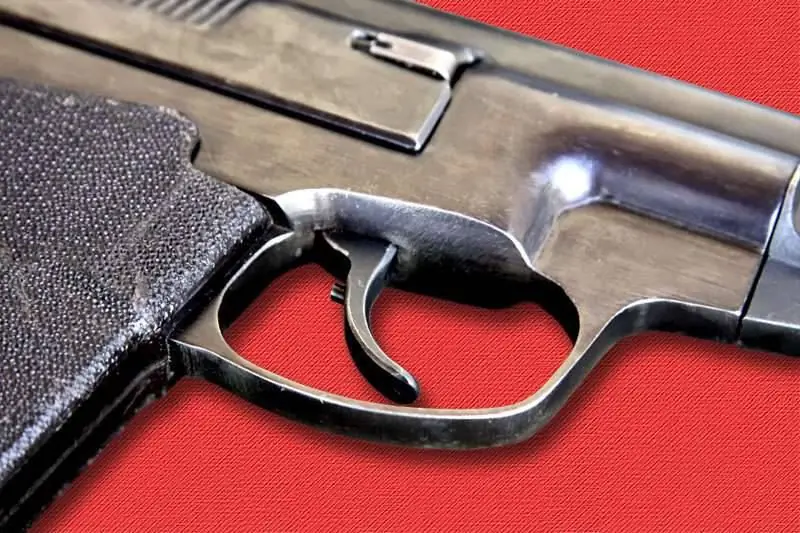
Among the large number of existing types of small arms, special-purpose models and, especially, silent firearms, are of great interest both for their uniqueness and the history of development. Including because the very fact of existence, the details and technical characteristics of such weapons became known only relatively recently to both amateurs and specialists. The unified and integrated system of “weapons with reduced unmasking factors” created by Russian designers created a real sensation in the early 90s of the twentieth century, when information about it became available to the general public. The system includes a pistol, sniper, machine gun and grenade launcher systems, consisting of special weapons and no less special ammunition. The fact that our system is still the best and has no analogues in the world was not written only by the lazy …
One of the representatives of this series, the pistol complex, will be discussed in this article. PSS is still the only self-loading pistol in the world chambered for a special cartridge with a powder gas cut-off in the sleeve. Moreover - regular, that is, officially accepted into service. From which it follows that it fully meets all the requirements for reliability and meets all the other strict requirements for military weapons.
Is it really difficult to repeat such a construction, or is such a complex “not very necessary”, or is it “not very good”, or are there any other reasons why he is left alone? Let's figure this out. But, for a general understanding and greater validity, we will also consider the background of the issue, paying attention, first of all, to attempts to create a self-loading silent weapon.
At the beginning, it is worth noting that in many popular science articles, the son of the inventor of the Maxim machine gun, Hiram Percy Maxim (1869 - 1936), is called the ancestor of the systems for jamming the sound of a shot. However, its product became popular and enjoyed commercial success only in 1909, and the first patent for an expansion-type multi-chamber silencer was received in 1899 by the Danes J. Boerrensen and S. Siegbjørnsen. It is also interesting that hunters were the first to use such silencers so that a miss would not frighten the game, and at the beginning of the 20th century, silencers for hunting carbines were freely sold to everyone. When silent weapons caught the attention of criminals, the sale of such devices was limited.
However, the designs of the mufflers of that time, their dimensions and, accordingly, the really achievable results did not quite suit the military, who also turned their attention to them for use by reconnaissance and all kinds of special units and groups, for which the unmasking of the shooter and the very fact of the shot were undesirable, to put it mildly … Therefore, the search for other constructive solutions continued.
An alternative to expansion-type silencers and a more effective idea in the field of silent firing is a way to eliminate the sound of a shot by "cutting off" the powder gases, leaving (locking) them in the barrel or other closed volume, preventing them from going out and precisely by this eliminating one of the main sources of sound shot. Among our compatriots, the pioneers in this area are the brothers V. G. and I. G. Mitin, who in 1929 filed an application and received a patent for "A revolver for silent firing with the use of a leading bullet and a pallet with an increased diameter remaining in the barrel bore."
According to the authors' idea, the revolver was supposed to have two drums - one combat, in the usual place, and the second additional, located coaxially with the first at the muzzle of the weapon. Both drums are fixed on a common axis and synchronized in their rotation. The cartridges, as usual, are loaded into the combat drum. At the same time, in the cartridge case, behind the bullet, there is a special pushing pallet. There are sockets in the muzzle drum and each such socket consists of a bullet-through hole and a pallet "socket". When fired, a bullet pushed by the pallet under the action of powder gases moves along the barrel, freely passes through the bullet-through hole and flies to the target. And the pallet, having a slightly larger diameter than the bullet, slows down and gets stuck in the “pallet socket” of the muzzle drum. The presence of special gaskets-seals eliminates the possibility of a breakthrough of the powder gases outward through the gaps, including between the movable drums and the fixed barrel … As a result, the powder gases are "cut off" and remain inside the weapon, in a closed volume, a three-piece "chamber" - in the sleeve (in the combat drum), in the barrel and in the muzzle drum. At the next cocking of the hammer, the combat and muzzle drums are synchronously rotated by a step of one socket. At this moment, most likely, the residual pressure of gases from all three "chambers" should have been released, after which the above-mentioned miraculous seals should again ensure the tightness of all three chambers as a whole. At the end of the shooting, it was required to knock out spent cartridges from the combat drum, as well as “spent” pallets from the muzzle. How protection from a shot was ensured when the pan was not removed from the muzzle drum is not completely clear.
Obviously, the design of the silent revolver, proposed in 1929 by the Mitin brothers, was complex and not devoid of many shortcomings. Judging by the data available today, it did not come to the production of prototypes of such a revolver. But this invention can be considered not only the beginning of domestic systems with a cutoff of powder gases, but also the first, albeit theoretical, attempt to create a silent pistol complex. Which would have, in addition to special, also the usual properties - multiple charges, "revolver" shooting, the ability to reload and reuse weapons.
The next interesting stage was the work that arose and was carried out on the basis of the idea and initiative of the Tula gunsmith designer from TsKB-14 - Igor Yakovlevich Stechkin. He proposed an improved version of the implementation of the idea of the Mitin brothers, while simultaneously solving one of the obvious problems of their design - the need to manually remove "spent" trays from the muzzle drum. In Stechkin's design, the pallet pushing the bullet almost also "gets stuck" in the pallet of the socket, but made at the end of the chamber in the form of a cone. And it is removed from it with the next shot - the next bullet "puts on" the pallet as a second shell, picks it up and, re-crimping with it already in the rifled part of the barrel, they leave the barrel as a whole. The pallet-cap pushing the next bullet is braked in a cone ("pallet socket") and provides a cutoff of the powder gases of the next shot.
The experiments carried out in Tula by the author himself and their first results interested the Customers and became the reason for staging in 1953 the research work "Study of the possibility of creating a pistol and a special-purpose cartridge for it" jointly by NII-61 (now TsNIITOCHMASH, Klimovsk) and TsKB- 14 (now - KBP, Tula). Yelizarov Nikolai Mikhailovich was appointed the scientific supervisor of this work, the engineer Gubel Iraida Semyonovna was the responsible executor.
For experimental shooting of TsKB-14, a mock-up of a pistol was developed and manufactured, intended for firing single shots. It was a simplified barrel group, but with all the functionally significant structural elements to implement the general idea. The barrel on the inner surface consisted of a chamber for a 9-mm pistol sleeve, a smooth-walled cylinder with a diameter of 9.0 mm. (and not a cone, as some sources mistakenly indicate), a front threaded part with a diameter of 7, 62 mm along the margins (occupying about 1/3 of the barrel length) and a smooth connecting cone between them with an inclination angle of 20 °. On both sides of the connecting cone, several vent holes were drilled in the walls of the barrel and chamber, connecting them to two expansion chambers.
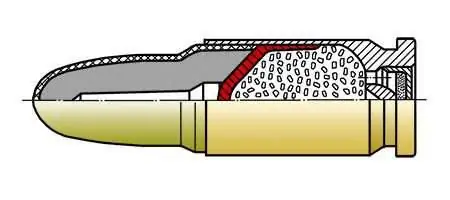
Schematic representation of the SP-1 cartridge
The bullet of the cartridge had a stepped shape, 9, 25/8, 00-mm and in the process of firing it was re-crimped twice. Leaving the bore, she had a total weight of 8, 95 grams and an initial speed of 120-140 m / s. Initially, according to the design proposed by TsKB-14, the bullet was supposed to have 4 deep longitudinal grooves ("grooves") on the front part, obviously, in the hope of a better connection between the cap and the bullet in the process of their joint re-compression in the connecting cone and in the rifled part of the barrel. But in the process of working out the design of the bullet and the methods of its manufacture at NII-61, it turned out that such grooves do not affect the general functioning of the shot, and also cause the high complexity of manufacturing a bullet with a shell in the shape of a clover leaf (including for breaking through the thin walls of the shell during its manufacture). The overall design of the bullet and pallet was refined and modified, the grooves were eliminated. But the general meaning of the author's idea remained unchanged.
It is customary to call this design "SP-1", as if emphasizing that it was the first actually tested and investigated design. The work on the SP-1 is described in detail in the third book "Modern domestic cartridges, how the legends were created" of the four-volume monograph by V. N. Dvoryaninov "Small arms combat cartridges", which shows the drawings of an experimental cartridge and ballistic weapons, the history of their development, technical characteristics of the system and a detailed description of its functioning.

As a result of the research, as is often the case, two main results were obtained - positive and negative.
A positive result was the fact that the stability and degree of muffling of the sound of a shot due to cutting off the powder gases by the pushing pan met the requirements and, simply put, pleased. In the process of this particular work, domestic cartridge-makers first investigated how the pallet works when firing and braking. Including at its various speeds, thickness, shape, size, and so on. This first and invaluable experience was of great use to them in the future.
A negative result was the obviousness that the proposed design, despite its fundamental performance, could not be considered as the basis of a combat, actually operating weapon. In addition to the discrepancy between the TTT in accuracy, penetration, as well as the identified problems with a large and unstable loss of bullet velocity in the process of its "connection" with the pan and their joint passage along the grooves, as well as insufficient obturation by the walls of the case of powder gases and other "trifles", there was the main problem is revealed - the extremely high sensitivity of the structure to small changes in the weight of the powder charge of the cartridge, that is, to the energy of the shot.
So, for example, when the gunpowder was loaded at 0, 16 - 0, 18 g, 30% of the bullets got stuck in the rifled part of the barrel, and when the weight of the charge increased to 0, 24 g, 100% of the caps flew out of the barrel without braking in the transition cone and giving sonorous shots. And this is under ideal conditions of shooting from the same ballistic weapon! That is, serious problems were inevitable under difficult operating conditions and different temperature conditions, in accordance with typical domestic requirements for reliability. Plus, ensuring the stable performance of the system in the manufacture of its components in real production, taking into account the inevitable tolerances for the accuracy of manufacturing both cartridges and weapons.
That is why, seeing and objectively assessing the current results, in 1954 I. Ya. Stechkin proposed to improve the design. Namely - to brake the pushing pallet at the level of the cut end of the cartridge case, as if transferring the brake cone there from the chamber of the weapon. More precisely, using the muzzle of the sleeve as such a cone. As a result, the cutting off of the powder gases now had to be carried out in the sleeve, at the end of which the spent pallet was stuck. And the removal of the pallet from the weapon would occur along with the removal of the spent cartridge case. So work began on the SP-2 cartridge, which became the first domestic silent cartridge with a cutoff of powder gases in the sleeve.
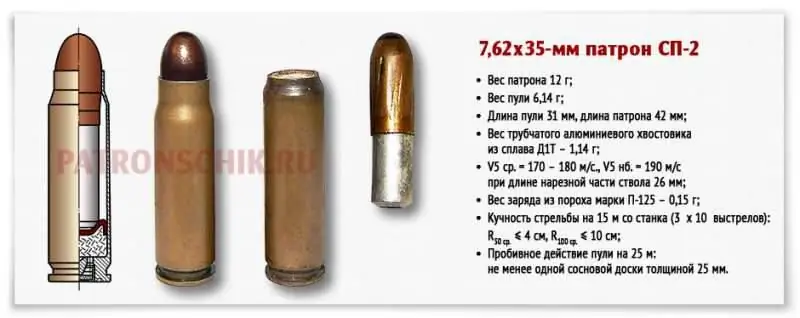
As a result, the SP-2 cartridge was put into service in 1956 together with the original weapon - the scout shooting knife (LRS), developed by the designers of the Tula Arms Plant, which combined the traditional edged weapon and a single-shot firing device located in the knife handle. Much later, in 1962-65, they also developed a 7, 62-mm double-barreled non-automatic pistol MSP ("Small-sized special pistol"). Both samples later used the SP-3 cartridge, the size of which in the case and chamber was identical to the SP-2 cartridge. Stechkin I. Ya. designed his TKB-506A firing device, externally made in the form of a cigarette case. Three SP-2 cartridges were loaded into it and reloaded manually, for each of them inside the "cigarette case" had its own barrel group and percussion mechanism. The design and details of the development of the SP-2 are also given in the third book of the monograph by V. N. Dvoryaninov "Live cartridges of small arms".
Analyzing the development of SP-1 and SP-2 cartridges, it is necessary to note some fundamental points that are important both for a general understanding of the further development of domestic "silent" ammunition and weapons, and for historical justice.
When comparing the configuration of the SP-2 cartridge case before and after the shot, as can be clearly seen in the photograph, it is noticeable that the muzzle of the cartridge case “disappears”. This is the result of dynamic braking of the pallet. In the process, plastic deformation of the sleeve barrel and, in part, of the pallet itself occurs. Having used up its kinetic energy in this way, the pallet gets stuck in the cut of the sleeve of the sleeve, cutting off and clogging the powder gases in the body of the sleeve, which is the main idea inherent in the design of the cartridge. Obviously, this process cannot be called simple in any way, especially since it is required to ensure its 100% stability both in different operating conditions and in the industrial production of all elements of the cartridge. Needless to say, domestic cartridge-makers faced a whole bunch of design and technological problems in this regard, but it was by working out the SP-2 that they found ways to solve them. The strength of the stamped pallet and the strength of the liner and the stable ballistic characteristics of the shot were ensured.
In the process of working out the cartridge, they faced the problem of bullet stability in flight. In search of a solution, the dimensions of the bore were refined by rifling fields and the traditional 4-rifled barrel with a 240 mm rifling pitch was replaced by a 6-rifled barrel with a steeper 160 mm pitch. This made it possible to fundamentally reduce the number of oval holes and had a positive effect on the accuracy of fire. This is the main reason for the use of a non-standard barrel for this and subsequent domestic ammunition of this type.
I also had to face the effect of a sheaf of sparks that accompanied the shot and was unacceptable as a serious unmasking factor. Some sources erroneously indicate that this is caused by the breakthrough of propellant gases when the pallet moves in the liner. However, as a result of research during the development of the SP-2, it turned out that the main reason is the movement of the bullet along the bore and the state of wear of the bore. To eliminate this effect, I also had to find my own little know-how. As well as for many other structural elements and their manufacturing technology.
Carefully examining the design of the ballistic weapon for the SP-1 cartridge, we note that at the beginning of the rifled part of the barrel, immediately after the brake cone for the cap pan, a number of bypass holes were made. Which, as indicated, also served "to eliminate the vacuum formed (with good obturation of the cap) between the cap and the bullet as it moves forward along the bore." This is an effect well known to anyone who has disassembled a bicycle pump. When removing a well-fitting piston from the pump housing, if you tightly close the hole for the hose with your finger, you feel its serious resistance to removal, and when the piston comes out of the housing, there is a clap. Such a development of events was feared by the author of the general idea I. Ya. Stechkin, introducing the above-mentioned bypass holes into the design. This assumption, true only deeply theoretically, was later repeated several times in the domestic history of the development of ammunition with the cutoff of powder gases and weapons for it. And also it is still present in almost all popular publications on this topic. The fact is that in practice it is not possible to ensure the absolute absence of a breakthrough of powder gases when the pallet moves between it and the walls of the sleeve. In addition, the bullet, re-crimping, cuts the shell into the rifling as it moves along the barrel, also not uniformly and does not "overlap" it like a pump piston. There are always gaps, which is why there is no need to talk about the formation of a vacuum behind the bullet.
Finishing the prehistory of the development of ammunition with a cutoff of powder gases in the sleeve, it remains to clarify some general points. There is no doubt about the talent and ingenuity of our designers. They were and will remain the first who managed to implement this in practice, bringing the general theoretical idea to the adoption of a live cartridge for service and its introduction into mass production. Therefore, the history of the beginning of the creation of this class of domestic ammunition and weapons does not need additional decoration and description of false victories or merits. The initiative and general design ideas came, undoubtedly, from TsKB-14 and I. Ya. Stechkin, who himself tested the first options. But the development of the design of the SP-2 cartridge and its development were carried out in full at NII-61 by Nikolai Mikhailovich Elizarov and Iraida Semyonovna Gubel.
It is also worth noting that the very idea of cutting off the powder gases was not first put forward by either the Mitin brothers or Igor Yakovlevich. Known, for example, US patents No. 1, 416, 827 and No. 1, 416, 828 issued on May 23, 1922 in the name of Bradford Holmes (Bradford B. Holmes, New York, NY, USA). In the description of the latter, the author pointed out that his "invention is intended for silent, flameless and smokeless firing from pistols, automatic rifles, machine guns and, in general, whenever fast [automatic] shooting is necessary."
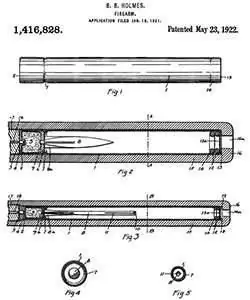
The cartridge was supposed to be a barrel sleeve, which housed a primer, a powder charge and a sub-caliber feathered bullet, which was set in motion by a bowl-shaped piston, as well as an "automatic braking muzzle device for slowing and stopping the piston in the muzzle, but allowing the bullet to exit." The deceleration of the pallet was to be provided due to the deformation of the shock-absorbing rings located at the end of the bullet acceleration, in the muzzle of the sleeve. When braking the pallet, the bullet had to "pull out" the rivet from the pallet, which had previously attached the bullet shank to the pallet and continue its flight to the target. And the hole formed in the pan from the rivet was intended to relieve the residual pressure of the powder gases. Interestingly, the groove in the bottom of the sleeve (7) was provided not only for fixing (fixing) the pallet and the bullet in the cartridge case when assembling the cartridge, but also so that the pallet, "straightening it out" while moving, "slightly increased the initial length of the sleeve”And the sleeve, pushing off from the front end of the chamber, provided the bolt with the necessary energy to reload the weapon and extract the spent cartridge case, thereby providing the possibility of creating an automatic self-loading weapon. Such is an interesting proposal … To be fair, I must say that the general idea of cutting off the powder gases is correct (excluding the hole in the pan from the rivet), but the design proposed by Bradford Holmes in 1922 does not stand up to strict criticism when analyzed in detail, especially taking into account practical experience and knowledge accumulated by the designers-cartridge-makers over the past almost 100 years.
We repeat once again that domestic specialists were and will remain the first who managed to implement the general idea in practice, who created a simpler and, most importantly, actually workable design of the SP-2 silent cartridge.
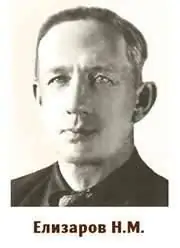
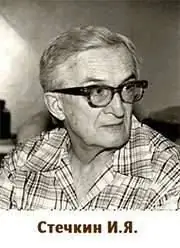
Its development gave impetus to the creation of even more advanced cartridges of a similar design. In the late 1950s - early 1960s. Specialists of the research structures of the special services developed a 9, 1-mm cartridge "Phalanx-A" for silent firing from a pistol (Product "D" and "DM") and a cartridge "Mundstuk-A" unified with it, designed for silent throwing of a grenade "Lizard". At the same time, around 1961, a 7.62-mm silent cartridge "Snake" ("PZ") was developed for the C-4 "Groza" double-barreled pistol, then its improved versions - "PZA" and "PZAM". These cartridges had greater power and better accuracy of fire, they used a standard bullet from 7, 62x39-mm cartridge mod. 1943. At the same time, they had larger dimensions, greater weight (especially "Phalanx-A") and a complex design, and were also not technologically advanced and expensive to manufacture.
Therefore, taking into account the advantages and disadvantages of the available standard cartridges for silent firing, at the end of 1962, the designers of TsNIITOCHMASH were tasked with developing a more technologically advanced and cheaper 7.62 mm silent cartridge, instead of the SP-2 and PZAM cartridges, but interchangeable with the SP cartridge -2 in overall dimensions. The last requirement was explained by the fact that the SP-2 cartridge was used for firing from the knife of the LDC scout. In addition, it was planned to develop a special pistol chambered for the SP-2.
This cartridge was named SP-3 and was developed mainly during 1963-1964. In 1965, an inventor's certificate No. 34306 was received for the design of a cartridge in the name of Ye. T. Rozanov. (responsible executor of the work), Smekaeva K. V. (scientific supervisor) and Nikishina G. I. (customer representative).
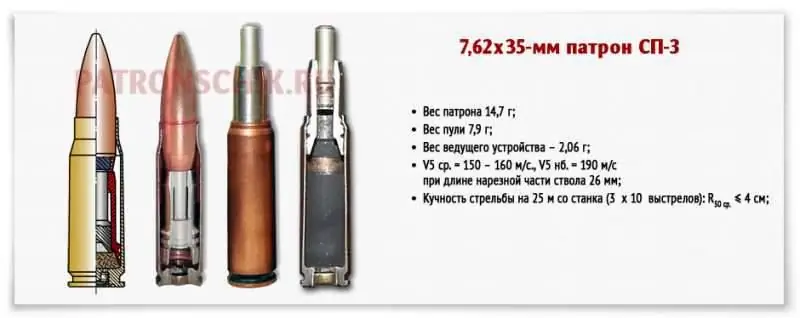
In the SP-3 cartridge, in accordance with the terms of reference, a standard bullet with a steel core from 7, 62x39 mm cartridge mod. 1943 and a sleeve from the SP-2 cartridge. The "highlight" of the design was the telescopic pushing device, which consisted of a sleeve and a rod located in it, which ensured the bullet guiding along the barrel bore when fired and cut off gases in the sleeve. In the technology of manufacturing elements of the cartridge and its assembly, there was a number of "know-how" to reduce sparking when fired. The use of the telescopic design of the leading device made it possible to create the SP-3 cartridge in the dimensions of the SP-2 cartridge, with a 2 times better accuracy of fire. In this case, the SP-3 cartridge is 30% shorter than the PZAM. The deceleration of the drive unit elements in the SP-3 is more extended in time, and the braking force is significantly reduced due to the sequential deceleration of the sleeve and stem and the plastic deformation of the liner slope. This, in turn, made it possible to use a thin-walled sleeve and reduce the weight of the cartridge in comparison with the PZAM cartridge by 3, 5 times, increase the manufacturability and reduce the cost of production by 3 - 4 times. Details about the history of development, subsequent modernization, design and technical characteristics of the SP-3, PZAM, PFAM and PMAM cartridges can be found in the third book of the monograph by V. N. Dvoryaninov "Live cartridges of small arms".
The SP-3 cartridge is the best and most perfect representative of the family of domestic silent cartridges with a pushing pan-stock, not only absorbing all the previous experience in their development, but also significantly improving in comparison with them. Experts still consider him the quietest and most graceful among them. In 1973, for its development, K. V. Smekaev. (scientific supervisor for research and development), Sabelnikov V. M. (director TSNIITOCHMASH) and Nikishin G. I. (representative of the customer) was awarded the title of Laureates of the USSR State Prize, and Rozanov E. T. (executive in charge) was awarded the Order of Lenin.
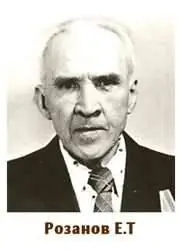
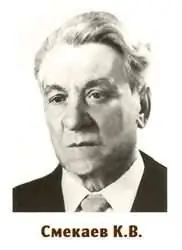
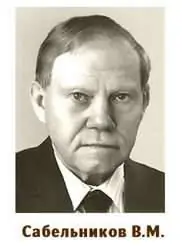
The SP-3 cartridge was adopted only in 1972. And during 1971 - 74, its so-called "introduction" at cartridge factories was going on. Thus, the development of the SP-3 cartridge, together with the development of its production, took a very long time - 12 years. It took such a long time to work out all the nuances of the design and technology of its manufacture, since the cartridge-makers faced a large number of problems and questions. Several times it seemed that the development of the cartridge was finally completed, but more and more new nuances and surprises “surfaced”.
On August 24, 1972, by order of the Minister of Defense of the USSR No. 145, "Small-sized special pistol" (SMP) chambered for SP-3 was put into service and received the index 6P24. The scout's shooting knife (NRS) did not undergo major changes and now it also used the SP-3 cartridge. But no self-loading (automatic) weapon was ever created for this cartridge.
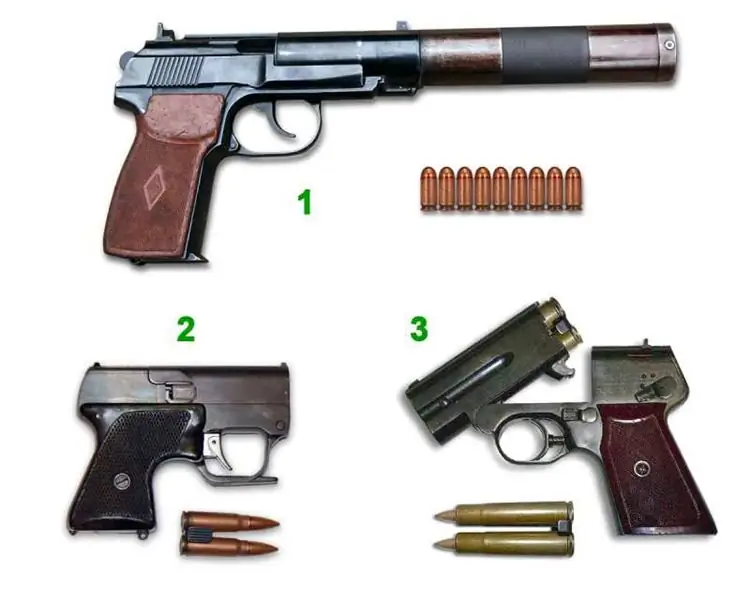
1 - 9-mm silent pistol PB (6P9) chambered for 9x18 PM with an expansion-type silencer (shown for scale);
2 - 7, 62-mm non-automatic double-shot pistol MSP chambered for SP3;
3 - 9, 1-mm non-automatic double-shot pistol S4M chambered for PFAM.
In articles on the history of small arms, it is often stated that a self-loading pistol chambered for the SP-3 cartridge could not have been developed due to the fact that its stock protrudes from the cartridge case by a significant amount after being fired. However, this is not entirely true. And not only because the length of the fired cartridge with the extended stem is only a few millimeters longer than the length of the cartridge with the bullet before the shot (see figure).
The development of a self-loading pistol chambered for the SP-3 was carried out in 1969 - 70. at the Tula Arms Plant, then in 1971 at TsNIITOCHMASH. These works showed the fundamental possibility of creating a self-loading weapon even for a low-power cartridge with a gas cut-off in the sleeve. But the SP-3 cartridge turned out to be unsuitable for this purpose, basically, and paradoxically, because of one of its advantages - the use of a thin-walled stamped sleeve. When extracting the spent cartridge case of the SP-3 cartridge, immediately after the shot, the primer fell out or the upper part of the case body was transversely broken under the influence of the high residual pressure of the powder gases. In order for it to decrease to an acceptable value due to the cooling of the gases, the removal of the cartridge case from the chamber during semi-automatic firing had to be done with a significant time delay. This forced to increase the free travel of the bolt carrier to values unacceptable in terms of the dimensions of the pistol, and the speeds of the moving parts of the automation in the extreme positions turned out to be much lower than was required to ensure the reliable operation of the pistol. Additional difficulties were caused by the metamorphosis of the SP-3 liner body and, especially, its muzzle when braking the pallet. By the way, this is what forced the gunsmiths to use in the design of the S-4 pistols and SMEs a not quite standard way of fixing the cartridge in the chamber - due to a special clip that held two cartridges by the grooves in the cases and inserted together with them into the pistol chambers when loading.
Since the need to create an automatic self-loading pistol was obvious, in 1971-1972. the search for technical solutions continued by the designers of TsNIITOCHMASH (department 46), in parallel with the specialists of the research structures of the special services. It was clear that both a new cartridge, of a different design, and a pistol of a non-standard design would have to be developed, since the known automation schemes were not suitable. And new, promising solutions and design schemes for weapons and cartridges were found!
In other words, such results are usually called inventions.