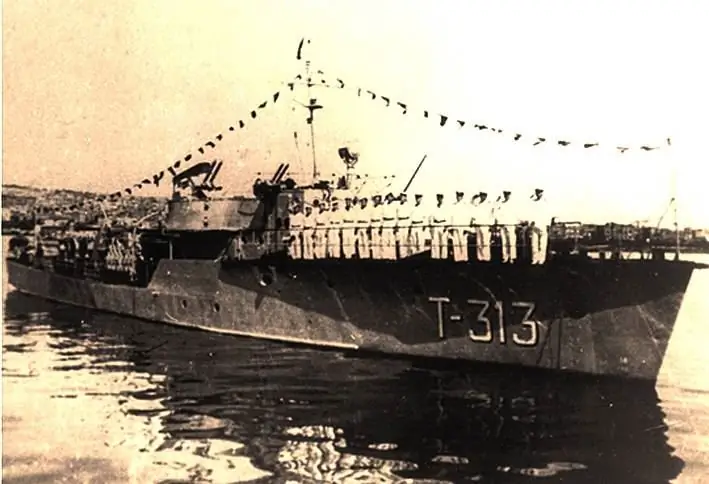
From the first days of the Great Patriotic War, the shipyards of Leningrad restructured their work in relation to wartime conditions. They eliminated combat damage to ships, produced weapons and ammunition, built barges, tenders, pontoons, armored trains, and participated in the creation of defensive lines around Leningrad. The needs of the front demanded the re-equipment of a number of shops at the factories. Separate industries, which were in the immediate vicinity of the front line and were subjected to systematic artillery fire, had to be transferred to more remote areas of the city. After Leningrad was in a blockade on September 8, 1941, the ships of the Red Banner Baltic Fleet were dispersed along the Neva and included in the general defense system of the city, acting as artillery batteries.
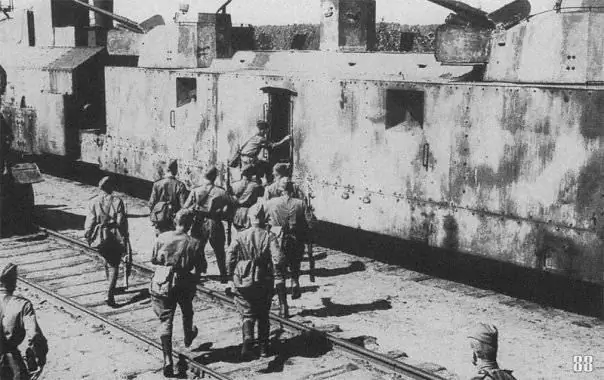
The warehouses had a large number of different armor, therefore, at the suggestion of Lieutenant Commander P. G. Kotov, shipbuilders, in accordance with the decision of the Military Council of the Leningrad Front, began the production of mobile defense means: artillery pillboxes, machine-gun points, shelters for snipers, command and observation posts, etc. For a year and a half, from August 1941 to January 1943, the factories manufactured and installed on the front line more than 7000 armored structures, for the manufacture of which 18400 tons of ship armor were used. Used for defense needs and long-range naval guns. They were installed on railway platforms, protected by ship armor and sent directly from the factories to the combat lines.
On the destroyers Strogiy and Stroyny, which took up combat positions near the Nevsky forest park and in the area of the Ust-Izhora village, the shipbuilders completed the installation work, which allowed the ships' artillery mounts to be put into operation on August 30, 1941. The ships and destroyer personnel had to work under systematic shelling and bombing, in a difficult time of siege, but in a short time they completed all the necessary complex of work on the ships.
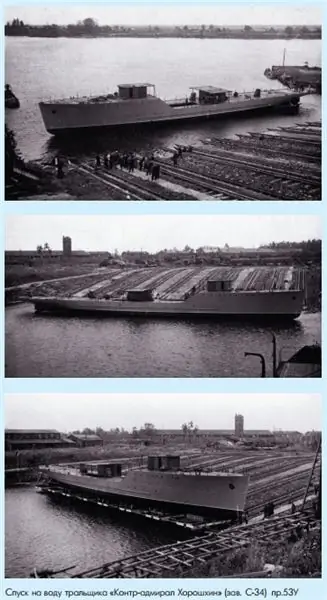
A great achievement of the Petrozavod team during the war was the delivery of minesweepers to the fleet. Throughout the war, Leningrad shipbuilders carried out a large amount of work on combat repair of ships. So, in 1941-1942 they repaired the battleship "October Revolution" after being hit by air bombs, restored the cruiser "Maxim Gorky" and the destroyer "Terrible", which were blown up by mines, the leader "Minsk", sunk during enemy bombing. Various kinds of repair work were carried out on the cruiser Kirov, the destroyer Vice-Admiral Drozd, the minelayer Ural, several base minesweepers and submarines.
At the end of December 1941, six base minesweepers of the "Verp" type approached the wall of Petrozavod, which took part in the evacuation of the garrison from the Hanko Peninsula, which took place in difficult ice conditions. Two ships had significant damage to the bow ends from the stem to the bulkhead of the fifth frame, which captured the underwater part of the hull to a considerable depth. The Military Council of the KBF took only three and a half months to complete all the work. In the absence of a dock, the only correct decision was made to repair the bow extremities with the help of caissons. It should be emphasized that during the Great Patriotic War, shipbuilders and naval sailors created an extensive caisson economy and gained extensive experience in the use of caissons. They were used at many unequipped bases to provide repairs to the underwater hulls of various ships. In total, about a hundred ships and auxiliary vessels were restored with the help of caissons during the war period.
Petrozavod made two wooden caissons of the same size. They had a transverse set of pine beams, on top of which a sheathing of pine boards was horizontally installed. To ensure watertightness, the grooves between the sheathing boards were putty and filled with pitch; in addition, the sheathing was pasted over with canvas on red lead. The cutout in the aft wall of the caisson was made according to the plaza pattern. To prevent outboard water from penetrating at the junction of the minesweeper's hull and the caisson, a felt cushion upholstered with canvas was installed along its section. Due to the fact that we worked in winter conditions, we had to cut ice around the bow ends and make lanes for the factory caissons. In the aft part of each caisson (along the contour), a steel panel with butts at the deck was installed and steel cables were brought in, with the help of which the entire structure was tightly crimped. To keep the caisson on an even keel after putting it under the ship and pumping out the water, two wooden beams were provided in its bow, passed into the side anchor haws; in addition, the ship's anchor-chain was laid on the deck of the caisson.
It was not possible to restore the bow ends of the riveted hulls of the minesweepers in their original form, since there were no riveters at the factories. Electric welding was used, and all the work was carried out by the forces of the ship's personnel under the guidance of factory foremen. The repair of six minesweepers was completed exactly on time, and in the spring campaign of 1942 they went into combat trawling.
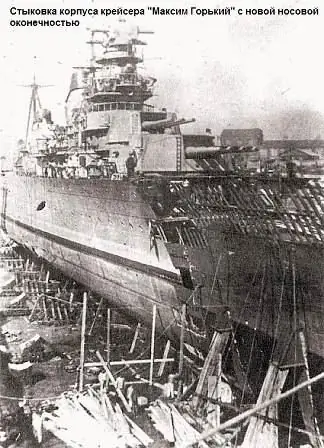
During the war years, the ships of the Red Banner Baltic Fleet often had to sail in ice conditions, which inevitably led to damage to the propeller blades. Due to the high workload of the docks, the repair and replacement of the propellers was carried out in most cases by the method of trimming the ship. It was especially widely used on ships of small displacement. So, for example, in 1941 and 1943 at Petrozavod the screws on minesweepers of the "Verp" type were replaced with the help of trimming; the stern ends were lifted by a stationary coastal boom equipped with hoists and two cargo hand winches with a carrying capacity of 3 tons. To increase the trim, liquid ballast was taken into the bow compartments of the ships, and solid ballast was laid on the forecastle. The stern was raised until the propeller hubs emerged from the water. Then a special raft was brought in, the buoyancy of which was enough to accommodate a brigade of locksmiths with the necessary tools and devices and the propellers themselves. The method of trimming for replacing propellers became widespread during the war years, both on warships and on ships of the merchant fleet.
To repair the bottom-outboard fittings and eliminate local damage to the hull at a small depth from the waterline, the ship inclining method was used by receiving water, pumping fuel or laying solid ballast on the deck at the edge of the corresponding side. Using this method, the citizens of Petrozavodsk in 1943 installed electric welding overhead sheets along the ice belt of the outer skin of the "Verp" type minesweepers; as a result, the ships were able to navigate in difficult ice conditions.
The short time allotted for the implementation of repair work, an acute shortage of materials and other difficulties of the blockade time constantly forced shipbuilders to look for ways out of critical situations. For example, when restoring the bow end of the destroyer Sentorozhevoy, torn off by the explosion of a torpedo, the Balts used the hull set of the end of the destroyer of another project, which was close in contours to the ship being repaired. The bow end of the cruiser "Maxim Gorky" was also restored.
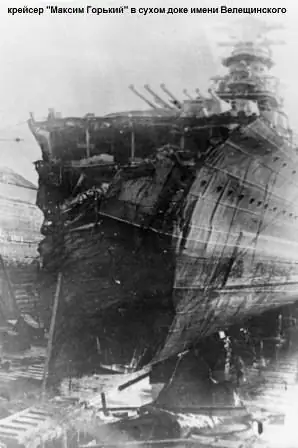
The Leningrad shipyards did not stop working for the needs of the front even in the most difficult months of the blockade. The winter of 1941/42 turned out to be especially cold and hungry. Public transport did not work, and the weakened people living far from their factories could not get to work. And the assignments for the repair of ships, for the production of weapons and ammunition continued to come in. Under these conditions, the administration of the factories organized trips to the homes of the workers; the completely weakened were sent to factory hospitals, where they received enhanced nutrition, after which they returned to work. So, at Petrozavod in mid-January 1942 only 13 people could work, by February 1 - 50; by mid-April, when the supply of food to the city had improved somewhat, 235 people were already employed in the repair of ships. No difficulties and hardships could prevent the workers from fulfilling the tasks assigned to them to ensure the combat effectiveness of the ships.
Frequent interruptions in the supply of electricity from the city grid forced shipbuilders at each enterprise to solve this problem in their own way. The Baltic, for example, used diesel generators of a floating crane with a total capacity of 2000 kW; and a reserve power plant with a capacity of 800 kW was equipped under a large slipway. At some factories, electricity was supplied to the workshops and to the stocks from ship generators. So, using ship DC diesel generators for the production of electric welding during the repair of minesweepers, at Petrozavod they achieved the characteristics required for welding with the help of ballast rheostats. When performing pneumatic work, ship compressors were used.
In the difficult winter of 1941/42, the blockade, the main supply of Leningrad was carried out along the ice Road of Life. But how will it be possible to ensure the massive transportation of goods with the onset of spring, when the ice melts, especially since there were clearly not enough ships on Ladoga? Having considered this issue, the State Defense Committee in March 1942 ordered the Leningrad shipbuilders to build an appropriate number of barges. Since the enemy occupied the left bank of the Neva at the Ivanovo rapids, ready-made ships could not be transported to Ladoga. Therefore, we decided to assemble the sections in Leningrad, deliver them by rail to Ladoga and then weld them on the slipway in Golsman Bay. The shipbuilders built the first barge in just 20 days. In April, the construction of small self-propelled ships began at almost all shipbuilding enterprises in Leningrad.
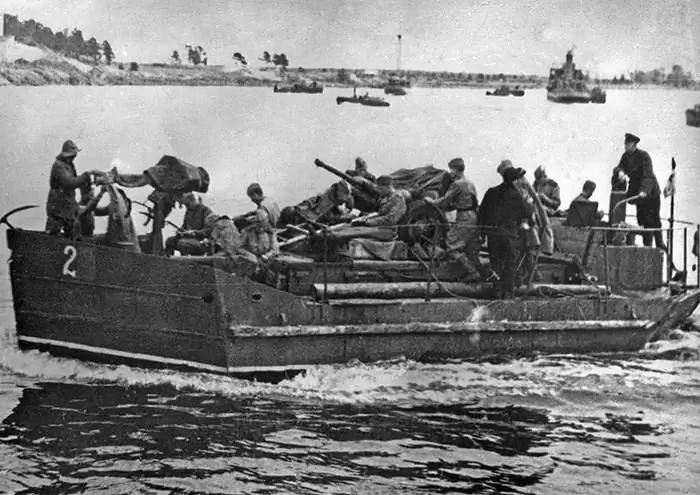
Those that were built, for example, at Petrozavod, received the name of a tender and had a carrying capacity of 10 tons (length 10, 5, width 3, 6, side height 1.5 m). To simplify the technology of metal processing and assembly of sections, the tender had straightened contours; The hull of a welded structure was assembled on a slipway from large sections: bottom, side, stern, bow and deck. A watertight bulkhead divided the ship into two compartments - aft (engine compartment) and bow (cargo hold). A 75 hp ZIS-5 automobile engine was used as the engine. sec., providing a speed of about 5 knots. The team consisted of a minder and a helmsman. On June 1, 1942, the first tenders and pontoons were shown to the members of the Military Council of the Leningrad Front. Until the end of the year, the Leningrad shipbuilders handed over to seamen only tenders over 100 units. The Ladoga military flotilla, reinforced by built ships, transported about 1 million tons of cargo and almost 1 million people, including 250 thousand soldiers and officers, over the summer of the same year.
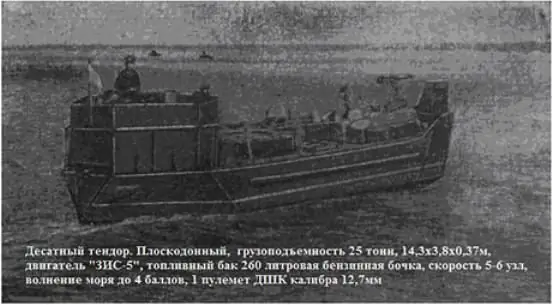
During the blockade of Leningrad, the front line passed four kilometers from the territory of the Ust-Izhora shipyard, so its main production had to be transferred to the city. The great need for minesweepers forced the Military Council of the Leningrad Front to mobilize all possible resources for the early introduction of minesweepers. A number of Leningrad factories received an order for the construction of small minesweepers. In the fall of 1942, a large group of naval sailors with experience in hull work was sent to the Ust-Izhora shipyard to help a small team of shipbuilders.
In the period of preparation for the complete defeat of the fascist troops near Leningrad, the question arose of the covert transfer of the 2nd Shock Army of the Leningrad Front to the Oranienbaum bridgehead. This important operation, which began in November 1943 and ended in January 1944, involved minesweepers, network minelayers and other floating craft. Its implementation was complicated by the difficult ice situation and the impossibility of using icebreakers due to the shallow depths of the Petrovsky Canal, which was used for covert escort of ships near the enemy-occupied shores. The role of icebreakers was assigned to shallow-draft base minesweepers, on which they not only reinforced the hulls, but also replaced the standard propellers with special ones intended for navigation in ice. Overhead steel sheets were welded along the ice belt of the outer skin, and in the area of the waterline, along the bulkheads and frames in the bow end, spacer wooden beams were installed. The hulls of the minesweepers, reinforced in this way, withstood sailing well in ice conditions.
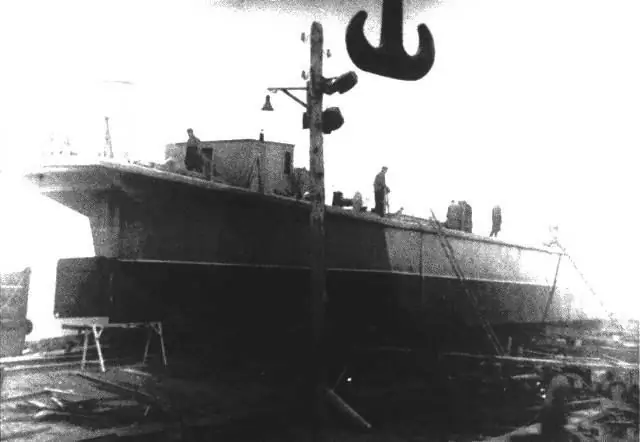
The need for sweeping operations in the shallow waters of the Baltic, which the Germans "stuffed" with many different types of mines, dictated the need to create a small minesweeper. The development of the project began on the mainland in July 1941. And in Leningrad, the documentation for the new "sea boat-minesweeper" of project 253 came already during the blockade. The artillery armament of the developed minesweeper was designed, first of all, to fight enemy aircraft and small ships. The ship was supposed to carry a sufficiently powerful and diverse trawling armament, which made it possible to destroy all types of mines known at that time in shallow water conditions. The minesweeper's displacement was 91, 2 tons, length 31, 78 m.
The main drawback of the project was the fact that the designers did not take into account the specific conditions of Leningrad. The outlines of the ship were drawn with classical curved curves, which necessitated complex, "hot" work on the bending of steel sheets. In addition to obvious technological difficulties, these processes required significant consumption of fuel and electricity, which was an unaffordable luxury for besieged Leningrad, since their value was equated to bread. Therefore, the specialists of the design bureau, which brought together almost all the engineers available in Leningrad, began to radically revise the project. The displacement of the ship was increased, the curvilinear complex contours of the bow and stern were replaced with multifaceted ones, which were formed by flat sheets. The experience of combat trawling accumulated in the Baltic during the first years of the war was also taken into account. This caused significant changes in the design of the all-welded hull with equipment, in addition, another gun appeared on the minesweeper's tank. As a result, a new project turned out, which was significantly different from the 253rd, so the letter L was added to the main index - "Leningrad". The production of working drawings and the start of construction began virtually at the same time. And when the draft design was sent for approval to Moscow, the first copies of the minesweepers were already afloat, and equipment and weapons were mounted on them.
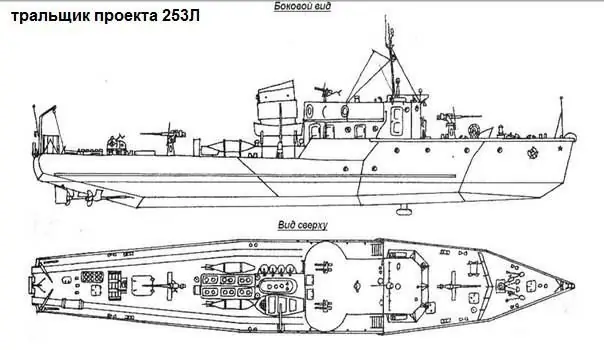
The head "hundred-ton" went for testing at the very beginning of November 1942. In the same month, the first minesweeper of Project 253L entered the Baltic Fleet. The sailors noted that ships of this type had good seaworthiness and fire properties and quite acceptable speed, which was little influenced by the "blockade" flat contours. The mass production of "hundred-ton" ships made it possible for the Baltic sailors to fully deploy sweeping operations at sea in the second half of the war and in the first post-war years. Also, in the conditions of the blockade, the Leningraders created such new types of ships as armored sea hunters, skerry monitors. It must be said that the creation of minesweepers took place in the extremely difficult conditions of besieged Leningrad and were carried out at the cost of real labor heroism of shipbuilders. Suffice it to say that during the delivery of the lead minesweeper, the KB personnel lost about two-thirds of their number, only the most persistent and physically enduring remained, who withstood the most difficult blockade conditions - hunger, cold, deprivation, the death of loved ones.