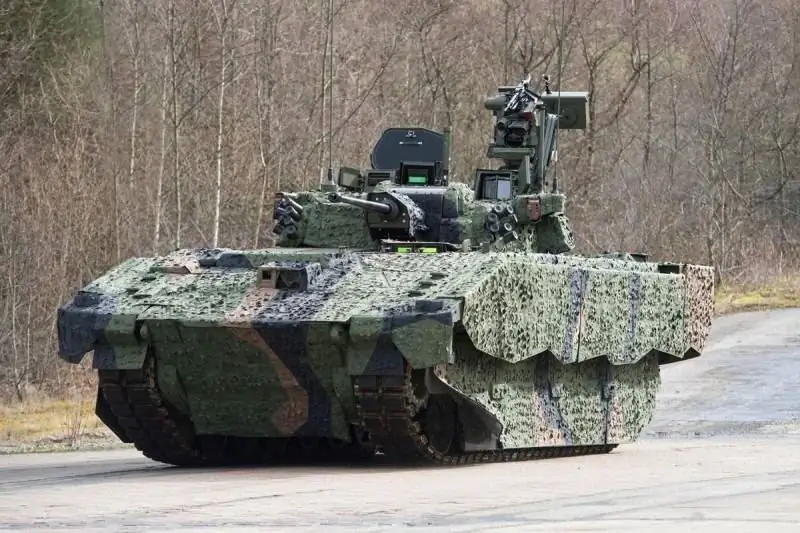
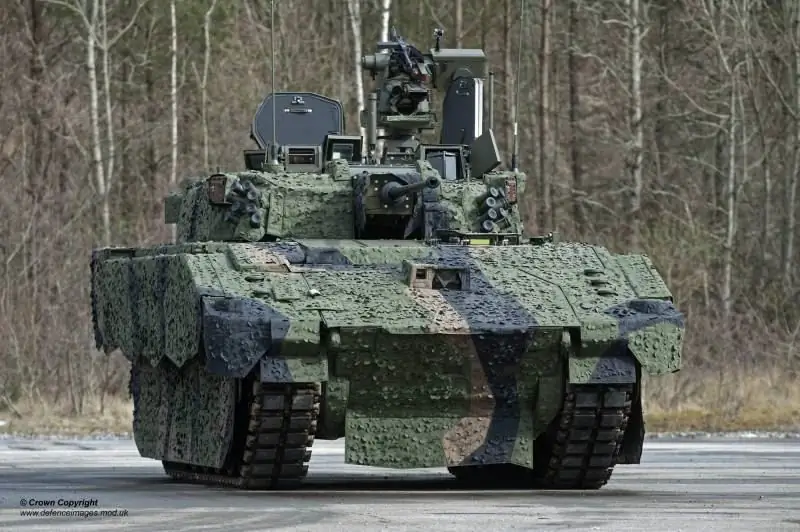
With crew firing trials slated for early 2017 and the first battalion equipped with Ajax vehicles to be formed in mid-2019, the British Army is quite close to fully meeting needs, which can be traced back to a number of programs dating back to the beginning of the 80s of the last century. Taking a closer look at the Ajax machine family
Despite its somewhat problematic past, the current Ajax family program is the newest and most advanced addition to the British Army's vehicle portfolio, which will form the backbone of the two new Army Strike Brigades announced in the Review. strategic defense and security 2015.
The roots of the Ajax program go back to the 80s of the last century, when, within the framework of a number of programs, including the promising family of light armored vehicles FFLAV (Future Family of Light Armored Vehicles), the tactical combat reconnaissance vehicle TRACER (Tactical Reconnaissance Armored Combat Equipment Requirement) and the multipurpose armored machine MRAV (Multi-Role Armored Vehicle), tried to find a replacement for the family of combat reconnaissance tracked vehicles CVR (T).
Under the FRES (Future Rapid Effects System) program, which emerged as a result of this activity, the British army expected to receive vehicles of two classes: the FRES SV (Specialist Vehicle) tracked reconnaissance "special vehicle" to replace the CVR (T); and the FRES UV (Utility Vehicle) wheeled "utility vehicle" to replace a number of legacy systems, including the Saxon armored personnel carrier, the FV432 and some CVR (T) vehicles. Like its predecessors, FRES was not free from problems and the FRES UV requirement was postponed in 2009 following the successful selection of General Dynamics UK as the first preferred applicant. It was decided that the weapons purchased in accordance with urgent operational requirements for the operation in Afghanistan, including the Ridgeback and Mastiff platforms, will currently fill the missing capabilities of the FRES UV platform. This made it possible to start this program again, and later it was announced that FRES SV would be purchased under a single SVR program (common base platform).
This version of the FRES SV program was larger than the program for the Ajax family, it was planned to purchase from 1200 to 1300 machines in 16 variants. But there were also noticeable "gaps" in it, including an anti-tank mine layer, an ATGM launcher, a ground observation vehicle (including a ground radar), a medical center and an ambulance, as well as an artillery mount with a 120-mm smooth-bore cannon. While some of these options are still being acquired through other projects, including a protected ambulance and a bridgelayer under the ABSV (Armored Battlefield Support Vehicles) program, some of the most important platforms, such as a self-propelled artillery unit and a mobile ATGM complex, and were not included in the plans to replace equipment.
Despite all these problems, the fate of the Ajax project may not have ended so rosy. Simultaneously with FRES, another American program was launched, the United States also sought to find a new combat vehicle, implementing several unsuccessful programs. The FCS (Future Combat System) program, which ran from 2003 to 2009, was a bold project to modernize the entire ground fleet of the American army, which was to be replaced by several inhabited and uninhabited platforms, including the RSV (reconnaissance and surveillance vehicle). The FCS was later heavily structured and essentially closed in April 2009. The manned ground vehicle program component was revived in a new guise of GCV (ground combat vehicle) - in a platform that, as the American army said at the time, “will be in demand across the entire spectrum of army operations and will incorporate the combat experience of Iraq and Afghanistan. . GCV was also not brought to a successful logical conclusion and, despite the fact that two developers were awarded contracts for technological samples with a total value of more than $ 889.6 million, the program was closed in 2015 in accordance with the budget request, which determined the budget reduction.
However, in addition to financial problems, other equally serious problems arose; by the time the project was canceled, its mass was estimated at 80 tons and in some configurations, in terms of physical size, it was larger than the M1 Abrams tank. In addition, a report by the Congressional Budget Office on the GCV program and possible alternatives to this new solution noted that although no alternative option met the unique requirements of the GCV, some platforms, including the German Puma BMP and the Israeli Namer, had several strengths that never did not contribute to the further advancement of plans for GCV. Although contracts were issued for the development of a promising FFV (Future Fighting Vehicle) combat vehicle - the successor to the GCV platform, a clear time frame for development and production is not currently defined; at best, the first results will appear no earlier than 2035.
After the issuance of a contract worth $ 4.3 billion to General Dynamics Land Systems UK (GDLS-UK) in September 2014 for 589 Ajax vehicles (then SCOUT Specialist Vehicle [SV]) in six variants, there was a flurry of subcontracts for subcontractors involved in the project … In this regard, it is worth mentioning the £ 130 million contract awarded to Rheinmetall for the production of turret hulls TSWM (Turret Structure and Weapons Mount); £ 125 million for Thales sighting systems and ancillary equipment, including the ORION main sight, situational awareness cameras, gunner scopes and the DNGS-T3 Stabilized Day / Night Gunnery Sight; Meggitt £ 27 million in ammunition handling systems and over £ 200 million in other contracts to allied businesses including Curtiss-Wright, Esterline, GKN Aerospace, Kent periscopes, Kongsberg, Marshall Aerospace and Defense, Over Oxley Group, Raytheon, Saab, Smiths Detection, ViaSat, Vitavox, Williams Fl, and XPI Simulation.
Preliminary tests of the Ajax and Ares variants have recently been completed, including sea trials, floating trials and live fire tests. Preliminary trials of the rest of the Ajax variants have begun, followed by extended trials. After combat firing as part of the crew, scheduled for the current year, all Ajax variants must undergo further sea trials in cold weather, testing the power plant and evaluating optical reconnaissance systems, information gathering and target designation. Serial production will begin at the General Dynamics European Land Systems Santa Barbara Sistemas plant in Spain, where the first 100 vehicles will be assembled. The remaining 489 vehicles will be assembled at the newly opened GDLS-UK assembly plant in the British city of Merthyr Tydville. This production will start operating at full capacity in the second half of 2017, and machine production will continue until 2024.
The Ajax family is based on technologies and systems developed for the Austrian Spanish Cooperation Development (ASCOD 2) infantry fighting vehicle, which itself is based on the previous version of ASCOD, which entered service in 2002.
Once fully operational, the Ajax family will consist of six main options; some of them are designed to perform several tasks at once, previously assigned to individual variants of the SCOUT SV platform.
The basic and most numerous variant of the vehicle (the total number of vehicles purchased will be 245) is the Ajax combat reconnaissance vehicle, which, for some reason, shares its name with the name of the entire family of vehicles. As a separate version of Ajax (the only option on which a new tower manufactured by Lockheed Martin UK will be installed) will perform reconnaissance and strike missions Reconnaissance and Strike (198 vehicles), Joint Fires Control fire control (23 vehicles) and Ground Based Surveillance (24 cars). The last two options (rather a sub-option) will have a smaller ammunition load for the gun, the freed up volume will be occupied by replacement equipment and additional personnel to perform specialized tasks.
The next largest option will be Athena, previously designated Protected Mobility Reconnaissance Support - Command and Control, of which 124 vehicles will be purchased. The Athena armored vehicle, based on the Ares variant, will perform operational control functions for units equipped with Ajax family vehicles. The crew of the vehicle will be five people: a commander and a driver-mechanic and three operators, a staff officer and two signalmen. In addition to a specialized set of operational control, a Watch keeper UAV control system is installed in the machine.
About 93 vehicles will be purchased in the Ares version (formerly Protected Mobility Reconnaissance Support), which will perform traditional reconnaissance tasks of the unit (34 vehicles) and an armored personnel carrier (59 vehicles). Ares, in fact, being the basic version of Ajax, performs the tasks of an armored personnel carrier without any significant modifications for additional equipment or weapons systems. The crew of the vehicle is two people plus four paratroopers, it is armed with the same remotely controlled combat module (DBM), like all Ajax platforms.
Three options will provide combat and engineering support, 51 Argus reconnaissance vehicles, 50 Apollo repair vehicles and 38 Atlas recovery vehicles; they were previously known as Protected Mobility Reconnaissance Support - Engineering Reconnaissance; Protected Mobility Reconnaissance Support - Engineering Repair; and Protected Mobility Reconnaissance Support - Engineering Recovery, respectively.
The Argus engineering reconnaissance platform allows demining units to conduct assessment, marking and other engineering work while under the protection of armor. Without leaving the car, you can measure trench ditches and slopes, mark passages and destroy explosive objects. The Apollo armored repair vehicle should work in conjunction with the Atlas variant to carry out full-fledged repair and evacuation operations. It can tow other Ajax machines as well as a dedicated highly mobile trailer used to transport components for field repairs. The crane rig can lift the power pack of an Ajax machine and also has the less common ability to pull its own power pack out of the engine compartment. Atlas is essentially the base variant of the Ajax family with standard recovery vehicle equipment installed, including two winches and an anchor anchor.
The reconnaissance and strike version of the Ajax is equipped with a two-man turret developed by Lockheed Martin UK. Many suppliers are involved in the production of turrets and weapons systems, including CTA International (CTAI), Curtiss-Wright, Esterline, Kongsberg, Meggitt, Moog, Rheinmetall, Thales and Ultra Electronics.
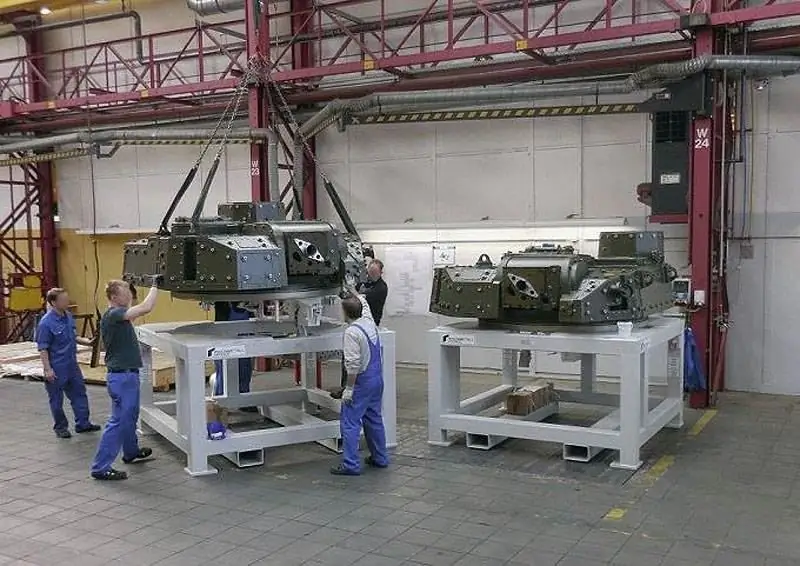
The German company Rheinmetall is responsible for the production of the basic steel turret hull, gun mount and weapon integration. The design of the turret hull, gun mount and weapon integration. The tower design is based on the Lance Modular Turret System (MTS). The STAI company is responsible for the main armament of the tower - the Case CTAS (Telescoped Armament System) 40-mm telescopic ammunition system, while the ammunition processing system is manufactured by Meggitt Defense Systems. The production of TDSS (Turret Drive Servo System) turret drives, horizontal and vertical guidance is given to Curtiss-Wright. The main cannon is supplemented by a coaxial 7.62mm Heckler & Koch L94A1 machine gun, four groups of four Thales smoke grenade launchers and a Kongsberg Protector DBM armed with a 7.62mm FN MAG machine gun.
Aiming and guidance systems include Esterline's Crew Display, Driver Display and Video Processing Unit. Thales supplies two sighting systems and a local situational awareness system. Communication between the chassis and tower systems, as well as the power supply of the tower systems, is via a Slip Ring from Moog.
The installed additional devices include internal and external communication systems; Core Infrastructure Distribution System (CIDS) backbone from Williams F1; equipment for the detection of chemical warfare agents; and a weather station.
The turret reservation system is classified, although the basic Rheinmetall structure is made of box-section steel; on top of it is installed frontal armor, consisting of spaced inclined sheets of armor steel. If necessary, additional composite / ceramic armor can be attached to the surface of these outer sheets using clamps, which further increases the level of armor. An ammunition supply system is located between the base and frontal armor in the front left of the turret. Also, between the base and frontal armor, but on the right side, there is a vertical guidance drive, a spring compensator and a liner ejection pipe. The latter ends with a spring-loaded armored cover, which is located at the top behind the launchers and is folded back to eject the cartridge case.
The armor protection of the original ASCOD turret corresponded to Level 3 in a circular manner and to Level 4 in a 60 ° frontal arc. It is worth noting that Level 3 corresponds to protection against 7.62 mm (7, 62x51 and 7, 62x54R) armor-piercing bullets with a reinforced core and a tungsten carbide core, and Level 4 corresponds to protection against the B32 14.5x114 mm armor-piercing incendiary bullet. The armor levels of the frontal projection and sides can be increased with additional panels up to Level 6 (30-mm full-caliber armor-piercing projectile or armor-piercing subcaliber and / or armor-piercing subcaliber feathered projectiles). Protection levels 3, 4 and 6 against fragmentation of 152/155 mm shells are equivalent to detonation distances of 60, 20 and 10 meters from the vehicle, respectively. The specific characteristics of the mine protection of the tower, as well as protection against IEDs (improvised explosive devices) of various types are not reported. The armor levels of the new turret, although classified, are expected to provide the same levels of protection as ASCOD or even higher in the base configuration.
It is assumed that either ERA units or elements of the so-called “non-explosive reactive armor” NERA can be added instead of or on top of the hinged armor. These modules use a combination of substances trapped between the plates within the armor module. These substances react instantly when exposed to a cumulative jet, forming an instant swelling due to a sharp increase in their own volume. This swelling throws out steel plates towards the cumulative jet, as in the case of conventional DZ elements. However, in this case, fragments of the module structure are not formed, as is the case with detonation of explosives. NERA modules provide protection against cumulative warheads, but they are not effective enough in protection against armor-piercing feathered subcaliber projectiles.
At the moment, the active protection complex (KAZ) has not been installed, although devices similar to the blocks of multispectral and radio frequency sensors of the warning system are mounted at each corner of the tower. Currently, the installation in the tower of a variant of the optical-electronic suppression complex, which is part of the MUSS (Multifunctional Self-Protection System) of Airbus Defense and Space, is being considered, but so far no decision has been made. MUSS increases the level of protection by suppressing the infrared missile guidance system, setting up an aerosol curtain and operating the KAZ. The possibility of installing KAZ on Ajax armored vehicles, as part of the MEDUSA technical assessment program, is being evaluated by QinetiQ under a contract with the British Laboratory of Defense Science and Technology, which was announced in July 2016.
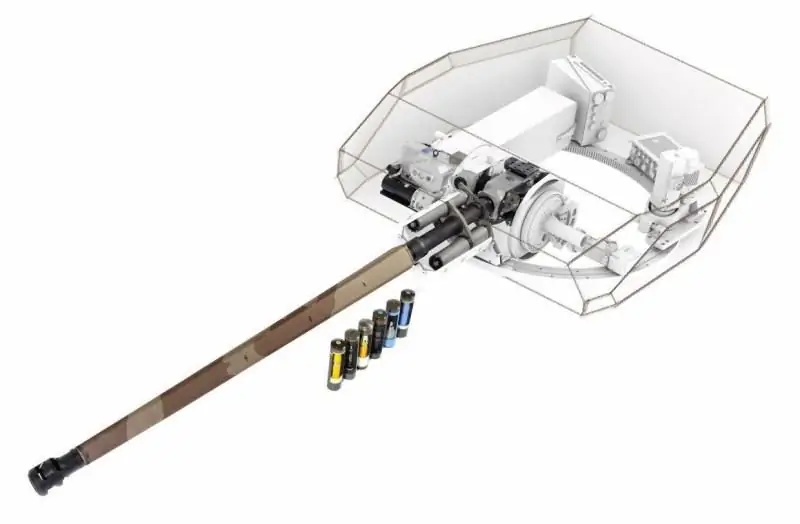
Armament
The turret of the Ajax vehicle is armed with a 40-mm CTAS automatic cannon with telescopic ammunition developed by the CTAI company. The system consists of a 40mm Cased Telescoped Cannon (40CTC), an ammunition handling system, a CTAS Controller (CTAS-C), a Gun Control Equipment (GCE) gun control equipment, a gun mount (cradle and mask) and a family of 40mm telescopic Case Telescoped Ammunition (STA) ammunition (a shot is a cylinder (body) in which a projectile is completely enclosed, surrounded by a warhead).
The development of guns capable of firing telescopic ammunition began in the early 50s, although the current 40-mm CTAS originates from work begun in France in the mid-80s and early 90s by the then GIAT Industries (now Nexter Systems). In 1994, GIAT Industries and Royal Ordnance (now BAE Systems) formed a CTAI joint venture to develop and market weapons based on the CTA ammunition family.
The first was developed by a 45 mm armament system (70x305 mm sleeve) in accordance with the previously concluded tripartite agreement (France, Great Britain, USA) on NATO standardization STANAG (Standardization Agreement) concerning the STA cannon. In 1997, with the advent of the CT2000 cannon, the 45 mm caliber was reduced to the current 40 mm (sleeve 65x225 mm), then the finished system was designated CTWS (Cased Telescoped Weapon System). Later the name of the system was changed to Cased Telescoped Cannon and Ammunition (CTSA) and finally took on its current form CTAS (Case Telescoped Armament System).
The electronically controlled 40CTS automatic cannon occupies a relatively small volume of 74 liters, is distinguished by electromechanical aiming and firing drives (induction firing mechanism), a swivel (swinging) chamber and a "push-through" direct loading system.
Dual recoil device return springs are fixed at an angle on the sides of the barrel 2, 8 meters long (70 calibers) in front of the gun cradle. The springs control the forward and backward movement of the retractable components of the gun (barrel and body) relative to the cradle rotating on the trunnions. The barrel of the current version of the gun is equipped with a heat-insulating casing.
One or more types of ammunition are housed in a linkless ammunition handling mechanism that feeds the projectiles to the "feed port" located to the right of the gun. If necessary, the type of ammunition changes in less than three seconds.
The CTAS-C electronic controller controls the azimuth and elevation angles (horizontal and vertical guidance), the operation of the ballistic computer, the sighting system, and can also program certain types of ammunition. Firing modes include single, burst and automatic fire up to 180 rounds per minute.
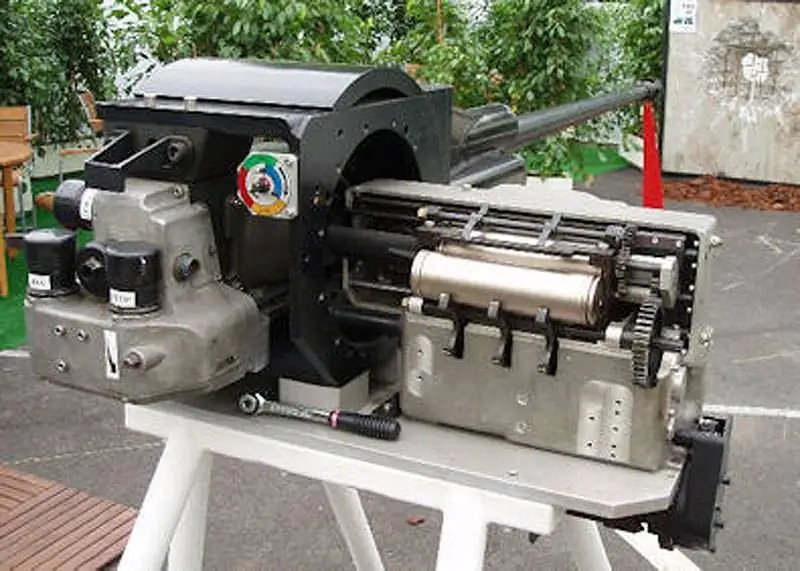
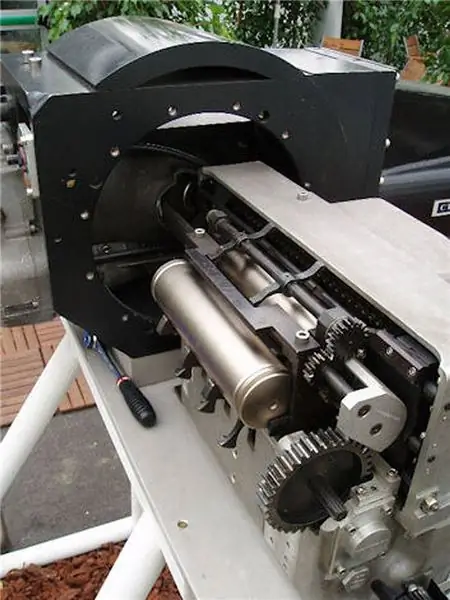
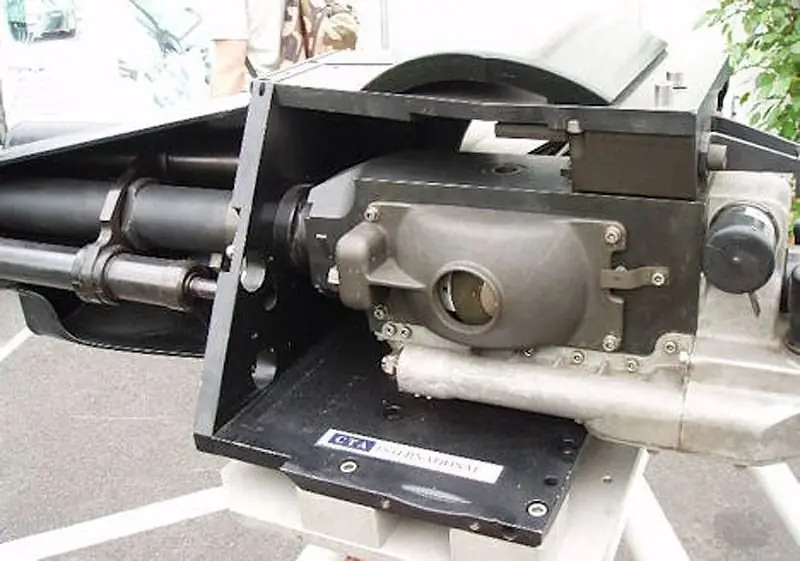
During operation and under the control of CTAS-C, projectiles of the selected type are fed from the ammunition processing system to the chamber feed window located along the axis of the trunnions at an angle of 90 ° to the axis of the bore. The chamber rotates 90 ° and aligns with the feed window and the projectile is sent to the chamber. The chamber is again rotated 90 °, and thus locked, aligned with the axis of the barrel, a shot is fired and the spent cartridge case is ejected. Recoil forces (peak 110 kN) force the recoil parts weighing 230 kg to move back by 42 mm, their movement is decelerated and then they return to their place with the double springs of the recoil device. The chamber then turns again through 90 ° and a new projectile is fed into the chamber, the spent cartridge case is pushed out of the chamber due to the filing of a new shot. The process repeats at the speed set by the CTAS-C controller.
The shape of the shots of the CTA family (40x255 mm) simplifies the feeding of ammunition, shortens the time for feeding and loading them, and also makes them more convenient for storage compared to the traditional design. Although they are similar in performance, maximum diameter and weight to the traditional 40x365R projectile for the 40/70 Bofors cannon, they are more than half the length, approximately 235 mm versus the 535 mm Bofors projectile.