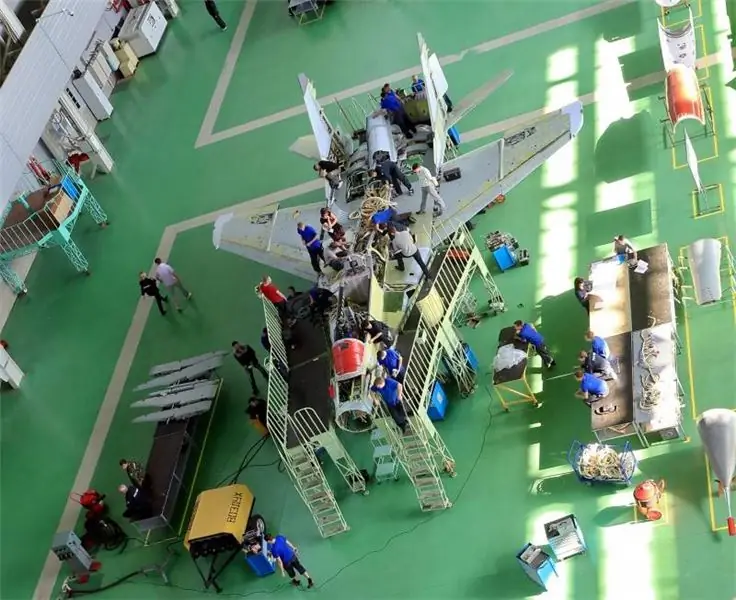
Successful aircraft manufacturers have always had strong planning. Today, the United Aircraft Corporation is implementing a new automated planning and monitoring system at most of its factories. One of the ambitious goals of these projects is to reduce aircraft assembly cycle times and increase labor productivity.
A modern aircraft - apart from design, technology, purpose and performance characteristics - is a product consisting of hundreds of thousands of elements - materials, parts, purchased components. And the plane is not assembled from them immediately, but through blanks, assembly units, units. The process goes from small to large - to compartments, tanks, wing parts. Moreover, the entire production process is stretched in cycles for months.
The Russian Aircraft Corporation (RAC) MiG has recently introduced an automated planning system. In 2016, the corporation completed a four-year project to increase the throughput of the fighter assembly line at production complex No. 1, located in the city of Lukhovitsy, Moscow region, from six to 24 aircraft per year, said Oleg Irkhin, head of the RAC MiG management organization service. RSK MiG has implemented several projects of automated control systems, both of its own design and of third-party contractors. They will serve to improve planning accuracy and track the progress of operations. One of the important parts of the project is related to the work of the domestic company Reitstep, says Irkhin.
“The United Aircraft Corporation several years ago began the implementation of automated planning systems at key sites - the Novosibirsk Aviation Plant. VP Chkalov, Komsomolsk-on-Amur Aviation Plant named after V. P. A. Gagarin (part of the Sukhoi company), as well as at enterprises in Voronezh and Moscow. Often the partner of the UAC was the company "Wrightstep", - says the adviser to the President of the UAC Petr Golubev. “And it takes about three years to fully assess the correctness of the system. Just so much time has passed at the majority of enterprises where the system has started working”.
The Soviet system no longer means "the best"
“In the USSR, there was a simple and effective, for those conditions, production management system. Unfortunately, it turned out to be completely inapplicable now. Working conditions have changed,”says Sergei Piterkin, Managing Partner of Wrightstep.
In the pre-perestroika time, the system worked for large-scale production - then a hundred civil aircraft were produced annually. A relatively short period of putting the machine into series - and the plant began to produce several almost identical products per month. Today, for example, in civil aviation, the series has become much smaller. An individual car may be, if not unique, then different from others. Accordingly, if you work according to the old system, for each product you need to carry out its own calculation of lead and backlog groups.
"Pull" correctly
Specialists of Rightstep (the company's headquarters is located in St. Petersburg) are implementing the Planning and Monitoring System both in aircraft construction and in related industries - helicopter construction, at some enterprises of Roskosmos.
One of the key management principles introduced with the new system is the transition to the so-called "pull", order-based production principle. In this case, the system is planning purchases of thousands of components "tied" to a specific end machine in a specific configuration for each customer and with the release date.. Each product (each order) is planned from this date (or - from the "take-off date") "back "By the time of the workshop production of assemblies and parts and the time of purchased or cooperative items, with an accuracy of one or several days and" down "and" down "- with a breakdown throughout the structure of the product, according to its technological composition," to ore ", i.e. e. to Accurate to the "shop call". At the same time, it is desirable that the Product Composition was maintained and entered into the SPM from the PDM system (from Product Data Management - product data management system), that is, from the organizational and technical system that ensures the management of all information about the product.
SPM rigidly stipulates “order-by-order” control, in which each aircraft is planned and controlled in production separately, according to its composition, determined by a specific serial number. And at the same time, the peculiarity of the SPM is that for each product a “directive” (“as it should”) and “calculated” (as it turns out) production and procurement plan are formed. And for each item of the composition of the order item - not only release, but also its launch into production and supply. At the same time, the “directive” plan can be configured with any desired (lifting for the plant) level of “rigidity”, ideally - for production / procurement “just in time”. And through this, to save the enterprise from many of today's "sores", for example, from overstocking of warehouses, from the production of a series of parts "in reserve",.
Response and accounting - now online
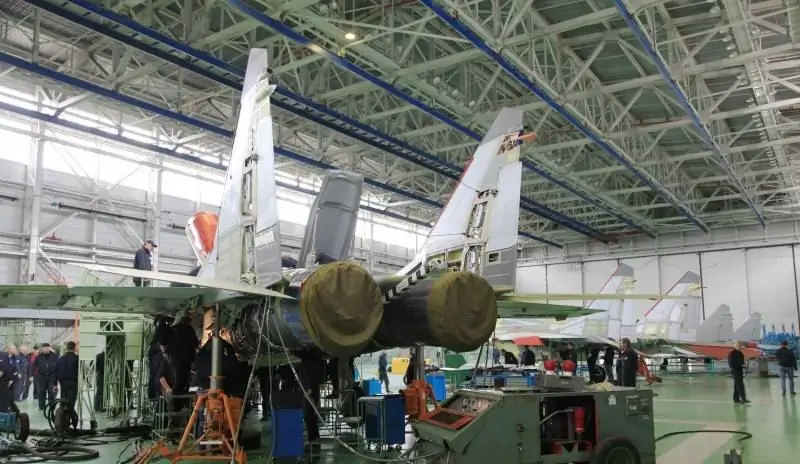
One of the conditions for the successful operation of the "pulling" system is the establishment of data exchange. Computer programs allow online monitoring of what is happening along the entire production and supply chain with a constant and simple indication of deviations from the plan. For example, earlier, when assembling the MiG-29 fighter, Oleg Irkhin's colleagues tracked about 200 key positions. Now, with the transfer of planning and monitoring to the SPM "Wrightstep", about 900 parameters are monitored. As a result, the volume of analyzed data has grown significantly. “For example, our older systems only monitored the completed build phase. The new software also makes it possible to “see” the beginning of this process. This way we can influence all stages of production in real time,”says Irkhin.
“It is important that the data is correct and processed correctly. Otherwise, the automated system will simply turn into automated chaos,”says Petr Golubev.
Planning and rescheduling is done frequently - at least every few days. This allows you to quickly take into account deviations arising in the production or purchasing process. SCM methods (from Supply Chain Management - supply chain management) and calculation algorithms are used, namely, modeling the supply chain of a plant and its environment.
The main postulate of system dynamics says that the efficiency of a production system depends primarily on the "speed of response" - on the time the system responds to external or internal changes. The higher the reaction rate, the more effective the system, including in monetary terms. For our real production facilities, this means fast and constant (ideally daily) re-planning, taking into account all changes taking place on and outside the plant. In practical application, this translates into rapid and frequent re-planning of the entire production and supply chain.