So, it is obvious that "bare armor" took place, but they were also covered to cover them, as was the case in the past, when surcoats were worn over chain mail. So, with white armor, the knights slapped a tabar cloak in the form of a short sleeveless cape that reached the waist, which was often covered with heraldic images. But often it was just a beautiful and expensive fabric.
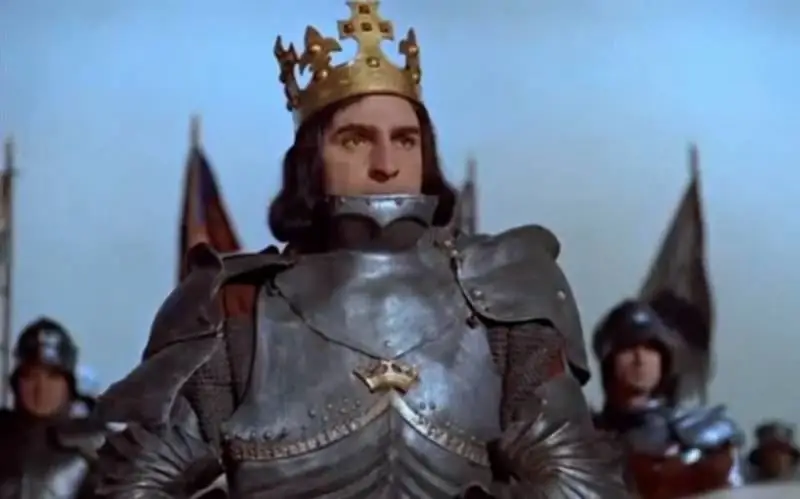
A shot from Laurence Olivier's film "Richard III": as you can see, Richard was "attached" here to a more reliable "chin", but … they completely forgot about the shoulder pads and besagyu - "defenders" of the armpits.
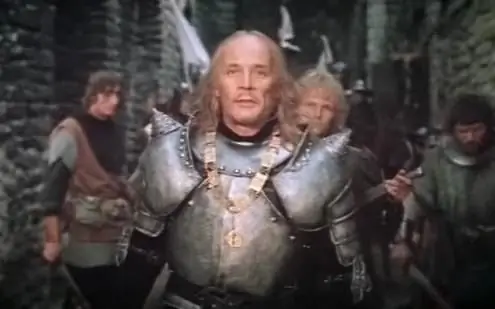
Our "Soviet" Richard III from the movie "Black Arrow" (1985) will look much more reliable in this regard. Although without the "pyramids" on the shoulders, it would be quite possible to do!
In Italy, wearing this cloak with armor has become so fashionable that Antonio Pisanello in 1450, on his painting “St. George”portrayed the saint not only in Milanese armor with characteristic massive shoulder pads, but also put on such a cloak, called the djornia. In 1476, such a cloak, worn over armor, was also worn by Duke Charles the Bold, and in it he died. Today, this cloak, which has become the prey of the Swiss, is exhibited in the Historical Museum of the city of Bern, so that what belongs to the clothes in the movie "Secrets of the Burgundian Court" is reproduced very accurately. For some reason, there was a problem with some of the details of the armor. This cloak is made of red satin, with sleeves and puffs near the shoulders, while tapering towards the wrists. D. Edge and D. Paddock believe that, in general, nothing indicates that this cloak was intended to be worn along with armor, but for some reason the duke put it on? And it is on the armor!
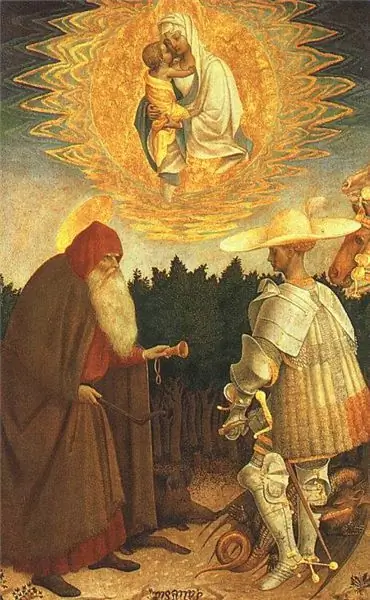
St. George and St. Mary”painting by Antonio Pisanello.
Interestingly, in St. George's painting by Pisanello, Giornia closes his armor to the knees both in front and behind, but at the same time their shoulders are fixed for some reason over not only the cloak, but also the sleeves that reach the elbow. I wonder how this could be done in reality? Well, and the saint is also depicted in a hat, which is somewhat amusing in our opinion, but apparently, it was quite consistent with the trends of that time.
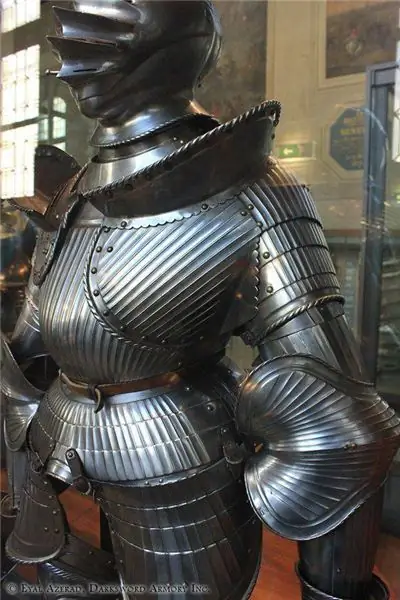
"Maximilian armor" of the XIV century. Germany. Army Museum, Paris. An example of rationalism, taste and quality.
It is known, again, that methods such as chasing and metal carving to decorate armor were used as far back as archaic Greece. But then they worked with copper and bronze. Now the gunsmiths had to decorate the iron, which was much more difficult. That is why the earliest way to decorate such armor was … coloring! Moreover, it is clear that the easiest way is to paint them with paint, but over time this technique was considered primitive and began to directly paint the metal itself. First of all, or rather, first of all, gunsmiths mastered the bluish bluing technology. At the same time, Italian masters achieved such art in it that they could not only get a uniform color even on the largest items, but also get any desired shade. Violet and especially red (sanguine) shade was very much appreciated. They knew how to give iron and an elegant gray tone, which distinguished many of the famous inlaid Milanese armor. Known black bluing, which was achieved by firing products in hot ash; well, brown bluing became fashionable in Milan back in the 1530s. That is, the armor continued to remain smooth and without any patterns, but … "white" was no longer, but were "red", "brown", "black" and "blue".
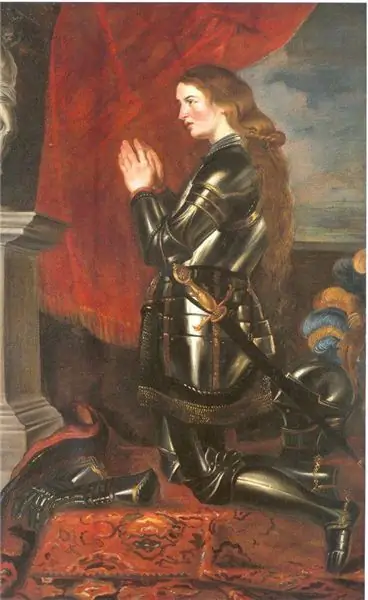
Joan of Arc. Painting by Peter P. Rubens, 1620. Jeanne is depicted in burnished armor.
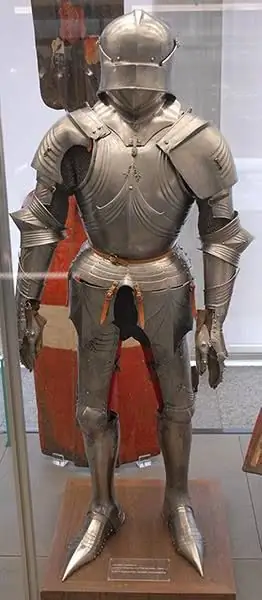
"White" Gothic armor. 1470 - 1480 German National Museum. Nuremberg, Germany.
Then, already in the middle of the 15th century, Italian craftsmen began to use engraving to decorate armor, which, already in the 1580s, began to be combined with gilding. Both parts of the armor and all the armor were gilded! The method was very simple, although very harmful. Gold was dissolved in mercury, after which, together with various additives, the resulting "amalgam" was applied to the product, which was heated on fire. At the same time, the mercury evaporated, and the gold was very firmly combined with the base metal. For example, very beautiful and at the same time durable gilding is visible on the Milanese armor made by the Fijino master, made in the 1560s.
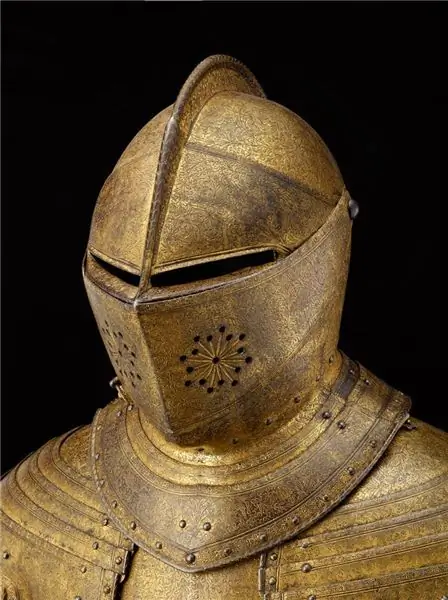
Gilded armor of King Charles I 1612 Royal Armory, Tower, London.
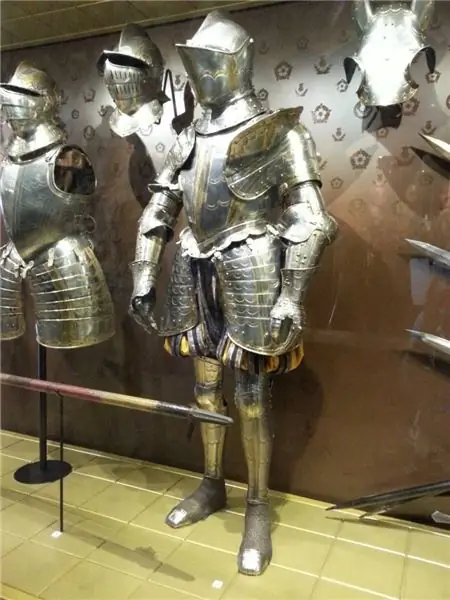
Armor 1570. Royal Armory, Tower, London. Decorated with embossing and gilding.
At the end of the 15th century, a method of decorating armor was invented, which consisted of trimming them, as well as stripes and emblems, which were made using acid etching. The decorative effect depends on whether the image on the metal was convex, and the background was recessed, or vice versa. In the first case, we see an image with a very flat relief, and in the second, something similar to a copper engraving. But etching was seldom used. It was combined with blackening and gilding. When using etching with blackening, special "niello" and caustic mineral oils were rubbed into the resulting depressions, after which the product was calcined. At the same time, the oil evaporated and the "mobile" was combined with the metal. In the case of etching with gilding, amalgam was rubbed into the recesses, after which heating followed again, followed by processing the product with files and polishing.
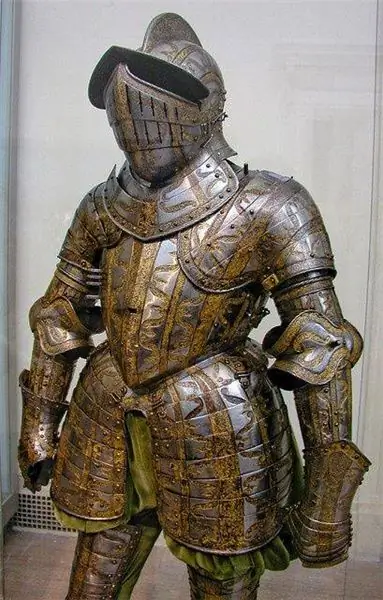
Ceremonial armor of the 16th century Metropolitan Museum of Art, New York. Decorated with etching and gilding.
Actually, it was possible to decorate with such blackening not only recesses, but also the entire surface of the armor. For this, the "black" is used, consisting of a mixture of silver, copper and lead in a ratio of 1: 2: 3, which looks like a dark gray alloy. Such blackening is called "niello", well, and its technology, like many other things, came to Europe from the East. And, by the way, only in the East were helmets and shells completely decorated with blackening. In Europe, this technique was mainly used by Italians; and already in the 16th century its use was greatly reduced, giving way to cheaper blacksmith bluing.
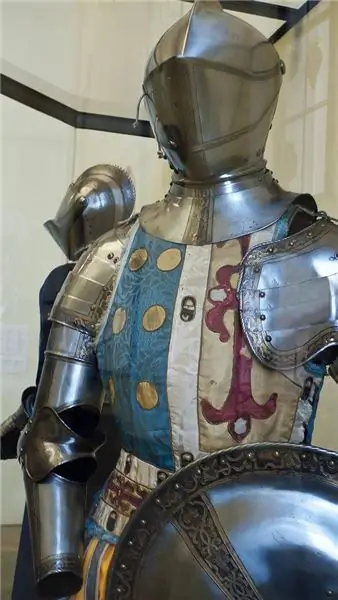
Ceremonial armor with a cloth-covered cuirass depicting the coat of arms of their owner. Belonged to don Sancho de Avila. Made in Germany in Augsburg in 1560 Philadelphia Museum of Art, Pennsylvania, Philadelphia.
With regard to etching, this method was also very simple and therefore became very widespread in Europe. Its essence was that a special "paste" of wax, bitumen and wood resin was applied to the surface of iron or steel, after which a drawing was scratched on it. At the same time, the "scratches" reached the metal itself, and the lines could be either very thin (for this they used needles), or rather wide. Then a side of wax was made around the drawing and, thus obtaining a semblance of a cuvette ", a special" etchant "was poured into it. Usually it was a mixture of acetic and nitric acids and alcohol. However, the "fatigue" of the composition was not very important, because at that time no one was in a great hurry to go anywhere. The time of removal of the composition from the surface of the product was important so that it did not eat through the metal. Then the “paste” was washed off, and the resulting pattern was corrected with graters or etched again to achieve a “play” of reliefs.
At the beginning of the 16th century, when many German armor was blued to black and blue, there was a way to decorate them with etching over blackening. In this case, the burnished surface was covered with hot wax and, as with conventional acid etching, a pattern was scratched on it so that the metal was visible. After that, as soon as the product was dipped in strong wine vinegar, the bluing disappeared, and white polished metal was revealed! After that, the wax was removed, and the light pattern on a black or blue background remained pleasing to the eye. Sometimes it was also scraped out with graters, and this technique was used until the 17th century.
A safer, albeit expensive, method of gilding was the blacksmith's method, which consisted in the fact that gold foil was applied to the red-hot surface of the iron product and smoothed with a polish. Known Germanic armor of the 1510s from Augsburg, decorated in this way.

Armor 1510 Milan. Needle engraving and gilding. Weight 8987 g. Metropolitan Museum of Art, New York.
A very ancient way of decoration is inlaid, taouching or "notching". In Italy, this technique spread in the 16th century as "lavoro all'Azzimina" or "alla Gemina", both of which have Arabic roots. This technique was used in the West even in ancient times, but later it was retained by the Indians, as well as by the Persians and Arabs, who decorated helmets and shells made of plates in this way. From them this art passed to the Spaniards and Italians. Already at the beginning of the 16th century, the technology of inlaid metal was successfully used by the masters of Toledo, as well as Florence and Milan, from where inlaid weapons were distributed throughout Europe. The essence of the method is well known and consists in engraving an ornament on metal, after which small pieces of gold or silver wire are hammered into the indentations made with a cutter. Then the metal product that has been "cut" is heated, and the inlay is securely connected to its base. There are two types of such incrustation: flat, flush with the surface of the product, and relief, that is, protruding above it. The latter, of course, is much more difficult, since the protruding parts need additional processing, while flat inlay is quite enough to file and polish. By the way, after that, the iron can be painted gray or blue, but this color will not fall on gold or silver! However, this technique is laborious, and therefore very expensive, which is why it is used on relatively small surfaces.
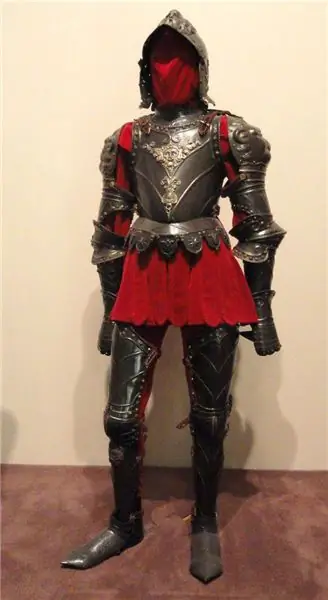
Embossed ceremonial armor 1500 - 1600 from Italy. Arsenal Higgins. Worcester, Massachusetts.
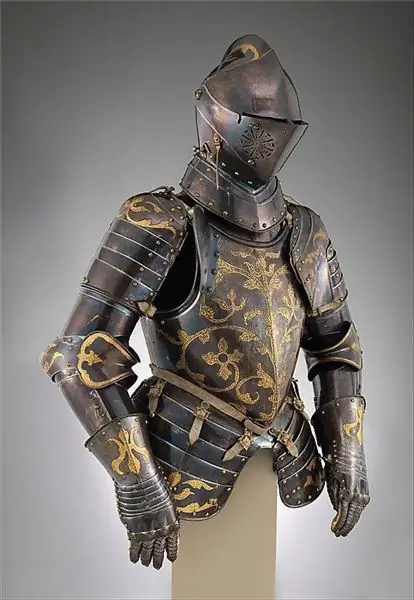
Embossed "notch" for metal. Armor for walking duel of Prince Christian I of Saxony. Metropolitan Museum of Art, New York.
Also, in the second half of the 15th century, such a method of finishing armor appeared, as iron chasing. It is clear that, again, even the Indians of the Copper Stone Age in America knew her. But they minted in copper. The hardness characteristic of iron greatly impedes this method of processing. But as soon as large surfaces appeared on the armor, the idea of subjecting them to chasing took possession of the minds of many weaponsmiths.
The difficulty lies in the fact that, unlike copper or silver, iron needs to be heated for minting. Rough processing always starts from the reverse side, knocking out the overall plastic shape, and thin processing is carried out both from the front and from the reverse side, which is why this technology received the French name "repoussé" - "counter-pushing". But then the technology became the common property of European masters, so that chased works are known in Milan, and in Florence, and in Augsburg.
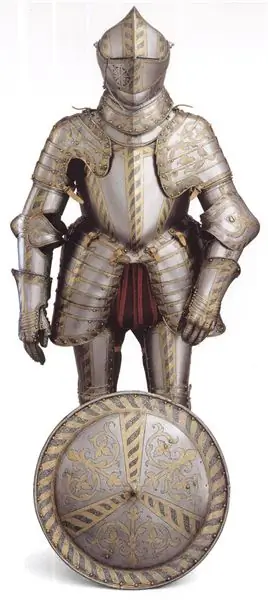
Parade combat armor with a round rhondache shield of Friedrich Wilhelm I, Duke of Saxe-Altenburg, Augsburg 1590. Royal Arsenal, Tower.
There is also iron carving. Here, work is carried out with the help of gravers and a chisel. And this technique has also been used to decorate armor and weapons. Italy was ahead of other European countries here and in the 16th century it overtook all of them. Although in the 17th century, French and German craftsmen appeared who surpassed the Italians in the beauty of their products. Chasing was used mainly in the manufacture of armor from sheet metal, and carvings on iron and other metals were used to decorate the handles of swords, swords and daggers, gun locks, barrels, stirrups, horse mouthpieces, etc. Chasing, like iron carving, was widely used masters from Milan, as well as Florence, Venice, and later became widespread in Augsburg and Munich, and was combined with inlay and gilding. Spanish armourers of the early 17th century combined chasing and carving with gilding, and the motives of their ornaments were not too rich, which indicates the beginning of the decline of this type of craftsmanship.
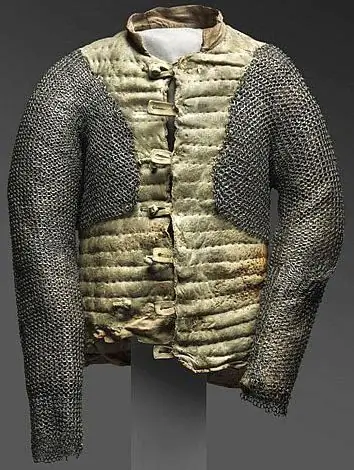
Chain mail, even when it was no longer used as a solid armor, continued to be used for a long time in such under-armor tunics worn under one-piece forged armor. Everything that they did not cover was covered by chain mail and, moreover, it did not restrict movement! Philadelphia Museum of Art, Pennsylvania, Philadelphia.
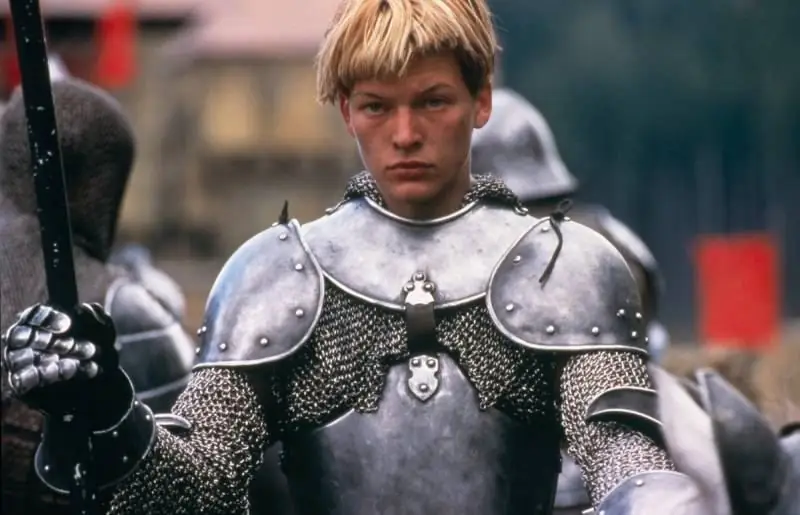
And this is how it looks in the 2005 film about Jeanne d'Arc. It was precisely the early cuirasses that consisted of two parts, both in front and in the back, and they were fastened with straps. Sometimes, only the lower part was worn, and the top was covered with cloth or chain mail.
Finally, enamel is perhaps the most luxurious type of decoration for armor and at the same time the most unnecessary. Enamel art appeared in the early Middle Ages and was widely used in jewelry, but for a long time it did not find use among gunsmiths. However, in the early Middle Ages, cloisonné enamel was used to decorate sword handles and shield details. Later, it came in handy for finishing sword hilts and sheaths, and the production centers of these were Limoges in France and Florence in Italy. Well, in the 17th century, enamel was mainly used to decorate the butts of richly decorated rifles, and on powder flasks.
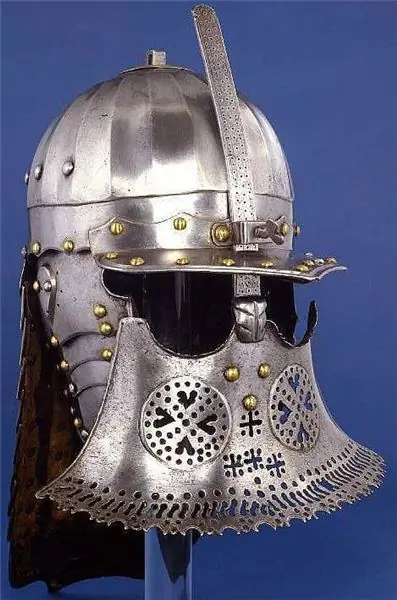
Polish hussar helmet decorated with a cut-out pattern, late 17th century. Fitzwilliam Museum.