Patriotism of the Soviet industrial elite was combined with joint responsibility for the end result
Inter-sectoral interaction at all times - both in the Russian Empire, and in the USSR, and today - did not belong to the strengths of the domestic industry. In contrast to Germany or the United States, where contractual obligations had and have an immutable and almost sacred force.
Take, for example, the relationship between Russian metallurgists and machine builders. In the second half of the 19th century, new transport engineering plants and shipyards did not receive the required amount of industrial metals from the Ural miners. The latter considered it unprofitable to make a lot of relatively cheap rolled products, since the same profit was provided by a much smaller volume of expensive roofing iron. The missing metal for car axles, engine shafts and ship skin had to be purchased abroad. Only by the end of the century, the problem was solved by the southern Russian metallurgical plants founded by Belgian or French industrialists. In the Urals, the French also built one plant - Chusovskaya.
It would seem that in Soviet times, such whims were out of the question. In addition, the metallurgical plants built in the 30s provided the country with metal as a whole. However, each time when machine builders requested new complex types of rolled products, metallurgists mastered them for years, or even decades.
Departmental feudalism
Let's turn to the history of Uralvagonzavod. Already in its first projects, it was planned to use solid-rolled steel wheels under four-axle cars as the design capacity reached its design capacity, the supplier of which was planned for the nearby Novo-Tagil Metallurgical Plant. However, the latter was being built by the metallurgical department, and it postponed the construction of the wheel rolling mill to 1938-1942, and not in the first place. As a result, the case did not start before the war. And after the war, the rental of wheels was not too interested in metallurgists. Result: up to the mid-50s, Tagil cars left the factory on short-lived cast iron wheels instead of steel ones. This brought huge losses to the railway workers, but there was no choice: either such cars, or none.
The same thing happened with the introduction of low-alloy steels in carriage building. They promised a noticeable reduction in the dead weight of the rolling stock while maintaining all the performance characteristics. The designers of Uralvagonzavod started designing cars made of low-alloy metal at the end of the 30s, but their serial production began only in the second half of the 50s, since metallurgists did not provide either appropriate rolled products or ferroalloys for casting parts.
It must be said that the virus of departmental feudalism affected the machine builders themselves. In the summer of 1937, an interesting story took place that characterized the interagency relations of that time. The Main Directorate of Metallurgical Enterprises sent to Uralvagonzavod an order for five thousand tons of blanks for the recently launched bandage mill of the Novo-Tagil Plant. The Main Directorate of Transport Engineering was outraged by the encroachment on a subordinate enterprise. Deputy Chief of the Main Directorate G. G. On July 11 Aleksandrov sent a letter to GUMP and Uralvagonzavod with the following statement: “We are extremely surprised that the solution of such an important issue as organizing the production of a bandage blank at Uralvagonzavod was carried out without our participation, and even more so - we were not even sent a copy of the outfit sent to Uralvagonzavod … I ask you to establish a firm procedure for issuing blanks to our factories only by agreement with us and through Glavtransmash."
As a result, metallurgists were denied the bandage steel, allegedly due to the technical impossibility of casting high-quality ingots in the open-hearth shop of the Uralvagonzavod. Meanwhile, already in 1936, an axial blank was cast here, and in 1937 - ingots for sheet rolling. Therefore, the ingots for the shroud mill, located a few kilometers from UVZ, had to be transported from the Vyksa and Kuznetsk plants. Moreover, their quality left much to be desired, and the volumes of supplies were insufficient.
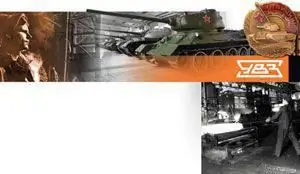
In 1938, history repeated itself. The main consumer of UVZ ingots was the Molotov (that is, Perm) Artillery Plant, which received a batch of blanks at the end of the year. And only a small number of them went to the bandage shop, which again had to import the missing metal for two or two and a half thousand kilometers. Industry interests in the distribution of Uralvagonzavodsk steel clearly prevailed.
Departmental illness did not spare the defense industry either. Numerous publications on the history of Soviet tank building are downright replete with examples of how the construction of prototypes or the deployment of mass production was delayed due to the non-delivery of metal, especially armor.
And even today the sectoral self-interest has not gone anywhere, it has only changed its form. Requests for new shaped forms of rolled products are simply fought off with exorbitant prices. There is no need to talk about a coordinated policy. After the collapse of the ruble exchange rate at the turn of 2014-2015, metallurgical companies raised prices for rolling stock by 30-60 percent. And they immediately began to complain about the machine builders for the equipment that had risen in price - after all, the machines are produced in Russia and are not tied to the dollar exchange rate.
It seems that in our country there is only one cure for cross-sectoral problems: the creation of vertically integrated systems, where the ore mined by our own forces is turned first into metal and then into finished machines.
Wartime unity
There is, however, a short period in our history when industry interests have receded into the background. We are talking about the Great Patriotic War. The undoubted patriotism of the Soviet industrial elite at that time was combined with the joint responsibility of all those involved in defense production for the end result. That is, the director of the armored rolling plant was responsible not so much for the volume of smelted and rolled steel, but for the number of tanks built.
The main step in this direction was made by the director of NII-48 A. S. Zavyalov. In the first days of the war, he turned to the government with a proposal to entrust the institute with the introduction of technologies for the production of special steels and armored structures at enterprises in the east of the country, for the first time involved in the manufacture of armored vehicles. In early July, teams of NII-48 specialists headed the technological restructuring of 14 largest enterprises. Among them were the Magnitogorsk and Kuznetsk Metallurgical Plants, the Novo-Tagil and Chusovka Metallurgical Plants, the Ural Heavy Machine Building Plant, the Gorky Krasnoye Sormovo, the Stalingrad Tractor Plant, the Stalingrad Red October and No. 264. Thus, Zavyalov violated the pre-war taboo: the list included enterprises of three people's commissariats.
Patriotism and compulsory suppression of departmental egoism provided Soviet metallurgy with unprecedented rates of development of defense products, neither in the pre-war nor in the post-war period. In a matter of months, in the east of the country (primarily in the Urals), the production of ferromanganese, ferrosilicon, ferrochrome, ferrovanadium and other alloys, without which it is impossible to obtain armor steel, was organized. After the loss of the western regions, Chelyabinsk remained the only ferroalloy plant in the USSR. On it, in a short time, the smelting was increased by two and a half times. 25 types of products were produced, but most of all were various types of ferrochrome. Smelting of ferromanganese was established in blast furnaces, and not only in low-tonnage old blast furnaces of the Nizhniy Tagil and Kushvinsky plants, but also in a large modern furnace of the Magnitogorsk Combine. Contrary to all pre-war ideas, ferrochrome was smelted in the second half of 1941 in their blast furnaces by metallurgists of the Nizhniy Tagil and Serov plants, and scientists from the Ural branch of the USSR Academy of Sciences provided great assistance in creating a new technology. Later, ferrosilicon smelting was mastered in the Serov blast furnaces.
There were no armored camps either in the Urals or in Western Siberia before the war; they had to be hastily transferred from enterprises that were in the combat zone.
In the summer of 1941, the evacuated equipment was still in transit. And then the chief mechanic of the Magnitogorsk Combine N. A. Ryzhenko suggested rolling the armor on a blooming mill. Despite the great risk, the idea was carried out. And in October, an armored camp, taken out from the Mariupol plant, entered service. It was assembled in just 54 days. According to the pre-war standards, this took a year.
The Novo-Tagil plant got the camp from Leningrad. Preparations for its admission began in July, initially it was assumed that it would be assembled at the site of the bandage. The bandage camp was disassembled, but it turned out that the old stock was not enough to install the armored camp and had to be placed elsewhere. The war forced to do what was not long ago considered impossible: just a year ago, attempts to conduct industrial construction by an integrated "high-speed" method in Nizhny Tagil had at best a partial success, and in the summer of 1941 the most complex construction operation was almost perfect. On September 10, the first Tagil steel sheet was rolled a month ahead of schedule. In total, by the end of the year, 13,650 tons of sheet metal were obtained, including about 60 percent of armor (the mill was tested on carbon steel, and in October - December, carbon steel was rolled with a shortage of armor ingots). As a result, already in January 1942, the monthly production of armor plates at the Ural factories exceeded six months in the entire pre-war Soviet Union.
No less amazing events took place at other little-known enterprises. During the war, the Zlatoust Metallurgical Plant was inferior to the Magnitogorsk Combine in terms of the volume of smelting and rolled steel, but it significantly surpassed it in its product mix - about 300 grades of alloy and carbon steel were produced here. Without supplies from Zlatoust, the production of many types of weapons, primarily tank engines, would have stopped.
Old Ural factories proved to be indispensable in the production of small batches of especially high-quality steel. For example, metal from Serov Metallurgical, the main manufacturer of calibrated rolled products, was invested in every Soviet tank. The Nizhnesalda plant switched to nickel iron and steel smelting. This list can be continued endlessly - during the war years, wherever there was at least one cupola, weapons-grade metal was melted.
There is a curious story with fluxes for automatic welding. Before and at the beginning of the war, they were smelted at one of the enterprises of Donbass, after the occupation of which centralized supplies completely stopped. At the end of 1941, employees of the Institute of Electric Welding of the Academy of Sciences of the Ukrainian SSR began to search for substitute materials available in the Urals in a more or less usable condition. And they found them - in the form of blast furnace slags of the Ashinskiy metallurgical plant. Only small improvements were required: the blast furnaces enriched their slags with manganese and thereby turned them into a completely suitable flux. The equipment necessary for testing was brought from Nizhny Tagil directly to Asha.
Examples of local cooperation between tank and metallurgical plants are very indicative. Before the launch of its own facilities, heat treatment of tank parts of the Ural Tank Plant No. 183 was carried out at the Nizhniy Tagil Metallurgical Plant.
The successful work of UTZ foundry workers was greatly facilitated by the help of the neighboring Nizhniy Tagil fireclay plant, which established the production of high-quality refractory stop flint plugs. This made it possible to perform trouble-free casting of heavy armor steel melts on shaped casting.
In 1942-1945, open-hearth furnaces at UTZ operated mainly on coke oven and blast furnace gas from the Novo-Tagil Metallurgical and Nizhny Tagil Coke Plants. The gas pipeline has been in operation since February 1942. Plant No. 183's own gas generating station provided no more than 40 percent of the needs.
Sometimes a simple piece of advice was enough to solve a problem. The information from local metallurgists about a small manganese mine developed in the 1870s helped to survive several weeks before the start of deliveries of ferromanganese without stopping the casting of tank tracks.
Another example: as the production of armored steel increased, the open-hearth shop could no longer keep up with the smelting of metal for the heads of aerial bombs. It was not possible to get it from the outside. Director Yu. E. Maksarev recalled the course of further events in his memoirs: “When I was at one of the meetings in the city committee, I met the director of the old, still Demidov plant and asked to take from me the casting of the bomb heads. He said: I cannot help with steel, but with advice I will help. And when I came to his plant, he showed me a one and a half ton Bessemer converter with medium blowing. He gave me the drawings and said that he knows that we have a good mechanized iron foundry, and your converters will weld”. This is how the order for the plant of September 8, 1942 appeared on the organization in the Griffin wheel shop of the Bessemer section of three small converters (one and a half tons of metal each). By September 25, the project was prepared by the design and technological department of the capital construction management, the specialists of the chief mechanic's department quickly welded converters and boilers - liquid iron storage tanks. The test run of the Bessemer department and the casting of an experimental batch of five names of parts took place at the turn of October-November 1942. Serial production began at the end of November.
At the end of the topic: cooperation between metallurgists and tank builders in wartime acted in both directions. The installers of the Ural Tank Plant participated in the commissioning of many new units of the Novo-Tagil Metallurgical Plant. In May 1944, a significant number of lining plates for the repair of the blast furnace were manufactured in the armored tower casting shop.
But the main assistant to the metallurgists was, of course, the Ural Heavy Machine Building Plant. The books of orders for UZTM for 1942-1945 are literally packed with documents on the production of spare parts and devices for metallurgical purposes - both for the needs of the tank industry and for enterprises of the People's Commissariat of Ferrous Metallurgy. In the fall of 1942, a special division for the production of equipment for metallurgical plants was officially restored at UZTM. It received the code "Division 15" and was subordinate to the deputy director for procurement shops and hull production.
Success at the intersection of industries
The cooperation of metallurgists and tank builders has led to the creation of a number of technologies that, without exaggeration, can be called real scientific and technical breakthroughs.
Having melted and rolled armor steel into sheets, metallurgists transferred their products to armored hull production. Here the metal was cut according to the template into the corresponding parts. In the production of "thirty-four" especially a lot of trouble was delivered by two parts of the hull: fenders (the inclined side of the side) and the vertical side plate. Both of them were long, even in width strips with oblique cuts along the edges.
The idea naturally suggested itself to roll a measuring strip equal in width to the finished parts. It was first formulated by the armored cars of the Mariupol plant in the summer of 1941. For trial rolling, we chose a slabbing mill at Zaporizhstal, where two echelons of armor ingots were sent. But then they did not have time to get down to business: the advancing German troops captured both the echelons and Zaporozhye itself.
At the turn of 1941-1942, during the evacuation and the development of the production of armor at the new factories, there was not enough stripe. However, in May 1942, the People's Commissariat of Ferrous Metallurgy again received an order to rent it - for T-34 and KV tanks. The task turned out to be difficult: the tolerances in width should not exceed -2 / + 5 millimeters, the crescent shape (bend) for the total length of the part was 5 millimeters. Cracks, sunsets and delamination were not allowed at the edges so that welding could be carried out without machining or flame cutting.
Experimental work began simultaneously in the rolling shops of the Magnitogorsk and Kuznetsk metallurgical plants, at first without any particular achievements. The rental of parts for the KV tanks was soon abandoned, but the T-34 was finally successful. The team of authors consisting of the head of the metallurgical department of the NII-48 G. A. Vinogradov, the chief engineer of the KMK L. E. Vaisberg and the engineer of the same plant S. E. stands "900" of the rail and structural mill is a completely new method of rolling "on the edge". In January 1943, 280 strips were issued, in February - 486, in March - 1636 pieces. In April, after all the required tests, the development of the gross production of measuring strips for the wheel arch liners of T-34 tanks began. Initially, they were supplied to UZTM and the Ural Tank Plant, and then to other factories - manufacturers of T-34 tanks. The scrap, which was originally 9.2 percent, had dropped to 2.5 percent by October 1943, and the substandard strips were used to make smaller parts.
A complete and accurate assessment of the new technology is given by the corresponding report of TsNII-48 dated December 25, 1943: “A fundamentally new method of rolling a wide armored strip“on the edge”was developed, tested and introduced into gross production, which was considered unfeasible until recently in the USSR and abroad. Obtaining a calibrated (measured) strip with a width of the finished part of the armored hull of the T-34 tank made it possible for the NKTP factories to adopt a new high-performance technology for the manufacture of armored parts without cutting longitudinal edges. Thanks to the application of the new method to one of the main armored parts of the T-34 tank (fenders), a very significant time saving (about 36%) was achieved when cutting them out. Achieved savings of 8C armor steel up to 15 percent and oxygen savings of 15,000 cbm per 1000 hulls”.
By the end of 1943, the rolling of a measuring strip was mastered for another part of the T-34 hull - the vertical part of the side. It only remains to add that the authors of this invention were awarded the Stalin Prize for 1943.
In the same 1943, by joint efforts of the laboratory of the Ukrainian Institute of Metals (headed by P. A. Aleksandrov) and workers of the Kuznetsk Metallurgical Combine and the Ural Tank Plant, a special periodic rolled profile was developed and mastered in production for the procurement of mass and critical parts of the "thirty-four" - balancer axes. The first experimental batch of a periodic profile was received at KMK in December, at the beginning of 1944 serial production began. By October, the Ural Tank Plant completely switched to the manufacture of balancer axles from a new blank, at the end of the year UZTM joined it. As a result, the productivity of the forging hammers increased by 63 percent and the number of part breakages decreased.
The successful work of the tank builders was greatly facilitated by the rolling stock of the bandage mill of the Novo-Tagil Metallurgical Plant. Starting in the spring of 1942, they supplied rolled shoulder straps with reduced machining allowances, in 1943 the allowances were reduced again. In combination with the new cutting tool, this made it possible to carry out laborious stripping of shoulder straps strictly on schedule and without much stress. A rare case: the People's Commissar of the Tank Industry V. A. Malyshev, in his order of September 28, 1943, considered it necessary to express special gratitude to the Tagil metallurgists.
And finally, the last example: in 1943, the rims of the T-34 support tanks, first at the Chelyabinsk Kirov plant, and then at other enterprises, began to be made from special profiled rolled products. This success was also noted in the order of V. A. Malyshev.
It remains to add that the specialists of the American company "Chrysler", having studied the T-34-85 tank captured in Korea, especially noted the perfection of the steel blanks from which the combat vehicle was made. And also the fact that they often outnumbered the products of the US metallurgical enterprises.