Working on projects for promising high and ultra-high cross-country vehicles, SKB ZIL by the mid-sixties created a large number of all-terrain vehicles of various types and with different characteristics. Experienced and serial wheeled vehicles showed high performance and successfully completed the assigned tasks. However, these successes did not stop the development of a promising direction and the further growth of cross-country characteristics. Soon, the first developments in the field of the so-called. auger-rotor snow and swamp-going vehicles. The first machine of this type under the brand name "ZIL" was the experimental model ShN-67.
By 1966, specialists from the ZIL Special Design Bureau, headed by V. A. Grachev found all the main ways to obtain the maximum possible characteristics of a wheeled all-terrain vehicle. Further development of such a technique was associated with the renewal of certain units, the use of new approaches, etc. At the same time, in parallel, it was possible to test completely new original ideas affecting the architecture of the chassis. Having received such an opportunity, the Plant named after. Likhachev took advantage of it.
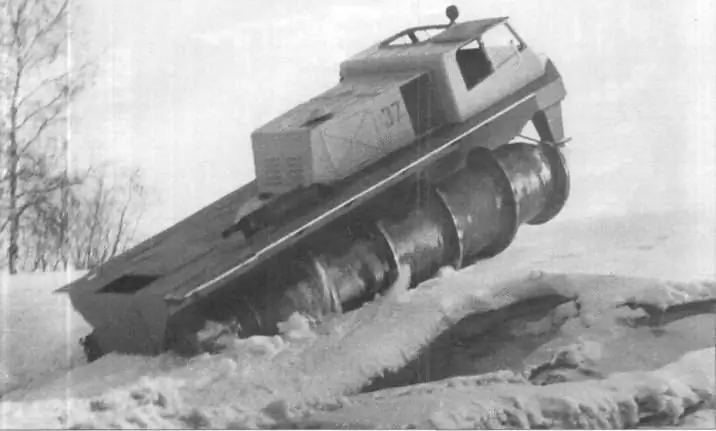
ShN-67 all-terrain vehicle on the snow
In 1966, the designers of SKB ZIL were able to get acquainted with an advertising film dedicated to a new experimental American-designed all-terrain vehicle. An unusual car from Chrysler was equipped with a chassis in the form of a pair of rotary-screw units that served as a propulsion device. As a result of watching a movie, it was decided to launch its own research program for a specific chassis. The first results in the framework of research work were planned to be obtained already this year.
Over the next few months, SKB ZIL exchanged experience with other automotive organizations that had already launched their projects of rotary-screw propellers. By the beginning of 1967, a certain amount of experience had been accumulated, which made it possible to start developing its own prototype.
For a number of reasons, in the documents of the SKB, the rotary-screw propeller was listed under the name of the screw or screw-rotor. This naming feature was reflected in the working title of the pilot project. The all-terrain vehicle was designated as SHN-67. The numbers indicated the year of creation. The designers and testers also gave the project a nickname - "Auger". It should be noted that in the future, the ShN-67 project was finalized, after which it was renamed into ShN-68, again according to the year of work.
Experimental vehicle SHN-67 was created as a demonstrator of technology, and therefore no special requirements were imposed on it. It was supposed to have a simple enough design to test the main bold ideas. To speed up construction, it was proposed to use the maximum possible number of ready-made components and assemblies. At the same time, certain products had to be developed and assembled from scratch.
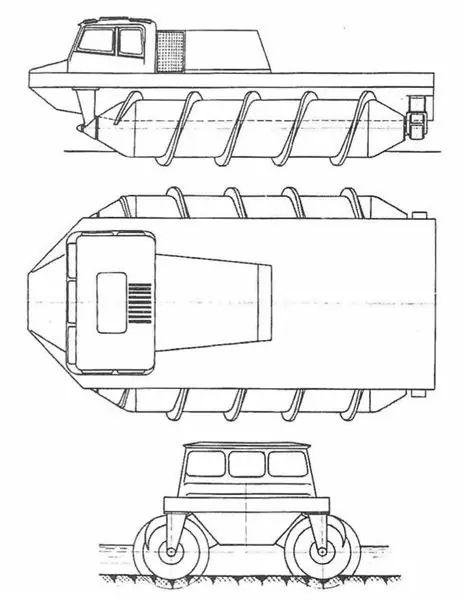
Machine diagram
Especially for the new project, it was necessary to develop a case of a non-standard design. It was based on a frame made of metal profiles, on which sheet sheathing was installed. The body was formed by several basic devices. So, its lower part was a kind of boat with a trapezoidal cross-section. The bow of the hull expanded, after which the cross-section of the units did not change until the very stern. Above the inclined sides of the "boat" were placed two developed shelves, the upper part of which was connected to the roof-deck of the hull. In the front of the hull, it was planned to place the crew cabin, behind which there was a box-shaped engine casing.
In the middle part of the frame, inside the "boat", a gasoline engine ZIL-375YA with a capacity of 180 hp was placed. The engine was connected to the so-called. main gear and swing mechanism, borrowed from the tracked vehicle M-2 from OKB MMZ. The delivery of torque to the propeller was carried out through a pair of inclined shafts located in the rear of the hull. They passed through the propeller legs and, with the help of reverse gears, built on the basis of the gears of the final drives of the ZIL-135L all-terrain vehicle, transferred power to the augers.
The fuel system of the all-terrain vehicle was based on the serial units of the ZIL-157 vehicle. The electrical equipment was borrowed from the ZIL-130 truck almost without modifications.
In the front part of the hull, under the side shelves, there were vertical supports with a movable mount for the front axles of the auger propeller. In the stern of the hull, on its inclined sides, a pair of larger and more voluminous racks were placed, in which the transmission devices were placed.
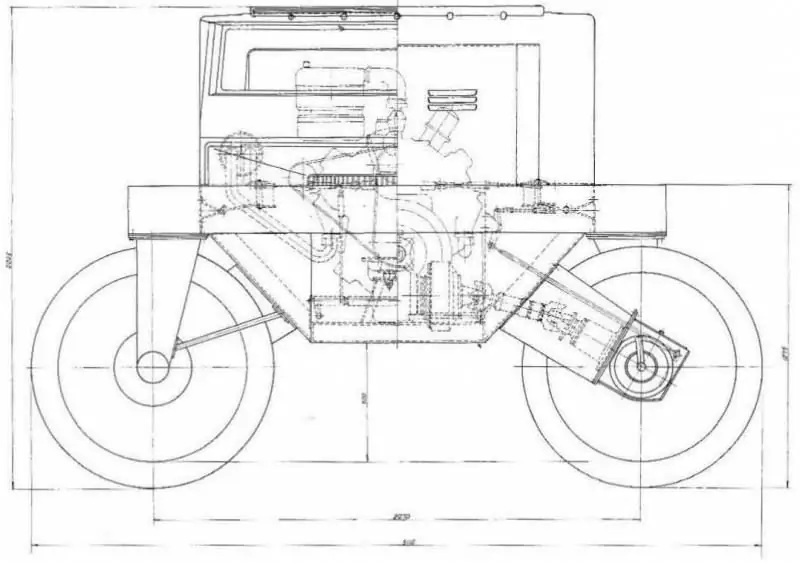
Body layout. Left - front view, right - back view
For obvious reasons, the rotor propeller for the experimental SHN-67 all-terrain vehicle was developed from scratch. The auger was a rather complex device 4, 2 m long and 1 m in diameter (lugs). The auger body was made of 2 mm steel and had a collapsible design. It was a long cylinder 800 mm in diameter, complemented by a pair of tapered fairings. To increase the rigidity of the structure, a 100 mm layer of polyurethane foam was applied on the inside of the body. Outside on the auger there was a spiral lug. A metal strip of trapezoidal section was rigidly attached to the body. The angle of the helix is 17 ° 40 '.
Two such devices were mounted on side racks and were located along the body of the vehicle. The augers were driven by transmission units located in the rear pillars. By controlling the auger, the driver could change the speed of rotation of the rotor propellers or change the direction of their rotation. All this, according to calculations, provided sufficient mobility and maneuverability.
In front of the hull of the experimental SHN-67 there was a closed three-seater cockpit. The fiberglass cockpit hood with developed glazing was borrowed from the PES-1 search and evacuation all-terrain vehicle. In the center of the cab there was a driver's seat from a GAZ-69 car. On the sides of it, a couple of places were provided for other testers. Access to the cockpit was provided only by a roof hatch. However, the low height of the all-terrain vehicle did not interfere with landing.
The finished auger-rotor snow and swamp-going vehicle was supposed to be of medium size. The length of the vehicle slightly exceeded 5.5 m, the width was 3.1 m, and the height was only 2 m. On a solid surface, the ShN-67 had a ground clearance of 500 mm. The curb weight was set at 3750 kg with a carrying capacity of 1250 kg. The total mass, therefore, had to reach 5 tons.
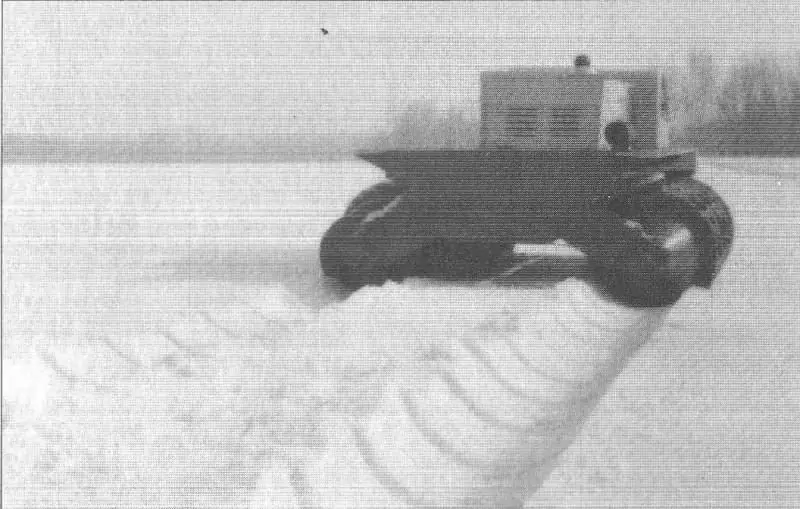
Driving on snowy terrain
Already in December 1966, SKB ZIL began assembling the frame of the future technology demonstrator. About a month later, the assembly of the units on the frame started. For a number of technical reasons, it was decided to remove some units of the used ZIL-375Ya engine, which, however, did not affect its performance in any way. By early March, the all-terrain vehicle was completed, and soon it was planned to test it on real tracks that were already used to test other equipment.
On March 4, 1967, an experienced ShN-67 was delivered to the ZIL test base in the village of Chulkovo near Moscow. The all-terrain vehicle was run-in in simple conditions, after which tests began to determine the maximum characteristics. Checks in rough terrain, swamp and snow continued until the end of March and collected all the necessary data.
Off-road, including soft mud, the "Auger" held himself confidently and, turning the propeller rotors, moved or maneuvered. Depending on the direction of rotation of the two augers, the machine could move forward or backward, or move sideways. For translational movement, both screws had to rotate in different directions, for lateral movement - in one direction.
The off-road performance was adequate, but the machine could not perform well on paved roads. In such conditions, the lugs of the unusual propeller wore out from friction on the surface much faster than on the ground. The all-terrain vehicle could float, and a pair of rotating rotors created a thrust of up to 600 kg.
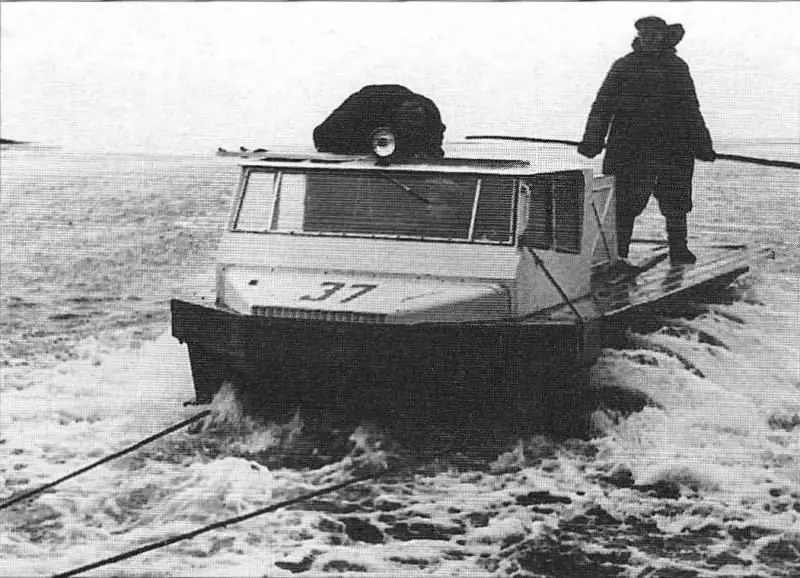
Auger on the water
Based on the test results of the ShN-67 all-terrain vehicle, it was decided to redesign the transmission and chassis. So, in the updated project, it was necessary to abandon the reverse gearboxes in favor of final drives with a two-stage bevel-cylindrical pair from the ZIL-130. This refinement increased the efficiency of the drivetrain and allowed the desired performance to be obtained, but at the same time led to the loss of the ability to turn in place.
New screw rotors have also been developed. Now it was proposed to make them from AMG-61 aluminum alloy while maintaining the existing structure. Instead of one spiral lug, it was now planned to use the so-called. two-way. The profile of this part changed to a triangular one, and the pitch was reduced to 1.6 m. The angle of the helix was brought to 32 ° 40’. According to calculations, this design of the auger made it possible to increase the maximum translational speed.
The updated version of the all-terrain vehicle was designated as SHN-68. The new project maintained maximum continuity with the existing one, and therefore it was possible to do without building a new prototype. The existing SHN-67 type auger received new transmission units and chassis devices, after which it was simply renamed. The restructuring of the ShN-67 according to the ShN-68 project was completed at the end of April 1968.
On May 6, the first tests of the updated machine took place on a reservoir in the Lytkarino area. Due to the new augers, the all-terrain vehicle was able to accelerate to 12 km / h. However, it was not without its problems. When leaving the water, the all-terrain vehicle rested its nose on a rather steep coast. The test driver tried to back up for a new attempt to lift, but the original propulsion device literally began to drag the car under the water. Fortunately, the driver noticed this in time and took measures to prevent flooding of the all-terrain vehicle.
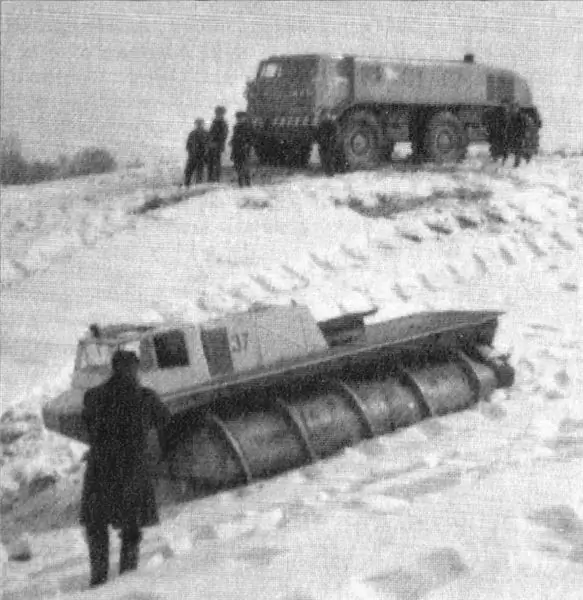
Joint tests of ShN-67 along with other equipment. In the background - the all-terrain vehicle ZIL-E167
Winter tests of the ShN-68 on the snow were carried out only in the spring of the following 1969. The field for testing was the fields of the Perm region, where then there was loose snow with a depth of about 1 m. Regardless of the time of day, the average air temperature remained negative until the end of the tests.
Several all-terrain vehicles were tested under the same conditions. Together with SHN-68, they studied several other machines, including the development of SKB ZIL. Most of these samples had non-standard chassis.
Comparisons have shown that the "Shnek", in contrast to a number of other samples, is capable of moving through snow with a depth of more than 900 m. The maximum speed in this case reached 18 km / h. Depending on the weight of the cargo on the site of the all-terrain vehicle, the speed was slightly reduced. With a mass of 5 tons, it only accelerated to 17.4 km / h.
SHN-68, among other things, was studied as a tractor. It was determined that the thrust of the car directly depends on its mass. So, with a total weight of 5 tons, a thrust of up to 1200 kg developed on the rear hook. With a machine weight of 3750 kg, this parameter was reduced to 970 kg. By towing the specified cargo, the all-terrain vehicle could continue to move. Exceeding the set load values led to slipping. The augers began to rotate freely, shoveling up soil or snow, and could no longer move the car.
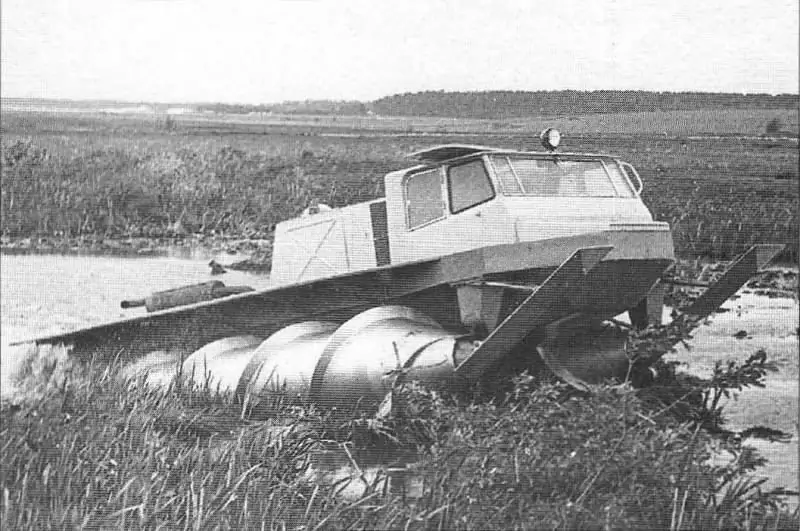
All-terrain vehicle in an updated configuration. Now it was called SHN-68
With a sufficiently high mobility on the snow, the all-terrain vehicle had limited capabilities in climbing the slopes. When moving forward, the augers threw snow under the bottom of the hull, as a result of which a sediment was formed under it, slowing down the movement. Such features of the machine limited the steepness of the overcome slope to 12 degrees. Moving back, the auger scattered snow to the sides, and therefore did not risk landing. Based on the results of such checks, it was decided to swap the augers. Now, when moving forward, the snow had to be scattered to the sides, and not raked under the bottom.
At the end of January 1970, new tests took place at the testing grounds of the Moscow region, during which, among other things, the maximum running characteristics were established. On compacted snow, SHN-68 was able to reach a speed of more than 30 km / h. Fuel consumption on virgin snow reached 86 l / h. In other conditions, the engine consumed significantly less fuel.
The summer test stage, during which the all-terrain vehicle worked on water and swampy terrain, showed the need for some improvements. So, it turned out that in such conditions, optimal acceleration is obtained when water and silt are ejected under the bottom of the hull. In addition, inspections have shown that the all-terrain vehicle needs additional skis to move through the swamp. Two inclined plates appeared in front of the front supports of the augers, removing vegetation from under the augers, and also simplifying the ascent to the shore or to floating areas of the vegetation cover.
Tests of the prototype ShN-68 were completed in the first months of 1970. This machine, being a demonstrator of technology, coped with its task perfectly and clearly showed all its features. In practice, it has been found that the auger rotor is indeed of certain interest in the context of the development of ultra-high passability technology. This undercarriage gave some advantages over other systems, although it was not devoid of disadvantages. First of all, this was manifested in the fact that the augers showed themselves well off-road, but they wore out extremely quickly on hard surfaces.
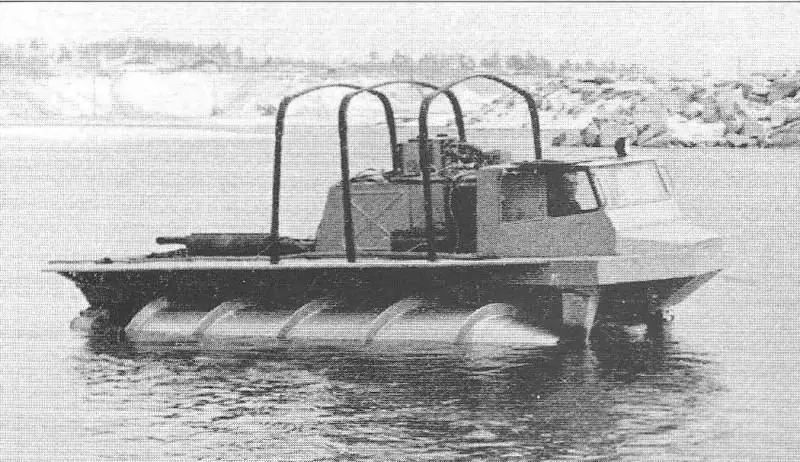
ShN-68 during tests on water
For further development of new ideas, a special stand was built at SKB ZIL, where it was planned to test different configurations of augers. Research work has allowed us to collect a lot of important information. In particular, a direct dependence of the thrust force and efficiency on the diameter of the auger body was established. At the same time, such results were best manifested on more viscous soils. Also, experts learned that the lug should not be higher than a quarter of the body diameter, otherwise there was a risk of reduction in efficiency. The elongation of the screw at the level of 4-6 units was considered optimal. Propellers with different proportions in this range had almost the same characteristics.
The results of the ShN-67 and ShN-68 projects interested both scientists and designers and the military. The search and rescue service of the Air Force naturally became interested in promising technology with uniquely high cross-country characteristics. Soon SKB ZIL received an order to develop a new snow and swamp-going vehicle with a rotary screw propeller, suitable for operation by rescuers. A couple of years later, the designers headed by V. A. The Grachevs completed this task and presented the PES-3 / ZIL-4904 machine.
The only built prototype of the ShN-67 model, subsequently redesigned according to the ShN-68 project, was to return to the manufacturer after the tests were completed. There he probably remained for some time, but there is no information about his further fate. There is reason to believe that at some point a unique machine of technical and historical interest was dismantled as unnecessary. Unlike a number of other prototypes and production models, by SKB ZIL, ShN-68 has not survived.
An experienced all-terrain vehicle with an original propeller showed its potential, and was also able to interest potential operators. Like other purely experimental machines, the prototype, nicknamed "Auger", confirmed the benefits of unusual ideas and contributed to the further development of technology. This process soon led to the emergence of several new all-terrain vehicles, one of which still remains in the ranks of the search and rescue service and ensures the evacuation of the landed astronauts.