It seems that NASA has decided to make a "Martian" super rocket with the whole world: for this three divisions of the agency were involved at once. These are the George Marshall Space Flight Center, the Lyndon Johnson Space Center and again the John F. Kennedy Space Center, which provides the entire history with its launch sites.
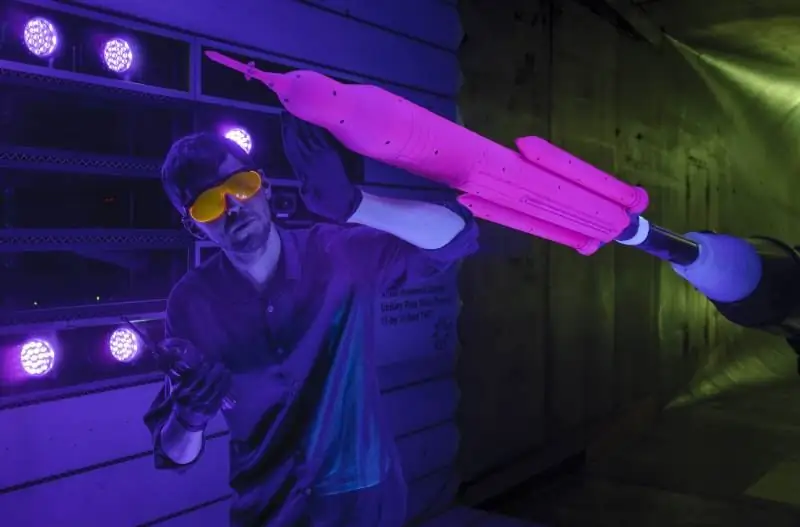
SLS mockup in NASA research wind tunnel
But this is not the whole company of developers. The Ames Research Center is responsible for the fundamental physical problems of the project, the Goddard Space Flight Center is responsible for the nature of payloads, and the Glenn Center, which deals with new materials and the development of payload fairings. Research programs in wind tunnels are assigned to the Lange Center, and testing of the RS-25 and J-2X engines is assigned to the Stennis Space Center. Finally, the assembly of the central block with the main propulsion system takes place at the Michuda plant.
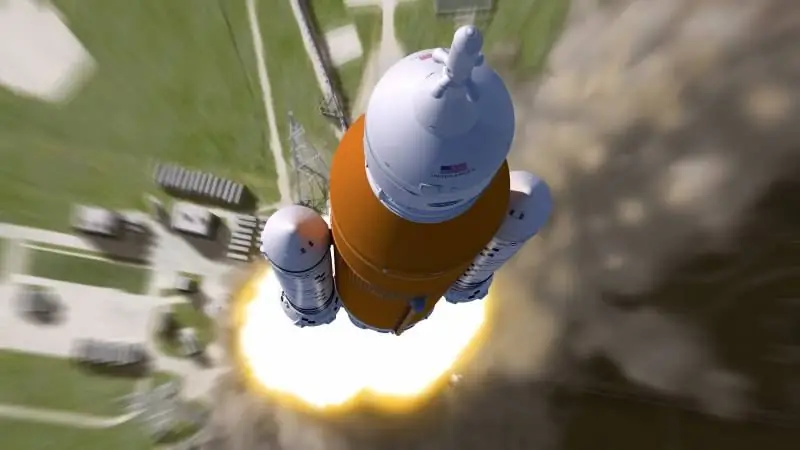
The entire SLS program is divided into three stages, united by several points: liquid oxygen and hydrogen in propulsion engines, as well as a multisection solid propellant booster. The first stage of the central block (Core Stage) with a length of 64.7 m and a diameter of 8.4 m will also be the same for all modifications. So, the firstborn SLS Block I has an equivalent payload mass of 70 tons - the necessary thrust for this weight is provided by four RS-25D engines. Actually, this first version of the SLS is intended for certification of the central unit and the implementation of experimental and experimental missions. The upper stage is represented by the "temporary cryogenic upper stage" ICPS (Interim Cryogenic Propulsion Stage), built on the basis of the second stage of the Delta IV Heavy launch vehicle. ICPS has one engine - RL-10B-2 with vacuum thrust of 11, 21 tf. Even in this "weakest" version of Block I, the rocket will develop a launch thrust by 10% more than the legendary Saturn V. The carrier of the second type was named SLS Block IA, and the equivalent carrying capacity of this giant should already be under 105 tons. Two versions are envisaged - cargo and manned, which should return the Americans more than forty years ago and finally send a person back out of low-earth orbit. NASA's plans for these vehicles are the most modest: as part of the EM-2 mission, somewhere in the middle of 2022, fly around the moon with a crew. A little earlier (mid-2020), it is planned to send astronauts to circumlunar orbit on the Orion spacecraft. But this information dates back to the summer of 2018 and has been repeatedly corrected before that - so, according to one of the projects, SLS was supposed to soar into the skies this fall.
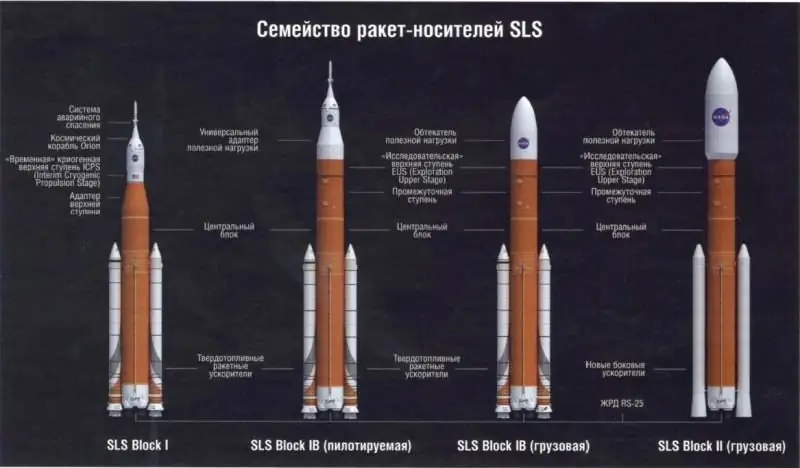
SLS Block II - a carrier with an equivalent payload of 130 tons, already equipped with five RS-25D engines on the central block, as well as an "exploration upper stage" EUS (Exploration Upper Stage), which, in turn, has one or two J- 2X thrust of 133.4 tf each. "Truck" based on Block II is distinguished by an over-caliber head fairing with a diameter of 10 meters at once. These will be true giants, if everything goes well for the United States: in the final version of the rocket, the launch thrust of the rockets will be 1/5 higher than that of the Saturn V. And the plans for the Block II series are also extremely ambitious - in 2033, send a manned mission EM- 11, which will wander in space for at least 2 years. But before this significant date, the Americans plan to fly into the lunar orbit 7-8 times. Whether NASA is seriously planning to land astronauts on Mars, no one knows.
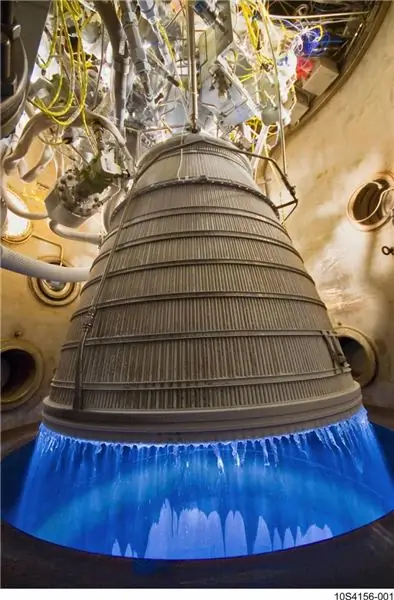
Tests of the CECE (Common Extensible Cryogenic Engine) experimental controlled-thrust cryogenic rocket engine, which was used under the RL-10 improvement program, operated since 1962 on Atlas, Delta iV, Titan and Saturn I rockets. -3.
The history of the SLS series engines as the main components of the rocket began in 2015 at the stands of the Stennis Center, when the first successful fire tests lasting 500 seconds took place. Since then, the Americans have been going like clockwork - a series of full-fledged tests for a full flight resource instills confidence in the performance and reliability of the engines. William Hill, First Deputy Head of NASA's Manned Research Systems Development Directorate, said:
“We have approved the SLS project, have successfully completed the first round of tests of the rocket engines and accelerators, and all the main components of the system for the first flight have already been put into production. Despite the difficulties that have arisen, the analysis of the results of the work speaks of confidence that we are on the right track to the first flight of the SLS and its use to expand the permanent presence of people in deep space."
During the work on the engine, changes were made - the carriers of the first and second stages were equipped with solid fuel boosters (accelerators), which is why the model was named Block IB. The upper stage of the EUS received a J-2X oxygen-hydrogen engine, which had to be abandoned in April 2016 due to a large proportion of new elements that had not been previously worked out. Therefore, we returned to the good old RL-10, which was mass-produced and has already managed to "swoop in" for more than fifty years.
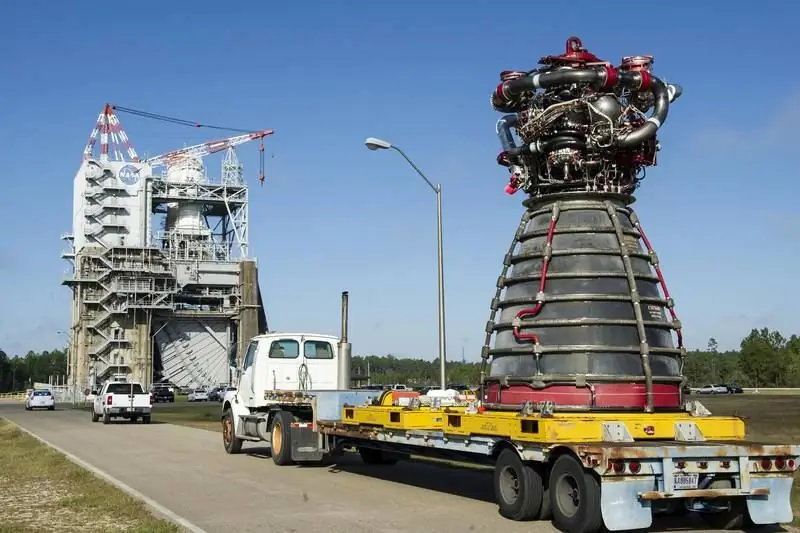
Reliability has always been paramount in manned projects, and not only at NASA. In the official documents NASA mentions: “A bundle of four RL-10 class engines meets the requirements in the best way. It has been found that it is optimal in terms of reliability. " The five-section booster was tested at the end of June 2016 and became the largest solid-propellant engine ever built for a real launch vehicle to date. If we compare it with the Shuttle, then it has a launch weight of 725 tons versus 590 tons, and the thrust is increased compared to its predecessor from 1250 tf to 1633 tf. But SLS Block II should get new super-powerful and ultra-efficient accelerators. There are three options. This is the Pyrios project from Aerojet Rocketdyne (formerly Pratt & Whitney Rocketdyne), equipped with two rocket engines powered by oxygen and kerosene with a thrust of 800 tf each. This is also not an absolute innovation - the "engines" are based on the F-1 developed for the first stage of the same Saturn V. Pyrios dates back to 2012, and 12 months later, Aerojet, together with Teledyne Brown, is working hard on a liquid booster with eight oxygen-kerosene AJ-26-500. The thrust of each can reach 225 tf, but they are assembled on the basis of the Russian NK-33.

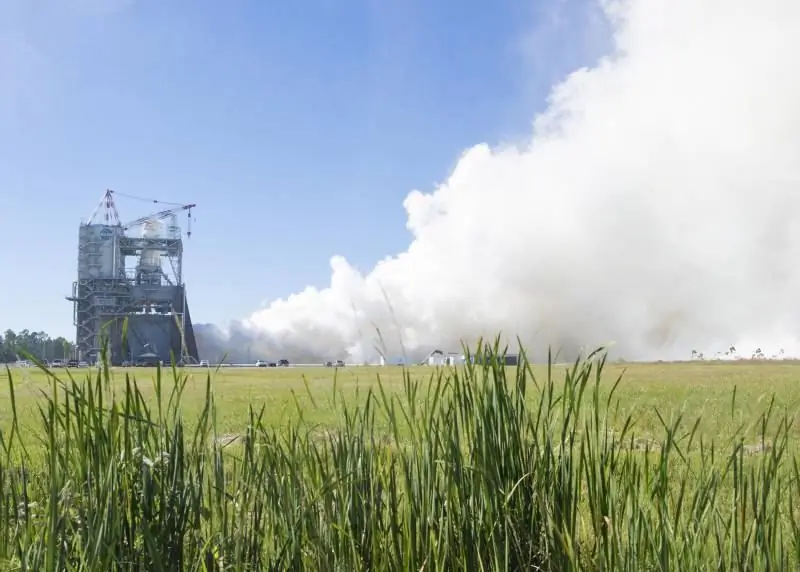
Testing the RS-25 oxygen-hydrogen engine at the Stennis Center booth, Bay St. Louis, Mississippi, August 2015
And finally, the third version of the engine for the SLS is presented by Orbital ATK and is made in the form of the most powerful four-section solid-fuel accelerator Dark Knight with a thrust of 2000 tf. But it cannot be said that everything was completely smooth for American engineers in this story: a lot of competencies and technologies were lost with the closure of the Apollo and Space Shuttle projects. I had to come up with new ways of working. For example, friction stir welding was introduced to assemble the fuel tanks of future missiles. The Michuda plant is said to have the largest machine for such a unique welding. Also in 2016, there were problems with the formation of cracks in the manufacture of the central block, more precisely, in the liquid oxygen tank. But most of the difficulties were overcome.
The Americans are gradually returning their astronauts to low-Earth orbits and beyond. A logical question arises: why do this if robots do an excellent job? We will try to answer this a little later.