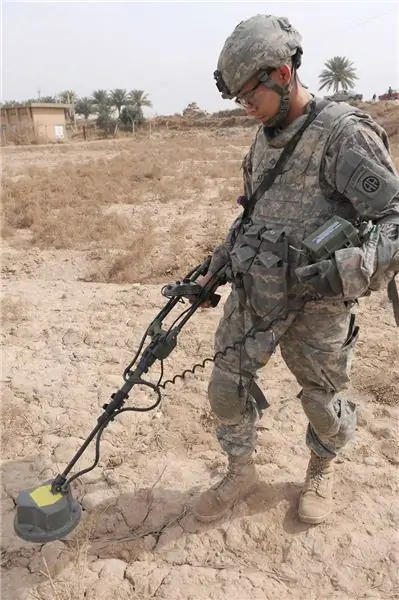
Counterinsurgency and asymmetric hostilities in recent years have once again brought close attention to mines and improvised explosive devices (IEDs). The use of mines and to some extent booby traps (an early term for IEDs) was part of the Western strategy during the Cold War. They could be used to deter hypothetical Warsaw Pact attacks on NATO. They also had a significant impact on operations in Vietnam, border conflicts in South Africa and most of the "small wars" of the late 20th century.
More recently, mines, and especially IEDs, were widely used in conflicts in Iraq and Afghanistan (although to this day news feeds are full of reports of terrorist attacks in these countries). Although some new technologies were later introduced, such as remote detonation of explosives using electronic warfare, the essence of efforts to combat mines and IEDs remains the same - to detect and / or neutralize them before they detonate.
Handheld detectors
Since the advent of the technology of detecting metal objects using an electromagnetic field, sappers with hand-held mine detectors working in front of the main units have become part of the standard demining tactics. These systems are typically a rod with a finder at the end that alerts the operator when an iron or iron alloy is found. Signal strength can indicate the size of an object. The potential object is marked and then can be identified as a real threat or not. According to Clay Fox of Vallon, a leader in mine and explosives detection technology, “The problem is how the detectors respond to what may or may not be a mine. That is, it may happen that this sensor alone may not be enough. In addition, non-metallic mines are often used, made without the addition of metal or with a minimal addition of metal. Therefore, the Vallon Mine Hound VMR3 combined mine detector uses a search head with a metal detector (induction principle) and a subsurface sensing radar (ground penetrating radar principle). The Marine Corps purchased Mine Hound mine detectors for use in Iraq. The US Army has signed a contract with L-3 SDS to develop the AN / PSS-14, a similar two-channel system also with an induction metal detector and ground penetrating radar. The ground penetrating radar emits a low-frequency signal, which detects violations of the integrity of the soil, is reflected back to the receiving antenna and processed by the processor. Improved signal processing algorithms eliminate “noise” (ie, false targets) and classify those objects that may be real mines.
Identified mines can either be physically removed from the deployment site or detonated in situ using a charge. Extraction can be potentially dangerous if the device has been laid with additional traps to prevent it from moving. Fox further clarified that “performance is not the only criterion for a mine detector. Weight, dimensions and ease of use are also very important parameters. This is why Vallon has incorporated advanced electronics into its product that significantly reduce size and weight.”For example, with a mass of only 1.25 kg, the VMC4 can detect explosive devices in metal and dielectric housings and short wires.
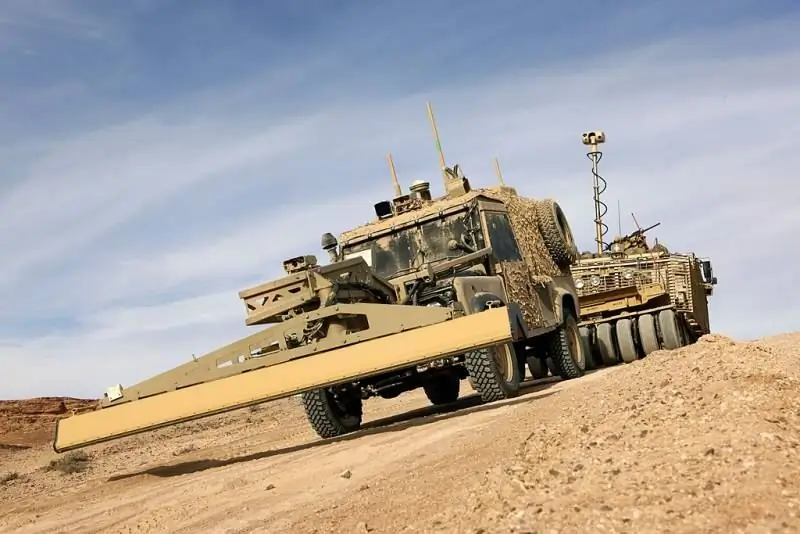
Vehicle systems
Manual demining has its drawbacks: firstly, this process is rather slow, and secondly, demining groups are defenseless against enemy fire and can be injured when a mine or IED detonates. Mine reconnaissance systems for vehicles are designed to search and detect (often while driving) all kinds of mines and IEDs placed on and along roads. Demining engineering vehicles are used to create passages in explored minefields.
Self-propelled systems for detecting mines and IEDs, as a rule, include a sensor kit installed in front of the vehicle, inside which the driver and operator are placed under the protection of armor. The Husky Mark III VMMD system was originally developed by the South African company DCD Protected Mobility (DCD). In front of the cab, located between the front and rear wheels, a subsurface radar from NIITEK Visor 2500, consisting of four panels with a total width of 3.2 meters, is installed. Husky can clear a three-meter wide passage, moving at a maximum speed of 50 km / h, when detected, it marks the location of an explosive object for its neutralization by specialized systems following it. The platform also has an NGC LN-270 inertial navigation system with GPS and a SAASM anti-jamming module, it is possible to add a See-Deep Metal Detector Array. With low ground pressure, the Husky platform is free to ride over high power anti-tank mines, while the cockpit and V-hull provide protection against a variety of lower power devices. The newest variant of the Husky features a two-seater cockpit for the driver and the sensor operator.
The VDM system from MBDA is equipped with a 3, 9 meter wide boom-mounted device for remote activation of an IED, a bottom-mounted metal detector and an automatic track marker. The VDM platform can accept additional sensors, but also work as part of a route clearance team. The combat experience of the French army has shown that the VDM system can clear 150 km in a day, moving at a maximum speed of 25 km / h.
Mobile striker trawls
There is a distinction between “careful clearance” and “violent clearance”. The second method is for the most part compulsory and involves the use of striking trawls and explosives. Chains appeared during World War II, when similar systems were installed on British tanks. Typically, this is a mechanically rotating drum with flails attached to it, mounted on brackets at the front of the machine. When the drum rotates, the flails, to which weights or hammers can be attached, hit the ground, thereby detonating mines and IEDs.
The Aardvark system from the British company Aardvark Clear Mine is a typical representative of such systems. A drum with replaceable flails rotates at a speed of 300 rpm, two operators are housed in an armored cabin. In 2014, the US Army began deploying its own M1271 live trawl, based on a 20-ton heavy tactical truck. It is equipped with foam filled wheels, a blast guard and 70 flails / hammers; during operation, the platform moves through the minefield at a speed of 1.2 km / h. The vibration is so great that the crew members sit in air-suspended seats. Other solutions, such as the PTD Mine from the Italian FAE Group, use modified heavy construction platforms. The advantage of such solutions is that parts for them and their service are already available in the commercial market and are often preferred to be used in humanitarian demining operations. In addition, FAE machines are remotely controlled. Pull trawls are a faster solution than other demining methods, but on the other hand they are limited to open spaces.
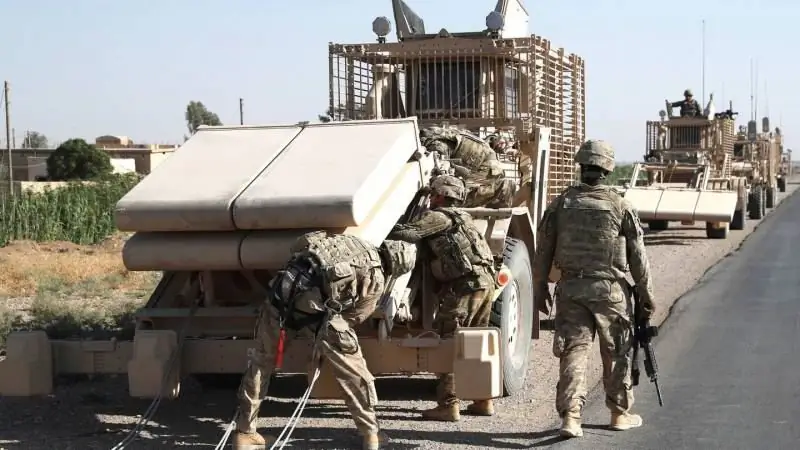
Machine-mounted rollers and plows
Another method of demining is the use of rollers installed at the front of the machine. They can often be mounted on standard tactical platforms ranging from main tanks to light wheeled and tracked vehicles. In fact, in this case, minimal modification is required - the installation of intermediate brackets between the machine and the roller system. The lightweight Spark II (Self Protection Adaptive Roller Kit) roller trawl from Pearson Engineering, specially designed for use on mine-protected wheeled vehicles, uses hydraulics to create the necessary pressure and air suspension to ensure that the rollers follow the ground contours. This is especially important in the full width clearance that the Spark II provides, as a mine can be missed if the roller is not in constant contact with the ground. In addition to full-width options, track mine sweepers are widely used, which are more common on heavier armored vehicles. They cover only the width of the tracks or wheels, but they weigh less and require less power to create pressure.
Mine plows (knife trawls)
The Pearson lightweight roller trawl LWMR (Light Weight Mine Roller), proven in real combat conditions by the American and Canadian contingents, can be installed on light combat vehicles, including the LAV and Stryker. A Rear Roller Kit (RRK) (one set of six individually suspended wheels) can be added to provide protection for vehicles following behind. In addition, the AMMAD (Anti Magnetic Mine Activating Device) system can be connected to groups of rollers to detonate anti-tank mines with a magnetic fuse and mines with a rod fuse. These mines detonate under the hull as the vehicle passes over them. The rollers perform well on hard ground, but will get bogged down on soft ground and mud.
Mine plows are installed and used in the same way as roller trawls. But their main element is knives or long teeth that dig into the ground and overturn buried mines. Pearson literature states that "mine plows require a more powerful carrier platform with good traction, so they are usually mounted on tracked vehicles." The clearing machine based on the M1 tank includes a mine plow, modified so that it can be accommodated on a multi-purpose landing craft. However, mines and IEDs are not always buried, which is why Pearson also offers a surface mine plow or knife. The Surface Mine Plow (SMP) practically slides along the flat surface of a road or trail, safely pushing aside mines and debris that could potentially be IEDs.
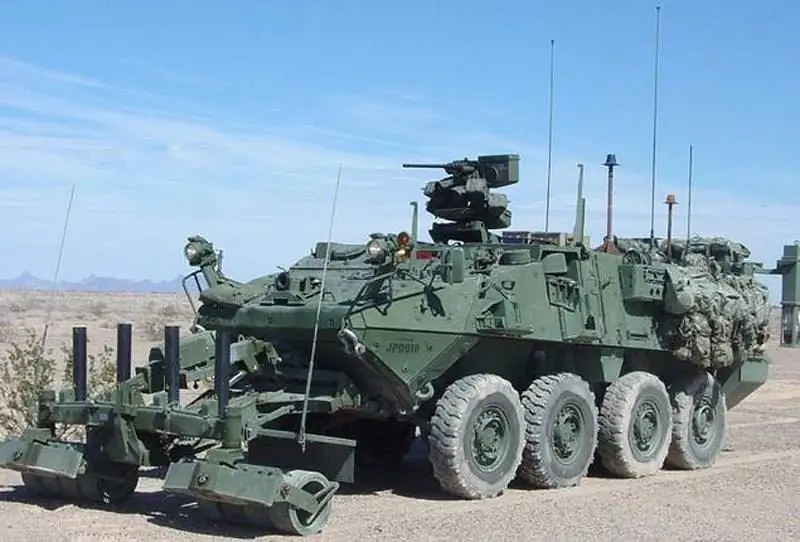
Linear charges
Explosive linear charges are specially designed for clearing and making passages in a minefield. The method is fast and destructive. Typically, the system is a group of explosive charges connected by a cable attached to the missile; the whole set is placed in a large box or on a special pallet. In the BAE Giant Viper system and its Python receiver, the linear charge set is placed on a trailer, often towed by an engineering combat vehicle or tank. After launch, the rocket pulls a chain of charges, which, after running out of fuel, falls to the ground along the area to be cleared. When the charge is detonated, an excess pressure is created, which causes the detonation of nearby mines. A system of this type cleans a passageway 8 meters wide and 100 meters long. The Americans are also armed with a similar system on a trailer, called MICLIC (MineClearing Line Charge). Other countries, including India and China, are also producing such systems. Linear charges are standard equipment on Maine's ABV punching machine.
There are also smaller systems specifically designed for dismounted infantry. They destroy anti-personnel mines, IEDs, booby-traps and tension mines. The size of the clearing passage depends on the size and weight of the system, which in turn directly affects its suitability for transport.
Mine disposal machines and IEDs
Many of the deployed mine and IED systems are designed to operate in more traditional minefields, placed along troop routes or as defensive obstacles. IEDs pose new challenges, such as the fact that they are often installed off-road and in hard-to-reach places that can only be reached on foot. The Buffalo platform, originally manufactured by Force Protection Industries (now part of General Dynamics Land Systems), allows the demining / route clearance team to identify and neutralize IEDs under armor protection. The Buffalo has a very high ground clearance and a V-shaped body for explosion protection. The armored cockpit has large windows so that the crew members, from 4 to 6 people, have a better command of the situation and identify possible threats. The machine also has a 9-meter-long arm-manipulator controlled from the cab with various hinges, which is used to excavate debris that can hide an IED, to determine the type of device using a video camera installed on the manipulator and dig or retrieve a mine or IED. Six countries operate the Buffalo platform, including the US, UK, France, Italy, Canada and Pakistan.
The unique capabilities of Buffalo have been implemented on other machines of the MRAP category (with increased protection against mines and improvised explosive devices) due to the installation of similar manipulator arms on them. Manipulators are also being further enhanced by the addition of various sensors, including chromatographic detectors, thermal imaging cameras, electromagnetic radiation sensors and other technologies that help to better recognize suspicious objects.
Jamming IED
The advent of radio-controlled IEDs (REDs), often detonated with a simple mobile phone, has created a new problem. These IEDs can detonate remotely at the command of the operator, who can choose the moment of detonation of the device. This makes them more effective, as they can be targeted and harder to counter. To neutralize the RSVU and other remotely controlled devices, signal jammers were adopted. An MBDA spokesman said that "the experience of the French army in Afghanistan and Mali has shown that the use of a silencer is essential to the survival and effectiveness of the route clearance team."
Most of the RSVU mufflers are installed on vehicles. The US Army operates an SRCTec Duke V3, and the Marine Corps operates a CVRJ (CREW Vehicle Receiver Jammer) system from Harris. The modular jamming system STARV 740 from AT Communications, designed to protect transport convoys, automatically scans the frequency bands in random order, identifies and jam the signal. Such systems consume a lot of energy and weigh between 50 and 70 kg.
For a dismounted soldier, light weight and low power consumption are critical factors. The US has developed and deployed the THOR III portable backpack system. Three separate blocks provide complete frequency jamming. Its further development is the ICREW system, which has further expanded the protected ranges and capabilities. Ideally, multiple such systems should be in place to create a protective dome in which the team can operate safely.
Robotic mine action systems
To create autonomous systems currently appearing on the market, either existing machines are used, which are equipped with subsystems for autonomous navigation and driving, or specially designed land-based robotic systems (SRTK). The US Army operates its AMDS system, which has three modules deployed as needed on the Man Transportable Robotic System (MTRS) remote-controlled robot. Supplied by Carnegie Robotics, they include a mine detection and marking module, an explosives detection and marking module, and a neutralization module.
Since 2015, Russia has also been armed with the Uran-6 SRTK developed by OJSC 766 UPTK, which was widely used by the Russian military in Syria. Weighing 6,000 kg, this multifunctional system can be equipped with a variety of tools, including a dozer blade, a manipulator arm, a cutter, a roller trawl, a striker trawl and a gripper with a lifting capacity of 1000 kg. One operator controls Uranus using four video cameras and a radio control system with a range of one kilometer. The American company HDT has successfully demonstrated its Protector robot with a striking trawl. Devices under the blows of this minitral break rather than detonate. In addition to specialized robotic systems, explosive ordnance disposal robots, which are also capable of identifying and neutralizing single threats, are becoming increasingly common.