Armored combat vehicles of a number of classes combine a relatively low combat mass and a sufficiently high level of protection. This combination of characteristics can be obtained due to several basic technical solutions. Depending on customer requirements and capabilities, designers sacrifice the level of protection or use new materials and technologies. Over the past decades, domestic and world industry has accumulated solid experience in the creation of well-protected, but light military equipment.
Historically, the very first way to reduce mass (for example, in line with the characteristics of the available chassis) was to reduce the thickness of the armor with a corresponding drop in the level of protection. The development of new steel alloys with higher characteristics was also carried out. Later, the search began for other metals and non-metallic materials that combine strength and low weight. Finally, from a certain time in the field of light armored vehicles, combined and spaced armor, previously used only on heavy vehicles, have been used. In addition, one should not forget about the possibility of installing dynamic or active protection, complementing the body's own armor.
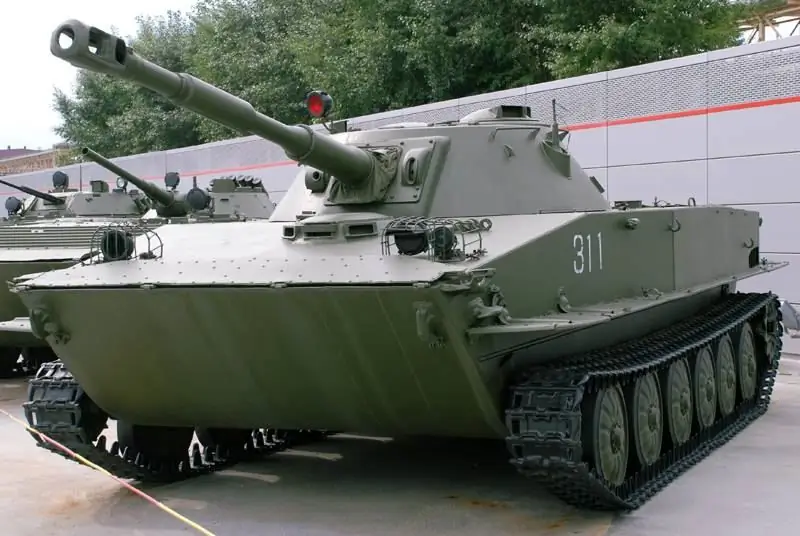
Floating tank PT-76. Photo Russianarmy.ru
Steel and floating
As the first example of a post-war domestic light armored combat vehicle, the PT-76 amphibious tank can be considered. It was created in the late forties in accordance with a special technical assignment. This machine was supposed to have bulletproof protection and float well, which made special demands on the design as a whole. The assigned tasks were successfully solved, although by today's standards the resulting tank was not distinguished by high perfection or outstanding protection characteristics.
The new type of amphibious tank received an oversized welded armored hull, designed to provide adequate buoyancy. The material of the body was armored steel of the "2P" brand. The frontal protection of the vehicle consisted of sheets with a thickness of 11 and 14 mm, the sides and stern were 14 and 7 mm thick, respectively. From above, the car was protected by a 5-mm roof, from below - by a 7 mm thick bottom. The turret armor was 8 to 17 mm thick.
The hull of the PT-76 tank had a length of 6, 91 m and a width of about 3 m. In the course of further modernization, the hull was refined, but its main features did not change. The combat weight of the amphibious tank was 14 tons - a little less than half accounted for the armored hull and turret.
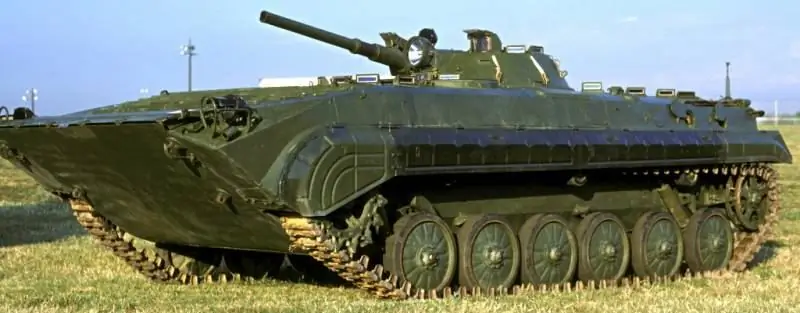
Infantry fighting vehicle BMP-1. Photo Wikimedia Commons
Armor thickness up to 14-17 mm, including those installed with an inclination of up to 80 °, had limited strength, and therefore the PT-76 had limited protection characteristics. The steel armor of this vehicle was guaranteed to withstand the hit of small arms bullets and shrapnel from all angles. The reinforced frontal projection could also withstand shelling from large-caliber systems and even small-caliber guns. At the same time, any tank or anti-tank gun of the late forties is guaranteed to hit the PT-76 at all effective ranges. A similar situation was with the recently appeared anti-tank grenade launchers.
The PT-76 amphibious tank met the requirements, but over time it managed to become obsolete. One of the reasons for this was the low perfection of the armor protection design. Already at the beginning of the sixties, a project was developed for a deep modernization of the reservation, which provided for the replacement of the main body material. In 1961, VNII-100 manufactured an experimental PT-76 hull using D20 aluminum alloy. Full-scale tests have shown that with a similar level of protection, such a hull is significantly lighter than a steel one. Such a hull did not go into production, but showed the potential of aluminum armor. Later, these ideas were applied in new projects.
Steel and aluminum
The next example of a successful design lightening can be the Soviet BMP-1 and BMP-2 infantry fighting vehicles. The first of them was developed at GSKB-2 of the Chelyabinsk Tractor Plant at the turn of the fifties and sixties in accordance with the new technical specifications and taking into account the available technologies. As a result, a very curious design was created, which included uncharacteristic elements. To obtain the optimal combination of weight and protection, it was proposed to combine steel and aluminum.
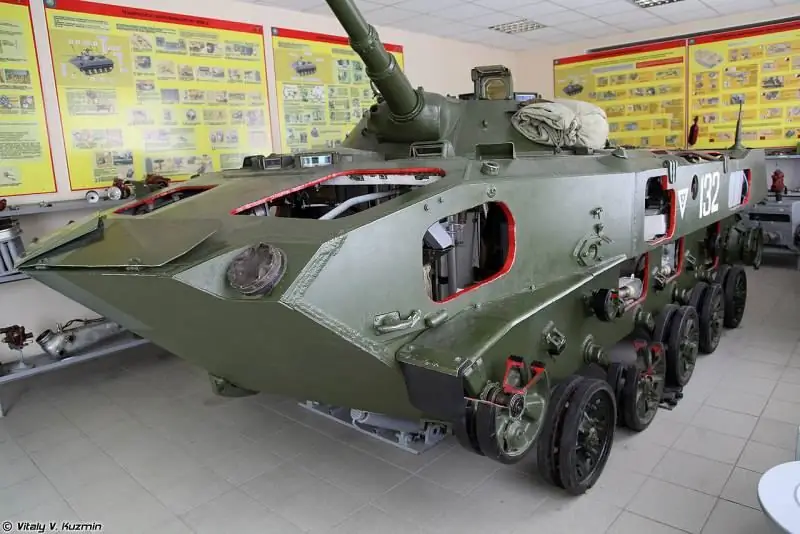
Training layout of BMD-1. The windows in the building allow you to evaluate the reservation. Photo Vitalykuzmin.net
The basis of the welded hull for the BMP-1 was again rolled steel sheets of high hardness. The forehead of the steel armored hull had a thickness of 7 mm (upper part with an inclination of 80 °) to 19 mm (lower). The sides were made from 16 and 18 mm sheets. The feed had similar protection parameters. The greatest thickness of the turret parts reached 33 mm. An interesting feature of the new car is an additional cover over the engine compartment. To protect against shelling and external influences, a large cover with characteristic transverse ribs appeared on the upper frontal sheet. It was made of an ACM-aluminum alloy with additions of zinc and magnesium.
The length of the BMP-1 hull exceeded 6, 73 m, the width - about 2, 9 m. The combat weight of the vehicle was determined at 12, 7-13 tons. The welded steel hull, without parts and assemblies installed on it, weighed a little more than 3870 kg. Steel tower - only 356 kg. The assembled frontal cover plate made of ACM had a mass of about 105 kg.
As the customer demanded, the BMP-1 could withstand the shelling of 7.62 mm armor-piercing bullets from all angles. Also, all booking sheets held up small and light fragments. Frontal projection protected from heavy machine guns at zero range. The shells of foreign cannons of 20 mm caliber could not hit the vehicle head-on from a distance of more than 100 m. For 23-mm systems, the maximum range was 500 m. At the same time, like any other light armored vehicle, the BMP-1 had no real protection against tank shells and anti-tank grenades.
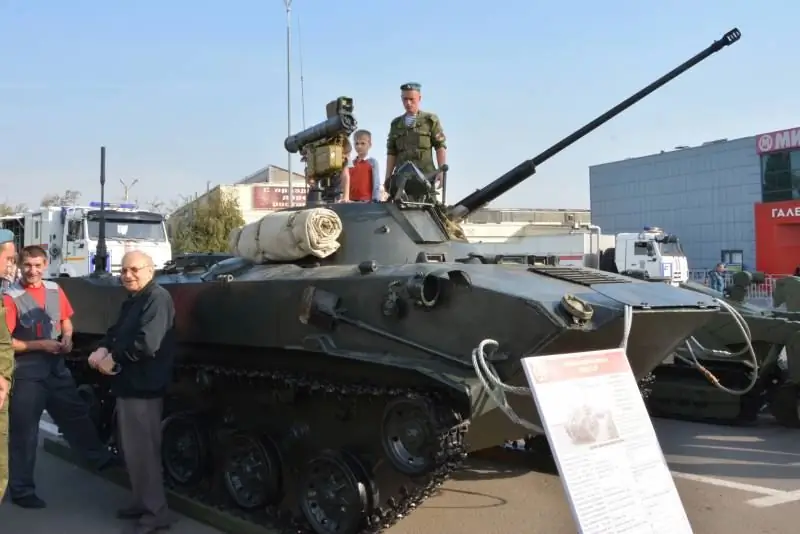
BMD-2K airborne combat vehicle. Photo by the author
A particularly high level of protection was not required from the BMP-1, and the necessary characteristics were obtained through a successful combination of already mastered and new materials. In fact, this infantry fighting vehicle can be considered the first large-scale domestic model, in the design of which aluminum booking was used. However, such a "record" did not last too long, and soon an even more interesting armored vehicle appeared.
Aluminum BMD
After the experiment with the aluminum body for the PT-76, Soviet scientists continued to work on finding the best options for lightweight protection and materials for it. By the mid-sixties, a new alloy of aluminum, magnesium and zinc was created under the designations ABT-101 and 1901. This alloy was considered as the basis for bulletproof armor of light combat vehicles. Soon, on its basis, the ABT-102/1903 alloy was created, which differed in a different viscosity, and thanks to this, it could provide protection against artillery shells.
In 1965, the Volgograd Tractor Plant brought the BMD-1 prototype airborne assault vehicles for testing. When developing them, the main task was to reduce the size and weight to values corresponding to the capabilities of military transport aircraft. It was possible to reduce the weight by using aluminum armor such as ABT-101 and some other light alloys. However, it was not possible to completely get rid of the relatively heavy steel. Some parts were still made from it.
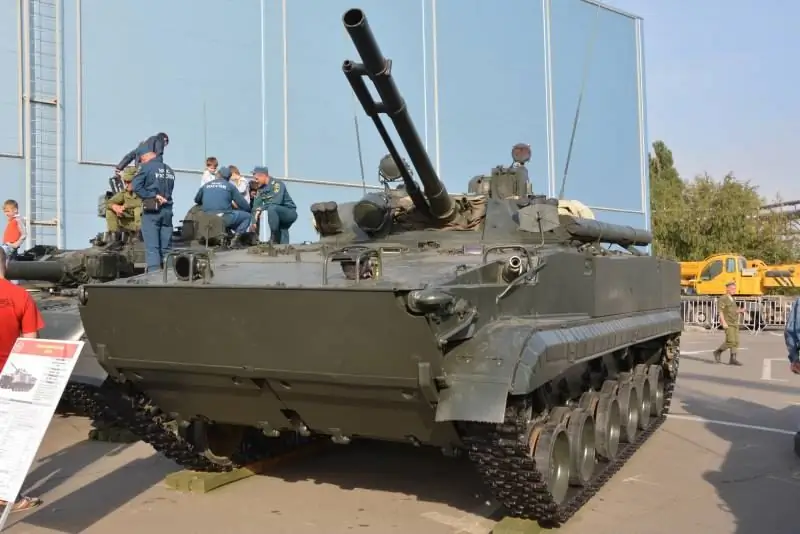
BMP-3 infantry fighting vehicle. Photo by the author
The frontal protection of the BMD-1 included several aluminum sheets placed at different angles to the horizontal and longitudinal axis of the vehicle. This design made it possible to further increase the reduced armor thickness. The upper parts of the forehead were 10 mm thick, the middle ones were 32 mm thick, and the lower ones were 10 mm thick. The hull side was assembled from sheets with a thickness of 20 and 23 mm. The feed consisted of parts 15-20 mm thick. The tower was made of steel, the maximum thickness of its protection was 22 mm.
The BMD-1 hull had a length of only 5.4 m with a width of just over 2.5 m. The combat weight of the entire vehicle was determined at 7.2 tons. front hemisphere. All-round protection against 7, 62-mm armor-piercing bullets was also required. Thus, the level of protection of the BMD-1 to some extent repeated the characteristics of the BMP-1. The landing vehicle was inferior to the infantry vehicle only in terms of the strength of its frontal armor. At the same time, the more compact body made of ABT-101 alloy was about half the weight of the steel one used on the BMP-1.
Later, a new airborne combat vehicle with a different fighting compartment and weapons was created on the BMD-1 chassis. At the same time, the aluminum case did not undergo major changes - in fact, the BMD-2 differed from its predecessor only in weapons and some internal devices. In the mid-eighties, a completely new machine BMD-3, created on the basis of different ideas and solutions, went into series. Nevertheless, modern aluminum armor was widely used in this project.
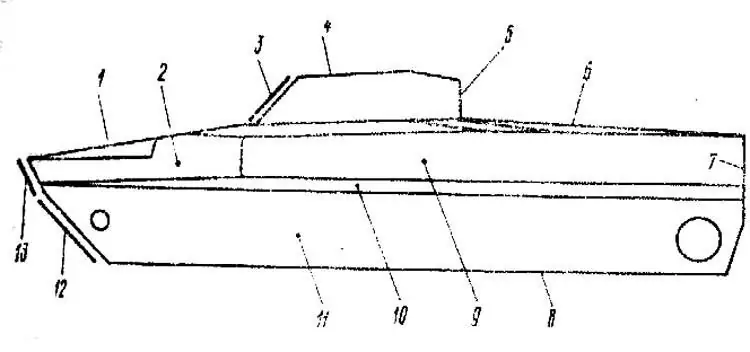
Armor protection BMP-3. 1 - upper frontal part (18 mm ABT-102); 2 - zygomatic leaf (60 mm ABT-102); 3 - frontal projection of the tower (16 mm BT-70SH + 70 mm air gap + 50 mm ABT-102); 4 - tower roof (18 mm ABT-102); 5 - aft part of the tower (43 mm ABT-102); 6 - roof (15 mm ABT-102); 7 - feed (13 mm ABT-102); 8 - bottom (10 mm AMG-6); 9 - board (43 mm ABT-102) 10 - niche sheet (15 mm ABT-102): 11 - bottom board (43 mm ABT-102); 12 - lower frontal part (10 mm BT-70SH + 70 mm air gap + 60 mm ABT-102); 13 - middle frontal part (10 mm BT-70Sh + 70 mm air gap + 12 mm BT-70Sh + 60 mm ABT-102). Figure Btvt.nador.ru
Aluminum and steel for infantry
In the eighties, in parallel with the promising BMD-3, a new BMP-3 infantry fighting vehicle was created. When creating it, the Kurgan Special Design Bureau of Mechanical Engineering took into account the need to increase the level of protection in connection with the development of weapons for light armored vehicles of a potential enemy. It was necessary to provide protection against 30-mm shells, but at the same time to prevent an unacceptable increase in mass. The solution to such problems was directly related to the application of the new booking.
BMP-3 received spaced armor, built on the basis of aluminum parts made of ABT-102 alloy and BT-70Sh armor steel. The upper frontal and zygomatic parts of the body are made of aluminum and have a thickness of 18 and 60 mm, respectively. The slightly forward-tilted middle front includes 10mm steel, 70mm air gap, 12mm steel, and 60mm aluminum. The lower part has a similar structure, but dispenses with the inner steel sheet. The sides are assembled from ABT-102 sheets with a thickness of 15 and 43 mm. The roof, stern and bottom are 15, 13 and 10 mm thick, respectively. The turret forehead received protection in the form of 16 mm steel, 70 mm air and 50 mm aluminum. An additional protection of the frontal projection is a wave-reflecting shield made of armor steel of small thickness.
The spaced and homogeneous armor of the BMP-3 provides all-aspect protection against large-caliber small arms. The frontal projection withstands shelling from a 30-mm cannon from a range of 200 m. At one time, various attachments were also offered to increase the level of protection. Overhead panels were intended to improve ballistic protection, and special explosive reactive armor helped to withstand shelling from an anti-tank grenade launcher.
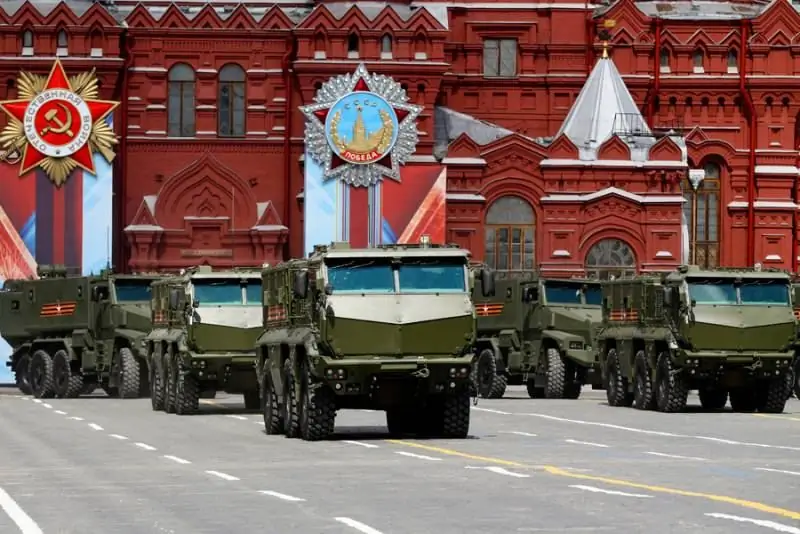
Typhoon-K armored cars in the parade line. Photo by the Ministry of Defense of the Russian Federation / mil.ru
The BMP-3 hull has a length of 7, 14 m and a width of about 3.3 m. The combat weight of the vehicle as a whole is 18, 7 tons. At the same time, the mass of an armored hull made of steel and aluminum does not exceed 3.5 tons. According to known data, the use of the ABT-102 alloy provided a reduction in body weight by almost a third in comparison with a steel unit with the same level of protection. In addition, the comparatively thick aluminum sheets allowed a rigid body to be assembled without separate structural elements, resulting in additional weight savings.
Steel and ceramics
Further development of means of protection leads to new variants of armored vehicles, characterized by a fairly high resistance to the main threats. Domestic cars of the Typhoon-K family, created by the KamAZ enterprise in recent years, can be considered a good example of this. In several projects of this line, it was possible to obtain very remarkable results in the field of protection.
The armored hulls of the Typhoon-K vehicles receive combined protection. A comparatively thin outer metal sheet is used, under which is placed ceramic tiles with specified characteristics. The lower layer of armor is a thicker steel sheet. When hitting such a package, a bullet or shrapnel pierces the outer layer, spending part of the energy, and ceramics inhibits it. In addition, steel and ceramics have different parameters of strength and hardness, which provokes the destruction of the damaging element. Bullet and ceramic fragments are held in place by an inner steel sheet.
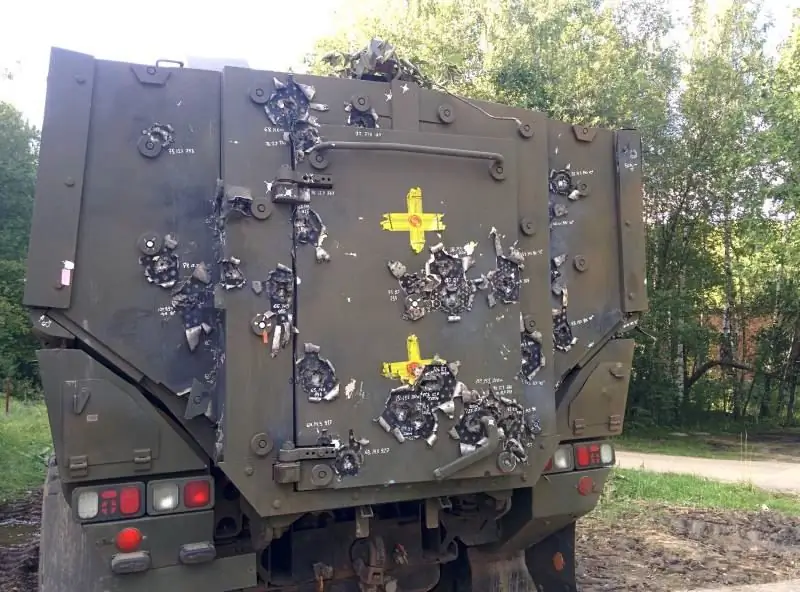
The feed of the KamAZ-63969 armored car after shelling tests. Photo by OJSC "KamAZ" / Twower.livejournal.com
One of the first was the so-called. corps armored car KamAZ-63969. Its combined armor could withstand shelling from 14.5mm weapons. There was also a variant with less powerful armor that protects against 12.7 mm bullets. This version of the armored car coped with all the tests, but did not interest the customer. A sample called "Typhoon K-63968" went into the series, which differed in the layout and characteristics of the reservation. However, the architecture of the protection remains the same and provides for the use of ceramic tiles.
The serial "Typhoon-K" has a hull with a length of slightly less than 9 m and a width of about 2.5 m. The total weight of the vehicle with a load of up to 2.6 tons exceeds 24.7 tons. It is possible to tow a trailer weighing up to 8 tons. The manufacturer does not specify the weight of the enclosure itself.
Another variant of combined armoring using ceramic materials is implemented in the Typhoon K-53949 project, also known as Typhoon 4x4 and Typhoonok. In this case, the ceramic plates are placed between the sheets of aluminum armor. This protection corresponds to level 3 of the STANAG 4569 standard and can withstand 7.62 mm armor-piercing rifle bullets.
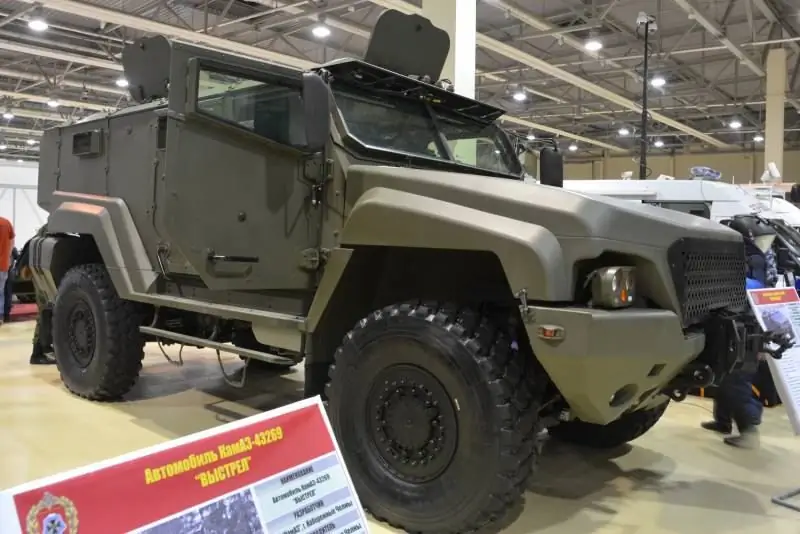
Armored car "Typhoon K-53949" with light armoring. Photo by the author
Typhoon 4x4 received a bonneted body with a total length of less than 6.5 m and a width of about 2.5 m. The curb weight of such a car is 12 tons, with another 2 tons for the payload. As in the case of the larger sample, the developers are in no hurry to specify the mass of the body itself and its protection, which does not allow us to fully assess the weight perfection of the design.
***
In the distant past, armored vehicle designers faced a serious problem in the form of a direct relationship between the level of protection and weight. Armored vehicles with steel hulls could show high resistance to damaging elements only with an appropriate weight. However, later, the development of metallurgy and the emergence of new alloys made it possible to solve these problems, thanks to which a significant number of combat vehicles appeared in our country and abroad, combining low weight and good protection.
The first solution to the problem of mass and protection was aluminum alloys, which could be used both independently and in combination with other materials or even with additional hinged armor. Then new ceramics appeared, also suitable for creating combined protection. The development of metals and ceramic materials continues and leads to the emergence of new options for protection.
It is easy to see that attempts to reduce the mass of the car while receiving good protection led to serious results by the mid-sixties. The aluminum and steel armor of the BMP-1, and after it the BMP-2, could protect the crew from small-caliber artillery shells. In the subsequent BMP-3 project, the combination of different materials and the presence of an air gap made it possible to once again improve protection. Currently, such developments are being developed and lead to new remarkable results.
The post-war development of materials science, which led to the emergence of new alloys and non-metallic materials, gave a serious impetus to the development of armored combat vehicles of various classes. Engineers were able to improve the protection characteristics of their vehicles without significantly increasing their weight. The resulting equipment is still in service with many countries, and all new projects are created taking into account the existing experience. At the same time, it should be expected that in the distant future, fundamentally new materials will appear that will again improve the characteristics of armored vehicles, and the processes of recent decades will be repeated.