Jetpacks of the fifties of the last century could not boast of high performance. Those vehicles that still managed to get into the air had too high fuel consumption, which negatively affected the maximum possible flight duration. In addition, the different designs had some other problems. Over time, the military and engineers became disillusioned with such technology, which was previously considered promising and promising. However, this did not lead to a complete stop of work. At the very end of the fifties, NASA became interested in this topic, which hoped to apply new technology in space programs.
In the foreseeable future, NASA specialists hoped not only to send a man into space, but also to solve several other problems. In particular, the possibility of working in open space, outside the ship, was considered. For a full-fledged solution of problems in such conditions, a certain apparatus was required with the help of which the astronaut could freely move in the desired direction, maneuver, etc. At the very beginning of the sixties, NASA requested assistance from the air force, which by this time had managed to conduct several similar programs. In addition, she attracted several aviation industry enterprises to work, which were invited to develop their own versions of a personal aircraft for the space program. Among others, such an offer was received by Chance-Vought.
According to available data, even at the stage of preliminary research, NASA specialists came to conclusions regarding the optimal form factor of promising technology. It turned out that the most convenient personal means of transportation would be a knapsack with a set of low-power jet engines. Such devices were ordered by contractor companies. It should be noted that other variants of the apparatus were also considered, however, it was the knapsack worn on the back of the astronaut that was recognized as optimal.
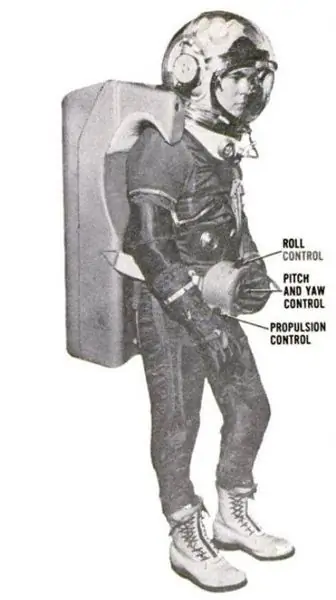
General view of the Chance-Vought spacesuit and the SMU. Photo by Popular Science magazine
Over the next few years, Chance Vout conducted a series of studies and shaped the appearance of a vehicle for space. The project received the designation SMU (Self-Maneuvering Unit). At the later stages of project development and during testing, a new designation was used. The device was renamed to AMU (Astronaut Maneuvering Unit - "Device for maneuvering an astronaut").
Probably the authors of the SMU project had an idea of the developments of the Wendell Moore team of Bell Aerosystems, as well as knew about other developments in this area. The fact is that the Bell jetpacks and the spacecraft that appeared a little later had to have the same engines, albeit with different characteristics. It was proposed to equip the SMU product with jet engines running on hydrogen peroxide and using its catalytic decomposition.
The process of catalytic decomposition of hydrogen peroxide by this time was actively used in various techniques, including in some early jetpacks. The essence of this idea consists in supplying "fuel" to a special catalyst that causes the substance to decompose into water and oxygen. The resulting vapor-gas mixture has a sufficiently high temperature, and also expands at a high speed, which makes it possible to use it as an energy source, including in jet engines.
It should be noted that decomposition of hydrogen peroxide is not the most economical source of energy in the context of jetpacks. It takes too much "fuel" to generate enough thrust to lift a person into the air. Thus, in Bell's projects, a 20-liter tank allowed the pilot to stay in the air for no more than 25-30 seconds. However, this was only true for flights on Earth. In the case of open space or the lunar surface, due to the lower (or absent) weight of the astronaut, it was possible to provide the required characteristics of the apparatus without an unacceptably high consumption of hydrogen peroxide.
In the course of the SMU project, several main issues had to be solved, the main of which, of course, was the type of jet engine. In addition, it was necessary to determine the optimal layout of the entire device, the composition of the necessary equipment and a number of other features of the project. According to reports, the study of these issues eventually led to the design of the original space suit, which was proposed to be used with the SMU / AMU product.
Major design work was completed in the first half of 1962, shortly thereafter, Chance-Vought produced a prototype space jetpack. In the fall of the same year, the device was first shown to the press. Images of the proposed system were published for the first time in the November issue of Popular Science. In addition, the article in this magazine provided a layout diagram and some key characteristics.
One of the photos published by Popular Science showed an astronaut in a new spacesuit with an SMU on his back. The proposed spacesuit had a spherical helmet with a lowered face shield and a developed lower part, which was supposed to rest on the astronaut's shoulders. There were also several connectors for connecting the spacesuit to the jetpack systems. The spacesuit from Chance-Vought was noticeably different from modern products for this purpose. It was made as light as possible and, apparently, was not equipped with a set of protective measures that are necessary to meet current requirements.
The knapsack itself was a rectangular block with a concave front wall and a set of means for fastening on the astronaut's back. So, on top of the front wall there were two characteristic "hooks" with which the knapsack rested on the astronaut's shoulders. In the middle part there was a waist belt on which a cylindrical control panel with several levers was located. Several cables and flexible pipelines were also provided for connecting the knapsack to the spacesuit.
The need to ensure long-term operation outside the spacecraft, as well as the imperfection of the technologies of that time, affected the layout of the apparatus. At the top of the SMU was a large closed-loop oxygen system unit. This device was designed to supply the breathing mixture to the astronaut's helmet, followed by pumping out the exhaled gases and removing carbon dioxide. Unlike hoses for supplying breathing mixture from a ship or cylinders for compressed gas, the system with carbon dioxide absorbers did not impair the maneuverability of the astronaut and allowed him to stay in open space for a long time.
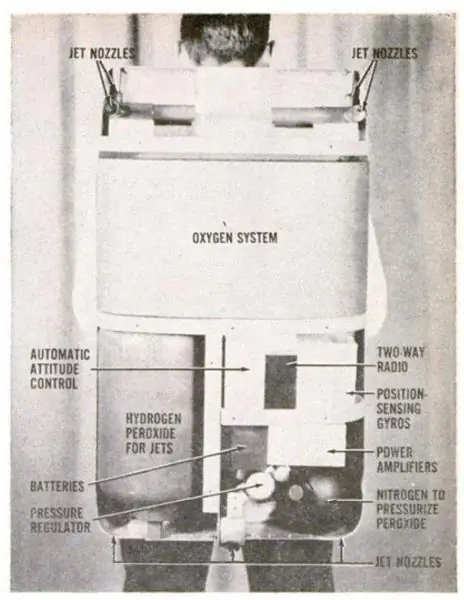
SMU without back panel. Photo by Popular Science magazine
According to reports, during the demonstration to reporters, the SMU was not equipped with a working life support system. This equipment was not yet ready for operation and needed additional checks, which is why it was replaced on the prototype with a simulator of the same weight and dimensions. It was in this configuration that the device took part in the first tests. Moreover, work in this direction was seriously delayed, which is why even a later prototype, built at the end of 1962, was tested without an oxygen system and was equipped only with its simulator.
The lower left part of the hull (relative to the pilot) was given for the placement of the hydrogen peroxide tank. To the right of it was a set of other equipment for various purposes. At the top of the lower right compartment was a radio station that provided two-way voice communication; under it were installed batteries and a power supply unit for the equipment, as well as a compressed nitrogen cylinder for the fuel supply system and a gas regulator.
On the side faces of the upper surface of the jetpack, four miniature engines with their own nozzles (two on each side) were provided. The same engines were found on the lower surface of the hull. In addition, two engines of a similar layout were located in the center of the lower surface. In total, 10 engines were available for the release of jet gases. The nozzles of all engines were turned and tilted on different sides and had to be responsible for creating thrust directed in the desired direction.
Each engine was reported to be a small block with a plate catalytic converter to induce fuel decomposition. There was a solenoid-controlled valve in front of the catalyst. All ten engines were proposed to be connected to a fuel tank, which, in turn, was connected to a compressed gas cylinder.
The principle of the engines was simple. Under the pressure of compressed nitrogen, hydrogen peroxide was supposed to enter the pipelines and reach the engines. At the command of the control system, the solenoids of the engines had to open the valves and provide "fuel" access to the catalysts. This was followed by the decomposition reaction with the release of the vapor-gas mixture through the nozzle and the formation of thrust.
The nozzles were positioned in such a way that, by synchronous or asymmetric switching on of the engines, it was possible to move in the desired direction, make turns or correct their position. For example, the simultaneous inclusion of all engines directed backward made it possible to move forward, and the turn was carried out due to the asymmetric inclusion of engines on different sides.
The first version of the SMU received a relatively simple control panel, made in a cylindrical case and located on a waist belt. On the side, under the right hand, there was a control lever for forward or backward movement. A lever was placed on the front wall for pitch and yaw control. Above there was another lever responsible for roll control. In addition, toggle switches were provided to turn on the engine, radio station and autopilot. With the help of such controls, the pilot could supply hydrogen peroxide to the required engines and thereby control his movements.
In addition to manual control, the SMU had automation designed to facilitate the astronaut's work. If necessary, he could turn on the autopilot, which, using a gyroscope and relatively simple electronics, had to monitor the position of the jetpack in space, adjusting it if necessary. It was assumed that such a regime would be applied during long-term work in one place, for example, when servicing instruments on the outer surface of the spacecraft. In this case, the astronaut was given the opportunity to perform various work, and automation had to monitor the preservation of the desired position.
The version of the SMU jetpack presented to reporters weighed about 160 pounds (about 72 kg). When used on the moon, the weight of the apparatus was reduced to 25 pounds (11.5 kg), and when operating in Earth orbit, the weight had to be completely free.
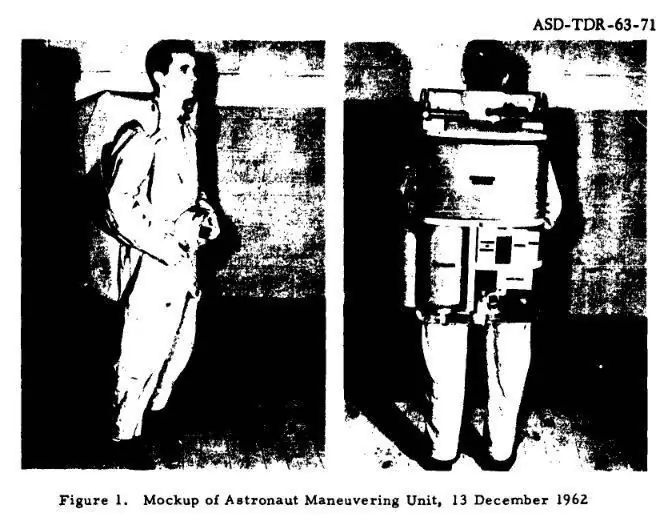
The layout of the SMU jetpack during testing. Photo from the report
According to a Popular Science publication, the SMU sample presented was calculated to allow an astronaut to fly up to 1,000 feet (304 m) on a single hydrogen peroxide refueling. The engine thrust, according to the developers, was enough to move large enough loads. For example, the possibility of moving an object, for example a spacecraft, weighing up to 50 tons was declared. In this case, the astronaut had to develop a speed of the order of one foot per second.
A few months before the demonstration of the SMU apparatus to journalists, in mid-1962, a prototype was delivered to Wright-Patterson Air Force Base (Ohio), where it was to be tested. To carry out all the necessary tests, specialists from the Ministry of Defense were involved in the project, as well as special equipment. So, as a test platform, a special KC-135 Zero G aircraft was chosen, which was used for research in conditions of short-term weightlessness.
The first flight with "zero gravity" took place on June 25, 62, and over the following months several dozen tests of the operation of the jetpack in zero gravity were carried out. During this time, it was possible to establish the fundamental possibility of using such systems in practice. In addition, some characteristics and basic flight data were confirmed. So, the thrust of the engines was enough for flying in an air atmosphere and performing some simple maneuvers.
Successful testing of the SMU device did not lead to a halt in design work. By the end of 1962, development began on an updated version of the jetpack for astronauts. In the modernized version of the project, it was proposed to change the layout of the apparatus, as well as to make some other adjustments to the design. Due to all this, it was supposed to improve the characteristics, primarily the “fuel” stock and basic flight data. After the start of work on the updated project, a new name AMU appeared, which soon began to be applied in relation to the previous SMU product, which is why some confusion is possible.
According to the available data, the modernized AMU did not differ much from the basic SMU in appearance. The exterior of the hull has not undergone major changes, and the system for attaching the apparatus to the astronaut's back has remained the same. At the same time, the layout of the internal units has radically changed. The flight range at the level of 300 m did not suit NASA, which is why it was proposed to use a new fuel tank. The AMU jetpack received a large, long hydrogen peroxide tank that occupied the entire central part of the hull. The volume of the new tank was 660 cubic meters. inches (10.81 L). Other equipment was placed on the sides of this tank.
Among other units, the new apparatus retained a tank for compressed nitrogen of the displacement system for supplying hydrogen peroxide. According to the project, nitrogen was to be supplied to the fuel tank at a pressure of 3500 psi (238 atmospheres). However, during the tests, lower pressures were used: about 200 psi (13.6 atm). The prototype of the AMU apparatus was equipped with engines of various powers. So, the nozzles responsible for moving forward and backward developed a thrust level of 20 pounds, used to move up and down - 10 pounds.
The AMU device in the future could receive a life support system, but even by the time testing began, such equipment was not yet ready. Because of this, the experienced AMU, like its predecessor, received only a model of the required system with the same dimensions and weight. After completing all the necessary design work and testing, the oxygen system could be installed on the space jetpack.
Shortly after the completion of assembly, at the very end of 1962 or early 1963, the AMU was sent to the Wright-Patterson base for testing. The specially equipped KC-135 Zero G aircraft again became the "proving ground" for his checks. Various checks continued at least until the end of the spring of 1963.
In mid-May 1963, the authors of the project prepared a report on the tests carried out. By this time, as stated in the document, more than a hundred flights on a parabolic trajectory were carried out, during which the operation of jetpacks in zero gravity was tested. During the tests, despite the short duration of flights with zero gravity, it was possible to master the control of both vehicles, as well as check their capabilities for transporting a pilot or cargo.
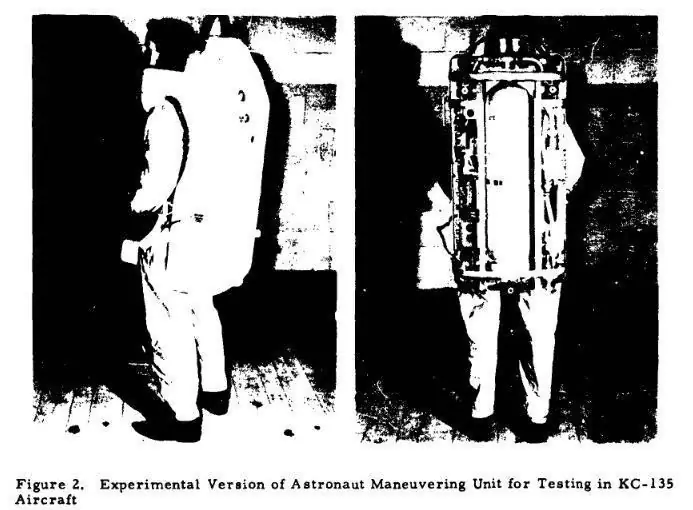
AMU backpack during testing. Photo from the report
The final part of the report stated that the AMU jetpack in its current form has satisfactory characteristics and can be used to solve the tasks assigned to it. It was also noted that engine thrust of up to 20 pounds is sufficient for controlled flight in the desired direction and for performing various maneuvers. The chosen arrangement of the nozzles of the engines provided, as written in the report, excellent control over the apparatus due to the placement at an equal distance from the center of gravity of the "pilot + knapsack" system.
The autopilot generally performed well, but needed improvements and additional tests. In some situations, this device could not correctly respond to a change in the position of the knapsack. In addition, it was proposed to "teach" control automation to ignore small (up to 10 °) deviations of the apparatus from the specified position. This mode made it possible to significantly reduce the consumption of hydrogen peroxide.
Astronauts who were to use the AMU product in the future had to undergo a special training course, during which they could not only master control, but also learn to "feel" the apparatus. The need for this was proven by several test flights under the control of a pilot with an insufficient level of training. In such cases, the pilot acted slowly and did not differ in accuracy of control.
In general, the authors of the report highly appreciated the AMU itself and the results of its tests. It was recommended to continue work on the project, to continue improving the entire structure and its individual components, as well as to pay attention to some flight modes. All these measures made it possible to count on the appearance of a workable jetpack for astronauts, fully suitable for solving all assigned tasks.
NASA and Chance-Vought, as well as a number of related organizations took into account the testers' report and continued work on promising projects. By the middle of the decade, based on the developments in the SMU / AMU project, a new device was developed, which was even planned to be tested in outer space.
Further work in the field of space jetpacks was crowned with success. In the early eighties, the first MMUs were sent into space, which were used as part of the equipment of the Space Shuttle spacecraft. This equipment was actively used in various missions to solve various problems. Thus, the idea of a jetpack, despite a lot of failures, came to practical use. True, they began to use it not on Earth, but in space.