the potential of existing systems. In practice, the possibility of increasing some of the landing characteristics without the use of new units was confirmed, which reduced the requirements for landing conditions and simplified the operation of the Shuttles. Already in the mid-nineties, all the main findings of the LSRA program were used in the development of existing guidance documents.

Test landing August 12, 1995
The only flying laboratory on the basis of a passenger liner, used as part of the LSRA project, soon went back to rebuilding. The CV-990 aircraft retained a significant part of the assigned resource, and therefore could be used in one role or another. The research stand for wheel mounting was removed from it and the skin was restored. Later, this machine was again used in the course of various studies.
The Space Shuttle complex has been in operation since the early eighties, but during the first few years, the crews and mission organizers had to comply with some rather tough ones related to landing. The Landing Systems Research Aircraft research program made it possible to clarify the real capabilities of the technology and expand the permissible ranges of characteristics. Soon, these studies led to real results and had a positive effect on the further operation of the equipment.