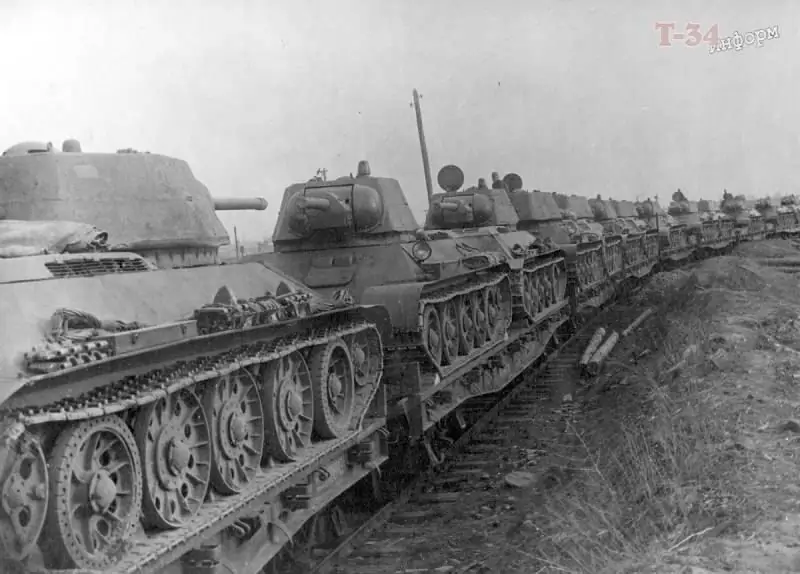
TsNII-48
The Central Research Institute of Structural Materials, or TsNII-48 Armored Institute, played a key role in the emergence of anti-cannon armor in Soviet tanks. At a time when the production of tanks was forced to move to the Urals and the tank crisis of 1941-1942 broke out, it was the Armored Institute specialists who coordinated efforts to resolve it. Consider the history of the emergence of this outstanding institution.
Andrey Sergeevich Zavyalov, one of the main creators of the legendary T-34 tank armor, became the ideological inspirer of the appearance of the TsNII-48 on the basis of the Izhora central armored laboratory. The young engineer began his career back in 1930 at the All-Union Scientific Research Institute of Metals, and two years later he was appointed head of the Central Factory Laboratory of the Izhora Plant.
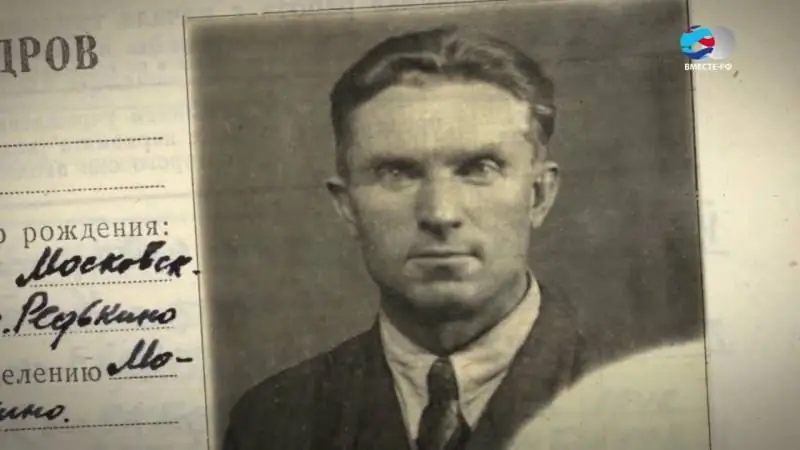
It was here that Zavyalov came up with the largely revolutionary idea of equipping tanks with anti-cannon armor, which was strengthened after testing the T-26 armor with a 37-mm cannon. It turned out that the light tank was not pierced through by the most powerful shells. Then a light tank was made from chrome-silicon-manganese steel of the PI brand of 15 mm thickness. By the way, this was bypassing the main technology, which required 10- and 13-mm cemented armor, which, unfortunately, neither Mariupol nor the Izhora plant was able to do with high quality. As a result, the T-26 was overweight by 800 kilograms, and even did not hold small-caliber shells - this was largely a consequence of the high proportion of rejects (up to 50%) in tank corps. Zavyalov sounded the alarm in 1935 (recall that he was one of the first in the world with such an initiative), but in the end he was almost fired as a "troublemaker." The Council of Labor and Defense, held in May 1936, at which Zavyalov conveyed his idea to Zhdanov and Stalin, helped. As a result, the Main Directorate for the Production of Armor appeared, to which the Izhora and Mariupol factories were transferred, and their laboratories were renamed into armored ones. Do not think that Andrei Zavyalov took care of only tanks in this way - in the educated laboratories, they worked, among other things, on the armor of destroyers and battleships, and later on the Il-2 attack aircraft.
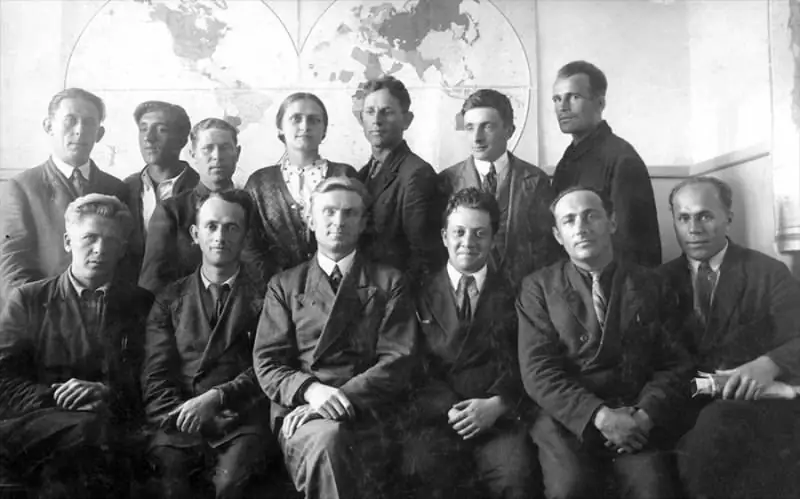
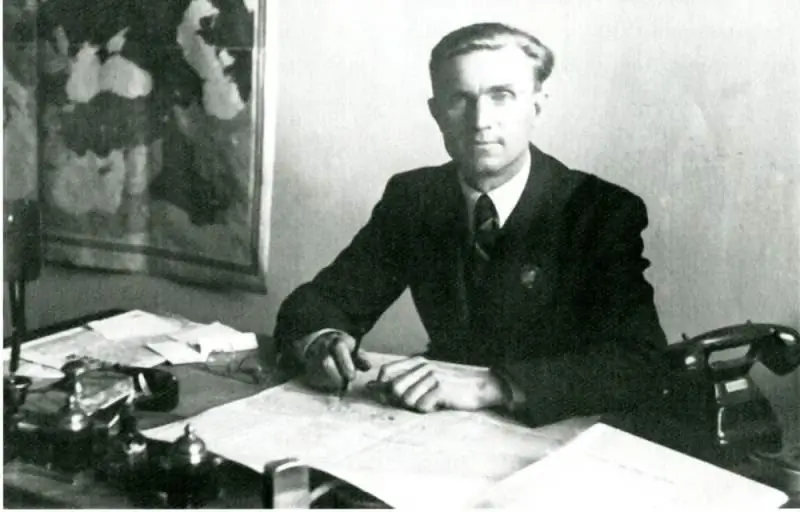
Since 1938, when the TsNII-48 was formed under the leadership of A. S. Zavyalov, the institute has been closely engaged in the development of new types of armored steel for medium and heavy tanks. Steel was brewed in 10-30-ton electric furnaces and 30-40-ton open-hearth furnaces with exact observance of all the nuances of armor production. The highest technological discipline required clean materials and containers, as well as precise dosing of alloying materials: manganese, chromium, nickel, silicon and molybdenum. One of the first brands of homogeneous armor at the Armored Institute was 2P steel, intended for areas of the hull that are not subject to high shock loads. However, the real glory of TsNII-48 was brought by the 8C armor steel, which is distinguished by its high hardness and is intended for the manufacture of rolled and cast armor parts. It was the 8C that would later become the basis of the armor power of the T-34 medium tanks.
The scale of research work at the Armored Institute is evidenced by the fact that during the search for the optimal recipe, more than 900 armor plates of various composition and thickness were shot. At first glance, the new solid armor had only advantages - it welded perfectly, confidently held most anti-tank shells with a caliber of up to 50 mm and surpassed the German counterparts in terms of the combination of qualities. However, 8C showed such remarkable properties only with strict adherence to the technological cycle of production, which was possible only at the Izhora plant and in Mariupol. So, if the carbon content in high-hardness armor is increased to 0, 36%, then the rejection by cracks in the parts increased to 90%! How cracks in the hulls became a real scourge of T-34 medium tanks in the first half of the war was described in the article “Cracks in the Armor. Defective T-34s for the front."
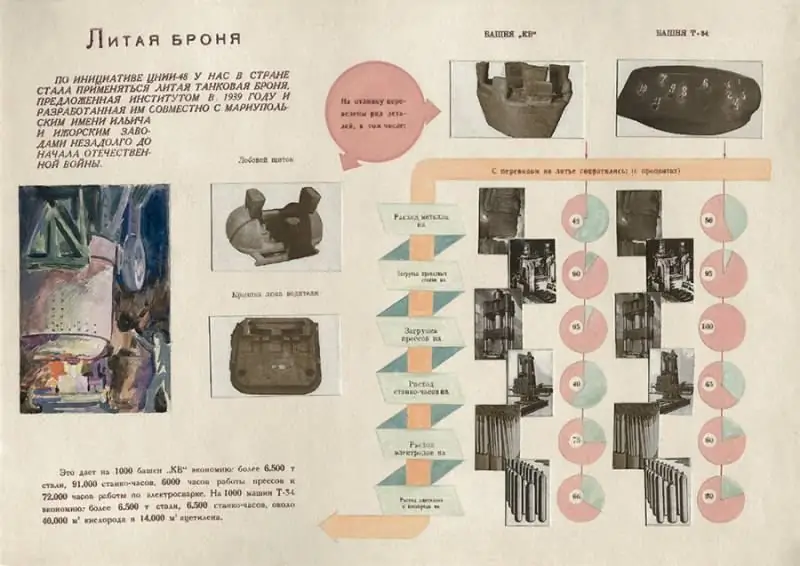
In fairness, it should be noted that the first medium tanks with cracks appeared in the Red Army not during the war, but back in 1940 on the T-34 of the first series, whose armored hulls were manufactured with violations. At the same time, it is important to know that heavy KV tanks did not suffer from such an ailment due to the different composition of the armor. It's all about the theoretical calculations and practical experiments of the Central Research Institute-48 of the late 30s, during which it became clear that 8C can be hit by armor-piercing ammunition with a caliber of more than 75 mm. And here, in all its glory, the negative aspects of high-hardness alloys were manifested - they did not just break through, but split into fragments of various sizes. A simple increase in thickness did not bring much effect - the compression wave, even without penetration, caused a very dangerous fragmentation field inside the tank. Therefore, for KV in the "Armor Institute" they welded homogeneous armor steel of medium hardness, capable of withstanding projectiles with a caliber of more than 75 mm. But here, too, there were some nuances. It turned out that homogeneous armor resists sharp-headed shells worse than multilayer, which can be fraught with normal damage to the tank. A couple of cases were even recorded during the Soviet-Finnish war, when harmless 37-mm sharp-headed shells very successfully hit the KV and entered the armor by 68 mm, that is, they almost pierced the tank. Then the head of the special technical bureau, N. A. Rudakov, began to sound the alarm, proposing to introduce an expensive procedure for cementation of armor, but things did not go beyond experiments at the Izhora plant. In the course of experimental work, it turned out that the advantage of cemented armor over homogeneous one manifests itself only at a thickness of more than 150 mm, which, of course, was not entirely possible to implement in a series. Actually, this determined the appearance of medium and heavy tanks of the Soviet Union, welded from homogeneous armor of high and medium hardness, which perfectly resists blunt-headed projectiles, but often succumb to sharp-headed projectiles approaching the target at angles close to normal. In other cases, rational corps angles were an excellent panacea for most of the German artillery (at least during the initial period of the war). Returning to the problem of cracking in the T-34 hulls, it should be said that they appeared on the KV, but were not critical and did not reduce the projectile resistance.
"Armor Institute" in the war
TsNII-48 specialists already in July 1941 were working on restructuring for the new military needs of the 14 largest enterprises in the Soviet Union. Among them are the Magnitogorsk, Kuznetsk, Novo-Tagil and Chusovskoy metallurgical plants, as well as the famous Uralmash and Gorky Krasnoe Sormovo. Among the many works of the Armored Institute, only by the beginning of 1942 the following projects were put forward for the Stalin Prize (as they say now): KV tanks in the main open-hearth furnaces of large capacity "," Development and implementation in production of the process of welding heavy tanks ", as well as" A new type of anti-cannon high-hardness tank armor with a thickness of 20, 30, 35, 40, 45, 50 and 60 mm from silicon chromium-nickel-manganese-molybdenum steel grade M3-2 ". In February 1942, at the Verkhne-Isetsky plant, TsNII-48 specialists developed and implemented the technology of casting turrets for T-60 light tanks, which significantly reduced energy and resource consumption.
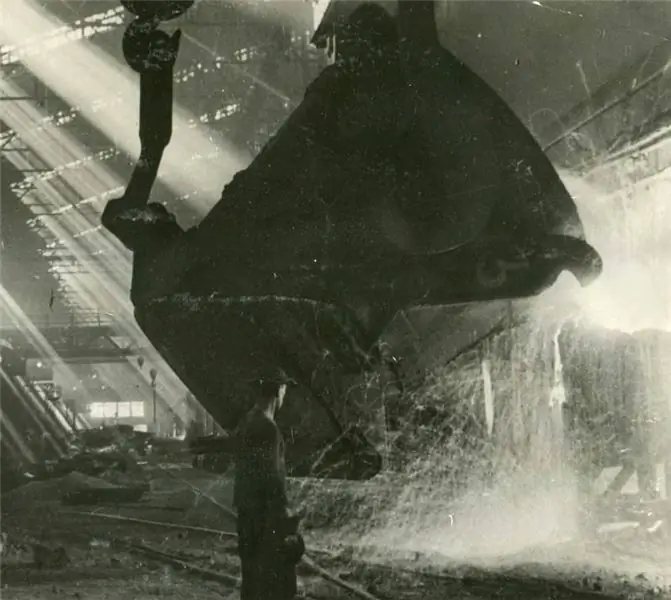
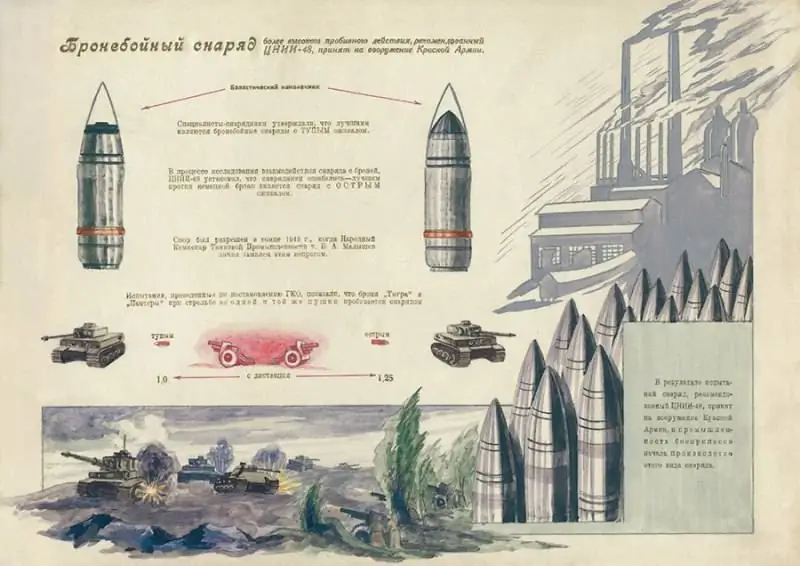
In general, the situation with the Magnitogorsk Metallurgical Plant was close to a catastrophe - at the beginning of the war, an order came to organize the production of armored steel for tanks. And before that, the enterprise produced exclusively "peaceful" steel, there were no specific "sour" open-hearth furnaces in the shops and, naturally, there was not a single specialist in casting of such complex compositions. As a result, the issue was resolved by TsNII-48 specialists, who were the first in the world to come up with the idea of smelting armor in the main furnaces - read the full name of the corresponding design work above. This allowed two months ahead of schedule to carry out the first issue of armor from 150-, 185- and 300-ton open-hearth furnaces. And on July 28, 1941, for the first time in the world, it was also possible to roll an armor plate on a civilian blooming that was not intended for this. As a result, every second Soviet tank was made of Magnitogorsk armor. And this scenario was repeated with varying degrees of success at other enterprises of the ferrous metallurgy of the Soviet Union. But such impetuosity, of course, has a downside.
In the book "Tank Industry of the USSR during the Great Patriotic War," Candidate of Historical Sciences Nikita Melnikov writes that according to the standards until 1941, the 45-mm side armor of the T-34 had to withstand a direct hit from a 45-mm anti-tank projectile from a distance of 350 meters. But already in 1942, at the height of the emergency production of tanks at the Ural enterprises, the standard for armor resistance was seriously reduced - exactly such an ammunition should not have penetrated the side of the tank already from 800 meters.
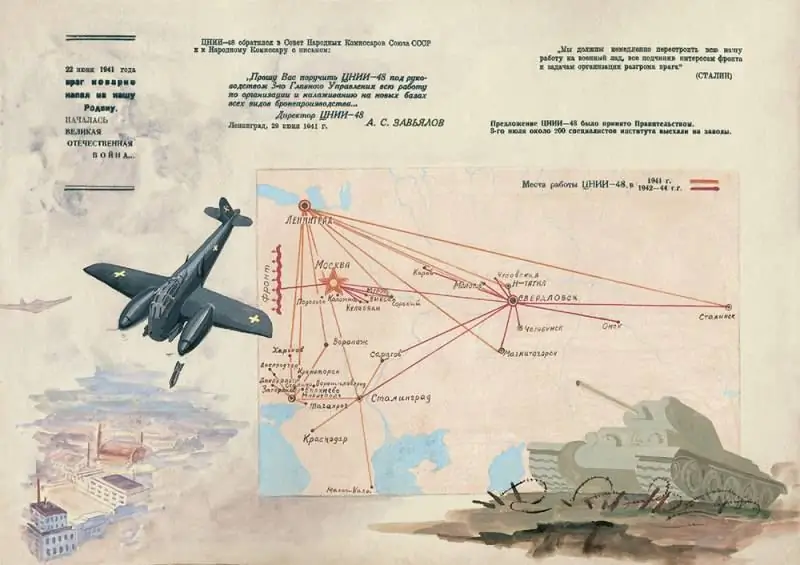
The Armored Institute can be credited with the introduction by the summer of 1942 of the technology for the production of cast turrets for KV tanks. This innovation, which became largely forced, among other things, reduced the volume of turret machining by 40%, reduced the consumption of scarce rolled armor by 20% and reduced press and bending work at tank factories by 50%. And the use of casting in the manufacture of the T-34 turrets (also using the TsNII-48 technology) allowed at least this part of the tank to get rid of the notorious cracks.
In addition to purely technological work at tank production facilities, TsNII-48 specialists were also engaged in statistical research on the battlefields. In the future, this became the basis for the development of tactics for the use of domestic armored vehicles and recommendations for the destruction of enemy vehicles.
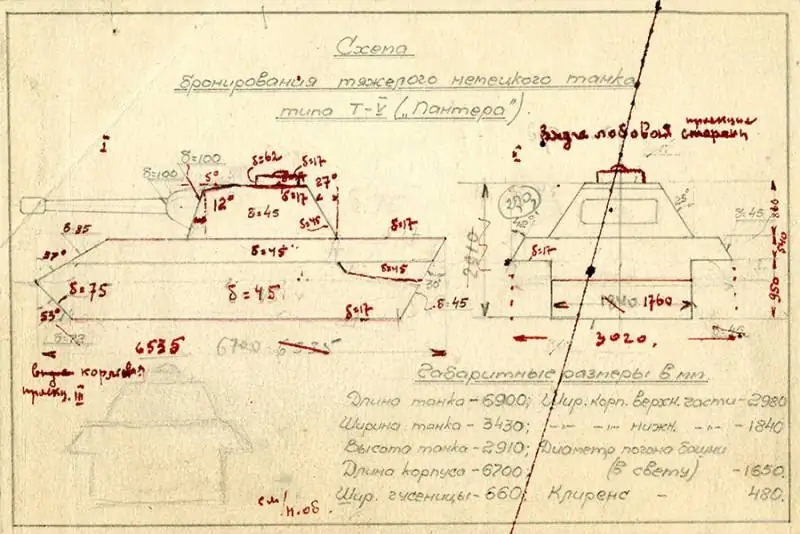
In the conditions of a shortage of alloying additions to the armor plates in 1943, a new brand of armor - 68L - was created at TsNII-48 together with the Ural Tank Plant No. 183. It was adopted as an inexpensive substitute for the 8C, since for 1000 tanks this alloy saved 21 tons of nickel and 35 tons of ferromanganese.
The Soviet Union emerged victorious from the Great Patriotic War, and a small team of TsNII-48 played a significant role in this, which became a real forge of armor steels for the front, whose work was accompanied by real triumphs and forced failures.