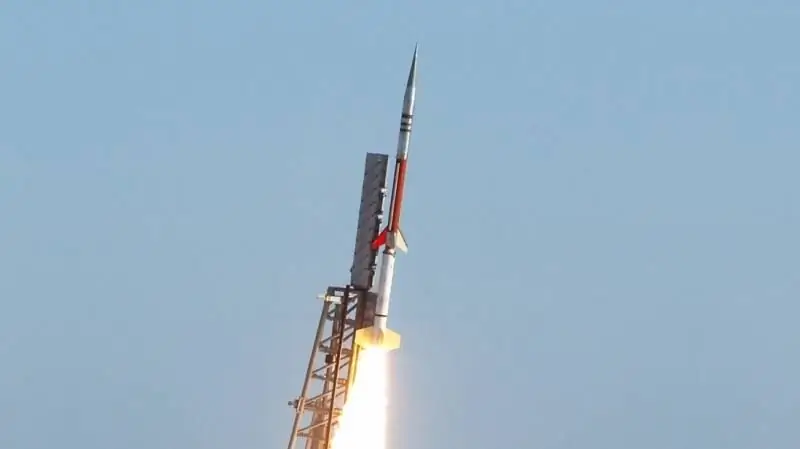
The conquest of outer space has become one of the most important and epoch-making achievements of mankind. The creation of launch vehicles and the infrastructure for their launch required tremendous efforts from the leading countries of the world. In our time, there is a tendency to create fully reusable launch vehicles capable of performing dozens of flights into space. Their development and operation still requires huge resources, which can only be allocated by states or large corporations (again, with the support of the state).
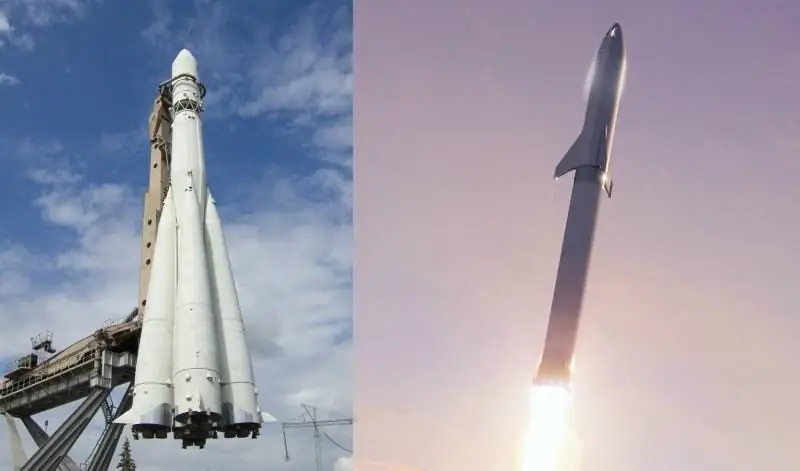
At the beginning of the XXI century, the improvement and miniaturization of electronic components made it possible to create small-sized satellites (the so-called "microsatellites" and "nanosatellites"), the mass of which is in the range of 1-100 kg. Recently, we are talking about "picosatellites" (weighing from 100 g to 1 kg) and "femto satellites" (weighing less than 100 g). Such satellites can be launched as groupage cargo from different customers or as a passing load to "large" spacecraft (SC). This launch method is not always convenient, since nanosatellites manufacturers (in what follows we will use this designation for all dimensions of ultra-small spacecraft) have to adapt to the schedule of customers for the launch of the main cargo, as well as due to differences in launch orbits.
This has led to the emergence of demand for ultra-small launch vehicles capable of launching spacecraft weighing about 1-100 kg.
DARPA and KB "MiG"
There were and are being developed many projects of ultralight launch vehicles - with ground, air and sea launch. In particular, the American agency DARPA was actively working on the problem of the rapid launch of ultra-small spacecraft. In particular, one can recall the ALASA project, launched in 2012, within the framework of which it was planned to create a small-sized rocket designed to launch from an F-15E fighter and launch satellites weighing up to 45 kg into low reference orbit (LEO).
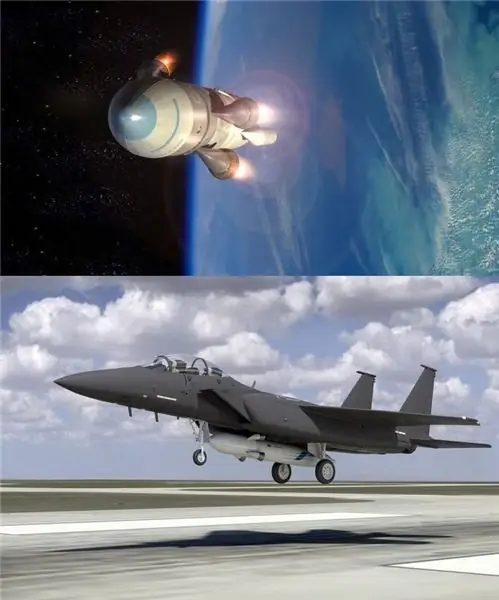
The rocket engines installed on the rocket were supposed to operate on NA-7 monopropellant, including monopropylene, nitrous oxide and acetylene. The launch cost was not to exceed $ 1 million. Presumably, it was problems with fuel, in particular with its spontaneous combustion and a tendency to explode, that put an end to this project.
A similar project was being worked out in Russia. In 1997, the MiG design bureau, together with KazKosmos (Kazakhstan), began developing a payload (PN) launching system using a converted MiG-31I interceptor (Ishim). The project was developed on the basis of the groundwork for the creation of an anti-satellite modification of the MiG-31D.
The three-stage rocket, launched at an altitude of about 17,000 meters and a speed of 3000 km / h, was supposed to provide a payload weighing 160 kg into orbit at an altitude of 300 kilometers, and a payload weighing 120 kg into an orbit at an altitude of 600 kilometers.

The difficult financial situation in Russia in the late 90s and early 2000s did not allow this project to be realized in metal, although it is possible that technical obstacles may arise in the development process.
There were many other projects of ultralight launch vehicles. Their distinguishing feature can be considered the development of projects by state structures or large (practically "state") corporations. Complex and expensive platforms such as fighters, bombers, or heavy transport aircraft often had to be used as launch platforms.
All this together complicated the development and increased the cost of the complexes, and now the leadership in the creation of ultralight launch vehicles has passed into the hands of private companies.
Rocket lab
One of the most successful and well-known projects of ultralight rockets can be considered the "Electron" launch vehicle of the American-New Zealand company Rocket Lab. This two-stage rocket with a mass of 12,550 kg is capable of launching 250 kg of PS or 150 kg of PS into a sun-synchronous orbit (SSO) with an altitude of 500 kilometers into LEO. The company plans to launch up to 130 missiles a year.
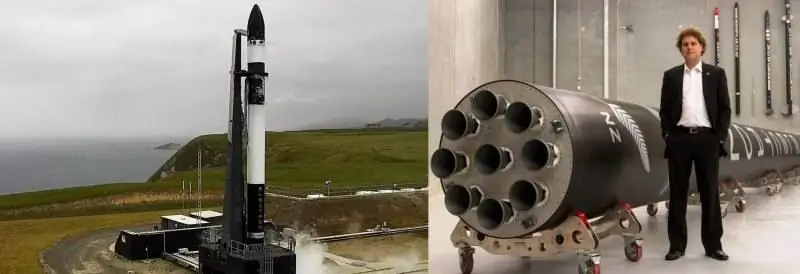
The design of the rocket is made of carbon fiber; liquid-propellant jet engines (LRE) are used on a fuel pair of kerosene + oxygen. To simplify and reduce the cost of the design, it uses lithium-polymer batteries as a power source, pneumatic control systems and a system for displacing fuel from tanks, operating on compressed helium. In the manufacture of liquid-propellant rocket engines and other rocket components, additive technologies are actively used.
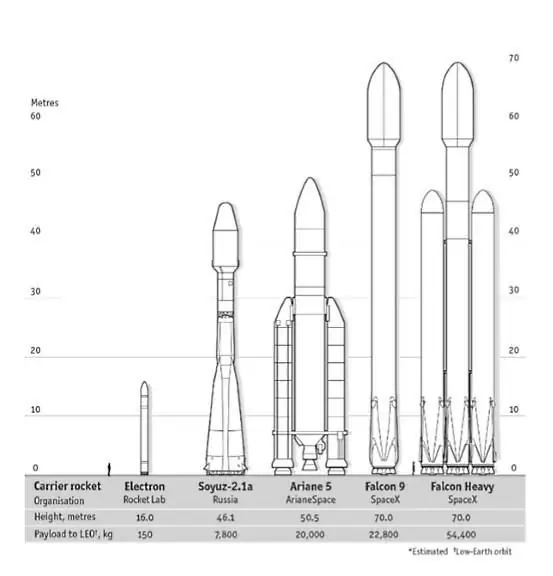
It can be noted that the first rocket from Rocket Lab was the Kosmos-1 meteorological rocket (Atea-1 in the Maori language), capable of lifting 2 kg of payload to an altitude of about 120 kilometers.
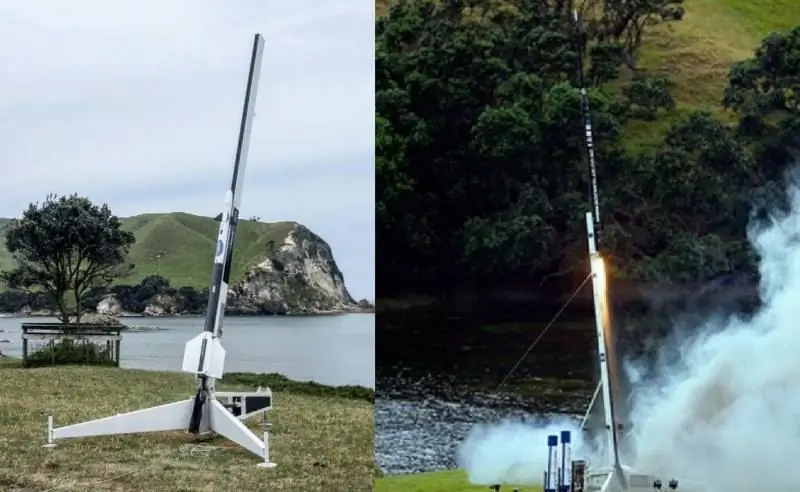
Lin Industrial
The Russian "analogue" of Rocket Lab can be called the company "Lin Industrial", which develops projects for both the simplest suborbital rocket capable of reaching an altitude of 100 km, and launch vehicles designed to output payloads to LEO and SSO.
Although the market for suborbital missiles (primarily such as meteorological and geophysical rockets) is dominated by solutions with solid fuel engines, Lin Industrial is building its suborbital rocket based on a liquid-propellant rocket engine running on kerosene and hydrogen peroxide. Most likely this is due to the fact that Lin Industrial sees its main direction of development in the commercial launch of the launch vehicle into orbit, and the liquid-propellant suborbital rocket is more likely to be used to develop technical solutions.
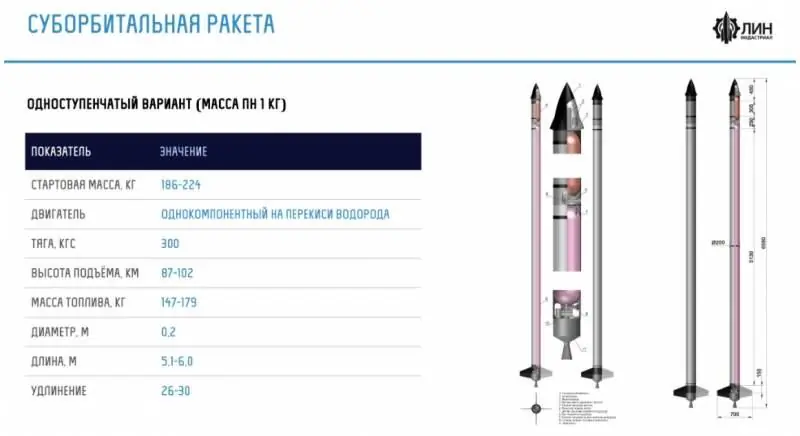
The main project of Lin Industrial is the Taimyr ultralight launch vehicle. Initially, the project provided for a modular layout with a series-parallel arrangement of modules, which makes it possible to form a launch vehicle with the possibility of outputting a payload weighing from 10 to 180 kg to LEO. The change in the minimum mass of the launched launch vehicle was to be ensured by changing the number of universal missile units (UBR) - URB-1, URB-2 and URB-3 and the third stage RB-2 rocket unit.
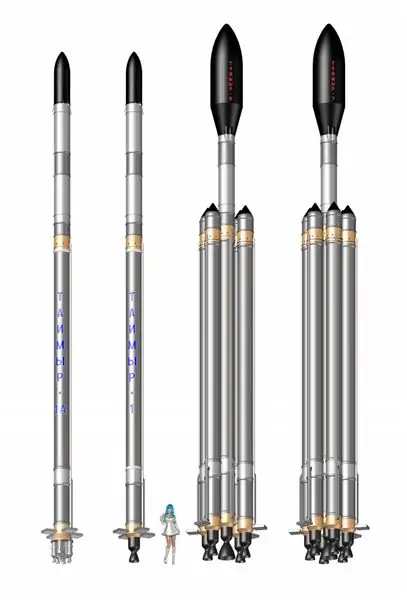
The engines of the Taimyr launch vehicle must operate on kerosene and concentrated hydrogen peroxide; the fuel must be supplied by displacement with compressed helium. The design is expected to widely use composite materials, including carbon fiber reinforced plastics and 3D-printed components.
Later, the Lin Industrial company abandoned the modular scheme - the launch vehicle became a two-stage, with a sequential arrangement of steps, as a result of which the appearance of the Taimyr launch vehicle began to resemble the appearance of the Electron launch vehicle by Rocket Lab. Also, the displacement system on compressed helium was replaced by fuel supply using electric pumps powered by batteries.
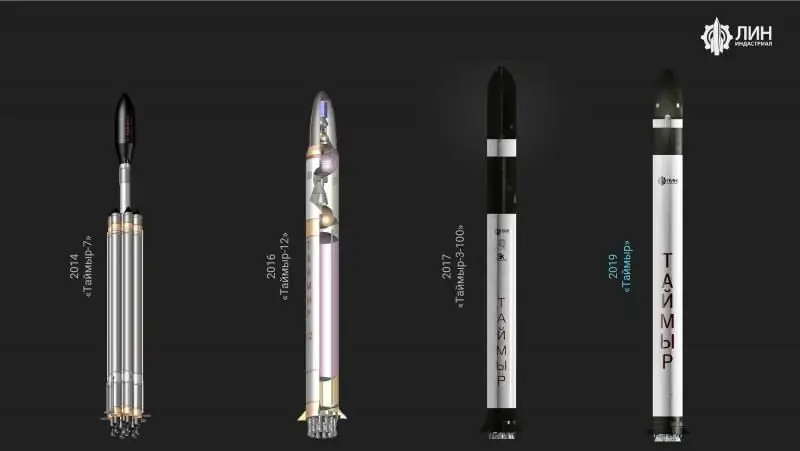
The first launch of the Taimyr LV is planned for 2023.
IHI Aerospace
One of the most interesting ultralight launch vehicles is the Japanese SS-520 three-stage solid-propellant rocket manufactured by IHI Aerospace, created on the basis of the S-520 geophysical rocket by adding a third stage and corresponding refinement of the onboard systems. The height of the SS-520 rocket is 9.54 meters, the diameter is 0.54 meters, the launch weight is 2600 kg. The payload mass delivered to LEO is about 4 kg.
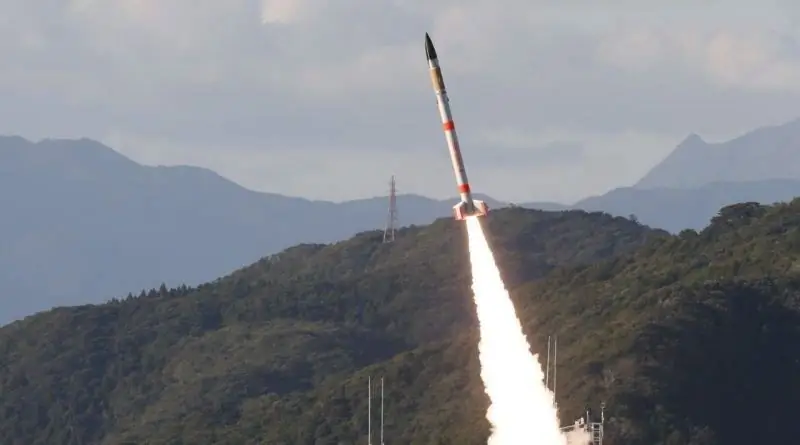
The body of the first stage is made of high-strength steel, the second stage is made of carbon fiber composite, the head fairing is made of fiberglass. All three stages are solid fuel. The control system of the SS-520 LV is periodically switched on at the time of separation of the first and second stages, and the rest of the time the rocket is stabilized by rotation.
On February 3, 2018, the SS-520-4 LV successfully launched a TRICOM-1R cubesat weighing 3 kilograms, designed to demonstrate the possibility of creating spacecraft from consumer electronic components. At the time of launch, the SS-520-4 LV was the smallest launch vehicle in the world, which is registered in the Guinness Book of Records.
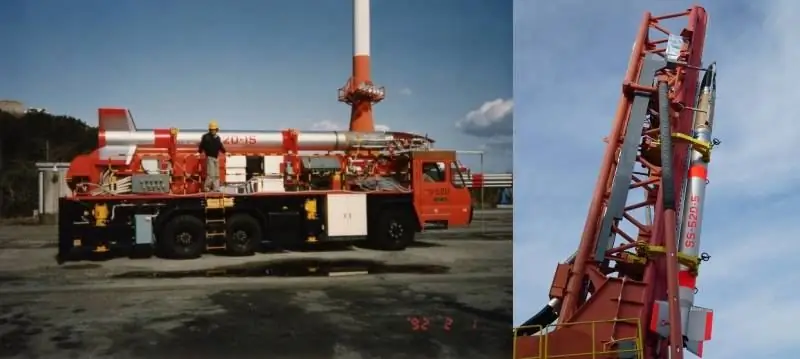
Creation of ultra-small launch vehicles based on solid-propellant meteorological and geophysical rockets can be a rather promising direction. Such missiles are easy to maintain, can be stored for a long time in a condition that ensures their preparation for launch in the shortest possible time.
The cost of a rocket engine can be about 50% of the cost of a rocket and it is unlikely that it will be possible to reach a figure less than 30%, even taking into account the use of additive technologies. In solid-propellant launch vehicles, a cryogenic oxidizer is not used, which requires special storage and refueling conditions immediately before launch. At the same time, for the manufacture of solid propellant charges, additive technologies are also being developed that allow "printing" fuel charges of the required configuration.
The compact dimensions of the ultralight launch vehicles simplify their transportation and allow launching from various points of the planet to obtain the required orbital inclination. For ultralight launch vehicles, a much simpler launch platform is required than for "large" rockets, which makes it mobile.
Are there projects of such missiles in Russia and on what basis can they be implemented?
A significant number of meteorological rockets were produced in the USSR - MR-1, MMP-05, MMP-08, M-100, M-100B, M-130, MMP-06, MMP-06M, MR-12, MR-20 and geophysical rockets - R-1A, R-1B, R-1V, R-1E, R-1D, R-2A, R-11A, R-5A, R-5B, R-5V, "Vertical", K65UP, MR-12, MR-20, MN-300, 1Ya2TA. Many of these designs were based on military developments in ballistic missiles or interceptors. During the years of active exploration of the upper atmosphere, the number of launches reached 600-700 rockets per year.
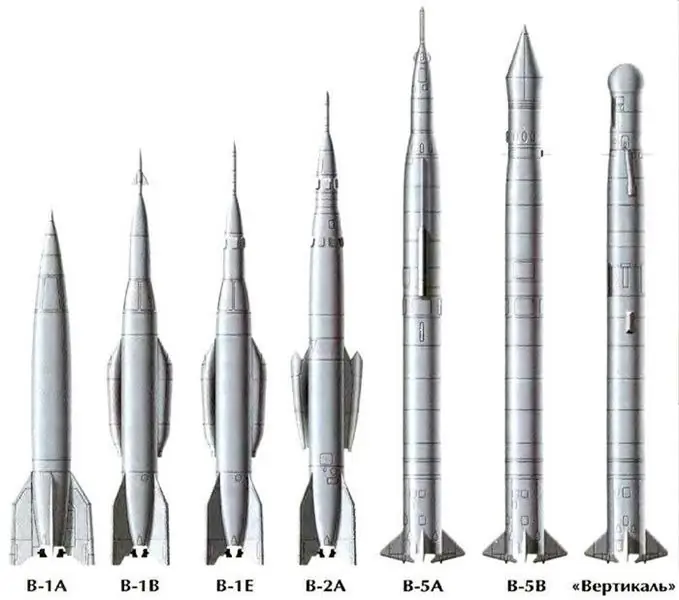
After the collapse of the USSR, the number of launches and types of missiles was radically reduced. At the moment, Roshydromet uses two complexes - the MR-30 with the MN-300 rocket developed by the NPO Typhoon / OKB Novator and the meteorological missile MERA developed by KBP JSC.
MR-30 (MN-300)
The missile of the MR-30 complex provides lifting of 50-150 kg of scientific equipment to an altitude of 300 kilometers. The length of the MH-300 rocket is 8012 mm with a diameter of 445 mm, the launch weight is 1558 kg. The cost of one launch of the MN-300 rocket is estimated at 55-60 million rubles.
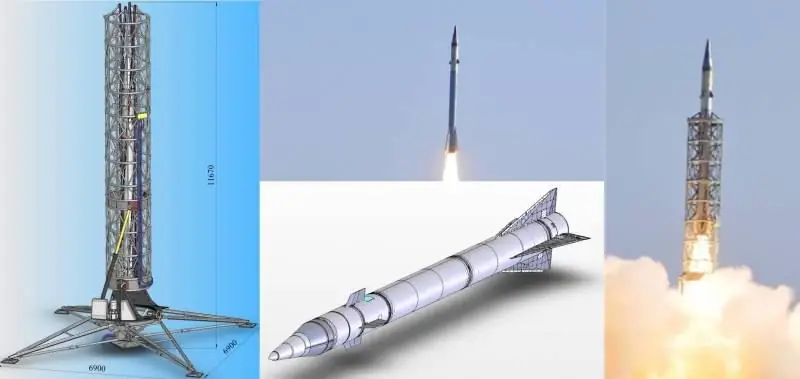
On the basis of the MN-300 rocket, the possibility of creating an ultra-small launch vehicle IR-300 is being considered by adding a second stage and an upper stage (in fact, a third stage). That is, in fact, it is proposed to repeat the rather successful experience in the implementation of the Japanese ultralight SS-520 launch vehicle.
At the same time, some experts express the opinion that since the maximum speed of the MN-300 rocket is about 2000 m / s, then to obtain the first cosmic speed of about 8000 m / s, which is necessary to put the launch vehicle into orbit, it may require too serious revision of the original project., which is essentially the development of a new product, which can lead to an increase in the launch cost by almost an order of magnitude and make it unprofitable compared to competitors.
MEASURE
The meteorological rocket MERA is designed to lift a payload weighing 2-3 kg to an altitude of 110 kilometers. The mass of the MERA rocket is 67 kg.
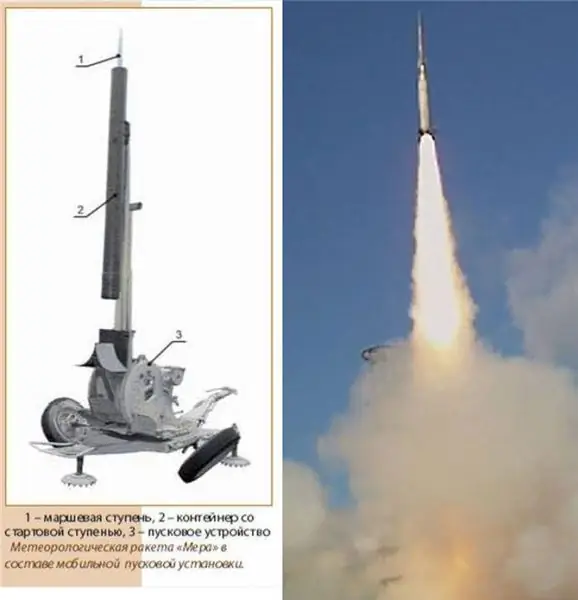

At first glance, the meteorological rocket MERA is absolutely unsuitable for use as a basis for creating an ultralight launch vehicle, but at the same time, there are some nuances that make it possible to challenge this point of view.
The meteorological missile MERA is a bicaliber two-stage, and the acceleration function is performed only by the first stage, the second - after separation flies by inertia, which makes this complex similar to the anti-aircraft guided missiles (SAM) of the Tunguska and Pantsir anti-aircraft missile and cannon complexes (ZRPK). Actually, on the basis of SAM for the air defense missile systems of the indicated complexes, the meteorological rocket MERA was created.
The first stage is a composite body with a solid propellant charge placed in it. In 2.5 seconds, the first stage accelerates the meteorological rocket to a speed of 5M (speeds of sound), which is about 1500 m / s. The diameter of the first stage is 170 mm.
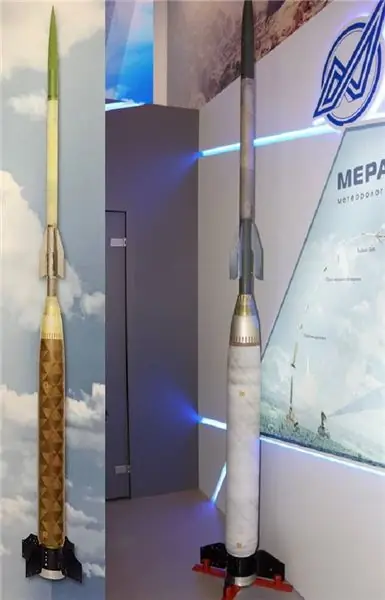
The first stage of the meteorological rocket MERA, made by winding a composite material, is extremely light (compared to steel and aluminum structures of similar dimensions) - its weight is only 55 kg. Also, its cost should be significantly lower than solutions made from carbon fiber reinforced plastic.
Based on this, it can be assumed that on the basis of the first stage of the meteorological rocket MERA, a unified rocket module (URM) can be developed, designed for batch formation of stages of ultralight launch vehicles
In fact, there will be two such modules, they will differ in the nozzle of a rocket engine, optimized, respectively, for operation in the atmosphere or in a vacuum. At the moment, the maximum diameter of casings manufactured by JSC KBP by the winding method is presumably 220 mm. It is possible that there is a technical feasibility of manufacturing composite housings of a larger diameter and length.
On the other hand, it is possible that the optimal solution would be the manufacture of hulls, the size of which will be unified with any ammunition for the Pantsir air defense missile system, guided missiles of the Hermes complex or MERA meteorological rockets, which will reduce the cost of a single product by increasing the volume of serial release of the same type of product.
The stages of the launch vehicle should be recruited from the URM, fastened in parallel, while the separation of the stages will be carried out transversely - the longitudinal separation of the URM in the stage is not provided. It can be assumed that the stages of such a launch vehicle will have a large parasitic mass in comparison with a monoblock body of a larger diameter. This is partly true, but the low weight of the case made of composite materials makes it possible to largely neutralize this drawback. It may turn out that a large-diameter case, made using a similar technology, will be much more difficult and expensive to manufacture, and its walls will have to be made much thicker to ensure the necessary rigidity of the structure than that of URMs connected by a package, so that in the end there is a lot of monoblock and package solutions will be comparable at a lower cost of the latter. And it is highly likely that a steel or aluminum monoblock case will be heavier than a packaged composite one.
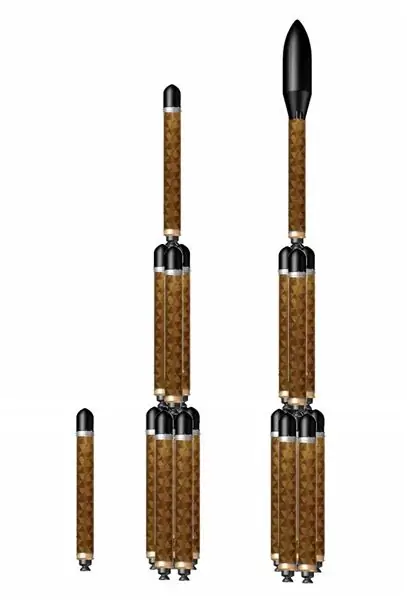
Parallel connection of the URM can be carried out using flat composite milled elements located in the upper and lower parts of the step (at the points of narrowing of the URM body). If necessary, additional screeds made of composite materials can be used. To reduce the cost in the structure, technological and cheap industrial materials, high-strength adhesives should be used as much as possible.
Similarly, the LV stages can be interconnected by composite tubular or reinforcing elements, and the structure can be non-separable, when the stages are separated, the load-bearing elements can be destroyed by pyro charges in a controlled manner. Moreover, to increase the reliability, the pyro charges can be located in several sequentially located points of the supporting structure and be initiated both by electric ignition and direct ignition from the flame of the engines of the higher stage, when they are turned on (for shooting the lower stage if the electric ignition did not work).
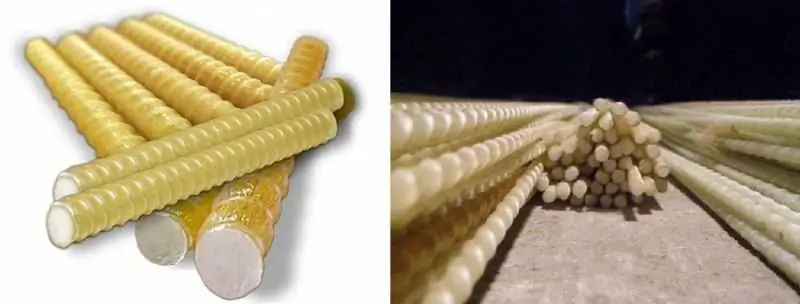
Launch control can be implemented in the same way as it is done on the Japanese ultralight launch vehicle SS-520. The option of installing a radio command control system, similar to that installed on the Pantsir air defense missile system, can also be considered to correct the launch of the launch vehicle at least on a part of the flight trajectory (and possibly at all stages of the flight). Potentially, this will reduce the amount of expensive equipment on board a single-use rocket by carrying it to a “reusable” control vehicle.
It can be assumed that, taking into account the supporting structure, connecting elements and the control system, the final product will be able to deliver a payload weighing from several kilograms to several tens of kilograms to LEO (depending on the number of unified rocket modules in the stages) and compete with the Japanese ultralight SS-LV. 520 and other similar ultralight launch vehicles developed by Russian and foreign companies.
For the successful commercialization of the project, the estimated cost of launching an ultralight MERA-K launch vehicle should not exceed $ 3.5 million (the SS-520 launch vehicle has such a launch cost).
In addition to commercial applications, the MERA-K launch vehicle can be used for the emergency withdrawal of military spacecraft, the size and weight of which will also gradually decrease.
Also, the developments obtained during the implementation of the MERA-K launch vehicle project can be used to create advanced weapons, for example, a hypersonic complex with a conventional warhead in the form of a compact glider, which is dropped after the launch of the launch vehicle to the upper point of the trajectory.